Kohlefaser/Epoxid für die Massenreduzierung im Automobilbau, Massenproduktion
IACMI-Projekt 3.2 bewertete kohlenstofffaserverstärkte Verbundwerkstoffe, die mit einem neuartigen Harzsystem auf Epoxidbasis angereichert sind, um strukturelle Verbundteile mit komplexer Geometrie zu entwickeln, um Metalle in hochbelasteten, sicherheitskritischen Anwendungen an Primärkarosseriestrukturen von Passagieren mit hohem Passagieraufkommen zu ersetzen Fahrzeuge. Eine der ersten evaluierten Anwendungen war der Einsatz eines Kohlefaser/Epoxid-Prepregs an der B-Säule eines Testfahrzeugs. Das Hochleistungs-Prepreg-Material reduzierte die Masse direkt um 3 Kilogramm und ermöglichte eine Verkleinerung des umgebenden Blechs, das dann in kostengünstigeren Legierungen spezifiziert werden konnte, was zusätzliche Gewichts- und Kosteneinsparungen ermöglichte. Quelle | Ford Motor Co.
Automobilhersteller in den meisten Regionen stehen vor anspruchsvollen Vorgaben für 2025 zur Reduzierung der Auspuffemissionen und/oder zur Verbesserung des Kraftstoffverbrauchs für Personenkraftwagen. Die Entwicklung grundlegend neuer Automobiltechnologien zur Erfüllung dieser Anforderungen ist jedoch kostspielig. Daher werden in vielen Ländern Konsortien eingesetzt, die es den Mitgliedern der Lieferkette ermöglichen, die Kosten für die vorwettbewerbliche Forschung zu teilen.
In den USA ist eine solche Organisation das Institute for Advanced Composites Manufacturing Innovation (IACMI – The Composites Institute, Knoxville, Tennessee, USA). Unter den Initiativen der Organisation arbeiten IACMI-Mitglieder aus Industrie, Wissenschaft und Regierung an mehrgleisigen Projekten – einschließlich integrierter Material-/Prozessentwicklung, Modellierung/Simulation, Verbindung mehrerer Materialien und Recycling – um technische Probleme zu lösen, Fahrzeugmasse zu verbessern, Energie zu reduzieren Verbrauch und Emissionen und schaffen neue US-Arbeitsplätze.
Projekt 3.2 und das unmögliche Harzsystem
Projekt 3.2 war eines der ersten Projekte, das IACMI bei seiner Gründung im Juni 2015 annahm, obwohl die im Projekt verwendete Technologie einige Jahre vor der Gründung von IACMI in Zusammenarbeit zwischen Ford Motor Co. (Dearborn, Michigan) mit der Entwicklung begonnen hatte. , USA) und was damals Dow Automotive war (jetzt The Dow Chemical Co., Midland, Michigan, USA). Als IACMI gegründet und Projekt 3.2 gestartet wurde, brachten Ford und Dow ihre früheren Arbeiten an einem neuartigen Epoxidharzsystem in das Programm ein. Nach dem Zusammenschluss mit IACMI wurde das Programm erweitert, um schließlich mehrere Phasen zu umfassen, die neue Verwendungen für dieses innovative Harz darstellen:eine Prepreg-B-Säule, einen All-Sheet-Moulding-Compound (SMC)-Kofferraumdeckel und eine SMC/Aluminium-Heckklappe.
Die von Dow für Ford entwickelte Harzfamilie namens VORAFUSE ist für den Einsatz in Prepreg und SMC sowie für die Verarbeitung auf Formpressanlagen ausgelegt, die in der nordamerikanischen Automobilindustrie weit verbreitet sind. Gemäß den Anforderungen von Ford beträgt die Glasübergangstemperatur des Harzes (Tg ) hat eine Temperatur von 150-160 °C, formt sich bei 145-155°C und härtet in weniger als 2 Minuten bei 150 °C aus (obwohl eine Aushärtung unter 1 Minute möglich ist), wodurch es schnell genug für große Mengen ( 100.000-plus/Jahr) Fahrzeugproduktion. Es erreicht Nachhärtungen von mehr als 95 %. Das System ist frei von Lösungsmittel- und flüchtigen organischen Verbindungen (VOC).
„Die von Ford definierten CTQs [Critical-to-Quality-Anforderungen] sind einzigartig und wurden noch nie zuvor in einem einzigen kommerziellen Produkt erreicht“, erklärt Dave Bank, Fellow, Dow Polyurethanes R&D. „Aus diesem Grund waren eine neue Chemie und eine Vielzahl von sehr ungewöhnlichen Produkten erforderlich, um diese anspruchsvollen Spezifikationen zu erfüllen.“
„Die thermodynamische Trennung von Lagerstabilität und Polymerisation in der Harz/Härter-Mischung ergibt eine trockene Paste, die ohne fortschreitende Härtung in Kohlefasern infundiert werden kann und eine trockene, nicht klebrige Formmasse ergibt“, fügt Bank hinzu. „Aber wenn die Spritzgussbedingungen 150°C erreichen, ist die Chemie ‚heiß‘ und die Aushärtung schreitet schnell voran.“ Dow hat 21 Patentanmeldungen eingereicht und bisher vier für die Technologie erhalten.
Zusätzliche Funktionen des VORAFUSE-Systems:
- Es ist bei Raumtemperatur über 50 Tage lagerstabil, bietet jedoch eine Schnapphärtung bei oder über 150°C. Es erfordert keine Gefrierlagerung vor dem Schneiden und Formen des Kits, solange die Lagertemperatur 40°C nicht überschreitet.
- Seine klebfreie Chemie ist ideal für die automatisierte Handhabung. Da ihm die Klebrigkeit von herkömmlichem Prepreg fehlt, verursacht es keine Ablagerungen und damit verbundene Probleme mit Robotern und anderen automatisierten Handhabungsgeräten.
- Es enthält ein neuartiges internes Formtrennmittel (IMR), sodass Verarbeiter 1.000 Teile formen können, bevor sie externe Formtrennmittel auf die Werkzeugoberflächen auftragen müssen. Epoxy steht normalerweise im Gegensatz zu IMR, da es ein so effektiver Klebstoff für Metalle ist.
- Unausgehärtetes Produkt kann zu hochwertigen Teilen recycelt werden, indem das Material zerkleinert und als diskontinuierliche faserverstärkte Mischung in Formsysteme zurückgeführt wird, die sich ideal zum Formen komplexer Geometrien wie Rippen/Vorsprünge eignet. Im Gegensatz zu herkömmlichem Epoxid-Prepreg und SMC kann der gesamte nicht ausgehärtete Schrott wiederverwendet werden, wodurch das Material nachhaltiger wird und Schrottverluste vermieden werden, die die Teilekosten erhöhen.
Phase 1:Prepreg-B-Säule
Nachdem VORAFUSE in Projekt 3.2 aufgenommen wurde, begann IACMI mit der Arbeit an einer Automobilanwendung, die Phase 1 des Gesamtprojekts werden sollte. Zu den Teammitgliedern gehörten Ford, Dow, DowAksa US LLC (der in Tucson, Az., US-amerikanische Zweig von DowAksa BV, einem 50/50-Joint Venture zwischen Dow Chemical und Aksa Akrilik Kimya Sanayii A.Ş., Çiftlikköy-Yalova, Türkei); Michigan State University (East Lansing, Michigan, USA); Purdue University (West Lafayette, Ind., USA); Universität von Tennessee-Knoxville (Knoxville, Tennessee, USA); Continental Structural Plastics (CSP, Auburn Hills, Michigan, USA); und Oak Ridge National Laboratory (Oak Ridge, Tennessee, USA).
In der ersten Phase entwickelten die Forscher ein kontinuierliches (geflochtenes und nicht gekräuseltes) kohlenstofffaserverstärktes Prepreg, das mit dem Epoxid imprägniert ist. VORAFUSE P6300 Harz wurde für die Kompatibilität mit DowAksa A42 D012 24K Standardmodul-Kohlenstofffasern formuliert. Das Ziel des Teams war es, das Kohlefaser/Epoxid-Prepreg zu verwenden, um strukturelle Verbundteile mit komplexer Geometrie zu entwickeln, um gestanztes Metall in hochbelasteten, sicherheitskritischen Anwendungen an Primärkarosseriestrukturen von Großserienfahrzeugen zu ersetzen.
Für den Technologiedemonstrator die B-Säule auf einer Seite eines Ford Fusion Testfahrzeug verwendet wurde. Die Realisierbarkeit wurde zunächst durch Simulation bewertet, und dann wurden physische Teile geformt und allen erforderlichen Tests unterzogen – einschließlich Fahrzeugcrashs in Originalgröße. Teile mit Bravour bestanden, wodurch die Masse im Vergleich zu etablierten Metallen um 3 Kilogramm pro Seite reduziert wurde. Unausgehärteter Schrott wurde recycelt, um die komplexen Rippenstrukturen der Säule zu bilden. Der Hochleistungsverbundstoff ermöglichte eine Verkleinerung des umgebenden Blechs, das dann in kostengünstigeren Legierungen spezifiziert werden könnte, was zusätzliche Gewichts- und Kosteneinsparungen bietet.
Nachdem alle Anforderungen von Ford erfüllt wurden, war die erste kommerzielle Verwendung des Materials für einen vorderen Dachkopf und eine vordere Bodenabschlussplatte am kohlenstoffintensiven Ford GT Supersportwagen.
Es überrascht nicht, dass das Kohlefaser-/Epoxid-Prepreg einen Kostenaufschlag mit sich bringt und daher am besten für Fahrzeuge mit erheblichen Massenreduzierungsanforderungen geeignet ist, die für erhebliche Gewichtseinsparungen einen Aufpreis zahlen können.
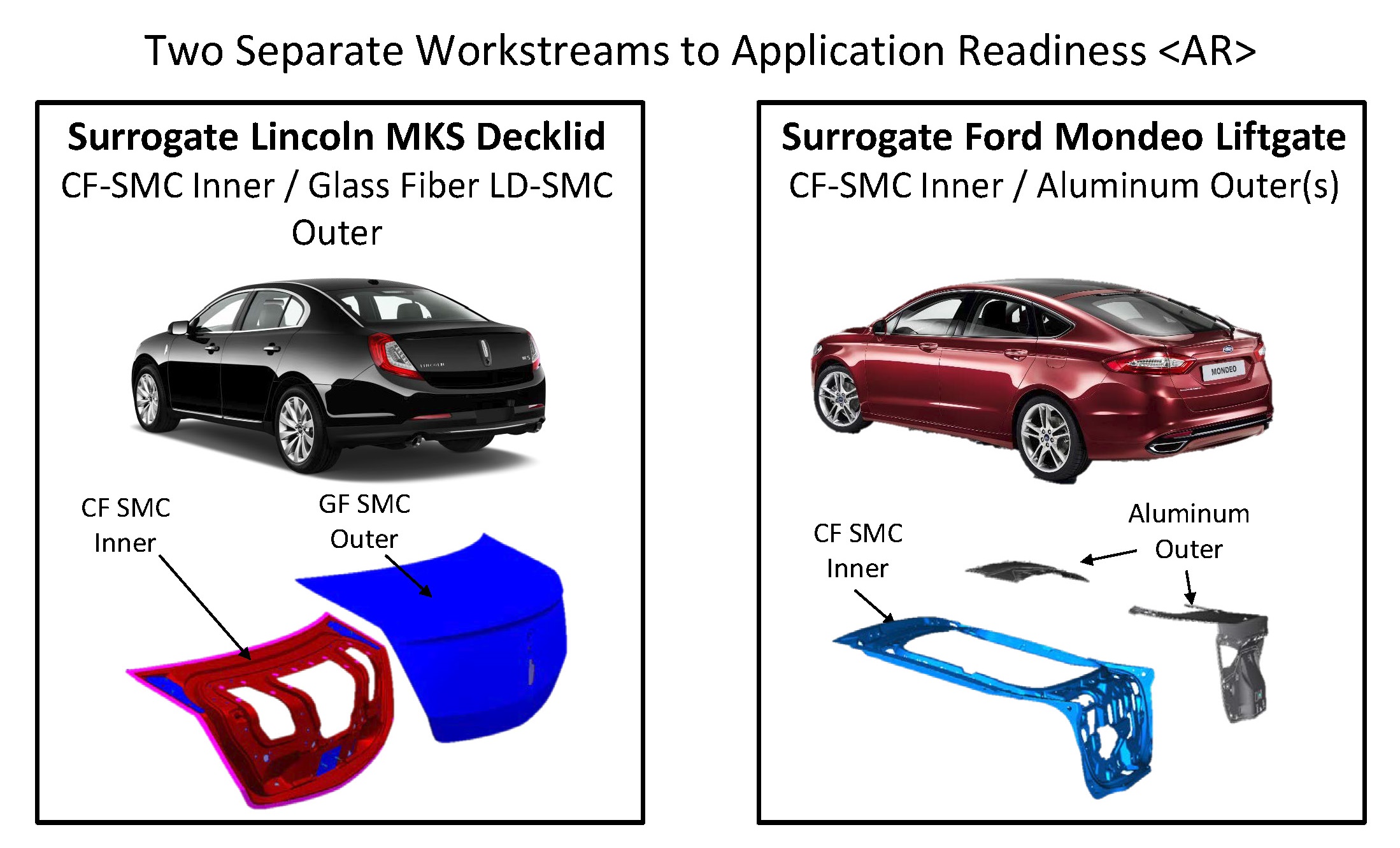
Phase 2/Workstream 1:Komplett-SMC-Deckdeckel
Aufbauend auf den Prepreg-Erfolgen untersuchten die Projektforscher als nächstes diskontinuierliche kohlenstofffaserverstärkte SMC mit dem neuartigen Epoxidharz in komplexen 3D-Strukturen mit sicherheitskritischen Funktionen. In einem Demonstrator wurde die Kohlefaser/Epoxid-SMC als Innen-/Strukturplatte eines geklebten Kofferraumdeckels (Kofferraumdeckel) verwendet und in einem anderen Demonstrator wurde sie für die Innen-/Strukturplatte einer viel größeren und komplexeren geklebten Heckklappe verwendet ( Heckklappe/Tür mit Fensterscheibe, Wischermotoren, Beleuchtung usw.). In beiden Arbeitsabläufen wurden die ursprünglichen Konstruktionsbeschränkungen, Hardware, Verbindungstechniken und Strukturklebstoffe unverändert gelassen. Anspruchsvolle mechanische Ziele von mehr als 300 MPa Zugfestigkeit und mehr als 40 GPa Zugsteifigkeit – vergleichbar mit etablierten Magnesium- und Aluminiumguss – wurden verwendet. SMC benötigte auch einen höheren Durchfluss als Prepreg, daher wurde eine etwas andere Qualität, VORAFUSE M6400, entwickelt.
Für den Kofferraumdeckel-Demonstrator, der einen inkrementellen Fortschritt gegenüber der aktuellen Glas-/SMC-Technologie darstellte, ersetzte das Kohlefaser-/Epoxid-SMC herkömmliches strukturelles glasfaserverstärktes ungesättigtes Polyester-SMC für eine Kofferraumdeckelinnenseite auf einem Lincoln MKS Prototypenfahrzeug. Die Kohlefaser/Epoxid-SMC-Innenplatte wurde an eine Glasfaser-/Polyester-SMC-Außenplatte niedriger Dichte (LD, 1,25 SG) geklebt, die eine Glasfaser-/Polyester-SMC-Einzelplatte mit Standarddichte (1,9 SG) ersetzte. Sowohl alte als auch neue Außenplattenmaterialien waren Klasse-A-kompatibel. Das Originalwerkzeug wurde wiederverwendet, um sowohl die Kohlefaser/Epoxid-SMC-Innenplatten als auch die Glasfaser-/Polyester-Außenplatten zu formen. Die Schrumpfung – obwohl sie zwischen beiden Harzsystemen leicht unterschiedlich war – war nahe genug, um keine Pass- und Oberflächenprobleme zu verursachen (mit anderen Worten, es wurden keine signifikanten Dimensionsänderungen beobachtet).
Beim virtuellen Prototyping wurde die geklebte Baugruppe einer Reihe von anspruchsvollen Lastfällen ausgesetzt, darunter Torsionssteifigkeit, vordere Eckensteifigkeit, Wasserfalldurchbiegung und Verriegelungslasten. Dutzende von Innen- und Außenblechen wurden als nächstes geformt, verklebt und getestet – einschließlich anspruchsvoller Heckaufpralle mit 89 Kilometern pro Stunde. Baugruppen haben sowohl virtuelle als auch physische Tests ohne Probleme bestanden.
Die Masse des Kofferraumdeckels wurde gegenüber dem Benchmark um 30 % (von 10,5 auf 7,33 kg) reduziert. Hätten die Budgets jedoch ein Umrüsten der Innenplatte ermöglicht – die aufgrund ihrer höheren mechanischen Leistung im Vergleich zum etablierten Hersteller hätte dünner ausgelegt werden können – dann berechnen die Forscher, dass die Masse mit 2-Millimeter-Wänden um mindestens 35 % und sogar noch weiter hätte reduziert werden können mit 1,5-Millimeter-Wänden.
Das Kohlefaser/Epoxid-SMC hat alle Ford-Anforderungen erfüllt und kann jetzt auf kommerziellen Plattformen verwendet werden, obwohl die Kosten höher wären als bei herkömmlichen Glasfaser/Polyester-SMC.
Phase 2/Workstream 2:SMC/Aluminium-Heckklappe
Für das letzte Projekt wandten sich die Forscher einem wirklich herausfordernden Szenario zu:Ersetzen von Leichtmetall durch Kohlefaser/Epoxid-SMC, um eine hybride (Metall/Verbund) geklebte Baugruppe für größere und komplexere Heckklappen von Ford Mondeo herzustellen Fünftürer/Fließheck-Testfahrzeuge. Um Änderungen an den Abläufen beim Fahrzeugbau zu minimieren, haben die Forscher die Baugruppe so konzipiert, dass sie vor der elektrophoretischen Rostbeschichtung (E-Coating) und den damit verbundenen Lack-Einbrennzyklen der Karosserie (BIW) hinzugefügt wird.
Kohlefaser/Epoxid-SMC ersetzte Magnesium für strukturelle/innere Paneele, die mit etablierten Aluminium-Außenpaneelen verklebt wurden. Da für die Herstellung der Verbundplatte neue Werkzeuge erstellt werden mussten, wurde das Teil neu konstruiert. Die Plattendicke wurde entsprechend den Steifigkeits-/Festigkeitsanforderungen und um eine Verrippung hinzuzufügen variiert. Außerdem wurden in hochbelasteten Befestigungsbereichen für Gasdruckfedern, Riegel, Scharniere und Schlösser metallische Verstärkungen verwendet, die die Verbundplatte etwas dicker machten – etwas, das der Bauraum zuließ.
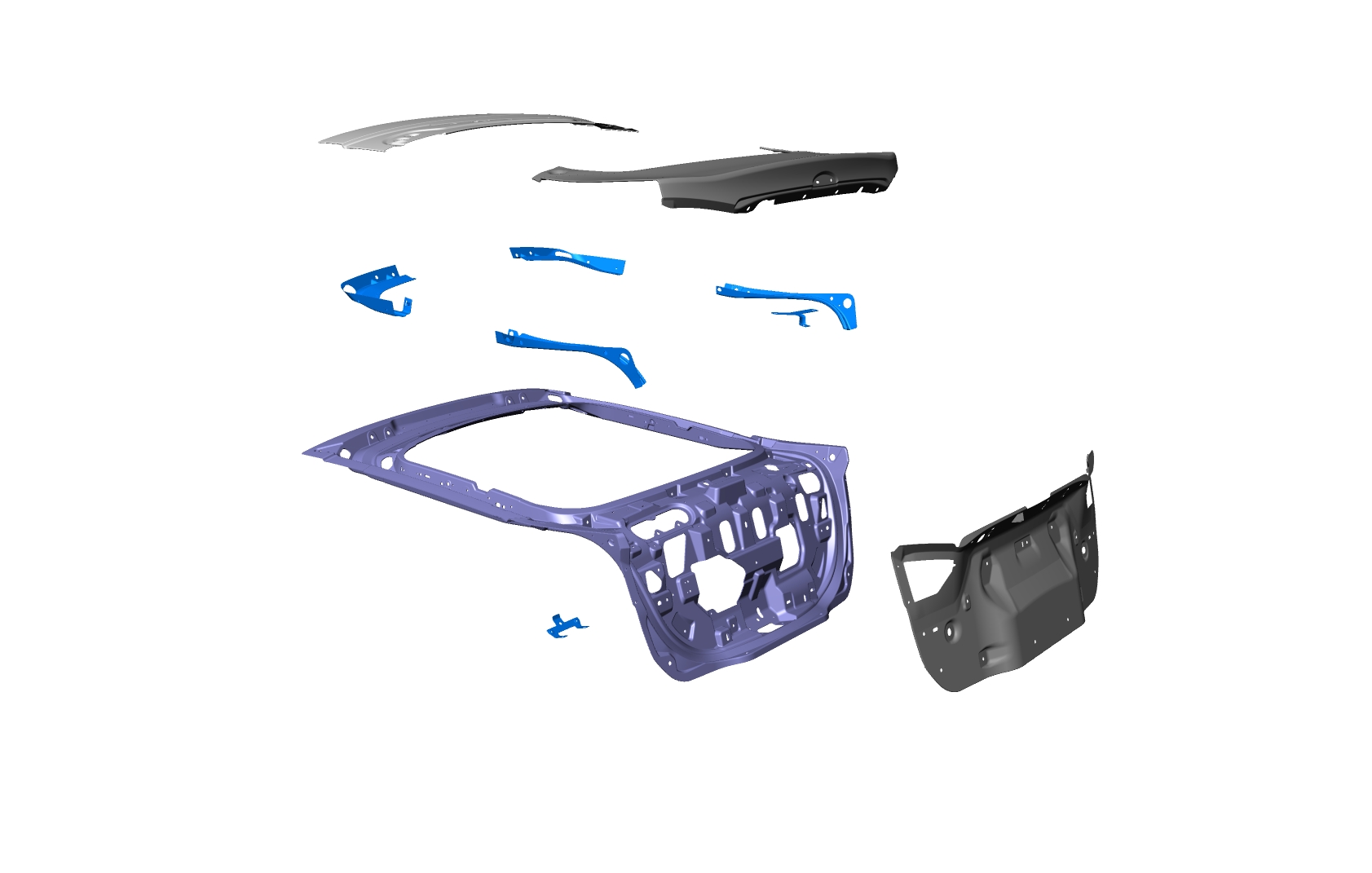
Eine Explosionsansicht der SMC/Aluminium-Heckklappe (mit Metallteilen) für die Fünftürer/Fließheck-Version des Ford Mondeo. Quelle | Ford Motor Co.
An diese Multimaterial-Baugruppen wurden hohe Anforderungen gestellt, darunter Torsions- und Biegebelastungen, Seitenstabilität, Korrosionsbeständigkeit, Langzeithaltbarkeit und Heckcrash-Tests. Außerdem mussten sie hohe Anforderungen an die Maßhaltigkeit in Bezug auf Ränder und Bündigkeit erfüllen.
Während das Hybridsystem die meisten Anforderungen problemlos erfüllte, gab es Pass- und Oberflächenprobleme aufgrund von Abweichungen des linearen thermischen Ausdehnungskoeffizienten (CLTE) zwischen den Verbundwerkstoff-Innenplatten und den Aluminium-Außenplatten, was zu Eigenspannungen in den Klebeverbindungen und Plattenverzug nach dem Abkühlen führte Nieder. Die anschließende Arbeit mit dem Simulationsteam der Purdue University konzentrierte sich auf die Verbesserung der Vorhersagen von Modul, Festigkeit und Härtungskinetik für den 1K-Epoxidklebstoff (ausgewählt wegen seiner Fähigkeit, E-Coating-Temperaturen zu überstehen) in der Hoffnung, einen besser funktionierenden Klebstoff nachzuentwickeln. Der Warpage wurde um eine Größenordnung reduziert, verfehlte das Ziel jedoch leicht. Mehrere Lösungen sind möglich:Es könnte ein 2K/Raumtemperatur- oder Induktions-Klebstoff ausprobiert oder ein neuer Hochtemperatur-Klebstoff entwickelt werden. Längerfristig würde das Ersetzen von Aluminium durch Kohlefaser-Verbundwerkstoff an der Außenhaut das Problem ebenso beseitigen wie die Offline-Produktion der Heckklappe und deren spätere Hinzufügung im Fahrzeugbau. Beide Optionen verursachen jedoch zusätzliche Kosten.
Projekt 3.2 ist jetzt abgeschlossen, hat aber interessante Technologien hervorgebracht, von denen einige – das B-Säulen-Prepreg und der SMC-Kofferraumdeckel – marktreif sind und einige auf Bereiche hinweisen, in denen weitere Arbeiten erforderlich sind.
„Die Zusammenarbeit mit IACMI und unseren industriellen und akademischen Partnern hat es uns ermöglicht, vom ersten Prinzip her viel tiefer in die Technologie einzutauchen, die Grundlagenforschung zu entwickeln und auf eine viel breitere Wissensbasis zurückzugreifen, als wir es allein hätten tun können“, fasst Patrick Blanchard, Leiter von Projekt 3.2, zusammen. technisch führend fortschrittliche Polymersysteme, Ford Forschung und Innovation. „Wir freuen uns darauf, neue kommerzielle Möglichkeiten und F&E-Aktivitäten zu identifizieren, um die Zusammenarbeit mit unseren IACMI-Partnern fortzusetzen.“
Harz
- Kohlefasergeräte für Ihr Zuhause
- Die 3 wichtigsten Anwendungen für den 3D-Druck von Kohlefasern in der Fertigung
- Innovative Anwendungen für Kohlefaser
- Kohlenstofffasern in Automobilanwendungen
- 5 lustige Anwendungen für Kohlefaserplatten
- Wofür wird Kohlefaserwickel verwendet?
- Materialien:Glas- und kohlenstofffaserverstärktes PP für die Automobilindustrie
- Hexion führt Zweikomponenten-Epoxidlösung für die Herstellung von Verbundwerkstoffen in der Luft- und Raumfahrt ein
- Foiling Motoryacht beeindruckt in Kohlefaser/Epoxid
- Serie für Automobilproduktionslinie