Hitachi Powdered Metals setzt auf Roboterautomatisierung und steigert Volumen um 400 % in einem angespannten Arbeitsmarkt
Pulvermetallurgie (PM) oder Sintern ist der Prozess des Verdichtens kundenspezifischer Mischungen von Element- oder Legierungspulvern in vorgefertigten Matrizen, um Maschinenteile unterschiedlicher Komplexität effizient herzustellen. Nach dem Verdichten werden die Formen in einem Ofen mit kontrollierter Atmosphäre erhitzt, um die Partikel zu binden und die Teile zu härten.
Das auch als Grünkompaktierung bezeichnete Verfahren liefert Near-Net-Komponenten, die typischerweise mehr als 97 Prozent des ursprünglichen Rohmaterials im fertigen Teil verbrauchen. Kundenspezifische Pulverlegierungsmischungen bieten die Möglichkeit, komplexe, sogar komplizierte Teile herzustellen, die die Festigkeits- und Toleranzspezifikationen erfüllen, die für äußerst anspruchsvolle Anwendungen erforderlich sind.
Das Werk von Hitachi Powdered Metal (USA) Inc. in Greensburg, Indiana, ist eines von neun solchen Hitachi-Werken weltweit. Es ist auf die Herstellung von Ventiltrieb- und Getriebekomponenten für Tierautomobilzulieferer in den USA spezialisiert und hat eine wachsende Präsenz bei Motorrad- und Landschaftsausrüstungsherstellern.
Anfangsmotivation
Hitachi Powdered Metals (HPM) begann im Jahr 2005 mit einer schrittweisen Investition in Industrieroboter im Werk Greensburg, angetrieben durch die Entstehung eines angespannteren Arbeitsmarktes und die Möglichkeit, ein extrem zerbrechliches Produkt herzustellen.
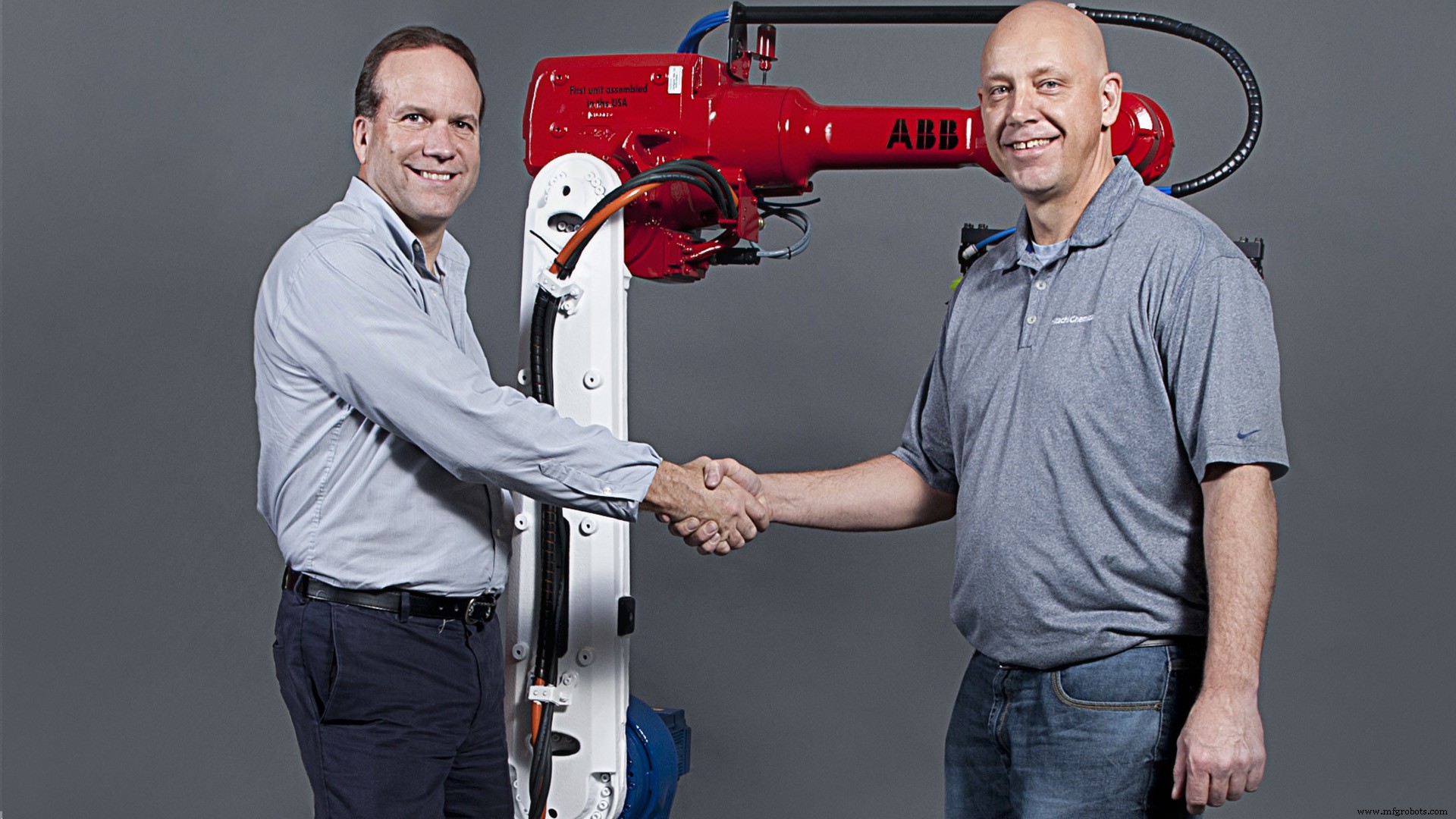
„Wir haben mit Robotern begonnen, weil wir ein Teil für einen Kunden herstellen mussten, der kleine, zerbrechliche Zähne hatte, die nicht manuell gehandhabt werden konnten, und zu diesem Zeitpunkt wurden alle unsere Verdichtungspressen von Hand bedient“, sagte Gregory Owens, Präsident von das HPM Werk Greensburg. „Die Senkung der Arbeitskosten war ebenfalls ein Faktor, aber kurz nach der ersten Installation eröffnete ein großer Automobil-OEM eine Produktionsstätte in der Stadt, und unser Arbeitskostenproblem wurde zu einem Problem der Verfügbarkeit von Arbeitskräften, da es extrem schwierig wurde, Mitarbeiter einzustellen und zu halten.“
Um die Kosten niedrig zu halten und Risiken während der ersten Testphase zu minimieren, erwarb HPM einen gebrauchten ABB S3-Roboter aus dem Jahr 1993 von CIM Systems Inc. im nahe gelegenen Noblesville, Indiana. James Adams, der einige Jahre zuvor zu HPM gekommen war ein Fertigungsentwicklungsingenieur, war durch seine Arbeit mit Robotern bei seinem vorherigen Arbeitgeber mit CIM, dem am längsten tätigen ABB Robotics Value Provider (d. h. Systemintegrator) in den USA, vertraut.
„CIM verfügte über einen gebrauchten Roboter, der uns den Weg in die Roboterautomatisierung erleichtern und unsere anfängliche Exposition begrenzen würde, falls er nicht wie beabsichtigt funktioniert“, sagte Adams. „Sie haben uns auch dringend benötigte Unterstützung bei der Programmierung und Integration des Systems in den bestehenden Betrieb gegeben.“
Reduzierter Ausschuss, bessere Arbeitsverteilung
Wenn die pulverisierten Metallteile aus der Presse kommen, bevor sie im Ofen gehärtet werden, können sie selbst bei der leichtesten Berührung leicht zerbröckeln. Mit dem neu installierten Roboter, der über einen Elektro-Magnetgreifer zum Handhaben des Teils verfügt, stieg die Ausschussrate des neuen Produkts von 11 Prozent bei manueller Tendenz auf 0,5 Prozent.
„Beim manuellen Herausziehen der Teile aus der Presse kam es zu erheblichen Handhabungsschäden. Das Teil könnte unmerklich verformt sein, aber Sie würden es nicht bemerken, bis es fünf Stunden später aus dem Ofen kam. Richtig programmiert und ausgestattet sind Roboter viel sanfter bei der Handhabung der Teile“, sagte Adams.
Das neue System ermöglichte es HPM, mehrere der manuellen Maschinenführer an weniger alltägliche Positionen in der Anlage zu versetzen, wodurch der Stress einer sich wiederholenden Aufgabe reduziert und die Arbeitskräfte effizienter neu verteilt wurden.
Produktion steigt um 400 Prozent
Im Laufe des nächsten Jahres fügte HPM fünf weitere gebrauchte S3-Roboter hinzu und wendete die Erkenntnisse aus dem ursprünglichen System an, um andere Kompaktpressen zu automatisieren. Nach 18 Monaten hatte HPM genug Schrott und Arbeit gespart, um in seinen ersten neuen Roboter zu investieren.
Spulen wir vor bis 2019. Mit über 200 installierten Robotern hat das Werk in Greensburg jetzt die gleiche Anzahl an Mitarbeitern wie vor 10 Jahren, produziert aber viermal so viel Volumen und liefert problemlos mehr Teile mit weniger Personal als jedes der globalen Hitachi PM-Werke .
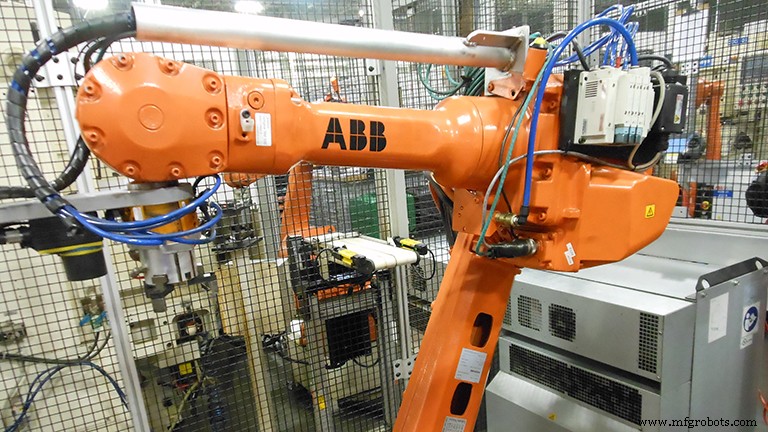
„Als der erste Roboter für das zerbrechliche Teil installiert war, wurde es sehr offensichtlich, dass wir von weiteren Roboterautomaten wirklich profitieren könnten“, sagte Owens. „Roboter haben unsere ursprünglichen Erwartungen bei weitem übertroffen, und angesichts des Arbeitskräftemangels, mit dem wir weiterhin konfrontiert sind, glaube ich ehrlich gesagt, dass Roboter uns davor bewahrt haben, möglicherweise nicht zu existieren.“
Mit dem Erfolg des ersten Roboters war das Tempo der nachfolgenden Installationen konstant. Es dauerte zehn Jahre, um 100 installierte Roboter zu erreichen, und dann, als sich Geschäft und Wirtschaft weiter verbesserten, nur noch vier Jahre, um die kürzlich installierten 200 sten zu erreichen Roboter.
Als sich die Möglichkeiten ergaben, kaufte HPM weiterhin gebrauchte ABB-Roboter in gutem Zustand, obwohl immer mehr neue Roboter zur Flotte hinzukamen. Tatsächlich war jeder seit #147 im Jahr 2015 hinzugefügte Roboter neu.
Die Installationsbasis von HPM umfasst eine Reihe kleiner und mittlerer sechsachsiger ABB-Roboter, einen Delta-Roboter und mehrere kürzlich hinzugefügte SCARA-Modelle. Zusammen mit 350 Mitarbeitern ist die Automatisierungsinvestition gut ausgelastet und läuft im Dreischichtbetrieb an fünf bis sechs Tagen in der Woche.
„Unsere Unternehmenszentrale befindet sich in Japan“, sagte Adams. „Sobald sie die Leistung der Roboter und den schnellen Return-on-Investment gesehen hatten, unterstützten sie unsere Roboteragenda sehr.“
Einige der Roboter, sowohl neue als auch gebrauchte, sind ABB Foundry Prime von ABB Robotics, Auburn Hills, Michigan. Es sind IP67-zertifizierte Modelle mit gut abgedichteten Verbindungen, die das Innenleben der Roboter vor dem feinen, scharfkantigen Metall schützen Pulver, die durch die Anlagenatmosphäre schweben. Die vielen standardmäßigen, IP65-zertifizierten Robotermodelle auf dem Boden von HPM sind robust und haben der staubigen Umgebung standgehalten.
Weitere Expansion
Die Verbreitung von Robotern bei HPM wurde durch die Replikation vorhandener Anwendungen und die Ausweitung der Automatisierung auf andere Funktionen in der Einrichtung unterstützt.
Nach der Installation des ersten Roboters, der die Kompaktpresse für das zerbrechlichste Produkt bediente, automatisierten Adams und sein Team die Entnahme der Kompaktpressen aus anderen Pressen nacheinander. Ein Teil dieses Prozesses bestand darin, jedes Teil auf eine Waage zu legen, um seine Unversehrtheit zu überprüfen. Nach der Überprüfung wurde das Teil auf ein Förderband gelegt, das zum Ofen führte.
Zusätzliche Arbeitseffizienz resultierte, und durch die geschickte Handhabung des Roboters stieg die Ausschussrate der weniger zerbrechlichen Teile von 7 Prozent auf dieselben 0,5 Prozent des ursprünglichen Teils.
Am Ende des Förderbandes werden die Teile auf Sinterschalen abgelegt, die gefüllt in Öfen zum Härteprozess gestellt werden. Dieser Ofenbeschickungsprozess wurde die zweite Hauptfunktion, die automatisiert werden musste.
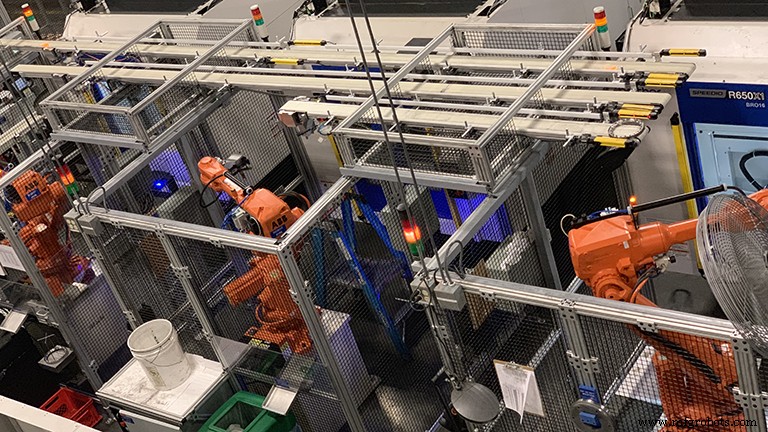
Anschließend wurden in gemessenem Tempo Roboter installiert, die die Teile von den Schalen nahmen und auf Paletten ablegten, während sie gleichzeitig Trennwände zwischen jede Palettenlage einsetzten.
„Als wir uns mit Robotern vertrauter machten, nahmen wir das, was wir gelernt hatten, und duplizierten Anwendungen in der gesamten Anlage“, sagte Adams. „Die Programmierung wurde viel einfacher, und am letzten Tag der Linieninstallation haben wir vorhandene Programme optimiert, kopiert und eingefügt, und wir waren in ein paar Stunden einsatzbereit.“
RobotStudio, die Offline-Simulations- und Programmiersoftware von ABB, wurde zu einem wertvollen Werkzeug, um die zunehmende Einführung von Robotertechnologie bei HPM voranzutreiben. Basierend auf dem ABB VirtualController, einer exakten Kopie der realen Software, die Roboter in der Produktion betreibt, führt RobotStudio realistische Simulationen durch, wobei Roboterprogramme und Konfigurationsdateien verwendet werden, die mit denen identisch sind, die in der Fertigung verwendet werden. Mit RobotStudio war Adams in der Lage, das optimale Zellenlayout zu entwerfen und seine Leistung zu überprüfen, bevor die Roboter in einen bestimmten Betrieb integriert wurden.
„Es ist die beste Software, die jemals entwickelt wurde“, sagte Adams. „Es spart Zeit und Geld sowohl bei der Erstellung von Systemen für neue Anwendungen als auch bei der Replikation von Systemen, die wir bereits in anderen Bereichen der Anlage installiert haben.“
Einführung von Vision
Die relative Einfachheit der Replikation existiert erst, nachdem eine bestimmte Anwendung im Fertigungsbereich installiert und verfeinert wurde. Neue Anwendungen sind oft anspruchsvoller. Nach 18 Monaten und der erfolgreichen Integration von sechs Pressen-Pflegerobotern hatte HPM das Vertrauen, die damals (2006) noch in den Kinderschuhen steckende Vision-fähige Technologie einzusetzen, um den komplexen Präge- oder Nachpressvorgang roboterhaft zu automatisieren.
Nachdem Teile aus dem Ofen kommen, können sie sich oft verziehen, was erfordert, dass sie in eine Presse gelegt werden, die sie wieder gerade oder flach prägt. Viele Teile haben Keilnuten oder Zähne, die in der Form so platziert werden müssen, dass alle Aspekte genau ausgerichtet sind. Vor der Ankunft der Roboter wurden die zu prägenden Teile von einem harten Automatisierungssystem gehandhabt, das bei vielen verschiedenen Produktvarianten häufige und zeitaufwändige Umrüstungen erforderte. Die Umstellungen dauerten so lange, dass Backups von 250 Produktchargen mit jeweils etwa 100 Teilen üblich waren.
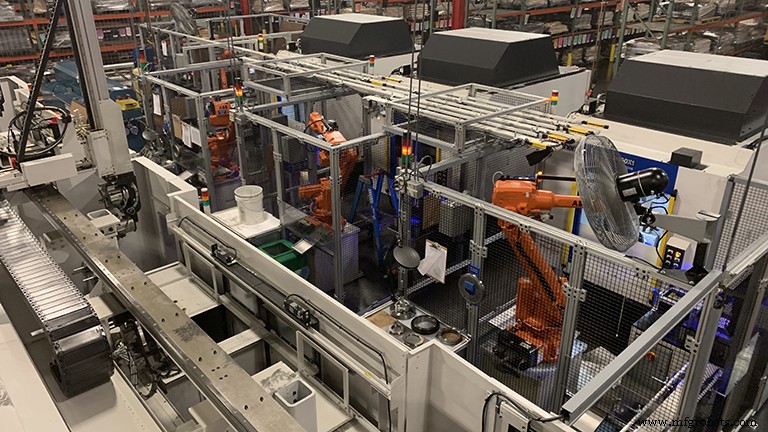
Mit dem Vision-fähigen Roboter gibt es keine Ausfallzeiten. Der Roboter ist in der Lage, das Teil aus einer Gruppe von vielen verschiedenen Teilen zu identifizieren, aufzunehmen, radial auszurichten und genau in der Nachpresse zu positionieren.
Da das Bildverarbeitungssystem mit der neuesten Robotertechnologie verbunden werden musste, war dies der erste neue ABB-Roboter, der im Werk Greensburg installiert wurde. Kurz nach Inbetriebnahme wurden zwei weitere neue Roboter für die gleiche Anwendung angeschafft.
„Vor der Installation des Prägestationsroboters war das Druckpersonal jeden Tag im Einsatz“, sagte Adams. „Sechs Monate nach der Installation des ersten Vision-Roboters gab es keine Backups mehr und die Mitarbeiter hatten ihre Wochenenden frei!“
Weitere Vision
Beim letzten der wichtigsten zu automatisierenden Prozesse, dem Depalettieren von Teilen, die zur speziellen Wärmebehandlung geschickt worden waren, setzte HPM die Vision erneut ein. Obwohl die Teile ordentlich auf einer Palette auf mehreren Ebenen positioniert verschickt werden, kommen sie relativ ungeordnet zurück und lassen sich nur schwer entstapeln. Ein ABB-Roboter mit integrierter Bildverarbeitung ist in der Lage, die Teile zu finden und sicher zu greifen, damit sie sicher depalettiert werden können.
„Das ist eine der einzigartigen Fähigkeiten von ABB-Robotern“, sagte Dave Fox, Präsident von CIM Systems, der bei der Integration der verschiedenen Bildverarbeitungssysteme half. „Die Teile liegen wirklich desorientiert auf den Kufen, nicht in gleichmäßigen Reihen, einige liegen auf dem Kopf. Ein typischer sechsachsiger Roboter hätte alle möglichen Singularitätsprobleme und würde in eine Position geraten, in der er sich nicht mehr bewegen kann. Aber der ABB-Roboter, der fortschrittliche Singularitätsvermeidung verwendet, ist in der Lage, die Teile zu finden, sie zu greifen und sie sicher auf einem Förderband zu platzieren, ohne einen Takt zu verpassen.“
SCARA-Roboter für die Qualitätsprüfung
Es überrascht nicht, dass eine kürzlich durchgeführte Suche nach einem effizienteren System zur Inspektion von Ventilführungen zu Robotern zurückführte, in diesem Fall zu einer Gruppe von SCARA-Modellen (Selective Compliance Assembly Robot Arm) von ABB, die typischerweise für die Montage von Kleinteilen und die Materialhandhabung verwendet werden.
Das HPM-Protokoll sieht eine 100-prozentige Inspektion aller Ventilführungen vor, was angesichts der Vielzahl der zu prüfenden Teile ein ziemliches Unterfangen ist:30 verschiedene Größenvarianten und 16 Erkennungspunkte für jedes Teil. Da das vorherrschende Hard-Automation-Testsystem nicht ausreichend mit dem Volumen Schritt halten konnte, begann Adams nach einem besseren System zu suchen.
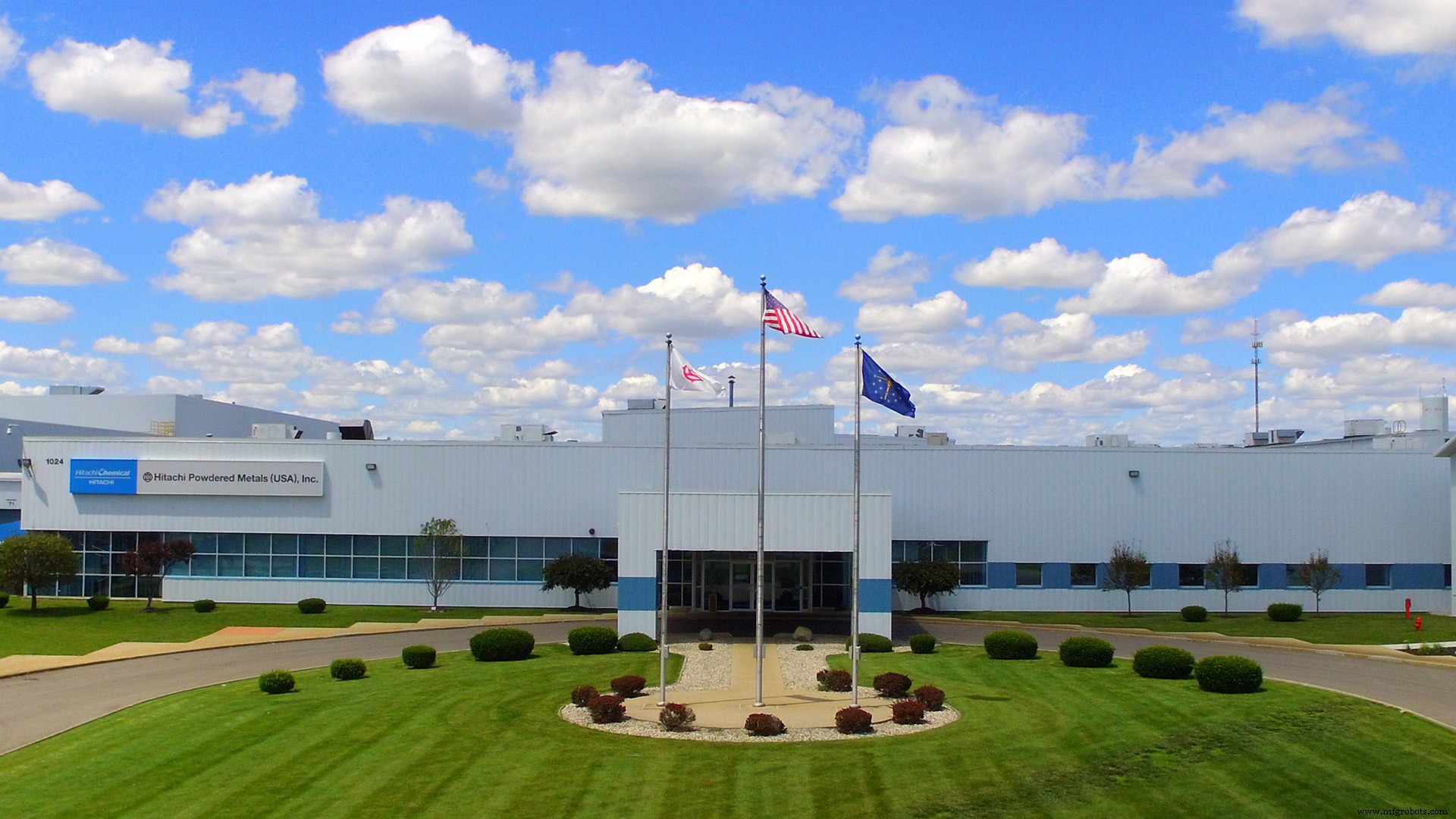
Nachdem Fox verschiedene Optionen geprüft hatte, die alle zu viele bewegliche Teile hatten und eine komplexe Konstruktion erforderten, schlug Fox vor, ein System rund um die SCARA-Roboter zu entwerfen, die ABB 2016 in sein Portfolio aufgenommen hatte. Sie waren sicherlich schnell genug, hatten eine hohe Wiederholgenauigkeit und hatten es eine geringe Standfläche und eine ungehinderte Form der Befestigung, die auf engstem Raum Platz findet.
Ein relativ einfaches System wurde mit drei SCARA-Robotern entwickelt, die einzelne Ventilführungen von einem Trichterförderer entnehmen und sie Sichtkameras und einem stationären „Komparator“ in den verschiedenen Winkeln präsentieren, die für den Zugriff auf die 16 Erkennungspunkte erforderlich sind. Die Teile, die bestanden wurden, wurden auf ein Förderband gelegt und die nicht bestandenen Teile wurden in Ausschussbehälter gelegt.
Mit der Flexibilität, jede unterschiedliche Teilevariation mit ähnlicher Leichtigkeit geschickt zu handhaben, kann das System ein Teil alle zwei Sekunden prüfen, 30 Prozent schneller als die vorherige Methode. Da die Bewegungen auf eine kurze Distanz beschränkt sind und die Teile sehr leicht sind, würde ein sechsachsiger Roboter nicht so effektiv arbeiten wie der schlanke SCARA mit begrenzter Reichweite.
„Die SCARAs sind eine großartige Ergänzung des ABB-Portfolios. Ohne diese Lösung hätte Hitachi wahrscheinlich nach einer anderen Technologie für die Teileinspektion suchen müssen“, sagte Fox. „Es war schön, eine andere Anwendung für Roboter zu finden, auch wenn das nicht die erste Option war, die mir in den Sinn kam.“
CIM-Systeme immer vorhanden
Eine Konstante, die vom ersten bei HPM installierten Roboter bis heute entweder im Vordergrund oder im Hintergrund mitgewirkt hat, ist CIM Systems. CIM ist bei Bedarf immer verfügbar und hat HPM mit neuen und gebrauchten Robotern eingerichtet, bei der Programmierung und Fehlerbehebung geholfen und, was vielleicht am wichtigsten ist, den HPM-Mitarbeitern beigebracht, viele Dinge selbst zu erledigen.
Wenn HPM Roboter in eine neue Anwendung integrierte, ob mit Vision oder auf andere Weise, übernahm CIM die Einrichtung und Programmierung, wobei es stets darauf bedacht war, sein Fachwissen zu teilen, einschließlich der Verwendung von RobotStudio. Während der gelegentlichen Pause in der Roboteranschaffungszeitachse von HPM stand CIM zur Verfügung, um Programme zu aktualisieren, schwer fassbare Ersatzteile für ältere Modelle zu finden oder Ratschläge zur Arbeit mit Robotern verschiedener Jahrgänge zu geben.
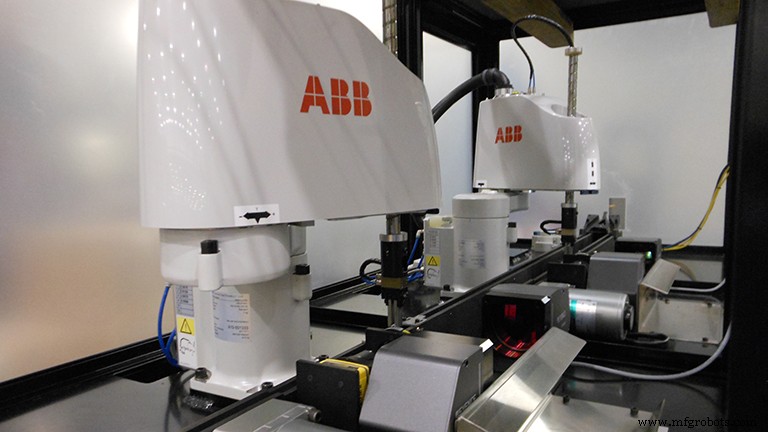
„Als wir jeden der verschiedenen Prozesse erreichten, ließen wir CIM die anfängliche Integration und Programmierung durchführen. Als wir begannen, Prozesse im gesamten Werk zu replizieren, hatten wir genug gelernt, um vieles selbst zu tun“, sagte Adams. „Aufgrund seiner engen Beziehung zu ABB weiß Dave Fox immer, wann neue Technologien auf den Markt kommen und welche Roboter für unsere verschiedenen Anwendungen optimal wären. Der Support von CIM Systems und der Service von ABB waren eine ideale Kombination.“
Bei einer so langjährigen Beziehung ist es keine Überraschung, dass der erste Roboter, der 2017 in der US-Fertigungsstätte von ABB in Auburn Hills vom Band lief, von CIM bei HPM in Betrieb genommen wurde. Der einzigartige IRB 2400-Roboter wurde im Werk kundenspezifisch in Rot, Weiß und Blau lackiert und ist an prominenter Stelle in der HPM-Anlage positioniert, wo er Inspektions- und Palettierungsaufgaben ausführt.
„Wir freuen uns, dass wir den ersten in Amerika hergestellten Roboter für HPM beschaffen konnten“, sagte Fox. „Dies ist besonders wichtig, da das Werk in Indiana über den flexibelsten Automaten der vielen globalen HPM-Anlagen verfügt.“
Unterstützung anderer HPM-Einrichtungen
Die HPM-Unternehmensleitung in Japan bemerkte die großen Produktivitätsverbesserungen, die das Greensburg-Team mit Robotern erzielte, und beauftragte Adams und Owens 2017 mit der Leitung einer „Global Robotics“-Initiative, um die anderen Hitachi-Pulvermetallwerke auf der ganzen Welt beim Ausbau ihres Einsatzes von Robotern zu unterstützen .
Das zweijährige Programm hat die Halbzeit überschritten, und die angeschlossenen Unternehmen beginnen, erhebliche Produktivitätssteigerungen zu realisieren, selbst bei den niedrigeren Arbeitskosten in den anderen Ländern.
Adams hat die Fernüberwachungsfunktion von ABB bei HPM eingerichtet, damit er oder Mitglieder seines Teams sehen können, wie Roboter arbeiten, und die meisten Probleme von überall außerhalb der Fabrik auf einem Laptop, Tablet oder Smartphone beheben können. Mit den neueren Robotern hofft HPM, die Vorteile von ABB Ability Connected Services nutzen zu können – dem einheitlichen, branchenübergreifenden, digitalen Angebot von ABB – das Echtzeitdaten über den Status und die Leistung von Robotern von jedem Standort aus bereitstellt.
Zukunftspläne
Die fortlaufende Mission von HPM umfasst die Verbesserung seiner Betriebsabläufe durch Roboterautomatisierung.
„Wir erwarten auf absehbare Zeit ein Wachstum von 10 Prozent pro Jahr, und wir müssen alles tun, um wettbewerbsfähig zu bleiben“, sagte Owens. „Wir prüfen, welche Getriebeteile wir für Elektrofahrzeuge herstellen können, und haben uns zum Ziel gesetzt, in Segmente außerhalb des Automobilbereichs wie Schwermaschinen vorzudringen, wo Metallpulver möglicherweise Teile aus anderen Materialien zu geringeren Kosten ersetzen kann .“
„Ich gehe davon aus, dass das Tempo der Roboterinstallationen stabil bleiben oder sogar zunehmen wird“, sagte Owens.
Informationen zu Hitachi Powdered Metals (USA) Inc. erhalten Sie unter www.hitachi-pm.us oder telefonisch unter 812-663-5058. Informationen zu CIM Systems Inc. finden Sie unter www.cimrobotics.com oder telefonisch unter 317-773-5600. Informationen von ABB Robotics erhalten Sie unter www.abb.com/robotics oder telefonisch unter 248-391-9000.
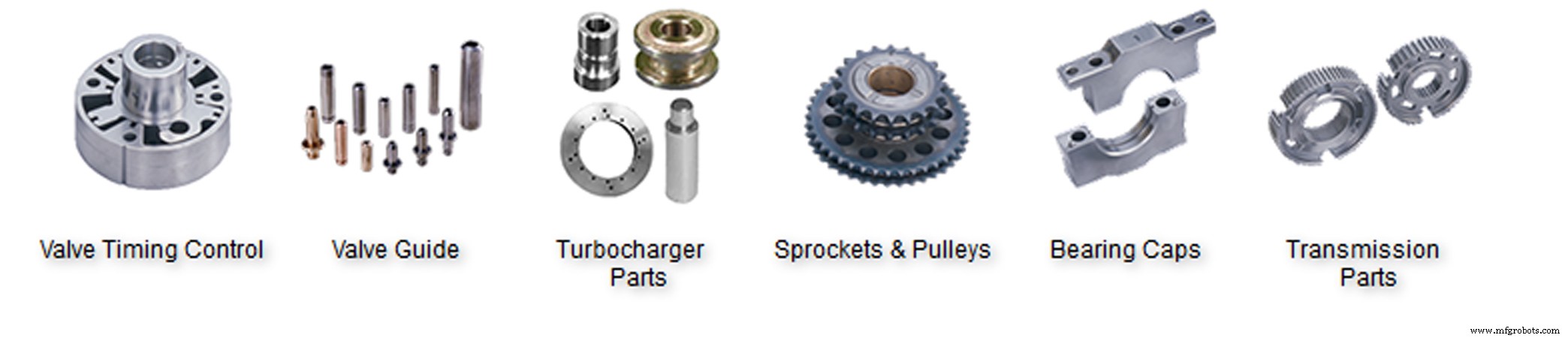
Automatisierungssteuerung System
- Logistik- und Lagerautomatisierung
- Mehr Automatisierung =leistungsfähigere Roboter
- NPE2018:Roboter und Automatisierung bewältigen steigende Komplexität
- Automatisierung:Kompatible Entgratklinge für Roboter
- ABB prognostiziert Schlüsseltrends, die die Roboterautomatisierung im Jahr 2022 verändern werden
- Eine neue Art von Roboter-"Gehirn" könnte moderne Fabriken verändern
- Hitachi erwirbt Robotik-Systemintegrator JR Automation für 1,4 Milliarden US-Dollar
- Hitachi schließt Übernahme von JR Automation ab
- ATI Industrial Automation führt neuen Schwingschleifer für Roboter ein
- Markt für robotergestützte Prozessautomatisierung erhält Impulse von Blue Prisms Digital Workforce und seiner außergewöhnlich gesicherten Automatisierung