Werksbesichtigung:STELIA Aerospace, Méaulte, Frankreich
Mit 7.000 Mitarbeitern weltweit und einem Umsatz von 2,2 Milliarden Euro im Jahr 2018 gibt STELIA Aerospace (Toulouse, Frankreich) klar seine Position in den Bereichen Primärprodukte und Industrie an:Nr. 1 in Europa/Nr. 3 der Welt für Flugzeugstrukturen, Nr. 1 weltweit für Piloten- und Besatzungssitze und Nr. 3 weltweit für Passagiersitze der First und Business Class.
Die Verwendung von Verbundwerkstoffen durch STELIA Aerospace erstreckt sich auf die vorderen Rumpfsektionen des Airbus A350, Flügel für ATR-Turboprop-Flugzeuge, verschiedene Hubschrauberstrukturen und in einigen Sitzprodukten, einschließlich des neuesten OPAL-Sitzes. Zu den Composites-Produktionsstätten gehören die französischen Standorte Méaulte (große Rumpfsektionen) und Salaunes (kleinere Verbundteile), Detailteile und Montage in Marokko und Tunesien sowie ein breites Sortiment an Verbundteilen für Flugzeuge, Verteidigung und Raumfahrt am bisherigen Standort von Composites Atlantic in Lunenburg, Neuschottland, Kanada.
STELIA Aerospace entstand aus dem Zusammenschluss zweier früherer Airbus-Tochtergesellschaften im Jahr 2015 – Aerolia und Sogerma. Der Standort Méaulte – 1,5 Autostunden nördlich von Paris – umfasst 49 Hektar mit 150.000 Quadratmetern Produktionsfläche, 1.500 Mitarbeitern und 500 Subunternehmern und ist ein wichtiger Bestandteil der Airbus-Lieferkette. Der Standort in einer Kleinstadt täuscht über ein Produktionskraftwerk hinweg:„2018 lieferte er 860 Rumpfnasesektionen für die A320, A330, A350, A380 und A400M“, sagt Francois Fournier, Kommunikationsmanager von STELIA Méaulte. Er ist mein Führer durch die „Fabrik der Zukunft“ der A350-Nasenrumpfproduktion des Standorts und die STELIALAB-R&T-Anlage, begleitet von Olivier Canal, STELIA Aerospace Méaulte, Leiter der R&T-Fertigung, Montage &Automatisierung, Verbundwerkstoffe &digitale Fabrik, und Simon Maire-Vigeur , Leiter der F&T-Verbundwerkstoffherstellung, STELIALAB.
„Fabrik der Zukunft“
In einer einführenden Präsentation in der Firmenzentrale erklärt Fournier, dass STELIA Aerospace in Zukunftstechnologien wie digitale Fertigung und Automatisierung inklusive Augmented Reality/Virtual Reality zur Effizienzsteigerung in der Produktion und Roboter/Cobots für eine effizientere Montage investiert hat.
„Die Zukunft sind Verbundwerkstoffe und metallischen Strukturen“, bemerkt Canal. „Wir versuchen, zukünftige Lösungen zu definieren, um unsere Mitarbeiter nicht zu ersetzen, sondern sie effizienter zu machen.“
Dieses Streben nach Effizienz wird vielleicht am besten durch die Initiative „Factory of the Future“ veranschaulicht, die vor fünf Jahren ins Leben gerufen wurde, um die Rampen in der A320- und A350-Produktion zu treffen. „Wir haben für diesen Standort eine neue Industriestrategie entwickelt“, erinnert sich Canal, der als Projektmanager für die Initiative verantwortlich war. „Wir wollten variable Produktionsraten erfüllen können und haben flexible Werkzeuge entwickelt, die wir von einem Programm zum anderen wiederverwenden können.“
Ein weiteres Ergebnis dieses Umdenkens war, Gebäude bestimmten Programmen zu widmen. „Jede würde eine Linie und ein Team haben“, sagt Canal, „und mit einem schlanken Fertigungsansatz entworfen werden, der sich darauf konzentriert, Verschwendung bei Arbeit, Bewegung, Materialien und Prozessen zu vermeiden.“ STELIA Aerospace hat auch die A320-Linie neu gestaltet und die Produktivität um 10 bis 20 Prozent gesteigert, „was tatsächlich eine erhebliche Verbesserung darstellt“, sagt Canal. „Wir haben dies in 2,5 Jahren erreicht, indem wir mehr als 50 Prozent des Fußabdrucks der Fertigung an diesem Standort verändert haben und gleichzeitig die Produktion aufrechterhalten und 100 Prozent termingerechte Lieferung ohne Qualitätsverlust.“ Dieser Erfolg wird der Unterstützung durch das hochrangige Management zugeschrieben, „aber wir haben auch hart dafür gearbeitet, dass die Arbeiter Eigentümer sind“, bemerkt er.
Canal erklärt, dass das Design des 30.000 Quadratmeter großen A350-Produktionsgebäudes von der Strömung diktiert wurde, beispielsweise in seiner U-Form, bei der Rohmaterialien an einem Ende eintraten und fertige Rumpfsektionen am anderen austraten. „Alles für die Produktion unserer A350-Strukturen befindet sich in diesem Gebäude, vom Layup bis zur Endmontage. Dies ist beispielsweise wichtig, damit Qualitätsprobleme schnell und einfach identifiziert und behoben werden können“, sagt er.
Für die A350 produziert STELIA Aerospace die Rumpfnase 11, die komplett aus Metall besteht, um Schäden durch Vogelschlag besser zu widerstehen, sowie die komplexe Metall/Verbund-Hybridbaugruppe für die Sektion 12 und die untere Einheit der Sektion 11/12, die die Nase enthält Fahrwerkschacht. Fournier zeigt das Video „Factory of the Future“ von STELIA Aerospace und zeigt die gepulste Linie, wie sie in der Automobilmontage verwendet wird. „Wir haben eine Demolinie eingerichtet, damit die Arbeiter diese bewegliche Linie schulen und entmystifizieren können, die zu einer bestimmten Taktzeit arbeitet, um die Produktion mit voller Leistung zu erreichen“, sagt Canal.
Ein weiterer Aspekt war die digitale Technologie. „Digitale Lösungen ermöglichten es uns, alle technischen Schemata und Schritte auf einem Tablet zu speichern und den Zugriff auf das neueste 3D-Modell für jeden Abschnitt sicherzustellen“, sagt Canal. Die Mitarbeiter werden so über wichtige Details und Änderungen informiert, während die Manager leicht über potenzielle Probleme informiert werden. „Wir haben auch Augmented Reality entwickelt, um die Montage zu erleichtern, zum Beispiel die Projektion auf die Rumpfschalen, die zeigt, welche Teile und wo die Befestigungen vorgenommen werden“, sagt Canal. Er fügt hinzu, dass Inspektion Cobots werden verwendet, um 3D-Scans von fertigen Abschnitten zu vervollständigen, die dann mit dem digitalen Modell verglichen werden, um Fremdkörper oder fehlende Teile, Qualitätsprobleme usw. zu identifizieren.
Unsere Tour begann im Reinraum des A350-Produktionsgebäudes, wo Coriolis (Quéven, Frankreich) Maschinen zur automatischen Faserplatzierung (AFP) große kohlenstofffaserverstärkte Polymer (CFK)-Rumpfschalen für das Unterteil der Sektion 11/12 und die Krone verlegen und zwei Seitenschalen für Abschnitt 12. Diese Schalen werden dann mit vorgefertigten Stringern verbunden, vakuumverpackt und in einem Autoklaven ausgehärtet. Nach dem Aushärten werden sie zugeschnitten und auf Handhabungswerkzeuge geladen, die einen einfachen Transport durch alle Schritte der Montage ermöglichen, einschließlich des Roboterbohrens und der Befestigung von Befestigungselementen. Jedes Paneel wird mittels automatisierter zerstörungsfreier Prüfung (NDT) geprüft. Fertige Baugruppen werden an die Airbus-Rumpfmontagelinie in Saint Nazaire, Frankreich, geliefert.
STELIALAB
Der nächste Halt ist das 2.000 Quadratmeter große STELIALAB R&T Center, das sich in der linken Hälfte des IndustriLAB befindet, einer regionalen Technologie- und Schulungseinrichtung, die sich südlich des STELIA-Komplexes befindet. Die Aktivitäten von STELIALAB sind auf Verbundwerkstoffe, Montage und digitale Technologien ausgerichtet.
Die Tour beginnt hier wieder im salle blanche (Reinraum), ein ziemlich großer, offener Raum mit Verpackungsmaterial und Layup-Tools. Simon Maire-Vigueur erklärt, dass die Mission der Gruppe darin besteht, die Zukunft für eine kostengünstige Massenproduktion für meist große und komplexe Teile zu identifizieren. Die Industrialisierung duroplastischer Verbundwerkstoffe umfasst Hochgeschwindigkeits-AFP- und Flüssigharzinfusions-(LRI)-Prozesse, einschließlich Resin Transfer Moulding (RTM) für große, geschlossene Kastenstrukturen wie Flügelkomponenten, Höhenleitwerke und Seitenleitwerke.
Wir verlassen den Reinraum und betreten den AFP-Raum, der von einer Coriolis-Maschine belegt wird, die bis zu 4 Meter lange Teile verlegen kann. Maire-Vigueur widmet sich der Forschung und Entwicklung und stellt fest, dass es an mehr als 200 Tagen pro Jahr belegt ist. STELIALAB hat ein Verfahren zur Integration von AFP-erzeugten Trockensteifen und Häuten entwickelt, die aus dem Autoklaven (OOA) mit einem Ofen oder selbstbeheizten Werkzeugen ausgehärtet werden. „Wir bevorzugen LRI mit geringerem Injektionsdruck, weil wir günstigere Werkzeuge verwenden können“, sagt Maire-Vigueur.
TPC-Roadmap
Diese AFP-Maschine wurde auch verwendet, um im Rahmen des ARCHES TP-Entwicklungsprogramms die Haut für den Helikopterrumpf/Heckausleger-Demonstrator aus vollthermoplastischem Verbundwerkstoff (TPC) zu verlegen. Es wurde auf der Paris Air Show 2017 und 2018 und 2019 auch auf der JEC World gezeigt und wurde aus 8 Kabeln 0,25 Zoll breitem Kohlefaser-/Polyetherketonketon (PEKK) -Band mit Laserheizung hergestellt. „Wir haben den Blitzeinschlagschutz beim Layup in das AFP integriert“, sagt Maire-Vigueur. „Die Haut wurde mit Kapton-Absackfolie OOA-gehärtet, was eigentlich nicht sehr praktisch ist.“ Omega-förmige Stringer wurden aus gekauften unidirektionalen Flachbandplatten hergestellt, die von Aviacomp (Toulouse, Frankreich) stanzgeformt wurden. Das gleiche Verfahren wurde für Rahmen verwendet, jedoch mit Platten aus gewebtem Material, das von Porcher (Badinières, Frankreich) geliefert und in Cetim (Nantes, Frankreich) gestempelt wurde. Obwohl die Spanten standardmäßig mechanisch befestigt wurden, wurden die Stringer durch automatisiertes, dynamisches Induktionsschweißen befestigt. „Dies ermöglicht niedrigere Kosten und neue Gestaltungsmöglichkeiten“, bemerkt Maire-Vigueur. „Wir haben auch das Umspritzen von Befestigungspunkten demonstriert, beispielsweise für elektrische Kabelbäume.“
Nach den Herausforderungen des Programms gefragt, nennt Maire-Vigueur die Layups, das Schweißen und den 15-Monats-Zeitplan. „Selbst die Prägung ohne zu großen Verzug im gewebten Material zu erreichen, war nicht einfach“, fügt er hinzu. Obwohl das Design des Heckauslegers vom Konstruktionsbüro von STELIA Aerospace in Toulouse fertiggestellt wurde, wurde die gesamte Produktion von STELIALAB überwacht. ARCHES TP war jedoch nur ein Schritt in der Roadmap von STELIA Aerospace für thermoplastische Verbundwerkstoffe. Das Unternehmen entwickelt weiterhin TPC-Technologien, um in den folgenden Jahren die Machbarkeit eines vollständigen TPC-Rumpfes zu demonstrieren.
Zukünftige Flugzeugstrukturen neu denken
Beim Verlassen des AFP-Raums führt der Rundgang durch eine sehr große, offene Halle, die zum Schutz des geistigen Eigentums durch temporäre Wände in sichere „Entwicklungszellen“ unterteilt ist. Durch die Halle gehen und nach links abbiegen, erreichen wir einen Bereich mit einem kleinen Scholz (Coesfeld, Deutschland) Autoklaven für 450°C und einer Injektionsmaschine für die Harzinfusion. „Da unsere Roadmap darin besteht, OOA zu härten, verwenden wir den Autoklav tatsächlich wie einen Ofen, um thermoplastische Verbundwerkstoffe ohne Druck zu härten“, erklärt Maire-Vigueur. Es gibt einen mit Vorhängen versehenen Trimmraum und einen Bereich daneben mit ZfP-Geräten, einschließlich eines kleinen C-Scan-Systems.
Wir drehen wieder um und betreten ein großes Testlabor. „Wir können polierte Querschnitte für die Qualitätskontrolle sowie Material- und Prozessuntersuchungen untersuchen“, sagt Maire-Vigueur. Das Labor verfügt außerdem über einen Arm von Romer (Hexagon Manufacturing Intelligence, Shropshire, Großbritannien) für die Koordinatenmessung und Geräte für Faservolumenverhältnis, Härte und chemische Tests. „Alle Ingenieure in unserem R&T-Team sind in der Lage, ihre eigenen Materialien und Prozesskontrollen durchzuführen“, bemerkt Maire-Vigueur. „Wir schulen sie, damit sie vom Design über die Fertigung bis hin zur Inspektion und Prüfung der fertigen Teile arbeiten können. Dies ist wichtig, um den gesamten Prozess zu verstehen und eine schnelle Einschätzung vermuteter Probleme und deren Ursachen zu ermöglichen. Design ist nicht von Herstellung und Qualitätsprüfung getrennt.“
Die letzte Station ist ein großes Automatisierungslabor in einem der ummauerten Bereiche. Ein kurzer Blick ins Innere zeigt die Erforschung neuer Baugruppen mit Robotern und Cobots. „Wir prüfen die Weiterentwicklung kleinerer, funktionalerer Werkzeuge und versuchen uns vorzustellen, wie man Teile schneller und kostengünstiger zusammenbauen könnte“, sagt Canal. „Unsere Kultur besteht darin, Grenzen zu überschreiten und neue Wege zu gehen. Wir waren führend bei der Implementierung von Robotik und sind jetzt führend bei der Förderung der Verbundwerkstofftechnologie. Wir haben unsere Fähigkeit bewiesen, die Zukunft zu überdenken und neu zu gestalten, und wir werden nie aufhören.“
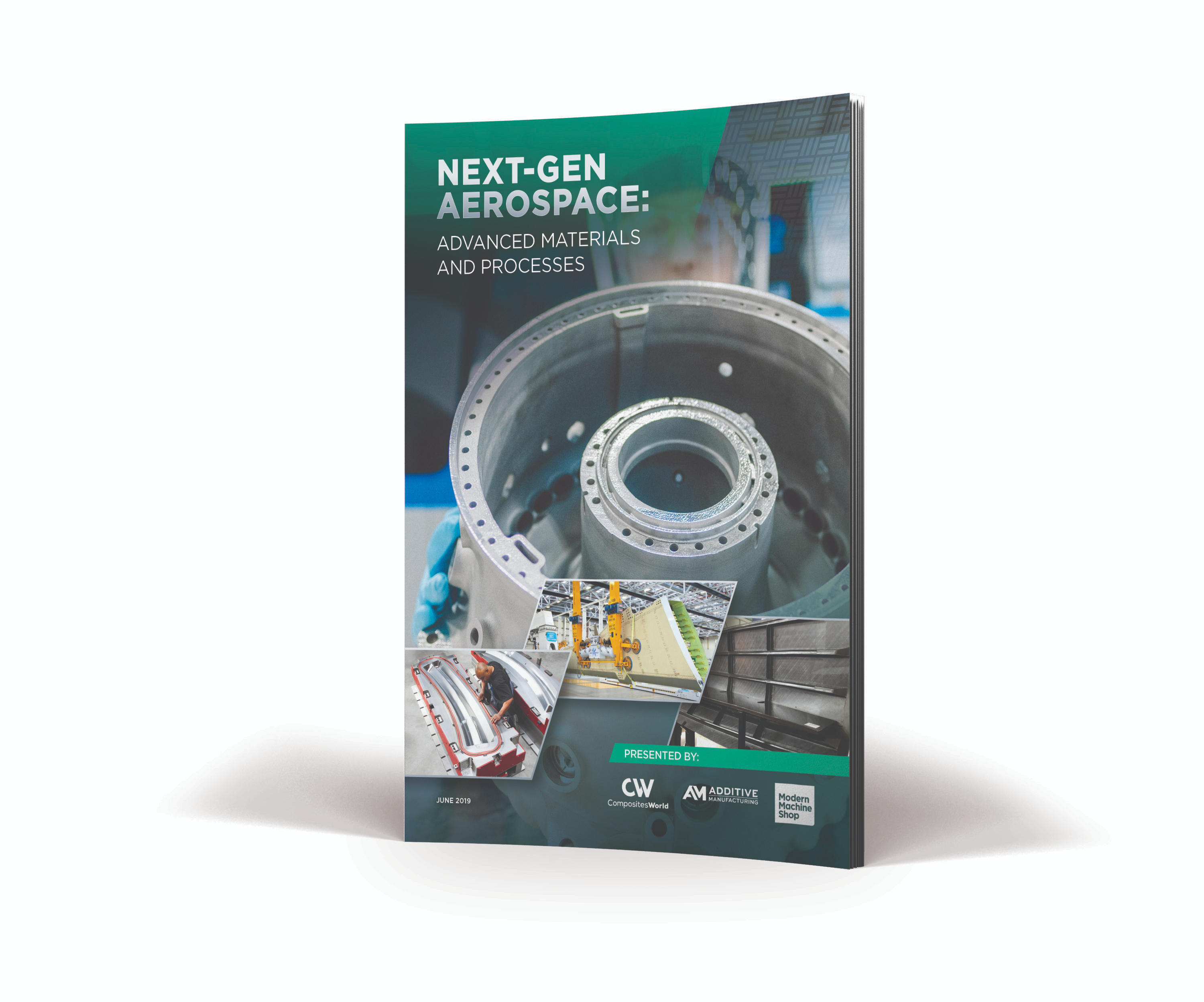
Die nächste Generation der Luft- und Raumfahrtfertigung
Da sich die kommerzielle Luftfahrtindustrie in den nächsten 20 Jahren voraussichtlich verdoppeln wird, erfordert die Deckung der Nachfrage nach Passagier- und Frachtflugzeugen neue Technologien und beispiellose Fertigungsraten.
Erfahren Sie mehr über die Materialien und Prozesse, die Flugzeuge der nächsten Generation prägen werden, in einer Sammlung von Geschichten von CompositesWorld, Modern Machine Shop und Additive Fertigung , verfügbar zum kostenlosen Lesen oder Herunterladen . Holen Sie es hier.
Harz
- Vespel®:Das Luft- und Raumfahrtmaterial
- Polyplastics erweitert die COC-Produktion von Topas
- Radici erweitert die globale Produktionskapazität erheblich
- Polykemi investiert in eine eigene US-amerikanische Compoundieranlage
- Rethink Robotics erhält neue Zentrale und Produktionsstätte
- Toyota wählt Standort für EV-Batterieproduktionsanlage in North Carolina aus
- Hersteller besuchen Southco für Werksbesichtigung, kontinuierliche Verbesserung Best Practice-Diskussion
- Arkema Inc. baut US-PEKK-Produktionsanlage
- Hexion führt Zweikomponenten-Epoxidlösung für die Herstellung von Verbundwerkstoffen in der Luft- und Raumfahrt ein
- Kaneka Aerospace erhält die AS9100D-Luft- und Raumfahrtzertifizierung