Warum die Inspektion auf der Maschine der Schlüssel zur Präzisionsbearbeitung ist
Zur Qualitätskontrolle von CNC-bearbeiteten Teilen verwenden die meisten Werkstätten eine Koordinatenmessmaschine. Ein CMM prüft, ob die Geometrie und Abmessungen eines fertigen Teils mit dem ursprünglichen Design übereinstimmen, und stellt sicher, dass der Kunde keine fehlerhaften Teile erhält. Es identifiziert selbst geringfügigste Fehler und ermöglicht dem Maschinisten, ein fehlerhaftes Teil nachzuarbeiten.
Für einen Besitzer einer Maschinenwerkstatt ist das CMM jedoch alles andere als eine perfekte Lösung. Während diese Art der Inspektion dem Kunden Sicherheit bietet, garantiert sie dem Maschinisten keine hohe Produktivität. Wieso den? Denn Fehler nach der Bearbeitung zu identifizieren bedeutet, dass Sie bereits zu spät sind, um Kosten zu decken. Wenn ein Teil nachbearbeitet werden muss, weil die KMG-Maschine ein negatives Ergebnis liefert, verringert sich der Wert dieses Teils um die Hälfte. Dafür wird doppelt so viel Zeit aufgewendet wie auch doppelt so viel Material.
Eine alternative Lösung ist die Maschineninspektion mit einem Werkzeugmaschinenmesssystem. Werkzeugmaschinenmesssysteme sind Messgeräte, die an der CNC-Maschine selbst angebracht sind und zum Einrichten von Teilen und Messen von Abmessungen während und unmittelbar nach dem Bearbeitungsprozess verwendet werden.
Dieser Artikel erklärt, wie wir in unserer CNC-Werkstatt die Inspektion auf der Maschine einsetzen und warum CNC-Maschinenwerkstätten diesem Beispiel folgen sollten.
1. KMG-Engpässe beseitigen
Die Beschränkung der Qualitätskontrolle auf ein KMG hat erhebliche Nachteile, und die Probleme können über eine bloße Verdoppelung der Arbeitszeit und der Materialkosten hinaus eskalieren. In einer geschäftigen Werkstatt wird jeder CNC-Maschine wahrscheinlich ein neues Setup zugewiesen, sobald ein Satz Teile vom Arbeitstisch entfernt wird. Wenn das KMG später einige Teile zurückweist, muss der Maschinist warten, bis eine Maschine verfügbar wird – oder schlimmer noch, einen anderen Job unterbrechen – und dann die Maschine wieder neu einrichten. Zurückgewiesene Werkstücke können die Produktion verlangsamen und einen Dominoeffekt erzeugen, der viele Aufträge verzögert.
Außerdem kann die Abhängigkeit von einem KMG zu langen Warteschlangen führen, da jeder Auftrag in der Werkstatt von derselben Maschine oder Maschinengruppe geprüft werden muss. Die Integration der Inspektion in die CNC-Maschinen selbst kann den KMG-Engpass entschärfen, da die Inspektionslast auf mehrere Systeme verteilt oder in einigen Fällen vollständig von der CNC-Maschine übernommen werden kann.
2. Effizienz verbessern
Der Einsatz eines KMG ist in der Regel für die Qualitätskontrolle erforderlich, insbesondere bei der Präzisionsbearbeitung, da es prüft, ob die Werkstücke den geometrischen und dimensionalen Spezifikationen entsprechen. Aber die Inspektion auf der Maschine muss das KMG nicht ersetzen; Stattdessen kann es allein oder zusammen mit dem CMM arbeiten, um die Inspektion – und den gesamten Produktzyklus – effizienter zu gestalten.
Ein Messsystem für Werkzeugmaschinen, das an der Maschinenspindel oder am Revolver montiert ist, bietet einer Werkstatt zahlreiche Vorteile. Das System kann zum Identifizieren und Einrichten von Werkstücken verwendet werden – ein Vorgang, der manuell 10 Minuten, mit einem Messtaster jedoch nur Sekunden dauern kann – und kann Merkmale während des Bearbeitungszyklus und unmittelbar danach messen, wenn sich die Werkstücke noch auf dem Arbeitstisch befinden. P>
Werkstücke schnell rüsten
Ein Messsystem kann auch Aufgaben wie die Überwachung der Oberflächenbeschaffenheit des Werkstücks und die Einleitung einer automatischen Offset-Korrektur übernehmen. Darüber hinaus unterbrechen viele Prüfroutinen den Bearbeitungsprozess nicht, sodass die Inspektion ohne Unterbrechung durchgeführt werden kann.
Messtaster sind nützlich, weil sie signifikante Fehler frühzeitig erkennen, was die Verschwendung sofort reduziert und, wenn danach ein KMG verwendet wird, die Wahrscheinlichkeit verringert, dass das KMG ein Teil zurückweist. Wenn ein KMG verwendet wird, ermöglichen Sonden auch dem Qualitätskontrollpersonal, ihre Abtastrate zu reduzieren. So können sie beispielsweise eines von 50 Teilen auf dem KMG statt eines von 20 prüfen, da sie wissen, dass die meisten möglichen Fehler von der Sonde auf der Maschine erfasst und korrigiert worden wären. Die Einführung der Inspektion auf der Maschine kann daher die Gesamtprüfzeit verkürzen und gleichzeitig den KMG-Engpass verringern, Teile schneller versenden und die Produktivität der Werkstatt steigern.
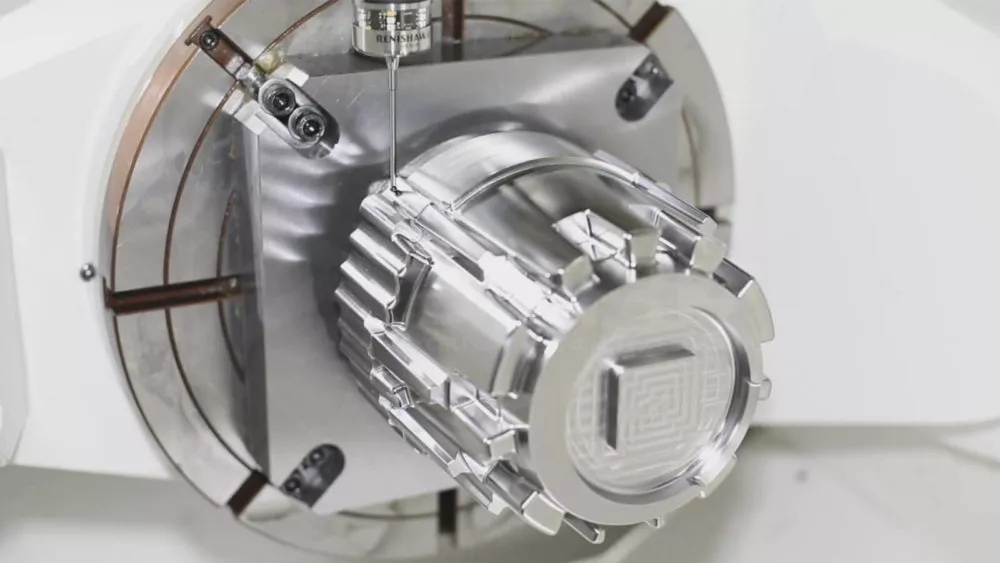
In-Prozess-Inspektion für bearbeitete Teile
3. Erhöhen Sie die Genauigkeit für die Nachbearbeitung
Die Inspektion auf der Maschine kann in praktisch allen CNC-Bearbeitungssituationen von Vorteil sein und die Wahrscheinlichkeit, dass fehlerhafte Teile verschrottet werden müssen, drastisch reduzieren. Tastsysteme sind jedoch besonders wertvoll, wenn es um die Präzisionsbearbeitung von Guss- oder Schmiedeteilen geht.
Die Bearbeitung von Teilen aus einem Werkstück aus extrudiertem Metall ist eine Sache, aber die Bearbeitung von geschmiedeten oder gegossenen Teilen ist eine ganz andere. Diese Metallbearbeitungsprozesse neigen dazu, geringfügige Abweichungen zwischen den Einheiten zu erzeugen, daher ist es entscheidend, dass die CNC-Maschine mit jedem leicht unterschiedlichen Teil richtig kalibrieren kann. Ein Messsystem auf der Maschine hilft der Maschine dabei.
Das On-Machine-Inspection-System gewährleistet die Genauigkeit bei der Bearbeitung als Sekundärprozess, selbst bei geometrischen Abweichungen zwischen den Teilen. Es ist besonders nützlich für Teile, die mit Druckguss und Feinguss hergestellt wurden.
4. Erhöhen Sie die Genauigkeit für Formen
Die On-Machine-Inspektion ist ein besonders wertvoller Vorteil bei der Herstellung von Formen für den Spritzguss und andere Formgebungsverfahren. Sonden erhöhen die Genauigkeit bei der Bearbeitung von Kernen und Hohlräumen, was zu besseren Formteilen und einer geringeren Abhängigkeit von der Nachbearbeitung von Kunststoffteilen führt, bei denen Unvollkommenheiten, die durch minderwertige Formen verursacht werden, behoben werden müssen.
Der Formenbau kann auf verschiedene Weise von einem On-Machine-Messtaster profitieren – vor, während und nach der CNC-Bearbeitung von Formkomponenten. Vor der Bearbeitung kann ein Messtaster das Werkstück lokalisieren und zusätzlich die Ausrichtung und Drehung des Teils bestimmen. Während der Bearbeitung kann es das Schneidwerkzeug automatisch neu ausrichten und Offsets als Reaktion auf Temperaturänderungen aktualisieren. Und bevor das Teil die CNC-Maschine verlässt, kann die Sonde werkzeugspezifische Aufgaben wie das Überprüfen und Verifizieren des Elektrodenzustands ausführen. Jede dieser Funktionen erhöht die Genauigkeit der Formenherstellung und damit die Qualität der Formteile.
Die Verwendung der Inspektion auf der Maschine kann daher die Qualität, Wiederholbarkeit und Genauigkeit von bearbeiteten Formen verbessern und gleichzeitig dazu beitragen, durch Temperaturänderungen verursachte Schwankungen zu verwalten und zu bekämpfen, die zu Merkmalen außerhalb der gewünschten Toleranz führen können.
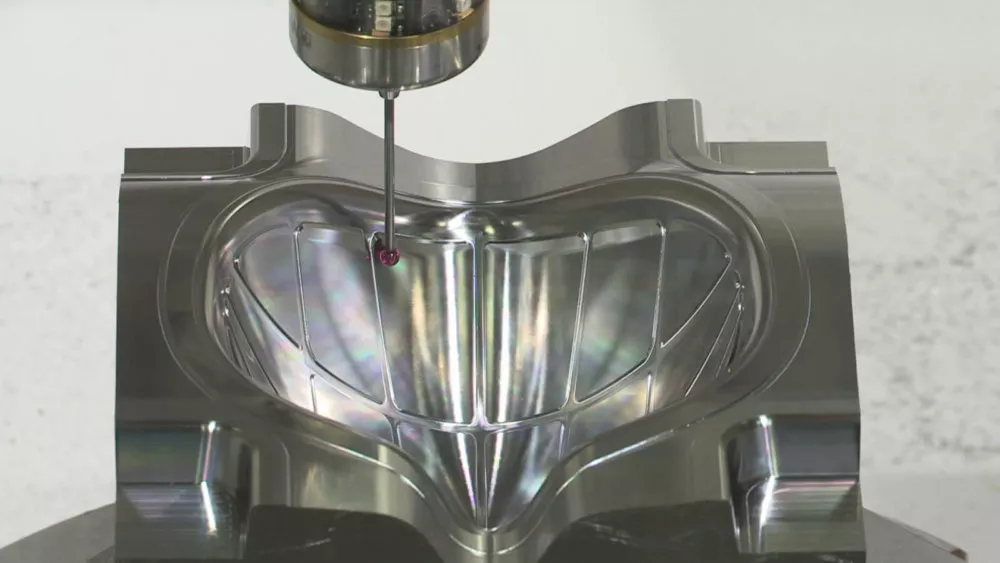
In-Prozess-Inspektion für Formhohlräume
Verbesserte Präzisionsbearbeitung
Zusammenfassend können On-Machine-Inspektionssysteme für CNC-Maschinen für Maschinenwerkstätten sehr wertvoll sein, da sie die folgenden Vorteile bieten:
- Erfassen Sie Fehler frühzeitig
- Sofortiges Feedback
- Automatische Offset-Korrektur
- Inspektionsrückstände reduzieren
- CMM-Engpässe beseitigen
- CMM-Abtastrate reduzieren
- Reduzieren Sie die Gesamtprüfzeit
- Schrott reduzieren
- Produktivität steigern
- Erhöhen Sie die Bearbeitungsgenauigkeit bei Guss- und Schmiedeteilen
- Erhöhen Sie die Bearbeitungsgenauigkeit bei Formhohlräumen
3ERP, ein Spezialist für Rapid Prototyping und Kleinserienfertigung, verwendet Werkzeugmaschinenmesstaster von Renishaw für die Präzisionsbearbeitung. Seit der Einführung dieser Strategie ist die Produktivität gestiegen und das Unternehmen konnte Teile schneller versenden.
Obwohl das KMG nach wie vor ein kritisches Element in den Qualitätskontrollverfahren von 3ERP ist, haben Messtaster auf der Maschine die Belastung des KMG verringert, während sie in Bezug auf die Prüffähigkeiten praktisch der eigenständigen Maschine entsprechen. Entscheidend ist, dass sowohl die Maschinenwerkstatt als auch der Kunde von diesem Umzug profitiert haben.
CNC-Maschine
- Auswahl Ihrer Präzisions-CNC-Bearbeitung von Metallen
- Präzisions-CNC-Bearbeitung und Metalle
- Metalle, die in der Präzisions-CNC-Bearbeitung verwendet werden
- Zu berücksichtigende Eigenschaften bei der Auswahl einer Präzisions-CNC-Werkstatt
- Präzisions-CNC-Bearbeitung vs. Standardbearbeitung
- Präzisions-CNC-Bearbeitung – Sicherheit geht vor!
- Werkstattausrüstung
- Toleranz und Präzisions-CNC-Bearbeitung
- Präzisions-CNC-Bearbeitung – Warum Genauigkeit wichtig ist
- Details, die wir über Ihr Präzisions-CNC-Bearbeitungsprojekt besprechen müssen