Sie verwenden es täglich. Aber was ist Polyethylen-Kunststoff?
Die 101 auf diesem allgegenwärtigen modernen Material
Polyethylen ist bei weitem die häufigste Art von Kunststoff für Verbraucher und wird in vielen alltäglichen Materialien verwendet. Es ist ein thermoplastisches Produkt, was bedeutet, dass es zu einer Flüssigkeit geschmolzen und dann viele Male wieder zu einem Feststoff abgekühlt werden kann. Unterschiedliche Verarbeitungsbedingungen führen zu unterschiedlichen Polyethylenqualitäten, die für sehr unterschiedliche Zwecke verwendet werden können – von flexibler Frischhaltefolie auf der einen Seite bis hin zu harten Abdeckungen für Pollerpfosten auf der anderen Seite.
Eine der attraktivsten Eigenschaften von Polyethylen ist seine Haltbarkeit. Es ist beständig gegen Ausbleichen und Absplittern und ist gleichzeitig unempfindlich gegen viele chemische Substanzen wie Säuren und Laugen. Polyethylen ist ein ausgezeichneter elektrischer Isolator. Es behält seine Eigenschaften bei extremer Kälte, kann aber bei hohen Temperaturen geschmolzen werden.
Polyethylen-Kunststoff:ein Kohlenstoff-Wasserstoff-Molekül
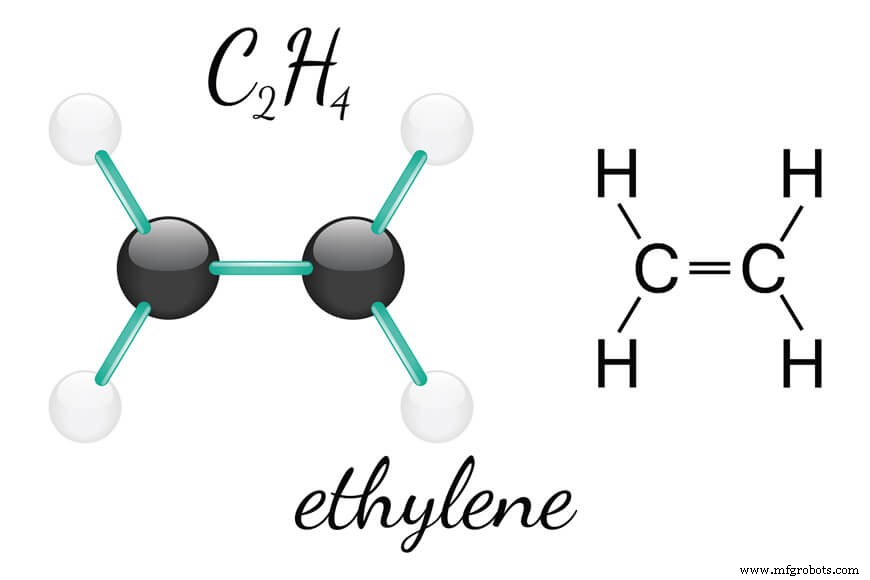
Molekülstruktur und allgemeine Eigenschaften
Polyethylen besteht aus Kohlenwasserstoffketten, wobei die grundlegendste Komponente das Ethylenmolekül ist, das aus 2 Kohlenstoff- und 4 Wasserstoffatomen besteht. Wenn Ethylenmoleküle in geraden oder verzweigten Ketten miteinander verbunden werden, entsteht Polyethylen. Bei diesem Prozess wird die Doppelbindung zwischen den 2 Kohlenstoffatomen gespalten und ein freies Radikal erzeugt, das sich mit dem nächsten Ethylenmolekül verbindet. Die Makromoleküle sind nicht kovalent verbunden, sondern werden durch zwischenmolekulare Kräfte in einer kristallinen Struktur zusammengehalten. Je geringer die Zahl der Seitenzweige, desto geringer die Kristallinität und damit die Dichte, was an den unterschiedlichen Eigenschaften der verschiedenen Polyethylentypen zu erkennen ist.
Polyethylen ist witterungsbeständig, kann aber bei längerer Sonneneinstrahlung spröde werden. Diese Einschränkung kann durch die Zugabe von UV-Stabilisatoren überwunden werden. Es kann entzündet werden und brennt weiter, nachdem die Zündquelle mit einer blauen Flamme mit gelber Spitze entfernt wurde, wodurch der Kunststoff abtropft. Die Oberflächenbeschaffenheit von Polyethylen verhindert ein Verkleben oder Bedrucken ohne Vorbehandlung. Polyethylen kann transparent, milchig-opak oder opak sein, abhängig von der Materialqualität, der Dicke des Produkts und dem Vorhandensein von Zusatzstoffen.
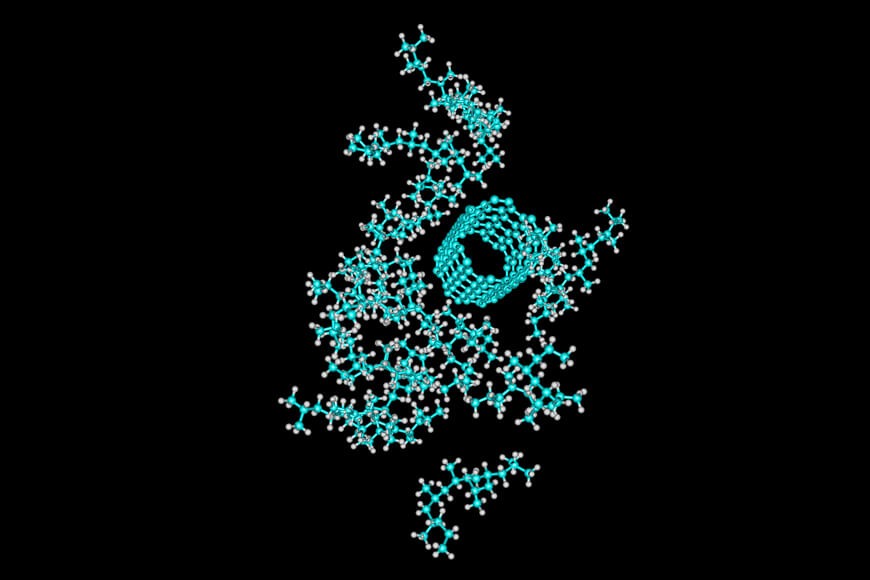
Klassifikationen von Polyethylen
Polyethylen niedriger Dichte (LDPE) wird mit langen und kurzen Verzweigungen in den Polymerketten gebildet. Das Vorhandensein dieser Verzweigungen verhindert, dass die Ketten zu eng zusammengepackt werden, und verleiht LDPE eine Flexibilität, die es für Anwendungen wie Plastiktüten, Kabelisolierung und Plastikfolie geeignet macht. LDPE ist sehr beständig gegen die meisten Chemikalien, einschließlich Säuren, Basen, Alkohole, Aldehyde, Ketone und Pflanzenöle. Es hat auch eine sehr geringe Wasseraufnahme.
Lineares Polyethylen niedriger Dichte (LLDPE) ist ähnlich wie LDPE, besteht aber aus weitgehend linearen Ketten mit vielen kurzen Seitenästen. Es wird oft durch Copolymerisation von Ethylen mit Alpha-Olefinen wie 1-Buten, 1-Hexen und 1-Octen hergestellt. Die Eigenschaften des Endprodukts können durch Anpassung der Zusammensetzungsformel manipuliert werden.
Polyethylen hoher Dichte (HDPE) besteht hauptsächlich aus geradkettigen Molekülen, die durch zwischenmolekulare Kräfte zusammengehalten werden. Das Fehlen von Seitenzweigen stellt sicher, dass die Ketten fest zusammengepresst sind. Diese hohe Dichte führt zu einem Produkt, das mäßig steif ist, wodurch es für Anwendungen wie Schneidebretter, Saftbehälter, Kunststoffholz und Spielzeug geeignet ist. HDPE hat eine gute chemische Beständigkeit und bleibt auch bei sehr niedrigen Temperaturen (-76 Grad Fahrenheit) zäh. Es hat eine wachsartige Oberflächenstruktur, die wetterfest ist.
Polyethylen mit ultrahohem Molekulargewicht (UWMPE) hat extrem lange Ketten und lässt sich zu Fäden mit höherer Zugfestigkeit als Stahl verspinnen. Die Stärke der zwischenmolekularen Kräfte zwischen den langen geraden Ketten erzeugt ein robustes Material mit einer sehr hohen Schlagfestigkeit. Es wird in Anwendungen wie kugelsicheren Westen verwendet. Wie andere Polyethylentypen ist UHMWPE gegen die meisten Chemikalien beständig, mit Ausnahme von oxidierenden Säuren. Es hat auch eine geringe Feuchtigkeitsaufnahme, aber seine selbstschmierenden Eigenschaften machen es sehr abriebfest.
Die American Society for Testing and Measurement (ASTM) legt Spezifikationen für verschiedene Polyethylenqualitäten fest, einschließlich Spezifikationen für verschiedene Anwendungen. Die wichtigsten Eigenschaften der verschiedenen Polyethylensorten sind in der folgenden Tabelle aufgeführt:
LDPE
HDPE
UHMWPE
Dichte (lb/in3)
.035
.035
.034
Wasseraufnahme, 24 Std. (%)
<0,01
0
0
Zugfestigkeit
1.800 – 2.200
4.600
3.100
Kerbschlagzähigkeit
Keine Pause
3
Keine Pause
Koeffizient der linearen Wärmeausdehnung (x10^-5 Zoll/Zoll/Grad F)
3
3
3
Max. Dauergebrauchstemperatur (def F)
160
180
180
Ca. Schmelztemperatur (Grad F)
230
260
280
Durchschlagsfestigkeit (V/mil) kurzzeitig, 1/8″ dick
460-700
450-500
900
LDPE
Dichte (lb/in3)
.035
Wasseraufnahme, 24 Std. (%)
<0,01
Zugfestigkeit
1.800 – 2.200
Kerbschlagzähigkeit
Keine Pause
Koeffizient der linearen Wärmeausdehnung (x10^-5 Zoll/Zoll/Grad F)
3
Max. Dauergebrauchstemperatur (def F)
160
Ca. Schmelztemperatur (Grad F)
230
Durchschlagsfestigkeit (V/mil) kurzzeitig, 1/8″ dick
460-700
HDPE
Dichte (lb/in3)
.035
Wasseraufnahme, 24 Std. (%)
0
Zugfestigkeit
4.600
Kerbschlagzähigkeit
3
Koeffizient der linearen Wärmeausdehnung (x10^-5 Zoll/Zoll/Grad F)
3
Max. Dauergebrauchstemperatur (def F)
180
Ca. Schmelztemperatur (Grad F)
260
Durchschlagsfestigkeit (V/mil) kurzzeitig, 1/8″ dick
450-500
UHMWPE
Dichte (lb/in3)
.034
Wasseraufnahme, 24 Std. (%)
0
Zugfestigkeit
3.100
Kerbschlagzähigkeit
Keine Pause
Koeffizient der linearen Wärmeausdehnung (x10^-5 Zoll/Zoll/Grad F)
3
Max. Dauergebrauchstemperatur (def F)
180
Ca. Schmelztemperatur (Grad F)
280
Durchschlagsfestigkeit (V/mil) kurzzeitig, 1/8″ dick
900
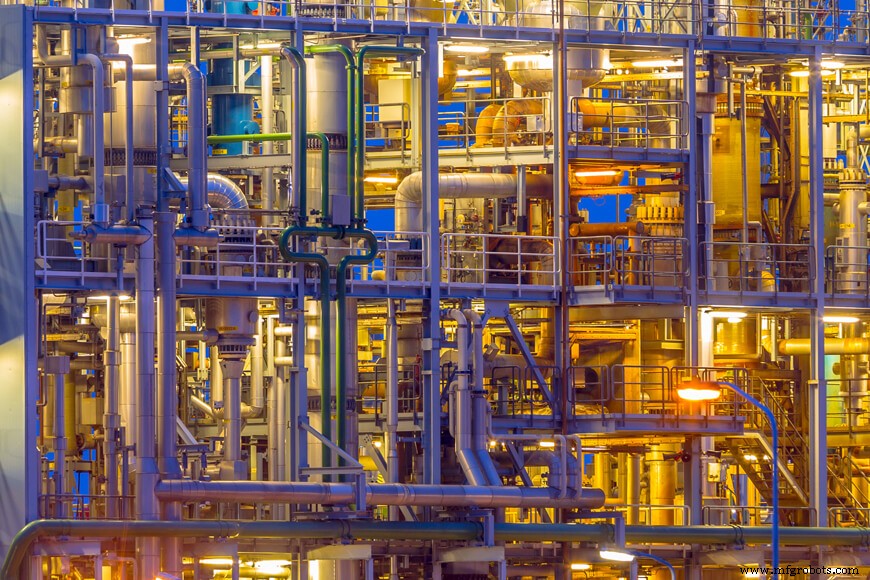
Wie wird Polyethylen-Kunststoff hergestellt?
Der Grundbaustein für Polyethylen ist das Ethenmolekül, bestehend aus 2 Kohlenstoffatomen und 4 Wasserstoffatomen. Ethen kommt in Erdgas vor und entsteht auch bei der Raffination von Rohöl. Eines der Produkte der ersten Stufe der Ölraffination ist Naphtha, das durch einen katalytischen Cracker verarbeitet wird, um Material mit höherer Oktanzahl herzustellen. Bei diesem Cracking-Prozess entsteht auch Ethen, das zur Weiterverarbeitung zu Polyethylen von anderen Produkten getrennt wird. Ethen ist ein Gas.
Je nach zu erzeugender Produktqualität gibt es unterschiedliche Verarbeitungsverfahren für Polyethylen.
LDPE wird durch Komprimieren des Ethengases auf einen Druck von 50.000 psi hergestellt, wonach es gekühlt und in einen Reaktor eingespeist wird. Dem Reaktor wird ein Initiator zugesetzt, der bewirkt, dass die Polymerisationsreaktion stattfindet. Ständiges Rühren des Materials im Reaktor sorgt für eine maximale Umwandlungsrate. Nach der Reaktion wird unverbrauchtes Ethen vom Produkt abgetrennt und zum Kompressor zurückgeführt. Das Polymer wird extrudiert, zu Pellets geschnitten und getrocknet, bevor es in Lagersilos gelangt. Pellets werden normalerweise für den Versand an Kunden verpackt, wo sie geschmolzen und zu fertigen Verbraucherprodukten verarbeitet werden.
HDPE wird in einem katalytischen Verfahren hergestellt, wodurch der Herstellungsprozess von Polyethylen bei niedrigeren Temperaturen und Drücken erfolgen kann. Ziegler-Natta- und Chromkatalysatoren waren die ersten verwendeten Katalysatoren, aber es werden ständig neuere Katalysatortypen entwickelt, um Produktionsprozesse und Eigenschaften von Produkten zu verbessern. Einige Prozesse mischen sogar verschiedene Arten von Polyethylen in einer Charge, wodurch die Grenzen zwischen den ehemals unterschiedlichen Produktqualitäten verschwimmen.
LLDPE wird ebenfalls in einem katalytischen Prozess unter Zugabe von Copolymeren wie Alpha-Olefinen (Butan, Hexan) hergestellt. Die Molekülstruktur von LLDPE ist eine lange Kette mit vielen kurzen Verzweigungen.
UHMWPE wird unter Verwendung von Metallocenkatalysatoren hergestellt, was zu extrem langen Kohlenwasserstoffketten führt (über 100.000 Monomerkomponentenmoleküle). Ein Sekundärprozess namens Gelspinnen nimmt ein erhitztes UHMWPE-Gel und extrudiert es durch eine Spinndüse. Das Produkt wird in einem Wasserbad gekühlt. Dieser Spinnprozess ergibt eine Faser mit einem hohen Grad an molekularer Orientierung (95 %), was ihr die extrem hohe Reißfestigkeit verleiht.
Kunststoffformteil aus Polyethylen
Polyethylen kommt vom Werk in Pelletform und wird gemäß seinen Spezifikationen sortiert. Kunden verwenden diese Pellets als Rohstoffe in ihren eigenen Herstellungsprozessen, bei denen sie durch Anwendung von Hitze und Druck geschmolzen und dann der flüssige Kunststoff in seine endgültige Form gebracht werden. Je nach Qualität des Rohmaterials und der Art des gewünschten Endprodukts gibt es verschiedene Verfahren zum Formen von Polyethylen:
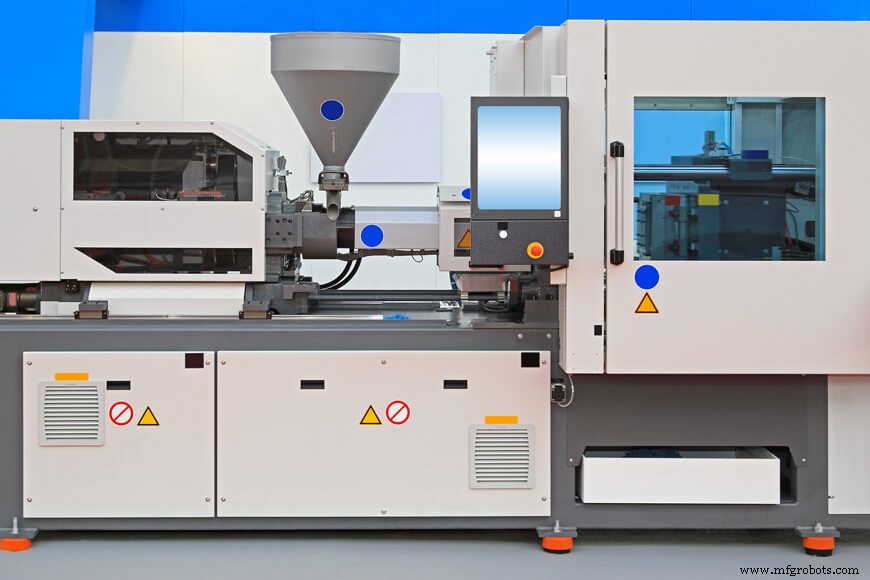
- Spritzguss
Spritzgießen ist eines der beiden gängigsten Verfahren zur Herstellung von Endprodukten aus Polyethylen. Pellets werden in einen beheizten Zylinder eingeführt, wo eine rotierende Schnecke den schmelzenden Kunststoff durch einen Einlauf in eine Form drückt. Eine festgelegte Menge Polyethylen wird mit einem hohen Druck von 10.000 bis 30.000 psi eingespritzt. Nach Abschluss des Einspritzvorgangs wird die Form abgekühlt, bevor sie geöffnet und das fertige Produkt entnommen wird. Dies ist der typische Prozess zur Herstellung von Massenartikeln wie Eimern und Flaschenverschlüssen. - Blasformen
Blasformen wird verwendet, um Produkte wie Flaschen und Spritzen herzustellen, bei denen es einen Hohlraum im Produkt gibt. Beim Blasformen wird im ersten Schritt ein Vorformling mit einem Standard-Spritzgusswerkzeug um einen Kernstift gespritzt. Sobald der Vorformling abgekühlt ist, wird er in die Mitte einer zweiten Form gelegt. Der Vorformling wird erneut erhitzt und Druckluft wird über den Kernstift zugeführt, um den geschmolzenen Kunststoff gegen die Innenwände der endgültigen Form zu blasen, wodurch der innere Hohlraum erzeugt wird. Nach dem Abkühlen wird der Stift entfernt. - Formpressen
Das Formpressen wird hauptsächlich für duroplastische Kunststoffe verwendet, also Kunststoffe, die nicht mehrfach erhitzt und umgeformt werden können. Pulver und andere Materialien können der Mischung hinzugefügt werden, um besondere Eigenschaften zu erzielen oder das Endprodukt zu stärken. Bei diesem Verfahren wird der Kunststoff durch erhitzte Platten geformt, die Druck auf den Kunststoff ausüben. Die kurze Zykluszeit in diesem Verfahren macht es attraktiv für Massenanwendungen wie Teile für die Automobilindustrie. - Spritzpressen
Beim Spritzpressen wird der Kunststoff in den geschmolzenen Zustand erhitzt, bevor er in einen Formpressprozess überführt wird. Wenn viele kleine Löcher oder Metalleinsätze vorhanden sind, bildet sich der geschmolzene Kunststoff leichter um diese herum, ohne die Ausrichtung zu stören. - Folienhinterspritzen
Bei diesem Verfahren wird ein Folien- oder Stoffmaterial in eine Spritzgussform eingelegt, bevor der Kunststoff eingespritzt wird, sodass die Folie im fertigen Produkt eingeschlossen wird. - Extrusion
Neben dem Spritzgießen ist die Extrusion eine der beliebtesten Methoden, um Polyethylen in eine gewünschte Form zu bringen. Pellets werden über einen Trichter in eine beheizte Kammer gefördert, wo eine Schnecke den schmelzenden Kunststoff vorantreibt. Am Ende der beheizten Kammer befindet sich ein Stempel, der den Kunststoff beim Austritt in die Atmosphäre formt. Dieser Prozess wird verwendet, um Endlosbleche, Rohre, Kabel, Rohrleitungen und mehr herzustellen. Das fertige Produkt landet auf einem Förderband, wo es luftgekühlt wird (manchmal unterstützt durch Gebläse). Das Produkt kann auch in Wasser eingelegt werden, um den Abkühlungsprozess zu beschleunigen. - Gasspritzguss
Beim Gasinjektionsguss wird ein Standard-Spritzgussverfahren um einen zusätzlichen Schritt erweitert. Die Form wird zu 70 % des gesamten erforderlichen geschmolzenen Kunststoffs gefüllt, dann wird Gas in die Kammer gepumpt, um den Kunststoff in das Ende der Form zu drücken. Der Nettoeffekt besteht darin, dass das Endprodukt aufgrund des Gasblasens ein hohles Zentrum hat und weniger Kunststoff verwendet wird. - Rotationsformen
Pulverförmiger Kunststoff wird in eine Hohlform gegeben und an einer rotierenden Nabe befestigt. Die Nabe dreht sich in einem Ofen um 2 Achsen, wodurch der Kunststoff schmilzt und die Innenwände der Form beschichtet. Die Nabe dreht sich während des Kühlzyklus weiter, bei dem häufig Wasser auf die Außenseite der Form gesprüht wird. Schließlich wird das fertige Produkt entnommen. Der Vorteil dieser Methode ist die Einfachheit der Formen, der fehlende Druck und das Fehlen von Schweißnähten und Verbindungen im fertigen Produkt. - Strukturschaumguss
Geschmolzener Kunststoff wird zusammen mit komprimiertem Gas in einen Akkumulator eingespritzt, um im Kunststoff einen Schaumeffekt zu erzeugen. Aus dem Akkumulator wird der geschäumte Kunststoff in die Form gespritzt. Durch den Druckabfall vom Druckspeicher zur Form dehnt sich der Kunststoff aus und füllt die Form. Nach dem Abkühlen ist die Haut glatt, aber der innere Kern ist aufgeschäumt, was dem Endprodukt eine hohe Steifigkeit verleiht. - Thermoformen
Thermoformen und Vakuumformen werden durchgeführt, indem man eine Plastikfolie nimmt, sie erhitzt, bis sie weich ist, und sie dann über eine Form drapiert. In einigen Fällen wird positiver Luftdruck angelegt, während in anderen Fällen ein Vakuum erzeugt wird, um den Kunststoff gegen die Form zu drücken. Nach dem Abkühlen wird das fertige Produkt ausgetragen. - Reaktionsspritzgießen
Reaktionsspritzguss ist eine neuere Technologie zur Formgebung von Kunststoffprodukten. Der Kunststoff wird bei einer niedrigeren Temperatur als beim herkömmlichen Spritzgießen mit anderen Komponenten gemischt. Innerhalb der Form tritt eine exotherme Reaktion auf, um den Kunststoff unter Druck zu setzen. Da niedrigere Temperaturen und Drücke erforderlich sind, werden die Produktionskosten gesenkt. Der Mischung können auch Glasfasern zugesetzt werden, um dem Endprodukt Festigkeit zu verleihen.
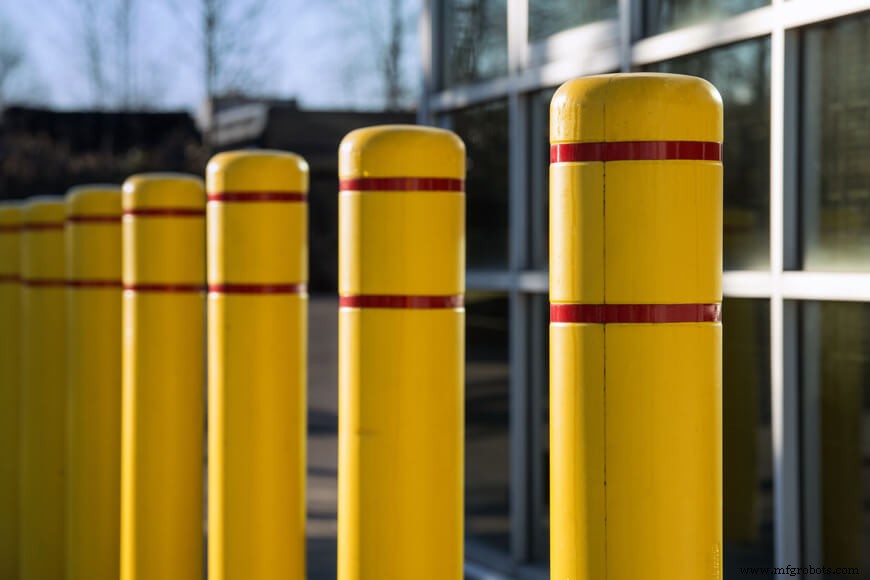
Wartung
Polyethylen ist ein sehr haltbares Material, das sich nicht leicht abnutzt oder schwächt. Eine anhaltende Sonneneinstrahlung kann jedoch im Laufe der Zeit zu einer Versprödung des Produkts führen. Für Rohrleitungen oder Tanks, die Witterungseinflüssen ausgesetzt sind, wird ein Inspektionszyklus empfohlen, um Spinnweben oder Risse aufgrund von Sprödigkeit zu identifizieren.
Die Langlebigkeit und Haltbarkeit von Polyethylen-Produkten ist so gut, dass viele Hersteller sie als wartungsfrei bezeichnen.
Anwendungen
Polyethylen ist die häufigste Form von Thermoplasten, die in Verbraucherprodukten verwendet wird, und hat eine Vielzahl von Anwendungen. Im Folgenden sind einige der häufigeren Verwendungen aufgeführt:
- Lebensmittelverpackungsmaterial: Da Polyethylen so widerstandsfähig gegen Wasseraufnahme und chemische Beschädigung ist, ist es als sicher für Lebensmittelverpackungen zertifiziert.
- Medizinische Schläuche: Die mangelnde Porosität von Polyethylen macht es aufgrund der Kontaminationsbeständigkeit zu einem idealen Material für Katheter und andere medizinische Produkte.
- Eimer, Flaschen und Behälter: Aufgrund der Härte von Kunststoff und seiner Beständigkeit unter Belastung eignet es sich für Konsumgüter.
- Kugelsichere Westen: UHMWPE-Fasern haben eine hohe Zugfestigkeit und sind dennoch sehr leicht – was sie ideal für Sicherheitsanwendungen macht.
- Hochfeste Kabel: Sie sind leicht und daher einfach zu installieren, aber robust und eignen sich daher für komplexe industrielle Anwendungen.
Recycling
Kunststoffprodukte haben wegen ihrer Auswirkungen auf die Umwelt viel schlechte Presse erhalten, aber wie bei den meisten potenziellen Schadstoffen ist es das Verhalten des Menschen – nicht das Produkt selbst – das zu Umweltschäden führt. Polyethylen ist nicht biologisch abbaubar, was es zu einem ungeeigneten Material für die Entsorgung auf Deponien macht.
Die Eigenschaften von Polyethylen machen es jedoch ideal für das Recycling, da es eingeschmolzen und zu einem anderen Produkt umgeformt werden kann. Darüber hinaus bedeutet seine Beständigkeit gegen chemische Kontamination und Absorption von Flüssigkeiten, dass das recycelte Produkt nicht viele Verunreinigungen enthält. Manchmal werden recycelte und neue Materialien im Herstellungsprozess von fertigen Konsumgütern miteinander vermischt. Recycling-Nummer #2 gilt für HDPE und #4 für LDPE; Viele Recyclinganlagen können diese beiden Qualitäten zur Wiederverwendung verarbeiten.
Viele Materialien, die zuvor als Umweltgefahren galten (z. B. Gummi), werden zunehmend recycelt, da sich die Menschen zu einem nachhaltigen Lebensstil bewegen und sich Recyclingtechnologien entwickeln.
Verwandte Artikel
- Immer noch neugierig? Check out:Was ist Polyurethan-Kunststoff?
- Und das Plastik passt! Siehe dazu Flexible Poller im Vergleich zu Verkehrsbegrenzern.
Quellen
- BPF. „Kunststoffprozesse“
- Kunststoffindustrie. „Methoden der Kunststoffverarbeitung“
- Polymer-Datenbank. „Polyolefine“
- Amerikanischer Chemierat. „Lebenszyklus eines Kunststoffprodukts“
- EBI. „Polyethylen“
- Britannika. „Polyethylen“
Metall
- Welche Metall-3D-Druckpulver können Sie im Jahr 2020 verwenden? [Leitfaden]
- Warum müssen Sie landwirtschaftliche Farbstoffe verwenden?
- Was ist OSGi und was bringt es Ihnen?
- Bluetooth Low Energy (LE)-Bereich:Was können Sie in diesem Anwendungsfall erwarten?
- Was kann man mit einem Faserlaser schneiden?
- Was ist Plastik? FAQs
- Was meinst du mit malen?
- Industrielle Kupplungen:Was sind sie und wie werden sie verwendet?
- Verstehen, was Naval Brass für Sie tun kann
- Bronzeguss und was Sie wissen müssen