Eine Einführung in die additive Fertigung mit Drahtlichtbogen [Update 2020]
Wire Arc Additive Manufacturing (WAAM) ist eine der weniger bekannten 3D-Metalldrucktechnologien, die jedoch ein enormes Potenzial für groß angelegte 3D-Druckanwendungen in mehreren Branchen birgt.
Dieser Leitfaden konzentriert sich auf die Funktionsweise von WAAM, seine Vorteile und Einschränkungen sowie auf wichtige WAAM-Unternehmen und erfolgreiche Anwendungen.
Wie funktioniert die additive Fertigung mit Drahtlichtbogen?
WAAM ist eine Variante einer Direct Energy Deposition-Technologie und verwendet ein Lichtbogenschweißverfahren zum 3D-Drucken von Metallteilen.
Im Gegensatz zu den üblicheren Metallpulver-AM-Verfahren schmilzt WAAM Metalldraht unter Verwendung eines Lichtbogens als Wärmequelle.
Der Prozess wird durch einen Roboterarm und die Die Form wird auf einem Substratmaterial (einer Grundplatte) aufgebaut, aus dem das Teil nach der Fertigstellung geschnitten werden kann.
Der geschmolzene Draht wird in Form von Perlen auf das Substrat extrudiert. Wenn die Perlen zusammenkleben, bilden sie eine Schicht aus Metallmaterial. Der Vorgang wird dann Schicht für Schicht wiederholt, bis das Metallteil fertig ist.
Hier sehen Sie den Vorgang in Aktion:
Materialien
WAAM kann mit einer Vielzahl von Metallen arbeiten, sofern diese in Drahtform vorliegen. Diese Liste umfasst Edelstahl, Nickelbasislegierungen, Titanlegierungen und Aluminiumlegierungen. Jedes schweißbare Metall kann auch mit WAAM verwendet werden.
Die Vorteile der additiven Fertigung mit Drahtlichtbogen
Die Möglichkeit, große Metallteile in 3D zu drucken
WAAM eignet sich besonders für die Herstellung von großformatigen Metallteilen. Dies steht im Gegensatz zu Powder Bed Fusion (PBF) Metal AM-Technologien, die typischerweise kleinere, hochauflösende Komponenten produzieren.
Im Gegensatz zu PBF AM-Maschinen, die einen begrenzten Bauraum haben, hat der Roboterarm einer WAAM-Maschine mehr Bewegungsfreiheit, d.h. die Größe eines Bauteils ist nicht durch den Platz begrenzt, sondern nur durch die Entfernung, die der Roboterarm erreichen kann. Dies ermöglicht die Herstellung größerer Teile, die mit PBF-Prozessen nicht möglich wären.
Günstigere Verfahren und Materialien
In Bezug auf die Materialkosten ist der beim WAAM-Druckprozess verwendete Schweißdraht deutlich günstiger als das beim Metall-PBF verwendete Metallpulver.
Dies liegt daran, dass die WAAM-Technologie auf dem bewährten Schweißen basiert Fertigungstechnik an sich. WAAM-Hardware umfasst normalerweise Schweißgeräte von der Stange, die weniger teuer sind als viele auf dem Markt erhältliche Metall-3D-Drucker.
Darüber hinaus ist Draht in der Regel einfacher zu handhaben als Pulver, was eine spezielle Schutzausrüstung erfordert benutzen.
Hochwertige Teile
Mit WAAM hergestellte Teile zeichnen sich besonders durch ihre hohe Dichte und starke mechanische Eigenschaften aus, die mit Teilen vergleichbar sind, die mit traditionellen Fertigungsmethoden hergestellt werden.
Da es sich bei dem Drahtvormaterial um ein 100 % dichtes Ausgangsmaterial handelt, wird durch den Herstellungsprozess eine vernachlässigbare Porosität verursacht, was zu einem sehr dichten Endteil führt.
Es ist für Reparaturarbeiten geeignet
WAAM ist auch eine gute Option für Reparatur- und Wartungsarbeiten an bestimmten Komponenten wie Turbinenschaufeln sowie Formen und Werkzeugen.
Verschlissene Teile oder beschädigte Teile können mit WAAM durch Einlagerung von neuem Material repariert werden auf seiner Oberfläche. Dies kann zu erheblichen Kosteneinsparungen führen, da die Notwendigkeit entfällt, ein neues Teil von Grund auf neu zu produzieren.
Die Einschränkungen von WAAM
Eigenspannungen und Verzerrungen
Eine Herausforderung im Zusammenhang mit WAAM ist das Wärmemanagement.
Der Druckprozess ist mit hohen Temperaturen verbunden, wodurch sich Eigenspannungen aufbauen – ein Problem, das häufig beim 3D-Metalldruck auftritt. Da Eigenspannungen oft zu Verformungen in einem Bauteil führen können, muss die Kühlung mit einkalkuliert werden.
Einige Materialien erfordern eine Abschirmung
Bei der Verwendung bestimmter Materialien wie Titan ist eine Abschirmung erforderlich, um eine inerte Atmosphäre zu schaffen, um die richtigen Baubedingungen zu gewährleisten.
Das bedeutet, dass der Prozess in einer Inertgaskammer stattfinden muss. Die Inertgaskammer begrenzt jedoch die Größe der Teile, die mit dieser Technologie hergestellt werden können, und die Installation einer solchen Kammer erhöht die Kosten der Ausrüstung.
Niedrige Auflösung
WAAM produziert in der Regel endkonturnahe Teile mit schlechter Oberflächengüte. Die Oberfläche eines Teils muss daher durch spanende Bearbeitung nachbearbeitet werden.
Wichtige WAAM-Player und Technologieanwendungen
WAAM3D
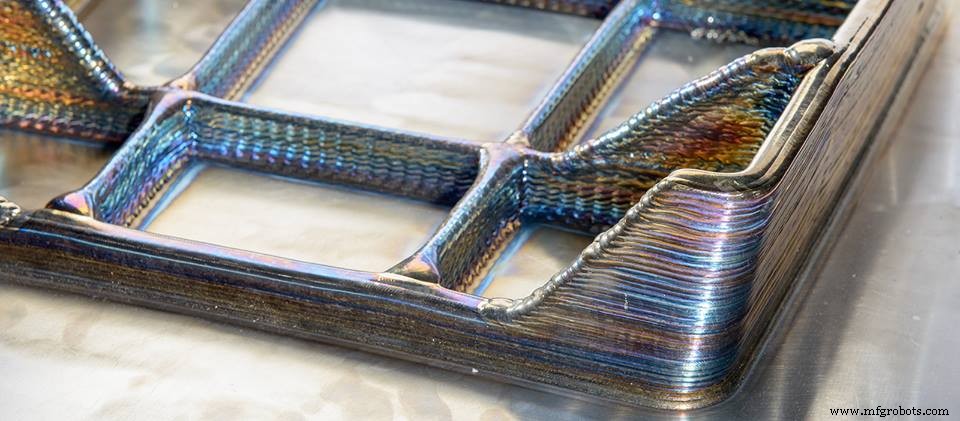
Ab 2020 bleibt der WAAM-Markt klein und eine Handvoll Unternehmen entwickeln diese Metall-3D-Drucktechnologie aktiv weiter.
WAAM3D ist vielleicht einer der weniger bekannten Namen auf diesem Gebiet, aber das Unternehmen hat umfangreiche Forschungen betrieben, bevor es seine Technologie auf den Markt brachte.
WAAM3D wurde in . gegründet 2018 zur Kommerzialisierung des geistigen Eigentums der Cranfield University im Bereich WAAM.
Nach Angaben des Unternehmens hat der Mangel an Lieferketten – nämlich Softwaretools, von WAAM entwickelte Hardware, Rohstoffe, Schulungen und Dienstleistungen – die verdiente industrielle Einführung von WAAM-Prozessen trotz der nachgewiesenen geschäftlichen Vorteile behindert .
Das Unternehmen zielt darauf ab, eine solche Lieferkette zu schaffen und den Einsatz von WAAM in der Luft- und Raumfahrt- und Verteidigungs-, Öl- und Gas-, Energie- und Nuklearindustrie zu fördern.
Bislang hat WAAM3D mehrere erfolgreiche Anwendungen seiner Technologie veröffentlicht.
Einer ist ein Heckrahmen für den Eurofighter Typhoon von BAE Systems. Das Titanteil, das in der ebenen Fläche 2,5 mx 1,5 m misst, trägt die zwei Eurojet EJ200-Triebwerke, die 60 kN (13.500 lbf) Trockenschub erzeugen können.
Ein weiteres Titanteil, ein 1 m langer Druck Schiff, wurde für Thales Alenia Space hergestellt. Durch den Einsatz von WAAM zur Herstellung dieser Komponente sparte das Team mehr als 200 kg Material pro Artikel ein und konnte zwei Teile des Behälters zu einem zusammenfassen.
Außerdem dauerte die Produktion des Teils angeblich mehrere Tage – eine deutliche Verkürzung der Vorlaufzeit, da die Herstellung des Teils in der Regel mehrere Monate dauert.
Anfang dieses Jahres hat WAAM3D seine erste Finanzierungsrunde der Serie A abgeschlossen, die das Unternehmen weiter voranbringen soll Kommerzialisierung der WAAM-Technologie.
AML3D
Die Cranfield University inspirierte die Gründung eines anderen Unternehmens:AML3D. Andrew Sales, Managing Director von AML3D, studierte in Cranfield und gründete, fasziniert vom Potenzial der Technologie, 2014 ein WAAM-Servicebüro in Australien.
2019 erhielt das Unternehmen die Zertifizierung durch die globale Akkreditierungsstelle der Schifffahrtsindustrie Lloyds Register. Mit der Zertifizierung lieferte AML3D sein erstes Teil an einen Schifffahrtskunden:einen Satz Verschleißringe aus martensitischem Edelstahl.
Die Teile werden traditionell geschmiedet und erfordern einen zusätzlichen Wärmebehandlungs-Nachbearbeitungsschritt. Dieser Prozess erhöht die Gesamtdurchlaufzeit auf sechs bis acht Wochen. Solche Artikel mit langer Vorlaufzeit müssen in einem physischen Bestand gehalten oder vorzeitig ersetzt werden.
Durch den Einsatz von WAAM konnte AML3D die Ringe zu den gleichen Kosten herstellen und die Vorlaufzeit auf nur wenige Tage reduzieren. Dies ist eine entscheidende Verbesserung für Schiffe, die für eine begrenzte Zeit im Dock bleiben.
Um seine Kapazitäten weiter auszubauen, plant das Unternehmen nun, in naher Zukunft eine Produktionsstätte in Singapur zu eröffnen. Dies wird durch die Nachfrage des Marine-Hubs Singapur getrieben, da der Standort ein strategischer Knotenpunkt für kommerzielle Schifffahrtsrouten ist.
Ramlab
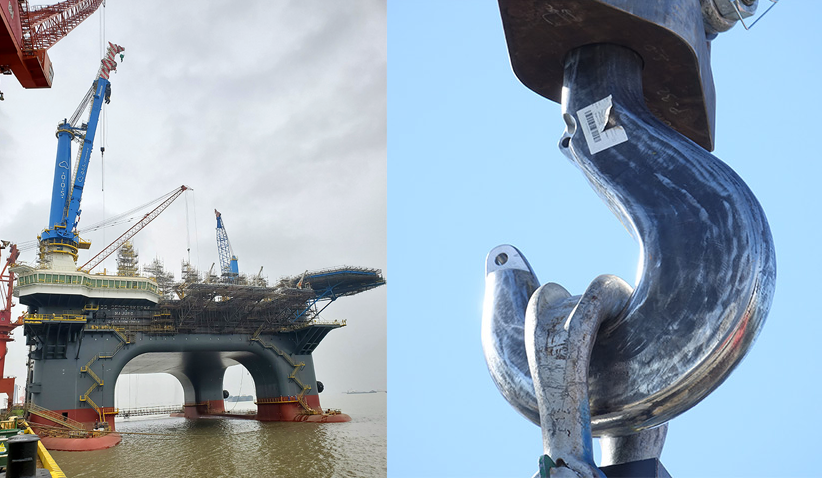
In ähnlicher Weise nutzt das Additive Manufacturing Fieldlab (RAMLAB) des Rotterdamer Hafens WAAM, um die Produktion von Schiffsteilen zu beschleunigen. Das Unternehmen sorgte 2017 mit dem 3D-Druck eines Prototyps des weltweit ersten zugelassenen Schiffspropellers für Furore.
Der „WAAMpeller“ besteht aus 298 Lagen Nickel-Aluminium-Bronze-Legierung und wiegt 400 kg. Das Teil wurde in sieben Monaten fertiggestellt und demonstriert das Potenzial von WAAM zur Optimierung der Produktion zukünftiger Schiffskomponenten.
Im Jahr 2018 startete Ramlab in Zusammenarbeit mit Huisman Equipment ein weiteres Projekt zum 3D-Druck eines großen Offshore Kranhaken mit einem Gewicht von fast 1000 kg. Huisman Equipment hat dieses Projekt noch weiter vorangetrieben und einen 36.000 kg schweren WAAM-Haken in 3D gedruckt, zertifiziert und installiert, der speziell für den Einsatz bei Offshore-Hebearbeiten entwickelt wurde.
MX3D
Eine der ersten Anwendungen, die die WAAM-Technologie der Welt zugänglich machte, war eine 3D-gedruckte Stahlbrücke, die vom niederländischen Start-up MX3D entwickelt wurde.
Das Brückenprojekt, das 2018 begann, dauerte mehr als ein Jahr, diente jedoch als Demonstration des Potenzials des großflächigen 3D-Metalldrucks.
Kürzlich hat das MX3D-Team seine Technologie verwendet, um einen Fahrradrahmen aus Aluminium in 3D zu drucken. Der futuristisch anmutende Rahmen wurde mit Hilfe einer generativen Designsoftware entworfen und in zwei Teilen in weniger als 24 Stunden in 3D gedruckt, was die hohe Druckgeschwindigkeit der WAAM-Technologie von MX3D demonstriert. MX3D hat auch ein „smartes Fixture-Setup“ entwickelt, mit dem angeblich jeder maßgeschneiderte WAAM-Rahmen problemlos für das Fahren vorbereitet werden kann.
Gefertec
Ein weiterer Akteur in der WAAM-Arena ist das deutsche Unternehmen Gefertec. 2017 stellte es seine 3DMP®-Fertigungstechnologie vor, die Teil der GTarc AM-Maschinenserie von Gefertec ist.
Die größte Anlage verfügt über ein 3-Achs-System zur Herstellung von Teilen bis 3 m3 mit einem Maximum Masse von 3000kg.
Das Interessante an den Maschinen von Gefertec ist, dass sie in ein Frässystem integriert werden können. Dadurch besteht die Möglichkeit, ein Hybridsystem zu erstellen, bei dem mit 3DMP®-Technologie ein Teil erstellt wird, das dann sofort mit der Bearbeitung fertig gestellt wird.
Ein Beispiel für den Einsatz der Gefertec-Technologie ist der 3D-Druck eines Metallradsatzlagerdeckels für eine Lokomotive. Dieses Modell der Lokomotive wurde in den 1960er und 1970er Jahren in Dienst gestellt, so dass die Beschaffung von Ersatzteilen, die oft nicht mehr erhältlich sind, schwierig sein kann.
Daher würde die Lieferung des Bauteils traditionell bis zu neun Monate dauern und in dieser Zeit wäre die Lokomotive außer Betrieb, was zu hohen Kosten führte.
Gefertec's Für die Herstellung dieses Ersatzteils wurde ein 3D-Drucker verwendet, und das Projekt, vom ersten Entwurf über das Reverse Engineering bis zur Produktion, wurde innerhalb von zwei Monaten abgeschlossen. Während dies die erste Produktion eines Werkstücks war, ist es mit einem etablierten Prozess möglich, die Durchlaufzeit noch weiter zu senken, möglicherweise auf nur wenige Wochen.
WAAM – die praktikable Option für die großtechnische additive Metallfertigung
Bei relativ neuen Technologien wie WAAM braucht es Zeit, bis sich Anwendungen entwickeln und die Vorteile in der gesamten Branche spürbar werden. Wir sehen jedoch, dass die Nachfrage nach großen 3D-gedruckten Metallkomponenten wächst, was darauf hindeutet, dass sich die Einführung von WAAM beschleunigen wird.
Letztendlich ist klar, dass WAAM die Herstellung großer Metallteile revolutioniert und Unternehmen die Möglichkeit einer schnelleren und kostengünstigeren Produktionsmethode bietet.
3d Drucken
- Additive Fertigung vs. subtraktive Fertigung
- Vorteile der additiven Fertigung
- Eine Umfrage zu Arbeitsabläufen in der additiven Fertigung
- Experteninterview:MELD Manufacturing CEO Nanci Hardwick über die Ausschöpfung des Potenzials der additiven Metallfertigung
- Metalladditive Fertigung:5 Fragen an einen potenziellen Metallpulverlieferanten
- Additive Manufacturing Podcast Folge 3
- Additive Manufacturing Podcast Episode 1
- Additive Fertigung in Verbraucheranwendungen
- Additive Fertigung in der Elektronik
- Additive Fertigung in der Luft- und Raumfahrt