Was ist Thermoplast?
Ein Thermoplast (manchmal auch als Thermoplast bezeichnet) ist eine Kunststoffart aus Polymerharzen, die beim Erhitzen zu einer homogenisierten Flüssigkeit und beim Abkühlen hart wird. Im gefrorenen Zustand wird ein Thermoplast jedoch glasartig und bruchanfällig. Diese namensgebenden Eigenschaften sind reversibel. Das heißt, es kann wiederholt aufgewärmt, umgeformt und eingefroren werden. Diese Qualität macht auch Thermoplaste recycelbar.
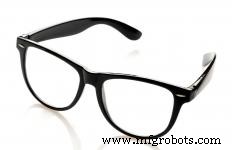
Es gibt Dutzende von Arten von Thermoplasten, wobei sich jede Art in ihrer kristallinen Organisation und Dichte unterscheidet. Einige Typen, die heute üblicherweise hergestellt werden, sind Polyurethan, Polypropylen, Polycarbonat und Acryl. Zelluloid, das als der erste Thermoplast gilt, erschien Mitte des 18. Jahrhunderts und beherrschte die Industrie etwa 100 Jahre lang. Während seiner Spitzenproduktion wurde es als Ersatz für Elfenbein verwendet. Heute wird es zur Herstellung von Gitarrenplektren verwendet.
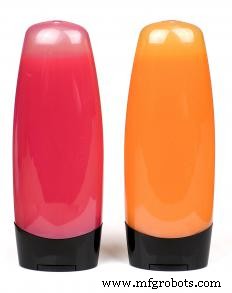
Manchmal werden Thermoplaste mit duroplastischen Kunststoffen verwechselt. Obwohl sie gleich klingen mögen, besitzen sie tatsächlich sehr unterschiedliche Eigenschaften. Während Thermoplaste zu einer Flüssigkeit geschmolzen und zu einem Feststoff abgekühlt werden können, zersetzen sich duroplastische Kunststoffe chemisch, wenn sie Hitze ausgesetzt werden. Ironischerweise neigen duroplastische Kunststoffe jedoch dazu, beim Abkühlen haltbarer zu sein als viele Thermoplaste.
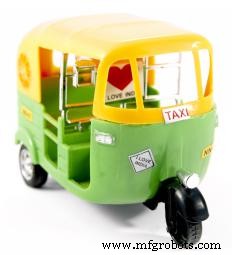
Thermoplaste unterscheiden sich auch von Elastomeren, obwohl einige beides sind. Während viele Thermoplaste bis zu einem bestimmten Punkt gedehnt werden können, neigen sie im Allgemeinen dazu, sowohl Widerstand zu leisten als auch in der Form zu bleiben, in die sie gedehnt werden. Elastomere erholen sich, wie der Name schon sagt. Die Zugabe von Weichmachern zur Schmelze kann jedoch einen biegsameren Thermoplasten ergeben. Tatsächlich ist dies normalerweise der Fall, wenn ein Thermoplast für das Spritzgießen oder Extrudieren von Kunststoff verwendet wird.

Die spezifische Wirkung eines Weichmachers besteht darin, die Glasübergangstemperatur (Tg) des Materials zu senken, das ist der Punkt, an dem es beim Abkühlen spröde und beim Erhitzen weich wird. Tg variiert mit jedem Thermoplasttyp und wird durch seine Kristallisationsstruktur bestimmt. Die Tg kann jedoch auch durch Einbringen eines Thermoplasten in ein Copolymer, wie Polystyrol, eingestellt werden. Bis zur Verwendung von Weichmachern neigten einige Thermoplast-Formteile dazu, bei kaltem Wetter zu reißen.
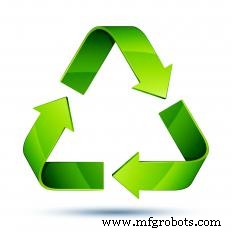
Thermoplaste gibt es schon lange, sind aber heute aus dem Alltag nicht mehr wegzudenken. Beispielsweise ist Acrylnitril-Butadien-Styrol (ABS) eine Art Thermoplast, der zur Herstellung von Sportgeräten, Spielzeug (d. h. LEGO®-Blöcken) und verschiedenen Autoteilen verwendet wird. Polycarbonat wird unter anderem zur Herstellung von Compact Discs (CDs), Trinkflaschen, Lebensmittelbehältern und Brillengläsern verwendet. Polyethylen ist wahrscheinlich der am häufigsten anzutreffende Thermoplast und wird zur Herstellung von Shampooflaschen, Einkaufstüten aus Plastik und sogar kugelsicheren Westen verwendet.
Sind Thermoplaste biologisch abbaubar?
Die biologische Abbaubarkeit ist ein wichtiges Maß für die Umweltfreundlichkeit einer Substanz. Einfach ausgedrückt bedeutet biologische Abbaubarkeit, dass ein Material auf natürliche Weise von Mikroorganismen abgebaut werden kann. Bakterien und Pilze helfen normalerweise bei der Zersetzung, indem sie sich von organischen Materialien ernähren. Sobald biologisch abbaubare Materialien abgebaut werden, bleiben ihre Grundbestandteile erhalten.
Warum normaler Kunststoff nicht biologisch abbaubar ist
Herkömmliche Kunststoffe sind nicht biologisch abbaubar. Denn Bakterien können sich nicht davon ernähren und sie in ihre ursprünglichen Bestandteile zerlegen. Obwohl Kunststoffe aus natürlich vorkommenden Materialien wie Öl hergestellt werden, ist es der Polymerisationsprozess, der dafür sorgt, dass sie nicht zerfallen können.
Wenn Rohöl zur Herstellung von Kunststoff verwendet wird, werden seine Kohlenwasserstoffe schließlich in kleinere Moleküle getrennt, die als Monomere bekannt sind. Zwei Schlüsselmonomere in der Kunststoffherstellung sind Ethylen und Propylen. Diese werden chemisch zu neuen Konfigurationen kombiniert, was zu langen, sich wiederholenden Molekülketten führt, die wir Polymere nennen. Sie werden später mit Additiven wie Flammschutzmitteln kombiniert, um die endgültige Form jeder Art von Kunststoff herzustellen.
Wenn also Kunststoffe Kohlenstoff enthalten, welche Bakterien können sie dann nicht abbauen? Der Polymerisationsprozess verwandelt die ursprünglichen Materialien in molekulare Verbindungen, die in der Natur nicht vorkommen. Bakterien und andere Mikroorganismen können Kohlenstoff in dieser Form nicht verbrauchen.
Thermoplaste und biologische Abbaubarkeit
Wie normaler Kunststoff werden auch Thermoplaste aus Polymeren hergestellt. Es gibt auch thermoplastische Stärke, die durch die Kombination nativer Stärken mit einem Weichmacher hergestellt wird. Diese nativen Stärken werden auch als reine Stärken bezeichnet, die aus Lebensmitteln wie Weizen und Kartoffeln gewonnen werden. Sie bestehen aus langkettigen Kohlenhydraten, die in kaltem Wasser unlöslich sind.
Der Prozess zur Herstellung thermoplastischer Stärken beginnt damit, dass die Weichmacher-Stärke-Mischung auf 70 bis 90 Grad Celsius erhitzt wird. Dieser Bereich liegt über normalen Stärkegelatinierungstemperaturen und schwächt bestehende Wasserstoffbindungen in der Stärke selbst. Die resultierende Mischung verwandelt sich in thermoplastische Stärke.
Biologisch abbaubare Kunststoffe wie thermoplastische Stärke können das Problem der biologischen Abbaubarkeit lösen. Stärke selbst ist biologisch abbaubar und ein nachwachsender Rohstoff. Je nachdem, welche Quelle Sie konsultieren, dauert es zwischen 30 und 90 Tagen, bis TPS abgebaut ist. Im Gegensatz dazu braucht die durchschnittliche Plastikflasche etwa 450 Jahre, um sich zu zersetzen.
Was ist der Hauptunterschied zwischen thermoplastischem und duroplastischem Kunststoff?
Thermoplastischer und duroplastischer Kunststoff mögen auf den ersten Blick ähnlich erscheinen. Schließlich sind sie beide aus Polymeren hergestellt. Sie reagieren jedoch unterschiedlich, wenn sie Gehör ausgesetzt sind. Duroplast schmilzt nicht – tatsächlich behält er nach dem Aushärten seine Form und Festigkeit bei.
Wenn also duroplastischer Kunststoff nicht wirklich schmilzt, warum wird er dann noch verwendet? Diese Unfähigkeit zu schmelzen wird in bestimmten Situationen zu einem Vorteil. Zu seinen einzigartigen Eigenschaften gehören eine Vielzahl von Farben und Oberflächen sowie zusätzliche Festigkeit nach ordnungsgemäßer Aushärtung. Außerdem sind sie korrosionsbeständig, weisen eine hohe Durchschlagsfestigkeit auf und sind kostengünstiger in der Herstellung. Aus diesem Grund wird duroplastischer Kunststoff in vielen Anwendungen verwendet:Automobilkomponenten, Haushaltsgeräte und Elektroteile, um nur einige zu nennen.
Wie können Thermoplaste und Duroplaste recycelt werden?
Sie werden überrascht sein zu erfahren, dass Thermoplaste recycelbar sind. Ein Grund dafür ist ihre Hitzetoleranz. Polymere in Thermoplasten sind stark, aber die chemischen Bindungen zwischen ihnen sind schwach. Dadurch können sie immer wieder erhitzt und gekühlt werden, ohne ihre strukturelle Zusammensetzung zu zerstören. Dies führt zu einer einfacheren Möglichkeit, sie wiederholt wiederzuverwenden.
Rund 75 % des weltweit produzierten Kunststoffs liegt in thermoplastischer Form vor. Ein Großteil davon umfasst Einwegkunststoffe für Lebensmittel- und Getränkebehälter. Polyethylenterephthalat, auch PET genannt, wird häufig in Wasserflaschen verwendet.
Recycling von Thermoplasten
Sobald recycelbare Kunststoffe ihren endgültigen Bestimmungsort erreichen, werden sie eingeschmolzen und durch Spritzguss wiederverwendet. Ein Hauptproblem beim Versuch, Thermoplaste und andere Kunststoffmaterialien zu recyceln, besteht jedoch darin, dass sie alle leicht unterschiedliche Zusammensetzungen haben. Deshalb ist es notwendig, diese verschiedenen Kunststoffarten zu trennen, wenn Sie planen, sie zu recyceln.
Beim Sammeln von Kunststoff zum Recycling sollten Sie einige Dinge beachten. Flaschen von Getränken, Körperpflegeprodukten, Waschmitteln und Lebensmittelbehältern können recycelt werden. Sie können auch nach Zahlen suchen, die auf den Kunststoffbehältern selbst eingeprägt sind. Eine kleine "1" bedeutet, dass es aus recyceltem PET besteht. Polyethylen hoher Dichte ist mit einer „2“ gekennzeichnet und zudem gut recycelbar. Wenden Sie sich für alles andere an Ihren örtlichen Recyclinghof oder die städtische Müllabfuhr.
Duroplaste und Recycling
Produkte aus duroplastischem Kunststoff müssen langlebig sein und können daher nicht einfach recycelt werden. Wissenschaftler untersuchen neue Wege, sie zu recyceln, einschließlich chemischer Linker, die diesen Gegenständen helfen, ihre Festigkeit zu bewahren und gleichzeitig leichter zu zerfallen. Dies ist eine aufregende Entwicklung, aber eine weit verbreitete Umsetzung wird möglicherweise noch einige Zeit nicht erfolgen. Sobald dies der Fall ist, kann verhindert werden, dass mehr Kunststoffmaterialien auf Mülldeponien landen.
Industrielle Ausrüstung
- Was Sie beim Kauf von Magneten beachten sollten.
- Was Sie beim Kauf einer gebrauchten CNC-Maschine beachten sollten
- Rückspulen der Lichtmaschine:Was ist das und wann wird es benötigt
- Was beim Bewegen von schwerem Gerät zu beachten ist
- Was beim internationalen Versand schwerer Ausrüstung zu beachten ist
- Was ist bei der Auswahl eines Maschinenumzugsunternehmens zu beachten?
- Worauf Sie beim Kauf von Industrieteilen achten sollten
- Worauf Sie beim Kauf eines Hüttenarbeiters achten sollten
- Was Sie beim Kauf von Winkelrollen beachten sollten
- Was bei der Auswahl von Greifern zu beachten ist