Funkenerosion:Aufbau, Anwendung, Vor- und Nachteile
Elektroerosionsbearbeitung, auch Elektroerosionsbearbeitung genannt, ist ein Prozess, der sich stark von den meisten herkömmlichen Bearbeitungsprozessen wie CNC-Drehen und -Fräsen unterscheidet. Bei letzteren Verfahren sind scharfe Schneidwerkzeuge erforderlich, um Material von dem zu bearbeitenden Werkstück abziehen zu können. Im Gegensatz zum Drehen und Fräsen nutzt der EDM-Prozess die Erosion von Metall durch eine Reihe von elektrischen Entladungen.
Lesen Sie unten weiter und erfahren Sie mehr über die grundlegenden Konzepte der EDM-Fertigung.
Wie funktioniert EDM?
Bei der Funkenerosionsbearbeitung werden elektrische Funken auf der Funkenerosionsmaschine verwendet, um einige Teile des Werkstücks zu erodieren. Diese „elektrischen Funken“ sind eigentlich Lichtbögen, die sich zwischen zwei stromführenden Leitern bilden, die in unmittelbarer Nähe zueinander gebracht werden. Die Lichtbögen sind für die Erzeugung extremer Hitze verantwortlich, die dazu führt, dass die elektrisch leitfähigen Materialien schmelzen und verdampfen. Innerhalb des Systems eines EDM-Prozesses wird das Werkstück mit dem Pluspol oder der Anode verbunden, während das für das Erodieren von Materialien zuständige Werkzeug mit dem Minuspol oder der Kathode verbunden wird.
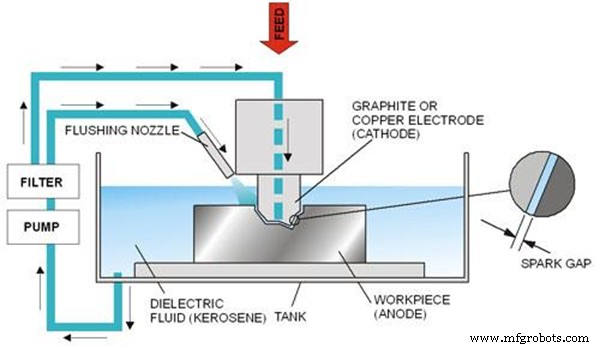
Grundlegender Aufbau eines EDM-Systems
Zur weiteren Erläuterung des Arbeitsprinzips finden Sie unten eine Aufschlüsselung der Grundkonstruktion eines Elektroerosions-Bearbeitungssystems (EDM).
1. DC-Impulsgenerator
Diese Komponente wandelt die Wechselstromversorgung in eine pulsierende Gleichstromversorgung um, die hoch genug ist, um einen Funken zwischen dem Erodierwerkzeug und dem Werkstück zu erzeugen.
2. Elektrodenwerkzeug
Dieser Teil des Systems ist mit der Kathode der Stromversorgung verbunden, während er auf einem Werkzeugständer montiert ist. Das Profil Ihres Werkzeugs ist genau das gleiche Profil, das auf Ihrem Werkstück verbleibt. Während des Prozesses bleibt zwischen dem Elektrodenwerkzeug und dem Werkstück ein sehr kleiner Spalt, der als Lichtbogenspalt bezeichnet wird (von Fertigungsingenieuren identifiziert). Die am häufigsten für Elektroden verwendeten Materialien sind Kupfer, Wolframlegierungen, Graphit, Stahl und Gusseisen.
3. Servomotormechanismus
Dieser Mechanismus steuert den Vorschub und die Bewegung des Werkzeugs in der Funkenerosionsmaschine. Der oben erwähnte Lichtbogenspalt wird kritisch durch einen programmierten Servomotormechanismus gesteuert.
4. Funkengenerator
Diese Komponente liefert die richtige Menge an Spannung, die für die Funkenerzeugung und die Aufrechterhaltung der Entladung benötigt wird. Die Erzeugung von hunderttausend Funken pro Sekunde ermöglicht einen erheblichen Materialabtrag vom Werkstück.
5. Dielektrikum
Sowohl das Elektrodenwerkzeug als auch das Werkstück werden in ein dielektrisches Fluid eingetaucht, während das Fluid an dem Spalt zwischen dem Werkzeug und dem Werkstück zugeführt wird. Darüber hinaus sollte das Dielektrikum so eingestellt werden, dass es bei einem konstanten Druck zirkuliert, um Metallteile, die vom Werkstück erodiert sind, abzudampfen. Ein zu hoher Flüssigkeitsdruck kann dazu führen, dass die Metallspäne schnell entfernt werden, was zu einem langsameren Schneidvorgang führt. Ein zu schwacher Flüssigkeitsdruck kann aufgrund der nicht abgesaugten Späne während des Erosionsprozesses einen Kurzschluss im System verursachen.
Die in diesem Prozess am häufigsten verwendeten dielektrischen Flüssigkeiten sind entionisiertes Wasser, Glykol und Silikonöl.
6. Werkstück
Dies vervollständigt das Ökosystem der EDM-Maschine, da das Werkstück mit der Anode verbunden ist. Um den Prozess zu ermöglichen, sollte das Werkstück ein guter elektrischer Leiter sein.
Art der EDM-Prozesse
Der EDM-Prozess wird je nach Form und Ansatz des verwendeten Werkzeugs in verschiedene Typen eingeteilt. Die drei gängigen Arten der elektrischen Entladung in der Industrie sind Drahterodieren, Senkerodieren und Lochbohrerodieren.
1. Drahterodieren
Wie der Name schon sagt, verwendet das EDM-Drahtschneiden einen sehr dünnen Draht (Kupfer- oder Messinglegierung, der normalerweise zwischen 0,004 Zoll und 0,0006 Zoll dünn ist), der von Diamantführungen gehalten wird, um eine zweidimensionale Form auf einem 3D-Werkstück präzise zu schneiden. Der Pfad wird von einem CNC-Programm gesteuert, das das einfache Schneiden komplexer Formen ermöglicht. Das Schneiden kann mit dem Schneidvorschub einer Bandsäge und eines Käseschneiders verglichen werden. Dieses Verfahren wird typischerweise zum Schneiden von Metall-Extrusionsmatrizen, Stempeln und Platten verwendet.
2. Senkerodieren
Diese Art des EDM-Prozesses, auch Ram-EDM genannt, verwendet Graphit- oder Kupferelektroden, die in einer umgekehrten Form ausgebildet sind, um einen Hohlraum in das Werkstück zu schneiden. Das zu verwendende Werkzeug wird in einer umgekehrten Form der gewünschten Form bearbeitet, um auf dem Werkstück zu verbleiben.
Senkerodieren eignet sich perfekt für die Bearbeitung von Formen, die zum Gießen und Spritzgießen verwendet werden, wo komplexe Hohlraumformen benötigt werden.
3. Lochbohren EDM
Bei dieser Art von EDM-Prozess wird das Elektrodenwerkzeug verwendet, um extrem dünne und tiefe Löcher zu schneiden, zu denen ein herkömmlicher Bohrer möglicherweise nicht in der Lage ist. Das Werkzeug für diesen Prozess ist so konstruiert, dass die dielektrische Flüssigkeit direkt durch das Loch zugeführt wird, also eine hohle Elektrode. Da Lochbohren EDM nicht durch das herkömmliche Bearbeitungsverfahren hergestellt wird, werden keine Grate in dem Werkstück gebildet. Lochbohren EDM wird zum Bearbeiten winziger Entlastungslöcher an verschiedenen Turbinenschaufeln, Matrizen und Formen verwendet.
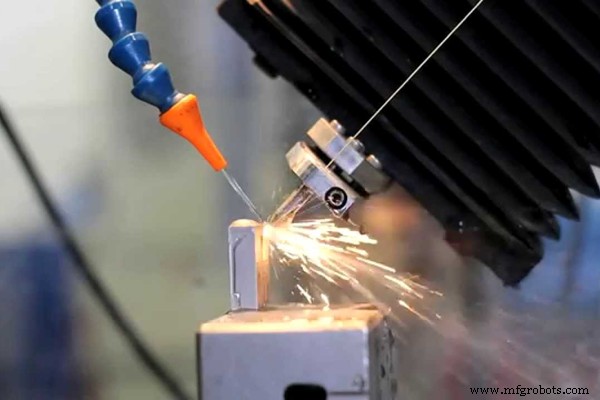
Was sind die Anwendungen der Funkenerosion?
Die EDM-Bearbeitung ist sehr gut in der Lage, komplizierte Formen und Geometrien herzustellen.
Aus diesem Grund wird die Elektroerosion im Allgemeinen für hochpräzise Anwendungen eingesetzt, bei denen die herkömmliche Bearbeitung nicht möglich ist. Nachfolgend sind die häufigsten Anwendungen der Funkenerosion aufgeführt:
Bohren kleiner Löcher
Viele Hersteller entscheiden sich für die EDM-Bearbeitung beim Bohren extrem kleiner Löcher, da dies das Risiko verringert, dass Werkzeuge abgelenkt und beschädigt werden. EDM-bearbeitete Löcher können eine sehr kleine Struktur haben und an den Kanten von Turbinenschaufeln, mikroskopisch kleinen Öffnungen für Kraftstoffsystemkomponenten und vielem mehr zu sehen sein.
Formen- und Formenbau
Die EDM-Bearbeitung wird häufig als ergänzender Prozess neben der konventionellen Bearbeitung bei der Herstellung von Formen und Gesenken eingesetzt. Wie oben erwähnt, wird der Drahtschneidetyp typischerweise zum Bilden von Rohlingen für die Formen verwendet, der Platinentyp kann verwendet werden, um komplexe Formen der Hohlräume zu bilden, und das Lochbohren kann zum Erzeugen von Druckentlastungslöchern verwendet werden.
Bestandteilzerfall
Die Erodiermaschine wird auch verwendet, um festsitzende Metalle in einem Werkstück zu entfernen, die auf herkömmliche Weise nicht entfernt werden können. Das Auflösen der festsitzenden Komponenten bedeutet, das Material zu zerstören oder zu entfernen. Einige Umstände umfassen abgescherte Schrauben an Gewindelöchern, Saugwerkzeuge an einem bearbeiteten Teil oder einen Stift, der an einem sehr wertvollen Teil feststeckt. Indem Sie die Komponenten zerlegen, können Sie das festsitzende Metall entfernen, ohne das zurückzugewinnende Teil zu beschädigen.
Medizinische Komponenten
EDM-bearbeitete Produkte bilden bei der Herstellung keine Grate, weshalb diese perfekt für die Herstellung verschiedener medizinischer Implantatkomponenten geeignet sind.
Luft- und Raumfahrtkomponenten
Es gibt viele Merkmale an einem Luft- und Raumfahrtteil, die mit einigen Standard-Schneidwerkzeugen nicht hergestellt werden können, und hier kommt die EDM-Bearbeitung ins Spiel. Die EDM-Bearbeitung ist in der Lage, anspruchsvolle Merkmale mit vordersten Turbinenrotorscheiben, dünnen Schlitzen und scharfen Quadraten herzustellen Löcher und sehr enge Anforderungen für tiefe Löcher.
Warum EDM bevorzugt wird?
Sehr gut in der Lage, komplexe Profile zu bearbeiten
Die Schnittfreiheit beim Erodieren ist weniger eingeschränkt als bei herkömmlichen Bearbeitungsvorgängen. Bei diesem Verfahren können verschiedene Merkmale, die mit Schaftfräsern und Bohrern kaum zu erreichen sind, problemlos geschnitten werden. Zu diesen Merkmalen gehören komplizierte Taschen, feine tiefe Löcher, dünne Wände und andere unregelmäßig geformte Geometrien.
Hohe Genauigkeit
Mit EDM-Technologie bearbeitete Teile können bis zu den kleinsten Toleranzen präzise sein, die in der metallverarbeitenden Industrie verwendet werden. Dies ist möglich, weil das Ökosystem der EDM-Bearbeitung das Werkstück nicht stark belastet und keine aggressiven Vibrationen aufweist. Abgesehen davon kann auch ein Skimming-Prozess durchgeführt werden, um seine Präzision und Genauigkeit zu erhöhen.
Gratfreie Oberflächengüte
Das aus der EDM-Bearbeitung hergestellte Werkstück kommt gratfrei heraus aufgrund der Natur des Prozesses, bei dem das erodierte Metall von dem Werkstück fast in Mikropartikel zerfällt, die dann ausgespült werden. Am wichtigsten ist, dass beim EDM-Schneiden keine scharfen Schneidwerkzeuge wie Schaftfräser, Sägen und Bohrer verwendet werden, weshalb dieser Prozess keine Grate am Werkstück verursacht.
Kann Hartmetalle schneiden
Die EDM-Bearbeitung ist in der Lage, Hartmetalle mit geringer Kraft und minimalem Aufwand zu schneiden, solange sie leitfähig sind. Die Härte des zu schneidenden Materials hat keinen Einfluss auf den Gesamtprozess.
Geringer Stress
Die in einem EDM-Prozess verwendeten Werkzeuge berühren das Werkstück nicht, im Gegensatz zu anderen Bearbeitungsverfahren, bei denen die Schneidwerkzeuge die zu schneidende Oberfläche berühren. Dies erklärt die minimale Belastung, die in das Werkstück eingebracht wird.
Hochgradig skalierbare Fertigung
EDM-Bearbeitungsprozesse sind im Produktionsmaßstab sehr vielseitig und eignen sich für die Klein- bis Großserienfertigung. Diese Prozesse sind sehr wiederholbar, was bedeutet, dass mehrere Teile mit gleichbleibender Qualität hergestellt werden können.
Lorem ipsum dolor sit amet, consectetur adipiscing elit. Ut elit tellus, luctus nec ullamcorper mattis, pulvinar dapibus leo.
Was sind die Einschränkungen des EDM-Prozesses?
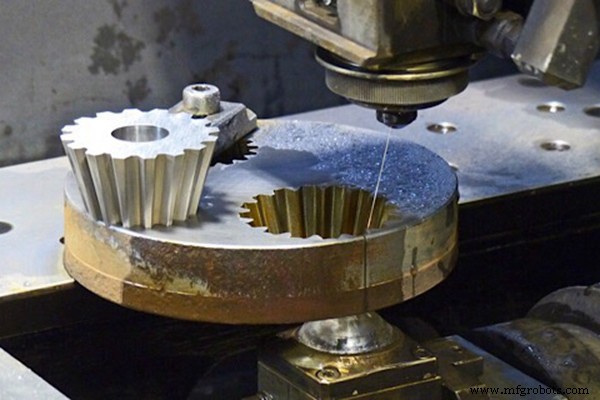
Nur auf leitfähige Materialien anwendbar
Die für die Erosion des Materials auf dem Werkstück verantwortliche Wärme beruht auf der Einführung elektrischer Entladungen, wodurch die Funkenerosionsbearbeitung mit nicht leitenden Materialien wie Verbundwerkstoffen, Kunststoffen und anderen dielektrischen Materialien nicht kompatibel ist.
Geringer Materialabtrag
Wie bereits erwähnt, erodiert die Funkenerosion das Material allmählich. Dadurch ist die Materialabtragsrate viel langsamer als bei herkömmlichen Bearbeitungsverfahren wie Fräsen und Drehen.
Hohe Produktionskosten
Die Kosten für die Herstellung von Teilen mit EDM beinhalten verschiedene Faktoren wie hoher Stromverbrauch, übermäßiger Werkzeugverschleiß und lange Bearbeitungszeit.
Zusammenfassung
Die Funkenerosion ist eine sehr sinnvolle Ergänzung zu verschiedenen konventionellen CNC-Bearbeitungsverfahren. Es spielt seine Stärken dort aus, wo es in der Lage ist, spezielle Features herzustellen, die durch Fräsen und Drehen schwer zu erreichen sind. Darüber hinaus weist das EDM-Verfahren auch beim Schneiden extrem harter elektrisch leitfähiger Metalle eine außergewöhnliche Genauigkeit auf und weist eine geringe Belastung während der Bearbeitung auf.
CNC-Maschine
- Vor- und Nachteile von Lost-Foam Casting
- Vor- und Nachteile der Kaltumformung von Metallen
- EDM-Bearbeitung:Aufbau und Arbeitsprinzip besprochen
- Warum Elektroerosionsbearbeitung gegenüber anderen Techniken beliebt ist?
- Was ist Funkenerosion (EDM)?
- Elektroerosionsmaschinen (EDM) Typen, Vor- und Nachteile
- Prototypenbearbeitung:Vor- und Nachteile von CNC für Prototypen
- Senkerodieren vs. Drahterodieren:Hauptunterschiede und Anwendungen
- Jenseits der CNC:Was ist Funkenerosion?
- Die Vor- und Nachteile der Technologie in der Fertigung