Additive Fertigung macht große Marinestrukturen vielseitiger
Die Möglichkeit, schnell verschiedene Iterationen von Teilen zu erstellen – ohne kostspielige dedizierte Werkzeuge entwickeln oder kaufen zu müssen – ist der Grund, warum die additive Fertigung (AM) so oft beim Prototyping von Teilen eingesetzt wird. Da sich Materialien und Drucktechnologien jedoch weiter verbessern, sind immer mehr Unternehmen in der Lage, die Geschwindigkeit und Vielseitigkeit von AM auch auf Endverbrauchsteile auszudehnen, insbesondere für Kleinserien- oder Einzelanwendungen, bei denen die Fähigkeit, schnell neue Designs zu produzieren, von Vorteil ist .
Vor kurzem haben zwei Unternehmen gezeigt, dass AM-Technologien aus Verbundwerkstoffen Lösungen für die Anpassung großer Meeresstrukturen wie autonomen Unterwasserfahrzeugen (AUV) und Motorbooten ermöglichen können.
Großformatiger 3D-Druck für anpassbare AUV-Produktion
Autonome Unterwasserfahrzeuge sind eine Art unbemannter Roboterfahrzeuge, die ohne physische Verbindung zu einem Boot oder Fernbedienung durch einen menschlichen Bediener unter Wasser reisen können und oft mit Kameras oder Sensoren für verschiedene Anwendungsfälle in der Verteidigung, Meeresforschung oder Offshore-Vermessungsanwendungen ausgestattet sind. Typischerweise bestehen die Außenrümpfe von AUVs entweder aus einem großen Metalldruckbehälter oder bestehen aus thermogeformtem Kunststoff oder Verbundwerkstoffen. Beide Optionen erfordern jedoch die Entwicklung und den Kauf spezieller Werkzeuge, was teuer sein kann und den Umfang der Anpassungsmöglichkeiten für AUV-Kunden begrenzt. Der AUV-Hersteller Dive Technologies (Quincy, Massachusetts, USA) hat entdeckt, dass der 3D-Verbunddruck viele der Einschränkungen der traditionellen Fertigung löst.
Im Jahr 2018 beschlossen die Mitbegründer von Dive Technologies, Bill Lebo, Jerry Sgobbo und Sam Russo, ihr eigenes Unternehmen zu gründen, um ein neues, leistungsfähigeres AUV zu entwickeln und auf den Markt zu bringen, das die Kundenanforderungen nach langer Lebensdauer und großer Nutzlastkapazität erfüllt.
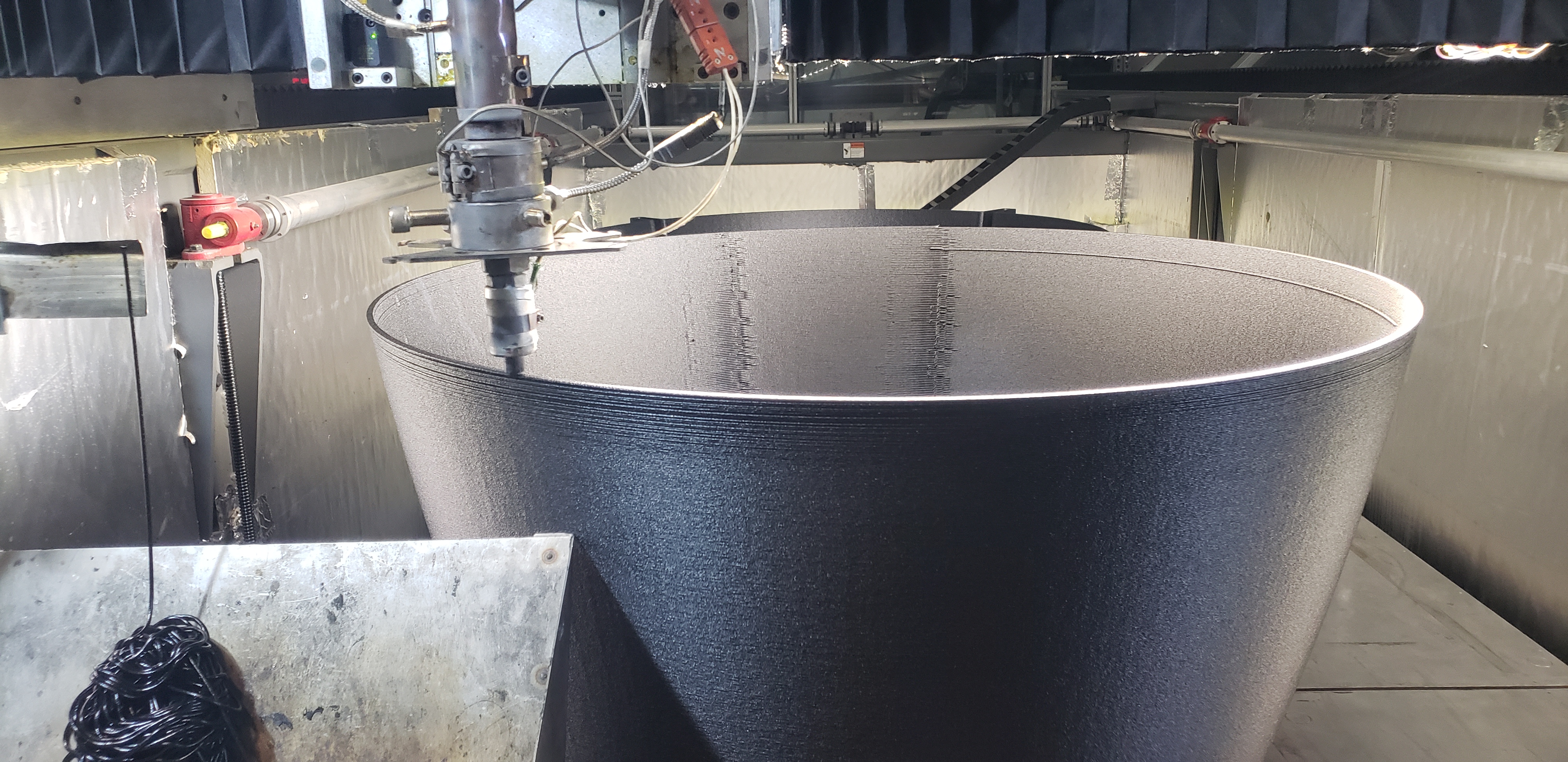
Was sie und ihr Team entwickelten, ist das DIVE-LD, ein 19 Fuß langes kommerzielles AUV mit einem Durchmesser von 4 Fuß, das bis zu 6.000 Meter tauchen und bis zu 500 Meilen zurücklegen kann und eine Nutzlast von bis zu 1 Kubikmeter trägt. Ursprünglich ging das Team davon aus, dass die endgültige Struktur seines Fahrzeugs thermogeformte Kunststoffe für die Außenhülle verwenden würde. Um das Design zu untersuchen und zu testen, sprach Dive Technologies mit dem Oak Ridge National Laboratory (ORNL, Oak Ridge, Tennessee, USA) über die Verwendung des 3D-Drucks für das Rapid Prototyping. Über ORNL wurde das Dive-Team mit dem Spezialisten für Large Format Additive Manufacturing (LFAM) Additive Engineering Solutions (AES, Akron, Ohio, USA) vertraut gemacht und begann mit dem AES-Team an einem Herstellungsprozess für seine AUV-Rumpfformen zu arbeiten.
Im Laufe der Arbeit an den 3D-gedruckten Prototypen erkannte Dive Technologies jedoch das Potenzial von LFAM, schnell fertige zu produzieren Komponenten, nicht nur Prototypen. Die 3D-gedruckten Prototypkomponenten erfüllten nicht nur die Teileanforderungen besser als erwartet, sondern die Einführung von AM für Serienfahrzeuge würde auch Werkzeugkosten sparen, es Dive ermöglichen, Endprodukte schneller als mit herkömmlichen Methoden herzustellen und ein neues, höheres Maß an schneller Anpassung für Kunden.
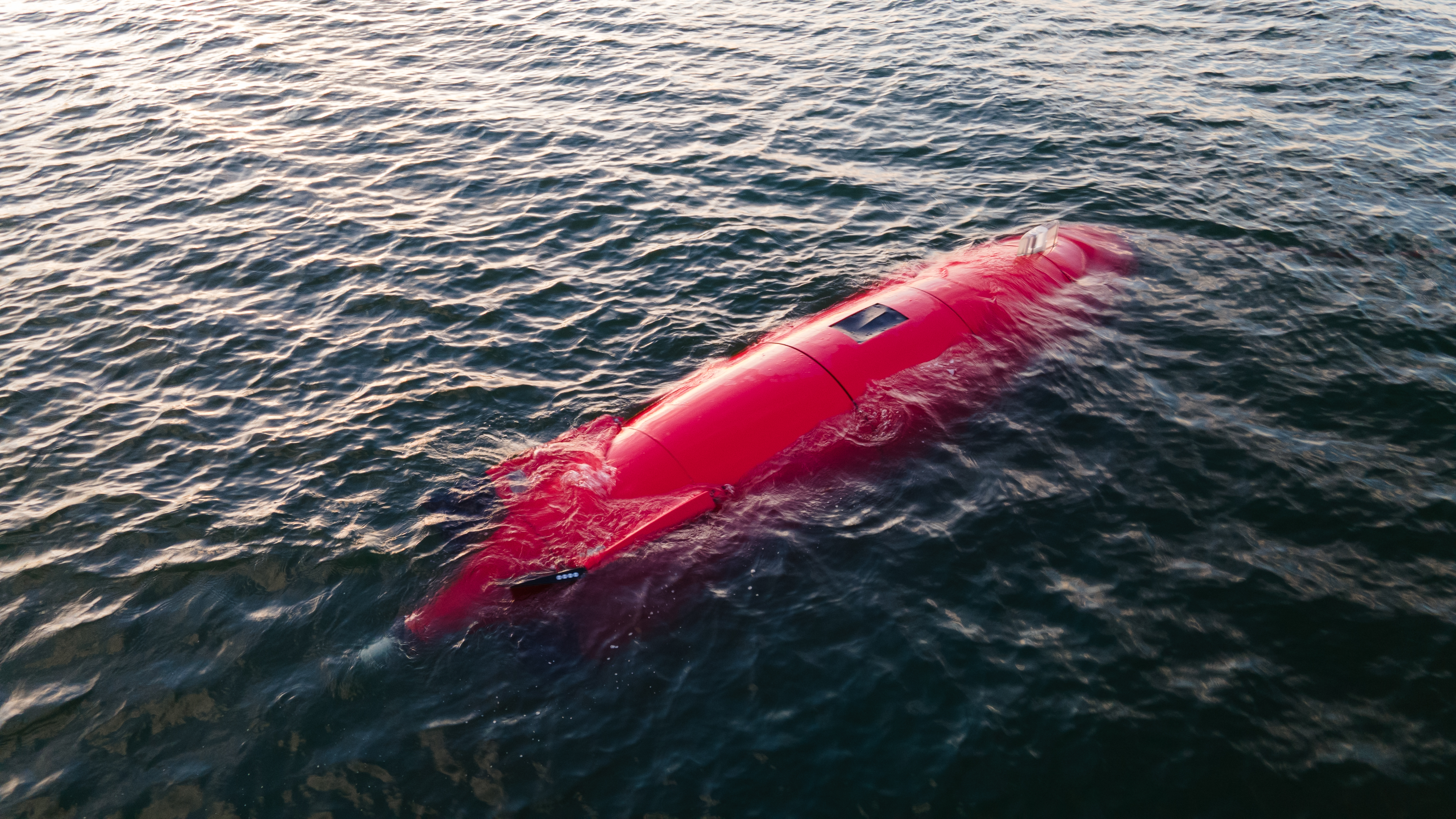
Die Außenhülle des DIVE-LD besteht aus neun röhrenförmigen Verkleidungen, die mit einem der vier Big Area Additive Manufacturing (BAAM) 3D-Drucker von AES von Cincinnati Inc. (Cincinnati, Ohio, USA) gedruckt wurden. Diese Verkleidungen werden aus gehacktem fasergefülltem ABS von Sabic (Riyadh, Saudi-Arabien) gedruckt. Laut dem Mitbegründer und VP von AES, Andrew Bader, kann AES alle Teile für einen kompletten Rumpf in weniger als zwei Tagen drucken. Nach der Lieferung an Dive werden die 3D-gedruckten Verkleidungen mit vier Befestigungselementen pro Verkleidung mechanisch befestigt und beschichtet, um eine glatte, hydrodynamische Außenfläche zu erzeugen. Nach erfolgreichen ersten Tests im Jahr 2020 baut Dive in diesem Frühjahr die ersten Kundenfahrzeuge und wird die erste Bestellung im Juni 2021 ausliefern.
Laut Russo ist AM zu einem zentralen Bestandteil des Wertversprechens von Dive Technologies für zukünftige Fahrzeuge und Produkte geworden. Die Partnerschaft mit Dive ist auch für den AES- und Composite-3D-Druck ein großer Schritt. Bader fügt hinzu:„Wenn Leute an 3D-Druck denken, denken sie normalerweise an Prototypen, Vorrichtungen und Werkzeuge, also zeigt dies, wozu 3D-Druck noch fähig ist.“
Um mehr über Dive Technologies und AES zu erfahren, lesen Sie „Großformatiger 3D-Druck ermöglicht eine werkzeuglose, schnelle Produktion für AUVs.“
Endlosfaser-AM und Automatisierung für vielseitiges Motorbootdesign
Seit der Patentierung seines Endlosfaserherstellungsverfahrens (CFM) im Jahr 2015 hat Moi Composites (Mailand, Italien) eine Reihe von Anwendungen für seine abscheidungsbasierte CFM-Technologie für den Endlosfaser-3D-Druck erforscht. Zu den Markenzeichen von CFM gehören die kundenspezifische Konstruktionssoftware von Moi Composites, der Einsatz von Roboterarmen, UV-Härtung und „Hybrid“-Fertigung – eher traditionelle Verbundlaminierung auf einem 3D-gedruckten Strukturkern. Kürzlich hat das Unternehmen seine CFM-Technologie als Lösung für ein kostengünstigeres, schnelleres und innovativeres Design von Schiffsstrukturen durch ein Demonstrator-Motorboot namens MAMBO demonstriert.
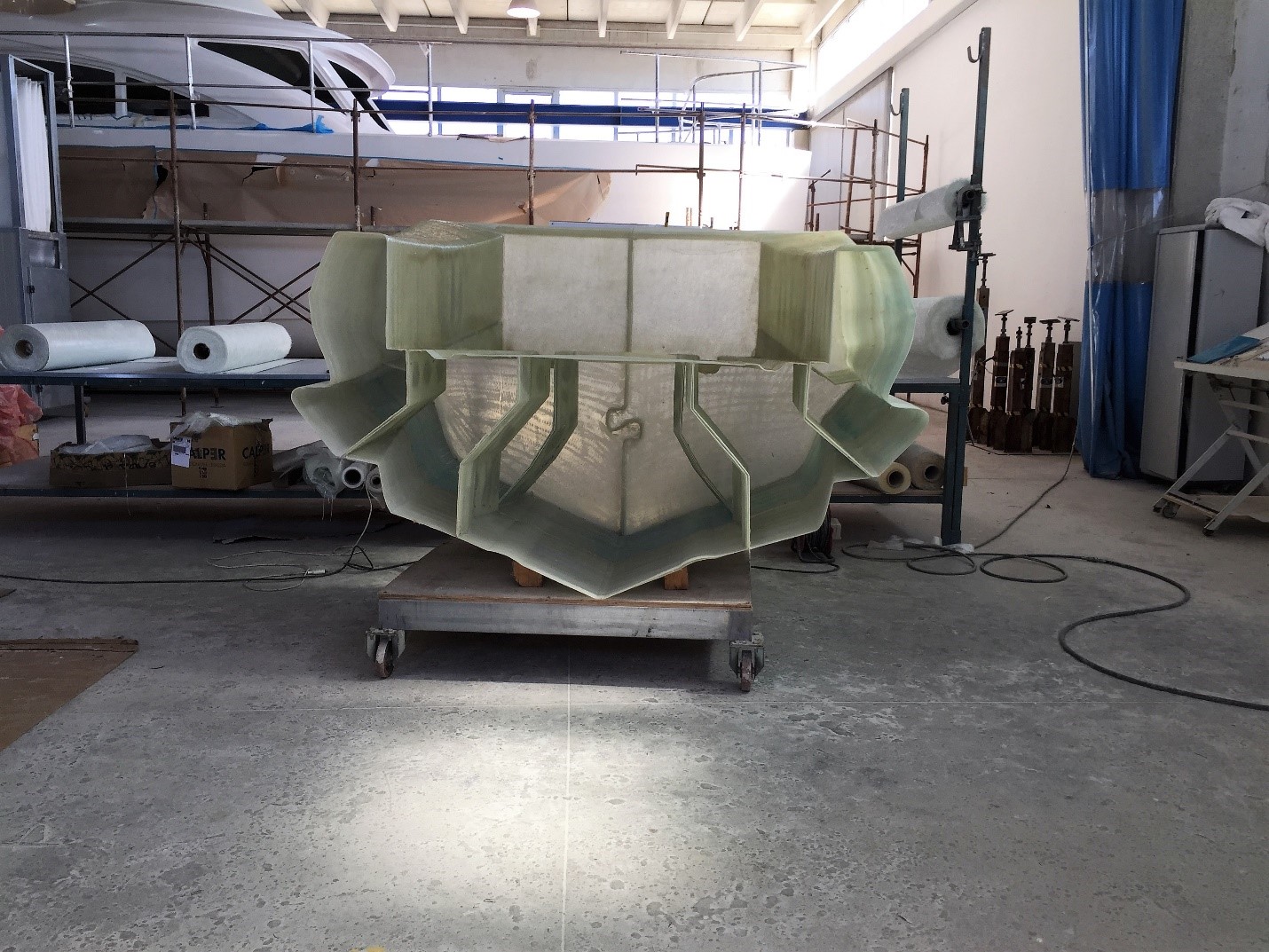
Laut Gabriele Natale, Mitbegründer von Moi Composites, nahmen er und sein Mitbegründer Michele Tonizzo 2017 an der Genoa Boat Show teil und erkannten, dass die Werkzeugkosten und die traditionellen Glasfaserinfusionsverfahren, die für viele Bootsrümpfe verwendet werden, die Möglichkeiten der Bootskonstrukteure einschränken, Neues zu erkunden und komplexere Designs. Natale erkennt, dass ihre formlose Endlosfaser-3D-Drucktechnologie eine bahnbrechende Lösung sein könnte, und sagt:„Von da an begannen wir mit der Entwicklung eines Plans und trafen uns mit Partnern in der Schifffahrtsindustrie.“
Das resultierende MAMBO-Boot ist 6,5 Meter lang x 2,5 Meter breit, mit einem Trockengewicht von ca. 800 Kilogramm, ausgestattet mit einem Navigationssystem, Korkboden, weißen Ledersitzen und einem 115-PS-Motor. Moi Composites arbeitete mit dem Marine Design Engineering Studio MICAD (Lecce, Italien) am strukturellen Designkonzept für das Boot zusammen, das organische Formen in seinen Strukturelementen kombiniert, inspiriert vom berühmten Arcidiavolo-Katamaran von Sonny Levi. Autodesk (San Rafael, Kalifornien, USA) Fusion 360 CAD und die additive Fertigungssoftware NETFABB wurden für das Design und die strömungsdynamische Analyse der Komponenten verwendet.
Der Rumpf und das Deck des Bootes, gedruckt aus unidirektionalem E-Glas von Owens Corning (Toledo, Ohio, USA) und Vinylesterharz, wurden für die Herstellung in 50 einzelnen Abschnitten unterschiedlicher Größe entworfen. Die Hälfte der Profile wurde im Mailänder Werk von Moi Composites gedruckt, die andere Hälfte in der Advanced Manufacturing Facility (ACF) des Partners Autodesk in Birmingham, Großbritannien Die CFM-3D-Drucktechnologie von Moi Composites und die dualen Roboter von Kuka (Augsburg, Deutschland) wurden in beiden eingesetzt Einrichtungen. Laut Dominique Müller, Forschungsleiter im Team für additive Fertigung bei Autodesk, ermöglichte das CFM-System im Technologiezentrum von Autodesk das schnelle Drucken des Bootes und ermöglichte es Autodesk, die Technologie, die Moi aus der Ferne mit der Autodesk-Software steuerte, besser kennenzulernen . Die Gesamtdruckzeit für alle Komponenten betrug ungefähr zwei Monate.
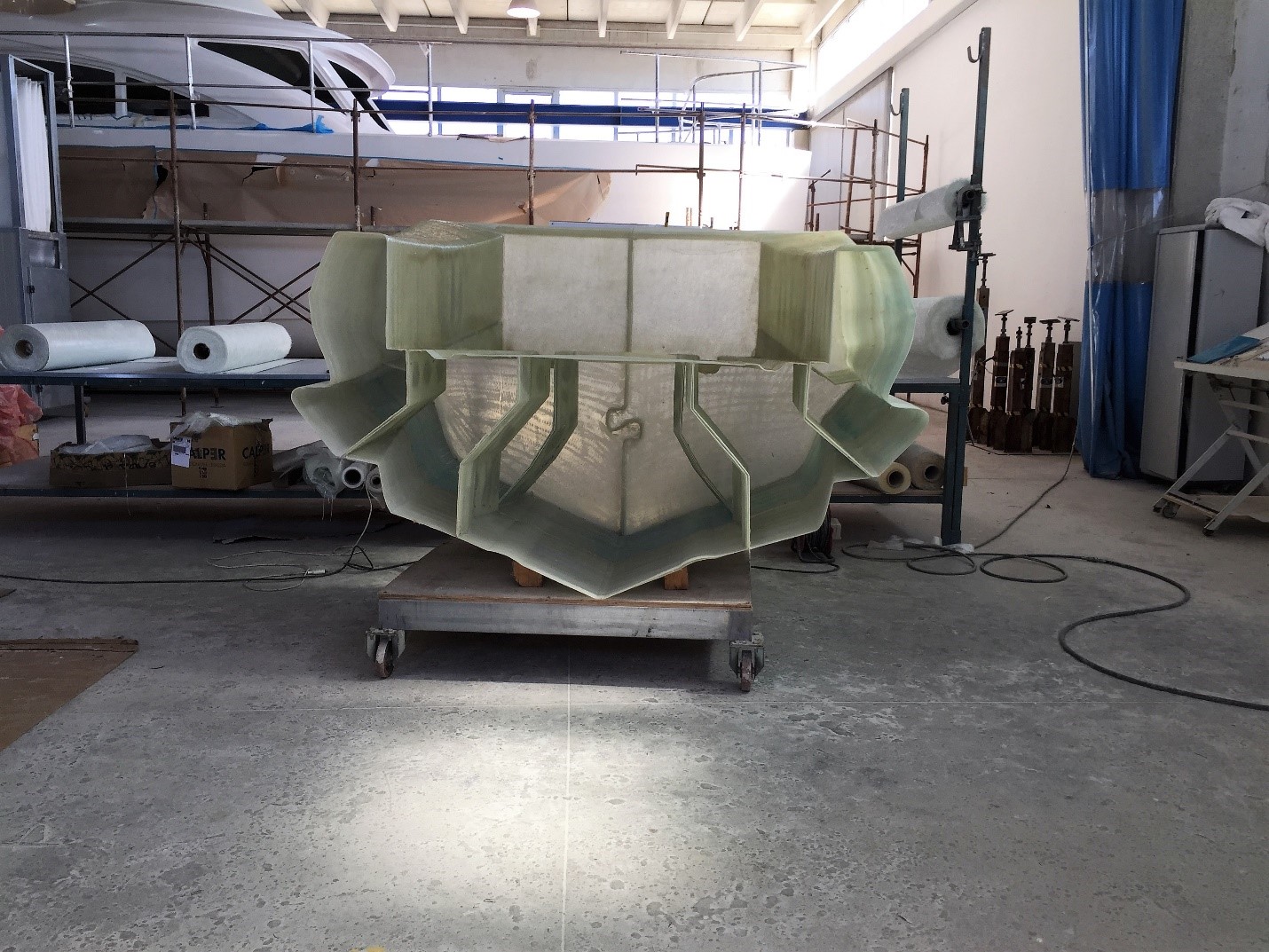
Die gedruckten Teile wurden an die Catmarine-Werft in Miggiano, Italien, geliefert, wo sie zusammengefügt und verklebt wurden. In einem hybriden Herstellungsprozess, ähnlich dem, den Moi bei Prothesen und anderen Teilen verwendet hat, wurde der gesamte Rumpf dann per Handlaminierung mit einer zusätzlichen Glasfaser/Polyester-Schicht mit PVC-Schaumkern laminiert, deren Dicke entlang der Struktur variiert, sagt Natale. Nachdem Rumpf und Deck vollständig zusammengebaut, geschliffen und gelbeschichtet waren, statteten die Partner von Moi Composites das Boot mit Antriebs-, Navigations- und anderen Systemen aus, um das Boot zu vervollständigen.
Erste Seeversuche und Stabilitätstests wurden im Herbst 2020 durchgeführt, wobei MAMBO bis zu 26 Knoten erreichte; Moi Composites plant, die Seeversuche im Sommer 2021 fortzusetzen, um auf die Zertifizierung des Bootes hinzuarbeiten.

„Additive Fertigung, Digitalisierung und Automatisierung können die Entwicklung neuer Konzepte und futuristischer Projekte beschleunigen, denn für jedes Boot, das Sie entwerfen möchten, müssen Sie eine neue Form erstellen. Mit dieser Technologie können Sie Ihr 3D-Modell ganz einfach modifizieren und erneut drucken. Dies ist besonders für Boote mit kurzer Laufzeit oder einmaligen Booten perfekt“, sagt Natale.
Weitere Informationen zu MAMBO finden Sie unter „MAMBO testet die Gewässer für den 3D-Druck großer Meeresstrukturen.“
Harz
- 5 gängige additive Fertigungsverfahren
- Additive Fertigung vs. subtraktive Fertigung
- Vorteile der additiven Fertigung
- Eine Umfrage zu Arbeitsabläufen in der additiven Fertigung
- Henkel bietet Werkstoffplattform für die additive Fertigung
- NCAMP veröffentlicht erstes Qualifizierungsprogramm für die additive Fertigung
- Nachhaltige Thermoplaste und additive Fertigung bilden in Colorado eine Allianz
- 5 Technologien, die die Fertigung revolutionieren
- Additive Fertigung in der Elektronik
- Additive Fertigung in der Luft- und Raumfahrt