Schwierigkeiten beim Transportdesign
Die Fahrzeugelektronik ist ein wichtiger Aspekt des Transportdesigns. Busse, Lastwagen, Motorräder und natürlich Autos haben alle mehrere Komponenten, die gleichzeitig interagieren, um Daten und Strom in jedem Fahrzeug bereitzustellen. Moderne Fahrzeuge verwenden Echtzeitdaten, um sie zu bedienen und ordnungsgemäß auszuführen. Zu diesen Systemen gehören Lenkung, Bremsung, HVAC, Motormanagement und vieles mehr. Die Entwicklung dieser Systeme erfordert viel Liebe zum Detail, da viele Entwickler gleichzeitige Konstruktionsformen haben, die es erfordern, dass mehrere Parteien die Komponenten separat entwickeln und herstellen. Lassen Sie uns einen Blick auf einige der Operationen werfen, mit denen sich ein Automobilingenieur beim Einrichten und Entwerfen der elektronischen Bestückung auseinandersetzen muss, und wie dies verbessert werden kann.
Übersicht über Elektronik innen und außen
Das externe elektrische Fahrzeugsystem bezieht sich im Allgemeinen auf zwei Arten. Es gibt Systeme für die Funktionalität und solche für die Sicherheit. Funktionssysteme sind solche, die es dem Fahrzeug ermöglichen, während der Fahrt richtig zu laufen.
Zündanlage (Zündspule, Spulenpakete, Zündkerzen und Kabel)
Motormanagement (Kraftstoffeinspritzung, Kühlsystem, Drosselklappensteuerung usw.)
Getriebeelektronik (automatische Gangschaltung)
Fahrwerkselektronik ( ABS, ASR, EBD, ESP)
Fahrerassistenz-Elektronik (Wischer, verstellbarer Spiegel, Blinklicht)
Moderne Fahrzeuge haben einen Sensor für alles, vom Reifendruck in Ihren Rädern bis zur Spannung in Ihrer Batterie. Interne Elektronik dient normalerweise dem Fahrgastkomfort, der Fahrunterstützung und zu Unterhaltungszwecken. Das Radio, die HVAC-Bedienelemente, das Armaturenbrett und die Fahrerbedienelemente sind alle in dieser Kategorie enthalten. Wenn jemand ein Fahrzeug gefahren ist, sind diese Komponenten bekannt. Die kurze Geschichte ist, dass das Zeitalter der mechanischen Systeme zu einem fernen Märchen heranwächst und moderne Fahrzeuge viel Wirkung erfordern, damit diese elektronischen Systeme richtig funktionieren. Werfen wir einen Blick auf einige der Probleme, mit denen Ingenieure und Hersteller konfrontiert sind, wenn sie diese Geräte miteinander verbinden.
Begrenzter Platz und Spielraum
Mit der Zunahme kraftstoffsparender Fahrzeuge besteht ein Bedarf an leichten Fahrzeugen mit hohem Benzinverbrauch. Unternehmen werden immer wettbewerbsfähiger, wenn es darum geht, leichte Fahrzeuge zu haben, die einen minimalen Kraftstoffbedarf benötigen. Dies bedeutet in der Regel, dass Komponenten und Fahrzeugstrukturen kompakter werden und der interne Stauraum für die Komponentenbestückung begrenzt wird.
Elektronische Systeme werden entweder basierend auf einem Standardstandort (Lichter, Scheibenwischer) oder der Verfügbarkeit eines Standorts (Batterien und Relaisboxen) platziert. Diese Systeme müssen gleichzeitig oder unabhängig arbeiten und sind mit anderen über eine gemeinsame Stromquelle verbunden. Es ist üblich, Kabel durch das gesamte Fahrzeug zu führen und kann sich für Elektroingenieure als eine Herausforderung erweisen.
Praktisch gesehen gibt es vier gängige Arten von Abstandsproblemen bei der Verkabelung.
Freigabe für die Installation
Freiraum für Verkabelung
Freigabe für den Betrieb
Servicefreigabe
Lassen Sie uns etwas tiefer auf die in modernen Fahrzeugen vorkommenden Freiräume und die Fragen eingehen, die bei der Konstruktion für sie gestellt werden müssen.
Freigabe für die Installation
Dies läuft auf eine Frage des Platzes hinaus. Gibt es genug Platz für die Komponente, wo Sie sie haben möchten? Gibt es Hindernisse? Können Türen, Motorhaube und andere bewegliche Körper über ihren vorgesehenen Bewegungsbereich störungsfrei funktionieren? Müssen die Komponenten vor oder nach einer anderen installiert werden, um Störungen bei der Installation zu vermeiden?
Freiraum für die Verkabelung
Können Sie nach der Installation der Komponente die dazugehörige Verkabelung erhalten? Ist genug Platz für die Kabelanschlüsse? Ist genügend Platz für die Wartung vorhanden? Ist nach dem Einbau der Stecker genügend Platz für den Kabelbaum? Ist Platz für Kabelbaumbiegungen?
Freigabe für den Betrieb
Wenn es sich bei der Komponente um einen Schalter oder Knopf handelt, können Sie diese von einer normalen Fahrposition aus erreichen? Wird eine benachbarte Komponente beim Versuch, eine solche Komponente zu betreiben, Störungen verursachen? Kann es bedient werden, wenn der Fahrer Handschuhe trägt? Beeinträchtigt der Betrieb von Komponenten andere?
Servicefreigabe
Wenn eine Komponente irgendwann ausfällt, kann sie ersetzt werden? Ist um das Bauteil herum Platz für Anpassungen? Gibt es Platz, um die Kabelstecker zu Testzwecken zu trennen?
Abfertigung muss berücksichtigt werden
Bei der Bestimmung der Position des Steckers und des Kabelbaums werden viele Überlegungen angestellt. Es ist wichtig, sicherzustellen, dass die Platzierung andere Designs nicht beeinträchtigt, ebenso wie die Funktionalität des Geräts. Wartungsfreundlichkeit, Wartung und persönliche Interaktion haben alle ihren richtigen Platz in der Komponentenposition.
Umweltbelastung
Fahrzeuge erzeugen große Wärmemengen und können Kabel und Komponenten beschädigen, wenn bei der Designplatzierung nicht vorsichtig vorgegangen wird. Dass ein Fahrzeug mit Hilfe des unter der Haube liegenden Motormanagements funktionieren muss, ist keine Neuigkeit. Sensoren für Bremsen, Aufhängung und Getriebe erfahren immense Bewegungen, die bei minimaler Belastung Kabel und Komponenten brechen können. Das Entwerfen von Systemen, die diese Szenarien berücksichtigen, ist entscheidend, um das System intakt zu halten.
Thermische Motorerzeugung
Die vom Motor erzeugte Wärme kann bei direktem Kontakt in Sekundenschnelle durch Isolierungen und Kunststoffstecker schmelzen. Die Temperatur eines Motors kann leicht die Schmelztemperatur von Kunststoffsteckern überschreiten. Die Auslegung der Komponentenplatzierung für einen sicheren Abstand zum Motor ist entscheidend, zumal der Verdrahtungsraum unter der Motorhaube begrenzt ist. Der Montageort für Steckverbinder muss fast in einem halbstatischen Zustand vorhanden sein. Wenn die Bewegung der Verkabelung durch an Komponenten oder Stellen installierte Befestigungsbinder eingeschränkt ist, an denen eine minimale Motorwärmeübertragung stattfindet.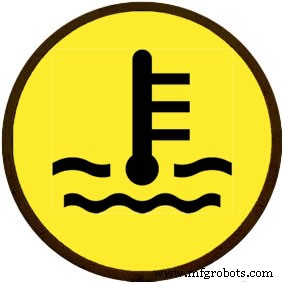
Komponentenfehler durch mechanische Bewegung
„Die Räder im Bus drehen sich und drehen sich“, dieser Satz ist keine einfache Zeile aus einem Kinderlied, sondern hat einen wahren Wert in der Drehbewegung, die von den Rädern des Fahrzeugs erzeugt wird. Sensoren werden in der Nähe oder innerhalb der Felge des Rades positioniert, um die Drehzahl zu bestimmen, die den Antrieb über die Fahrzeuggeschwindigkeit informiert. Diese kleinen zerbrechlichen Geräte müssen positioniert werden, um Kollisionen zu vermeiden und den Sensor zu beschädigen.
Dämpfungssystem war bisher rein mechanisch und funktionierte ohne elektronische Hilfe. Heute nutzen Feder-Dämpfer-Systeme dynamische Rückmeldungen von Straßenbedingungen, die die Fahrzeugsensoren überwachen und die Dämpfung basierend auf persönlichen Einstellungen und Fahrbedingungen ändern. Das Dämpfungssystem erfordert einen großen Federweg, damit sich die Komponenten und die Verkabelung bewegen können. Eine angemessene Kabellänge, Teileinterferenzen und ein hochwertiges Design sind erforderlich, um die Systemintegrität zu erhalten und beschädigte Komponenten zu vermeiden.
Wie können wir das für Ingenieure einfacher machen
Zuken ist führend auf dem Automobilmarkt, wenn es um die Entwicklung und Integration von Fahrzeugkomponenten von der Elektrotechnik bis zum Maschinenbau geht. E3.series ist eine Engineering-Plattform, die Funktionen bietet, die die beiden Disziplinen zu einem gemeinsamen Programm zusammenführen. Integrieren des mechanischen Designs von Fahrzeugen mit elektrischen Systemen, um ein Modell mit dem Besten aus beiden Welten zu produzieren. Der automatisierte Konstruktionsprozess hilft beim Konstruieren und Modellieren besserer Fahrzeuge. Konstruktionsprojekte enthalten Daten vom Schaltplan über die Kabelbaumerstellung bis hin zu Stücklisten und Produktionsformaten. Die sofortige objektorientierte Architektur stellt sicher, dass alle Designelemente, Attribute und Änderungen sofort in die Produktion übernommen werden.
E3.Kabeldesign und Dokumentation
E3.cable wird zum Entwerfen und Dokumentieren von Kabelplänen und Kabelbaumlayouts verwendet. Einzelne Leiter werden im Design miteinander kombiniert, um neue Kabel und Kabelbäume zu entwickeln. Abschirmungen und Twisted-Pair-Strukturen können den Kabeln hinzugefügt und automatisch in der Schaltplanerstellung gemeldet werden.
E3.3D Routing Bridge
Um das Beste im Showdesign zu erreichen, hat Zuken Verbindungen zwischen E3.series und allen großen MCAD-Anbietern (mechanisches CAD) entwickelt, die die Erstellung vollständig integrierter Designmodelle ermöglichen. Mit der E3.3D Routing Bridge können Schaltplan- und Verbindungsinformationen aus der E3.series an alle gängigen MCAD-Systeme angebunden werden. Funktionen einschließlich:
Komponenteninformationen an MCAD übertragen (Steckverbinder, Stifte, Spleiße)
Übertragen von Daten zu MCAD
Auf Kollisions- oder Kollisionserkennung in MCAD prüfen
Auf Drahtbiegeradius prüfen
Länge von Drähten und Segmenten in MCAD automatisch berechnen
Automatische Erstellung der Fertigungsdokumentation in E3.Formboard
Sie müssen Ihre aktuelle Volumenmodellierungsplattform nicht ändern, da sie leicht integriert werden kann mit:
CATIA V5
Solidworks
PTC Creo (Pro/Engineering)
Autodesk Inventor
Siemens NX
Solid Edge
NX I-deas
Das elektrische System von Fahrzeugen muss bei der Konstruktion und Entwicklung für die Fertigung eingehend berücksichtigt werden. Die Schritte, um die Vor- und Nachteile der Geräte- und Verdrahtungsplatzierung richtig zu verstehen, hilft bei der Bestimmung des zukünftigen Projekterfolgs. Es ist immer von Vorteil, die besten Werkzeuge für Ihre Ingenieure zur Verfügung zu haben, und die Entwicklung der besten Qualität für die Verbraucher ist immer das Hauptziel.
War das Verlegen von Kabeln durch Ihr Design mühsam? Geben Sie einen Kommentar zu den Problemen ein, mit denen Sie fertig werden mussten.
Industrietechnik
- Wahrscheinliche Fehler in unbewiesenen Systemen
- Zahlensysteme
- Stromsignalsysteme
- GE Transportation und Port of LA kommen zusammen, um diese Fracht zu verfolgen
- Ein kostengünstiges passives Kühlsystem, das keinen Strom benötigt
- Vorteile eingebetteter Technologien für modulares Design
- Die Sensorsysteme, mit denen ADAS funktioniert
- 4 Arten von Bestandskontrollsystemen:Fortlaufende vs. periodische Bestandskontrolle und die sie unterstützenden Bestandsverwaltungssysteme
- 6 Arten von Nieten, die Konstrukteure kennen müssen
- Informieren Sie sich über die Designfaktoren, die sich auf die Leiterplattendicke auswirken