Kohlefaser in Druckbehältern für Wasserstoff
Wasserstoff als CO2 -freie Alternative zu fossilen Brennstoffen ist seit Jahrzehnten in Sicht, und das Wachstum bei Druckbehältern aus kohlenstofffaserverstärktem Kunststoff (CFK) für die Wasserstoffspeicherung ist definitiv auf dem Vormarsch. Im Jahr 2020 wurde Wasserstoff jedoch zu einem Mandat, das von der Europäischen Kommission (EC) als eine der wichtigsten Prioritäten identifiziert wurde, um den europäischen Grünen Deal für eine nachhaltige Wirtschaft und eine klimaneutrale EU bis 2050 zu erreichen. Zu den wichtigsten Ereignissen für Wasserstoff in der Luftfahrt gehören:
- Mai 2020 — Clean Sky 2 und The Fuel Cells and Hydrogen Joint Undertaking (FCH JU) veröffentlichten „Wasserstoffbetriebene Luftfahrt“, in der detailliert beschrieben wird, wie wasserstoffbetriebene Flugzeuge mit kurzer Reichweite (85-165 Passagiere) bis 2030 in Dienst gestellt werden könnten. 2035.
- Juni 2020 – Frankreichs Pandemie-Hilfsprogramm in Höhe von 17 Milliarden US-Dollar ist an die Ziele des Berichts „Wasserstoffbetriebene Luftfahrt“ gebunden; Air France will CO2 . senken -Emissionen bei Inlandsflügen bis 2024 halbieren.
- Juli 2020 — EK veröffentlicht „Eine Wasserstoffstrategie für ein klimaneutrales Europa“ und fordert Investitionen in Höhe von 65 Mrd 10 Milliarden im Zeitraum 2020-2030).
- Juli 2020 — Airbus-Chef Guillaume Faury im Interview mit der Aviation Week Herausgeber Graham Warwick, verpflichtet sich zum ersten dekarbonisierten Flugzeug-EIS bis 2035; Er prognostiziert den Start des Programms bis 2027-28 und die Reife der notwendigen Technologien bis 2025.
- Juli 2020 — ZeroAvia (Hollister, Kalifornien, USA) absolviert Testflug einer einmotorigen, sechssitzigen Piper Flugzeug umgerüstet, um komprimierten Wasserstoff (H2 .) zu verwenden ) Gas und enthüllt US-basierte Flugtests für einen ähnlich modifizierten Twin-Turboprop, 19-Sitzer Dornier Tun 228 laut Roadmap zur Zertifizierung eines H2 mit 20 Sitzen -motorisierte Flugzeuge mit einer Reichweite von 500 Meilen bis 2023.
- August 2020 — Universal Hydrogen (Los Angeles, Kalifornien, USA) kündigt Doppeltankmodule für ein 50-sitziges Flugzeug (siehe Foto) sowie die Betankungslogistik und Infrastruktur für regionale Fluggesellschaften/Betreiber an, bis 2024 kommerziell zu sein.
Die Lebensfähigkeit von Wasserstoff als Kraftstoffquelle – unabhängig von der Branche – hängt von der raschen Entwicklung einer Vielzahl von Transport-, Liefer- und Speichertechnologien ab, die noch jung sind, sich aber schnell entwickeln. Die Kommerzialisierung dieser Technologien wird nicht einfach sein, aber sie werden in Angriff genommen. Unten finden Sie eine Zusammenfassung einiger Arbeiten, die gerade durchgeführt werden.
Universeller Wasserstoff
Universal Hydrogen wurde 2020 von Paul Eremenko, ehemaliger CTO von Airbus SE (Leiden, Niederlande) und United Technologies Corp. (Farmington, Connecticut, USA) mitgegründet Betankungsinfrastruktur. Eine Schlüsselkomponente ist sein Kraftstoffmodul, das aus zwei H2 . besteht Lagertanks in einem Rahmen aus kohlefaserverstärktem Polymer (CFK). „Wir werden die Module nach Bedarf an den Standort liefern, sodass keine Wasserstoffspeicherinfrastruktur erforderlich ist“, erklärt J.P. Clarke, CTO von Universal Hydrogen. „Die Module werden einfach wie eine Batterie oder Bordküche in das Flugzeug geladen.“
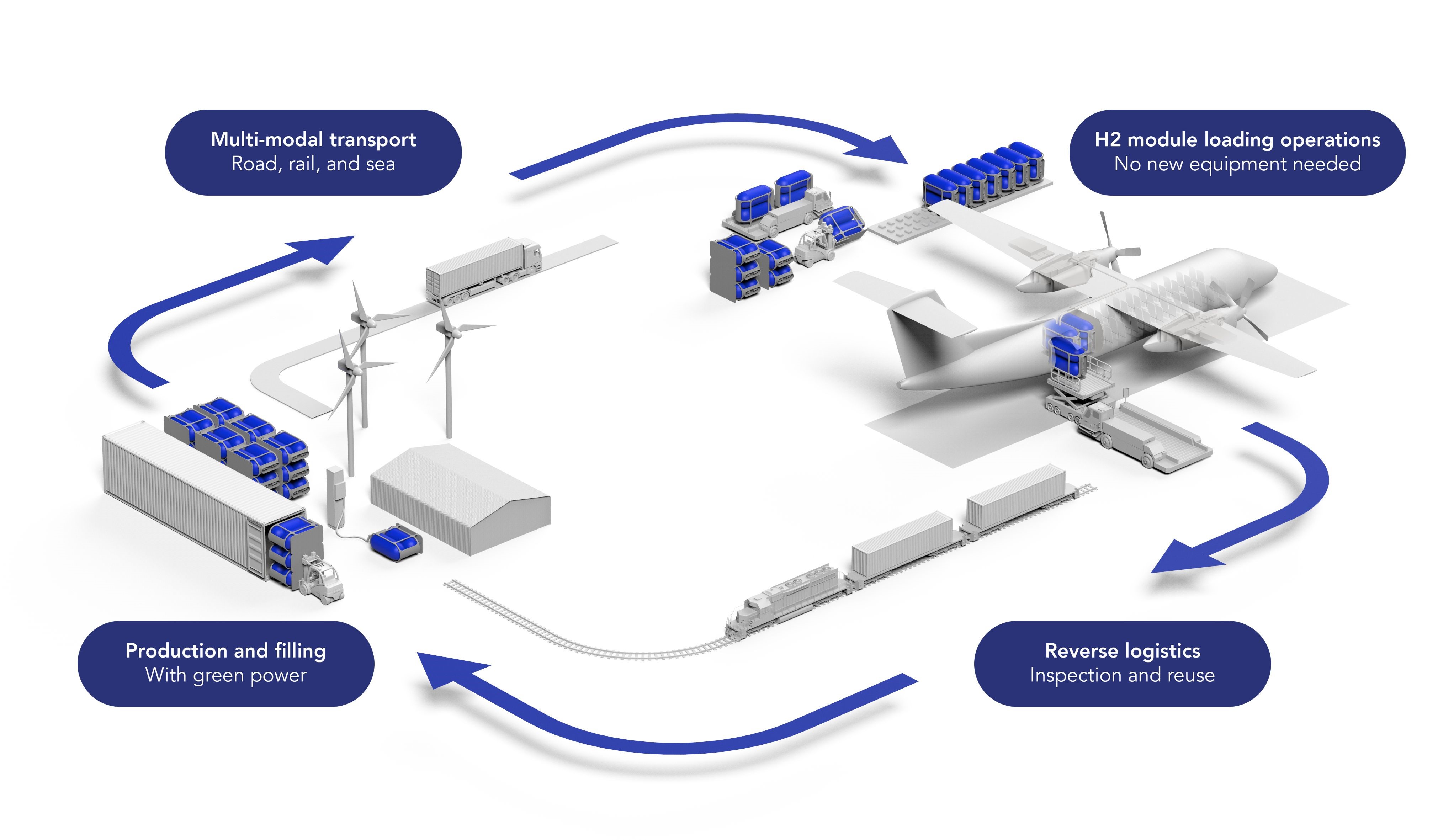
Bildnachweis:Universal Hydrogen
Module wurden zuerst für den 50-sitzigen Dash entwickelt 8 und ATR Turboprop-Regionalflugzeuge. Diese Module verfügen über 2,7 m lange Tanks mit einem Durchmesser von 3 Fuß, die entweder Kohlefasern verwenden, um H2 . zu halten Gas bei 850 bar mit einer Dichte von 50 kg/m 3 , oder isolierte Metalltanks zur Aufnahme von flüssigem H2 (LH2 ) bei Standarddruck und -temperatur von 71 kg/m 3 Dichte. Obwohl die LH2 Tanks bieten einen höheren volumetrischen Wirkungsgrad, die isolierten, aber ungekühlten Tanks müssen innerhalb von 42 Stunden verwendet werden, da LH2 verdampft, wenn es nicht bei -253°C aufbewahrt wird. „Beide Tanktypen sitzen in einem leichten, strukturoptimierten Verbundrahmen, der auch Schlagfestigkeit und einige Tragfähigkeiten verleiht“, sagt Clarke.
Die H2 Gastanks enthalten eine undurchlässige Polymerauskleidung, die mit Schichten aus trockenem Kohlefasergeflecht und einer schützenden Außenschicht aus Kevlar-Aramidfasern umwickelt ist. „Es ist kein Harz erforderlich“, erklärt Clarke. „Der Liner spricht die Durchlässigkeit an, während das Carbon die Reifen- und Axialbelastungen aufnimmt und die äußere Schicht plus Rahmen Beschädigungen verhindert; dadurch werden Gewicht und Dicke reduziert. Dieses integrierte Tank- und Rahmendesign hat es uns in Kombination mit der Zuordnung von Funktionen zu jeder der Tankschichten ermöglicht, einige signifikante Verbesserungen des Massenanteils zu erzielen.“
Der Massenanteil wird berechnet, indem die Masse der gespeicherten Wasserstoffmasse durch die des gesamten Moduls dividiert wird. Je größer der Massenanteil, desto besser. „Wir haben eine sehr umfangreiche Handelsstudie durchgeführt, die den Massenanteil und die volumetrische Effizienz im Kontext des Dash untersucht hat 8 und ATR Flugzeuge“, bemerkt Clarke. „Sie betrachten also Volumen und Gewicht des Treibstoffs im Vergleich zu dem, was in diese Flugzeuge passt, die erreichbare Reichweite und das maximale Startgewicht, die Gewichtsverteilung usw. Mit H2 Gas bei 850 bar können wir mit einer 45-Minuten-Reserve ca. 400 Seemeilen und mit der LH2 about ca. 550 Seemeilen fliegen Panzer. Die durchschnittliche Bühnenlänge für eine Turboprop-Mission beträgt jedoch etwa 300 Seemeilen, daher ist die riesige die meisten dieser Flüge können mit gasförmigem H2 . durchgeführt werden mit CFK-Tanks.“
Wird Universal Hydrogen mit einem Hersteller von Verbundtanks zusammenarbeiten? „Unsere Strategie besteht darin, dort zusammenzuarbeiten, wo es sinnvoll ist, und an unserem Kerngeschäft festzuhalten“, sagt Clarke. Er bekräftigt den Fokus von Universal Hydrogen:„Wir wollen der Anbieter des Kraftstoffs und der Infrastruktur sein. Wir stellen die Module bereit und bringen sie dorthin, wo sie gebraucht werden, damit sich unsere Partner auf den Rest des Flugzeugdesigns und -betriebs konzentrieren können. Unser Ziel ist es, ein Wegbereiter der wasserstoffbetriebenen Luftfahrt zu sein.“
SpaceTech4Sea
Wie der Luftverkehr unterliegt auch die Schifffahrt Vorschriften zur Reduzierung von CO2 und andere Treibhausgasemissionen (THG). Ab Januar 2018 müssen Schiffe mit mehr als 5.000 BRZ, die Fracht oder Passagiere in Häfen im Europäischen Wirtschaftsraum (EWR) laden oder löschen, ihr CO2 monitor überwachen und melden Emissionen. Darüber hinaus hat die Internationale Seeschifffahrtsorganisation (IMO) im Rahmen ihres MARPOL-Übereinkommens zur Verringerung der Verschmutzung durch Schiffe ab Januar 2020 vorgeschrieben, dass der Schwefel in Heizöl von 3,50 % m/m (Masse nach Masse) auf 0,50 % reduziert werden muss. Die IMO hat sich auch zu einer ersten THG-Strategie verpflichtet, bis 2050 eine Reduzierung um 50 % gegenüber dem Niveau von 2008 anzustreben.
„Die beste Möglichkeit, die Vorschriften einzuhalten, besteht darin, zunächst auf Flüssigerdgas (LNG) umzustellen“, sagt Dr. Panayotis Zacharioudakis, Geschäftsführer von Ocean Finance (Athen, Griechenland), einem Beratungsunternehmen für maritime Nachhaltigkeit und Koordinator der EU-Projekte SuperGreen und SpaceTech4Sea. SuperGreen wird in Griechenland ein nachhaltiges und umweltfreundliches Transportsystem schaffen, das aus elektrischen Pendlerschiffen und zwei Hybrid-LNG/Elektro-Katamaranen besteht, die den Hafen von Piräus mit anderen Häfen im östlichen Mittelmeernetz verbinden werden. „Für dieses Projekt bauen wir eine Hochgeschwindigkeitsfähre aus CFK“, erklärt Zacharioudakis. „Wenn wir einen hochmodernen LNG-Tank aus Metall verwenden würden, würde er sieben Tonnen wiegen, was etwas mehr als 70 Passagieren entspricht [100 Kilogramm pro Person mit Gepäck]. Also müssten wir die Passagierkapazität um 70 reduzieren.“
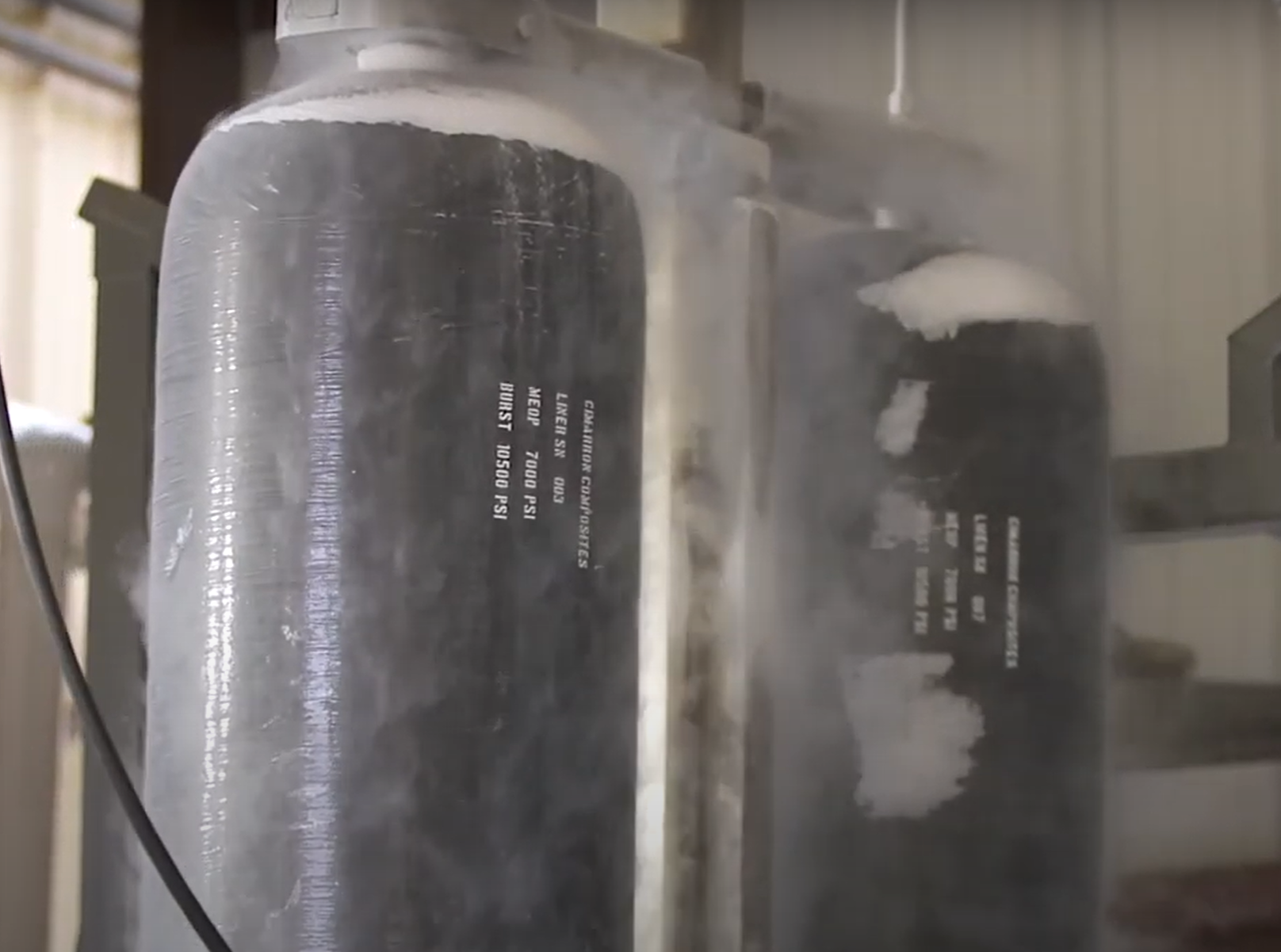
Warum das zusätzliche Gewicht? „Im Vergleich zu Diesel muss LNG bei kryogenen -163°C gelagert werden und die Metalltanks müssen Materialien, Konstruktion, Isolierung und Betriebssysteme verwenden, die den Anforderungen der IMO für gasförmige Kraftstoffe oder dem IGF-Code entsprechen“, sagt Zacharioudakis. Für Ocean Finance war das zusätzliche Gewicht nicht akzeptabel, daher begann man mit der Suche nach möglichen Lösungen und fand einen Bericht über Kryotanks von Cimarron Composites (Huntsville, Ala, USA), die mit der NASA entwickelt wurden.
„Zu diesem Zeitpunkt haben wir das Projekt SpaceTech4Sea der EASME (Europäische Agentur für KMU) gestartet“, sagt Zacharioudakis. „Die Idee ist, die Luft- und Raumfahrttechnik für maritime Anwendungen zu modifizieren.“ Dritter Projektpartner ist die Klassifikationsgesellschaft American Bureau of Shipping (ABS, Houston, Texas, USA), die die Technologie validieren und qualifizieren wird. Im September 2019 erteilte ABS die grundsätzliche Zulassung (AIP) für Cimarrons Konzeptentwurf eines ultraleichten, kryofähigen LNG-Verbundtanks. Seitdem hat es Sub- und Full-Scale-Tanks für die Zertifizierung gebaut und getestet. „Sie haben gerade die letzten Tests abgeschlossen“, sagt Zacharioudakis. „In etwas mehr als zwei Monaten werden wir eine vollständige Zertifizierung für Composite-LNG-Tanks für den Marinemarkt haben. Dieser Tank ermöglicht eine Gewichtseinsparung von mehr als 85 % gegenüber einem herkömmlichen Metalltank.“
Obwohl die meisten Besonderheiten des Tanks proprietär sind, sagt der Gründer und Präsident von Cimarron Composites, Tom DeLay, dass er aus Kohlefaser und einem fortschrittlichen duroplastischen Harz unter Verwendung von etwas Harzinfusion und nasser Filamentwicklung hergestellt wird. „Wir haben Tanks mit 25 Zoll und 40 Zoll Durchmesser getestet und sprechen mit dem CFK-Fährbauer für SuperGreen über Tanks mit einem Fassungsvermögen von fünf Kubikmetern [5.000 Liter], die mit einem Tank von 2 Metern Durchmesser erreicht werden könnten und 2,5 Meter lang.“ Ocean Finance sieht einen Markt für mehr als tausend solcher Tanks und wird mit Cimarron zusammenarbeiten, um eine automatisierte Produktion, möglicherweise in Griechenland, aufzubauen.
Und was ist mit Wasserstoff? „Während wir diese LNG-Projekte abgeschlossen haben, haben wir begonnen, uns mit Wasserstoff zu befassen“, bemerkt Zacharioudakis. „In Europa gibt es so viel Interesse, Aktivität und jetzt auch Fördermittel. Ein Problem ist jedoch, dass die Schifffahrtsvorschriften vorschreiben, dass Tanks eine Haltezeit von bis zu 15 Tagen für LNG bieten müssen. Dies wird für LH2 . gleich sein .“ DeLay räumt ein, einen kryofähigen Tank für LH2 entwickelt zu haben (-253 °C, siehe oben) ist viel schwieriger als die Entwicklung eines kryofähigen Tanks für LNG (-196 °C); Eine der Herausforderungen besteht darin, Materialien zu finden, die Versprödung und Rissbildung widerstehen. Er arbeitet jetzt mit Ocean Finance zusammen, um eine Handelsstudie abzuschließen, in der die technischen und wirtschaftlichen Faktoren der Verwendung von flüssigem gegenüber gasförmigem H2 . untersucht werden für Seeschiffe.
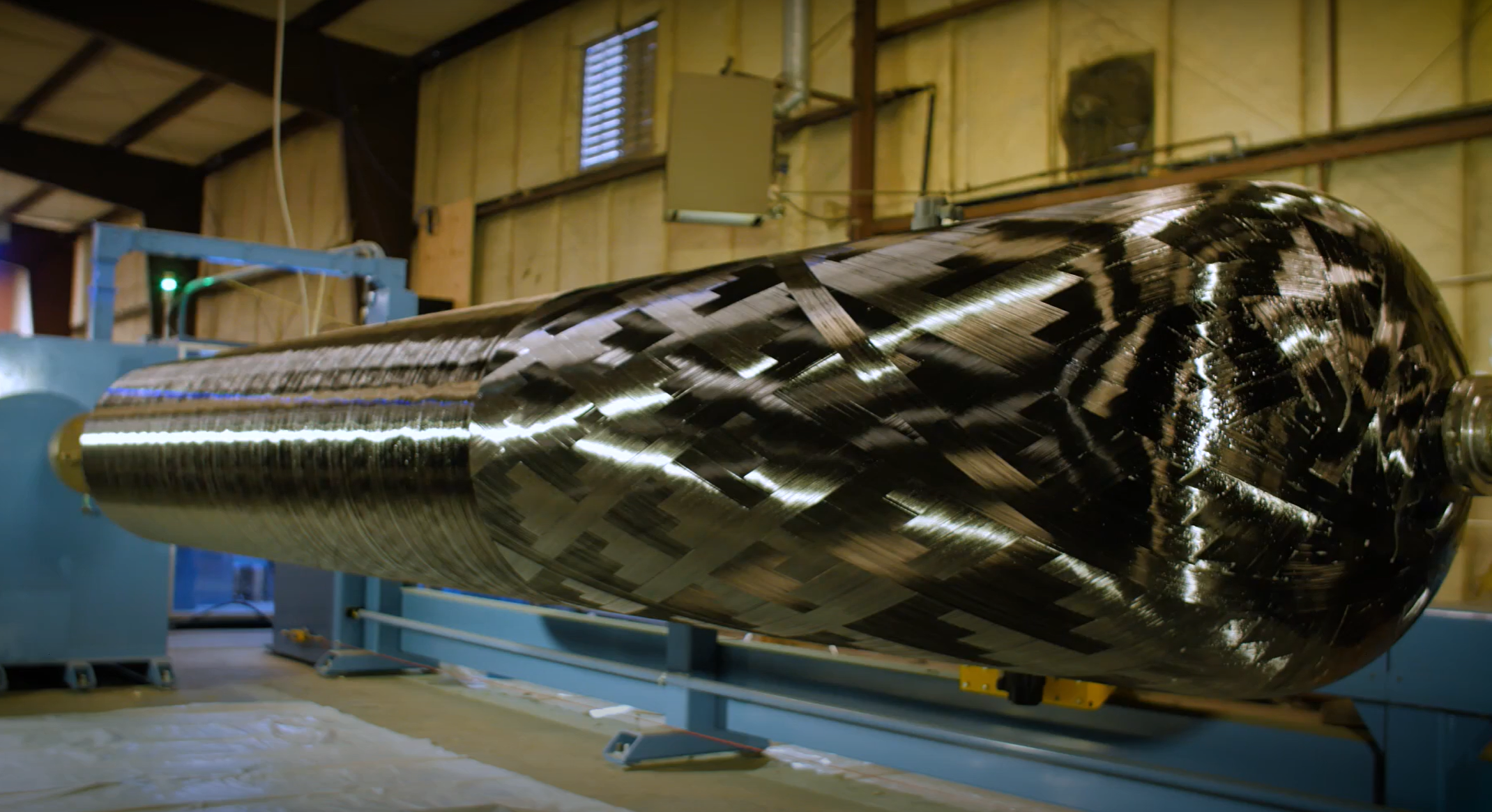
Neptun-Panzer für H2 Gas
Cimarron Composites hat insbesondere bereits einen CFK-Tank vom Typ IV für die Hochdruckspeicherung von Wasserstoff und anderen Gasen entwickelt. „Unser ursprünglicher Jupiter-Tank wurde für den Transport der meisten Industriegase, einschließlich Wasserstoff, bei einem Druck von 4.350 psi [300 bar] entwickelt“, sagt DeLay. „Wasserstoff wird jedoch bei höheren Drücken effektiver transportiert, weshalb wir den Neptun-Tank mit 7.500 psi [517 bar] entwickelt haben.“
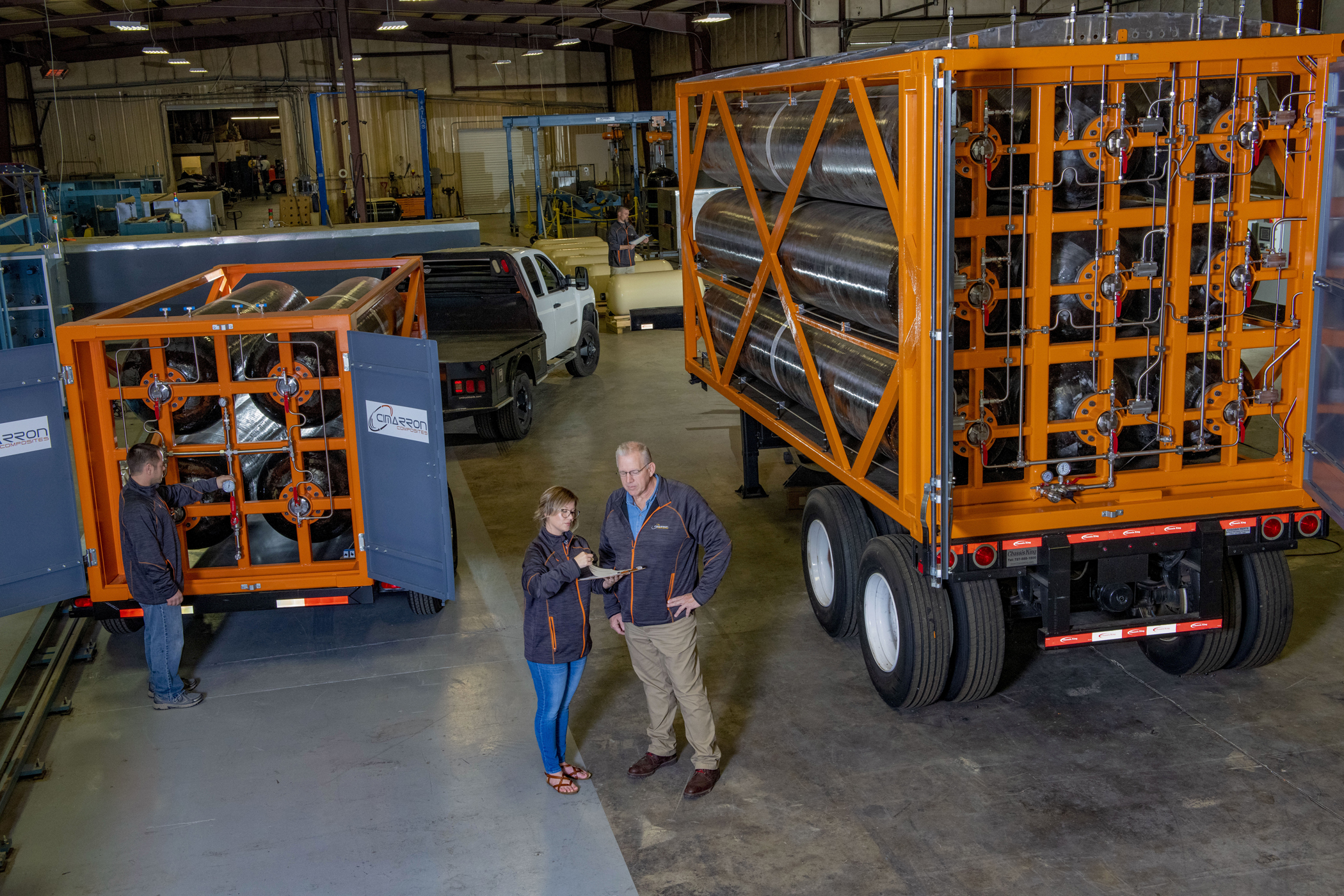
Sowohl die Jupiter- als auch die Neptun-Tanks haben die unzähligen Tests gemäß den Anforderungen der UN ISO 11515 bestanden und sind in einer Reihe von Durchmessern und Längen bis zu 26 Fuß erhältlich. „Diese Tanks wurden für den Versand in Standardmodulen per Lkw, Bahn oder Schiff entwickelt“, so Delay. „Wir haben festgestellt, dass ein Durchmesser von 30 Zoll eine ideale Packungseffizienz hat, sodass wir mehr Wasserstoff transportieren können als mit Zylindern mit größerem Durchmesser. Bei einer Länge von 19 Fuß passen neun Tanks in einen Standard-20-Fuß-Container. Bei 67 Kilogramm Wasserstoffgas pro Tank können wir 600 Kilogramm in einem 20-Fuß-Container und 1.200 Kilogramm in einem Standard-40-Fuß-Container bewegen.“
„Wir kaufen Kohlefaser von allen wichtigen Lieferanten, darunter Toray [Tokio, Japan], Mitsubishi Rayon [Tokio], Teijin [Rockwood, Tennessee, USA] und Hyosung [Seoul, Südkorea]“, fügt DeLay hinzu, „aber für Neptun haben wir uns bei drei verschiedenen Lieferanten gleichzeitig qualifiziert. Wir formulieren das Harz selbst unter Verwendung handelsüblicher Produkte und kontrollieren den Faser- und Harzgehalt sowie die Spannung während des Filamentwickel- und Ofenhärtungszyklus sehr streng, um thermischen Stress zu vermeiden. All dies trägt zur mechanischen Leistung der Panzer bei.“
Unabhängig davon, ob der Bedarf an kryogenen Flüssigkeitsspeichern oder Hochdruck-Gasspeichern besteht, DeLay sieht die Möglichkeiten immer größer. „Wir haben Jahre gebraucht, um unser Know-how aufzubauen“, sagt er, „angefangen von Treibstofftanks für Raketen bis hin zu den großen Lager- und Transporttanks, die wir jetzt entwickeln und produzieren. Vor einem Jahr war ich skeptisch gegenüber Wasserstoff und dachte, der einzige Grund dafür sei ein Vorstoß der Regierung. Aber jetzt bekommen wir sehr große Bestellungen und Anfragen aller Art. Wir sehen, dass weltweit eine Vielzahl von Industrien ernsthaft in Wasserstoff investieren und Regierungen diese Entwicklung unterstützen. Es sieht so aus, als wären wir mit den richtigen Produkten zur richtigen Zeit bereit.“
Harz
- Kohlenstofffasern
- Warum Kohlefaser ein großartiges Herstellungsmaterial für Schmuck ist
- Kohlefasergeräte für Ihr Zuhause
- Was ist Kohlefaser?
- 5 Tipps zum Finden des besten Herstellers von Kohlefaserteilen
- Kohlefaserverstärkter Kunststoff (CFK)
- Die 3 wichtigsten Anwendungen für den 3D-Druck von Kohlefasern in der Fertigung
- Innovative Anwendungen für Kohlefaser
- Ist Kohlefaser leitfähig?
- Konsortium sucht Lösungen für thermoplastische Kohlefaser-Verbundstrukturen