Drehen mit gleichmäßiger Schnitttiefe:Warum ist es wichtig und wie funktioniert es?
Gleichmäßige Schnitttiefen:Warum ist das wichtig und wie funktioniert es?
Die Art und Weise, wie wir die Schnittiefe beim Profilschruppen berechnen, wurde neu hinzugefügt. Was tut es? Warum ist es wichtig? Und wie unterscheidet sie sich von der Standardstrategie?
Lassen Sie uns einen Blick darauf werfen, was wir heute tun, und es als „Konstante Schnitttiefe“ bezeichnen, weil wir der Software sagen, dass sie dies für uns tun soll.
Wenn wir unsere maximale Schnitttiefe auf 2 mm einstellen würden, würde dieser 2-mm-Schnitt von der Rohteilgrenze nach unten angewendet, wobei die tatsächliche Modellgeometrie ignoriert wird, Sie aber die erwarteten Ergebnisse erhalten, nämlich einen vorhersagbaren Stepdown für jeden Durchgang des Dreheinsatzes, bis wir ihn erreichen die untere Begrenzung (rotierter Mittelpunkt des Teils).
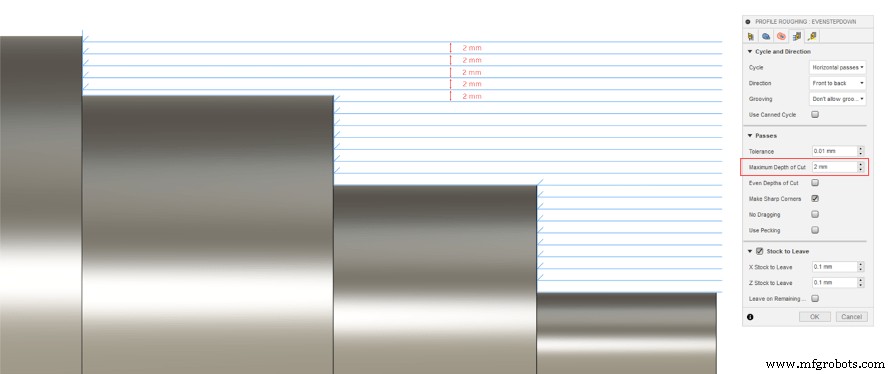
Eine maximale Schnitttiefe erzeugt hier unabhängig von der Teilegeometrie 2 mm Durchgänge.
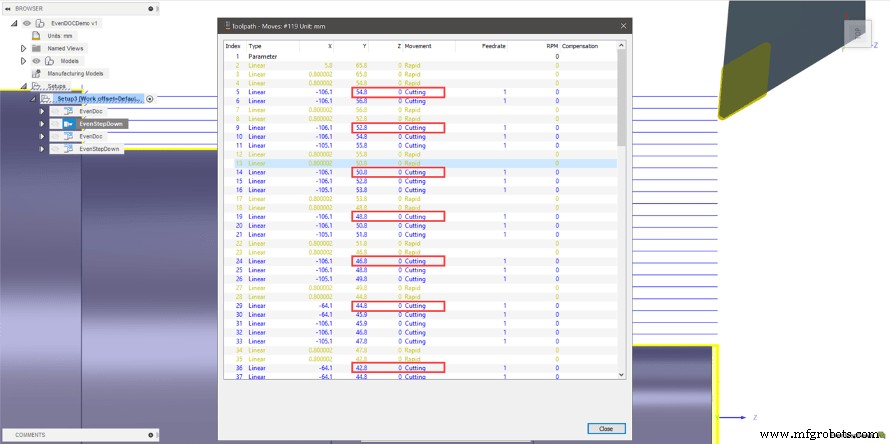
Beim Anzeigen der Werkzeugwegbewegungen wird jeder Durchgang bei 2 mm angezeigt.
Was ist das Problem?
Der hier hervorgehobene winzige Pass ist der Hauptschuldige.
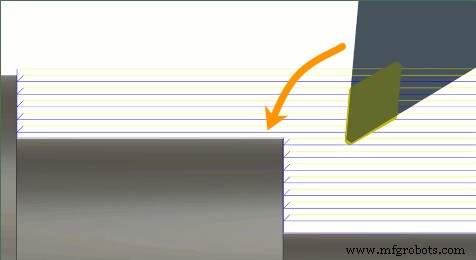
„Konstante Schnitttiefe“ auf mehreren Schultern
Was ist das Problem mit diesem kleinen Pass, fragen Sie sich vielleicht? Es ist einfach nicht die gleiche Schnitttiefe. Aber diese kleine Änderung sagt uns viele Probleme voraus, um später zu bestimmen, wie wir Korrekturen vornehmen können, um die richtige Toleranz und Oberflächengüte zu erhalten. Gleichmäßige Schnitttiefen bedeuten, dass wir eine gleichmäßige Spandicke, eine vorhersagbare Durchbiegung des Teils oder Werkzeugs und eine gleichmäßige Wärmeableitung während des Schnitts haben.
Warum ist es wichtig?
Die Variablen auf ein Minimum zu beschränken, ist immer das ideale Szenario. Die Minimierung von Variablen gewährleistet eine schnelle Diagnose eventuell auftretender Probleme. Wenn wir beispielsweise eine größere Werkzeugablenkung haben, während wir über mehrere Schultern hinweg denselben Betrag schneiden, können wir einfach unsere Werkzeugversätze in der Steuerung anpassen, um die Ablenkung für jeden Durchmesser zu berücksichtigen. Wenn wir eine konstante Schnitttiefe haben, die zu einem dünnen Endschruppgang an einer Schulter führt, die anderen beiden jedoch gleich sind, können wir Schwankungen im resultierenden Durchmesser haben, die einfach auf der Werkzeugablenkung basieren. Um nun ein Problem zu beheben, bei dem wir Variabilität haben, müssen wir zu Fusion zurückkehren, um die Abmessungen des einzelnen Durchmessers zu ändern, um ihn in die Toleranz zu bringen, ohne die anderen beiden Durchmesser zu stören.
Bei Teilen, die mehrere Schultern enthalten, wie in dem Beispiel, das wir uns ansehen, ist die ideale Methode zur Bearbeitung der Schnitttiefe möglicherweise nicht immer eine konstante vorgeschriebene Zahl. Der Benutzer kann unmöglich dafür verantwortlich gemacht werden, jeden Schulterdurchmesser zu messen und eine durchschnittliche Schnitttiefe von der Oberkante des Materials über das gesamte Teil zu berechnen.
Sogar Depths of Cut ist hier, um den Tag zu retten!
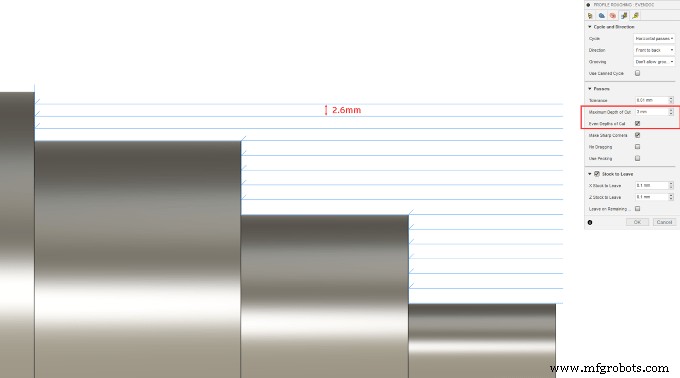
Eine auf 3 mm eingestellte „Maximale Schnitttiefe“ mit aktivierter „Gleichmäßiger Schnitttiefe“ erzeugte eine Tiefe von 2,6 mm, um ein besser vorhersagbares Ergebnis zu erzielen.
Also, wie funktioniert es?
Einfache Geometrie
Wir teilen jeden Durchmesser in eine „Region“ auf, um die richtige Abstufung jeder Region zu berechnen, und führen sie dann zu einem Durchschnitt zusammen, der sich gleichmäßig auf alle Breiten verteilt. Nachfolgend finden Sie zwei grundlegende Beispiele dafür, wie Bereiche im Algorithmus definiert werden, je nachdem, ob der Benutzer vertikale oder horizontale Durchgänge auswählt. Für diesen Fall haben wir der Software eine vorgeschlagene „maximale Schnitttiefe“ von 3 mm gegeben. 3 mm ist nicht die exakte Schnitttiefe, die für jeden Durchgang ausgegeben wird, wie bei einer konstanten Schnitttiefe, aber ein Wert, der nicht überschritten werden sollte. Der Algorithmus blickt nun auf das Modell voraus und teilt es basierend auf der Erkennung von Ebenen in Regionen auf und berechnet die Tiefe jedes Durchgangs, damit sie gleichmäßig verteilt sind. Das Ergebnis sind 2,6 mm für jeden Durchgang und eine vorhersagbare Schnittbedingung, die von Schulter zu Schulter konstant ist.
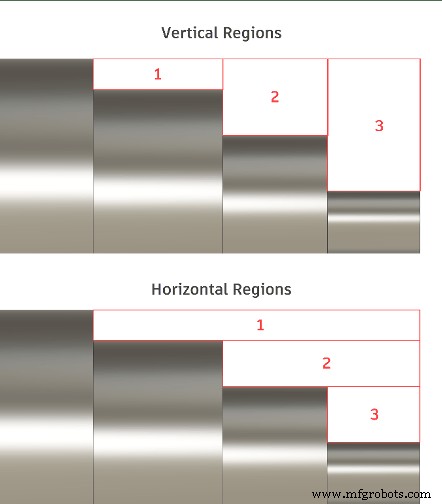
Vertikale und horizontale Bereiche, einfache Geometrie
Komplexe Geometrie
Aber was passiert, wenn die Teilegeometrie komplizierter ist? Dieses erste Beispiel einer komplexeren Geometrie zeigt, wo möglicherweise eine ungleichmäßige Schnitttiefe auftritt.
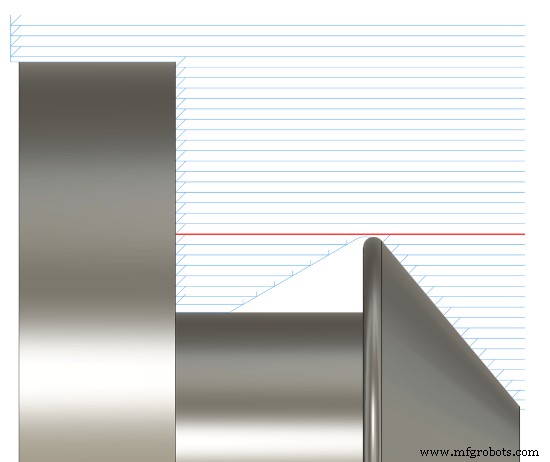
„Konstante Schnitttiefe“ auf komplexen Schnittpunkten zeigt einen dünnen Schnitt über dem Scheitel dieser Geometrie.
Da es keine einfache Möglichkeit gibt, Regionen basierend auf flachen Oberflächen zu identifizieren, wie definieren wir die Region, um diesen Teil aufzuteilen?
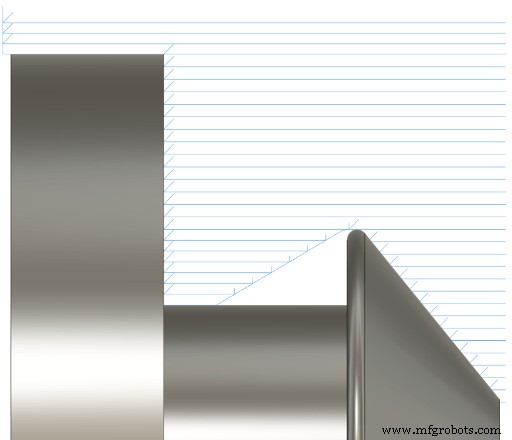
„Gleichmäßige Schnitttiefe“ auf der komplexen Kreuzung
Durch die Verwendung der Wendepunkte des Modells können wir die zu teilenden Bereiche bestimmen und die Schnitttiefe für komplexe Formen gleichmäßig berechnen.
Winkelige Gesichter
Der letzte Fall sind abgewinkelte Gesichter. In diesem Fall können wir uns ein NPT-Gewindebeispiel ansehen, das eine 5-Grad-Verjüngung zur Welle hat. Der Algorithmus betrachtet alles, was größer als 5 Grad ist, als Region; alles andere wird als nicht aufteilende Region betrachtet. Wie in der konischen Fläche unten.
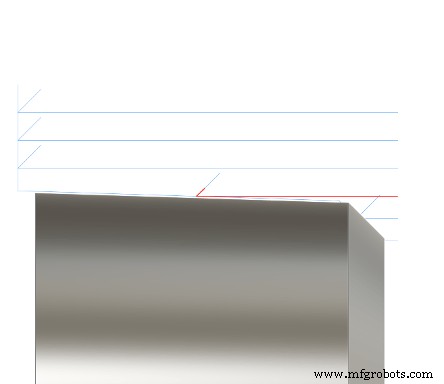
„Konstante Schnitttiefe“ auf <5 Grad konischer Oberfläche
Da es keine Ebene gibt, um die Region oder einen Wendepunkt zu bestimmen, können wir nicht eindeutig identifizieren, was eine richtige teilbare Region ist, um eine gleichmäßige Schnitttiefe zu erreichen. Tatsächlich können wir hier aufgrund der abgewinkelten Oberfläche überhaupt keine gleichmäßige Schnitttiefe erzielen. Aber um die kleine verbleibende Materialmenge zu eliminieren, können wir bestimmen, was das Minimum und das Maximum eines Bereichs für abgewinkelte Flächen sind. Aus diesem Grund haben wir für die Betrachtung von Regionen einen maximalen Winkel von 5 Grad eingebaut. Wenn der Winkel größer als 5 Grad ist, wird er nicht als „flacher“ Bereich betrachtet. Geben Sie uns unten die besten Ergebnisse.
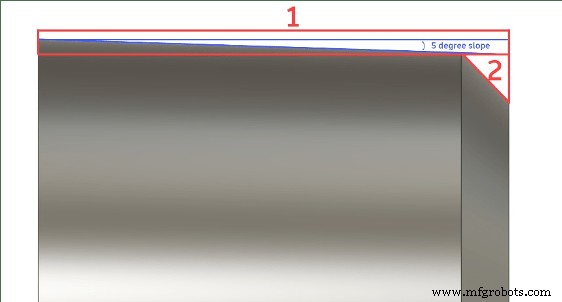
Regionen für>5-Grad-Neigung
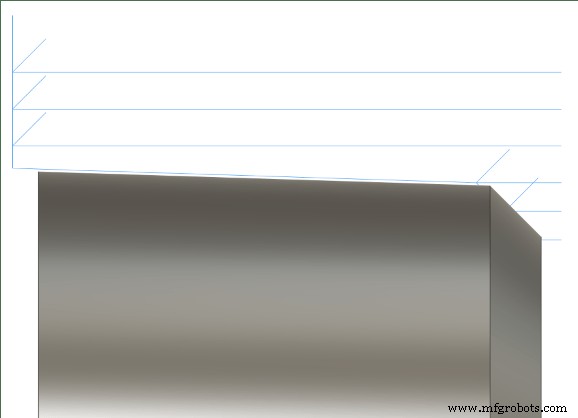
„Gleichmäßige Schnitttiefe“ auf konischer Oberfläche von>5 Grad
Was kommt als nächstes?
Wir begannen mit einer gleichmäßigen Schnitttiefe beim Schruppen des Außendurchmessers und des Innendurchmessers mit fast jeder Einstellungskombination mit Ausnahme einiger weniger:kein Schleppen, Rückschneiden und Restmaterialbearbeitung (Bearbeitung vom Guss).
Wir haben uns bei den Annahmen im Algorithmus einige Freiheiten genommen und möchten den Benutzern mehr Auswahlmöglichkeiten eröffnen. Beispielsweise ist die maximale Schnitttiefe die einzige Eingabe, was ist also die minimale Schnitttiefe? Derzeit handhaben wir es nach Region. Jede flache Region, die kleiner als die maximale Schnitttiefe ist, betrachten wir ebenfalls nicht als Region. Wir werden versuchen, ein minimales Schnitttiefenfeld zu öffnen, um diesen Wert besser zu kontrollieren.
Werfen Sie einen Blick auf diese neuen Fertigungstechniken. Sie verwenden Fusion 360 noch nicht, versuchen Sie es noch heute.
Industrietechnik
- Was ist eine Kniehebelpresse und wie funktioniert sie?
- Was ist Spritzpressen und wie funktioniert es?
- Was ist eine Übertragung und wie funktioniert sie?
- Was ist 3D-Druck? – Typen und wie funktioniert er?
- Was ist Lichtbogenschweißen? - Typen und wie funktioniert es
- Was ist ein Winkelmesser und wie funktioniert er?
- Was ist ein CNC-Bohrwerk und wie funktioniert es?
- Was ist eine Industriekupplung und wie funktioniert sie?
- Wie funktionieren Chatbots? | Warum ist es wichtig für Ihr Unternehmen | 2018
- Hydrauliksystemkomponenten:Wie sie funktionieren und warum sie wichtig sind