MMF #3:Faserverstärkte Living-Scharniere, die stark genug sind, um darauf zu stehen
MarkForged Mechanical Features [MMF] ist eine Reihe von Blog-Posts, in denen Best Practices für die Entwicklung gängiger traditioneller Konstruktionsteile und mechanischer Features für den verbundverstärkten 3D-Druck mit MarkForged-Druckern beschrieben werden.
Bei FFF (Fused Filament Fabrication) 3D-Druckern kommt es häufig zu einer schlechten vertikalen Bauteilfestigkeit, insbesondere wenn sie unter Spannung belastet werden. Bei diesen 3D-Drucktechnologien ist die Verbindung entlang der vertikalen Achse schwächer als die Festigkeit des konstituierenden Materials, da in jedem Teil Hunderte von Schichten entlang der vertikalen Achse miteinander verklebt sind, sodass sich die Verbindung zwischen den einzelnen Schichten wie eine Naht oder a . verhält beim Laden knacken. Die Festigkeit einer Schicht in der Ebene ist höher als die Adhäsion zwischen den Schichten, da der Kunststoff in jeder Schicht als kontinuierliches Extrudat aufgetragen wird und die Festigkeitseigenschaften des Teilmaterials selbst aufweist. Beim Mark Two tritt dieser Richtungsunterschied in den Festigkeiten (oder Anisotropie) auch bei unserem Continuous Filament Fabrication (CFF)-Prozess auf – alle von uns verarbeiteten Verbundfasern haben eine beeindruckende Zugfestigkeit, aber weil sie entlang Ebenen parallel zur Bauplatte, diese Stärke wird nicht direkt in die vertikale Achse übersetzt. Das richtige Design für 3D-gedruckte Teile beinhaltet die Anpassung der Geometrie einer Komponente, so dass sie hauptsächlich in der horizontalen Ebene geladen wird, und Teile, die mit einem Markforged-Drucker erstellt wurden, sind keine Ausnahme. Mit einigen netten Design-Tricks im Ärmel können Sie dieses Problem jedoch umgehen und industrietaugliche 3D-gedruckte Teile auf dem Mark Two mit viel mehr isotropen Eigenschaften erstellen.
Wenn Sie schon einmal mit unseren Materialien gearbeitet haben, ist Ihnen vielleicht aufgefallen, dass unser Nylon an sich ziemlich flexibel sein kann. Dies ermöglicht die Konstruktion von Filmscharnieren oder flexiblen Abschnitten von Komponenten, die ohne jegliche Montage eine Verbindung oder ein Scharnier bilden können. Erfahren Sie hier mehr über die Gestaltung von Filmscharnieren und Biegeelementen.
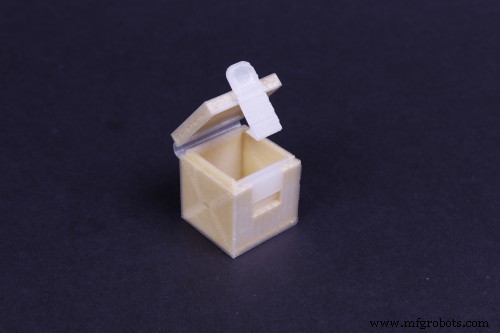
Während die Faserverstärkung des Markforged-Druckers das Nylon ziemlich versteifen kann, können Sie mit Kevlar® faserverstärkte Scharniere herstellen. Bei diesen faltbaren 3D-gedruckten Strukturen sorgt das Nylon für die Flexibilität und die Faser für die Verbindungsfestigkeit. Mit ein wenig faserverstärktem Origami können Sie skelettierte Teile mit minimalem Trägermaterial entwerfen, die in alle Richtungen stark sind. Hier ist ein Beispiel:
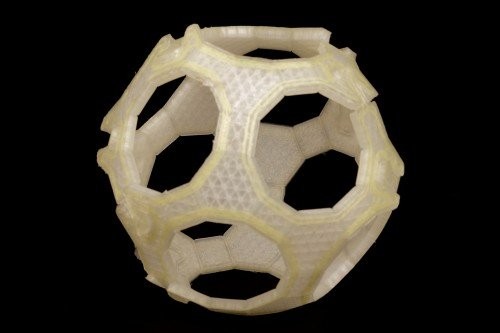
Ein Teil wie dieses hätte wahnsinnig viel Zeit und Unterstützungsmaterial benötigt, um wie abgebildet zu drucken, und es wäre entlang der vertikalen Achse ziemlich schwach gewesen, also habe ich es so entworfen:
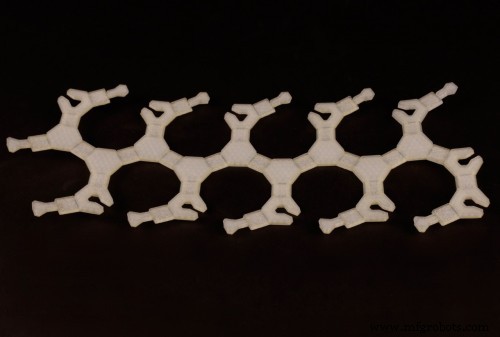
Wenn man sich das Faserlayout in Eiger ansieht, sieht man in diesem Druck nur eine Lage konzentrisch gemusterten Kevlars. Ich habe mich für Kevlar entschieden, weil Kohlefaser und Glasfaser zwar fester sind, Kevlar jedoch das flexibelste der von uns angebotenen Materialien ist und einen Großteil seiner Zugfestigkeit auch bei scharfem Biegen beibehält. Kohlefaser und Glasfaser sind viel steifer und brechen bei Biegeradien, die Kevlar problemlos verarbeiten kann. Die einzelne Schicht Kevlar bietet genug Kraft, damit dieser Ball ein paar Dutzend Pfund aufnehmen kann, aber genug Flexibilität, damit sich die Gelenke gut falten können.
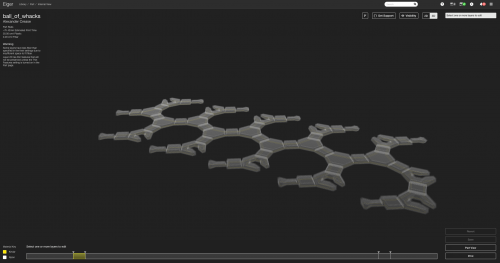
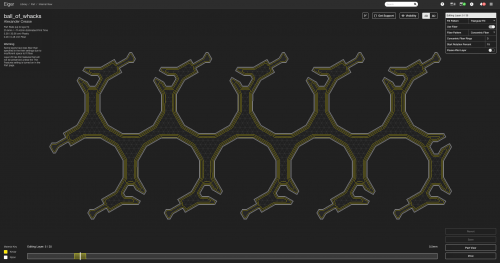
Nachdem ich das Polyeder entworfen hatte, erhöhte ich den Einsatz, um zu sehen, ob ich etwas Faltbares in 3D drucken könnte, das stark genug war, um mein Körpergewicht zu tragen. Ich beschloss, es einfach zu halten und entwarf in Autodesk Fusion 360 einen faltbaren Kevlar-Würfel. Ich brauchte eine Methode zum Befestigen der Flächen des Würfels und eine Verbindung zum Verbinden von Flächen, die nicht direkt nebeneinander lagen. Ich begann mit der Modellierung von vier Flächen des Würfels, jede als separate Komponente, damit ich in der CAD-Umgebung das gewünschte Faltverhalten für mein Gelenk simulieren konnte. Um eine Verbindung zwischen den einzelnen Flächen zu gewährleisten, habe ich eine Schnappverbindung entworfen, damit beim Falten jeder Fläche in die richtige Ausrichtung die Fläche einrastet und die Schnappverbindungen verhindern, dass sich der Würfel entfaltet oder verformt.
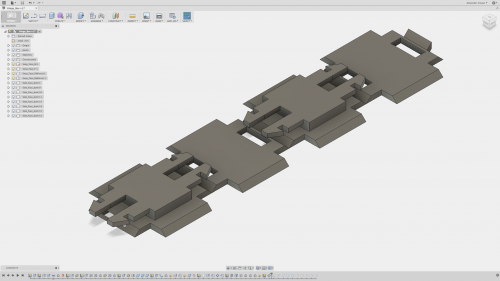
Ich habe auch eine kleine Nut- und Zapfenverbindung an den Kanten hinzugefügt, die sich verbinden würde, sobald die linke Seite auf die rechte Seite traf.
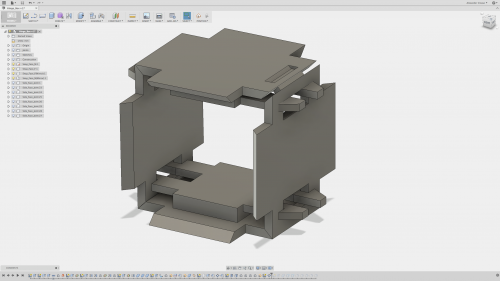
Ich beschloss dann, mit den verbleibenden beiden Seiten der Schachtel etwas Interessantes auszuprobieren – an jedem offenen Restrand habe ich von jeder Seite einen Abschnitt entworfen. Jeder Abschnitt hat eine Drehverschlusslasche und eine Aussparung für die entsprechende Lasche am angrenzenden Abschnitt. Sobald die Schachtel gefaltet ist, können diese alle zusammengeschnappt werden, um die verbleibenden beiden Seiten zu bilden. Im Bild unten habe ich eines der Teile transparent gemacht, um die Fasen zu zeigen, die ich hinzugefügt habe, um eine schwalbenschwanzartige Verbindung zu schaffen, die von der Flexibilität des zu verdrehenden Materials abhängt.
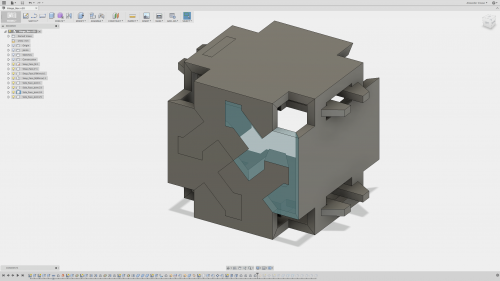
Sobald die Geometrien jedes Gesichts in Stein gemeißelt waren, „entfaltete“ ich den Würfel in CAD, so dass alle Körper in der Ausrichtung flach gelegt wurden, in der ich das Stück drucken wollte. Sie werden in der Abbildung unten feststellen, dass jede der Komponenten treffen sich an ihren Rändern – sie sind noch nicht verbunden. An diesem Punkt musste ich dies noch zu einem einzigen, einheitlichen Teil kombinieren, indem ich die Schichten hinzufügte, die zum Erstellen des lebenden Scharniers erforderlich sind.
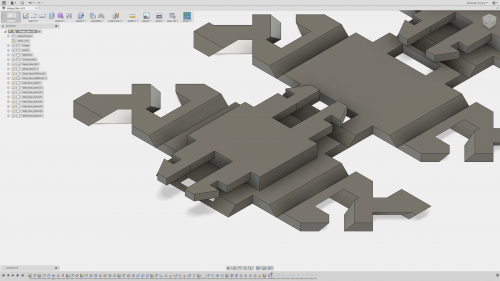
Dazu habe ich die Profile der Unterseiten jedes Bauteils erfasst und um 0,875 mm extrudiert und alle einzelnen Körper zu einem zusammengefasst. Dies verleiht dem Filmscharnier Stärke:Die Dicke von 0,875 mm fügt gerade genug Material hinzu, damit eine einzelne Schicht Kevlar hineinpasst und ein faserverstärktes Filmscharnier entsteht. Beachten Sie unten, dass jetzt jede Kante, an der sich die einzelnen Komponenten treffen, jetzt eine Dicke hat.
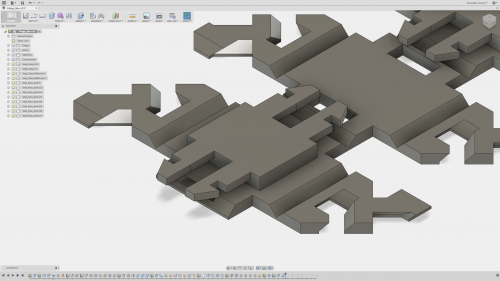
Und hier ist die vollständige Ansicht des ausgelegten und druckfertigen Teils:
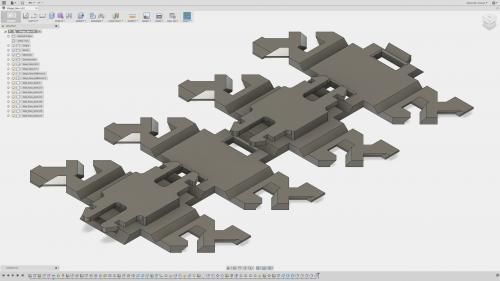
In Eiger habe ich auf dieser ersten Kevlar-Schicht konzentrische Faserringe gelegt, um die Verbindung herzustellen und zu verstärken. Um den Rest des Teils zu verstärken, habe ich Sandwichplatten erstellt, die auf jeder Seite über dieser ersten Kevlar-Schicht beginnen. Wie wir in einem älteren Beitrag erklärt haben, sind Sandwichpaneele von grundlegender Bedeutung für Verbundwerkstoffe, da sie eine hohe Festigkeit bei geringem Gewicht bieten. Die Sandwichpaneele verstärken jede Seite des Würfels, um sie zu starken und steifen 3D-gedruckten Komponenten zu machen – denken Sie daran, dass jede Seite nur etwa 3 mm dick ist. Ich konnte auch Kevlar in die Schnappverbindungen einbauen, um ihre kleinen Eigenschaften zu verstärken, die wir in einem früheren Beitrag besprochen haben. Das folgende GIF zeigt die ersten Schichten, einschließlich der Kevlar-verstärkten Living-Scharnier-Schicht (Schicht 5) und die unteren Schichten der Sandwichplatte (Schichten 6-8).
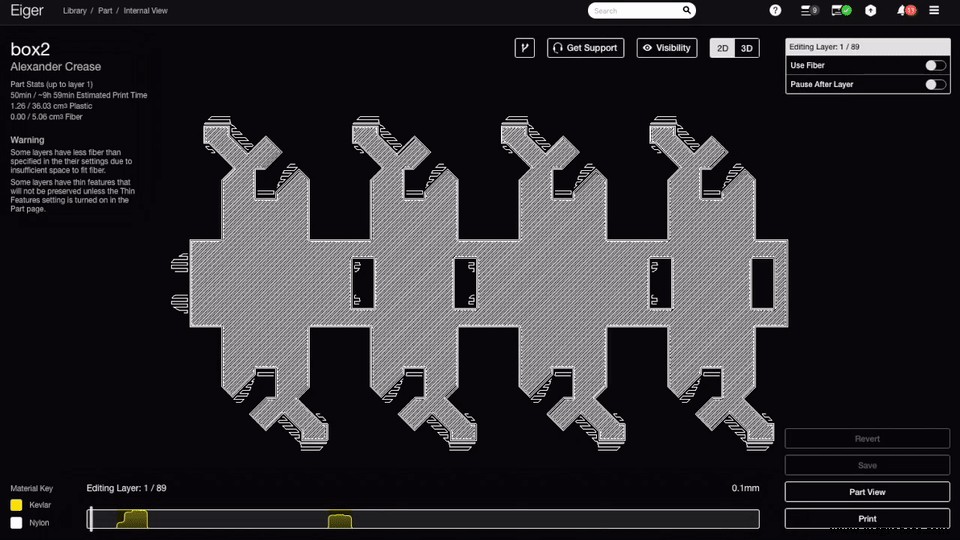
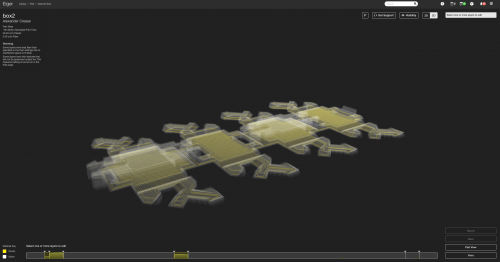
Nachdem es gedruckt war, habe ich alles zusammengeschnappt und die Seitenwandverbindungen verdreht und einen 3D-gedruckten faltbaren Würfel mit etwas Kevlar-Verstärkung hergestellt!
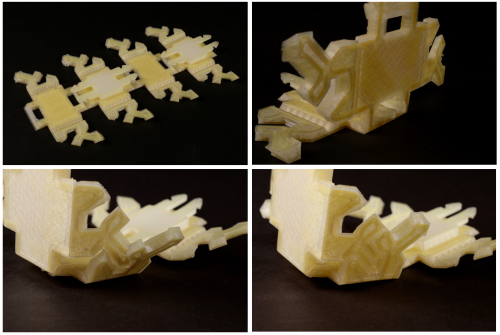
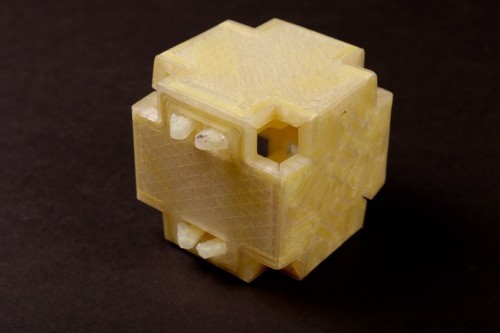
Jede Seite des Würfels bietet eine wesentliche Verstärkung sowohl beim Zug als auch beim Biegen, wodurch der Würfel insgesamt sehr schwer zusammendrückbar und entlang der drei Hauptachsen isometrisch ist. Ich konnte mein gesamtes Körpergewicht (ca. 130 lbs) darauf legen, ohne auch nur eine Andeutung von Verformung. Da ich jedoch eine ziemlich kleine Person bin, habe ich einen viel strengeren Test gemacht. Ich habe keine sehr guten Messwerte erhalten, aber ich würde schätzen, dass es etwa 300-400 Pfund hielt, bevor es versagte. Folgendes ist passiert:
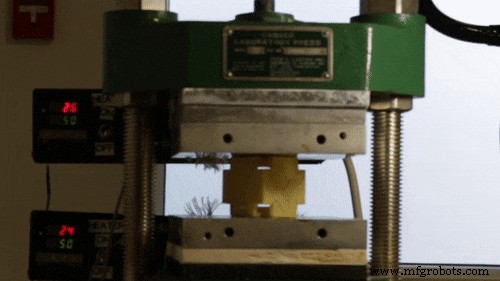
Nach ein paar hundert Pfund war das Überraschendste, dass das Teil nicht wirklich brach, alle Gelenke einfach auseinandersprangen und der gesamte Würfel flachgedrückt wurde, sodass er mit ein wenig Begradigung wieder in seine ursprüngliche Form gebracht werden kann. Indem Sie also faltbare Strukturen mit faserverstärkten lebenden Scharnieren erstellen, können Sie einige wirklich starke 3D-gedruckte Teile in alle Richtungen herstellen.
Sie möchten diese selbst ausdrucken? Laden Sie die STL- oder .mfp-Datei herunter!
Möchten Sie die Stärke selbst testen? Bestellen Sie hier ein kostenloses Musterteil!
3d Drucken
- Was sind Bi-Fold-Scharniere?
- 5 Vorteile der Wahl von Aluminiumscharnieren
- Eine Einführung in die durchgehenden Scharniere
- Die Vorteile von lebenden Scharnieren
- Die vorhandene Lasertechnologie ist stark genug, um Außerirdische in einer Entfernung von 20.000 Lichtjahren anzulocken
- Mein erster angepasster Mini-CNC-Fräser – Er muss stark genug sein
- Ferro-Titanit® U
- DIFENDER 400
- Druckfestigkeit verstehen
- So entwerfen Sie 3D-gedruckte lebende Scharniere