Anwendungs-Spotlight:3D-gedruckte Raketen und die Zukunft der Raumfahrzeugfertigung
Der 3D-Druck entwickelt sich schnell zu einer aufregenden Technologie für die Herstellung von Raumfahrzeugen und insbesondere für Raketen. Sowohl Start-ups als auch etablierte Hersteller setzen auf den 3D-Druck, um Raketenkomponenten mit verbessertem Design und Leistung zu geringeren Kosten und schnelleren Durchlaufzeiten herzustellen.
Diese Woche setzen wir unsere Application Spotlight-Reihe fort, indem wir uns die Vorteile des 3D-Drucks für Raketenteile und sogar ganze Raketen ansehen.
Schauen Sie sich die anderen Anwendungen an, die in dieser Serie behandelt werden:
3D-Druck für Wärmetauscher
3D-Druck für Lager
3D-Druck für die Fahrradherstellung
3D-Druck für die digitale Zahnheilkunde und die Herstellung von Clear Alignern
3D-Druck für medizinische Implantate
3D-Druck für die Schuhherstellung
3D-Druck für elektronische Komponenten
3D-Druck in der Bahnindustrie
3D-gedruckte Brillen
3D-Druck für die Endfertigung
3D-Druck für Halterungen
3D-Druck für Turbinenteile
Wie 3D-Druck leistungsfähigere Hydraulikkomponenten ermöglicht
Wie 3D-Druck Innovationen in der Kernkraftindustrie unterstützt
Warum wird 3D-Druck zur Herstellung von Raketenkomponenten verwendet?
Der Wettlauf, Satelliten ins All zu bringen, wird immer heftiger.
Aus diesem Grund stehen die Hersteller von Raumfahrzeugen vor der Herausforderung, die Entwicklung und Produktion von Raketen zu beschleunigen und gleichzeitig Kosten zu senken und die Effizienz zu steigern.
Bei der konventionellen Raketenfertigung machen jedoch mehrere Prototyping-Zyklen und Produktionsschritte den Prozess lang und sehr kostspielig.
Zum Beispiel kann es zwischen 10 und 14 Monate dauern, um eine konventionelle Brennkammer herzustellen (eine strukturelle Raketenkomponente, bei der ein Gemisch aus Treibstoff und Druckluft gezündet wird).
Um diese Brennkammern herzustellen, müssen die Hersteller separate Komponenten gießen und schmieden. Kühlkanäle müssen dann um bearbeitet werden die Kammer – ein sehr zeitaufwändiger, arbeits- und kostenintensiver Prozess.
Angesichts dieser Herausforderungen beginnen große Raketenhersteller bereits, Brennkammern mit additiver Fertigung herzustellen. Einmal konstruiert, kann eine 3D-gedruckte Brennkammer innerhalb weniger Wochen hergestellt werden, wodurch Hersteller Produktionszeiten und -kosten deutlich reduzieren können.
Die Herstellung von Hardware für den Weltraumstart erfordert außergewöhnliche Leistung und Präzision. Um eine erfolgreiche Einführung zu gewährleisten, müssen alle Teile nahtlos zusammenarbeiten.
In der traditionellen Fertigung stoßen Ingenieure bei der Konstruktion hochkomplexer Raketenteile auf Grenzen. Der Metall-3D-Druck ermöglicht es Ingenieuren, einige der Einschränkungen herkömmlicher Prozesse zu überwinden und komplexere Raketenkomponenten schneller zu entwickeln.
Die 3D-Drucktechnologien zur Herstellung von Raketenkomponenten
Bis heute haben Raumfahrtunternehmen im Großen und Ganzen laserbasierte Metall-3D-Drucktechnologien wie Selective Laser Melting (SLM) übernommen, um Raketentriebwerksteile wie Brennkammern, Einspritzdüsen, Düsen, Pumpen und Ventile herzustellen. SLM wendet einen leistungsstarken, fein abgestimmten Laser auf eine Schicht aus Metallpulver an, wodurch Metallpartikel miteinander verschmolzen werden. Der Prozess wird für Hunderte von Schichten wiederholt, bis ein Teil entsteht.
SLM bietet hohe Präzision (kann bis zu 20 Mikrometer dünne Schichten drucken) und ist für die Arbeit mit einer Vielzahl von Hochleistungsmetallen optimiert , von Titan bis zu Nickellegierungen. Diese Technologie wird typischerweise für kleinere Teile verwendet.
Zusätzlich zu SLM verwenden einige Raumfahrtunternehmen die Direct Energy Deposition (DED)-Technologie, um große Komponenten herzustellen. DED-3D-Drucker arbeiten, indem sie Metallmaterial mit einem Laser oder einem Elektronenstrahl schmelzen, während es durch eine Düse auf die Bauplattform aufgebracht wird.
Normalerweise haben DED-Maschinen hohe Materialauftragsraten und können mit Metallmaterialien in Pulver- oder Drahtform arbeiten, wodurch hochdichte Teile mit endkonturnahen Formen erzeugt werden.
Die Vorteile des 3D-Drucks für Raketen
Iterationsfähigkeit schnell
Einer der größten Vorteile des 3D-Drucks für Raketenteile ist die Möglichkeit, Designs sehr schnell zu wiederholen.
“Mit Additiv können Sie fünf Iterationen eines Designs durchlaufen, bevor Sie mit einer herkömmlichen Methode auch nur die ersten erhalten, und alle fünf zusammen werden wahrscheinlich weniger als eine kosten traditionelle Iteration “, sagt Scott Killian, Aerospace Business Development Manager bei EOS North America, in einem Interview mit engineering.com.
Ein 3D-Drucker kann Raketenteile ohne Werkzeug direkt aus einer Konstruktionsdatei erstellen. Wenn ein Teil modifiziert werden muss, können Ingenieure einfach Änderungen an einer Original-CAD-Datei vornehmen und viel schneller ein neues, modifiziertes Design erstellen, als dies mit herkömmlichen Verfahren möglich wäre.
Designflexibilität
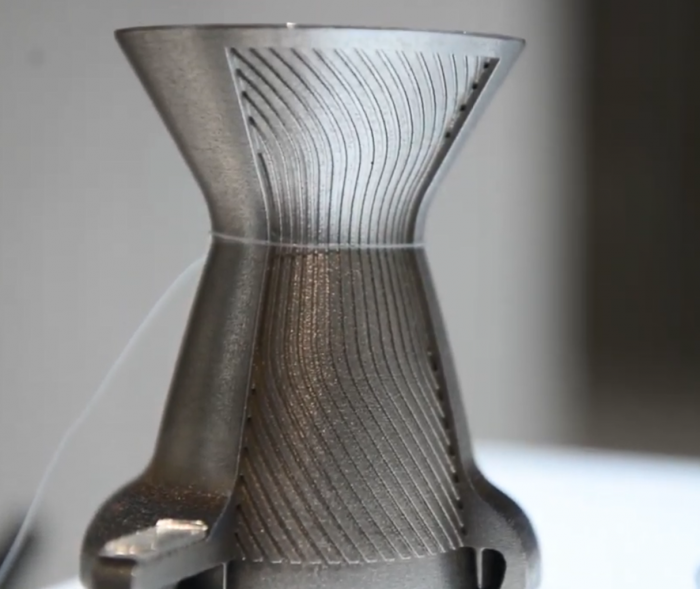
Ohne die Abhängigkeit von Werkzeugen bietet der 3D-Druck den Ingenieuren von Raumfahrzeugen die Flexibilität, komplexe Formen und Geometrien zu erstellen, die mit herkömmlichen Verfahren nicht erreichbar wären.
Betrachten Sie Brennkammern. Als entscheidende Komponente in allen Raketentriebwerken muss eine Brennkammer einer Umgebung mit hohem Druck und Temperaturen von bis zu 5 000 ° F (2760 ° C) standhalten, da sich die Treibstoffe im Inneren vermischen und entzünden.
Um eine effiziente Leistung zu erzielen, erfordert diese Komponente komplexe interne Kühlkanäle, die mit Gasen gefüllt sind, die auf weniger als 38°C über dem absoluten Nullpunkt abgekühlt sind.
Traditionell sind diese Kühlkanäle sehr kompliziert und teuer in der Entwicklung. Sie erfordern spezielle Werkzeuge, um Kühlkanäle CNC zu bearbeiten und die Außenwand der Kammer zu löten. Diese separaten Segmente müssen dann zu einem Stück verschweißt werden.
Der 3D-Druck hingegen rationalisiert den Prozess, indem er die direkte Herstellung der gesamten Kammer ermöglicht. Darüber hinaus ermöglicht es komplexe Kühlkanaldesigns, wie im Bild oben gezeigt, die nicht bearbeitet werden könnten.
Günstigere Raketenteile
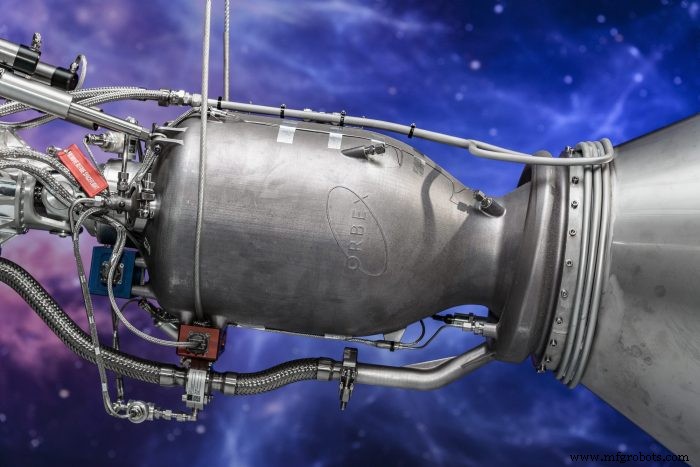
Triebwerke sind der teuerste Teil einer Trägerrakete (ein raketenbetriebenes Fahrzeug, das verwendet wird, um Satelliten oder andere Raumfahrzeuge ins All zu bringen). Die Kosten eines Triebwerks können bis zu 40 % der Gesamtkosten der Rakete ausmachen. Durch die Verwendung von 3D-Druck zur Herstellung wichtiger Triebwerksteile können Raketenhersteller die Gesamtkosten eines Raumfahrzeugs drastisch senken.
Der 3D-Druck ermöglicht es Ingenieuren, die Produktion von Raketentriebwerkskomponenten zu rationalisieren und eine Reihe von Produktionsschritten zu umgehen. Je weniger Schritte, desto weniger Ausrüstung und Feinabstimmung sind erforderlich, was letztendlich zu niedrigeren Produktionskosten führt.
Außerdem bedeutet die Automatisierung des Produktionsprozesses mit 3D-Druck, dass die meisten Arbeitskosten aus der Gleichung eliminiert werden .
Das britische Luft- und Raumfahrtunternehmen Orbex hat beispielsweise SLM-Technologie und eine Nickellegierung verwendet, um ein Triebwerk für seine Prime-Trägerrakete in 3D zu drucken. Der 3D-Metalldruck ermöglichte es Orbex, die Durchlaufzeit um 90 % zu reduzieren und die Kosten um 50 % im Vergleich zu traditionelleren Produktionsprozessen wie der CNC-Bearbeitung zu senken.
Elon Musks kommerzielles Raumfahrtunternehmen SpaceX in Privatbesitz hat hat auch den 3D-Druck angenommen, um Kosten zu senken und mehr Flexibilität im Produktionsprozess seiner Draco- und SuperDraco-Triebwerke zu bieten. Das Unternehmen verwendet einen SLM-basierten 3D-Metalldrucker, um Inconel-Brennkammern herzustellen.
Laut Musk „können durch 3D-Druck robuste und leistungsstarke Motorteile zu einem Bruchteil von . hergestellt werden Kosten und Zeit traditioneller Herstellungsmethoden .“
Vereinfachte Montage
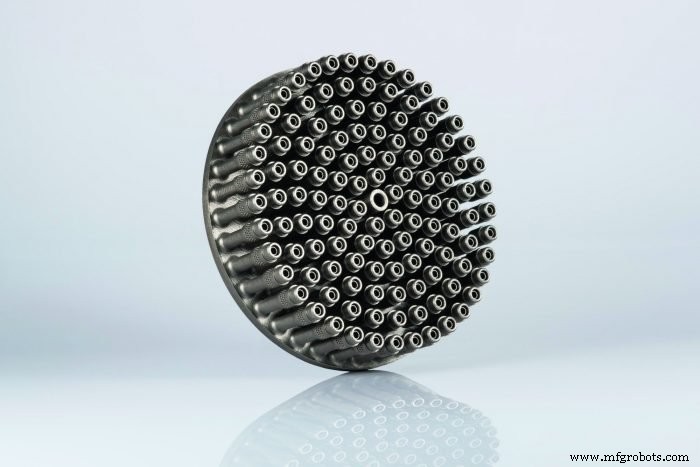
Darüber hinaus können Ingenieure auch die Anzahl der Schritte im Montageprozess erheblich reduzieren. Dies kann durch den 3D-Druck von Raketenteilen erreicht werden, die aus mehreren Komponenten als ein einziges Stück bestehen.
Nehmen Sie als Beispiel einen Injektorkopf. Ein Injektorkopf ist eines der Kernelemente eines Antriebsmoduls, der das Kraftstoffgemisch in den Brennraum drückt.
Traditionell werden Injektorköpfe aus Dutzenden oder sogar Hunderten von Teilen hergestellt, die bearbeitet und zusammengeschweißt werden müssen. Im Gegensatz dazu kann der 3D-Druck solche Bauteile als Einzelstück herstellen.
Forscher des Deutschen Zentrums für Luft- und Raumfahrt (DLR) haben mithilfe des 3D-Drucks ein neues Design eines Injektorkopfes für eine kleine Satelliten-Trägerrakete entwickelt.
Das Ergebnis ist ein monolithisches Teil, das 10 % leichter ist. Durch die Reduzierung der Komponentenanzahl von 30 auf nur noch eines eliminierte das Forschungsteam auch bekannte Fehlerstellen an Befestigungsstellen. Schließlich soll das neue, optimierte Design die Teileleistung verbessern und die Lebensdauer des Teils verlängern.
Ebenso vereinfachte der Metall-3D-Druckspezialist EOS die Montage eines Injektorkopfes für seinen Ariane-6-Träger , entwickelt von ArianeGroup, einem Joint Venture von Airbus Group und Safran.
Der Einsatz der SLM-Technologie ermöglichte es dem Team, einen Injektorkopf als eine Komponente neu zu konstruieren, anstelle der 248 Komponenten, die für ein herkömmliches Design erforderlich sind. Weitere Vorteile waren eine Kostenreduktion von 50 % und eine dreimal kürzere Lieferzeit.
Beispiele für 3D-gedruckte Raketenteile
Die 3D-gedruckte Rutherford-Engine von Rocket Lab
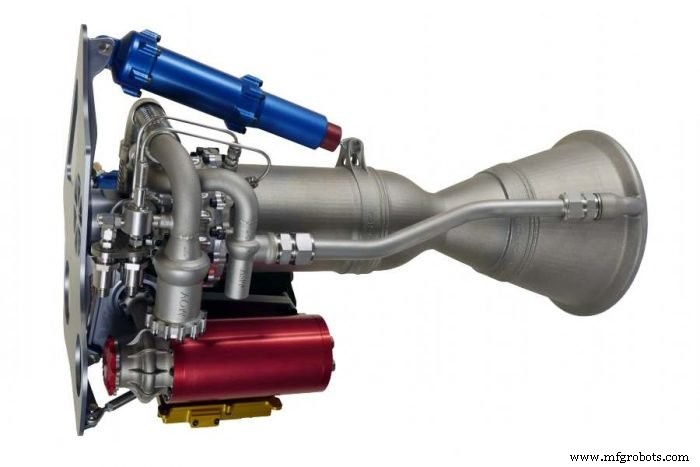
Im Juli stellte Rocket Lab, ein in Kalifornien ansässiges Luft- und Raumfahrtunternehmen, das 100. 3D-gedruckte Rutherford-Raketentriebwerk fertig. Das Unternehmen verwendet 3D-Druck seit 2013 für alle seine primären Triebwerkskomponenten (einschließlich Brennkammern, Einspritzdüsen, Pumpen und Haupttreibstoffventile).
Neun Rutherford-Flüssigtreibstofftriebwerke treiben die Electron-Rakete von Rocket Lab an. der aus Verbundwerkstoffen besteht und bis zu 225 kg Nutzlast tragen kann. Die Triebwerksteile werden mit der Electron Beam Melting (EBM)-Technologie in 3D gedruckt, die Triebwerksteile billiger als herkömmliche Verfahren herstellen soll.
Kürzlich hat Rocket Lab erneut die Zuverlässigkeit von 3D-gedruckten Triebwerken bewiesen und mit seinem Elektronenwerfer vier Satelliten erfolgreich in die Umlaufbahn gebracht.
Bis 2020 plant das Unternehmen, zwei Markteinführungen pro Monat durchzuführen. Da der 3D-Druck es Rocket Lab ermöglicht, einen Motor in wenigen Tagen statt in Monaten zu produzieren, ist das Team gut aufgestellt, um diesen Plan in die Tat umzusetzen.
3D-Druck ganzer Raketen
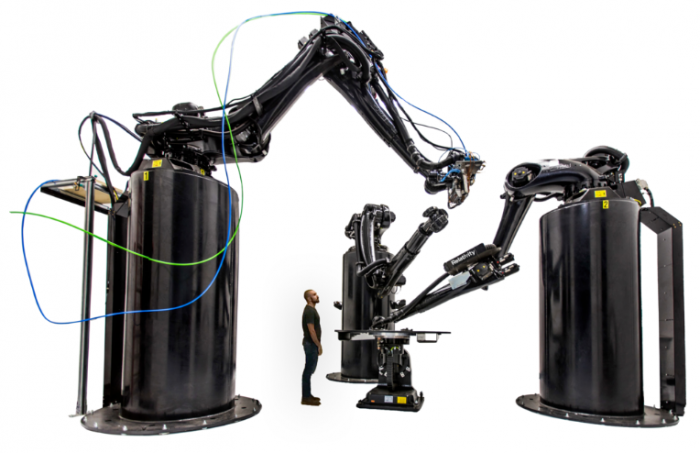
Das kalifornische Startup Relativity Space will über 3D-gedruckte Raketentriebwerke hinausgehen. Das Unternehmen entwickelt eine terranische Rakete, von der rund 95 % der Komponenten 3D-gedruckt werden.
Um dies zu erreichen, hat das Unternehmen Stargate entwickelt, einen der weltweit größten DED-Metall-3D-Drucker. Mit der Fähigkeit, Komponenten mit einem Durchmesser von bis zu 2,7 m (9 Fuß) und einer Höhe von etwa 4,5 m (15 Fuß) herzustellen, druckt Stargate alle Treibstofftanks und andere große Raketenkomponenten.
Durch die Verwendung von 3D-Druck zur Herstellung praktisch einer ganzen Rakete hofft Relativity Space, das Gewicht der Rakete erheblich zu reduzieren, was möglicherweise die Startkosten senken kann und gleichzeitig die Nutzlast erhöht.
3D-Druck wird auch die Anzahl der zu montierenden Teile reduzieren und so die Festigkeit und Stabilität der Rakete erhöhen.
Für kleinere Teile setzt das Unternehmen die SLM-Technologie ein.
Laut Relativity Space ermöglicht es der 3D-Druck, Designs schnell zu ändern und weniger Werkzeug und Arbeit zu verwenden, als normalerweise bei der Raketenentwicklung erforderlich wäre. Letztendlich könnte Relativity Space dadurch in weniger als zwei Monaten vom Rohmaterial zu einer flugbereiten Rakete werden.
Relativity Space ist derzeit das einzige Unternehmen, das 3D-Drucktechnologien für eine ganze Rakete anwendet. Wird sich das Konzept einer 3D-gedruckten Rakete als erfolgreich erweisen? Die Antwort wird letztendlich im Testen und Starten liegen. Der Teststart der 3D-gedruckten terranischen Rakete ist für Ende 2020 geplant.
Die Zukunft des 3D-Drucks in der Luft- und Raumfahrt
Der 3D-Druck hat die Art und Weise revolutioniert, wie Raketen und Raketentriebwerksteile konstruiert und hergestellt werden. Die Grundlagen des Raketendesigns haben sich vielleicht nicht geändert, aber der 3D-Metalldruck hat neue Möglichkeiten zur Verbesserung der Raketenleistung eröffnet und bietet mehr Designfreiheit.
Die Technologie kann dazu beitragen, die Herstellungskosten von Triebwerken, einer der teuersten Raketenkomponenten, zu senken. Dies wird erreicht, indem die Anzahl der Produktionsschritte reduziert und häufigere Designiterationen ermöglicht werden.
Obwohl die Fähigkeiten des 3D-Drucks über Motorenteile hinaus noch getestet werden müssen, ist das Potenzial der Technologie für vollständig 3D-gedruckte Raketen in der Zukunft ist wirklich aufregend.
3D-Druck hat sich zu einer wichtigen Fertigungstechnologie für die Produktion von Raumfahrzeugen entwickelt, die es Ingenieuren ermöglicht, schneller Innovationen zu entwickeln und die nächste Generation der Raumfahrt zu verwirklichen.
In unserem nächsten Artikel werfen wir einen Blick auf den 3D-Druck in der Schuhindustrie. Bleiben Sie dran!
3d Drucken
- Generatives Design und 3D-Druck:Die Fertigung von morgen
- Anwendungs-Spotlight:3D-Druck für die digitale Zahnheilkunde und die Herstellung von Clear Alignern
- Robotik und die Zukunft von Produktion und Arbeit
- Die Vorteile von Rapid Prototyping und 3D-Druck in der Fertigung
- Industrielle Automatisierung:Eine kurze Geschichte der Fertigungsanwendung sowie der aktuelle Stand und die Zukunftsaussichten
- Die Zukunft der Industriemaschinen im Jahr 2020 und darüber hinaus
- Welche Rolle werden Robotik und 3D-Druck in der Fertigung der Zukunft spielen?
- Automatisierung und die Zukunft der digitalen Fertigung?
- Die Zukunft des 3D-Drucks in der Fertigung
- Ist 3D-Druck die Zukunft der Fertigung?