Software, CNC-Schnittstelle steigert die Produktivität der Push-Programmierung
Schnelle, intelligente Steuerungen machen mit großen Aufgaben kurzen Prozess.
Vernetzte Fertigungs- und Digitalisierungstechnologien treiben viele der wichtigsten Innovationen bei CNC-Maschinensteuerungen voran, die Werkstätten dabei helfen, Metall zu schneiden und Teile so schnell und effizient wie möglich herzustellen. In den meisten Fällen ist Software wegweisend, wenn es darum geht, sowohl CNC-Programmierern als auch Bedienern in der Werkstatt dabei zu helfen, Teile einfach und mit höchstmöglicher Präzision herzustellen.
Die CNC-Ausrüstung von heute strotzt geradezu vor den neuesten Hardware-Fortschritten, darunter schnellere Prozessoren, mehr integriertes RAM für rechenintensive Aufgaben sowie neuere Solid-State-Laufwerksoptionen, die nahezu sofortige Startzeiten sowie einen sorgenfreien Betrieb ermöglichen raue Geschäftsumgebungen.
Die neuesten Softwareentwicklungen mit Funktionen wie Apps für die vernetzte Fertigung, fortschrittliche 3D-Simulationen und berührungsbasierte Benutzeroberflächen bieten CNC-Konstrukteuren jedoch weiterhin die besten Möglichkeiten, sich von der Masse abzuheben.
„Die Steuerungssoftware ist wirklich der einzige Ort für Werkzeugmaschinenhersteller, um bahnbrechende Innovationen einzuführen“, sagte Michael Cope, technischer Produktspezialist, Hurco Cos. Inc., Indianapolis. „Da es nur wenige neue und innovative mechanische Lösungen gibt, insbesondere ohne die Einführung einer neuen Metallurgietechnologie oder ähnlichem, bietet es modernste Software und Änderungen an der grafischen Benutzeroberfläche, die CNC-Steuerungen leistungsfähiger, vielseitiger und benutzerfreundlicher machen der Bereich zu sein, in dem sich jeder Bauherr von der Konkurrenz abhebt.“
Können wir reden?
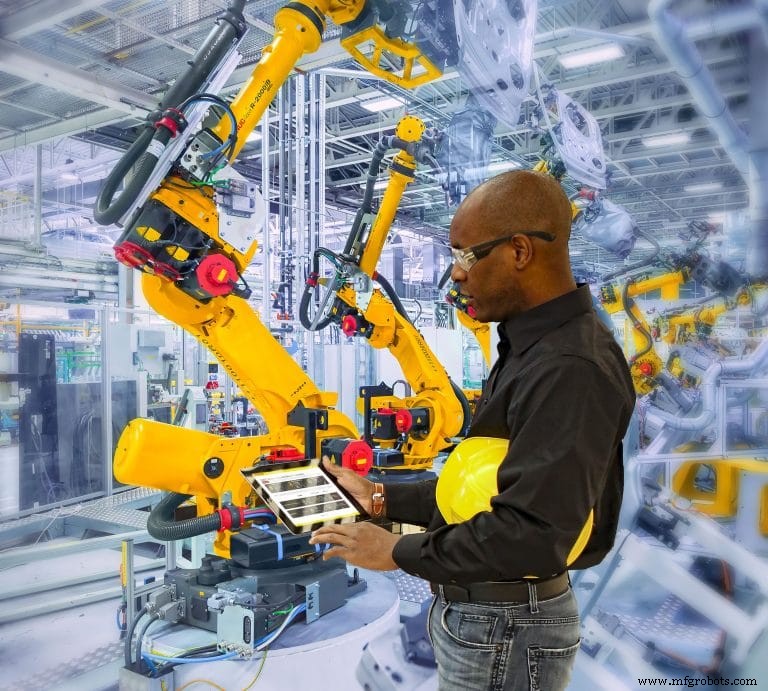
Während die Fertigungsindustrie ihre Digitalisierung durchläuft, fügen Entwickler von CNC-Steuerungen und Werkzeugmaschinenhersteller weiterhin neue Merkmale und Funktionen mit den neuesten Sensoren, Prozessoren und Software hinzu. Auf der IMTS präsentierten insbesondere die Steuerungsentwickler FANUC und Siemens neue Geräte und Strategien zur Vernetzung ihrer Steuerungen und Automatisierung für das industrielle Internet der Dinge (IIoT) und die Ermöglichung von Industrie 4.0.
Auf dem IMTS-Stand der in Rochester Hills, Michigan, ansässigen FANUC America Corp. zeigte das Unternehmen seine neuesten IIoT-Technologien, darunter das Datenerfassungs- und Überwachungssystem FANUC Intelligent Edge Link and Drive (FIELD) und seine Zero Down Time auf ROBOT-LINKi (ZDT), das prädiktive Analysen verwendet, um Ausfallzeiten aufgrund unerwarteter Ausfälle zu vermeiden.
FANUC zeigte auch neue CNC-Funktionen, einschließlich einer verbesserten, hochauflösenden 3D-Modell-Bearbeitungssimulation für fünfachsige und zusammengesetzte Bearbeitungsfunktionen; sein neuestes Series 0i-Model F Plus, die nächste Generation seiner Series 0i-Steuerungen; und seine QSSR-Funktion (Quick and Simple Startup of Robotization) zur Verbindung der CNCs von FANUC mit den Robotern des Unternehmens. Darüber hinaus hat FANUC Vision-Funktionen direkt in seine CNCs integriert.
„Wir sehen einen großen Schub in Richtung der Verwendung integrierter Bildverarbeitungssysteme auf CNCs“, sagte Paul Webster, technischer Leiter der CNC-Einheit von FANUC America in Hoffman Estates, Illinois, USA. „Das wird gerade veröffentlicht; Die Hardware-Technologie ist die gleiche wie auf der Roboterseite, aber sie ist anders implementiert.“ Das System, das eine andere Software als die in FANUC-Robotern verwendeten Bildverarbeitungssysteme verwendet, „ermöglicht eine flexible Implementierung der Bildverarbeitung durch die CNC“, sagte Webster.
Der neueste Trend, CNC-Werkzeugmaschinen miteinander zu verbinden, kann Herstellern eine höhere Produktivität und zuverlässigere Qualität bieten, bemerkte Tiansu Jing, Sinumerik-CNC-Produktmanager für den Siemens-Geschäftsbereich Machine Tools in Elk Grove Village, Illinois. „Siemens bietet variable technische Innovationen für alle Fertigungsbereiche, einschließlich der großen wie Aerospace und Automotive“, sagte er. „Die Innovationen konzentrieren sich nicht nur auf die Verbesserung der Engineering-Geschwindigkeit der Maschinenbauer durch die Einführung eines neuen, leistungsstarken TIA-Portals und von Safety Integrated Plus, sondern auch auf die ‚Kunst‘ der Digitalisierungsprodukte, die den Endkunden Möglichkeiten bieten, sich zu verbinden, überwachen, analysieren und optimieren ihre Maschinen.
„Smart Manufacturing/Industrie 4.0, auch ‚Digitalisierung‘ genannt, ist der Wendepunkt in der Fertigung“, so Jing weiter. „Durch die Vernetzung der Maschinen ergeben sich viele neue Möglichkeiten und neue Geschäftsmodelle. Um ihren Kunden einen besseren Service zu bieten, müssen die Hersteller ihre Produktivität und Qualität steigern, um bessere Produkte in kürzeren Lieferzeiten anbieten zu können. Um ihre Wettbewerbsposition auf dem Markt zu stärken, müssen die Unternehmen in ähnlicher Weise die Zeit verkürzen, die für die Entwicklung neuer Produkte benötigt wird.“
Maschinisten sind immer auf der Suche nach einfacheren und schnelleren Schneidvorgängen, fügte Jing hinzu. „Für verschiedene Arten von Maschinen benötigen sie unterschiedliche Funktionen, um dieses Ziel zu erreichen, z. „Top Surface“ für Formen- und Stanzen für eine bessere Oberflächenqualität in kürzerer Zeit und „Tool Manager“ zur einfachen Verwaltung aller Werkzeuge, um die Maschinenstillstandszeiten aufgrund von Werkzeugbruch usw. zu reduzieren“, sagte er.
Die Software Elemente von CNC-Steuerungen haben das einfache Hinzufügen spezialisierter Routinen und Makros ermöglicht, die die Produktivität sowohl bei großen Herstellern als auch bei kleineren Werkstattbetrieben steigern.
„Hersteller sind ständig auf der Suche nach höherer Produktivität und besserer Qualität“, bemerkte Jing.
„Begrenzt durch das Werkzeugmaterial und die Maschinenmechanik ist es schwierig, die Schnittgeschwindigkeit drastisch zu verkürzen, sodass das neue Potenzial zur Steigerung der Produktivität durch ein besseres Management der gesamten Wertschöpfungskette der Produktion, einschließlich der Verteilung der Aufgaben auf verschiedene Maschinen, optimierte Werkzeuganordnung, Simulation vor dem eigentlichen Schneiden, um das Design zu überprüfen, und Online-Analyse von Maschinenkomponenten, einschließlich Werkzeugen usw.
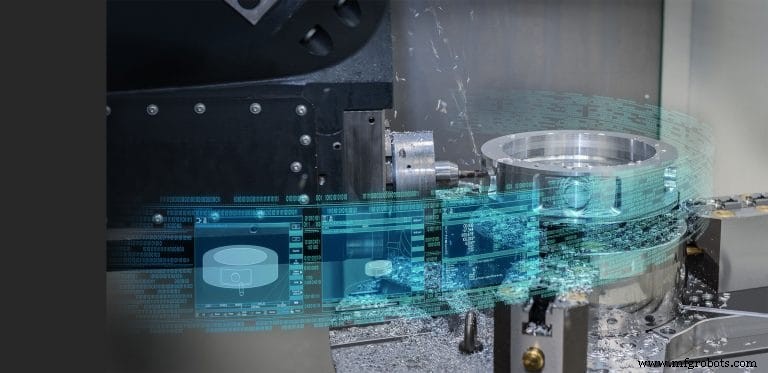
„Siemens bietet komplette Produktlinien an, um großen und kleineren Herstellern dabei zu helfen, ihren virtuellen Zwilling einzurichten und ihre Produktion zu analysieren, um die Produktion vom Produktdesign bis zur Auslieferung zu optimieren“, fuhr Jing fort. Die Siemens-Software umfasst Manage MyMachine, Analyze MyPerformance, Analyze ToolPath und Run MyVNCK, um das Design zu überprüfen, das Teileprogramm zu optimieren, das Schneiden zu simulieren und die Maschinen auf optimalem Leistungsniveau zu halten, fügte er hinzu.
Durch die Verbindung von Maschinen mit Industrie 4.0 und Smart Manufacturing kann die Industrie laut Hurco’s Cope das Spiel verändern und die Qualifikationslücke schließen, die heute in der Fertigung besteht. „Diese neuen Standards bieten die Möglichkeit, Maschinen und Steuerungen miteinander interagieren zu lassen und Maschinen zu ‚Helfern' innerhalb einer großen Fertigungszelle zu machen, in der ein bestimmter Auftrag oder ein bestimmtes Programm an die nächste verfügbare Werkzeugmaschine gesendet werden kann und nicht von einem abhängig ist bestimmte Maschine verfügbar wird. Sie können auch Job- oder Maschinen-Feedback an bestimmte E-Mail- oder Textempfänger senden.
„Die Leistungsfähigkeit und Vielseitigkeit der Arbeit mit Automatisierung wird in den kommenden Jahren für Geschäfte jeder Größe immer unschätzbarer werden“, fuhr Cope fort. „Aufgrund der geringeren Mitarbeiterzahl könnten kleinere Shops möglicherweise sogar mehr von dieser Technologie profitieren als größere Shops, weil sie dadurch mehr Stunden am Tag nutzen können – auch ohne verlängerte Zweit- und Drittschichten.“
Auf seinem IMTS-Stand zeigte Hurco Automatisierung mit kollaborativen Robotern, mehrachsigen seriellen Robotern und Palettensystemen, die die Automatisierung für die High-Mix-/Low-Volume-Teileproduktion demonstrierten, die in vielen Job-Shops zu finden ist, sagte Cope und stellte fest, dass die Automatisierungsausstellung eine Gemeinschaftsleistung war zwischen Hurco und Erowa, Universal Robots, FANUC, Online-Ressourcen und Industrial Controls &Automation.
„Hurco hat umfangreiche Engineering-Ressourcen eingesetzt, um unser patentiertes softwaregesteuertes Bewegungssteuerungssystem namens UltiMotion zu entwickeln“, sagte Cope. „Mit UltiMotion, enormen Speichermengen und NC-Block-Look-Ahead (alles Standardfunktionen unserer Steuerung) profitieren alle Branchen, aber unsere Formenbauer und Luft- und Raumfahrtwerkstätten werden davon besonders profitieren. Die Kombination aus Geschwindigkeit, Durchsatz und Reaktionsfähigkeit der Achsen wird dazu beitragen, dass der Kunde die bestmöglichen Teile mit kürzeren Zykluszeiten und hervorragenden Oberflächengüten produziert.“
Einzelne Setups, Simulation preisgekrönt
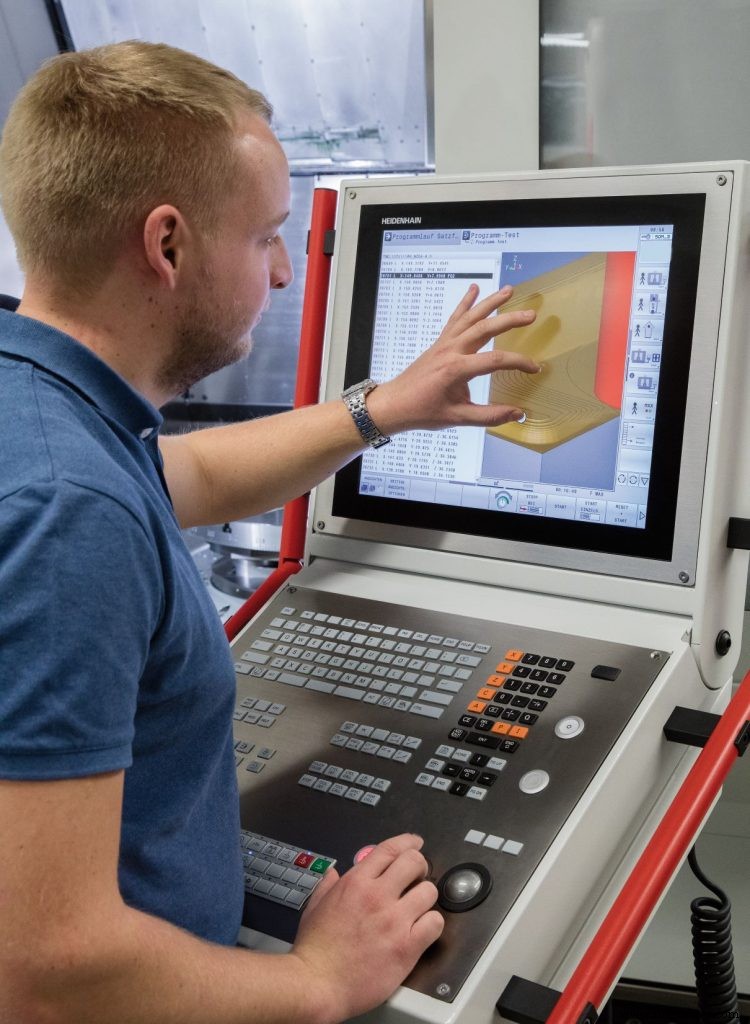
Effizienteres Arbeiten mit Einzelaufspannungen auf mehrachsigen Maschinen ist heute ein Trend bei CNCs, bemerkte Gisbert Ledvon, TNC Business Development Manager, Heidenhain Corp., Schaumburg, Illinois. „Die Leute wollen mehr auf einer Maschine machen, wenn sie können, also hat sich die Fünf-Achsen-Bearbeitung offensichtlich weit entwickelt, nicht nur für die volle Fünf-Achsen-Bearbeitung, sondern immer mehr für die 3+2-Bearbeitung, weil die Leute wettbewerbsfähig bleiben müssen“, sagte Ledvon . „Wenn sie so weitermachen wie bisher, werden sie nicht wettbewerbsfähig sein.“
Während einige Bearbeitungsarbeiten in die USA zurückkehren, ist dies bei der einfachsten Bearbeitung nicht der Fall, fügte er hinzu.
„Das komplexe Zeug kommt zurück. Es gibt einen Trend dahingehend, dass Menschen mehr mit einer Werkzeugmaschine erreichen wollen, also entweder fünf Achsen oder eine Fräs-Dreh-Anwendung auf einer Fräsmaschine. Sie wollen ein bisschen mehr in die Automatisierung einsteigen, also wollen sie eine einfache Funktionalität auf ihrer Steuerung, um vielleicht einen einfachen Palettenwechsler zu verwalten, und davon Prioritäten setzen.“
Bearbeitungsoperationen für das Wälzschälen und das komplexe Verzahnen haben ein Comeback erlebt, unterstützt durch eine neuere Software in der TNC-Steuerung von Heidenhain, fügte er hinzu. Komplexe Bearbeitungsvorgänge erfordern eine hochpräzise 3D-Modellierung in Simulationssoftware, wie sie Heidenhain kürzlich der TNC-Toolbox hinzugefügt hat, einschließlich der dynamischen Kollisionsüberwachung.
„Obwohl Sie möglicherweise eine externe Kollisionsüberwachung haben, wie zum Beispiel mit einem CAM- oder Vericut-Programm, das Ihr Programm überprüft, damit es keine Kollisionen gibt, möchten die Leute dies auch auf der Maschine [Steuerung] tun, wenn sie können“, Ledvon sagte. „Wenn die Maschine ihnen visuell zeigen kann, ob sie ein Kollisionsproblem haben, wollen sie das 3D-Modell der Kinematik der Maschine sehen und das einfach doppelt überprüfen, wenn sie die Programmierung vornehmen – sie wollen diese Überprüfung immer noch auf dem Maschine.“
Die Simulation von Teilen auf der CNC-Steuerung wird immer häufiger, mit neuen CNC-basierten Simulationen, die auf der IMTS von FANUC und anderen vorgestellt wurden. Die Simulation von FANUC bietet laut Webster eine vollständige 3D-Teilsimulation, die den Festkörper des Teils zeigt, während es Bearbeitungsvorgängen unterzogen wird.
Die Verwendung von Volumenkörpermodellen wächst auch im Angebot von CNC-Entwicklern, bemerkte Hurco Cope. „Ein Trend, den sich einige Steuerungen allmählich zu eigen machen und den wir sicherlich wachsen sehen werden, ist die Möglichkeit, Volumenkörpermodelle direkt in die Steuerung zu importieren – und daraus Programme zu erstellen. Obwohl wir seit mehreren Jahren STL-Dateien zur Verwendung als Lagergeometrie importieren können, hat Hurco auf der IMTS 2018 eine neue Funktion eingeführt, den 3D-Import mit verbessertem 3D-DXF, die von den Messebesuchern sehr gut angenommen wurde“, fügte Cope hinzu. „Da viele Benutzer Solid-Modell-Dateien von ihren Kunden erhalten, ist es ein erheblicher Vorteil, diese Datei einfach in die Steuerung laden und ein Teileprogramm erstellen zu können, ohne dass ein CAM-System erforderlich ist.“
Was Maschinisten am wichtigsten ist

Benutzerfreundlichkeit steht ganz oben auf der Wunschliste der meisten Maschinisten, und CNC-Entwickler machen stetige Fortschritte in diesem Bereich, wobei FANUC seine Benutzeroberfläche in den letzten Jahren überarbeitet hat und viele andere Entwickler benutzerfreundlichere Touchscreen-Oberflächen hinzugefügt haben.
„Sie wollen Geschwindigkeit, wollen nicht warten und sie wollen Genauigkeit“, sagte Robin Cave, Software-Ingenieur bei der Mazak Corp. in Florence, Kentucky Code vor dem Schneiden beginnt mit einer ziemlich guten Simulation, die
alles zeigt.“
Mazaks CNC-Reihe Mazatrol Smooth, zu der SmoothX, SmoothG und SmoothC gehören, wurde vor etwa drei Jahren von Mazak in Japan mit Mitsubishi-Hardware und dem eingebetteten Betriebssystem Windows 8 überarbeitet. Diese CNCs bieten eine intuitive Bedienung für Benutzer mit Touchscreens, die es ermöglichen, einen Teilprozess zu optimieren, bemerkte Cave, indem sie Schieberegler und andere grafische Eingaben verwenden.
"Es ist eine schreiend schnelle Steuerung", sagte Cave von den Smooth CNCs und bemerkte, dass Georgia Tech die Steuerung getestet hat. „Es verarbeitet schneller als alles, was wir zuvor gemacht haben, und die Solid-State-Laufwerke tragen wirklich zur Geschwindigkeit bei. Sie brauchen nicht immer viel Geschwindigkeit, aber wenn Sie einen Schaftfräser mit Kugelkopf interpolieren, müssen Sie schnell viel Code fressen“, sagte Cave. „Auf solche Dinge trifft man eher in der Formenbau- und Luft- und Raumfahrtindustrie.
„Eine weitere wirklich große Sache bei unseren Kunden ist unser SMC – unsere reibungslose Maschinenkonfiguration“, fuhr Cave fort. „Die Kunden wollten, dass unsere Maschinen flexibler sind. Manchmal müssen sie wirklich genau sein, manchmal nicht.“ Die SMC ermöglicht es Maschinenbedienern, Schieberegler einfach einzustellen, um die Maschine je nach den Bearbeitungsbedingungen mehr oder weniger genau zu machen, bemerkte er, was dazu beiträgt, Programmieraufgaben auf der Maschine zu vereinfachen.
Eine Plattform für alles
Die Vielseitigkeit der Bearbeitung ist heute ein Schlüsseltrend für CNC-Anwender, bemerkte Todd Drane, Marketing Manager bei Fagor Automation-USA, Elk Grove Village, Illinois. „Hersteller wollen eine einzige CNC-Plattform, die jede Anwendung bewältigen kann, die sie in der Fertigung haben“, sagte Drane und merkte an, dass dies einen besseren Austausch des Werkstattpersonals ermögliche. „Sobald sie eine CNC-Plattform kennengelernt haben, ist die Integration in einen neuen Prozess für diese Person viel einfacher, wenn die Betriebsplattform mit dem neuen Prozess dieselbe bleibt.“
Zu den neuesten Entwicklungen gehört die CNC-Plattform 8065 von Fagor, die mit proprietären fortschrittlichen Funktionen ausgestattet ist, die für die Hochgeschwindigkeitsbearbeitung erforderlich sind, während gleichzeitig die beste Oberflächengüte und maximale Genauigkeit beibehalten werden, sagte Drane. Die Adaptive Real-Time Feed and Speed (ARFS)-Funktion von Fagor ermöglicht es der CNC, Bearbeitungsbedingungen wie Spindellast, Servoleistung und Werkzeugspitzentemperatur zu analysieren und sowohl den Achsvorschub als auch die Spindeldrehzahl für eine maximale Produktivität der Bearbeitungsleistung anzupassen, fügte Drane hinzu . „Das Ergebnis ist eine Reduzierung der Zykluszeit, gepaart mit einer hervorragenden Oberflächengüte. Eine verlängerte Spindel- und Servomotorlebensdauer wird ebenso erreicht wie eine verbesserte Werkzeugnutzung.“
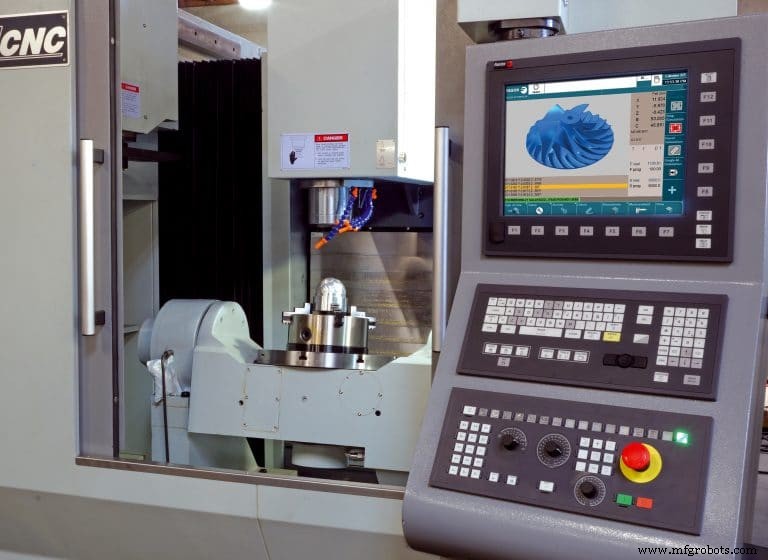
Die Fagor 8065 CNC ist außerdem mit der luft- und raumfahrtspezifischen High Speed Surface Accuracy (HSSA)-Bearbeitungsfunktion ausgestattet, die die mechanische Belastung der Maschine reduziert und die Lebensdauer der Werkzeugmaschinen verlängert. Aufgrund der geringeren Maschinenvibration ist die Maschine außerdem in der Lage, sich gleichmäßiger zu bewegen und höhere Vorschubgeschwindigkeiten zu erzielen, sagte Drane. „Darüber hinaus ermöglicht das integrierte Bode-Diagramm-Tool die Messung des Frequenzgangs der Maschine und bietet so die Möglichkeit, die durch die verschiedenen Betriebsbedingungen und Umgebungen erzeugten Maschinenvibrationen tatsächlich zu filtern.“
Fagor bietet auch seine Anwendung Fagor Machining Calculator (FMC) an, die sowohl auf den CNC-Plattformen 8060 als auch 8065 verfügbar ist. Die Funktion besteht aus einer Datenbank mit zu bearbeitenden Materialien und Bearbeitungsvorgängen (Fräsen und Drehen) und einer Schnittstelle zur Auswahl geeigneter Schnittbedingungen (Achsen-Bearbeitungsvorschubgeschwindigkeit und Spindeldrehzahl für jeden Vorgang). Ein weiterer Fortschritt bei Fagor-CNCs ist das kompakte Hardwaredesign der Steuerungslinie, sagte Drane. „In der heutigen Fertigung ist, wie ein Kunde feststellte, Platz Geld“, bemerkte er. „Daher hat Fagor nicht nur kompakte CNCs entwickelt, sondern auch kompakte Antriebe und sogar Motoren. Die Idee ist, schlanke Lösungen bereitzustellen, die den Anforderungen entsprechen, im Gegensatz zu einem Cookie-Cutter-Ansatz.“
Automatisierungssteuerung System
- CNC-Drehmaschine verbessert die Produktivität
- Roboter-Programmiertool reduziert Kalibrierungsprobleme
- Modellierungssoftware vereinfacht die Roboterprogrammierung
- CNC-Softwarefunktionen Dialogprogrammierung
- CNC-Programmierbeispiel mit Fanuc G71 Schruppdrehzyklus und G70
- Sinumerik 840D CNC-Programmierung
- CNC-Programmierung für CNC-Maschinisten
- CNC G01 Winkelprogrammierung
- M-Codes – CNC-Programmierquiz
- G-Codes – CNC-Programmierquiz