Etwas, das Sie nicht über Druckguss wissen
Druckguss ist ein Metallgussverfahren , dessen Charakteristik darin besteht, hohen Druck auf geschmolzenes Metall unter Verwendung eines Formhohlraums auszuüben. Und Formen werden normalerweise aus stärkeren Legierungen hergestellt. Das Verfahren ähnelt dem Spritzgießen. Um den Menschen ein umfassendes Verständnis des Druckgusses zu vermitteln, hat die Firma JTR organisiert und zusammengefasst, was Druckguss ist. Was ist der Prozess des Druckgießens? Was sind die Materialien des Druckgusses? Und andere Fragen, ich hoffe, Sie können den Begriff „Druckguss“ vollständig verstehen „.
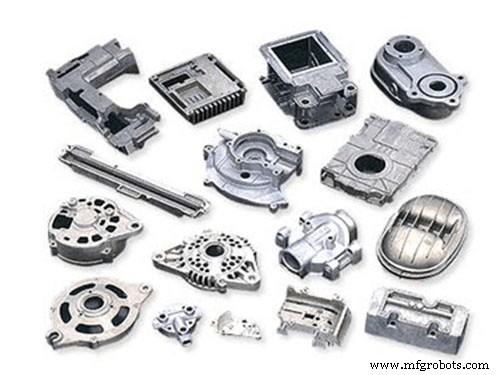
Definition von „Druckguss“
Druckguss ist eine Präzisionsgusstechnik, die hohe Spannungen nutzt, um geschmolzenes Metall in eine Metallform und Schimmel mit komplizierten Formen zu bringen. Durch Druckguss hergestellte Aufstriche werden als Druckguss bezeichnet.
Die meisten Druckgussteile sind eisenfrei, wie z. B. Zink-, Kupfer-, Aluminium-, Magnesium-, Blei-, Zinn- und Blei-Zinn-Legierungen sowie deren Legierungen. Je nach Druckgussart wird ein Kaltkammer-Druckgussgerät oder ein Warmkammer-Druckgussgerät benötigt.
Die Zugfestigkeit dieser Materialien ist fast doppelt so hoch wie die von gewöhnlichen Gusslegierungen, was eine positivere Bedeutung für Autoräder, Rahmen und andere Teile aus Aluminiumlegierungen hat, die voraussichtlich aus höherfesten und schlagfesten Materialien hergestellt werden.
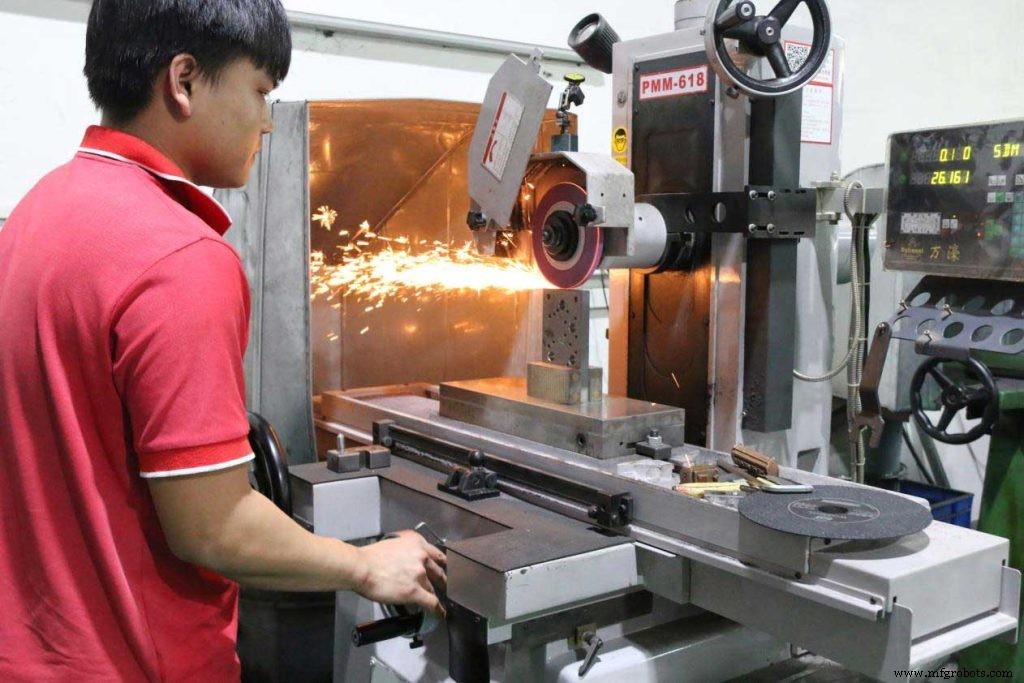
Druckgussverfahren
Der typische Druckgussprozess besteht hauptsächlich aus 4 Schritten oder Hochdruckguss. Diese vier Schritte, einschließlich Formvorbereitung, Materialfüllung, Einspritzen und Auspacken, sind auch die Grundlage für verschiedene kundenspezifische Druckgussverfahren.
Schmiermittel wird während des gesamten Vorbereitungsverfahrens in den Formhohlraum gesprüht. Das Schmiermittel kann nicht nur helfen, das Temperaturniveau der Form zu regulieren, sondern auch die Gussfreigabe unterstützen. Die Form kann dann geschlossen werden, und auch das geschmolzene Metall kann mit hohem Druck in die Form gegossen werden, der zwischen etwa 10 und 175 MPa variiert.
Nachdem das geschmolzene Metall eingefüllt ist, wird der Druck aufrechterhalten, bis der Guss erstarrt. Die Pressstange schiebt danach alle Gussstücke heraus, und da es mehrere Hohlräume in einer Form geben kann, kann es auch mehrere Gussstücke pro Gussstück geben.
Der Prozess des fallenden Sandes erfordert die Trennung von Rückständen, einschließlich Formöffnungen, Kanälen, Toren und Graten. Der Prozess wird normalerweise durchgeführt, indem das Gussteil durch eine spezielle Trimmform gedrückt wird. Andere Möglichkeiten, Sand fallen zu lassen, sind Sägen und Schleifen. Wenn das Tor zerbrechlich ist, können Sie das Gießen direkt schlagen, was Personalressourcen sparen kann. Überschüssige Gussform kann nach dem Schmelzen wiederverwendet werden.
Die Hochdruckinjektion führt zu einem sehr schnellen Füllen der Form, sodass die gesamte Form mit geschmolzenem Metall gefüllt werden kann, bevor irgendein Teil erstarrt. Auf diese Weise können auch schwer zu füllende dünnwandige Teile ausreichend gefüllt und Oberflächenunstetigkeiten des Druckgussteils vermieden werden.
Dies führt jedoch zusätzlich zu Lufteinschlüssen, da die Luft beim schnellen Füllen der Form nur schwer entweichen kann. Das Anbringen von Entlüftungen an der Trennlinie kann dieses Problem verringern, aber wirklich exakte Prozesse können auch Porosität in der Gießmitte hinterlassen. Nachdem die meisten Teile druckgegossen sind, können sie vom Oberflächenveredelungsservice verarbeitet werden um einige Strukturen zu vervollständigen, die nicht durch Gießen vervollständigt werden können, wie z. B. Bohren und Polieren.
Defekte können nach Abschluss der Ausräumung untersucht werden. Zu den häufigsten Mängeln gehört Stagnation (unzureichende Füllung der Lösung). Diese Mängel können durch eine unzureichende Temperatur der Form oder des geschmolzenen Metalls, Metallverunreinigungen sowie wenige Entlüftungsöffnungen, übermäßiges Schmiermittel usw. verursacht werden. Andere Probleme bestehen in Porosität, Schrumpfung, thermischer Spaltung und auch Fließspuren. Fließspuren sind Spuren, die durch Anschnittdefekte, scharfe Ecken oder überschüssige Schmiersubstanz auf der Gussoberfläche hinterlassen werden.
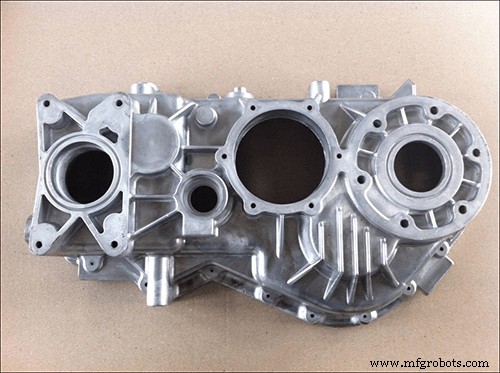
Metall für Druckguss
Metalle, die beim Druckguss verwendet werden, umfassen hauptsächlich Zink, Kupfer, Aluminium, Magnesium, Blei, Zinn und Blei-Zinn-Legierungen, obwohl Druckguss selten, aber machbar ist. Weitere einzigartige Druckgussstähle bestehen aus ZAMAK, Aluminium-Zink-Legierungen sowie den Standards der American Aluminium Association:AA380, AA384, AA386, AA390 sowie AZ91D-Magnesium. Die Eigenschaften des Druckgusses zahlreicher Metalle sind wie folgt:
Zink: Das am einfachsten zu spritzgießende Metall, kostengünstig zur Herstellung kleiner Komponenten, einfach zu beschichten, hohe Druckfestigkeit, Plastizität und Langlebigkeit.
Aluminium :Leicht, hohe Dimensionsstabilität bei der Herstellung komplexer und dünnwandiger Gussteile, starke Korrosionsbeständigkeit, gute mechanische Eigenschaften, hohe thermische und elektrische Leitfähigkeit und hohe Festigkeit bei hohen Temperaturen
Magnesium: Einfach zu bearbeiten, hohes Verhältnis von Festigkeit zu Gewicht, das leichteste unter den häufig verwendeten Druckgussmetallen
Kupfer :Hohe Härte, starke Korrosionsbeständigkeit, die besten mechanischen Eigenschaften von häufig verwendeten Druckgussmetallen, Verschleißfestigkeit und Festigkeit in der Nähe von Stahl.
Blei und Zinn: Als spezielle Korrosionsschutzkomponenten können hohe Dichte und extrem hohe Maßhaltigkeit eingesetzt werden. Aus Gründen der öffentlichen Gesundheit darf diese Legierung nicht in Geräten zur Lebensmittelverarbeitung und -lagerung verwendet werden. Legierungen aus Blei, Zinn und Antimon (manchmal mit etwas Kupfer) können Handschriften im Buchdruck und Bronzieren herstellen.
Metall | Mindestquerschnittsfläche | Mindestschräge |
Aluminiumlegierung | 0,89 mm (0,035 Zoll) | 1:100 (0,6°) |
Messing und Bronze | 1,27 mm (0,050 Zoll) | 1:80 (0,7°) |
Magnesiumlegierung | 1,27 mm (0,050 Zoll) | 1:100 (0,6°) |
Zinklegierung | 0,63 mm (0,025 Zoll) | 1:200 (0,3°) |
Die oberen Massengrenzen für Druckguss mit Aluminium, Kupfer, Magnesium und Zink sind jeweils 70 lbs (32 kg), 10 lbs (4,5 kg), 44 lbs (20 kg) und 75 lbs (34 kg). P>
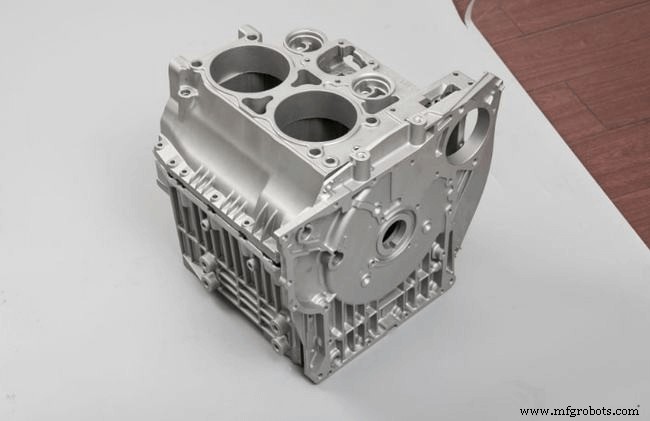
Vor- und Nachteile des Druckgusses
Vorteile des Druckgusses
Zu den Vorteilen des Druckgusses gehört, dass Gussteile eine hervorragende Maßhaltigkeit aufweisen können.
In der Regel hängt dies vom Gussmaterial ab. Im Vergleich zu anderen Gießverfahren entstehen beim Druckguss Teile mit glatten Oberflächen und einem Rundungsradius von ca. 1-2,5 Mikron. Im Druckguss können Teile mit Wandstärken von etwa 0,75 mm hergestellt werden, im Vergleich zu Kokillen- oder Kokillenguss. Es kann direkt Teile von internen Strukturen gießen, wie z. B. Drahtmäntel, Heizelemente, hochfeste Lagerflächen. Weitere Vorteile sind die Reduzierung oder Vermeidung der Nachbearbeitung von Teilen, die Produktionsgeschwindigkeit von Gussteilen, die Zugfestigkeit von Gussteilen (Festigkeit bis zu 415 MPa) und die Fähigkeit, Metalle mit hohem Fließvermögen zu gießen.
Nachteile des Druckgusses
Der größte Nachteil des Druckgusses sind seine hohen Kosten. Der Preis für Druckgussausrüstung (Druckgussmaschinen) und Formen und formverwandte Komponenten ist im Vergleich zu anderen Gießverfahren relativ hoch. Daher hat die Druckgussfertigung nur bei der Massenproduktion von Teilen einen hohen wirtschaftlichen Wert.
Weitere Nachteile sind:Das Druckgussverfahren eignet sich nur für relativ flüssige Metalle und die Gussmasse muss zwischen 30 Gramm und 10 Kilogramm liegen. Beim normalen Druckguss wird es immer Lunker in der letzten Gusscharge geben. Daher kann keine Wärmebehandlung oder Schweißung durchgeführt werden, da sich das Gas im Spalt unter Wärmeeinwirkung ausdehnt, was zu inneren Mikrodefekten und zum Ablösen der Oberfläche führt.
Warmkammer-Druckguss und Kaltkammer-Druckguss
Es gibt zwei verschiedene Arten, Teile im Druckguss herzustellen:Warmkammer-Druckguss und Kaltkammer-Druckguss . Bei beiden Herstellungsverfahren werden die Formen vor dem Gießvorgang mit einem Trennmittel besprüht, damit sich später gegossene Teile leicht aus den Formen lösen lassen. Allerdings wird die Schmelze nicht direkt in den Formhohlraum gegossen, sondern zunächst in den Gießhohlraum der Druckgießmaschine gegossen. Von dort wird die Legierung durch einen Kolben (eine sogenannte Gießgruppe) durch einen oder mehrere Kanäle in die Form gepresst. Der Unterschied zwischen den beiden Verfahren ist der Aufbau der Gießkammer, wie unten beschrieben.
Warmkammer-Druckguss
Beim Warmkammer-Druckguss ist sein Metallbad ein geschmolzener Zustand aus flüssigem, halbflüssigem Metall, das die Form unter Druck füllt. Zu den Vorteilen dieses Systems gehören eine hohe Zyklusgeschwindigkeit (ungefähr 15 Zyklen pro Minute), eine einfache Automatisierung und ein einfaches Schmelzen des Metalls. Zu den Nachteilen gehören die Unfähigkeit, Metalle mit höheren Schmelzpunkten druckzugießen, und die Unfähigkeit, Aluminium druckzugießen, wodurch Eisen aus dem Schmelzbad herausgetragen würde. So werden Warmkammer-Druckgussmaschinen im Allgemeinen für Legierungen aus Zink, Zinn und Blei verwendet. Darüber hinaus ist Warmkammer-Druckguss schwierig für den Druckguss großer Gussteile zu verwenden, bei denen es sich normalerweise um Druckguss kleiner Gussteile handelt.
Kaltkammer-Druckguss
Kaltkammer-Druckguss kann zum Druckgießen von Metallen verwendet werden, die im Warmkammer-Druckgussverfahren nicht verwendet werden können, einschließlich Aluminium-, Magnesium-, Kupfer- und Zinklegierungen mit höherem Aluminiumgehalt. Das Metall muss bei diesem Verfahren zunächst in einem separaten Tiegel geschmolzen werden. Eine Menge geschmolzenen Metalls wird dann in eine unbeheizte Einspritzkammer oder -düse überführt. Diese Metalle werden durch hydraulischen oder mechanischen Druck in die Form eingespritzt.
Der größte Nachteil dieses Verfahrens ist die lange Zykluszeit aufgrund der Notwendigkeit, das geschmolzene Metall in die Kältekammer zu überführen. Kaltkammer-Druckgussmaschinen werden ebenfalls in vertikale und horizontale Typen unterteilt. Vertikale Druckgussmaschinen sind normalerweise kleine Maschinen, während horizontale Druckgussmaschinen verschiedene Modelle haben.
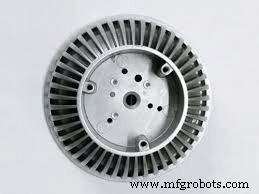
Einsatzgebiete des Druckgusses
Druckguss wird hauptsächlich für die Massenproduktion verwendet, d. h. zum Gießen vieler gleichartiger Teile. Trotz des hohen Drucks im Herstellungsprozess wird eine hohe Gussqualität erreicht. Das Druckgussverfahren eignet sich besonders zur Herstellung sehr dünner (bis 1 mm) (Leichtbau-)Teile.
Am häufigsten werden Druckgusskomponenten wie Räder, Zylinderblöcke, Zylinderköpfe, Ventilkörper und Krümmer für die Automobilindustrie hergestellt. Darüber hinaus verwenden andere Branchen Druckgussteile:
- Luft- und Raumfahrt
- Haushaltsgeräte
- Möbel
- Elektrowerkzeuge
- Elektronische Produkte
- Mechanisch
- Lichttechnik
Zukünftig werden sich Gießereien auch für andere Branchen wie Elektrofahrzeuge interessieren. Dies bietet großes Potenzial für Leichtmetallguss.
Wählen Sie ein Druckgussunternehmen Ihres Vertrauens
Druckguss ist seit dem 19. Jahrhundert in der Fertigung weit verbreitet. Als führender Druckgussdienstleister in China bietet JTR seinen Kunden seit vielen Jahren komplette Druckgusslösungen. Hochwertiger Druckgussservice ist der Schlüssel zu unserer Rentabilität. Wenn Sie also Ihr Design umsetzen müssen, können Sie sich an uns wenden. Sie müssen nur das Design oder die Kreativität vervollständigen, und wir erledigen den Rest.
Industrietechnik
- 6 Dinge, die Sie über 3D-Druck nicht wussten
- 5 lustige Fakten über Druckguss
- Warum Sie mehr über Industrie 4.0 wissen als Sie denken
- Was Sie über die CMMC-Zertifizierung wissen müssen
- Alles, was Sie über Metallguss wissen müssen
- Alles, was Sie über MFD-Kondensatoren wissen müssen
- Dinge, die Sie über Metallguss wissen sollten
- 5 Dinge, die Sie nicht über Titan wussten
- Alles, was Sie über die Metallbearbeitung wissen müssen
- Alles, was Sie über Sperrholz wissen müssen