5 Möglichkeiten, wie 3D-Druck die traditionelle Fertigung ergänzt
Es wurde vorhergesagt, dass der 3D-Druck traditionelle Fertigungstechnologien ersetzen wird. Die wahre Stärke der Technologie liegt jedoch möglicherweise nicht in der Konkurrenz, sondern in der Ergänzung und Ergänzung konventioneller Herstellungsverfahren.
Um diese Behauptung zu untermauern, untersuchen wir im Folgenden fünf wichtige Möglichkeiten, wie der 3D-Druck die traditionelle Fertigung unterstützen kann.
1. 3D-Druck leistungsfähigere Spritzgussformen
Spritzgießen beinhaltet den Prozess des Schmelzens und Einspritzens von Kunststoffmaterial in ein spezielles Formwerkzeug, das als gewünschtes Objekt geformt wird. Wenn Kunststoff aushärtet, nimmt er die Form des Formhohlraums an. Spritzgießen ist der beste Weg, um hochpräzise und komplexe Produkte und Teile in Serie herzustellen.
Der Prozess birgt jedoch auch einige Herausforderungen. Spritzgussteile werden beispielsweise dadurch gekühlt, dass Kanäle – im Wesentlichen Durchgänge nahe der Werkzeugoberfläche – durch das Werkzeug hindurch gebaut werden. Diese Kanäle sind normalerweise gerade Linien, was manchmal zu einer ungleichmäßigen Kühlung führen kann und das Risiko einer Verformung des Teils erhöht.
Effiziente Kühlung kann mit konturnahen Kühlkanälen erreicht werden, die sich der Form des Teils anpassen. Allerdings lassen sich solche Kanäle mit herkömmlichen Verfahren nur schwer herstellen, was den 3D-Druck zu einer attraktiven Alternative zur Herstellung von Spritzgussformen macht.
Formen mit konturnahen Kühlkanälen zu erstellen hilft nicht nur die Qualität der Formteile zu steigern, sondern hilft auch die Kühlzeit deutlich zu verkürzen.
3D-Druck hilft bei der Optimierung der Spritzgusslinie
Ein Beispiel dafür ist die Alfred Kärcher GmbH &Co. KG, die jährlich Millionen ihrer K2-Hochdruckreiniger weltweit verkauft. Bei dem Versuch, eine solche Nachfrage zu decken, sah sich das Unternehmen mit einem Produktionsengpass konfrontiert, wodurch die Produktion der Scheibengehäuse erhöht werden musste.
Anstatt weitere Spritzgussmaschinen anzuschaffen, suchte Kärcher nach Möglichkeiten, die Produktivität der bestehenden Maschinen zu steigern. Die Lösung fand das Unternehmen im Metall-3D-Druck.
Kärcher wandte sich an LBC Engineering, ein Teil der Renishaw GmbH, das feststellte, dass die Zykluszeit des Spritzgusses durch die Ineffizienz des Kühlprozesses beeinflusst wurde. Die Gehäuseformen waren mit traditionellen Kühlsystemen ausgestattet, die in geraden Linien gebohrt wurden, wodurch heiße Stellen erzeugt wurden, die die Zykluszeit verlängerten.
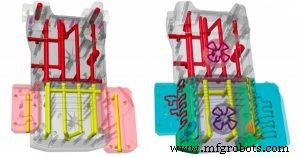
LBC Engineering modifizierte das Design der Form, indem es zwei 3D-gedruckte Kerne erstellte, um eine konforme Kühlung an den identifizierten Hotspots zu gewährleisten.
3D-gedruckte konturnahe Kühlkanäle halfen, die Wandtemperatur in den Werkzeugen von 100 °C auf 70 °C zu senken, wodurch die Kühlzeit von 22 auf 10 Sekunden verkürzt wurde, was einer Reduzierung um 55 Prozent entspricht.
Zusammen mit einigen Anpassungen an peripheren Komponenten, wie der Materialzuführung und dem Handlingsystem, hat sich die Zykluszeit für Gehäuse von 52 auf 37 Sekunden reduziert. Der 3D-Druck lieferte den Löwenanteil dieser Reduzierung und ermöglichte es Kärcher, die Produktivität seiner Linie zu steigern und die Ziele der Karkassenproduktion zu erreichen.
In einem anderen Beispiel hat der Spritzgussprofi Pat Zaffino eine mehrschichtige Roboterabscheidungstechnologie entwickelt, die konforme Kühlkanäle in 3D auf die Oberfläche von Spritzgussformen druckt.
Anfang dieses Jahres hat Zaffino ein neues Unternehmen, Conformal Cooling Solutions Inc. (CCS), gegründet, um die Vorteile der Verwendung von konformen Kühlkanälen zu fördern.
'Erstellen von konformen Kühlkanälen die der Form der Kavität und des Kerns folgen, fördert die Temperaturgleichmäßigkeit in den zu spritzenden Kunststoffen, und Gießer, die diese Technologie verwenden, sehen beeindruckende Ergebnisse:verkürzte Zykluszeiten, verbesserte Qualität der Kunststoffteile und vor allem Kosteneinsparungen“, sagte er. in einem Interview mit canplastics.com.
Da die Technologie billiger und einfacher zu übernehmen wird, könnten Formen mit 3D-gedruckten konformen Kühlkanälen letztendlich zu einem neuen Standard in der Branche werden.
2. 3D-Druckmuster für den Feinguss
Im Feinguss werden verbrauchbare Wachsmodelle und Keramikschalen verwendet, um komplexe und detaillierte Teiledesigns zu erstellen. Traditionell werden diese Muster spritzgegossen. Die Kosten für Spritzgussformen können jedoch mehrere tausend Dollar erreichen, mit Vorlaufzeiten von einer bis vier Wochen. Dies macht den Prozess für Personen unerschwinglich, die möglicherweise nicht über so viel Kapital verfügen oder kurze Lieferfristen für Teile haben.
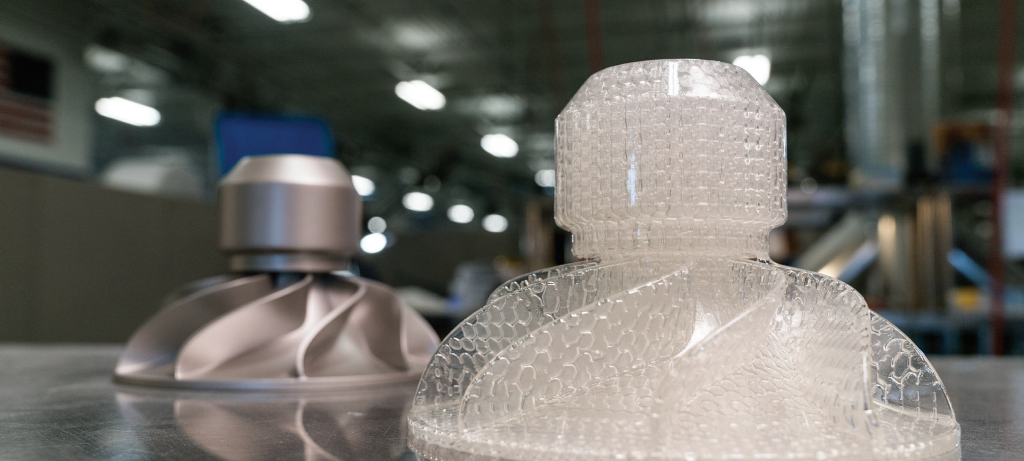
Aus diesem Grund können Unternehmen 3D-Druckmuster in einem Material wählen, das für den Feinguss geeignet ist. Viele Hersteller von 3D-Druckern haben 3D-druckbare Materialien speziell für das Gießen entwickelt, darunter Wachs, gießbare Harze und einige Thermoplaste, basierend auf PLA und ABS.
Diese Materialien werden typischerweise mit Stereolithographie (Harze) und FDM ( Kunststoffe) Technologien, die hochpräzise Muster mit hervorragenden Ausbrenneigenschaften erzeugen.
Ein weiterer Vorteil dieses Ansatzes ist das relativ geringe Risiko, ihn auszuprobieren. Muster können mit professionellen Desktop-3D-Druckern in 3D gedruckt werden, die weniger als 5.000 US-Dollar kosten, ein Bruchteil der Kosten teurer industrieller 3D-Druckgeräte.
Beschleunigung der Vorlaufzeiten für Gussteile mit 3D-Druck
3D-gedruckte Feingussmodelle werden zunehmend verwendet, um kundenspezifischen Schmuck mit komplizierten Designs und kürzeren Vorlaufzeiten herzustellen. In einem Beispiel konnte das kanadische Schmuckunternehmen Vowsmith – das auf maßgeschneiderte Ringe spezialisiert ist – seine Produktions- und Lieferzeiten um 50 % verkürzen, indem es die Wachs-3D-Drucker von 3D Systems in seinen Workflow integriert hat. In einem einzigen Druck produzierte das Unternehmen zwischen 35 und 40 personalisierte Ringmuster, die zum Gießen bereit sind.
Die Technologie wird zunehmend auch in Gießereien eingesetzt, um komplexe Muster für verschiedenste industrielle Anwendungen zu erstellen. Beispielsweise hat Invest Cast, Inc. vor kurzem die neue digitale Gießereilösung von 3D Systems in seine Modellherstellung integriert.
Die Möglichkeit, endgültige Gussteile ohne Werkzeuge herzustellen, hat den Kunden von Invest Cast die Freiheit gegeben, Testen Sie mehrere Iterationen schnell und kostengünstig, um letztendlich bessere Endteile zu erhalten.
Laut Invest Cast hat der 3D-Drucker ProJet MJP 2500 IC von 3D Systems beim Feingussprozess erheblich Zeit eingespart . Die Technologie ermöglicht es dem Unternehmen, in 2-5 Tagen vom Modell zum Metall zu gelangen, was einer durchschnittlichen Vorlaufzeit von etwa 6-12 Wochen bei Feingussformen entspricht.
3. Produktivitätssteigerung mit 3D-gedruckten Schneidwerkzeugen
3D-Druck kann verwendet werden, um Schneidwerkzeuge herzustellen – kleine Wendeschneidplatten aus Hartmetall, die Material von der programmierten Werkzeugbahn entfernen.
Einige Hochleistungswerkstoffe wie ultrahochfeste Stähle, Titan- und Nickellegierungen können schwer zu bearbeiten sein und können zu einem schnellen Verschleiß des Werkzeugs führen.
3D-Druckwerkzeuge mit benutzerdefinierten Geometrien und eingebauten Kühlkanälen, die überschüssige Wärme, die während der Bearbeitung in der Nähe der Schneidzone erzeugt wird, effektiv abführen können, können die Werkzeugstandzeit und -leistung erhöhen.
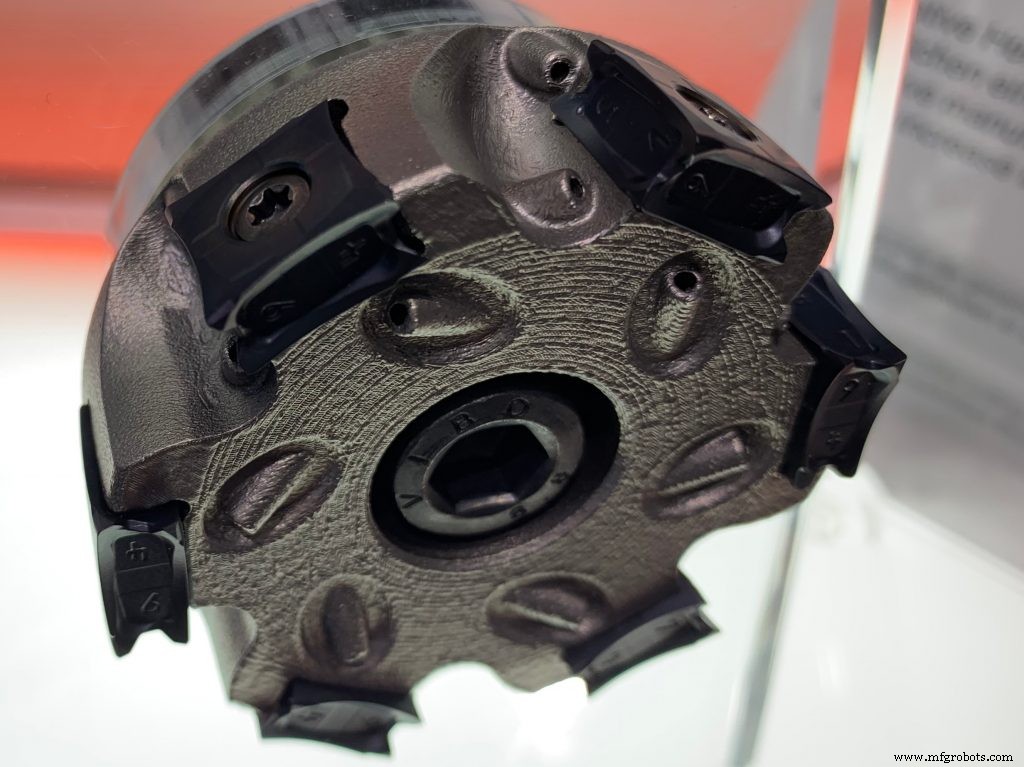
Der Werkzeugspezialist LMT Tools Inc. hat die Technologie verwendet, um innere Kühlmittelkanäle in einem Fräswerkzeugkörper zu erzeugen, der zuvor gerade Löcher hatte. Die Freiheit des 3D-Drucks, gekrümmte Kanäle bereitzustellen, ermöglicht es dem Fräswerkzeug von LMT, Kühlmittel genau dort zuzuführen, wo es benötigt wird. Laut LMT hat das Testschneiden beim Fräsen von Titan dank dieser Konstruktionsänderung eine Verbesserung der Werkzeugstandzeit um 50 Prozent gezeigt.
Komet Group steigert die Werkzeugproduktivität mit 3D-Druck
Einer der weltweit führenden Anbieter von Präzisionsschneidwerkzeugen, die Komet Group, wendet den Metall-3D-Druck auch in der Werkzeugherstellung an.
Durch die Verwendung von Aluminiumlegierungen und laserbasierter Technologie des britischen Spezialisten Renishaw konnte Komet mehr Schneidkanten in das Werkzeug einbringen und seine Geometrie optimieren, um die Werkzeugproduktivität zu steigern.
Ingenieure haben beispielsweise die Kühlmittelkanäle des Werkzeugs optimiert, um sicherzustellen, dass jede Schneide über einen separaten Kanal präzise mit Kühlmittel versorgt wird. Dank dieser konstruktiven Verbesserungen kann die Bearbeitungszeit pro Einheit um bis zu 50 Prozent reduziert werden.
AM bietet auch das Potenzial zur Reduzierung des Bauteilgewichts, da das Material nur dort eingesetzt werden kann, wo es für die optimale Funktionalität im Bauteil erforderlich ist. Es wird auch berichtet, dass es konventionelle Produktionsmethoden in Bezug auf die Lieferzeit für alle Spezial- oder Versuchswerkzeuge, die von Komets Kunden benötigt werden, übertrifft.
3D-Druck für einen effizienteren Fräskopf
Darüber hinaus hat der schwedische Werkzeugsystemhersteller Sandvik Coromant kürzlich einen neuen Fräser mit einem 3D-gedruckten Metallkopf vorgestellt. Als Premiere für das Unternehmen markiert die Komponente einen Schritt in Richtung des Engagements des Unternehmens im 3D-Druck für die Endverbrauchsproduktion.
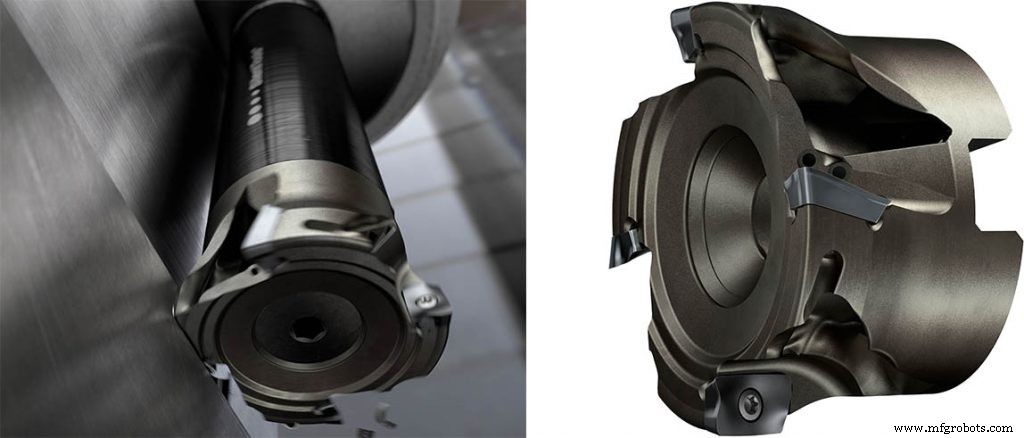
Der neue Lightweight CoroMill 390 von Sandvik Coromant ist ein Metallfräskopf auf Basis des CoroMill 390-Designs. Das Werkzeug, das aus Sandviks charakteristischem Osprey-Pulver aus Titanlegierung hergestellt wird, wurde speziell entwickelt, um Vibrationsprobleme beim Metallfräsen mit langen Überhängen zu überwinden.
Solche Eigenschaften sind eine häufige Anforderung an Komponenten, die in der Luft- und Raumfahrt sowie in der Öl- und Gasindustrie verwendet werden. Tiefe Hohlräume in einem CNC-bearbeiteten Teil können durch Vibrationen beeinträchtigt werden, was zu einer langsameren Produktion, kürzeren Werkzeugstandzeiten und schlechter Oberflächengüte führt. In Kombination mit den Silent Tools-Fräsadaptern des Unternehmens kann das 3D-gedruckte Werkzeug die Bearbeitungsproduktivität um 50 Prozent steigern.
4. Reparatur von abgenutzten und beschädigten Werkzeugen
3D-Druck kann nicht nur verwendet werden, um neue Werkzeuge und Formen herzustellen, sondern auch um beschädigte Werkzeuge zu reparieren. Unternehmen der Luft- und Raumfahrt, des Schiffbaus und der Industriegüter beginnen, AM-Verfahren wie Direct Energy Deposition (DED) zu verwenden, um Komponenten wieder in ihre ursprüngliche Form zu bringen.
Auch bekannt als Laserauftragschweißen, erzeugt DED mit einem Laser ein Schweißbad auf der Bauteiloberfläche. Das Material wird dann als Pulver oder Draht in das Schmelzbad gegeben. Die geschmolzenen Partikel verschmelzen und verfestigen sich, während die Düse manipuliert wird, um dem Bauteil die gewünschte Struktur zu verleihen.
Anfang dieses Jahres startete ein Konsortium aus 7 britischen Unternehmen und Organisationen ein 1,2-Millionen-Pfund-Projekt namens DigiTool , um eine kostengünstige Reparatur von Werkzeugen und Formen durch den Einsatz von AM-Technologien zu ermöglichen.
Mit 3D-Druck können Unternehmen im Werkzeug- und Formensektor die Kosten für den Austausch und die Reparatur von Formen mit dem Potenzial zur Beschleunigung überwinden den Wartungsprozess auf. Dies wird Unternehmen helfen, Kosten und Material zu sparen und gleichzeitig ihre Nachhaltigkeit mit weniger Verschwendung zu verbessern.
Schnellere Reparatur eines Formeinsatzes
Der deutsche Werkzeug- und Formenbau HWF hat 3D-Druck verwendet, um einen Formeinsatz zu reparieren. Eine der Herausforderungen für HWF war der Aufbau einer 300 x 20 x 20 mm großen Struktur auf einem typischen Formmaterial.
In der Vergangenheit wurden solche Strukturen mit a manuelles Laserauftragschweißverfahren mit Drahtvorschub, um das Risiko von Rissen, Verformungen und veränderten metallurgischen Eigenschaften zu vermeiden. Der Schweißer kann jedoch zwischen 60 und 80 Stunden benötigen, um die Aufgabe zu erledigen.
Heute verwendet HWF die DED-Technologie von OR Laser, die es ermöglicht, die gleiche Struktur durch Auftragen von 250 µm dicken Schichten zu erzeugen. mit einer Leistung von 5000 mm³ pro Stunde. Die Produktionszeit kann somit auf 24 Stunden verkürzt werden.
Dank dieses Verfahrens wird auch das Grundmaterial deutlich weniger angegriffen als bisher, wodurch das Risiko von Rissen und Materialhinterschneidungen, die oft durch konventionelle Reparaturmethoden verursacht werden, stark reduziert wird.
5. Mehr Flexibilität mit Hybridprozessen
Die Kombination von additiven und subtraktiven Fähigkeiten in einem Hybridsystem ist eine weitere Möglichkeit, wie AM die traditionelle Fertigung ergänzen kann. In diesem Szenario können additive und subtraktive Technologien eine Reihe von Möglichkeiten für eine verbesserte Fertigung aus einer Hand eröffnen.
Hybridfertigung nutzt die wertvollsten Fähigkeiten beider Technologien:die geometrische Komplexität von AM und die hohe Präzision subtraktiver Methoden. Dadurch kann ein Teil in einem Arbeitsgang additiv erstellt und bearbeitet werden, was den Produktionsprozess beschleunigt.
Mehrere kommerzielle Hybridsysteme sind mittlerweile auf dem Markt erhältlich. DMG MORI kombiniert beispielsweise DED mit 5-Achs-CNC-Fähigkeit in seinem hybriden Fertigungssystem.
Matsuura und Sodick verfolgten einen anderen Ansatz und kombinierten Powder Bed Fusion (PBF)-Technologie und CNC-Fähigkeit in ihren hybriden Fertigungssystemen. Um im Wettbewerb mithalten zu können, hat DMG MORI kürzlich mit einem eigenen PBF- und CNC-Hybridsystem reagiert.
Neben einem eigenständigen Hybridsystem besteht auch die Möglichkeit, ein bestehendes CNC-Bearbeitungszentrum mit dem Ambit-Pulverbeschickungs-Laserauftragskopf von Hybrid Manufacturing Technologies nachzurüsten.
Mit der Technologie von 3D Hybrid können Unternehmen einer CNC-Maschine auch eine Kombination aus Pulver- und Drahtzufuhrfunktionen hinzufügen. Dadurch kann ein konventionelles subtraktives System mit relativ geringem Kosten- und Arbeitsaufwand in ein hybrides Fertigungssystem umgewandelt werden.
Obwohl das Versprechen der hybriden Fertigung faszinierend ist, haben wir gerade erst begonnen zu lernen, wie diese Technologie sein kann effizient und nachhaltig angewendet werden.
Einführung des 3D-Drucks als ergänzende Technologie
3D-Druck kann ein wertvolles Gut für Hersteller werden, die ihre traditionellen Herstellungsprozesse optimieren möchten.
Mit der Technologie lassen sich leistungsfähigere Formen und komplexe Gussmodelle herstellen sowie die Effizienz von Zerspanungswerkzeugen steigern. Darüber hinaus können Hybridmaschinen Unternehmen mehr Freiheit und Flexibilität in Konstruktion und Fertigung bieten.
Anstatt die additive Fertigung als konkurrierende Technologie zu betrachten, sollten Hersteller sie daher als weiteres Werkzeug in der Toolbox aufnehmen und die Vorteile nutzen, die sie bietet.
3d Drucken
- 5 Vorteile des 3D-Drucks in der Fertigung
- 4 Wege, wie 3D-Druck die Medizinbranche verändert
- 8 Wege, wie der industrielle 3D-Druck die Fertigung revolutioniert
- 6 Möglichkeiten zur Senkung der Herstellungskosten mit 3D-Druck
- 6 Möglichkeiten, die Kosten des 3D-Drucks zu senken
- 3D-Druck ist überall
- 5 Wege, wie der 3D-Druck die Automobilindustrie verändert
- Additive Fertigung in Medizin und Zahnmedizin
- Die Zukunft des 3D-Drucks in der Fertigung
- Ist 3D-Druck die Zukunft der Fertigung?