Streben Sie nach Leistung ohne Ausfallzeiten, indem Sie „das Blut der Maschine testen“
Mitte der 2000er Jahre stürzte das Druckluftsystem im Werk von Toyota North America in Georgetown, KY, durchschnittlich mehr als einmal im Jahr ab. Das veranlasste einige im Werk zu der Frage, ob die Nutzung von maschinellem Lernen und KI dieses Problem lösen könnte, indem Anomalien erkannt, Fehler identifiziert und vor allem bevorstehende Ausfälle vorhergesagt werden, bevor sie auftreten.
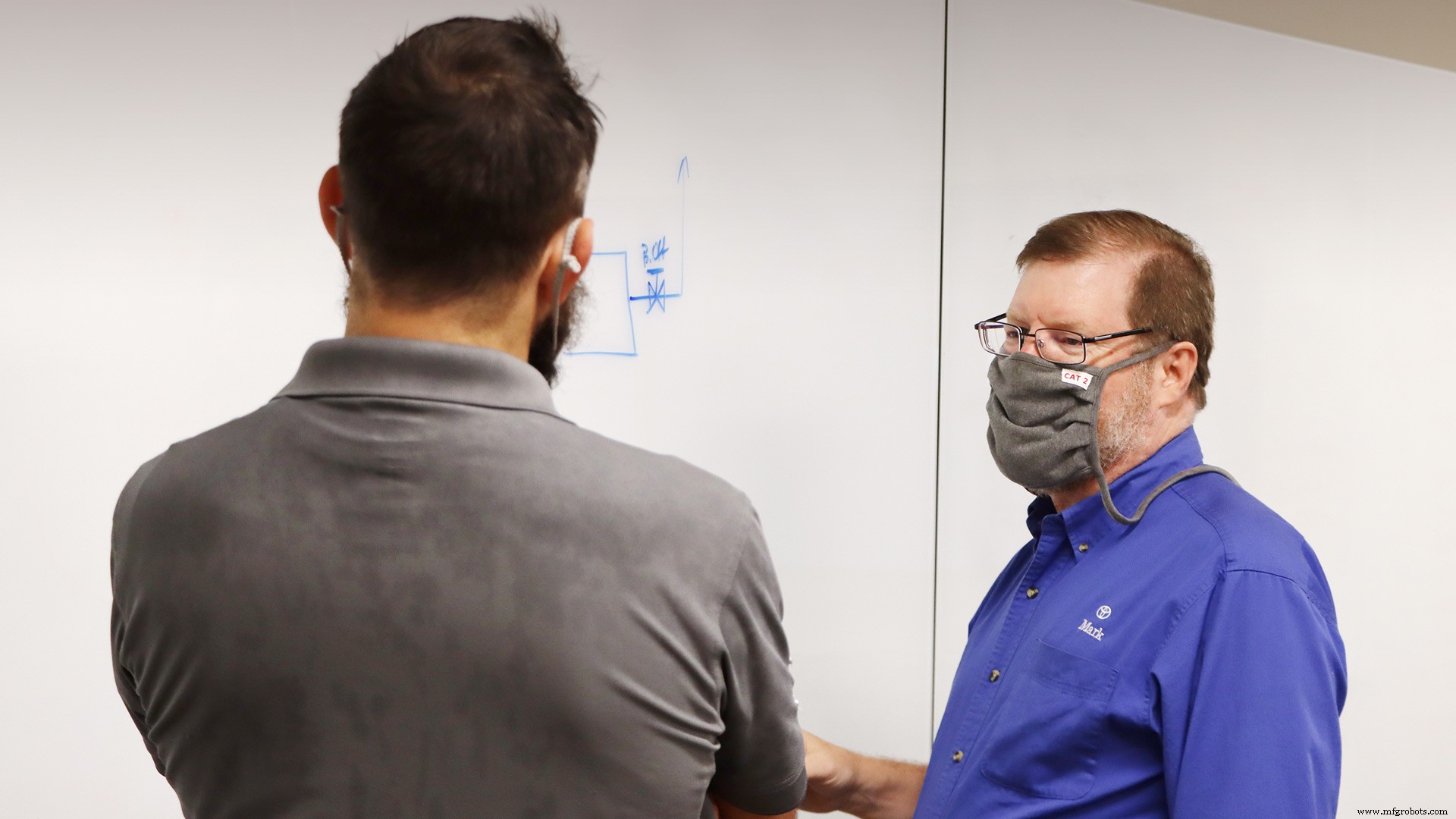
Ein ungeplanter Ausfall der Druckluftanlage bedeutete natürlich, dass die gesamte Fabrik ein Problem hatte. Die Lackiererei verwendete Druckluft, um neue Fahrzeuge zu sprühen. Das System erweckte Druckluftwerkzeuge zum Leben und nichts im Vergleich zu Druckluft zum Abblasen von Sand und anderen Rückständen.
Da während zwei Schichten alle 25 Sekunden ein fertiges Fahrzeug von einem der drei Bänder des Werks rollt, waren die Folgen erheblich, wenn die Druckluftversorgung ausfiel.
„Die Kosten, wenn die Leitung ausfällt, sind enorm“, sagte Mark Rucker, Projektmanager und Fachexperte für Elektrotechnik im Werk. „Es gibt also einen guten Anreiz, einen guten, zuverlässigen und stabilen Nutzen zu haben.“
Das mehrere Millionen Dollar teure Druckluftsystem besteht aus einem Dutzend Zentrifugal-Luftkompressoren von Ingersoll Rand, jeder so groß wie ein kleiner Sattelzug. Die Endstufenschaufeln jedes Kompressors rotieren mit 20.000 U/min einen Bruchteil eines Zolls von ihrem Gehäuse entfernt. Wenn eine Klinge auch nur geringfügig außerhalb der Spezifikation arbeitet und das Gehäuse berührt, ist sie weg. Die gesamte Maschine muss für etwa 100.000 $ neu aufgebaut werden.
Das Wackeln der Klinge ist jedoch nicht die Ursache für einen Absturz; es ist das Ergebnis.
Der Absturz – a.k.a. ein Schwall oder Rückfluss – tritt auf, wenn etwas dazu führt, dass der normale Luftstrom vom Kompressor zu einem Rohr versucht, sich umzukehren, und die Luft im Rohr zurückgedrückt wird.
Die Häufigkeit, Kosten und Folgen von Unfällen veranlassten Toyota, Jay Lee, den Gründungsdirektor von Intelligent Maintenance Systems, um Hilfe zu bitten.
Jay Lee war der Industrie-4.0-Kurve voraus
Zu Beginn des neuen Jahrtausends, vor dem Ruf von Toyota, war Lee Ingenieurprofessor an der University of Cincinnati, der sich vorstellte, dass alle Maschinen in einer Fabrik vernetzt sind und Daten für eine intelligente Wartung bereitstellen. Zu dieser Zeit existierte jedoch ein Großteil der Technologie, die erforderlich war, um Lees Vision Wirklichkeit werden zu lassen, noch nicht.
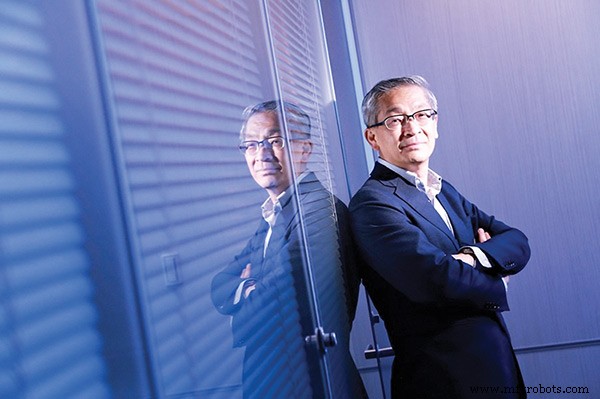
„Vor zwanzig Jahren glaubten nur sehr wenige Menschen, dass dies möglich ist“, sagte Lee, der derzeit vom Unterricht beurlaubt und stellvertretender Vorsitzender und Vorstandsmitglied der Foxconn Technology Group in Wisconsin ist.
In seiner industriellen Vision sind Maschinen wie Patienten und Daten, die von Sensoren gesammelt werden, die Maschinen überwachen, geben Aufschluss über ihre Gesundheit. Experten leiten Prognosen ab, indem sie die von ihnen gesammelten und analysierten Daten interpretieren.
„Ich sagte:‚Warum nicht das Blut der Maschine testen?‘ Und was ist das Blut der Maschine?“ sagte Lee. "Daten. Die Frage lautet:„Welche Daten möchten Sie erhalten?“ Das hängt davon ab, was Sie analysieren möchten. Wir müssen den Kontext und Inhalt verstehen und weiter ein Beziehungsmodell zwischen den unsichtbaren Unbekannten formulieren.“
Versteckt in den Daten ist eine Aussage über abweichendes Verhalten einer Maschine oder eines Prozesses. Die Erschließung dieser Bedeutung führt zur Vorhersage der Qualität, zur Bestimmung der Stabilität der Maschine oder des Prozesses und zur Vermeidung potenzieller Ausfälle. „Genau darum geht es heute bei Industrie 4.0“, sagte Lee.
Der Begriff „Industrie 4.0“ wurde natürlich erst etwa zur Zeit der Initiative der Bundesregierung im Jahr 2013 populär.
Keine Abstürze seit 2006
Bei Toyota schlossen sich Lee und sein Team von Datenanalysten mit Rucker und einer Gruppe qualifizierter Wartungsarbeiter und Anlageningenieure zusammen, um das Problem mit dem Druckluftsystem anzugehen.
Die Einfachheit ihrer Fragen strafte die Komplexität der bevorstehenden Aufgabe Lügen.
„Können wir ein Reverse-Flow-Problem vorhersagen, bevor es einen Absturz verursacht?“ sagte Rücker. „Können wir sehen, dass sich rechtzeitig etwas entwickelt, um etwas dagegen zu unternehmen?“
Durch monatelanges Ausprobieren im Jahr 2005 sammelte und analysierte das Team High-Fidelity-Daten von einem der Kompressoren und suchte nach Anomalien. Manchmal erstellte das Team einen Anstiegs- oder Annäherungszustand, um die Maschine dazu zu zwingen, ein abweichendes Verhalten zu zeigen, und zu sehen, wie das im Datensatz aussah.
Am Ende zahlte sich die Arbeit des Teams aus. Seine Mitglieder sahen den besten Prädiktor für einen beginnenden Pumpzustand in Stufe zwei (von den vier Stufen, die der Kompressor durchläuft, wenn der Fortschritt von Normaldruck auf 120 Pfund Druck pro Quadratzoll oder PSI erfolgt).
„Was ist die Physik dahinter, warum ist das der Prädiktor?“ sagte Rücker. „Keine Ahnung, egal. Wir haben gerade gesehen, dass dies zuverlässig einen zukünftigen Anstieg vorhersagt, und es sagt es mit Sekunden der Warnung voraus.“
Der nächste Schritt bestand darin, an jedem Kompressor einen Differentialsensor anzubringen und einen maschinellen Lernalgorithmus für die zentrale Steuereinheit zu erstellen. Tests bestätigten, dass der Kompressor anfing, sich zurückzuziehen, sobald die zweite Stufe zu „wackeln“ begann.
„Jedes Mal, wenn wir es getestet haben, hat es uns vor Ärger bewahrt“, sagte er. "Seit 2006 hatten wir keine Abstürze mehr."
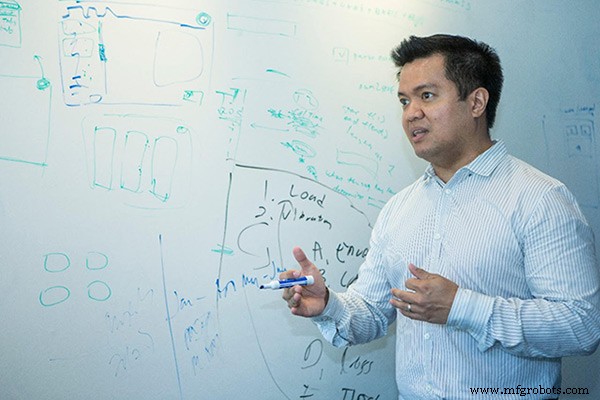
Während das Kompressor-Surge-Projekt ein Erfolg war, schlug ein anderes Projekt fehl, das sich darauf konzentrierte, die Lebensdauer von Lagern in den Druckluft-Giganten vorherzusagen. Das Team konnte nicht genügend zuverlässige Wartungsdaten finden und sie mit Betriebsdaten der Maschinen koppeln, um nützliche Korrelationen herzustellen, sagte Rucker.
„Das ist wahrscheinlich die richtige Mischung aus Forschung und Entwicklung“, sagte er. „Du probierst Dinge aus und weißt nicht, ob es funktionieren wird oder nicht. Und wenn Sie in der Hälfte der Fälle Ihr Geld zurückbekommen, ist das ein Gewinn. Und hin und wieder findet man einen, der für alles andere bezahlt – wie zum Beispiel den Überspannungsschutz.“
Flexibilität ist der Schlüssel
Anschließend veröffentlichte Lee eine Abhandlung über das Toyota-Projekt und half 2013 bei der Gründung von Predictronics mit Patrick Brown, einem Mitarbeiter von Intelligent Maintenance Systems, und zwei seiner Universitätsstudenten, David Siegel und Edzel Lapira. Braun. Lapira und Siegel bilden die Predictronics C-Suite.
So wie Toyotas Rucker Lee um KI-Hilfe bat, wenden sich Unternehmen an Predictronics, um Hilfe bei ihren Bestrebungen nach null Ausfallzeiten zu erhalten.
„Unterschiedliche Kunden haben normalerweise unterschiedliche Reifegrade“, sagte Lapira, der CEO ist. „Wir haben einige Kunden, die bereits über eine Datenerfassungsstruktur verfügen:Sie haben einen Data Lake, wissen aber nicht, was sie mit den Daten anfangen sollen. Wir haben auch einige Kunden, die bei null anfangen müssen.“
Kunden mit 50 oder 60 Jahre alten Vermögenswerten müssen noch früher ansetzen.
Predictronics wird zunehmend von Kunden mit älteren Maschinen angesprochen. Lapira und seine Kollegen schicken sie zum Einkaufen von Komponenten wie Beschleunigungsmessern und Wandlern.
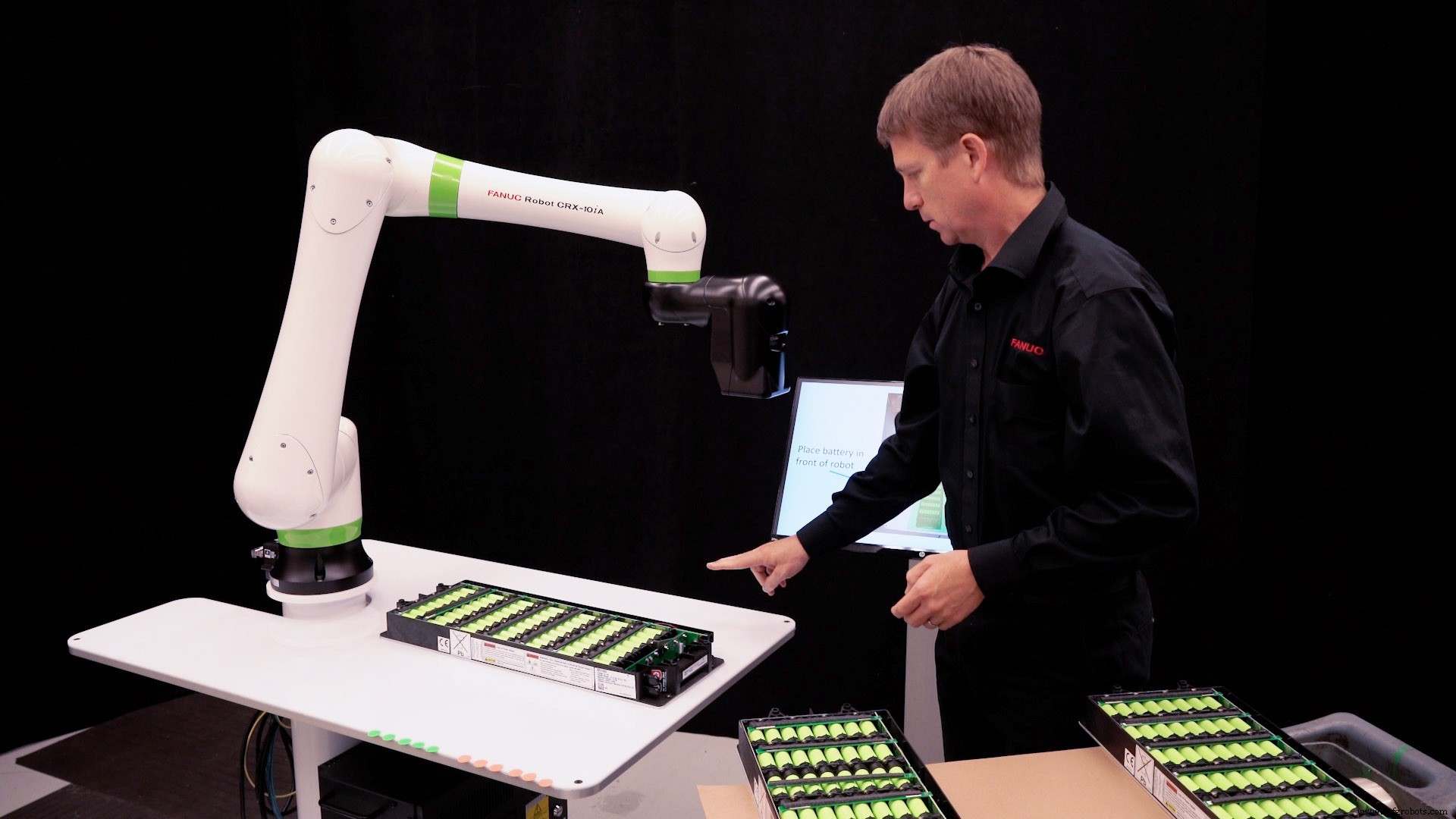
„Das sind die verschiedenen Analog-Digital-Wandler, die wir brauchen, um diese Daten herauszubekommen“, sagte er.
Seit seiner Gründung im Jahr 2013 hat Predictronics mehr als 70 Fabriken mit KI-Lösungen geholfen, darunter viele Fortune-500-Unternehmen.
Predictronics arbeitete mit einem Kunden, einem Halbleiterhersteller, zusammen, um eine Vorhersagelösung für die virtuelle Metrologie zu entwickeln, die in der Lage war, die Beziehung zwischen Sensor und Messvariablen zu lernen.
Das Projekt war aufgrund der Hunderte von gemessenen Signalen, die von der Halbleiterausrüstung abgeworfen wurden, eine Herausforderung.
Aber es gibt bekannte statistische Methoden, um die Zahl der Möglichkeiten einzugrenzen, sagte Siegel.
„Zusätzlich zu diesen Methoden hat in den letzten Jahren eher die Gemeinschaft des maschinellen Lernens Methoden entwickelt, die einen Klassifikationsregressionsalgorithmus enthalten, der einen eingebauten Teil zur Variablenauswahl enthält“, sagte er. „Das grenzt es also auf die Top 10 oder 20 oder 30 Variablen ein. Dann arbeiten Sie mit dem Kunden zusammen oder verwenden Ihr eigenes Wissen, um zu bestimmen, was am sinnvollsten in die Software und das Analysemodell aufgenommen werden kann.“
Ob Predictronics das aus früheren Erfahrungen gewonnene Wissen in seinem vorlagenbasierten Ansatz anwendet, der hilft, die Kosten niedrig zu halten, oder eine Lösung, die in einem Teil eines Unternehmens formuliert wird und dann intern skaliert werden kann, „um eine Lösung zu finden, die direkt die kritischsten anspricht Probleme, aber auch flexibel genug ist, um auf andere Probleme angewendet zu werden, ist der Schlüssel“, sagte Brown.
Due-Diligence-KI
Fabriken, die sich nach einem Anbieter von KI-Lösungen umsehen, wie es Toyota für sein Druckluftproblem getan hat, sollten sorgfältig vorgehen, um genau das Richtige zu finden.
Es hilft, die richtigen Fragen zu kennen, sagten die Experten von Predictronics:
Wo wurden Ihre Dienste bisher genutzt?
Hat Ihre Lösung eine deutliche Verbesserung des Geschäftsbetriebs in Bezug auf reduzierte Ausfallzeiten oder gesteigerte Qualität gezeigt?
Wurde Ihre Lösung in meiner Branche eingesetzt?
Verfügt Ihr Team über Branchenkenntnisse?
Funktioniert Ihre Lösung mit älteren Geräten?
Funktioniert Ihre Lösung mit einer Vielzahl von Sensoren?
Verwendet Ihre Lösung maschinelles Lernen?
Wie viele Daten werden zum Trainieren des Modells benötigt?
Benötigt es nur Daten von einer gesunden Maschine oder auch Daten von einer heruntergekommenen oder fehlerhaften Maschine, um daraus zu lernen?
Roboter wollen auch KI
Während die Werkzeugmaschinen in einer Werkstatt unter dem Einfluss von KI besser funktionieren, gibt es keinen Grund, warum Roboter das nicht auch können.
Fanuc America hat kürzlich „AI Error Proofing“ zu seiner Robotersteuerung und der Vision-Funktion des Roboters, iRVision, hinzugefügt, die maschinelles Lernen (ML) für die Teileinspektion verwendet.
Mit der Fehlervermeidungsfunktion verwendet ein Bediener Bilder, um das ML zu trainieren, auf zwei unterschiedliche Situationen zu prüfen – ob beispielsweise eine geschweißte Mutter vorhanden oder nicht vorhanden ist – und ein Teil zu akzeptieren oder abzulehnen.
Da iRVision bis zu 27 Kameras unterstützen kann, kann die Fehlervermeidungsfunktion an beliebig vielen Stellen im Herstellungsprozess eingesetzt werden.
„Sie möchten Ausschuss oder Fehler identifizieren, bevor Sie einem schlechten Teil weiter Wert hinzufügen“, sagt Josh Person, Staff Engineer in der Machine Vision Group von Fanuc.
„Oft kann man einen Fehler in einer Phase sehen und die nächste Phase würde ihn vertuschen“, fügte er hinzu.
Während der Einrichtung kann der Bediener mehrere Beispiele von Werkstücken präsentieren und sie in zwei Kategorien einteilen – gut und schlecht. Wenn das Beispiel in keine der beiden Klassen fällt, wird „unbestimmt“ ausgegeben. Unbestimmte Beispiele können dann hinzugefügt werden, um das erlernte Modell zu verbessern.
Automatisierungssteuerung System
- SICHT:Für Blinde
- Bewertung der Vorteile von DevOps für IoT-Leistungstests
- Automatisierung:Was sie für die Zukunft des Geschäfts bedeutet
- Die Zukunft der kontaktlosen Lieferung
- Danke für die Erinnerungen!
- Die Vorteile der Automatisierung für Ihr Unternehmen
- So wählen Sie den richtigen Filter für Ihre Anwendung aus
- Fünf Wege, um den richtigen Kompressor für den Heimbastler zu finden
- Richtlinien für die Auswahl des richtigen Druckluftdienstleisters
- Begrüßung von Dorothy Parnell als Blog-Autorin für The Compressed Air Blog