Thermoplastische Verbundstruktur ersetzt Metalle an sicherheitskritischen Bremspedalen
Die Automobilindustrie stellte in den 1990er Jahren Gaspedale von Metallen auf spritzgegossene Kurzglas-Thermoplaste um. Die Umrüstung von Bremspedalen – als sicherheitskritische Komponenten mit anspruchsvollen Anforderungen an Steifigkeit, Festigkeit und Torsionsbelastung – dauerte jedoch viel länger. Tier-1-Automobilzulieferer Boge Rubber &Plastics Group (Damme, Deutschland) ist der erste Zulieferer, der die anspruchsvollen Leistungs- und Kostenziele der OEMs für Bremspedale aus thermoplastischen Verbundwerkstoffen erreicht. Einzigartiges Design, drei verschiedene Materialien und ein maßgeschneiderter Produktionsprozess ermöglichen es dem Unternehmen, Pedale herzustellen, die stärker, steifer, leichter und kostengünstiger sind.
Eine Nische finden, die zählt
Boge ist Entwickler und Produzent von Produkten zur Schwingungsdämpfung und Antriebsstrang-/Fahrwerksmontage sowie leichten Kunststoffmodulen und Pedalboxen (u.a. Kombinationen aus Brems-, Kupplungs- und Gaspedal) für die Automobilindustrie. Es produziert seit 2008 Automobilkomponenten aus Endlosfaser-Organoblech mit Kurzglas-Overmolding-Compounds. 2018 wurden unidirektionale (UD) thermoplastische Bänder hinzugefügt. Durch kontinuierliche Prozessinnovation wurden Zykluszeit und Kosten reduziert und das Geschäft gesteigert.
„2015 kam mein Chef zu mir und sagte:‚Die Veränderungen, die du gemacht hast, sind schön, Daniel, aber es wäre gut, wenn du einen größeren Markt mit wirklich zählenden Produktionsmengen finden würdest‘“, erinnert sich Dr.-Ing . Daniel Häffelin, Senior Manager/Leiter Leichtbauteam im Boge Global Innovation Center. Ein Team von Boge-Ingenieuren nahm die Herausforderung an und überlegte, wie die Glasfasereffizienz gesteigert werden kann, um Kosten zu senken und mehr Geschäfte zu machen.
„Organoblech ist ein tolles Produkt, aber man muss es richtig einsetzen, nur dort, wo es gebraucht wird“, erklärt Häffelin. „Wir hatten unseren Produktionsprozess bereits sehr schlank gemacht, also würden wir nicht viel gewinnen, wenn wir versuchen, die Zykluszeiten weiter zu verkürzen. Wir kamen zu dem Schluss, dass der beste Weg zur Kostensenkung darin bestand, die Menge der verwendeten Endlosfasern zu reduzieren, indem wir diese Fasern effizienter nutzen.“
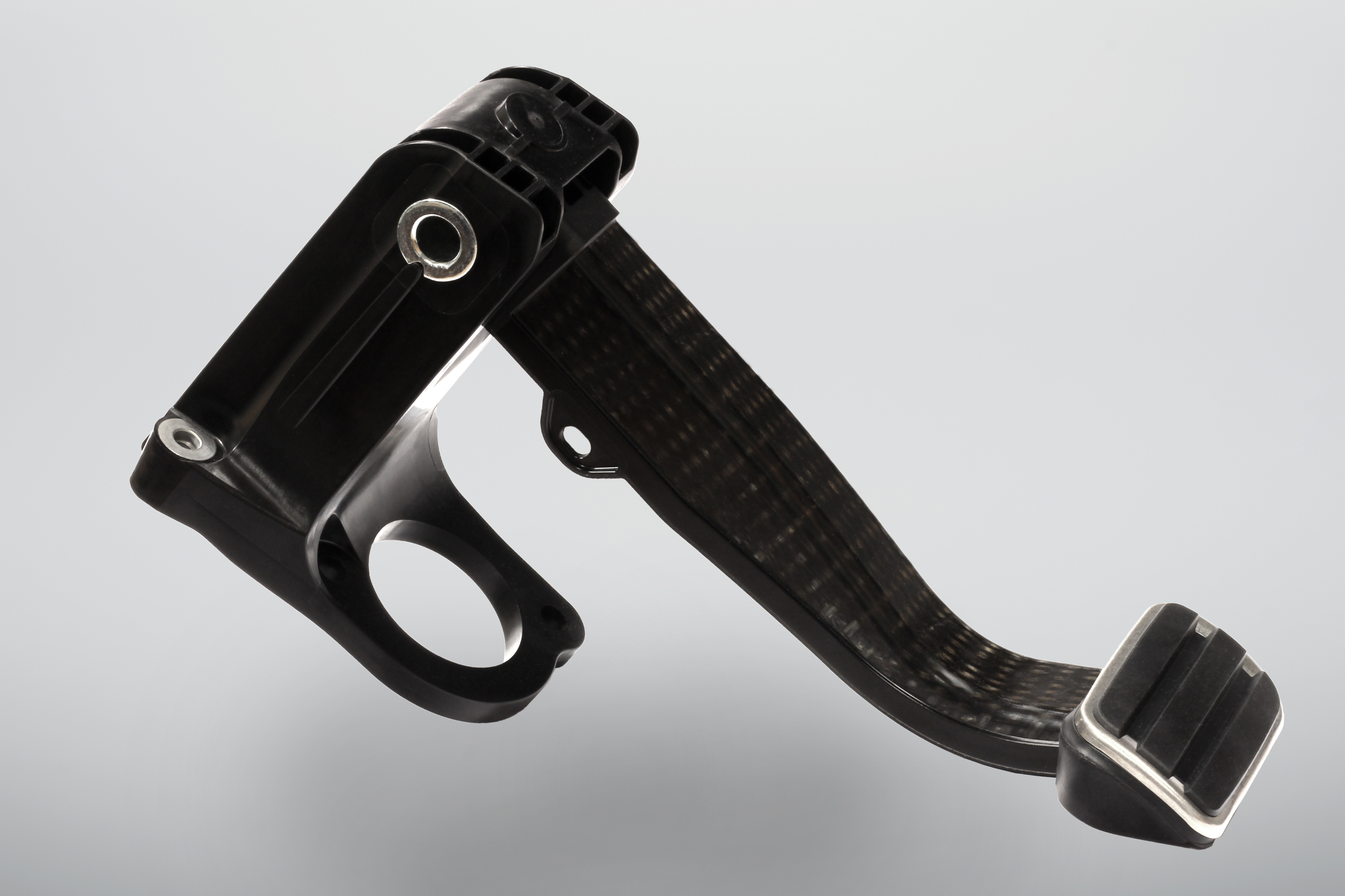
Pedale einfach kleiner oder dünner zu machen, würde auch nicht funktionieren, da die Größe und Form des Bremspedals praktischen Einschränkungen unterliegen, ganz zu schweigen von den anspruchsvollen Leistungsspezifikationen aufgrund seiner sicherheitskritischen Natur. Am sinnvollsten war es, Wege zur besseren Kontrolle der Faserorientierung zu finden, um die lokalen Eigenschaften in den Bereichen des Teils zu optimieren, in denen die höchsten Spitzenlasten auftreten, und Möglichkeiten zur Reduzierung der Wanddicke in weniger kritischen Bereichen zu bieten.
„Wir suchten nach einer Möglichkeit, Fasern lokal zu ‚steuern‘, damit wir sie genau dort platzieren konnten, wo wir sie brauchten, um Steifigkeit und Festigkeit zu erhalten“, fügt Dr. Torsten Bremer, CEO der Boge Rubber &Plastics Group, hinzu. „Wir wussten im Prinzip, dass dies möglich war, weil wir bereits Bestückungsautomaten für Sportartikel und Medizin in Betracht gezogen hatten, aber sie waren zu teuer. Da haben wir entschieden, dass wir einen neuen Prozess brauchen.“
„Wir haben bereits mit einem deutschen OEM zusammengearbeitet, um Wege zu finden, Bremspedale aus Verbundwerkstoff herzustellen, die ihren Leistungs- und Kostenanforderungen entsprechen“, erinnert sich Burkhard Tiemann, Executive Vice President, Product Line Leader – Plastics der Boge Plastics &Rubber Group. „Wir sagten zu unserem Kunden:‚Wir werden ein neues Verfahren mit UD-Tapes und Organoblech entwickeln‘. Sie sagten uns:‚Wenn Sie Masse und Kosten weiter reduzieren können, werden wir es tun.‘ Das war unser Ausgangspunkt. Wir haben 2015 ein großes Versprechen gegeben, ein All-Composite-Bremspedal zu liefern, das billiger, leichter und in hohen Stückzahlen produziert werden kann. Es hat drei Jahre gedauert, die Details auszuarbeiten und unsere ersten Produkte auszuliefern.“
Faserlenkung
Bremspedale aus Verbundwerkstoff müssen dieselben Leistungsspezifikationen erfüllen wie Pedale aus etabliertem Stahl oder Aluminium. Dazu gehören spezielle Anforderungen an das Versagensverhalten bei Belastungen von bis zu 3.000 Newton und stahlähnlicher Durchbiegung bei maximaler Belastung. Angesichts dieser Anforderungen und des begrenzten Bauraums erfordert die maximal belastbare Hauptschalenstruktur des Pedals eine durchgehende Faserverstärkung. Daher entschied sich das Team, Organoblech als Rückgrat des Pedals zu verwenden. UD-Tapes würden dann verwendet, um die Steifigkeit/Festigkeit lokal zu erhöhen und die Innenwände bei Belastungsspitzen im Bereich des Teils zu verstärken, das später beim Vorformen zu einem U-Kanal gebogen wird. Und in Bereichen, in denen funktionale Geometrien wie Rippen erforderlich waren, wurde eine Schnittglas-Umspritzmasse spezifiziert. Das Team war der Ansicht, dass dieser hybride Ansatz die Fasereffizienz steigern und gleichzeitig den Materialverbrauch, die durchschnittliche Wanddicke und die Zykluszeit reduzieren würde.

Das Team begann mit intensiven Simulationsarbeiten, um die Faserstandorte während der Produktion zu optimieren. Die Grundlage für Boges Arbeit bildete das 2011-2014 öffentlich geförderte deutsche Forschungsprogramm SoWeMa (Software, Tools, and Machine Development for a Fully Automatic and Closed Lightweight Manufacturing Chain).
„Die SoWeMa-Recherche deckte viele der Fragen ab, die wir uns ein Jahr später für unser eigenes Unternehmen stellen würden“, erklärt Häffelin. „Da Design zum Kern-Know-how von Boge gehört, haben wir mit den Grundlagen des SoWeMa-Programms begonnen und unsere eigenen FE-Simulationsfunktionen (Finite-Elemente) für anisotrope Layup-Strukturen entwickelt.“
Ein Schwerpunkt war die kombinierte Topologieoptimierung für das Tape-Layup und die Rippenstruktur. „Wir haben einen Iterationszyklus erstellt, um die Platzierung der Tapes zu optimieren und die Rippenstruktur entsprechend anzupassen, da beide über die Steifigkeit und Festigkeit des Teils miteinander verbunden sind“, fährt K. Siebe, FEA-Ingenieur, CRRC Innovation Center, fort. „Da die Materialkombination aus UD-Tapes, Organoblech und Kurzfasermaterialien einzigartig ist und ihre Anwendung an ein bestimmtes Feuchtigkeits- und Temperaturfenster gebunden ist, haben wir eigene Materialkarten entwickelt, um das Verhalten dieser Materialien bei physikalischen Tests genauer zu charakterisieren. ”
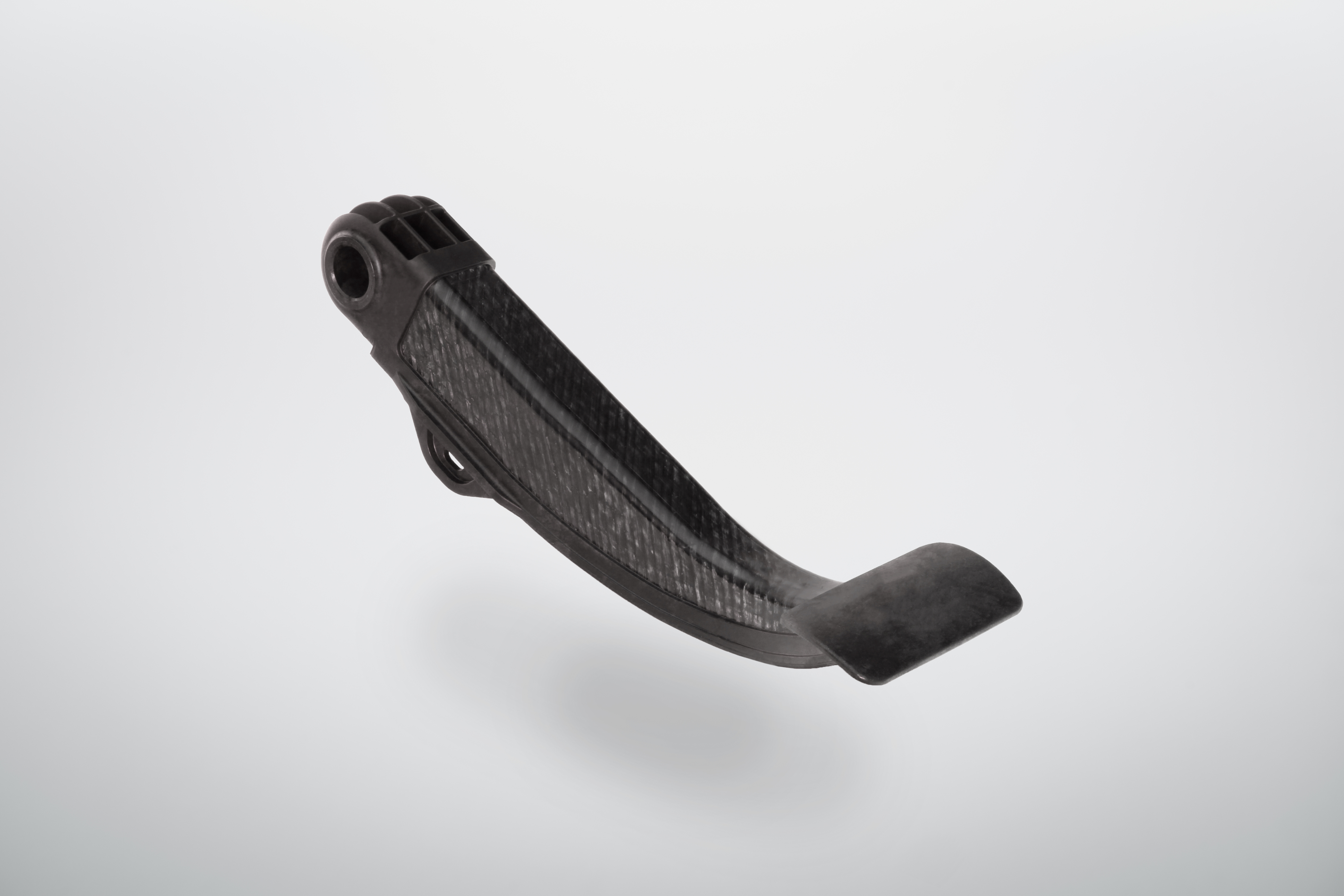
Boge spezifizierte den Schichtaufbau und die Faserarchitektur für jedes Material basierend auf Simulationsergebnissen und einem gegebenen Pedaldesign. Lanxess Deutschland GmbH (Köln, Deutschland) liefert Organoblech in Faservolumenfraktionen (FVF) von 45-50%. Thermoplastische UD-Bänder mit FVFs von 55-60% wurden von Celanese Corp. (Irving, Texas, USA) geliefert. Kurzglas-Injektionsmassen für diese Anwendung mit 40-60% Fasergewichtsanteil (FWF) wurden von mehreren Quellen geliefert. Alle Materialien sind schwarz und verfügen entweder über eine Polyamid 6 oder 6/6 (PA6, PA6/6) Matrix. Um die Kundenspezifikationen zu erfüllen, ist PA6 das Standardharz für alle drei Verbundwerkstofftypen. Je nach Luftfeuchtigkeit und Temperatur während der Herstellung sowie Platzverhältnissen und Pedalgeometrie kann Boge jedoch auch PA6/6 für das Overmolding-Harz verwenden, da die beiden Polymere ähnlich genug sind, um sich gut zu verbinden.
Dreistufige Produktion
Parallel zur Konstruktion arbeitete das Team an einem dreistufigen Produktionsprozess. Im ersten Schritt wird ein Tailored-Fibre-Blank erstellt, indem vorgeschnittene und vorverfestigte Organobleche als stabile Basis verwendet werden, auf denen UD-Tapestreifen, die an Lastpfaden ausgerichtet sind, strategisch angeheftet werden, um die Schalenstruktur des Teils zu verstärken. Im zweiten Schritt wird der Rohling bewegt und nacheinander erhitzt, konsolidiert und geformt/drapiert. Im dritten Schritt wird es mit Kurzglasmasse umspritzt, um die Rippenstruktur zu erzeugen.
Um schnelle Taktzeiten zu erreichen, war bei dieser Anlage Roboterhandling selbstverständlich. Ein wichtiges Prozessmerkmal, das das Team integrieren wollte, war die Flexibilität, Bänder jeder Länge, in jeder Ausrichtung und in jeder Position auf einer Seite der Organoblechschale zu platzieren und diese Bänder per Laser an die Schale zu heften, damit sie sich nicht verschieben in nachfolgenden Schritten.
Eine weitere Entscheidung des Teams war, den Tailored Blank nicht direkt nach dem Layup vorzukonsolidieren, sondern kurz vor dem Drapieren/Vorformen und Umspritzen. Das Team argumentierte, dass das Material während des Drapierens/Vorformens sowieso wieder erwärmt werden müsste, und um kostengünstig zu sein, musste die Gesamtzykluszeit nahe 1 Minute gehalten werden. Daher erhitzt und verfestigt Boge den Rohling kurz vor dem Drapieren/Vorformen durch einen schnellen Temperaturanstieg in Kombination mit hohem Druck, um eine starke mechanische Verbindung zwischen Band und Organoblech herzustellen. Das Aufheizen stoppt und die Teiletemperatur beginnt zu sinken, während der noch heiße konsolidierte Rohling in die Drapierkavität einfährt, bevor er erneut bewegt und in einer zweiten Kavität mit Rippen und anderen Funktionsmerkmalen umspritzt wird. Zwischen allen drei Materialien werden starke mechanische Bindungen mit nachgewiesener Polymerkettenpenetration erreicht. Es ist keine Nachbearbeitung erforderlich.
Um die Qualitätsanforderungen für diese sicherheitskritischen Teile zu erfüllen, entwickelte das Team außerdem ein schnelles, genaues und Industrie 4.0-konformes System, das Bild-, Kraft-, Zeit-, Druck- und Temperatursensoren verwendet, die das Material in jedem Schritt des Herstellungsprozesses überprüfen. Das System speichert diese Daten dann und verknüpft sie mit der eindeutigen Identifikationsnummer jedes Pedals. Dies gewährleistet eine 100-prozentige Rückverfolgbarkeit aller beteiligten Materialien, Schichten und Prozesseinstellungen.
Bisherige Erfolge
Der maßgeschneiderte, vollautomatisierte und qualitätskontrollierte Prozess von Boge hat 2018 den Schritt vom Prototypen zur Großserienfertigung geschafft. Die aktuelle Fertigungszelle produziert etwa jede Minute ein neues Pedal und kann bis zu 1 Million Teile pro Jahr fertigen. Die Vollverbundpedale verwenden 33 % weniger Organoblech als frühere Designs und die nominale Wandstärke wurde von 3 auf 2 Millimeter gesenkt. Die Pedale sind außerdem 50-55% leichter, erfüllen oder übertreffen jedoch die Festigkeitsanforderungen für Stahl. Die leichteren Pedale verbessern die Fahrhaptik für Verbraucher und das gesamte System ist am Ende der Lebensdauer zu 100 % recycelbar. Mit dem aktuellen Verfahren sind Verbundpedale zu Aluminiumpreisen gleichwertig und etwas teurer als Stahl. Weitere Anwendungen im Automobil- und Sportbereich sind in Entwicklung.
Wie sieht die Zukunft aus, wenn Automobilhersteller ihre Ressourcen auf die Elektrifizierung von Flotten verlagern? „Da Drive-by-Wire [elektromechanische Betätigungssysteme] und die Elektrifizierung des Antriebsstrangs immer häufiger werden, könnten Gaspedale wegfallen, aber Bremspedale werden bleiben“, sinniert Häffelin. „Wir werden jedoch wahrscheinlich eine stärkere Integration der Elektronik, einschließlich Sensoren, in Bremspedalen sehen. Das erhöht die Komplexität der Teile erheblich und macht Verbundwerkstoffe noch mehr wettbewerbsfähiger als Metalle.“
Materialeinsatz, Prozessschritte und Ausrüstungskriterien werden in CW näher erläutert 's Folgeartikel vom Januar 2021, "Bespoke process produziert jede Minute ein Verbundbremspedal."
Harz
- Langfaserverstärkter Nylon-Verbundstoff ersetzt Aluminium-Motorgehäuse
- Durchgehend faserverstärkter thermoplastischer Verbundwerkstoff vollständig aus natürlichen Ressourcen hergestellt
- Solvay erweitert die Kapazität von thermoplastischen Verbundwerkstoffen
- Oribi Composites, Packard Performance-Partner für Offroad-Powersports-Thermoplast-Verbundrad
- Konsortium sucht Lösungen für thermoplastische Kohlefaser-Verbundstrukturen
- INEOS Styrolution baut Produktionsstätte für thermoplastischen Verbundwerkstoff StyLight
- Xenia führt thermoplastische CF/PP-Composite-Compounds ein
- Thermoplastische Verbundrohre auf dem Vormarsch in der Tiefsee
- NIARs NCAMP-qualifizierender TenCate thermoplastischer Verbundwerkstoff
- TenCate feiert den Zusammenschluss des Konsortiums für thermoplastische Verbundwerkstoffe in Brasilien