Neue Technologie treibt das Wachstum des Roboterschweißens voran
Ist es der richtige Zeitpunkt, Ihren Schweißbetrieb zu automatisieren? Sind Sie besorgt darüber, wie lange Sie Ihre erfahrenen Schweißer behalten können? Müssen Sie Ihren Durchsatz erhöhen, sehen aber nicht, wie Sie das mit den verfügbaren Arbeitskräften tun sollen? Herausgefordert durch härtere Materialien? Eine Vielzahl von technischen Fortschritten macht es relativ einfach, diese Probleme zu lösen, indem Sie Ihren Schweißvorgang automatisieren und sich überraschend schnell amortisieren.
Dreimal schneller
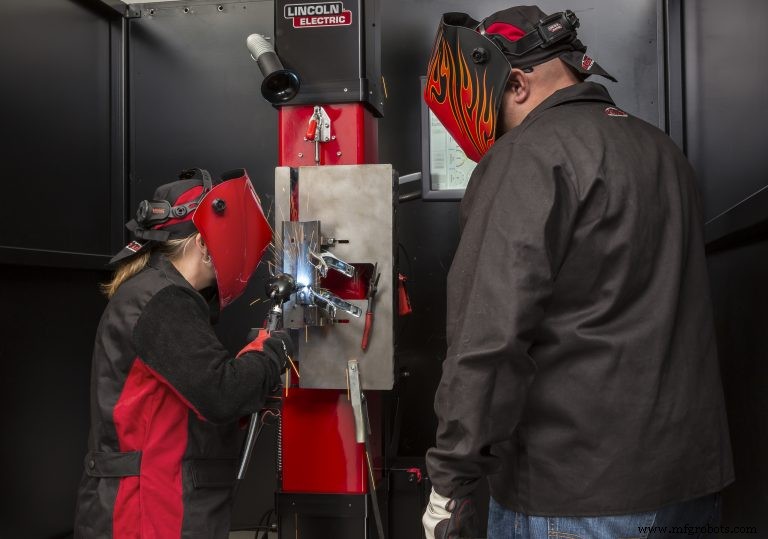
Es gibt zwei große Kategorien von automatisiertem Schweißen, sogenannte „feste“ Automatisierung und „flexibles“ (oder Roboter-) Schweißen. Feste Automatisierung ist oft anwendungsspezifisch und am besten, wenn die Teilegeometrie und die Schweißnaht sehr einfach sind. Zum Beispiel ist es im Allgemeinen die beste Lösung zum Schweißen von Rohren. Aber für die meisten industriellen Anwendungen und alles Komplexe ist das Roboterschweißen ideal und steht im Mittelpunkt dieses Artikels.
Wie Jason Lange, Manager Inside Sales, Lincoln Electric Co. (Cleveland), erklärte:„Der Hauptzweck eines Roboters besteht darin, bei der Wiederholbarkeit einer Schweißnaht zu helfen. Nummer zwei ist, den Missbrauch des Schweißers zu reduzieren. Den ganzen Tag Teile zu bewegen und unter verschiedene Vorrichtungen zu kriechen, ist für einen Menschen anstrengend. Roboter helfen der Ergonomie.“
Es ist doppelt wichtig, es den Schweißern zu erleichtern, weil sie immer schwerer zu finden sind. „Es gibt viele technische Schulen im ganzen Land, die in Schweißprogramme investieren, um zu versuchen, diese Lücke zu schließen“, fuhr Lange fort. „Aber an jedem Tag übersteigt die Zahl der Rentner die neu hinzukommenden Mitarbeiter, wodurch eine Lücke entsteht. Roboterschweißen hilft, diese Lücke zu füllen.“
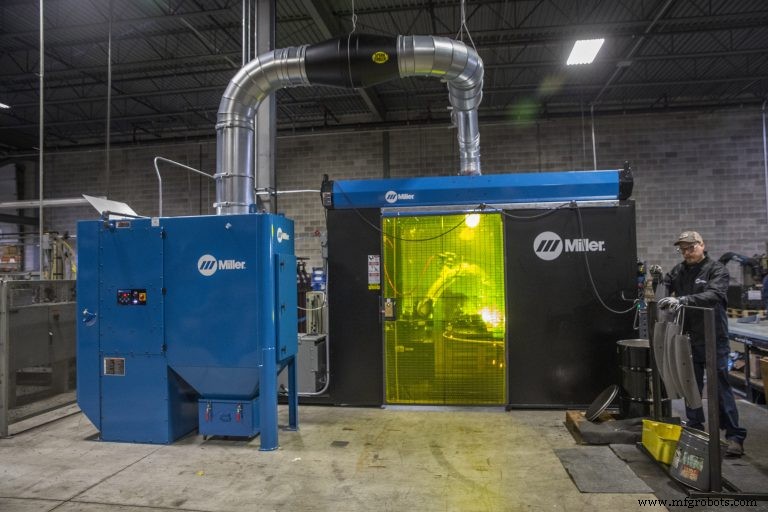
Gleichzeitig ist „die Amortisation eines Robotersystems in der Regel viel besser als Sie vielleicht denken“, erklärte Erik Miller, Business Development Manager – Laser Group bei Miller Electric Mfg. Co. (Appleton, WI). „Ein Robotersystem fertigt so viele Teile wie drei Schweißer. Sie sparen zwei Gehälter pro Schicht und die durchschnittlichen Kosten einer vorgefertigten Zelle betragen 100.000 bis 120.000 US-Dollar. Es amortisiert sich in etwa einem Jahr. Wenn Sie einen Prozess automatisieren und sich in weniger als einem Jahr amortisieren können, tun Sie dies normalerweise sofort. Wenn es zwei Jahre sind, sollten Sie ernsthaft darüber nachdenken.“
Roboterautomatisierung ist also eine große Hilfe bei der Steigerung des Durchsatzes. Die für diesen Artikel befragten Quellen betonten jedoch, dass dies kein Ersatz für qualifizierte Arbeitskräfte sei. „Sie brauchen immer noch einen guten Schweißer, um diesen Roboter zu betreiben“, wie Lange es ausdrückte.
Materialwechsel sind ein weiterer Grund für die Automatisierung
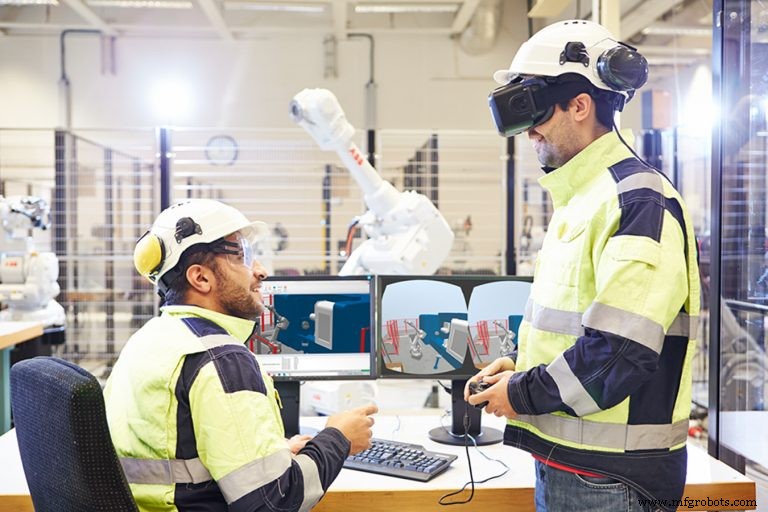
Änderungen bei den Arbeitsmaterialien in den letzten zehn Jahren haben zu Verbesserungen beim Schweißen geführt, von denen viele nicht manuell angewendet werden können, wie z. B. Laserschweißen, so Erwin DiMalanta, Director, Welding &Cutting Business Line, ABB Robotics (Auburn Hills, MI) . „Die Hersteller von Bergbaufahrzeugen bis hin zu Automobilen verwenden unterschiedliche Materialien, um Kosten und Gewicht zu reduzieren und unterschiedliche Antriebsstranglösungen unterzubringen“, sagte er. „Automobilhersteller haben auf mehr hochfeste und ultrahochfeste Stähle umgestellt, die metallurgische Eigenschaften haben, die sie stärker, leichter und korrosionsbeständiger machen, aber dennoch eine hohe Umformbarkeit und Schweißbarkeit aufweisen. Das verändert die Art und Weise, wie Metallstrukturen entworfen, geformt und montiert werden, drastisch.“ Während Hersteller herkömmliche Stanzwerkzeuge verwendet haben, um Merkmale in das Teil zu schneiden, verwenden sie jetzt Heißprägeverfahren und automatisierte Lasertechnologien, um die Teile zu formen und zu schneiden.
„Ein weiteres Beispiel ist die Umstellung auf Aluminium für mehr Anwendungen“, sagte DiMalanta. „Je nach Auto können mittlerweile bis zu 90 % der Karosserie aus Aluminium bestehen. Aufgrund der höheren Leitfähigkeit benötigt man zum Punktschweißen von Aluminium mehr Strom und Strom ist gleichbedeutend mit Wärme. Wir werden jedoch dünnere Materialien verwenden. Bei manchen Fahrzeugen sind die Materialien etwa 1 mm dick. Wie gehen Sie also mit diesen gegenläufigen Trends um?“
Die Antwort ist eine verbesserte Technologie sowohl für die elektronische als auch die mechanische Steuerung des Lichtbogenschweißens und der verstärkte Einsatz des Laserschweißens. Zum Lichtbogenschweißen sagte DiMalanta, dass „Stromquellen jetzt extrem fortschrittlich und elektronisch gesteuert sind. Die Abscheidung von Material in einem Schweißbad wird sorgfältig mit kundenspezifischen Wellenformen gesteuert.“ Miller fügte hinzu, dass solche speziellen Wellenformen „den Wärmeeintrag auf Teile kontrollieren, was Verformungen reduzieren und auch das kosmetische Erscheinungsbild von Schweißnähten verbessern kann.“
Er wies auch auf ein mechanisches Verfahren namens Active Wire von Panasonic hin. „Es handelt sich um einen bidirektionalen Drahtvorschub, bei dem der Draht vorwärts geführt wird, um den Kurzschluss zu erzeugen, und dann rückwärts aus der Pfütze herausgeführt wird, wobei dieser nähmaschinenartige Vorgang bei 120 Hertz wiederholt wird. Dies reduziert den Wärmeeintrag und reduziert auch Spritzer erheblich. Es verbessert auch die Konsistenz des Lichtbogenschlags bei jeder Schweißung. Es ist sehr beliebt beim Aluminiumschweißen und beim Schweißen von dünnen Blechen.“
Je leichter die Komponente, desto fortschrittlicher müssen die Materialien werden, um komplexe Strukturen zu ermöglichen und gleichzeitig die Festigkeit beizubehalten, sagte DiMalanta. „Roboter und ihre fortschrittlichen Softwaresysteme helfen dabei, die Prozesse zur Handhabung dieser Materialien mit dem Pfad des Roboters zu verbinden.“
Laserschweißen eine überzeugende Option
Mit seiner blitzschnellen Fähigkeit, eine Vielzahl von Materialien (einschließlich unterschiedlicher Materialien) zu schweißen, ist der Laser wahrscheinlich das Größte, was dem Schweißen seit Jahrzehnten passiert ist. Und wie Masoud Harooni, Senior Advanced Technology Engineer – Laser Welding bei Trumpf Inc. (Hoffman Estates, IL) es ausdrückt:„Die größte Neuigkeit beim Laserschweißen in den letzten Jahren ist der Rückgang der Laserpreise.“
„Laserschweißsysteme sind einfacher zu steuern“, so Harooni weiter. „Du wählst eine Leistung und eine Geschwindigkeit. Sobald es eingestellt ist, bearbeiten Sie das gesamte Teil mit wenig Spritzern. Beim Lichtbogenschweißen muss der Lichtbogen aufrechterhalten werden und die Schweißparameter reagieren empfindlich auf Änderungen des Abstands zwischen Brenner und Werkstück. Verschiedene Teile des [Werkstücks] benötigen mehr Strom oder weniger Strom, was zu einer geringeren Prozessstabilität führt. Auch wenn die Regelkreise moderner Lichtbogenschweißanlagen sehr gut sind, sind diese Anlagen nie wirklich perfekt eingestellt. Lasergeschweißte Bauteile erfordern deutlich weniger Nachbearbeitung als lichtbogengeschweißte Bauteile, die oft geschliffen werden müssen. Sie haben auch das Problem, mit Spritzern fertig zu werden und die Düse in Lichtbogenschweißsystemen reinigen zu müssen.“
Vielleicht noch wichtiger ist, dass Laserschweißen eine tiefere Schweißnaht ohne Hitzeschäden erzielen kann, selbst bei Materialien wie Aluminium und Magnesium, die beim Lichtbogenschweißen anfällig für Risse oder Porosität wären. Harooni erklärte, dies liege daran, dass Laser eine Leistungsdichte von 108 Watt pro Quadratzentimeter erreichen können. Dabei entsteht ein Schlüsselloch, ein tiefer Hohlraum, der durch Verdampfen des Metalls des Werkstücks entsteht. Wenn sich der Laserstrahl entlang des Teils bewegt, behält er dieses winzige Schlüsselloch bei, das von einem Schmelzbad umgeben ist, während das Material dahinter erstarrt.
„Sie erhalten eine starke, tiefe Schweißnaht ohne extreme Wärmezufuhr in das Teil“, sagte er. „Lichtbogenschweißen hat nicht die Leistungsdichte, daher besteht die einzige Möglichkeit, eine tiefere Schweißnaht zu erreichen, darin, die Wärmezufuhr zu erhöhen. Die mechanischen Eigenschaften von geschweißten Teilen mit geringerer Wärmeeinbringung und weniger Verzug sind viel besser als Teile mit höherer Wärmeeinbringung.“
Miller erklärte, dass „der anfängliche Einfluss des Laserschweißens aufgrund des hohen Volumens und der [technischen Vorteile] im Automobilschweißen lag. Blechhersteller sollten sich auch mit dem Laserschweißen befassen. Die wirklichen Vorteile liegen im Ersatz des Widerstandspunktschweißens, das für die Fertigung mittlerer bis kleinerer Stückzahlen eine Herausforderung darstellen kann. Die Befestigung kann schwierig sein, da sowohl die Ober- als auch die Unterseite des Teils zugänglich sein müssen, während beim Laserschweißen nur die Oberseite zugänglich ist, sodass es einfacher zu automatisieren ist. Sie können auch einen Roboter mit geringerer Nutzlast zum Laserschweißen verwenden, zusammen mit einer einfachen feststehenden Optik.“
Im Vergleich zu einem großen Nutzlastroboter mit einem starken Arm, der ein großes Werkzeug mit zwei Elektroden trägt, können Hersteller jetzt einen sichereren 8-kg-Roboter verwenden, einen Prozesskopf daran montieren und das Widerstandspunktschweißen relativ einfach automatisieren.
„Der andere Bereich in der Blechbearbeitung, in dem das Laserschweißen von Vorteil ist, ist die Kartonherstellung“, sagte er. „Außeneckschweißnähte, die ein kosmetisches Erscheinungsbild erfordern und die anschließend wenig bis gar keine Metallnachbearbeitung erfordern, sind ein Bereich, in dem wir großes Interesse festgestellt haben.“
Laut Miller bietet Laser eine gute Lösung für Teile mit eingeschränktem Zugang. Ein Laser benötigt für die Schweißnaht nur eine Sichtlinie, während der Roboter bei einer Lichtbogenschweißanwendung einen sperrigen Brenner in und um Teile herum bewegen muss, was sehr schwierig sein kann. „Beim Laserschweißen sind wir oft 500 mm vom Werkstück entfernt. Es ist, als würde man mit einer Strahlenkanone schießen. Laser hat auch viel höhere Bearbeitungsgeschwindigkeiten und einen geringeren Gesamtwärmeeintrag in das Teil, was den Verzug reduziert. Es ist ein perfektes Werkzeug für das autogene Schweißen.“
Der Nachteil des Laserschweißens, erklärte Harooni, sei, dass man „entweder sicherstellen muss, dass praktisch keine Lücken zwischen den Komponenten vorhanden sind, oder eine Schmelzlinie verwenden muss, die Laserschweißen mit Drahtunterstützung kombiniert, in der man den Draht so in das Bad einschmilzt kann die Lücke schließen. Aber das Laserschweißen ist so viel schneller, dass sich die zusätzliche Investition in die Vorrichtung lohnt. Wenn Sie zum Beispiel 50 Teile pro Tag mit Roboter-Lichtbogenschweißen herstellen, könnte Roboter-Laserschweißen 300, 500 oder sogar Tausende desselben Teils an einem Tag herstellen.“
Einstieg in die Schweißautomatisierung
Der Einstieg in die Schweißautomatisierung ist einfacher denn je. Erstens bieten die Hauptakteure eine Offline-Setup-Software an, die den nächsten Auftrag auf einem PC mit einem hohen Maß an Realismus programmiert, dieses Programm an den Roboter überträgt und die Schweißung startet. ABB verwendet sogar Virtual-Reality-Techniken, um Benutzern die „Zusammenarbeit“ mit Roboterschweißgeräten zu ermöglichen.
„Man kann den Roboter sozusagen buchstäblich am Hals packen und steuern wie einen Hund an der Leine“, erklärt DiMalanta. „Dies kann viel intuitiver sein als die Verwendung eines Programmierhandgeräts.“
Zweitens können diese Systeme über Mechanismen verfügen, die sich automatisch an Positionsänderungen von einem Teil zum nächsten anpassen und die Schweißqualität überwachen.
Wie David Schaefer, Produktspezialist bei Miller Electric, erklärte:„Es gibt mehrere Sensortypen, die sich mit Änderungen der Gelenkposition befassen. Das eine ist einfach die Berührungserkennung und das andere die Nahtverfolgung durch den Lichtbogen. Bei Verwendung der Berührungserkennung kann der Roboter herunterkommen und seinen Lichtbogenschweißdraht verwenden, um das Teil zu prüfen. Es überprüft das Delta zwischen dem programmierten Ort und dem tatsächlichen Ort, um sich im Grunde selbst neu zu programmieren.
„Bei der Nahtverfolgung durch den Lichtbogen, wenn Sie über eine Naht fahren, wie bei einer Kehlnaht oder einer Überlappnaht, wenn das Material dick genug ist, erkennt es die Änderung der Stromstärke und bestimmt, wann es in der Naht ist und wann nicht die Verbindung und folgt dann dieser Schweißnaht, während sie schweißt“, fuhr Schaefer fort. „Sie haben auch die Möglichkeit, Laseroptiken anstelle von Drahtsensoren zu verwenden, aber es ist die gleiche Grundidee.“
Lange von Lincoln Electric sagte:„Ein anderer Weg, dies zu tun, ist eine Kamera, die entweder ein 2D- oder 3D-Bild des Teils aufnimmt. Wir können Programme und Verbindungen basierend auf der physischen Position der Teile versetzen. Neuere Kameras sind nicht so stark von Blendung betroffen wie Kameras noch vor ein paar Jahren. Sie können mehr Farben sehen und die Definitionen eines Teils lesen, indem sie Schatten und Reflexionen von dem Teil unterscheiden.“ Harooni fügte hinzu, dass „die heutige Optik uns auch die Möglichkeit gibt, die Qualität der Schweißnaht in Echtzeit zu überprüfen, ohne dass eine zerstörende Prüfung erforderlich ist.“
Drittens bieten die Roboter alle eine Form der Kollisionserkennung. Miller von Miller Electric sagte, dies sei die bedeutendste Verbesserung des Roboterarms selbst. „Früher erstellte ein Kunde sein Programm basierend auf der bekannten X-Y-Z-Position des Brenners. Nehmen wir an, der Roboter hat die halbe Schicht geschweißt und der Bediener lässt eine Klammer offen. Der Roboter würde wahrscheinlich gegen die Klemme schlagen und die Fackel verbiegen. Das würde dazu führen, dass jede Schweißnaht in diesem Programm falsch ausgerichtet wäre, da das Ende des Brenners gebogen wurde und sich diese Position geändert hat. Wenn der Roboter heute selbst bei hoher Geschwindigkeit auf ein Objekt trifft, liest er die resultierende Stromspitze als Hindernis. Dadurch wechselt der Roboter sofort in den Flex-Servo-Modus, der die Anwendung der Bremse um eine bestimmte Strecke verzögert, die für jede Achse festgelegt wird. Der Roboter wird praktisch „schlaff“. Dadurch kann der Roboter den Impuls abbauen und Schäden am Werkzeug minimieren. Das bedeutet, dass Sie eine Hochgeschwindigkeitskollision haben können, ohne die Fackel zu verbiegen.“
Viertens bieten alle großen Player vorgefertigte Roboterzellen mit allem, was Sie brauchen, auf einer Palette (oder mehreren). „Eine Arbeitszelle wäre eine vollständig konstruierte Einheit mit allen vorhandenen Sicherheitsvorkehrungen“, sagte Lange. „Normalerweise sieht man Zäune oder Stahlwände, normalerweise Sicherheitsscanner, Lichter, Druckknöpfe, um den Roboter in Gang zu setzen, Schlüsselverriegelungen und eine Art Positionierungsvorrichtung vor dem Roboter, wie z. B. eine Drehscheibe oder ein Riesenrad. Diese Vorrichtungen bringen das Teil in die Arbeitszone, während der Bediener auf der gegenüberliegenden Seite weitere Teile lädt. Oder Sie könnten nur einen festen Tisch haben, an dem der Roboter verarbeiten wird. Es würde auch eine Schweißstromquelle, den Brenner und einige Reibahlen geben, um die Bits bei Bedarf zu reinigen. Sie müssen es nur an Strom und eine Gasquelle anschließen.“ Und wenn eine der Standardlösungen nicht funktioniert, sind kundenspezifische Komplettlösungen verfügbar.
Also, worüber muss man sich Sorgen machen?
„Wenn wir uns mit einem potenziellen Kunden über Schweißautomatisierung beraten, schauen wir uns seine vorgelagerte Fertigung an“, erklärt Schaefer von Miller Electric. „Wenn sie Laser und CNC-Ausrüstung verwenden, um das Material zu biegen, zu brechen und zu schneiden, werden sie viel erfolgreicher beim Roboterschweißen sein, als wenn sie es von Hand schneiden oder eine Kappsäge verwenden würden. Diese Werkstätten kommen jetzt damit durch, denn wenn sie die Teile von Hand schweißen, können sich die Schweißer entsprechend anpassen, der Roboter jedoch nicht.“ Miller fügte hinzu, dass das Schweißen normalerweise das Letzte ist, was in einer Anlage automatisiert wird, da vorgelagerte Prozesse zuerst genau sein müssen. „Teile müssen genau geschnitten und dann genau gebogen werden. Dann kannst du sie schweißen“, sagte er.
Neben der Sicherstellung, dass Teile wiederholbar sind, ist eine Vorrichtung erforderlich, die die Lücken begrenzt oder beseitigt, wie Schaefer erklärte:„Man kann keine Luft schweißen. Ein menschlicher Bediener kann eine Lücke sehen und entsprechend reagieren, im Allgemeinen durch Erhöhen des Drahtvorstands, um die Stromstärke zu verringern, was die Wärme und das Eindringen verringert, und dann mit dem Weben beginnen, um die Lücke zu füllen. Ein Roboter wird dies nicht tun. Es wird durchbrennen.“
Umgekehrt, sagte Lange, haben einige Kunden in einigen Fällen Tausende oder Hunderttausende von Dollar für Werkzeuge zum Halten von Teilen ausgegeben, obwohl sie diesen Preis durch die Verbesserung vorgelagerter Prozesse halbieren konnten. Dadurch wird die erforderliche Wiederholbarkeit nachgeschaltet, was letztendlich die Werkzeugkosten senkt und die Menge an Nacharbeit und Ausschuss verringert.
Nach der Teilequalität und Wiederholbarkeit ist das zweitwichtigste Anliegen „den Schweißprozess in seiner Gesamtheit zu kennen und zu verstehen schweißt sich selbst und schweißt durch das automatisierte Gerät“, sagte Lange.
Wen sollten Sie also schulen, um das automatisierte Schweißen durchzuführen? Entweder ein erfahrener Schweißer oder jemand, der das Schweißen (was Wochen dauert) und die Schweißautomatisierung erlernen möchte.
Schaefer warnte:„Sie brauchen die richtige Kultur in der Anlage. Menschen mit Jobs können sich bedroht fühlen, wenn die Automatisierung in die Einrichtung kommt. Ich würde mit meinen Leuten sehr offen über die Vorteile sprechen, wie es das Unternehmen effizienter macht, ihm hilft zu wachsen und wettbewerbsfähiger zu sein und letztendlich mehr Leute einzustellen.“
Schließlich müssen die Losgrößen groß genug für die Automatisierung sein. Wie Lange es ausdrückte:„Die Zeit, die für die Offline-Programmierung, das Einsetzen des Roboters und das schnelle Einrichten benötigt wird, zahlt sich definitiv aus, wenn Ihre Losgrößen ungefähr einen Tag oder anderthalb Tage laufen. Wenn Sie stündlich ein Teil wechseln, ist Ihr ROI möglicherweise nicht ganz so effektiv.“
Automatisierungssteuerung System
- Neue drahtlose Technologie 2015
- Neue Technologie im Fokus der NPE2018:Die Revolution von „4.0“
- Neues Healthcare Technology Center von Hahn Automation
- Robotische Automatisierungssysteme machen Spatenstich für neue Anlage
- 4 Möglichkeiten zur Verbesserung der Roboterschweißleistung
- Die Schüler bauen ein Roboter-Müllsortiersystem mit B&R-Technologie
- Acieta bringt neue Roboter-Maschinenladezelle auf den Markt
- Robotiq bringt neue robotergestützte Bin-Picking-Lösung auf den Markt
- AMRC treibt Innovationen in Technologie und Kreislaufwirtschaft voran
- Robotischer Durchbruch des Manufacturing Technology Centre