Großteilbearbeitung testet horizontale Werkzeugmaschinenfähigkeiten
Vielseitige Plattformen verarbeiten die Verarbeitung mit maximaler Effizienz
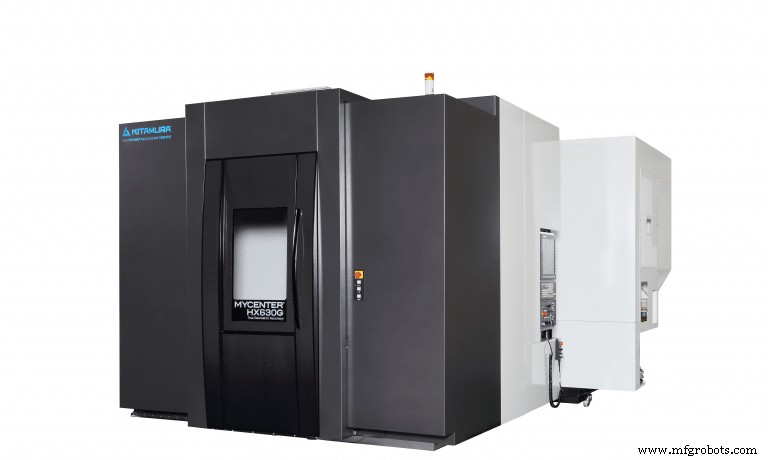
Horizontale Bearbeitungszentren (HMCs) sind vielseitige vierachsige und zunehmend fünfachsige Maschinenplattformen, die die Bearbeitung von mehrseitigen großen Teilen durch Minimierung der Teilehandhabung maximieren. Sie werden in so unterschiedlichen Branchen wie Luft- und Raumfahrt, Automobil, Energieerzeugung und allgemeinem Maschinenbau eingesetzt.
Mit ihren nahezu universellen Produktionskapazitäten bieten HMCs den Herstellern viele Wahlmöglichkeiten, wodurch sie weniger anfällig für das zyklische Auf und Ab einer Branche wie Öl und Gas sind. HMCs sind ohne weiteres automatisierbar. Sie sind typischerweise mit Doppelpaletten für auf Spanntürmen montierte Teile oder ein einzelnes Werkstück ausgestattet oder können mit Palettenpools von sechs oder mehr Paletten automatisiert werden. Für die unbeaufsichtigte Lights-out-Produktion sind lineare flexible Fertigungssysteme (beschickt von Stockern und bedient von schienengeführten Portalrobotern oder sechsachsigen Robotern auf einem Sockel) verfügbar. Einzelne große Werkstücke reichen von Motorblöcken bis hin zu Ölfeldbohrern, Pumpengehäusen und Verteilern sowie Familien von auf Grabsteinen montierten Komponenten.
Anpassmaschinen, große Teile
Wenn es um die Bearbeitung großer Teile geht, sind laut Sal Swierczek, stellvertretender Verkaufsleiter, Kitamura USA Inc., Wheeling, Illinois, die Steifigkeit der Maschine und ihre grundlegende Konstruktion entscheidend für die Prozesseffizienz, Genauigkeit und Konsistenz.
„Kitamuras HXiG-Serie von HMCs reicht von 250 bis 1250 mm Tischgröße mit 8.000 U/min oder 12.000 U/min vierstufigen, zahnradgetriebenen Spindeln, die ein Drehmoment von 430 bis 900 ft-lb zum Schneiden exotischer Materialien liefern“, sagte er. „Diese HMCs verfügen über ölgekühlte Doppelkugelumlaufspindeln auf Hohlkehlen, die gemäß Kitamuras patentiertem Verfahren induktionsgehärtet und geschliffen werden, um eine Oberflächengüte von unter 4 µm für überlegene Verbindung, Genauigkeit und langfristige Zuverlässigkeit zu erreichen. Handwerkskunst in Handscraping-Techniken ermöglicht konsistente Genauigkeiten von ±0,002 mm Vollhub und ±0,001 mm Wiederholbarkeit.“
Die erste Überlegung ist natürlich, dass das Werkstück in den Arbeitsbereich der Maschine passt, egal ob ein Teil auf den Tisch geladen wird oder mehrere Teile geladen werden, um den Durchsatz zu erhöhen, so Swierczek. „Zu den wichtigsten Kriterien für die Maschinenauswahl gehören die Maschinenkapazität (einschließlich der Gesamtmaschinengröße), die Spindelleistung, die Steifigkeit, die Anzahl der Werkzeuge, die Auswahl der Magazingröße sowie die Konizität und Größe der Werkzeuge“, sagte er. „Horizontale Kitamura-Maschinen haben standardmäßig einen APC mit zwei Stationen [automatischer Palettenwechsler] mit der Option, die Anzahl der Paletten mit Palettenpools vor Ort zu erhöhen.“
Swierczek fügte hinzu, dass „die Fähigkeit zur Automatisierung eine der Herausforderungen ist, denen sich Unternehmen heute gegenübersehen, und das ist die Schwierigkeit, qualifizierte Bediener und Arbeitskräfte zu finden, die mit der Lights-Out-Bearbeitung umgehen können.“
Horizontale Bearbeitungszentren bieten die dringend benötigte Flexibilität in der Teilebearbeitung. „Im Vergleich zu einem Drei-Achsen-Bearbeitungszentrum minimieren Voll-Vier-Achsen-Bearbeitungszentren die Teilehandhabung und reduzieren die Anzahl der Male, die ein Teil gewendet werden muss, von sechs auf zwei“, sagte Swierczek. „Mit der vierten Achse des Bearbeitungszentrums kann der Bediener das Teil von vorne und von beiden Seiten anfahren und für die Endbearbeitung neu positionieren.“
Darüber hinaus können Kitamura HMCs auf eine vollständige Fünf-Achsen-Bearbeitung erweitert werden, wenn das Geschäft einer Werkstatt wächst. Kitamura bietet seine eigene Arumatik-Mi, eine symbolgesteuerte CNC-Steuerung, die mit der FANUC-Programmierung kompatibel ist. Die Arumatik-Mi-Steuerung erkennt den Werkzeugverschleiß und steuert die Schnittvorschubgeschwindigkeit automatisch, indem sie die Spindellast während der Bearbeitung überwacht. Die Werkzeugstandzeit wird maximiert und die Zykluszeit drastisch verkürzt, indem sie sich an veränderte Schnittbedingungen anpasst. Zu den weiteren Vorteilen gehören die Reduzierung der Unterbrechungszeiten und die Vermeidung von Maschinenabstürzen und/oder menschlichen Fehlern.
Maschinen für große Teile
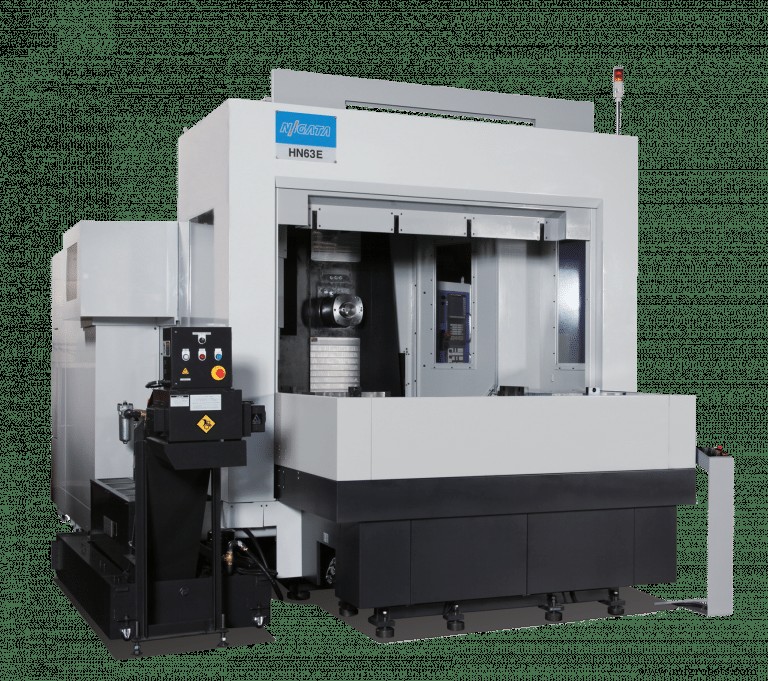
Für die Bearbeitung großer Teile bietet Methods Machine Tools Inc., Sudbury, Massachusetts, zwei horizontale Bearbeitungszentren an:Niigata und KIWA Japan. „Die Linie von KIWA Japan ist bekannt für Hochgeschwindigkeits- und hochzuverlässige Bearbeitung, typischerweise für Lohnfertiger und Tier-1- und Tier-2-Automobilwerkstätten“, sagte Dale Hedberg, Vice President of Operations. „Die Niigata-Produktlinie ist für Schwerzerspanungsanwendungen konzipiert, bei denen eine Niederfrequenzbearbeitung und hohe Metallabtragsraten erforderlich sind.“
Die Produktlinie von Niigata umfasst die fünfachsigen HN50E-5X und HN63E-5X, die vierachsigen HN50 bis HN1600, die HN800 bis HN1600-BAR und die Plan- und Konturbearbeitungsmaschinen HN800 und HN1000-FC. Maschinenplattformen haben eine Tischgröße von 500 mm bis 1.600 mm. Spindelkonusgrößen sind CAT-50 BIG Plus, HSK100A, mit Spindeloptionen von 6.000 und 8.000, 12.000 und 15.000 U/min.
„Die Branche tendiert derzeit zu fünfachsigen Plattformen in horizontalen Bearbeitungszentren, die Niigata sowohl in den Größen 500 als auch 630 mm anbietet“, sagte Hedberg. „In der Luft- und Raumfahrt- und Energieindustrie konzentriert sich Niigata auf niederfrequente Bearbeitungsanwendungen, die von den natürlichen Dämpfungseigenschaften der Maschinen profitieren. Die Niederfrequenzbearbeitung wird zu einem beliebten Begriff, wenn es um die Hochdrehmomentbearbeitung von Titan und Inconel für eine bessere Werkzeugstandzeit und Langlebigkeit der Spindel geht“, erklärte er.
Die Fähigkeit, Vibrationen von Schnittkräften zu dämpfen, ist natürlich den Gussteilen und Metall-auf-Metall-Kontaktflächen der Maschine eigen, die für die passende Oberflächengüte von Hand geschabt werden. Typische Anwendungen in den Bereichen Energie und Stromerzeugung sind laut Hedberg Flansche, Fracking-Köpfe und Blisks.
Bei der Bearbeitung großer Teile mit HMCs sind diametrale Genauigkeit des Verfahrwegs in jeder Achse und Steifigkeit besonders wichtig, um Präzision und Wiederholbarkeit zu erreichen. Hedberg sagte:„Das Schöne an der Fünf-Achsen-Bearbeitung ist, dass Sie keine aufwändige Vorrichtung oder kundenspezifische Werkstückhalterung benötigen, es sei denn, Sie bearbeiten ein einzigartiges Teil, das möglicherweise eine fensterartige Vorrichtung oder eine spezielle Spannmethode erfordert.“
Anwendungsorientierte HMCs
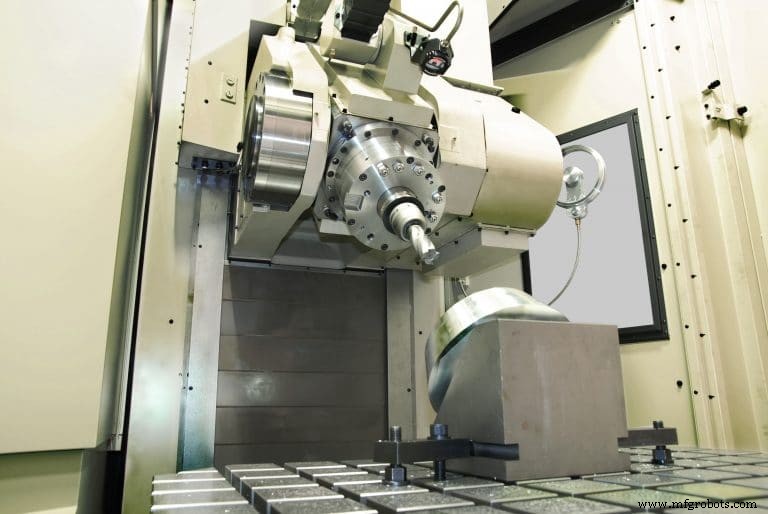
Mitsui Seiki USA Inc., Franklin Lakes, N.J., orientiert sich an der Kundennachfrage nach der Entwicklung neuer horizontaler Bearbeitungszentren – insbesondere an aktuellen Modellen, die für die Bearbeitung großer Teile am gefragtesten sind, so Präsident Robb Hudson. „Heute kommt die Nachfrage nach großen Teilen definitiv aus der Luft- und Raumfahrt, die derzeit ein großer Treiber ist, sowohl bei der Teilefamilie von Strahltriebwerken als auch bei Strukturkomponenten. Andere Zielmärkte sind der Formen- und Formenbau, der Weltraum sowie die Verteidigungs- und Industriegasturbinensektoren“, sagte er.
„Unsere horizontalen Bearbeitungszentren mit Paletten von 1 m und mehr und Begleittischkonfigurationen, die Gewichte von 1.000 bis 10.000 lb [453-4.535 kg] aufnehmen können, gelten als unsere Maschinen für große Teile. Es ist wichtig zu beachten, dass unsere Maschinen in diesem Größenbereich alle von Kunden stammen, die die Entwicklung vorangetrieben haben. Wir haben die Maschinen nicht gebaut und dann nach Märkten gesucht. Sie sind alle aus den Anforderungen eines Kunden für eine bestimmte Anwendung abgeleitet.“
Um für die Fertigung großer Teile in Betracht gezogen zu werden, haben Mitsui Seiki-Maschinen alle die gleichen technischen Hauptmerkmale. Hudson sagte:„Meiner Meinung nach gibt es zwei Kategorien – große Teile, die auch einen großen Materialabtrag erfordern, und Teile, die einfach umständlich sind und leichtere Schnitte erfordern. Mitsui Seiki ist im Bereich der großen Teile tätig, der das Hochleistungsschneiden von zähen Materialien erfordert. Daher verfügen unsere Maschinen über viel Masse, Steifigkeit, große Kastenführungen, Kugelumlaufspindeln mit großem Durchmesser für reichlich Schub, robustes axiales Drehmoment und spezielle Servomotoren, um das Teil im Arbeitsbereich zu bewegen und die erforderlichen Schnittkräfte aufzunehmen.“
Laut Hudson sind alle diese Merkmale sowie Steuerungs- und Konstruktionspräzision erforderlich, um die richtige Leistung für die Anwendung zu liefern. Er fügte hinzu, dass die Spannvorrichtung ein wichtiges Element in der Fertigung großer Teile ist und oft so umfangreich und schwer ist wie das Werkstück, das sie hält.
Automatisierung einfacher gemacht
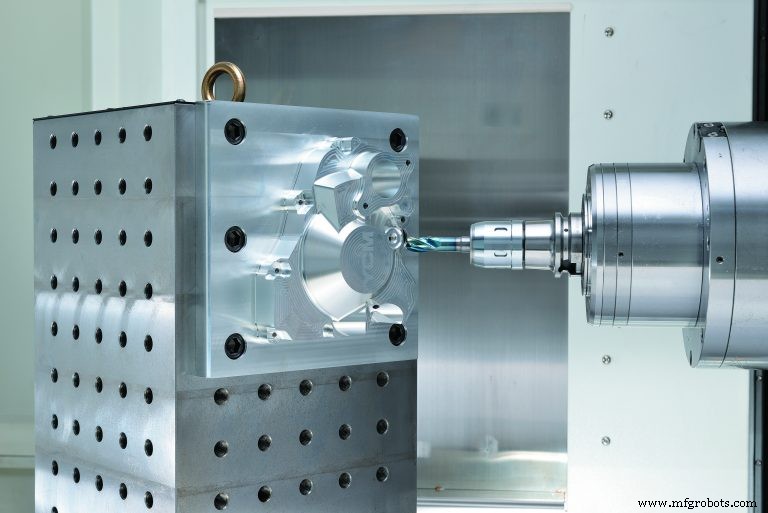
Während die Einrichtung der Automatisierung mit jeder Art von Maschine kompliziert ist, scheinen HMCs aufgrund des Volumens ihrer Produktionsleistung einfacher zu automatisieren, so Mel Gay, regionaler Verkaufsleiter, YCM Technology (USA) Inc., Carson, Kalifornien.
„Die Geschwindigkeit, mit der die investierten Dollars zurückerlangt werden, ist immer das Hauptanliegen beim HMC-Einkauf“, sagte er. „Beliebte Größen sind 500/630 mm mit einer minimalen Werkzeugkapazität von 60–120 Werkzeugen für kleine Werkstätten und 240 Werkzeugen und mehr für große Fabriken. Größere Werkzeugkapazitäten ermöglichen komplexere Aufträge mit minimaler Rüstzeit, insbesondere bei der Zellenkonfiguration mit mehreren Paletten.“
Auf der IMTS stellte YCM den NH500A 6 APC aus, der auf Branchen wie die Automobilindustrie ausgerichtet ist, die hohe Stückzahlen produzieren. Der NH500A hat eine 30-PS-Spindel mit 20.000 U/min und eine Palette von 500 x 500 mm.
„Produktivität beginnt mit dem hochstabilen T-Fuß-Fundament mit Rippenkonstruktion“, sagte Gay. „YCM kombiniert dieses Fundament mit einem einteiligen gegossenen Spindelstock und einem doppelwandigen Säulendesign. Die Direktantriebsspindel verfügt über Präzisions-Keramikkugellager, was eine höhere Schnittdynamik und höhere Spindeldrehzahlen ermöglicht.“
Hochpräzise Rollenführungen auf allen Achsen ermöglichen schnelle Geschwindigkeiten von 2.362 ipm (60 m/min) und Schnittvorschübe von bis zu 1.575 ipm (40 m/min), so Gay. Das Präzisions-Palettenindexierungssystem bietet Platz für einen APC mit sechs Paletten für einen hohen Durchsatz einer einzelnen Komponente oder von Teilefamilien.
„Alle diese Merkmale ermöglichen die Nutzung der neuesten Schneidwerkzeugtechnologie, die Verbesserung der Teileverarbeitung und die Senkung der Gesamtbetriebskosten“, sagte er.
Große Teile von HMCs in Amerika gebaut
DMG Mori, Hoffman Estates, Illinois, stellt in seinem Werk in Davis, Kalifornien, vier Modelle horizontaler Bearbeitungszentren her. Die NHX 4000 und NHX 5000 sind Maschinen der dritten Generation mit 40er Konus und 400- und 500-mm-Paletten; Die NHX 5500 und NHX 6300 sind Maschinen der zweiten Generation mit 50er Konus und 500- und 630-mm-Paletten.
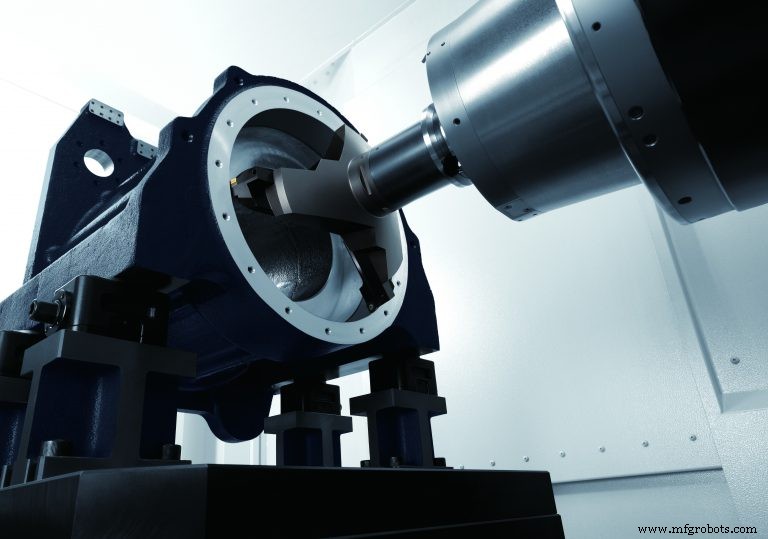
„Unsere Horizontalfräsen sind sowohl für die Anforderungen unserer Kunden in den Bereichen Energie, Luft- und Raumfahrt, Industrieanlagen und Auftragsfertigung sowohl für die schweren Schnitte als auch für die hohen Genauigkeitsanforderungen ausgelegt“, sagte John McDonald, Executive Vice President of Development and Product Management.
Typische Werkstücke sind große Ventile und Turbinenteile für die Energiewirtschaft; Motor-, Differential- und Getriebegehäuse in Industrieanlagen; und Strukturbauteile in der Luft- und Raumfahrt. Die Materialien reichen von Titan oder Edelstahl bis hin zu Gusseisen oder Aluminium – je nach Anwendung.
„Unsere Kunden erzielen eine hohe Produktivität durch Automatisierung durch den Einsatz von Palettenpoolsystemen für die High-Mix-Produktion oder durch spezielle Roboterbeladung mit unserer integrierten Vorrichtungshydraulik durch den Tisch, die standardmäßig in unseren horizontalen Bearbeitungszentren enthalten ist“, sagte McDonald. „Großteilebearbeitung und Schwerzerspanung sind auf eine optimierte Maschinenstruktur angewiesen. Alle unsere horizontalen Maschinen haben eine vollständig Finite-Elemente-optimierte Struktur, einschließlich einer hochbelastbaren Dreipunkt-Stützbettstruktur aus Gusseisen, einer powerMASTER-Spindel (50-Kegel-Maschinen) und Rollenlinearführungen. Alle unsere Maschinen sind standardmäßig mit Linearskalen ausgestattet, die es unseren Kunden ermöglichen, die höchste Genauigkeit über die lange Lebensdauer der Maschine aufrechtzuerhalten.“
Die standardmäßige powerMASTER-Spindel mit 50er Konus hat 12.000 U/min mit einer optionalen High-Speed-Version mit 16.000 U/min. Der NHX 6300 verfügt außerdem über eine optionale Spindel mit hohem Drehmoment und 8.000 U/min, die für die Hochleistungszerspanung von schwer zu bearbeitenden Metallen wie exotischen Materialien und schwerem Gusseisen erhältlich ist.
Die Steuerungsschnittstelle CELOS von DMG Mori bietet eine Auswahl an Anwendungen zur Prozessoptimierung. Ganz im Sinne von Industrie 4.0-Initiativen vereinfacht und beschleunigt die CELOS-Steuerungsschnittstelle alle Schritte der Teilebearbeitung, von der Idee bis zum fertigen Produkt, sowohl von der Fertigung von Einzelteilen bis hin zur Serienfertigung.
CELOS Apps ermöglichen die durchgängige Verwaltung, Dokumentation und Visualisierung von Auftrags-, Prozess- und Maschinendaten sowie die Verknüpfung von Werkstatt- und übergeordneten Unternehmensstrukturen und schaffen so die Basis für eine durchgängig digitalisierte und papierlose Produktion, so DMG Mori. Mit der CELOS PC-Version ist diese Funktionalität sogar von einem Bürorechner aus erreichbar.
„Wir bieten auch Technologiezyklen an, die es unseren Kunden ermöglichen, komplexe Bearbeitungsprozesse einfach zu realisieren“, sagte McDonald. „Zum Beispiel ermöglicht Machine Vibration Control (MVC) dem Bediener, stabile Schnittvorschübe und -geschwindigkeiten während der Schwerzerspanung zu finden. Machine Protection Control (MPC) hingegen bietet Spindelschwingungsüberwachung, Werkzeuglastüberwachung und Kollisionserkennung, um Schäden zu verhindern oder zu reduzieren. Durch das Sammeln und Analysieren dieser Daten hilft die CELOS-Steuerungsschnittstelle
Werkstätten dabei, ihre Produktivität zu maximieren, eine noch höhere Genauigkeit zu erreichen und die Spindeln mehr Stunden am Tag laufen zu lassen“, sagte McDonald.
Fähigkeit im Bauwesen
Die horizontalen Bearbeitungszentren von Okuma, wie das MA-600HII, sind laut Errol Burrell, Produktspezialist für Bearbeitungszentren, Okuma America Corp., Charlotte, N.C., eine beliebte Wahl für die Automobil-, Formenbau-, Energie- und Luft- und Raumfahrtindustrie.
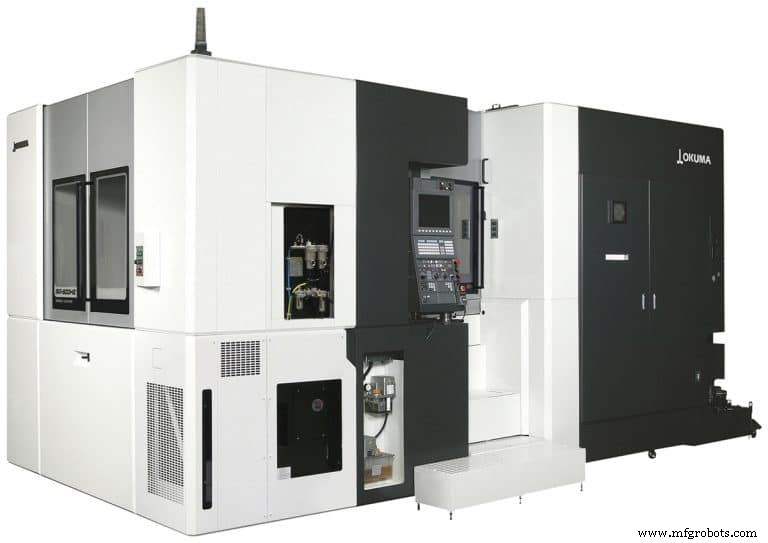
„Aufgrund ihrer konstanten thermischen Stabilität liefern sie Genauigkeit und Stabilität bei der Bearbeitung großer Teile“, sagte er. „Maschinen werden auf ihr thermisches Profil getestet und Daten über mögliche thermische Verformungen werden in Echtzeit in die Steuerung zurückgemeldet, um eine eventuell erforderliche Kompensation durch die TAS-Software (Thermal Axis Stabilizer) von Okuma zu ermöglichen.“
Die MA-600HII ist eine 50-Kegel-Maschine mit einer 6.000-U/min-Spindel und einem Standardmagazin für 40 Werkzeuge, das auf 60 Werkzeuge und sogar auf 285 oder 400 Werkzeuge aufgerüstet werden kann, sodass sie sich ideal für Auftragsfertigung oder Produktionsfertigung eignet . Der MB-8000H ist praktisch die gleiche Plattform mit einem 800-mm-Tisch, und die nächstgrößere ist der MB-10000H mit einem Box-in-Box-Design anstelle einer Säule.
Okuma-Maschinen werden auf jeder Passfläche von Hand geschabt, um die Genauigkeit und Produktivität über einen längeren Zeitraum zu erhöhen, um Kosten zu senken und maximale Rentabilität zu erzielen, sagte Burrell.
Typische Ölfeldkomponenten wie Pumpengehäuse profitieren von der einzigartigen Turn-Cut-Fähigkeit von Okuma. „Bei Pumpengehäusen ermöglicht unsere Turn-Cut-Fähigkeit das Drehen eines Flansches auf horizontalen Okuma-Bearbeitungszentren“, sagte Burrell. Turn-Cut ist eine auf Okuma HMCs verfügbare Programmieroption, mit der die Maschine Bohrungen und Durchmesser mit kreisförmigen und/oder eckigen Merkmalen erstellen kann. Dadurch können Benutzer Merkmale an großen, unausgeglichenen Teilen auf derselben Plattform drehen, auf der Standard-CNC-Bearbeitungsfunktionen ausgeführt werden. Turn-Cut macht den Kauf von Spezialmaschinen, Werkzeugen, Vorrichtungen oder Zusatzkomponenten überflüssig.
Turn-Cut hat keinen Einfluss auf die Leistung oder Langlebigkeit der Maschinen. Wenn schweres Fräsen erforderlich ist, ist die mit Turn-Cut ausgestattete Okuma HMC laut Okuma immer noch so leistungsfähig wie eh und je. Am wichtigsten ist, dass Turn-Cut Bearbeitungsarbeiten ermöglicht, ohne dass eine Sekundärmaschine für eine Drehanwendung verwendet werden muss. Teile wie Ventile, Rohre oder verteilerartige Teile sind ideale Kandidaten für Turn-Cut.
Auf der IMTS präsentierte Okuma sein automatisches vertikales Palettensystem Tower Pallet. Er lagert auf zwei Ebenen zwölf 20 x 20″ (500 x 500 mm) große Paletten mit einer maximalen Tragfähigkeit von jeweils 500 kg (1.100 lb). Das integrierte APC-System liefert kurze Lade-/Entladezeiten mit einem servomotorgetriebenen Schwenksystem für den Betrieb ohne Licht, so das Unternehmen.
Volle vierte Achse, Automatisierung
Mazak Corp., Florence, Kentucky, bietet eine vollständige Reihe von HMCs zusätzlich zu seinen großen vertikalen Bearbeitungszentren in Brückenbauweise, vertikalen Fünf-Achsen-Bearbeitungszentren mit Drehen (INTEGREX) und seiner VARIAXIS-5-Achsen-Trunnion-Style-Maschine, je nach Produkt Spezialist Jared Leick.
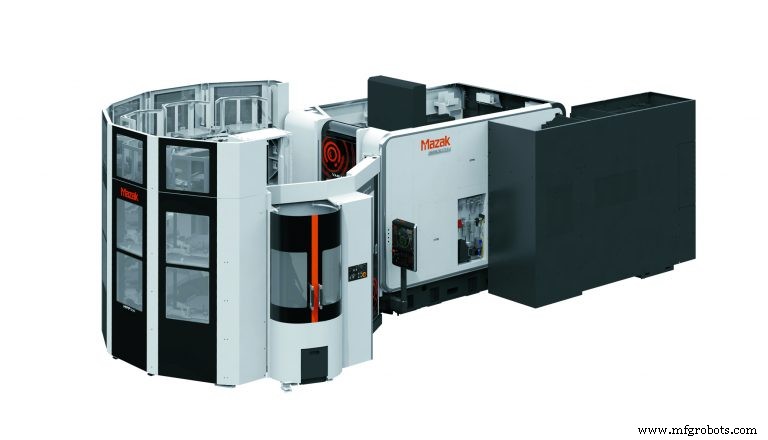
„Die Bearbeitung großer Teile mit 50-Kegel-Spindeln erfolgt auf Maschinen mit Tischen/Paletten von 800 bis 1.600 mm, einschließlich unserer Quill-Serie HMC mit Tischen von 1.250 bis 1.600 mm sowie unserer HCN-6800 mit einem 630-mm-Tisch für große Motorblöcke für Automobil- und Energiekomponenten.“
Die 50-Kegel-Linie umfasst drei zusätzliche Modelle in der Serie (HCN-8800, HCN-10800 und HCN-12800) mit 10.000 U/min Standard- und optionalen 8.000 U/min und 6.000 U/min 50-PS-Spindeln für die Bearbeitung von rostfreiem Titan mit höherem Drehmoment und andere exotische Metalle. Für die Bearbeitung großer Aluminiumbauteile für die Luft- und Raumfahrt und die Halbleiterindustrie ist eine Spindel mit 16.000 U/min verfügbar, sagte Leick.
Mazak bietet vollständige vierachsige HMCs an, die etwa 60 % aller vom Unternehmen verkauften HMCs ausmachen, sagte er. Vierachsige HMCs mit einer Standardpositionierung von 0,0001o ermöglichen das Drehen einer zwei- oder vierseitigen Vorrichtung zum Bohren von Verbundwinkeln, das Indexieren um 90o und das Zurückdrehen. Der vollständige Vier-Achsen-Betrieb ermöglicht das Konturieren und kann verwendet werden, um die Zykluszeit zu verkürzen und die Verarbeitung zu vereinfachen, insbesondere bei komplexen Teilen.
Die verfügbare Automatisierung umfasst das PALLETECH-System von Mazak, das eine große Anzahl von Maschinen in einer FMS-Konfiguration und einen schienengeführten Roboter aufnehmen kann, sowie Mazaks neues Multi-Paletten-Pool (MPP)-Einzelmaschinen-Automatisierungssystem für 400- und 500-mm-Maschinen. „Wir haben HMCs mit sechsachsigen FANUC-Robotern auf einer Schiene automatisiert, die Teile in verschiedenen Stationen zum Lasermarkieren, Waschen und Entgraten positioniert“, sagte Leick.
Die Mazak HCN-5000 HMC ist jetzt mit dem MPP-System des Unternehmens erhältlich, einer einfachen Automatisierungslösung in kompakter Bauweise. Laut Leick haben Geschäfte, denen die für die Unterbringung eines herkömmlichen linearen horizontalen Palettenlagers erforderliche Bodenfläche fehlt, jetzt die Möglichkeit, für eine kontinuierliche Produktion zu automatisieren.
MPP bietet den Komfort eines größeren Mazak PALLETECH-Systems und benötigt dabei bis zu 30 % weniger Platz. Servomotoren an jeder Achse sowie eine Palettenanordnung auf zwei Ebenen, die jede Palette im gleichen Abstand von der Mitte des Lagers hält, gewährleisten ein schnelles und stabiles Be- und Entladen, sagte er.
Hersteller können den standardmäßigen 10-Paletten-Stapler des Systems so umkonfigurieren, dass er 16 Paletten aufnehmen kann, um die Leistung zu erhöhen. Unter Berücksichtigung der großen, schweren Teileoperationen der HCN-5000 hat Mazak diese neueste MPP zu ihrer größten Version in Bezug auf die Kapazität der Teilegröße gemacht. Das System nimmt 500 mm² große Paletten auf, die Werkstücke mit einem Durchmesser von bis zu 800 mm und einer Höhe von 1.000 mm aufnehmen können.
Automatisierungssteuerung System
- Video zum horizontalen Bearbeitungszentrum
- Verschiedene Arten der CNC-Bearbeitung
- Vielfalt der Werkzeugmaschinenautomatisierung auf der Ausstellung
- Unterricht in Hochleistungsbearbeitung:Werkzeughalter nicht vergessen
- Niagara Gear fügt interne Bearbeitungskapazitäten hinzu
- Auftragseingänge für Werkzeugmaschinen gehen im September zurück
- Fuji stellt Multitasking-Maschine vor
- Methods Machine Tools zur Übernahme von Koch Machine Tool
- Was ist eine Horizontalbohrmaschine?
- Bearbeitungsprozess und Werkzeugmaschine verstehen