Qualität 4.0:Wie drahtlose IoT-Sensornetzwerke die Fertigung verändern
Qualitätskontrolle ist in jeder Branche von grundlegender Bedeutung, aber in der Fertigung ist sie überkritisch. Volatile Marktnachfrage, hohe Material- und Produktionskosten sowie die unternehmenskritische Natur der Endprodukte zwingen Hersteller dazu, ausschließlich erstklassige Qualität und eine minimale Ausschussquote anzustreben. Da das Internet der Dinge (IoT) allmählich in der Fertigungsindustrie Einzug hält, ist das Qualitätsmanagement ein Bereich mit Transformationsmöglichkeiten.
Die Qualitätsmanagement-Herausforderung auf einen Blick
Effektives Qualitätsmanagement beruht auf der Fähigkeit, eine Vielzahl von Maschinen- und Prozessparametern, die sich auf die Produktqualität auswirken, ständig zu überwachen und zu steuern. Um sicherzustellen, dass die Produkteigenschaften konsistent und auf dem neuesten Stand sind, wird die Ausrüstung ständig neu kalibriert, wenn Prozessabweichungen und andere Änderungen in der Produktionslinie auftreten. Doch mit der wachsenden Komplexität von Werkzeugsystemen und Fertigungsprozessen bleiben viele Prozessvariablen aufgrund der Grenzen von sperrigen kabelgebundenen Netzwerken unberücksichtigt.
Die kabelgebundene Kommunikation ist zwar ideal für zeitkritische Automatisierungsaufgaben mit hohem Durchsatz, aber es fehlt ihnen die Flexibilität und Erschwinglichkeit, die erforderlich sind, um Telemetriedaten in großem Maßstab und über die Maschinenebene hinaus zu erfassen. Typischerweise werden Faktoren wie Umgebungsbedingungen trotz ihres großen Einflusses auf die Qualitätsvariabilität oft nicht untersucht und kontrolliert. Beispielsweise kann in der Automobilherstellung eine ungünstig niedrige Raumtemperatur die Qualität von 3D-gedruckten Bauteilen beeinträchtigen, da sie zu schnell abkühlen.
Darüber hinaus sind die meisten kabelgebundenen Industriesysteme, die im letzten Jahrhundert entwickelt wurden, nicht für den Datenaustausch außerhalb der Fabrikhalle gedacht. Dadurch entstehen getrennte Dateninseln, die nicht zur Steigerung der Produktionseffizienz und des Durchsatzes zur Verfügung stehen. Stattdessen hängen Prozessoptimierung und Qualitätsmanagement oft von einer reaktiven, manuellen Nachkontrolle ab. Neben teuren menschlichen Eingriffen führt dies zu erheblichen Qualitätsschwankungen und damit verbundenen Kosten, während es schwierig wird, die eigentliche Ursache von Qualitätsproblemen aufzuspüren.
Einstieg in Industrie 4.0:Proaktives Qualitätsmanagement
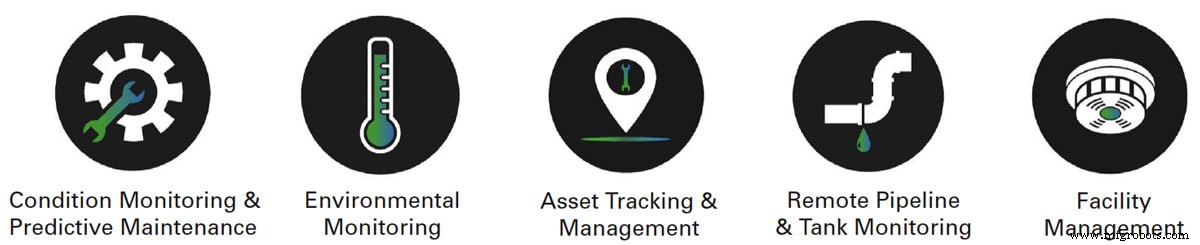
Die dringende Suche nach verbesserter Prozesstransparenz spricht für das enorme Potenzial des IoT und seines Gegenstücks, Industrie 4.0, für ein proaktives Qualitätsmanagement.
Drahtlose IoT-Netzwerke erfassen eine große Anzahl granularer kritischer Datenpunkte entlang der Produktionslinie. Zum Beispiel Druck, Vibration, Temperatur und Feuchtigkeit. Mit potenziell Tausenden von Sensoren, die vor Ort installiert sind, werden Daten alle 10 bis 20 Sekunden gesammelt und über eine Basisstation an das bevorzugte Backend-System des Benutzers gesendet, egal ob vor Ort oder in der Cloud. Mithilfe einer Remote-IoT-Plattform werden alle Sensordaten für Echtzeitüberwachung, umsetzbare Erkenntnisse und Prozessautomatisierung konsolidiert. Warnungen können sofort ausgelöst werden, wenn bei laufenden Geräten und Prozessen Bedingungen außerhalb der Spezifikation auftreten. Dies bietet Herstellern eine beispiellose Kontrolle über ihre Betriebsabläufe und Produktausgaben. Über die reaktive End-of-Run-Qualitätsprüfung hinaus ermöglichen IoT-Daten einen proaktiven Qualitätssicherungsansatz, um Fehler viel früher im Prozess zu diagnostizieren und zu verhindern, um einen maximalen Produktionsdurchsatz und Wiederholbarkeit zu erzielen. Dies führt auch zu reduzierten Kosten und Abfall. Gleichzeitig liefert es wertvolle Einblicke zum Erreichen und Aufrechterhalten von Best Practices.
Fünf führende Anwendungen für proaktives Qualitätsmanagement:
1. Zustandsüberwachung und vorausschauende Wartung
IoT-Sensoren erfassen und kommunizieren wichtige Gesundheits- und Betriebsmetriken wie Druck, Vibration, Temperatur, Feuchtigkeit und Spannung zahlreicher Maschinen und Anlagen im gesamten Industriekomplex (Zustandsüberwachung). Diese massiven Datenflüsse erzeugen nicht nur ein aufschlussreiches Bild der aktuellen Produktionsprozesse und der Anlagenleistung, sondern unterstützen auch Analysemodelle, um ein bevorstehendes Problem proaktiv vorherzusagen und eine bedarfsorientierte Inspektion und Reparatur (vorausschauende Wartung) zu planen. Beispielsweise verringert eine hohe Feuchtigkeit im Getriebe die Leistung rotierender Komponenten, was zu Korrosion, beeinträchtigter Produktqualität oder sogar Maschinenausfällen führt. Übermäßige Vibrationen von Motoren und Pumpen weisen auf mögliche Montagefehler, Wellenfehlausrichtung und Lagerverschleiß hin. Mit vorausschauender Wartung können Ausfälle im Voraus verhindert werden, wodurch die Ressourcennutzung maximiert und kostspielige Verluste aufgrund von Ausfallzeiten reduziert werden.
2. Umweltüberwachung
Umgebungsbedingungen können in der Produktion und im Qualitätsmanagement eine bedeutende Rolle spielen. Mit Hilfe von Umgebungssensoren, die Temperatur, Luftfeuchtigkeit und Luftqualität messen, können Anlagenbetreiber optimale Umgebungen für verschiedene fabrikweite Prozesse von ihrer Kommandozentrale aus fernüberwachen und steuern. Beispielsweise verhindert die Aufrechterhaltung eines idealen Luftdruckunterschieds das Eindringen von Staub in den Fertigungsbereich und sichert so die Produktqualität in der pharmazeutischen und mikroelektronischen Industrie. Klebe- und Lackierprozesse in der Automobilproduktion können mit einem optimalen Feuchtigkeitsniveau verbessert werden. Ebenso kann eine genaue Temperaturüberwachung von Verarbeitungs- und Lagereinrichtungen die Produktsicherheit in der Lebensmittelindustrie gewährleisten.
3. Asset-Tracking und -Management
IoT-Sensoren, die an einzelnen Assets wie Werkzeugen, Maschinen und Fahrzeugen angebracht sind, erfassen und melden detaillierte Informationen über den aktuellen Zustand sowie darüber, wo und wie sie verwendet werden. Durch ein ganzheitliches Echtzeitbild der standortübergreifenden Assets können Bediener schnell nicht ausgelastete Geräte lokalisieren, drohende Probleme und Engpässe diagnostizieren und Werkzeuge und Teile einfach mobilisieren. Letztendlich ermöglicht die Anwendung von IoT für das Asset-Management Unternehmen, Wartungsaktivitäten und die Nutzungsdauer von Assets zu optimieren und gleichzeitig fehleranfällige manuelle Aufzeichnungen und übermäßige Bestellungen zu eliminieren.
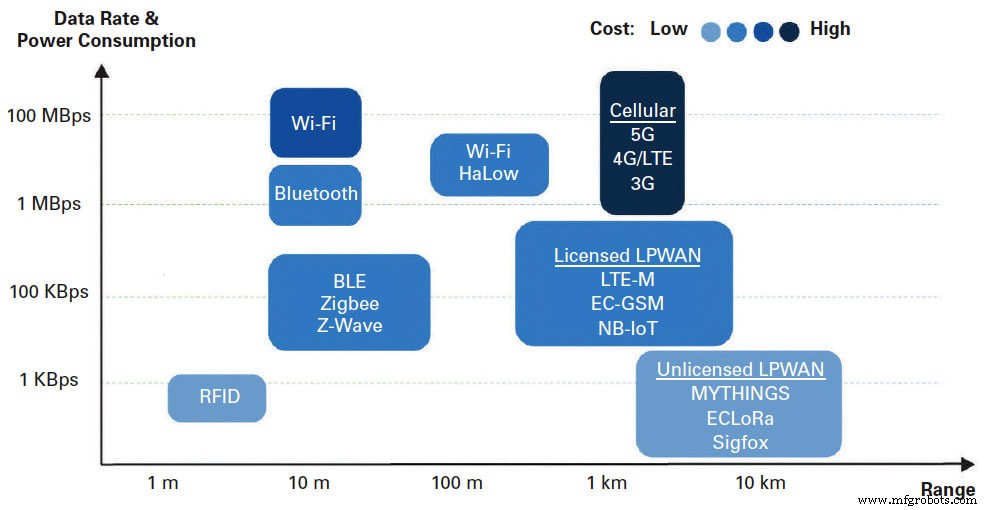
4. Fernüberwachung von Pipelines und Tanks
Tanks und Rohrleitungen sind in vielen Prozessindustrien kritische Anlagen. Das Überlaufen oder Austreten von chemischen Produkten und Gasen führt nicht nur zu Produktionsausfällen, sondern verursacht auch schwere Umweltschäden und gefährdet die öffentliche Sicherheit. Durch die Implementierung von Füllstands-, Vibrations-, Durchfluss- und Drucksensoren können Unternehmen den strukturellen Zustand ihrer weit verteilten Tanks und Rohrleitungen rund um die Uhr im Auge behalten und gleichzeitig manuelle Kontrollen reduzieren. Warnungen werden über potenzielle Verschüttungen, Lecks oder Brüche ausgegeben, die zu Katastrophen führen könnten. Es können auch Warnungen über niedrige Materialfüllstände in Tanks ausgegeben werden, damit diese rechtzeitig nachgefüllt werden können, um die Produktivität zu verbessern.
5. Facility Management
IoT ermöglicht die digitale Verwaltung und den Schutz kritischer Anlagen. IoT-fähige Aufzüge, Rauchmelder, Feuermelder und andere Einrichtungsressourcen in der gesamten Fabrik können regelmäßig Daten über ihren Batteriezustand oder „Lebens“-Status senden. Dies hilft Herstellern, zeitaufwändige manuelle Inspektionen einzusparen und gleichzeitig schnell auf alle Probleme zu reagieren, die die Produktionslinie unterbrechen könnten.
Zukunftssichere drahtlose Konnektivität für Qualität 4.0
Da die Datenerfassung in den meisten Industrieumgebungen eine inhärente Herausforderung darstellt, können IoT-Bereitstellungen oft überwältigend komplex, teuer und einschüchternd erscheinen. Es wird prognostiziert, dass es bis 2025 36,8 Milliarden aktive IIoT-Geräte geben wird, gegenüber 17,7 Milliarden heute. Da immer mehr Unternehmen versuchen, von neuen IoT-Anwendungen zu profitieren, ist es wichtig, die langfristige Zuverlässigkeit, Integrierbarkeit und Verwaltbarkeit des Kommunikationsnetzwerks zu berücksichtigen, wenn es skaliert wird, um Tausende von verbundenen Endpunkten aufzunehmen. Die Realität ist, dass alles darauf hinausläuft, die richtige IoT-Konnektivität für den richtigen Geschäftsfall auszuwählen.
Drahtlose Instrumentierung ist nicht unbedingt neu in der Fertigung, aber entscheidende Anforderungen in Bezug auf Reichweite, Leistung und einfache Integration schränken die praktikablen Optionen ein. Industrielle Überwachungsanwendungen könnten beispielsweise erfordern, dass täglich Millionen von Nachrichten von Tausenden von Sensoren gesendet werden. Dies erfordert eine hochgradig skalierbare und energieeffiziente Lösung, um den häufigen Austausch und die Entsorgung von Batterien zu vermeiden, die die Gesamtbetriebskosten schnell in die Höhe treiben können. Ebenso erfordern riesige, strukturell dichte Industrieanlagen eine zuverlässige drahtlose Kommunikation, die große Entfernungen zurücklegen und physische Hindernisse überwinden kann. Auch das traditionelle Design von Fertigungsanlagen bringt Herausforderungen mit sich. Drahtlose Lösungen müssen sich in ältere Geräte wie SPS integrieren lassen, um Datensilos aufzubrechen und Zugriff auf zuvor unzugängliche Informationen zu ermöglichen.
Legacy-Wireless-Technologien können mit den Reichweiten-, Leistungs- und Kostenanforderungen in IoT-Sensornetzwerken nicht Schritt halten. Herkömmliche Mobilfunkverbindungen (z. B. 3G, LTE usw.) und drahtlose lokale Netzwerke (Wi-Fi) sind zu teuer und energiehungrig, um kleine Datenmengen von einer großen Anzahl von Sensorgeräten zu übertragen. Andere Lösungen wie Bluetooth, Zigbee und Z-Wave haben eine stark eingeschränkte physische Reichweite; und obwohl viele von ihnen eine Mesh-Topologie verwenden, um ihre Abdeckung zu erweitern, ist Multi-Hop-Relaying stromaufwändig und erfordert eine komplexe Netzwerkplanung und -verwaltung. Daher eignen sich Mesh-Netzwerke bestenfalls für Anwendungen mit mittlerer Reichweite.
Low-Power-Wide-Area-Networks (LPWAN) sind insofern einzigartig, als sie diese Fallstricke überwinden und eine effiziente, erschwingliche und einfach zu implementierende Lösung für massive IoT-Netzwerke bieten. Die Attraktivität von LPWAN ergibt sich aus seinen beiden charakteristischen Merkmalen:große Reichweite und geringer Stromverbrauch. Während Wi-Fi und Bluetooth bestenfalls über zehn oder hundert Meter kommunizieren können, ist ein LPWAN in der Lage, Signale bis zu 15 km in ländlichen Gebieten und bis zu 5 km in städtischen, baulich dichten Gebieten zu übertragen. Darüber hinaus reduzieren leichtgewichtige, leistungsoptimierte Protokolle die Transceiver-Kosten und ermöglichen gleichzeitig eine sehr lange Batterielebensdauer für Sensorknoten.
Es ist jedoch wichtig zu beachten, dass die Servicequalität je nach LPWAN-Technologie variiert. Dies liegt hauptsächlich an zwei Gründen – ihrem Betrieb im lizenzfreien Spektrum und der Verwendung einfacher asynchroner Kommunikation, typischerweise reinem ALOHA (ein Knoten greift auf den Kanal zu und sendet eine Nachricht, wann immer es Daten zu senden gibt). Neben erheblichen Leistungsvorteilen erhöhen unkoordinierte Übertragungen in asynchronen Netzwerken die Wahrscheinlichkeit von Paketkollisionen und Datenverlusten erheblich. Da drahtlose IoT-Bereitstellungen und Funkverkehr in den lizenzfreien Sub-GHz-Bändern schnell zunehmen, sind Legacy-LPWANs möglicherweise mit ernsthaften Quality of Service (QoS) und Skalierbarkeitsproblemen verbunden, die durch Gleichkanalstörungen verursacht werden. In gleicher Hinsicht sind die Standardisierung und die zuverlässige Mobilitätsunterstützung weitere wichtige Faktoren, die nicht außer Acht gelassen werden dürfen.
Abschluss
Die Fähigkeit, verborgene Muster zu identifizieren, zukünftige Probleme vorherzusagen, Nutzung und Kosten vorherzusagen und Erkenntnisse aus IoT-Sensordaten abzuleiten, wird den industriellen Prozess für immer verändern. Während der Sektor seit einiger Zeit Kommunikationstechnologie einführt, tragen neue drahtlose Konnektivitäten wie LPWAN dazu bei, erheblich mehr Datenpunkte zu einem viel niedrigeren Preis online zu bringen. Inmitten der zunehmenden Herausforderungen der Branche kann die IoT-Implementierung ein Wendepunkt sein, um das Qualitätsmanagement und die betriebliche Effizienz auf die nächste Stufe zu heben und im Wettbewerb an der Spitze zu bleiben.
Dieser Artikel wurde von Wolfgang Thieme, Chief Product Officer, BehrTech (North York, ON, Kanada) geschrieben. Für weitere Informationen kontaktieren Sie Herrn Thieme unter wthieme@ behrtech.com oder besuchen Sie hier .
Sensor
- Wie Cloud-Anbieter die Perspektiven für das IoT-Daten- und Analysemanagement ändern
- Einfaches IoT – RaspberryPI HDC2010 wie es geht
- Wie IR-Sensor 2.0 die IoT-Technologie verbessern wird
- Wie IoT-gestützte Lager das Lieferkettenmanagement verändern – Teil 3
- Wie IoT-gestützte Lager das Lieferkettenmanagement verändern – Teil 1
- So füttern und pflegen Sie Ihre drahtlosen Sensornetzwerke
- Wie AR und IIoT die Fertigung verändern
- Wie drahtlose Energie die Fertigung verändert
- Wie Millennials die Fertigungsindustrie verändern
- Wie IoT Flottenmanagementsysteme unterstützt?