Studie zum Effekt der Aufprallrichtung auf den nanometrischen Schleifprozess mit Molekulardynamik
Zusammenfassung
In der modernen Ultrapräzisionsbearbeitung spielt das Schleifstrompolieren eine wichtige Rolle. Ultrafeine Partikel, die im Medium der abrasiven Strömung suspendiert sind, entfernen das Material im Nanobereich. In diesem Beitrag werden dreidimensionale Molekulardynamik (MD)-Simulationen durchgeführt, um den Einfluss der Schlagrichtung auf den Schleifprozess während des Schleifflusspolierens zu untersuchen. Die Molekulardynamik-Simulationssoftware Lampps wurde verwendet, um das Schneiden von einkristallinem Kupfer mit SiC-Schleifkörnern bei verschiedenen Schnittwinkeln (0 o –45 o ). Bei konstantem Reibungskoeffizienten fanden wir einen direkten Zusammenhang zwischen Schnittwinkel und Schnittkraft, der letztendlich die Anzahl der Versetzungen bei der Fließbearbeitung erhöht. Unsere theoretische Studie zeigt, dass ein kleiner Schnittwinkel zur Verbesserung der Oberflächenqualität und zur Reduzierung interner Fehler im Werkstück von Vorteil ist. Es besteht jedoch kein offensichtlicher Zusammenhang zwischen Schnittwinkel und Reibungskoeffizient.
Hintergrund
In der modernen Ultrapräzisionsbearbeitung spielen Materialabtragstechnologien eine wichtige Rolle in der Mikroelektronik, der Mikromechanik und der Herstellung optischer Elemente. Der Bedarf an miniaturisierten Geräten mit hoher Maßhaltigkeit und Oberflächenqualität macht Ultrapräzisionsprozesse zur bevorzugten Wahl in dem genannten Bereich [1]. Darüber hinaus liegen die Änderungen der Oberflächenkomponenten und der unterirdischen Struktur im Nanometerbereich. Die Schleifpartikelfluss-Poliertechnologie spielt in vielen Bereichen der Präzisionsbearbeitung eine wichtige Rolle und dient ebenso wie andere nicht-traditionelle Finishing-Technologien zur Verbesserung der Oberflächenqualität. Diese Technologie hat aufgrund ihrer bedeutenden Rolle viele Forscher angezogen. E. Uhlmann und andere Forscher haben über die Computersimulation des Schleifkornpolierens von Keramikoberflächen für die geplanten Experimente berichtet, um den Schleifflüssigkeitsfluss verschiedener Bearbeitungsfaktoren auf die Wirkung von Schneidstoffen zu überprüfen [2]. Sehijpal Singh und andere Forscher verwenden die Abrasiv-Fluss-Poliertechnologie zum Schneiden von Kupfer- und Aluminiummaterialien. Bei der rasterelektronenmikroskopischen Analyse fanden sie eine tiefe Rillenoberfläche ihres Werkstücks [3]. G. Venkatesh und andere Forscher haben über eine ultraschallunterstützte Schleifkorn-Poliertechnologie für das konische Zahnrad auf der komplexen Oberfläche des Endbearbeitungsprozesses berichtet. Bei dieser Technik ist die Schleifkorngeschwindigkeit höher als beim herkömmlichen Schleifkornfluss, um mit der Oberfläche des Werkstücks zu kollidieren, was die Bearbeitungseffizienz verbessern kann. Aufgrund ihrer experimentellen und theoretischen Methoden stellten sie fest, dass diese Technologie eine der besten Optionen für die Endbearbeitung von Zahnradblättern ist [4, 5]. K. Kamalet al. untersuchten die rheologischen Eigenschaften der Schleifflüssigkeit in der Flüssigkeit Schleifmittelviskosität, Schergeschwindigkeit und Kriechzeit [6]. Allerdings basieren die meisten Studien zum Schleifen des Fließschleifens auf der Makroebene und nur sehr selten wurde der Mikroebene Aufmerksamkeit geschenkt. Beim Schleifprozess fließen die Schwebstoffe des Mediums mit einer bestimmten Geschwindigkeit entlang des Mediums unter dem Aufprall der mikroschneidenden Werkstückoberfläche (Abb. 1).
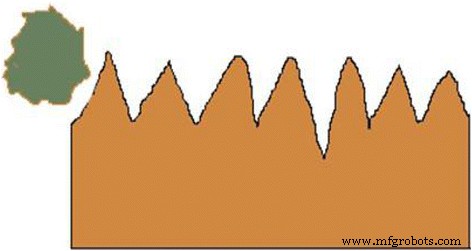
Skizze des abrasiven Schneidwerkstücks. Alle Abbildungen beziehen sich auf die Wirkung des Einflusses der Richtung auf den abrasiven nanometrischen Schneidprozess mit Molekulardynamik. Abbildung 1 ist die Skizze eines abrasiven Schneidwerkstücks. Beim Polierprozess mit abrasivem Fluss fließen die suspendierten Partikel im Medium mit einer bestimmten Geschwindigkeit entlang des Mediums unter dem Aufprall der mikroschneidenden Werkstückoberfläche
Da die Form der Schleifkörner nicht regelmäßig ist, haben sie bestimmte Kanten und Ecken, die ähnlich wie das Werkzeug auf die Oberfläche des Werkstücks einwirken. Aber der Schneidprozess ist auf der atomaren Skala, was sich offensichtlich vom Materialabtragsprozess unterscheidet. Ein nanoskaliges Schneiden umfasst wenige Nanometer oder weniger der Materialoberfläche, aber es ist sehr schwierig, diesen Prozess experimentell zu beobachten. Daher ist die MD-Simulation als theoretische Untersuchungsmethode sehr nützlich bei der Untersuchung des nanometrischen Schneidprozesses. Molekulardynamik als Computersimulationstechnik, die eine zeitbasierte statistische Mechanikmethode verwendet, um die Wechselbeziehung von Atomen für die Vorhersage und Analyse von Bedingungen zu untersuchen. Dies ist auch ein leistungsstarkes Werkzeug zur Simulation und zum Verständnis von Materialabtragsprozessen. In der Literatur gibt es zahlreiche Studien zu MD als Werkzeug zur Untersuchung der Präzisionsbearbeitung. Oluwajobi und Chen haben umfangreiche Arbeiten zur MD-Simulation der nanoskaligen Kupferbearbeitung durchgeführt [7]. In ihren Studien untersuchten sie verschiedene Parameter für die Nanobearbeitung wie minimale Schnitttiefe, Geometrie und interatomares Potenzial [8]. Darüber hinaus waren die Ergebnisse von MD-Simulationen in der Vergangenheit auch erfolgreich, um eine Reihe von Problemen im Zusammenhang mit dem nanometrischen Schneidprozess von spröden Materialien wie Silizium zu lösen [9]. Komanduriet al. führten eine MD-Simulation für das nanometrische Schneiden von Einkristallen aus reinem Silizium ohne Defekte unter Verwendung des Tersoff-Potentials durch. Sie untersuchten die Auswirkungen von Spanwinkel, Schnittbreite, Schnitttiefe und Freiwinkel auf den Materialabtrag und die Oberflächenerzeugung [10]. Goel et al. untersuchten die atomistischen Aspekte der duktilen Reaktion von SiC während des nanometrischen Schneidprozesses. Sie entdeckten das Vorhandensein eines sp3-sp2-Ordnungs-Unordnungs-Übergangs, der schließlich zur Graphitisierung von Diamant führte [11]. Cai et al. verwendeten MD, um das Schneiden von Silizium im Nanomaßstab im duktilen Modus zu untersuchen. Sie berichteten über die Werkzeugschneide und deren Auswirkungen auf die Schubspannung im Werkstückstoff [12]. Arafinet al. hat die Wirkung des Schneidkantenradius beim Schneiden von Siliziumwafern im duktilen Modus im Nanomaßstab diskutiert [13]. Auch verschiedene andere Forscher haben die unterschiedlichen Bedingungen bei der Nanobearbeitung von Silizium mithilfe von MD-Simulationen hervorgehoben. Dort werden Untersuchungen zu Schnittkräften, Schnitttiefe, Temperatur, Schubspannung und anderen Parametern durchgeführt. Allerdings fehlt es in diesem Bereich an adäquaten experimentellen Validierungen. Qihong Fanget al. untersuchten den Wechselwirkungsmechanismus von Versetzungen in verschiedenen heterogenen Materialien mit unterschiedlichen Skalen sowie die Versetzung und den Zusammenhang zwischen Materialzähigkeit und Bruchschäden. Sie verwenden molekulardynamische Simulationen, um die Nanoeindrückung auf drei verschiedenen Kristallstrukturen zu untersuchen, darunter einkristallines, polykristallines und nanozwillingspolykristallines Kupfer. Mit zunehmender Ritzrate steigen Ritzkraft und Werkstücktemperatur aufgrund starker plastischer Verformung und großem Spanvolumen kontinuierlich an, was zu Versetzungsschlupf, GB-Schlupf und Zwillings-/Entzwillingsbildung führt [14, 15].
Methoden/Experimentelle
Beim Abrasiv-Flow-Polier-Experiment wurde das Werkstück normalerweise mit SiC-Schleifmittel geschnitten. Nachdem das Modell der SiC-Schleifkörner etabliert war, wurde die molekulardynamische Simulation des Werkstücks mit der Software Lampps durchgeführt. Das Modell von zwei SiC-Schleifschneid-Monokristall-Kupfer mit unterschiedlichen Winkeln wurde konstruiert. Ein Simulationsmodell eines SiC-Schleifkorns beim Crashschneiden von einkristallinem Kupfer ist in Abb. 2 gezeigt.
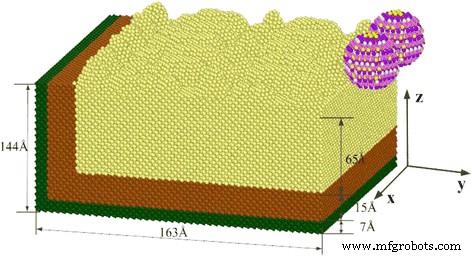
Simulationsmodell des SiC-Schleifschneidens von einkristallinem Kupfer. Abbildung 2 zeigt das Simulationsmodell des SiC-Schleifschneidens von einkristallinem Kupfer; wir haben zwei SiC-Schleifmittel zum Schneiden von einkristallinem Kupfer gebaut. Beim Abrasiv-Flow-Polier-Experiment wurde das Werkstück normalerweise mit SiC-Schleifmittel geschnitten. Nach der Konstruktion des SiC-Schleifmodells wurde die molekulardynamische Simulation des Werkstücks durchgeführt. Das Modell von zwei SiC-Einkristall-Kupfer-Schneidschneiden mit unterschiedlichen Winkeln wurde konstruiert
Die Größe des Modells ist in Abb. 2 dargestellt, während die Anzahl der simulierten Atome 159.020 betrug. Der Schleifradius beträgt 15 Å, die Gesamtzahl der C-Atome und Si-Atome in den Schleifkörnern beträgt 1406. Die Zahl der Kohlenstoff- und Siliziumatome betrug 681 bzw. 725. Die Relaxationsschrittzahl ist für das simulierte Gleichgewichtsensemble auf 10.000 Schritte eingestellt, Kollisionssimulationsschritte auf 100.000 Schnittschritte, jeder Simulationsschritt betrug 0,001 ps, Schnittsimulation, die SiC-Schleifpartikel in Schnittrichtung Geschwindigkeit von 80 m/s. AFM-Analysewert Körner kollidieren Mikrobearbeitungswerkstück während des Polierens, SiC-Schleifkörner, um die molekulare Kollisionsdynamik bei verschiedenen Winkeln des Schneidprozesses zu untersuchen. Beim abrasiven Fließschneiden nimmt die Schnittkraft mit zunehmender Schnittgeschwindigkeit zu und die Größe der Schnittkraft beeinflusst direkt die Schnittwirkung. Daher hat die Wahl einer angemessenen Schnittgeschwindigkeit einen wichtigen Einfluss auf die Schnittqualität. Um eine hohe Schnittqualität zu erzielen, haben wir die Schnittgeschwindigkeit von 80 m/s gewählt, da sie die Schnittkraft erzeugt, die die Wechselwirkung zwischen den Werkstückatomen schnell zerstören kann [16].
In Molekulardynamiksimulationen bei niedrigen Schnittgeschwindigkeiten wie 10 m/s werden atomare Verschiebungskarten und das Muster, wie die Schnittkraft von Siliziumkarbid-Schleifpartikeln und Schnittwinkel mit der Simulationsschrittgröße variieren, wie in den Fig. 1 und 2 gezeigt. 3 und 4. Da die Schnittgeschwindigkeit zu gering ist, reicht auch die Schnittkraft nicht aus, was zu weitaus geringeren Verformungen und Verschiebungen des Gitters führt. Insgesamt ist die Schnittleistung gering und die Schnittqualität relativ schlecht. Im Gegensatz dazu können bei einer Schnittgeschwindigkeit von bis zu 80 m/s im mikroskopischen Experiment chemische Bindungen zwischen Kupferatomen schnell und effektiv aufgebrochen werden, um das Ziel eines sofortigen qualitativ hochwertigen Schneidens zu erreichen. Daher sind nach umfassender Analyse 80 m/s Schnittgeschwindigkeit für die Simulation sinnvoll.
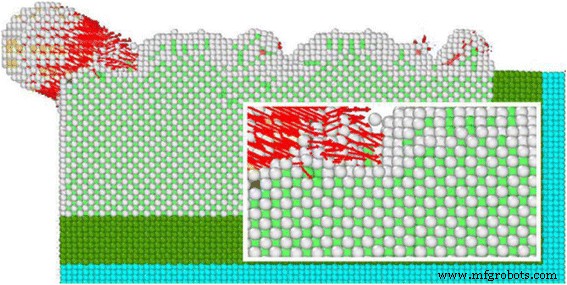
Atomare Verschiebung mit niedriger Geschwindigkeit
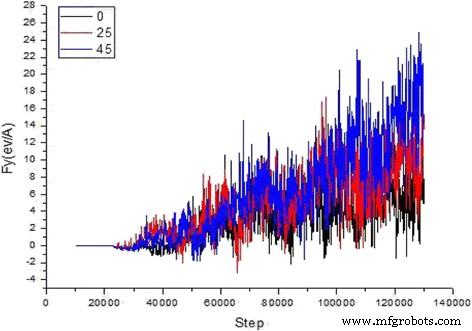
Die Beziehung zwischen der Schnittkraft, dem Schnittwinkel und dem Simulationsschritt
Um die Machbarkeit und Glaubwürdigkeit zu simulieren, wählen wir eine sinnvolle empirische Potentialfunktion, um die interatomaren Potentiale von Atomen zu berücksichtigen. Entsprechend den verschiedenen Objekten können wir die Potentialfunktion in eine Paarpotentialfunktion und eine Vielteilchenpotentialfunktion unterteilen. Die beiden Modelle zwischen einkristallinem Kupfer und abrasiven Körnern beschreiben die interatomaren Potentiale von Atomen zwischen ihnen durch das Morsepotential [17], das EAM-Potential wird verwendet, um die interatomaren Potentiale von Atomen zwischen Kupferatomen zu beschreiben [18,19,20], und die Wechselwirkung zwischen SiC-Partikeln wird mit dem Tersoff-Potential beschrieben [21].
Während des Polierprozesses ist die Kollisionsrichtung der Schleifkörner im Medium zufällig; ihre Bahnen verlaufen nicht genau entlang der Oberfläche des Werkstücks. Beim Mikroschneidprozess ist die Schnittrichtung der Schleifkörner nicht immer orthogonal zum Werkstückstoff. Der Schnittwinkel bezeichnet den Grad des Winkels zwischen der Schnittrichtung des Schleifkorns und der Horizontalebene. Positiv ist es, wenn sich Partikel der Werkstückoberfläche nähern. Die Skizze des Schnittwinkels ist in Abb. 5 dargestellt.
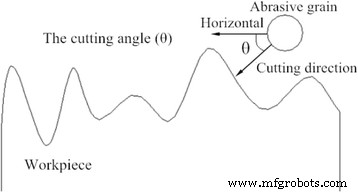
Die Skizze des Schnittwinkels. Abbildung 5 zeigt die verschiedenen Schnittwinkel beim Schneiden der Schleifkörner. Schleifkorn aus verschiedenen Richtungen beim Schneiden des Werkstückmaterials, das Material hat eine andere Leistung und Bearbeitungsqualität
In dieser Studie wird die MD-Simulation verwendet, um Multi-Schleifmittel mit unterschiedlichen Aufprallrichtungen des geschnittenen monokristallinen Kupfers zu simulieren. Wie in Abb. 5 gezeigt, liegt der Schnittwinkel zwischen 0° und 45°, während die Oberfläche des Kupferwerkstücks rau ist.
Ergebnisse und Diskussion
Analyse der Kollision der SiC-Schleifschneidmechanik
Der Einfluss des Siliziumkarbid-Schleifmittels auf das Schneiden von einkristallinem Kupfermaterial wird durch Zerstörung der Gitterstruktur eines Einkristalls aus Kupfermaterial erreicht. Während des Durchschlags wurden Wechselwirkungen zwischen Kupferatomen, die Scherspannung, die von C, Si-Atomen von SiC-Schleifpartikeln auf die Cu-Atome des Werkstückmaterials ausgeübt wird, als Schnittkraft identifiziert, die ein wichtiger physikalischer Parameter dafür ist, dass die Schnittkraft spiegelt den Entfernungsprozess von einkristallinem Kupferwerkstückmaterial zutiefst wider. Wie bereits erwähnt, gibt es einen großen Unterschied zwischen Mikro- und Makro-Schneidkraft. Im Allgemeinen ist die Makroschneidkraft die Summe aus Schneid- und Schleifkraft, während beim Mikroschneiden die Schneidkraft durch die Wechselwirkungen zwischen den Schleifkörnern und den Atomen des Werkstücks erzeugt wird.
In Abb. 6 haben wir die Veränderungen der Scherspannung von Schleifkörnern in verschiedenen Richtungen, die Wirkung der Scherspannung mit verschiedenen Richtungen und die Verteilung der Schnittkräfte entlang verschiedener Schnittwinkel gezeigt.
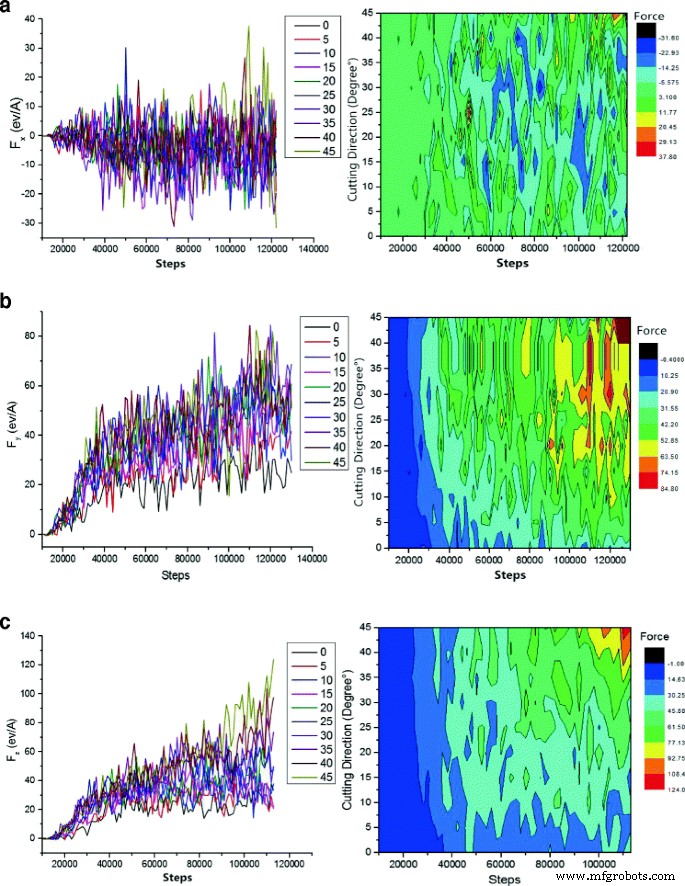
Wie sich Schnittwinkel und Simulationsschrittweite auf die Schnittkraft auswirken. Abbildung 6 zeigt die SiC-Schleifschnittkraft und das Schnittwinkel- und Simulationsschrittdiagramm, mit zunehmender Schnitttiefe nimmt die Anzahl der Kristallstrukturzerstörung zu, der Maximalwert der Schnittkraftschwankung wird ebenfalls größer. a [100] Richtung der Schnittkraft. b [010] Richtung der Schnittkraft. c [001] Richtung der Schnittkraft
Die Siliziumkarbid-Schleifkörner schneiden und prallen auf einkristallines Kupfermaterial in verschiedenen Winkelkanten wie [010] und [100] auf. Die Schnittkräfte entlang der Richtungen [001] und [010] waren Scherkräfte. Bei weiterer Simulation nahm die Schnitttiefe allmählich zu, was die Schnittkräfte entlang der Richtung [001] und [010] anhaltend erhöht hat. Bis zu einer bestimmten Grenze schwankten diese Kräfte jedoch, wie aus Abb. 6 ersichtlich ist. Wenn sich abrasive Partikel auf die Materialien des Werkstücks zubewegten, änderte sich die Wechselwirkung (von Anziehung zu Abstoßung) zwischen den äußersten Kupferatomen und den Atomen vollständig von SiC (Si und C). Anfänglich waren beim Schleifen des Werkstückmaterials die Schnittkräfte aufgrund der abstoßenden Kräfte von Kupferatomen unzureichend. Für den Endbearbeitungsprozess sollten die Schnittkräfte ausreichend hoch sein, damit die Schleifkörner die chemischen Bindungen in Kupferatomen leicht brechen können, um sich frei zu bewegen. Darüber hinaus hat das Schnitttiefeninkrement direkte Beziehungen zu den atomaren Wechselwirkungen. Als sich die Atome zu stapeln begannen, erhöht sich die Schnittkraft beständig, bis die Schleifpartikel in das Werkstück eindringen, was eine konstante Schnittkraft erforderte. In diesem relativ stabilen Stadium wurde die Schnittkraftschwankung dem Grad der Gitterverformung, der Gitterrekonstruktion, der amorphen Phasenänderung und der Erzeugung von Spänen unterworfen. Während die Schleifkörner entlang der Schneidrichtung marschierten, wurde eine äußere Kraft auf die Kupferatome im FCC-Gitter ausgeübt, was zu Verschiebungen der Kupferatome führte. Diese Verschiebung kollabiert das FCC-Gitter und wandelt es in eine neue Gitterstruktur mit Verschiebung um. Eine ähnliche Situation wird auch bei der Schnittkraft beobachtet. Es gibt keine positive lineare Korrelation zwischen der Schneidkraft entlang der Richtung von [010] und dem Kollisionswinkel der Partikel. Bei der Kollision mit 0°, 5°, 10° und darüber hinaus war die Kraft in [010]-Richtung kleiner und schwankte weniger als in anderen Schnittrichtungen. Schneiden mit kleinerem Winkel, grundsätzlich Grate entfernen, da der Grat in einem Höhenbereich von 3,5 ~ 15 Å definiert werden kann. Wenn diese Richtungen miteinander verglichen werden und die Schnitttiefe relativ kleiner ist, werden die Beschädigung und Verformung der Kristallstruktur mäßig sein. Daher wurde während des gesamten Schneidevorgangs die Scherkraft entlang der [010]-Richtung kleiner gehalten, wie im Kurvendiagramm von Fig. 6b gezeigt. In der späteren Simulationsphase erreichte die Schnittkraft das Minimum von 0°. Es wurde auch festgestellt, dass die Schneidkraft eine direkte Beziehung zum Winkel hat, wie in Fig. 6c gezeigt, was der Tatsache zugeschrieben werden kann, dass bei einer Partikelgeschwindigkeit von 80 m/s ein größerer Schneidwinkel erreicht wird. Andererseits wurden im gleichen Simulationsschritt je größer die Komponentengeschwindigkeit entlang der [001]-Richtung, ein größerer Winkel, tiefere Partikel geschnitten und desto mehr Atomgitter wurden zerstört. Es gab jedoch eine positive Korrelation zwischen dem Schnittwinkel und der Schnittkraft. Wenn sich Körner entlang der [100]-Richtung bewegten, waren Reibungen zwischen C-, Si- und Cu-Atomen die Quelle der Schnittkraft. Die Schnittkraft zeigte also keinen allmählich steigenden Trend. Bei weiterer Simulation jedoch nahm die Schnittkraft zu und schwankte, was eng mit der Verformung und Rekonstruktion des Gitters sowie der Erzeugung amorpher struktureller Phasenübergänge zusammenhing. Bevor die Schleifkörner zerstören konnten, wird durch die Wechselwirkung zwischen den Atomen des Werkstücks Material abgetragen, was letztendlich die Schnittkraft konsequent erhöht hat. Beim Erhöhen der abrasiven Schneidkraft über den kritischen Wert (Atombindungskraft) hinaus wird das Atomgitter beschädigt und die Bindungen dissoziieren, was zu einer amorphen Struktur führt. Dabei fiel die Schnittkraft auf einen relativ niedrigen Wert. Die Schnittkraftschwankungen traten während des gesamten Prozesses der abrasiven Fließbearbeitung kontinuierlich auf, was auf die Zunahme der Schnitttiefe zurückzuführen ist, und es fand mehr Kristallstrukturzerstörung statt. Daraus wird geschlossen, dass in diesem Stadium der Maximalwert der Schwankung der Schneidkraft größer war. Wie in Abb. 6b gezeigt, nahm der rote Bereich während der späteren Simulationsphase eine größere Fläche ein, was darauf hindeutet, dass die Schnittkraft deutlich erhöht wurde. Bei der gleichen Simulationszeit war die Schnittkraft kleiner, wenn der Schnittwinkel weniger als 15° betrug, was bedeutet, dass ein kleiner Teil des Kristallgitters zerstört wurde.
Energieanalyse für den SiC-Schleifschlag-Schneidprozess
Die Thermodynamik-Gesamtenergie ist die Summe aus der gesamten potentiellen Energie und der gesamten kinetischen Energie in einem System, die die Wirkung der am Werkstück durch Schleifkörner geleisteten Arbeit zeigt. Der Einfluss des Schneidwinkels des Siliziumkarbid-Schleifmittels auf die Energieänderung des Systems ist in Abb. 7 dargestellt. Beim Schneiden von einkristallinen Kupfer-Werkstoffen mit Siliziumkarbid-Schleifkörnern wirkt die von den Schleifkörnern auf den Werkstückstoff geleistete Arbeit In zwei Wegen; ein Teil wird in kinetische Energie umgewandelt, die die Wärme der einkristallinen Kupferatome erhöht Kontakt mit Siliziumkarbid-Partikeln Funktionierendes Polieren, der andere Teil wird in potentielle Energie umgewandelt, die Änderungen in der inneren Struktur des einkristallinen Kupferwerkstücks, der Gitterverformung und die Gitterenergiefreisetzung.
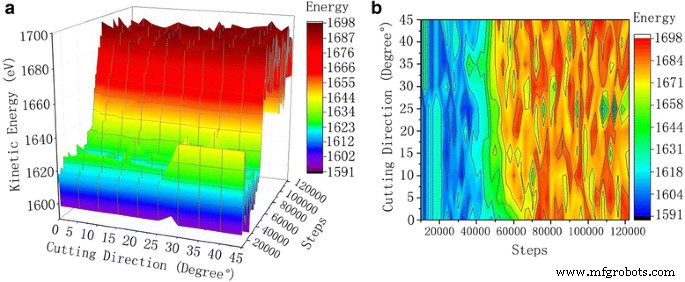
Kinetische Energiekurve der Werkstückatome. Abbildung 7 zeigt den Verlauf der kinetischen Energie der verschiedenen Schnittwinkel während des Schnittprozesses. Mit zunehmender Anzahl der Simulationsschritte schwankt die kinetische Energie der Atome in einem niedrigen Bereich und dann innerhalb der Fluktuationen in einen höheren Bereich. a 3D-Kurve. b Kontur
Beim Schleifkornschneiden von einkristallinen Kupferwerkstücken steht die kinetische Energie des Systems in engem Zusammenhang mit der Arbeit, die das Werkstückmaterial durch SiC-Schleifmittel verrichtet. Durch Berechnung der Geschwindigkeit der Teilchen im System zu jedem Zeitpunkt kann die kinetische Gesamtenergie des Systems berechnet werden:
$$ K=\sum\limits_{i=1}^N\frac{1}{2}{m}_i\left({v}_{\textrm{ix}}^2+{v}_{\ mathrm{iy}}^2+{v}_{\mathrm{iz}}^2\right) $$ (1)In der Formel \({v}_{\mathrm{ix}}^2\), \({v}_{\mathrm{iy}}^2\) und \({v}_{\mathrm {iz}}^2 \) repräsentieren die Geschwindigkeitskomponente x , y , z Richtung Atome.
Die kinetische Kurve in Abb. 7 ließ uns schlussfolgern, dass beim Inkrementieren der Simulationsschritte die kinetische Energie der Atome zunächst in einem niedrigen Bereich und dann in einem höheren Bereich schwankt. Bei der Bewegung von Schleifkörnern wird eine weitreichende abstoßende Wechselwirkung zwischen den äußersten Kupferatomen und Si, C-Atomen (SiC) gefunden. Die Kupferatome im Werkstück beginnen, kinetische Energie zu erhalten und sich zu bewegen. Wenn die Siliziumcarbid-Partikel den Kupfer-Einkristall berühren, erhöht sich die Atomtemperatur des Kontaktbereichs, was die atomare thermische Bewegung erhöht. Wenn das Schneiden stabil ist, wird die kinetische Energie der Kupferatome im Material übertragen und in ein dynamisches Gleichgewichtsmuster umgewandelt, und die kinetische Energie der Atome schwankt in einem hohen Bereich.
Die Analyse der kinetischen Energie führte zu dem Schluss, dass während des Schneidprozesses, wenn die Partikel das Werkstück berühren, die Atome im extrudierten Bereich eine Gitterverformung erfahren, sich die Atomkoordinaten ändern und sich die Verschiebung mit der kinetischen Energie ändert. Wenn die Schleifpartikel in einkristallines Kupfer eindringen, erscheint der Spitzenwert der kinetischen Energie des einkristallinen Kupferwerkstücks, wenn das Werkstück vollständig in das Werkstück eindringt. Denn die kinetische Energie und potentielle Energie von Schleifpartikeln werden lediglich ineinander umgewandelt. Die Energie des gesamten Systems ändert sich jedoch nicht, mit Ausnahme der bewegten Teilchen, die in das Werkstück eindringen. Darüber hinaus zwingt die Bewegung der Siliziumkarbid-Partikel die Werkstückatome dazu, sich gleichzeitig mit ihnen zu bewegen. Die bei der atomaren Reibung erzeugte Wärme wird durch die kinetische Energie und die durch Versetzungsbewegung freigesetzte Dehnungsenergie freigesetzt.
Die Umwandlung zwischen Wärme und kinetischer Energie wird nach folgender Formel berechnet:
$$ \frac{1}{2}{\sum}_i{m}_i{v}_i^2=\frac{3}{2}{nk}_B{T}_i $$ (2)In der Formel n ist die Anzahl der Atome; vi stellt die momentane Geschwindigkeit dar; k B ist die Boltzmann-Konstante und T ich ist die Temperatur der Atome.
Die Schnittkraft erhöht die Atomtemperatur des Bereichs, in dem das Schleifmittel das Werkstückmaterial berührt. Unter Berücksichtigung der thermischen Bewegung des Atoms und der kinetischen Energie der Atome nimmt die kinetische Energie der Kupferatome teilweise zu. Das simulierte System wird auf das kanonische Ensemble eingestellt; die Gesamtsystemtemperatur schwankt in einem bestimmten Bereich. Die beim Schneiden von Schleifpartikeln erzeugte Wärme wird schnell auf die Atomschicht mit konstanter Temperatur übertragen, sodass sich die kinetische Gesamtenergie des Systems nur sehr wenig ändert.
Wie aus der Potentialenergiekurve von Fig. 8 ersichtlich ist, neigt bei Erhöhung der Anzahl der Simulationsschritte auch die potentielle Energie zwischen dem Monokristall der Kupferatome im Werkstück dazu, anzusteigen. Wenn Siliziumkarbid-Schleifmittel den Einkristall des Kupferwerkstücks vom Anfang bis zum vollständig stabilen Schneiden berühren, verformt sich das Werkstückmaterial allmählich und die Kupferatome verdrängen sich, was zu einer Verzerrung des Kristallgitters im Kristall führt. Dadurch entsteht auch ein elastisches Spannungsfeld, bei dem die Dehnungsenergie zunimmt. Wenn die Dehnungsenergie nicht ausreicht, um die materiellen Atome neu anzuordnen, kommt es zu einer Versetzung der Atome, die die Gesamtenergie des Systems erhöht. Im Gegensatz zu den Potentialkurven von 0° bis 45° können wir eine Konsistenz der thermischen Bewegung von Atomen bei konstanter Temperatur sehen. Es gibt keinen signifikanten Zusammenhang zwischen der atomaren kinetischen Energie und dem Schnittwinkel von SiC-Schleifkörnern. Die kinetische Energie der Atome hängt eng mit der thermischen Bewegung der Atome zusammen. Die Änderung der potentiellen Energie und der Gesamtenergie hängt jedoch offensichtlich mit dem Schnittwinkel der SiC-Schleifpartikel zusammen. Die Größe der atomaren potentiellen Energie nimmt mit zunehmendem Schnittwinkel zu. Bei einem Schnittwinkel zwischen 0° und 20° wird eine deutliche Änderung der potentiellen Energie beobachtet. Wenn der Schnittwinkel jedoch zwischen 25° und 45° liegt, bleibt die potentielle Energie als solche erhalten, und die gesamten potentiellen Energiekurven reichen von 0° bis 20° Schnittwinkel. Wie in Abb. 9 gezeigt, ähnelt der Trend der Gesamtenergie der Kurve der potentiellen Energie. Die Gesamtenergiewerte aller Schnittwinkel liegen sehr nahe beieinander. Dies liegt daran, dass die Gesamtenergie gleich der potentiellen Energie und der kinetischen Energie des Systems ist, während sich die kinetische Energie während des Schneidvorgangs nicht mit dem Schnittwinkel ändert. Die Änderung der kinetischen Energie des Werkstücks ist bei unterschiedlichen Schnittwinkeln sehr gering. Daher ist die Änderungskurve der potentiellen Energie ähnlich der Kurve der Gesamtenergie. Beim Vergleich der atomaren Verschiebungsdiagramme von Fig. 9 kann festgestellt werden, dass die Schnitttiefe in einkristallinen Kupferwerkstücken bei gleichen Schnittbedingungen größer ist, wenn der Schnittwinkel zwischen 25° und 45° liegt, was auf die größere Verschiebung zurückzuführen ist von Kupferatomen. Entlang der [001]-Richtung der SiC-Partikel werden mehr atomare Schäden im Gitter und Versetzungen erzeugt. Die während dieser Zeit erzeugte Dehnungsenergie ist höher, was zu einer hohen potentiellen Energieänderungskurve und einer Gesamtenergieänderungskurve der Werkstückatome führt.
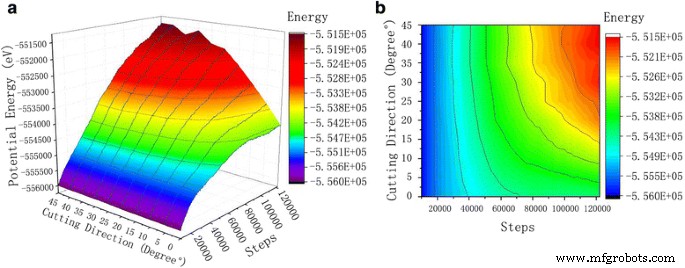
Potentielle Energiekurve des Werkstücks. Fig. 8 ist ein Diagramm potentieller Energievariationen bei verschiedenen Schnittwinkeln während des Schneidprozesses. Mit der Zunahme der Anzahl von Simulationsschritten neigt das Potential zwischen den einkristallinen Kupferatomen aufweisenden Werkstücken dazu, anzusteigen. a 3D-Kurve. b Kontur
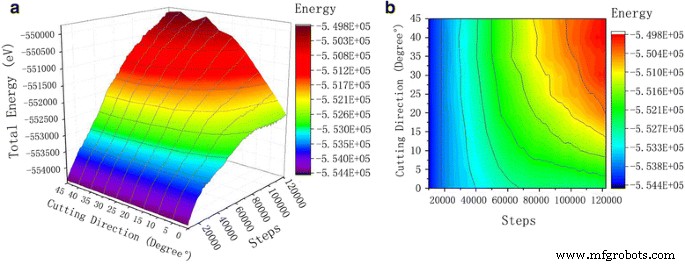
Gesamtenergiekurve. Abbildung 9 zeigt die Gesamtenergiekurve. Während des SiC-Schneidens des einkristallinen Kupferwerkstücks zeigt sich die Wirkung der Schleifkörner auf das Werkstück in zwei Formen:Ein Teil davon wird in kinetische Energie umgewandelt, die Atomwärme wird erhöht und die lokale kinetische Energie wird beim Polieren größer die Verbindungsfläche des einkristallinen Kupferwerkstücks und der SIC-Partikel; der andere Teil wird in potentielle Energie umgewandelt, die innere Struktur des monokristallinen Kupferwerkstücks wird verändert, das Gitter wird verformt und die Gitterenergie wird freigesetzt und in potentielle Energie umgewandelt. a 3D-Kurve. b Kontur
Analyse der atomaren Verschiebung beim kollidierenden Schneidprozess von SiC-Schleifpartikeln
Beim Schneiden von Werkstückmaterial unter verschiedenen Winkeln bewegen sich die Schleifkörner entlang der Schnittrichtung, wodurch die Kupferatome im Werkstück gezwungen werden, sich zu bewegen. Aus der Analyse der Bewegungsrichtung des Werkstücks werden die Wirkung der Schleifkörner auf das Werkstückmaterial, die Spanform und der Materialabtrag vollständig geklärt. Gemäß der von Ackland-Jones vorgeschlagenen Bindungswinkelanalysemethode werden unterschiedliche Atomgitterstrukturen zu Beobachtungszwecken und zur Analyse durch verschiedene Farben markiert. Die ZOY-Ebene wird ausgewählt, um den Schneidprozess eines einzelnen SiC-Partikels zu beobachten, und das Atomverschiebungsdiagramm des Schneidbereichs wird vergrößert, wie in Abb. 10 zu sehen ist.
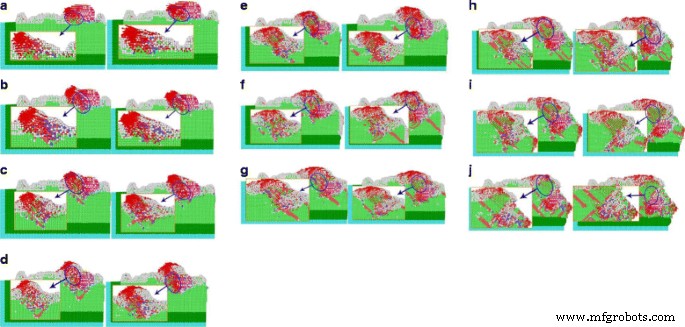
Unterschiedliche Schnittwinkel führen zu atomaren Verschiebungen. Abbildung 10 beschreibt atomare Verschiebungen verschiedener Schnittwinkel. Wenn die einkristallinen SiC-Schleifpartikel mit dem Werkstück kollidieren, das Kupfer in verschiedene Richtungen schneidet, wobei SiC-Schleifkörner geschnitten werden, nimmt die Schnitttiefe zu, da die Geschwindigkeit der Schnittrichtung bei 80 m/s liegt, die [001]-Richtung Die Bewegungsgeschwindigkeit ist v z = 0.8 ∗ sin θ , mit zunehmender Schnitttiefe der Schnittwinkel, [001] bei gleichem Schnittwinkel nimmt die Simulationsschritte zu, gleichzeitig ist die Schnittiefe groß. a 0° Verschiebung. b 5° Verschiebungen. c 10° Verschiebung. d 15° Verschiebung. e 20° Verschiebung. f 25° Verschiebung. g 30° Verschiebung. h 35° Verschiebung. ich 40° Verschiebung. j 45° Verschiebung. (Atomfarbe: HCP-Struktur,
BCC-Struktur,
FCC-Konfiguration als weiße amorphe Struktur)
Wenn die einkristallinen SiC-Schleifpartikel mit dem Werkstück beim Schneiden von Kupfer in verschiedenen Richtungen kollidieren, nimmt die Schnitttiefe während des Prozesses zu. Die Geschwindigkeit der Schnittrichtung beträgt 80 m/s, wobei die Bauteilgeschwindigkeit in [001]-Richtung v . beträgt z = 0.8 ∗ Sündeθ . At the same simulation step, cutting depth increases with increasing the cutting angle. As shown in Fig. 10, there is an atomic position shift in both of the surface and interior of the workpiece material, contacting with the abrasive grains, where atoms of different lattice types are arranged and doped with each other. Due to the movement of these abrasive particles, the copper atoms accumulated at the tip of the abrasive grains, which results no cracks during abrasive particles cutting. It can be seen that the material removal mode of the abrasive particles is plastic deformation. At the same time, due to abrasive cutting, the atoms displacement in single crystal copper increases from 15° to 45°.
The number of the workpiece atoms along the abrasive grain motion direction also increases, and the atomic displacement is perpendicular to the direction of abrasive cutting. This part of the atomic displacement is due to that of the abrasive particles, change the cutting action to the extrusion upon the workpiece atoms. At cutting angle, the abrasive particles is between 0° and 10°, while the cutting depth is smaller than those of the 15° to 45°. Abrasive particles are performing mainly the cutting function, the extrusion of the workpiece atoms is marginal, and the number of atoms is small whose displacement direction is perpendicular to the direction of the abrasive grain motion. With the repeated cutting on the workpiece surface by numerous abrasive particles, the abrasive particles having large cutting angle produce deep pits on the workpiece material during the whole cutting process, while ones following smaller cutting angles will continue cutting along the cutting mark produced by the former. Under the combined action, the workpiece material is cut to a certain depth (micro-cutting) followed by whole abrasive flow polishing.
Dislocation Collision Analysis for SiC Abrasive Cutting
Dislocation is a special arrangement of atoms in crystal along certain crystal surface and crystal direction, or a boundary between the slip zone and the non-slip zone on the slip surface. Dislocation can be divided into edge dislocation, spiral dislocation, and mixed dislocation, among which mixed dislocation is most common. In the process of abrasive particle cutting, the single crystal copper workpiece is plastically deformed, the atoms move, and the crystal lattice breaks and reconstructs, which results in a large number of dislocations. The analysis for dislocation and bond angles at different incidence angles is shown in Fig. 10. In the simulation model of abrasive flow simulation, two abrasive particles are used for cutting the workpiece material. For ease of analysis, the generation and change of different dislocation lines in single crystal copper material, during cutting process and the different lattice structures in the cutting part are analyzed in the view of one single SiC particle on the YOZ surface, as shown in Fig. 11.
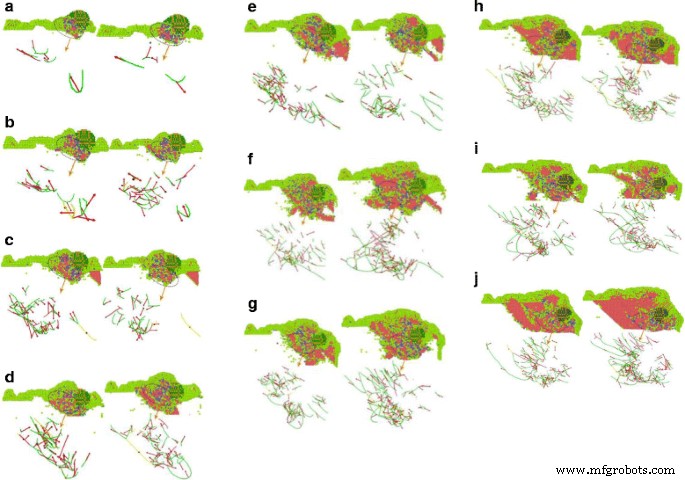
Different angles-bond angle dislocation line charts. Figure 11 represents the cutting dislocation line and the bond angle. As the repeated cuttings on the workpiece surface are done by the numerous abrasive particles during the polishing process, in the entire cutting process, the abrasive particles with larger cutting angle produce bigger pits, while the following abrasive particles with smaller cutting angles continue to polish along the cutting trace. Therefore, certain depth is done on the workpiece material and the whole micro-cutting of abrasive flow polishing is achieved. a Dislocation lines with 0° cutting angles. b Dislocation lines with 5° cutting angles. c Dislocation lines with 10° cutting angles. d Dislocation lines with 15° cutting angles. e Dislocation lines with 20° cutting angles. f Dislocation lines with 25° cutting angles. g Dislocation lines with 30° cutting angles. h Dislocation lines with 35° cutting angles. ich Dislocation lines with 40° cutting angles. j Dislocation lines with 45° cutting angles. (Note:the upper part of the key angle analysis, the figure in the atomic color: HCP
BCC
Amorphous structure
Abrasive grain; the lower part of the dislocation line diagram, the figure dislocation line color:
Stair-rod,
Shockley,
Hirth,
Perect,
Frank,
Burgers vectors)
Key angle analysis diagram of each cutting angle is shown in Fig. 11, where the sample from the interior workpiece simulation at time 60 and 70 ps, the atoms are colored individually according to different arrangement of atoms through BAD technology. To facilitate the analysis of the lattice changes in the cutting part, atoms of the FCC structure in the workpiece material are removed. By DXA techniques, different types of dislocations are marked in diverse colors:red arrow indicates the Burgers vector (Burgers vectors), green for Shockley partial dislocations (Shockley), light blue for the Frank partial dislocations (Frank), pink pole position for the pressure error (Stair-rod), and blue for the whole dislocation (Perfect).
As can be observed from the analysis of the bond angle portion in Fig. 11, a large number of dislocations and lattice deformations occurred under the impact of external cutting forces. The bond angle analysis shows that the internal HCP structure of the workpiece appears more clearly with increasing of cutting angle. On further simulations, the structure of HCP increases gradually. The silicon carbide particles continuously cut and squeeze the workpiece material at 80 m/s speed, resulting in a phase transition from the FCC structure to the HCP structure. During this phase transition, the atomic strain of the workpiece continues to increase. However, when the stress state of atoms of the workpiece has exceeded the threshold of thermodynamic phase transition, it turns to metastable state. As the strain increases, the HCP phase begins to nucleate and grow spontaneously, and the FCC lattice of copper undergoes absolute destabilization, which induces a sudden change in mechanical quantities. As the kinetic energy of the atom is directly related to the atomic temperature (formula 1), there is a saltatory augment in the kinetic energy change curve, as can be seen from Fig. 7. This is due to high strain energy, accumulated in the single crystal copper workpiece before the nucleation of HCP. The HCP structure increases the system temperature through metastable nucleation and partial stress release. Due to the abrasive cutting and extrusion, bonds of copper atoms in workpiece material break down which results in disorder. The original regular lattice structure is broken, where the partial copper atoms gradually change into disorder and form an amorphous structure. It can be seen from the bond angle analysis diagram that (Fig. 11) atoms with relatively disordered displacement tend to form amorphous structures at 60 and 70 ps, which is because of silicon carbide abrasive particles. At the same time, many atoms with the same displacement direction are transformed into HCP structures. Meanwhile, the particles shear downward and the atomic structure is rearranged due to the displacement of atoms in the original amorphous structure, results an amorphous structure of HCP. Atoms that have already been transformed into HCP structures, even before the next cut stage, change back into amorphous structure. As the cutting depth increases, the number of amorphous atoms near the abrasive particles also increases.
When the FCC crystal structure undergoes cutting by abrasive particles, a shear stress generates in atoms, which results in the displacement of atoms in the lattice and the arrangement of various lattice structures. In moving the atoms of workpiece, the rigid displacements of the atoms produce dislocations, also called as dislocation lines (Fig. 11). Dislocation line can be termed as the boundary between the slip zone and the non-slip zone, on the slip surface. According to the relation between the dislocation and the PATS vector, dislocation is parallel to the PATS vector, called the screw dislocations. The vertical ones are edge dislocations, and the mixed dislocations are neither parallel nor vertical. In Fig. 11, most of the dislocation lines are neither parallel nor vertical to PATS vectors, which are typical mixed dislocations. In the cutting process of abrasive particles, the dislocation line changes, moves and grows around the abrasive particles. The closer the particle, the greater the density of the dislocation line. Dislocation lines are also very dense, when the arrangement of atoms is complicated. The abrasive particles marked as orange, produce a large amount of HCP, BCC, and amorphous structures around them, which interlace and blend with each other to form dislocations that increases the internal energy of the crystals. When atoms arrange their self just like shown in Fig. 12b, possess maximum potential energy. While for the arrangement, shown in Fig. 12a–b, the atoms situate at the lowest potential energy position. The number of dislocation lines is directly related to the magnitude of strain energy of the crystal. The total strain energy of the unit length dislocation can be measured with the given formula:
$$ W=\alpha {Gb}^2 $$ (3)
Schematic view of dislocation changes. Dislocation is a special arrangement of atoms in crystals. It is the crystal in the atomic arrangement along a certain crystal face and crystal orientation occurred in a certain wrong line, and it is the boundary of the slip surface within the area where the slip has occurred and the area with no slip has occurred. In Fig. 12a –c , the relative displacement of the rigidity of the upper atom and the underlying atom produce dislocations, the upper atom belongs to the sliding region, and the lower atoms belong to the non-slip region, they are in the slip surface of the intersection line which is called dislocation line, that is, dislocation. Figure 12 is the process of dislocation generation and development
Where, α is the geometric factor (type dislocations, dislocation density) parameter related to, and generally 0.5 ~ 1.0; G is the shear modulus, and b is the slippage distance.
When the workpiece material is being cut, particles break the atomic arrangement and the lattice reconstructs, which constitutes, macroscopically, the plastic deformation of the workpiece material. In the process of plastic deformation, the dislocation was supposed to escape from the crystal and decrease the dislocation density. However, this dislocation density increases due to dislocation propagation. There are many ways of dislocation multiplication and the main one is the Frank–Reed dislocation source theory, of which the growth mechanism is shown in Fig. 11. As illustrated in Fig. 11, the density of the dislocation line increases markedly from 60 to 70 ps when the cutting simulation proceeds, change both the number and shape of dislocation lines in accordance with Frank–Reed dislocation source theory. At simulation time of 60 ps, there are many long Shockley dislocations. But after another 10 ps simulating, the long Shockley dislocation line becomes less and shorter. The original straight dislocation lines turn into bent, which is especially evident near the abrasive grains. From formula 3, the strain energy of the dislocation is proportional to b 2 . From the viewpoint of energy, the dislocations with the smallest b in the crystal should be most stable with low energy; however, dislocations with larger b will break down into ones. In addition, the energy of the dislocation is valued by the unit length of the dislocation line. Given the shortest line between two points is the straight, the strain energy of straight dislocation is lower than that of the bent one, means straight dislocations are more stable. Frank–Reed dislocation source theory argued that the long dislocation line becomes shorter and breaks down into smaller dislocations, thus decreasing the strain energy of the crystal.
Analysis for Friction Coefficient Between Workpiece Surface and Abrasive Particles
To quantitatively disclose mechanical properties and surface effect of SiC abrasive cutting single crystal copper material, the tangential force ([010] direction) and normal force ([001]direction) on the cutting surface are further analyzed. The friction coefficient can be defined as the ratio of the tangential force to the normal force, with the formula below:
$$ f=\frac{F_y}{F_z} $$ (4)Figure 13 shows the variation of friction coefficient along different cutting angles during abrasive cutting. The change of friction coefficient can be divided into two periods. Period I, when the cutting distance is less than half of the size of the abrasive particle, the friction coefficient fluctuates violently in certain range due to surface effect of the material; while in period II, all the friction coefficients fluctuate in very small range, and the friction coefficients remains steady state at different angles. However, at cutting angle of 5°, there is a small amount of abnormal fluctuation at the end of simulation. Moreover, in period I, abrasive particles contact the workpiece atoms to the abrasive grains enter into the workpiece of half abrasive diameter (shown in Fig. 13b), the cutting movement distance reaches 7.5 Å. In Fig. 6, the cutting force change curve shows that the tangential force and normal force are in an oscillating phase during period I. Since the friction coefficient can be characterized as the adhesion among atoms in the contact surface and is related to the two atoms contacting with each other, regardless of the cutting mode, which can interpret the phenomenon that change of cutting angle does not cause significant change of friction coefficient, as shown in Fig. 13a.
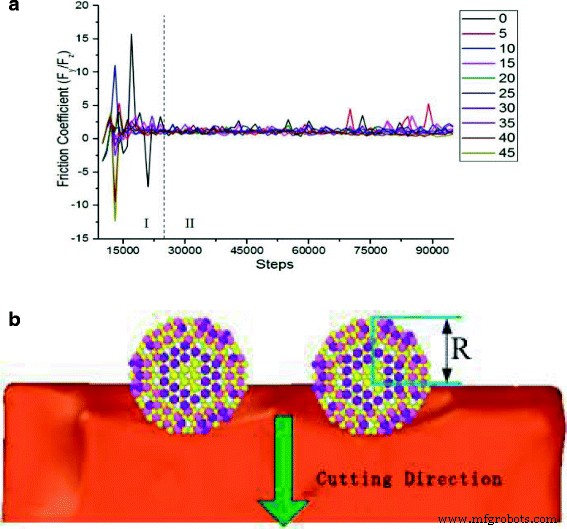
Friction coefficients of different cutting angles. Figure 13 is the changes of the frictional coefficients during SIC particles cutting single crystal copper from different angles. The change in cutting angle did not cause significant changes in friction coefficient. It described two kinds of coefficient of friction in contact with the relevant atoms in the cutting process, regardless of the cutting mode. a Friction coefficient variation curve with cutting angle. b Instantaneous structure when SiC abrasive grains move 7.5 Å
Schlussfolgerungen
The micro cutting simulation of single crystal copper by SiC abrasive particles is achieved during abrasive flow polishing. Comprehensive analysis of the SiC abrasive cutting reveals that when SiC abrasive particles cut at angle from 0° to 15°, cutting forces in along Y and Z direction are relatively small and tend to stay steady. A larger cutting angle results more dislocations, which brings about larger grooves damaging of the workpiece material. In the process of cutting, it is necessary to avoid more dislocations, which has an immediate adverse effect on the performance of all aspects of crystal material. Therefore, a cutting angle of 0° is better than other angles. Considering the amount of dislocation produced, or the change of cutting force and energy in the cutting process; cutting with small or medium angles is not only beneficial for improving surface quality but reduce the internal defects.
Nanomaterialien
- Oberflächeneffekt auf den Öltransport in Nanokanälen:eine molekulardynamische Studie
- Molekulardynamische Modellierung und Simulation des Diamantschneidens von Cer
- Toxizität von PEG-beschichteten CoFe2O4-Nanopartikeln mit Behandlungseffekt von Curcumin
- Untersuchung des nanoskaligen Reibungsverhaltens von Graphen auf Goldsubstraten mittels Molekulardynamik
- Temperatur- und Druckabhängigkeiten der elastischen Eigenschaften von Tantal-Einkristallen unter <100> Zugbelastung:eine molekulardynamische Studie
- Synthese und In-vitro-Studie einer Dual-Mode-Sonde, die auf Integrin αvβ3 abzielt
- Wärmeleitfähigkeit von zwei Arten von 2D-Kohlenstoffallotropen:eine molekulardynamische Studie
- Abrasive Wasserstrahlbearbeitung und -schneiden
- Vorteile des Laserschneidverfahrens
- Trennschleifen Vor- und Nachteile