AFRL bewertet Flechten, SMP-Werkzeuge und VARTM für kostengünstigere zukünftige Triebwerkseinlasskanäle
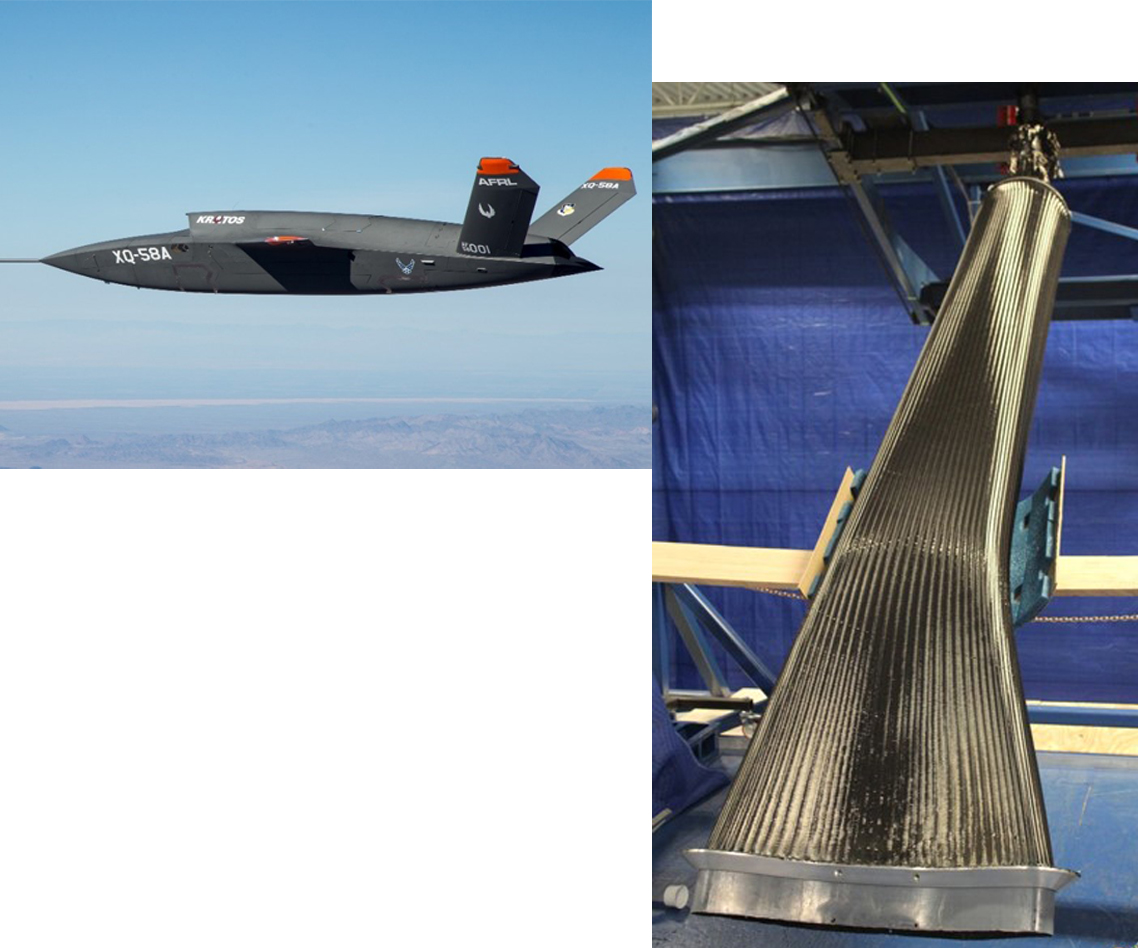
Ein Teil der Wissenschafts- und Technologiestrategie 2030 der US-Luftwaffe umfasst den Masseneinsatz kostengünstiger unbemannter Flugsysteme, um zukünftige Einsätze zu unterstützen. Um diese Vision zu verwirklichen, müssen neue Fertigungsstrategien identifiziert werden, die die schnelle Herstellung hochwertiger Komponenten für die Luft- und Raumfahrt zu niedrigeren Kosten unterstützen können, als dies derzeit mit Legacy-Prozessen möglich ist.
Die Manufacturing and Industrial Technologies Division des Air Force Research Laboratory (AFRL, Dayton, Ohio, USA) und das in Ohio, USA ansässige Auftragnehmerteam der Cornerstone Research Group (Dayton), A&P Technology (Cincinnati) und Spintech LLC (Xenia), führten Untersuchungen durch zur Quantifizierung der Vorteile des Ersetzens eines herkömmlichen Prepreg-Handlaminats durch trockenfasergeflochtene Vorformlinge und vakuumunterstütztes Harzspritzpressen (VARTM) für die Herstellung eines 2,8 m langen, S-förmigen Motoreinlasskanals aus Verbundwerkstoff.
Die Einlasskanäle von Flugzeugtriebwerken sorgen für eine konstante Luftzufuhr, um ein Abwürgen des Triebwerkskompressors zu verhindern. Der Einlass muss so wenig Widerstand wie möglich erzeugen. Die kleinste Lücke in der Luftstromversorgung kann zu großen Motorproblemen sowie zu erheblichen Effizienzverlusten führen. Damit der Einlasskanal ausreichend Luft bei minimalen Turbulenzen liefern kann, muss er sauber und fehlerfrei sein.
Der neuartige Herstellungsansatz für den S-förmigen Einlasskanal ersetzt das Handlaminieren von Prepreg auf einem mehrteiligen Stahldorn, gefolgt von einer Autoklavenhärtung durch einen automatisierten Umflechtungsprozess, der stattdessen trockene Fasern aufträgt. Der sehr schwere mehrteilige Stahldorn wird durch einen leichten einteiligen Formgedächtnispolymer (SMP) Dorn ersetzt. Die trocken geflochtene Kohlefaser wird mit VARTM mit einem kostengünstigen Epoxidharz und Ofenhärtung zu einer Verbundstruktur verarbeitet.
Das Team schloss die Analyse der Überflechtarchitektur sowie die Herstellung eines SMP-Formwerkzeugs und des SMP-Dorns ab, der als Werkzeug während des Vorform-Überflechtprozesses dient. Aufgrund der komplexen Geometrie des S-förmigen Einlasskanals waren mehrere Iterationen erforderlich, um die Einstellungen der Übergeflechtmaschine zu optimieren und die Faltenbildung des Verbundmaterials zu minimieren. Es werden insgesamt vier Einlasskanäle hergestellt und die Kosten für Altteile und die Produktionszeit werden mit dem neuen Design verglichen.
„Wir glauben, dass die Einführung eines wiederverwendbaren Formgedächtnis-Polymerdorns zusammen mit dem automatisierten Überflechtprozess und einer ofenbasierten VARTM-Verbundhärtung zu erheblichen Kosten- und Zykluszeiteinsparungen führen wird“, sagt Craig Neslen, Fertigungsleiter für das Low Cost Attritable Aircraft Technologieinitiative in der Division Manufacturing and Industrial Technologies bei AFRL. „Die Quantifizierung der Fertigungsvorteile und die Validierung der strukturellen Integrität werden entscheidend sein, um einen positiven Business Case zu erstellen und Konstrukteure und Hersteller davon zu überzeugen, dass die neuen Materialien und Prozesse in zukünftige kostengünstige Motoreinlasskanalkonstruktionen integriert werden sollten.“
Der letzte Einlasskanal wird an die U.S. Air Force zur weiteren Integration in das komplementäre Flugzeugkonstruktions- und Fertigungsprogramm innerhalb des Aerospace Systems Directorate von AFRL geliefert. Die Division Aerospace Vehicles wird statische Bodentests des integrierten geflochtenen Rumpfs und der Einlasskanalstruktur durchführen.
„Obwohl wir noch alle Auswirkungen der Abriebtoleranz auf die Konstruktionskriterien und die daraus resultierenden verwendeten Herstellungsmaterialien und -prozesse definieren müssen, haben wir eine Basis mit Schwellenwerten für Festigkeit und Steifigkeit, die wir durch groß angelegte Flugzeugbodentests bewerten werden. “, sagte Ray Fisher, Luft- und Raumfahrtingenieur in der Division Aerospace Vehicles.
AFRL ist das wichtigste wissenschaftliche Forschungs- und Entwicklungszentrum der US Air Force. Es spielt eine wesentliche Rolle bei der Entdeckung, Entwicklung und Integration erschwinglicher Kriegskampftechnologien für unsere Luft-, Weltraum- und Cyberspace-Streitkräfte. Mit mehr als 11.000 Mitarbeitern in neun Technologiebereichen und 40 weiteren Betrieben auf der ganzen Welt bietet AFRL ein vielfältiges Portfolio an Wissenschaft und Technologie, das von Grundlagenforschung bis hin zu fortschrittlicher Forschung und Technologieentwicklung reicht. Weitere Informationen finden Sie unter:www.afresearchlab.com.
Harz
- Elektronik der Zukunft:schnelle Entwicklungsplattform für Wärmebild- und IR-Sensorik
- CNC-Werkzeuggrundlagen für besseres Schneiden und Schnitzen von Holz
- Materialien:Glas- und kohlenstofffaserverstärktes PP für die Automobilindustrie
- Antifog-PC-Folie für Visiere, Linsen und Brillen
- Hochviskoses PEEK für Spritzguss und Extrusion
- High-Flow-POM für die Medizin- und Gesundheitsbranche
- Trelleborg gibt neuen Distributor für Werkzeugmaterialien an
- Wo sich Kunst und Wissenschaft des Flechtens treffen
- Design für den Edge- und IoT-Erfolg
- Herstellung und Werkzeugbau von Metallteilen für Kraftstoffeinspritzsysteme