Entwerfen einer 3D-gedruckten Tesla-Turbine – Teil 1
Einführung
Willkommen zu einer zweiteiligen Miniserie zum Nachrüsten einer Tesla-Turbine mit Markforged-Teilen. Diese Blogs sind Anwendungstechnik in Reinform; Wir werden Techniken verwenden, die in früheren Blog-Beiträgen mit Anleitungen definiert wurden, um diesen Teil zu entwerfen und zu drucken. Am Ende haben wir hoffentlich eine funktionsfähige Tesla-Turbine mit Markforged-Teilen, die sich mit extrem hohen Geschwindigkeiten drehen kann. Im ersten Teil besprechen wir die Grundlagen der Tesla-Turbine und die Onyx-Reproduktion des Turbinengehäuses.
Was ist eine Tesla-Turbine?
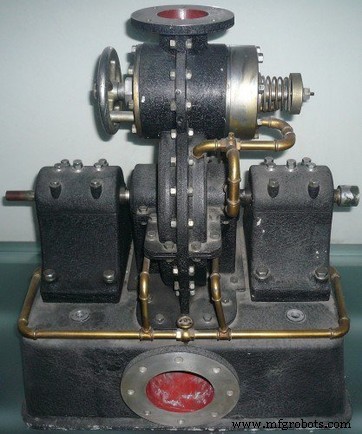
Eine Tesla-Turbine ist eine schaufellose Zentripetalströmungsturbine, die von Nikola Tesla im frühen 20. Jahrhundert patentiert wurde. Wie seine Gegenstücke mit Schaufeln wandelt er sich bewegende Flüssigkeiten in Energie um. Anstatt jedoch abgewinkelte Klingen zum Drehen einer Welle zu verwenden, werden glatte, parallele Scheiben verwendet. Fluide treten tangential zu den Scheiben am Außenrand der Turbine in die Turbine ein und erzwingen die Rotation durch Viskosität und Oberflächenschichthaftung. Wenn die Flüssigkeit langsamer wird und Energie verliert, dreht sie sich spiralförmig zum Zentrum der Turbine und tritt durch die Auslassöffnung aus. Das folgende GIF zeigt die Flüssigkeitsbewegung und die Energieübertragung in einer Tesla-Turbine.
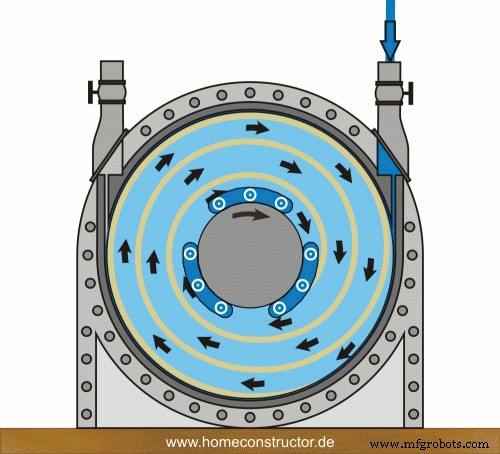
Als Nikola Tesla seine Tesla-Turbine zum ersten Mal schuf, bezeichnete er sie als seine „wichtigste“ Erfindung. Er stellte die Theorie auf, dass die Turbine einen Wirkungsgrad von 90 % beibehalten könnte und dass ihre Einfachheit in Design und Konstruktion zu einer Revolution in der Stromerzeugung führen könnte. Er hatte Recht:Die beiden anderen damals verwendeten Rotationsmotoren (Kolbenmotor und Schaufelturbine) waren teuer in der Herstellung und hatten viele Teile, die oft brachen. Im Gegensatz zu diesen beiden Maschinen war die Tesla-Turbine extrem einfach. Es mussten keine komplexen Merkmale hergestellt werden; Tatsächlich mussten die Klingen nicht einmal perfekt beabstandet sein. Theoretisch war es der perfekte nächste Schritt bei Rotationsmotoren.
Leider hatte die Maschine in der Praxis zwei Hauptfehlerstellen. Während Tesla die Turbine zunächst als nahezu perfekt effizient bewarb, funktionierte sie in Wirklichkeit nur mit einem Wirkungsgrad von etwa 40 %. Sein Verständnis der Grenzschichtdynamik berücksichtigte den Luftwiderstand nicht richtig. Diese Entwicklung war bedauerlich, aber keineswegs vernichtend; eine Turbine, die mit einem Wirkungsgrad von 40 % arbeitet, übertrifft immer noch beschaufelte Turbinen, die im Bereich von 25 bis 30 % arbeiten. Wenn sie zuverlässig Strom produzieren könnten, der der von beschaufelten Turbinen überlegen ist, wären Tesla-Turbinen ein bekannter Name. Sie konnten nicht. Tesla-Turbinen drehen sich mit extrem hoher Geschwindigkeit – die ursprünglichen Testturbinen von Tesla drehten sich mit Drehzahlen zwischen 9.000 und 36.000 U/min – so schnell, dass sich die Schaufeln der Turbinen während des Betriebs stark verziehen würden. Verformungen flößten kaum Vertrauen ein und Teslas „wichtigste“ Erfindung geriet in Vergessenheit. Heute werden Tesla-Turbinen in kleinem Maßstab als Lehr-Requisiten oder Vorführungen hergestellt. Obwohl sie nie ihrer Rechnung gerecht wurden, sind sie immer noch faszinierende Maschinen.
Neuerstellung einer Turbine mit 3D-gedruckten Teilen
Für dieses Projekt haben wir ein Tesla-Turbinendesign vom Olin College Machine Shop verwendet, das drei Kernsysteme umfasst:eine Wellen- und Rotorbaugruppe, ein Lagergehäuse und ein Turbinengehäuse. Die Wellenbaugruppe wird vollständig durch das Lagergehäuse eingeschränkt und durch das Turbinengehäuse eingeschlossen. Das Lagergehäuse und das Turbinengehäuse passen mit einer eng anliegenden Metallpassung und acht Schrauben zusammen.
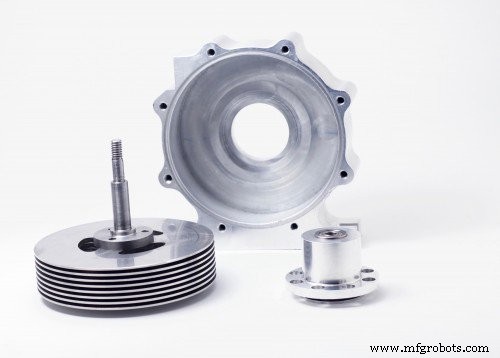
Die Einfachheit dieser Turbine eignet sich gut für die Bearbeitung. Es hat eine große Teilevielfalt in Material und Funktion, von einer gehärteten Stahlwelle bis hin zu einem Gehäusedeckel aus Polycarbonat. Jedes Teil der Turbine kann mit einer 2-Achsen-CNC-Maschine oder weniger hergestellt werden. Unten ist eine kurze Stückliste von bearbeiteten Teile in der Turbine.
Turbinengehäuse: CNC-gefrästes Aluminium
Lagerhalter: Gedrehtes und CNC-gefrästes Aluminium
Welle: Gedrehter Stahl
Wellenabstandshalter: Wasserstrahlstahl
Klingen: Wasserstrahl, dann gedrehter Stahl
Klemmplatte: CNC-gefrästes Aluminium
Riemenscheibe: Gedrehtes Aluminium
Einlassblock: CNC-gefrästes Aluminium
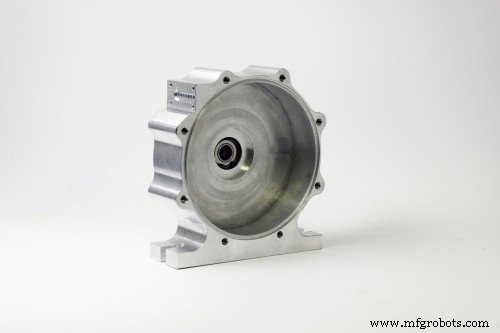
Einige Teile der Turbine eignen sich nicht gut für die additive Fertigung. Die Anforderungen an Präzision und axiale Festigkeit machen das Bedrucken der Stahlwelle sehr schwierig, und die Turbinenschaufeln und Abstandshalter profitieren davon, dass sie schwer sind (und somit eine große Rotationsträgheit aufweisen). Dies ist eine seltene Anwendung, bei der unser beeindruckendes Verhältnis von Festigkeit zu Gewicht nicht von Vorteil ist. Aus diesen Gründen haben wir uns entschieden, die gesamte Wellenbaugruppe (Welle, Distanzstücke, Schaufeln und Klemmplatte) in Ruhe zu lassen und uns auf die äußeren Teile der Turbine zu konzentrieren. Stattdessen haben wir uns auf zwei Teile konzentriert:Das Turbinengehäuse und das Lagergehäuse (auf die wir im nächsten Teil eingehen werden). Im Gegensatz zur Wellenbaugruppe war das Gehäuse ein perfekter Ersatzkandidat. Es ist komplett aus Aluminium, CNC-gefräst und ohne Toleranzen kleiner als 0,001 Zoll. Durch den 3D-Druck konnten wir die Festigkeit beibehalten und gleichzeitig das Gewicht drastisch reduzieren.
Anforderungen an das Turbinengehäuse
Das Turbinengehäuse hatte mehrere wichtige Anforderungen. Zunächst musste es nahtlos in das Lagergehäuse eingreifen. Dies bedeutete, dass er +0,001/-0 in Bezug auf die Fixierung am Lagergehäuse betragen musste. Das wohl wichtigste Merkmal des gesamten Gehäuses, ein engmaschiges Netz dämpft Vibrationen, die die Turbine bei hohen Drehzahlen auseinanderreißen könnten. Zweitens benötigte das Turbinengehäuse sechzehn Gewindebohrungen; acht auf der Rückplatte zur Montage des Lagergehäuses und acht weitere auf der Vorderseite zur Montage einer Abdeckplatte. Die Abdeckplatte aus Polycarbonat ist aus struktureller Sicht ein untergeordneter Teil, ist jedoch äußerst wichtig, um sicherzustellen, dass die Hochdruckluft durch die Turbinenschaufeln strömt. Schließlich muss der Hohlraum der Turbine eine sehr kleine Spielpassung mit den Schaufeln haben. Eine kleine Spielpassung gibt den Schaufeln Spielraum zum Drehen und minimiert gleichzeitig den Spalt zwischen den Schaufeln und der Hohlraumwand, was zu erheblichen Effizienzverlusten führt.
Design und Glasfaser-Routing
Die Neukonstruktion der Turbine für den Druck erforderte einige kleinere Änderungen, um die oben genannten Anforderungen zu erfüllen. Zuerst haben wir Unit-Tests verwendet, um die erforderliche Toleranz für das Lagergehäuseeingriff maßlich zu überprüfen. Um die erforderliche Toleranz einzuhalten, kamen wir zu dem Schluss, dass wir das Loch im CAD um ca. 0,002 Zoll unterdimensionieren müssen (Hinweis:Dies ist keine universelle Zahl, sondern eine aus den von uns durchgeführten Komponententests. Um mehr über Komponententests zu erfahren, schau dir diesen Blogbeitrag an). Als nächstes haben wir alle Gewindebohrungen in der Aluminiumversion durch Hohlräume für Heatset-Gewindeeinsätze ersetzt (Link hier). Heatset-Einsätze sind eine zuverlässige Methode zur Befestigung in 3D-gedruckten Teilen und gewährleisten solide Verbindungen, wo Gewindebohrungen nicht möglich sind.
Wir haben im gesamten Teil konzentrische Kohlefasern verlegt, um das Design zu verstärken. Damit die Lagergehäuseaufnahme und die Folgekräfte das Teil nicht verformen, haben wir die Rückwand des Teils mit möglichst vielen Faserringen ausgefüllt. Die Wände des Teils erforderten weniger Festigkeit, daher haben wir uns mit einem Faserring auf jeder Wandschicht festgelegt. Mit dieser Strategie konnten wir die Ringfestigkeit des Teils mit minimalem Faseranteil erheblich steigern. Nachdem das Teil in Eiger ausgelegt war, waren wir druckfertig.
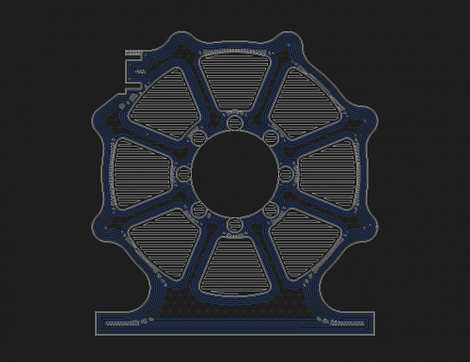
Dimensionale Überprüfung
Der Turbinenkörper passt auf einen Mark Two; Wir haben uns jedoch aus einem einfachen Grund dafür entschieden, es auf dem Mark X zu drucken:die Überprüfung der Laserabmessungen. Unit-Tests haben uns gezeigt, dass unsere Dimensionen genau sein sollten; Jetzt konnten wir die Genauigkeit mitten im Druck überprüfen. Wir haben zwei Laserscans konfiguriert:einen zur Überprüfung der Passung mit dem Lagergehäuse und einen weiteren zur Überprüfung des Hohlraumdurchmessers. Während des Drucks haben wir jeden Scan in Eiger überprüft, um die Maßhaltigkeit zu gewährleisten. Der bemaßte Scan zeigte einen Fehler von 0,0004″, weit innerhalb der Toleranz.
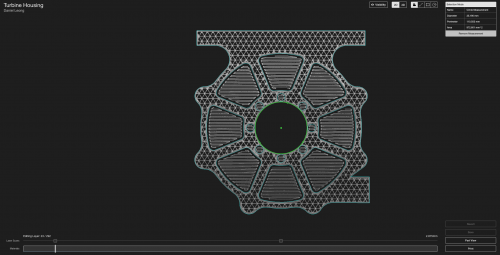
Nächste Schritte
Nachdem der Druck fertig war, setzten wir die Gewindeeinsätze ein und befestigten das Aluminium-Lagergehäuse. Inklusive der Einsätze, die gedruckte Turbine 170g, die im Vergleich zum 570g Aluminiumgehäuse mikroskopisch klein war. Nachdem wir überprüft hatten, dass das Metallgehäuse und die Wellenbaugruppe funktionierten, haben wir das Lagergehäuse entworfen und gedruckt, das wir in der nächsten Ausgabe dieser Serie behandeln werden.
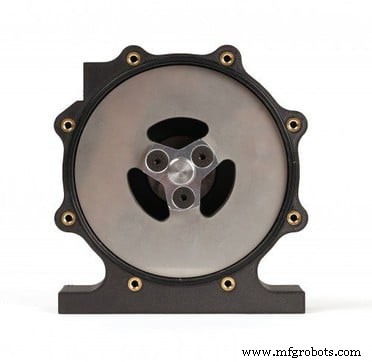
Lesen Sie den zweiten Teil dieses Beitrags hier und folgen Sie uns auf Facebook, Twitter, Instagram und Linkedin für weitere Updates!
3d Drucken
- Die 10 wichtigsten Tipps, die Sie beim Entwerfen Ihres FDM-Teils beachten sollten
- Metall-3D-Druckanwendungen (Teil 2)
- Entwerfen einer 3D-gedruckten Tesla-Turbine – Teil 1
- Inprozesskontrolle:Verbesserung von 3D-gedruckten Teilen
- Ein Teil der Woche – 3D-gedruckter Stoßdämpfer
- 3D gedruckte Extremdrohnen
- Maßgenauigkeit von 3D-gedruckten Teilen
- Wie man stärkere 3D-gedruckte Teile erhält
- Inspektionsmethode für 3D-gedruckte Teile (Teil 3)
- Zylindrizität in GD&T