Vollelektrisches Motorboot testet das Wasser auf recycelte Kohlefasern
RS Sailing (Romsey, Großbritannien) ist bekannt für die Herstellung von Segelbooten von Weltklasse und behauptet, bei ihrer Herstellung so viele recycelbare Materialien wie möglich zu verwenden. Vor drei Jahren gründete das Unternehmen die Schwestermarke RS Electric Boats, die sich auf die Entwicklung und Herstellung von batterieelektrischen Festrumpfschlauchbooten (RIB) spezialisiert hat – leichte Motorboote mit einem starren Rumpf und aufgeblasenen Hochdruckluftschläuchen an den Seiten des Bootes für zusätzlichen Auftrieb. RIBs werden in der Freizeit verwendet und werden oft von Ersthelfern, Militärpersonal oder Trainerstab für Bootsrennen eingesetzt.
Alex Newton-Southon, CEO – Design &Technologies bei RS Sailing, erklärt, dass RS Electric Boats das Gleiche auf dem Schifffahrtsmarkt tun möchte, da die Autohersteller mehr elektrifiziert werden wollen und über nachhaltige Fertigung und Materialien nachdenken. „Für uns ist klar, dass Elektroboote der Markt sein werden. In Wirklichkeit ist ein herkömmlicher Außenbordmotor etwa 50-mal umweltschädlicher als heutige Autos. Wir wollen unseren Beitrag zum Schutz des Planeten leisten“, sagt er.
In den letzten drei Jahren war es ein Ziel, den Markt in Richtung nachhaltigerer Antriebs-, Material- und Herstellungsentscheidungen zu drängen, da RS Electric Boats daran gearbeitet hat, sein erstes batterieelektrisches RIB zu entwickeln und zu vermarkten. 2019 stellte RS Electric Boats die Pulse 58 vor concept RIB auf der Internationalen Bootsausstellung in Düsseldorf in Deutschland. Dieses Vorführboot wies mehrere Flachsfaser-/Bio-Epoxid-Komponenten auf, darunter Rumpf, Deck und Konsolen.
Seitdem wurden die Materialentscheidungen und das Gesamtdesign mindestens dreimal wiederholt – „plus eine erhebliche Menge an Optimierungen am gesamten Boot“, räumt Newton-Southon ein –, was letztendlich zum Pulse 63 . führte , soll Anfang 2022 auf den Markt kommen.
Die erste Flachsfaserverbund-Iteration:Pulse 58
Die meisten RIBs werden von standardmäßigen kraftstoffbetriebenen Motoren angetrieben, mit einigen Ausnahmen für kleine (ein- bis zwei-Personen-) batteriebetriebene Designs. RS Electric Boats behauptet den Puls 63 , das für bis zu acht Personen ausgelegt ist, ist das erste in der Branche, das einen vollelektrischen Antrieb für ein Boot dieser Größe verwendet.
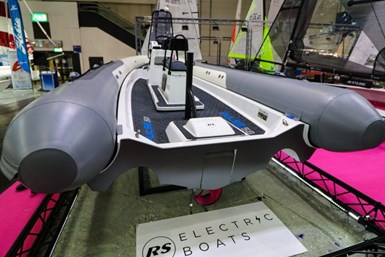
Der Rumpf und die Gesamtform des Bootes mussten speziell für den elektrischen Antrieb entwickelt werden. „Wenn man mit der Entwicklung eines batterieelektrischen RIB beginnt, ist eine Sache sehr offensichtlich, dass man nicht einfach ein elektrisches Antriebssystem in ein normales Boot einbauen kann. Sie müssen bei Null anfangen, denn das Design muss es dem Boot ermöglichen, sehr effizient zu sein, und das hängt zum Teil vom Gewicht ab. Es ist sehr wichtig, dass das Boot so stark und steif wie möglich konstruiert ist, um es so leicht wie möglich zu machen“, erklärt Newton-Southon.
Die Batteriekonsole sei „die Hauptstruktur des Ganzen“, fügt er hinzu. Der Bootsrumpf ist eine solide monolithische Struktur mit einem verbundenen Deck, das auch die Batterien beherbergt. Es werden keine Querschotte oder Rahmen benötigt.
Der 5,8 Meter lange Puls 58 RIB, das RS Electric Boats 2019 auf den Markt brachte, verfügte über einen Rumpf, ein Deck, eine Konsole, einen Batteriekasten und Sitzleisten, die vom lokalen Hersteller Norco (Poole, Großbritannien) durch Infusion aus biobasiertem Epoxid, natürlich gewonnenen Flachsfasern und bei Bedarf recyceltem PET-Kern hergestellt wurden.
In den Jahren 2019 und 2020 wollte RS Electric Boats die Produktion für die Pulse 58 . hochfahren und beginnen mit dem Verkauf an Kunden. Durch die COVID-19-Pandemie verursachte Rückschläge sowie Beschaffungsprobleme bei den biobasierten Materialien führten jedoch zu einer kurzen Verzögerung und einigen Designverschiebungen.
Design-Iterationen und recycelte Kohlefaser:Pulse 63
Im Mai 2021 beschloss RS Electric Boats, die Marke zu aktualisieren und sich an Designänderungen und Materialentscheidungen auszurichten, die in Vorbereitung auf den Produktionshochlauf getroffen wurden. Die zusammengesetzten Komponenten für den umbenannten 6,3-Meter-Pulse 63 werden von MTAG Composites Ltd. (Coningsby, Großbritannien) hergestellt, einem Hersteller, der seit vielen Jahren mit RS Sailing in der Werkzeugentwicklung und im Bootsbau zusammenarbeitet. Wie vermarktet, der Pulse 63 RIB kann eine Höchstgeschwindigkeit von 23 Knoten erreichen und hat eine maximale Reichweite von 100 Seemeilen. Es kann auch mit einer Vielzahl von optionalen Funktionen wie Abschleppstangen, Einpunkt-Hebebühnen, Überdachungen und verschiedenen Sitzkonfigurationen angepasst werden.
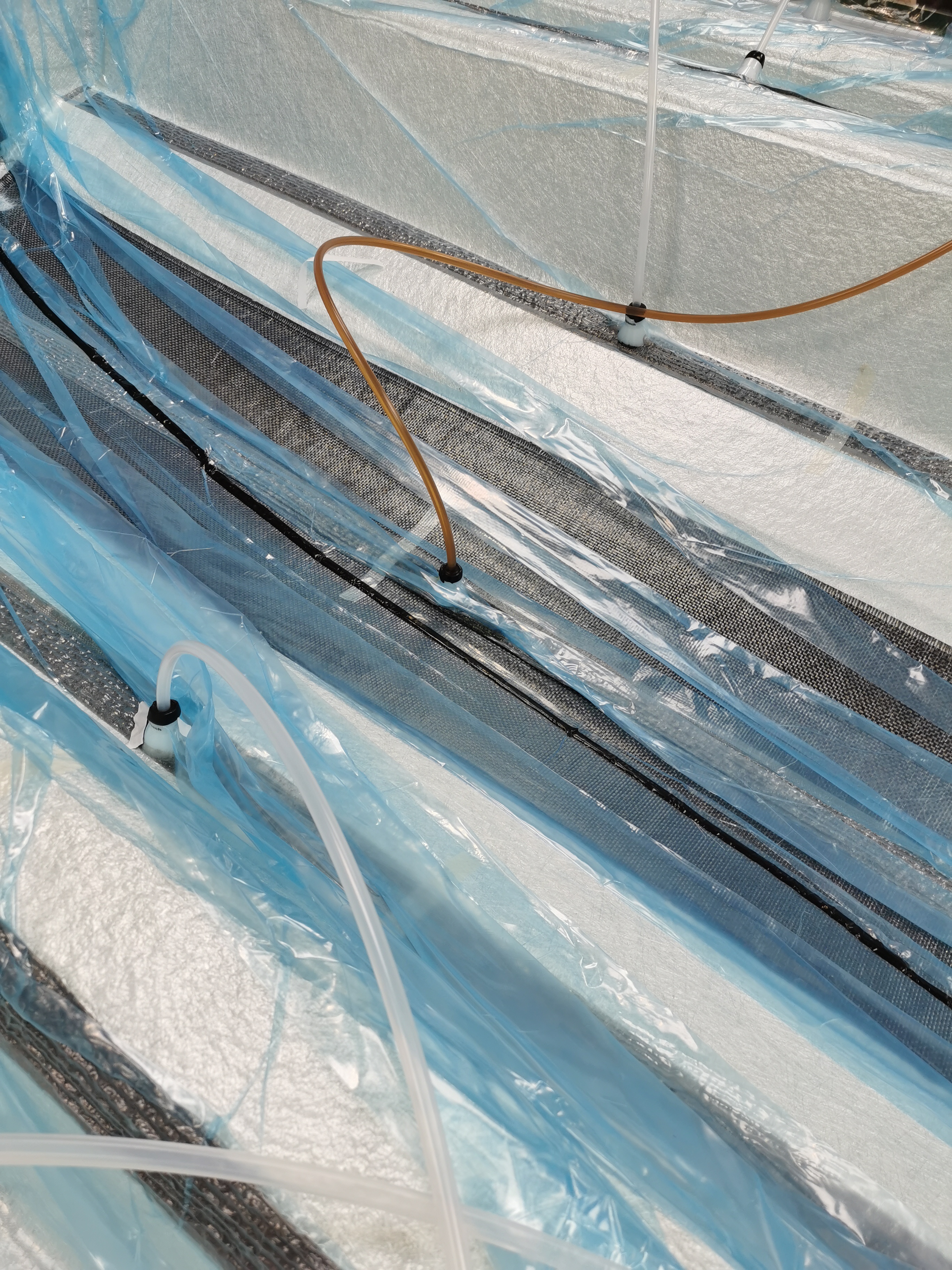

Zu den Verbundkomponenten des Bootes gehören Rumpf, Deck, Innenboden, Konsolen, Motorkasten und Luken. Die Beschaffung der Flachsfasern und des biobasierten Epoxids, die im ursprünglichen Design verwendet wurden, erwies sich jedoch bei den für die Serienproduktion der Boote erforderlichen Mengen als schwieriger als erwartet.
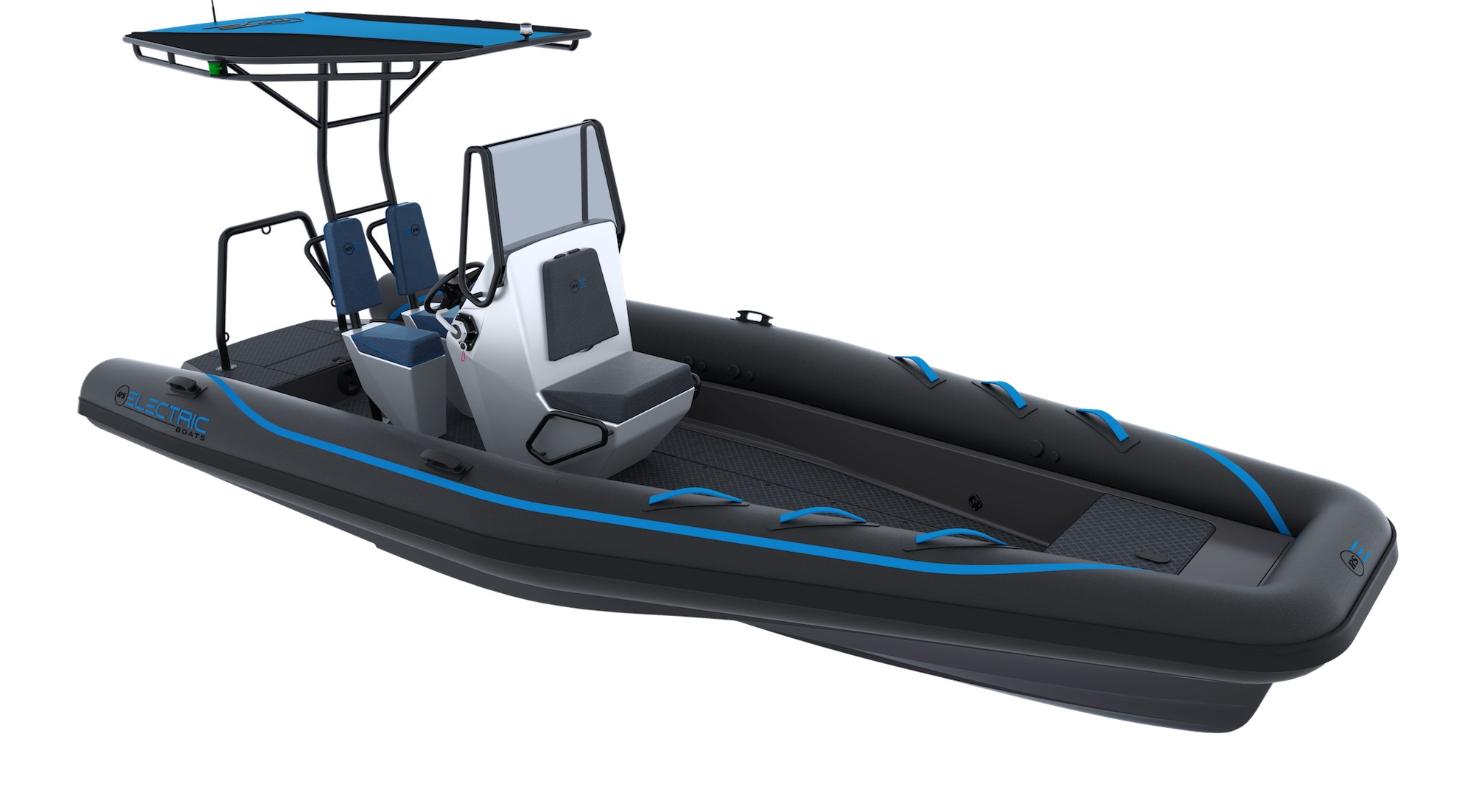
„Die Materialentscheidungen werden sich in den nächsten Jahren sicherlich ändern, da Naturfasern und biobasierte Harze immer zugänglicher werden“, sagt Newton-Southon. Derzeit kombiniert der monolithische Rumpf des Bootes mit Vinylester angereicherte Glas- und Kohlefasergewebe. Um das Gewicht zu reduzieren, wird der Rumpf nicht entkernt, sondern mit Kohlefaserschichten verstärkt. Alle anderen Verbundkomponenten des Bootes – Innendeck, Boden, Konsolen, Motorkasten und Luken – werden aus recycelten Kohlefasern und Vinylester mit recyceltem PET-Kern (geliefert von 3A Composites Core Materials, Sins, Schweiz) nach Bedarf hergestellt. „Der Rumpf besteht derzeit nicht aus recycelten Materialien, nur um uns etwas mehr Zeit für die Entwicklung und Tests zu geben“, bemerkt er.
Bei dem Harz hat sich RS Electric Boats aus mehreren Gründen für einen traditionelleren Vinylester gegenüber biobasiertem Epoxid entschieden. Einer davon war die Verfügbarkeit. Laut Newton-Southon verlief der Versuch, wirklich nachhaltige Harze – in kommerziellen Mengen – herzustellen, langsamer, als ihm lieb war. „Es geht nicht nur um die Preise“, sagt er, „sondern darum, langfristig an Produkte glauben zu können. Was passiert mit diesen Produkten in 10 Jahren? Hält das Material? Sie sind so neu, dass wir es noch nicht genau wissen. Es gibt eine Nachfrage und wir sind bereit, für nachhaltigere Materialien etwas mehr auszugeben, aber wir müssen uns auf die Lebensdauer des Produkts verlassen können.“
Das biobasierte Epoxid erwies sich auch bei der Harzinfusion als schwierig zu verwenden. „Wenn Sie Epoxidharz in einem Infusionsprozess verwenden, können Sie keine wiederverwendbaren Silikon-Vakuumbeutel verwenden“, erklärt Newton-Southon. Das Epoxid reagiert mit dem Silikon und Silikonbeutel, die für 100-150 Zyklen ausgelegt sind, halten möglicherweise nur fünf. „Am Ende fällt eine riesige Menge an Deponieabfällen aus dem Herstellungsprozess an“, sagt er. Vinylester wurde als beste Option für die Verwendung mit Silikonbeuteln ausgewählt.
Er fügt hinzu:„Wenn Sie derzeit eine Lebenszyklusanalyse der Materialien durchführen, sind wir der Meinung, dass die Reduzierung des Infusionsabfalls auf Deponien weitaus wichtiger ist als der Versuch, ein etwas nachhaltigeres Harz zu verwenden. Der Prozess ist so nachhaltig mit so wenig Abfall wie möglich.“
Tim King, technischer Vertriebs- und Marketingleiter und Projektmanager bei MTAG Composites, stellt fest:„Biobasierte Vinylester kommen auf den Markt, aber sie sind für Produkte dieser Größe noch nicht kommerziell rentabel. Sie werden nur in relativ kleinen Mengen hergestellt.“
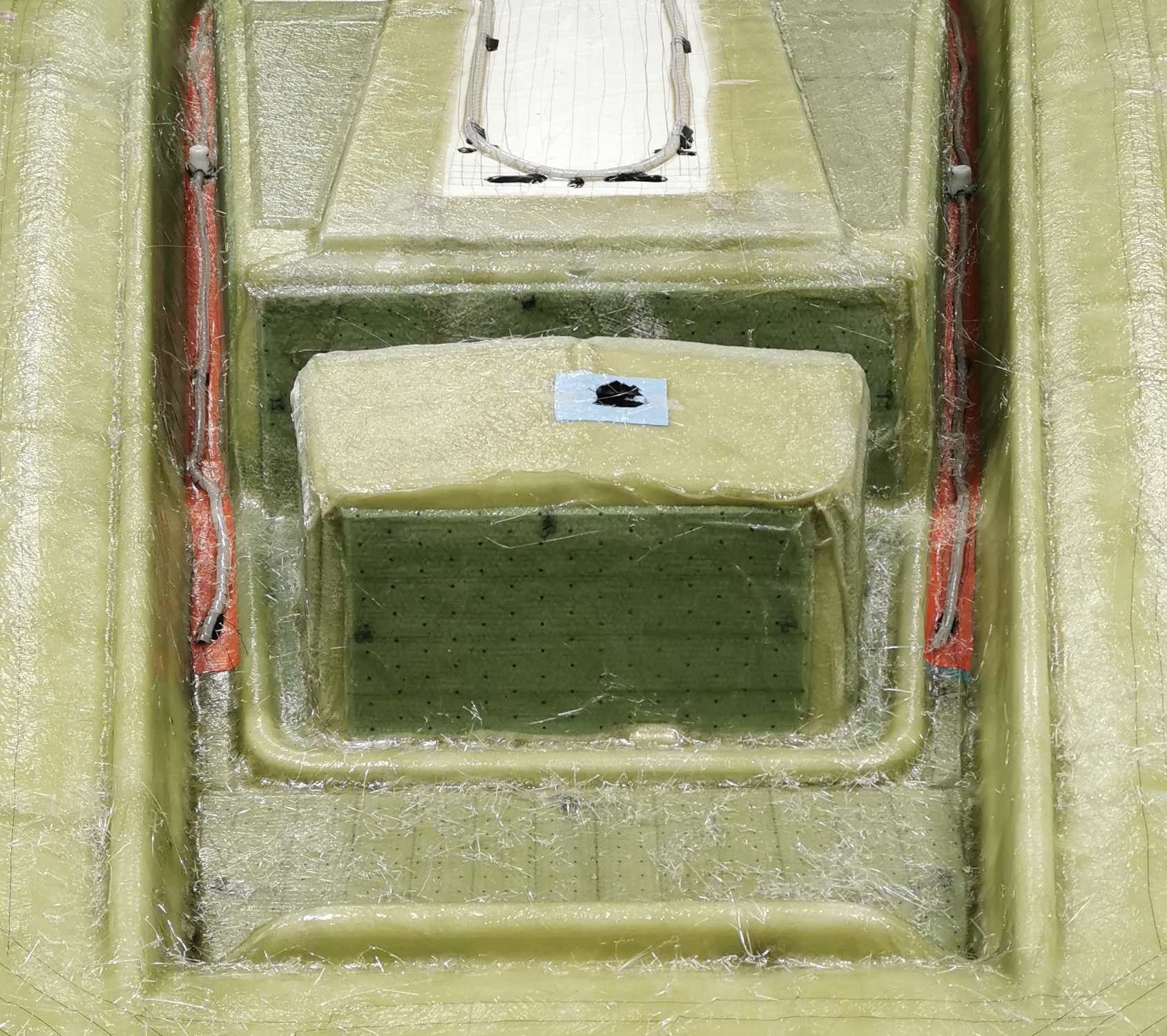
Für die Faser ist die recycelte Kohlefaser für die Boote wiederverwendeter Schrott aus der Arbeit von MTAG Composites an Kohlefaser-Flugzeugsitzen. „Es ist eine direkte Wiederverwendung, verarbeitet durch den Dritthersteller Gen 2 Carbon [ehemals ELG Carbon Fibre, Coseley, Großbritannien]“, sagt King.
Anstatt die Fasern zu zerkleinern oder zu einem Prepreg zu verarbeiten, infundiert MTAG direkt ein trockenes recyceltes Kohlefaservlies. „Dies ist bei der Dichte der recycelten Fasern besonders schwierig. Es mag nicht, mit Harz zu füllen, aber wir haben einen Prozess gefunden, um dies erfolgreich zu tun“, sagt King.
Das Verfahren wurde erstmals 2019 auf dem RS Neo Vorschiff demonstriert, wo MTAG Composites und RS Sailing die traditionelle Glasfaserverstärkung durch recycelte Kohlefasern ersetzten. „Dies gibt es schon seit einigen Jahren, aber ich weiß, dass wir bei MTAG und Gen 2 froh sind, dass dieses Produkt und dieser Prozess vorankommen“, sagt King.
Zum ästhetischen Erscheinungsbild der recycelten Faser fügt er hinzu:„Man kann es natürlich mit einem Gelcoat abdecken, aber für mich persönlich gefällt mir die Optik des recycelten Produkts sehr gut. Es ist schön zu sehen, dass dieses identifizierbare Quellmaterial wiederverwendet wird.“
Am Ende bestehen „rund 60 % der Verbundkomponenten des Bootes aus recycelten Materialien, entweder PET-Kern oder Kohlefaserabfällen“, sagt King. Alle Kompositteile werden unter Vakuum infundiert, mit Ausnahme einiger kleiner Zubehörteile, die von Hand mit trockenen Materialien verlegt werden.
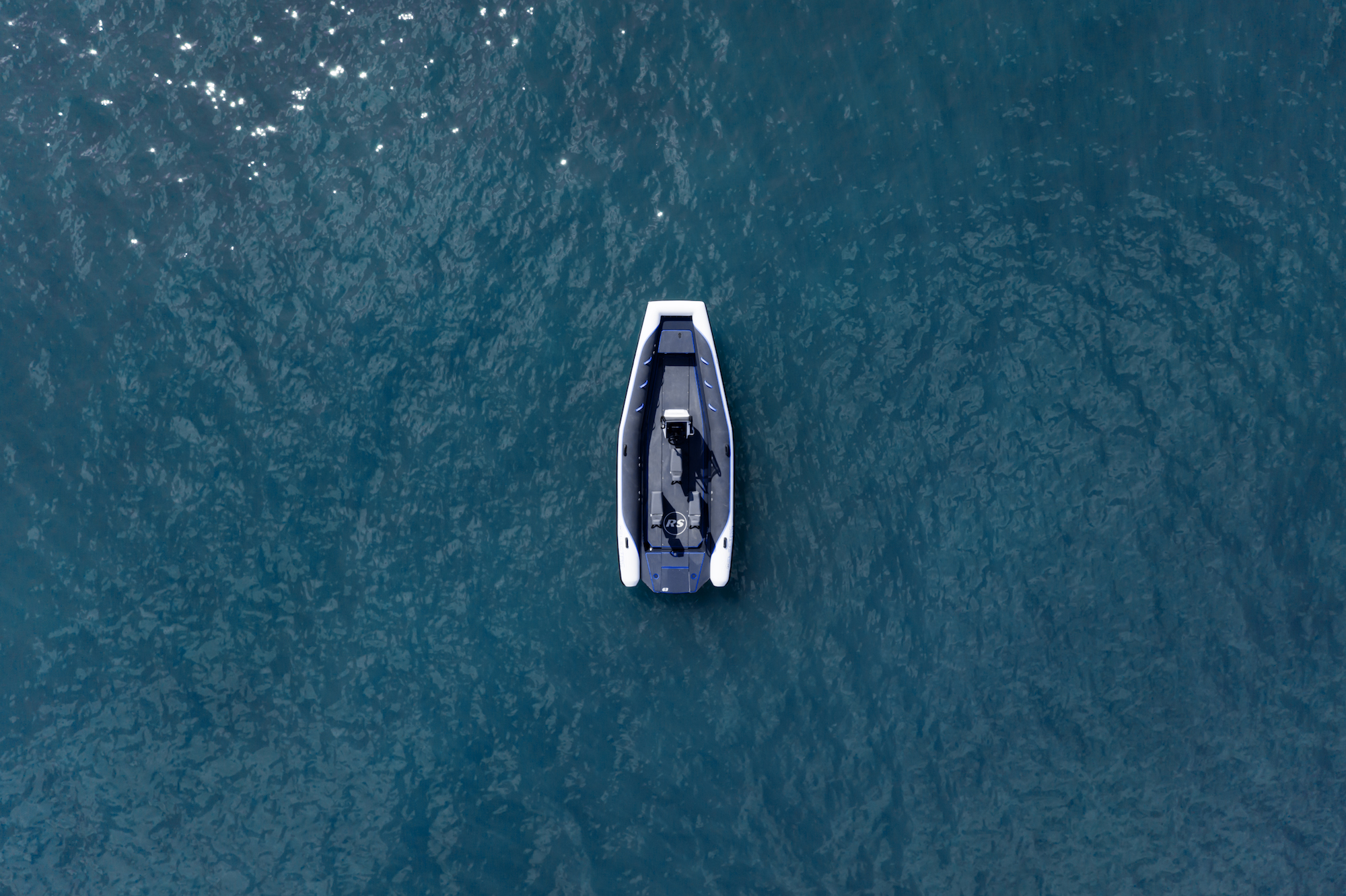
Segeln im Jahr 2022. Etwa 60 % der Komponenten des Pulse 63 werden laut Hersteller MTAG aus recycelten Materialien hergestellt. Bildnachweis:RS Sailing
Das Werkzeug für den Pulse 58 diente als Basis für den neuen Pulse 63 Werkzeuge, die MTAG Composites gemäß den Spezifikationen von RS Electric geändert hat. Alle Werkzeuge – insgesamt 22, bestehend aus vier festen Infusionswerkzeugen, sechs Werkzeugen für das Handlaminieren und 12 Werkzeugen mit Silikonbeutel – sind aus Verbundwerkstoffen und werden im eigenen Haus von Norco oder MTAG hergestellt. Um Designänderungen am Rumpf Rechnung zu tragen, mussten einige der Werkzeuge nachbearbeitet werden, und für einige wurden spezielle Einsätze hergestellt, um der Form wieder Form zu verleihen.
„Wir haben einen sehr aktiven Formenbau im Haus und einige sehr erfahrene Leute, die in der Lage waren, die ursprünglichen Prototypenwerkzeuge zu übernehmen und in einigen Fällen ziemlich drastische Änderungen daran vorzunehmen“, erklärt King. Das Team begann im Februar 2021 mit den Werkzeugen und die endgültigen Werkzeuge wurden im August geliefert.
Die ersten vier Puls 63 Boote sollen bis Ende des Jahres produziert werden und im Januar 2022 auf der Internationalen Bootsausstellung in Düsseldorf ausgestellt werden. Newton-Southon fügt hinzu, dass Verbundmaterialien für die Pulse 63 . verwendet werden und zukünftige RS Electric Boats-Modelle werden sich wahrscheinlich mit der Verfügbarkeit neuer Materialien und mit der Marktnachfrage ändern. „Wir gehen einen Schritt nach dem anderen vor, aber ich denke, eine Sache, in der wir ziemlich gut geworden sind, ist, der Lieferkette zu helfen, zu verstehen, welche Arten von Produkten der Markt braucht.“
Harz
- Die Vorteile von Kohlefaser in der Luft- und Raumfahrtindustrie
- Die Top 5 der Verwendung von Kohlefasern im Sport
- Kohlefasergeräte für Ihr Zuhause
- Die Vorteile einer Kohlefaserprothese
- Die Rolle von Kohlefasern in Luft- und Raumfahrtmaterialien
- Wie die Luft- und Raumfahrtindustrie Kohlefaser für ihre Bedürfnisse nutzt
- 5 Tipps zum Finden des besten Herstellers von Kohlefaserteilen
- Kohlenstofffaser-Innovationen in der Medizinindustrie
- Kann Kohlefaser recycelt werden?
- Innovative Anwendungen für Kohlefaser