Die Vorteile vertikaler Bearbeitungszentren
Die Anbieter vertikaler Bearbeitungszentren blicken optimistisch auf das Jahr 2022. Sie erwarten einen verstärkten Einsatz von Automatisierung und ein gesteigertes Bewusstsein für die Vorteile der Bearbeitung mit mehr als dreiachsiger Ausrüstung.
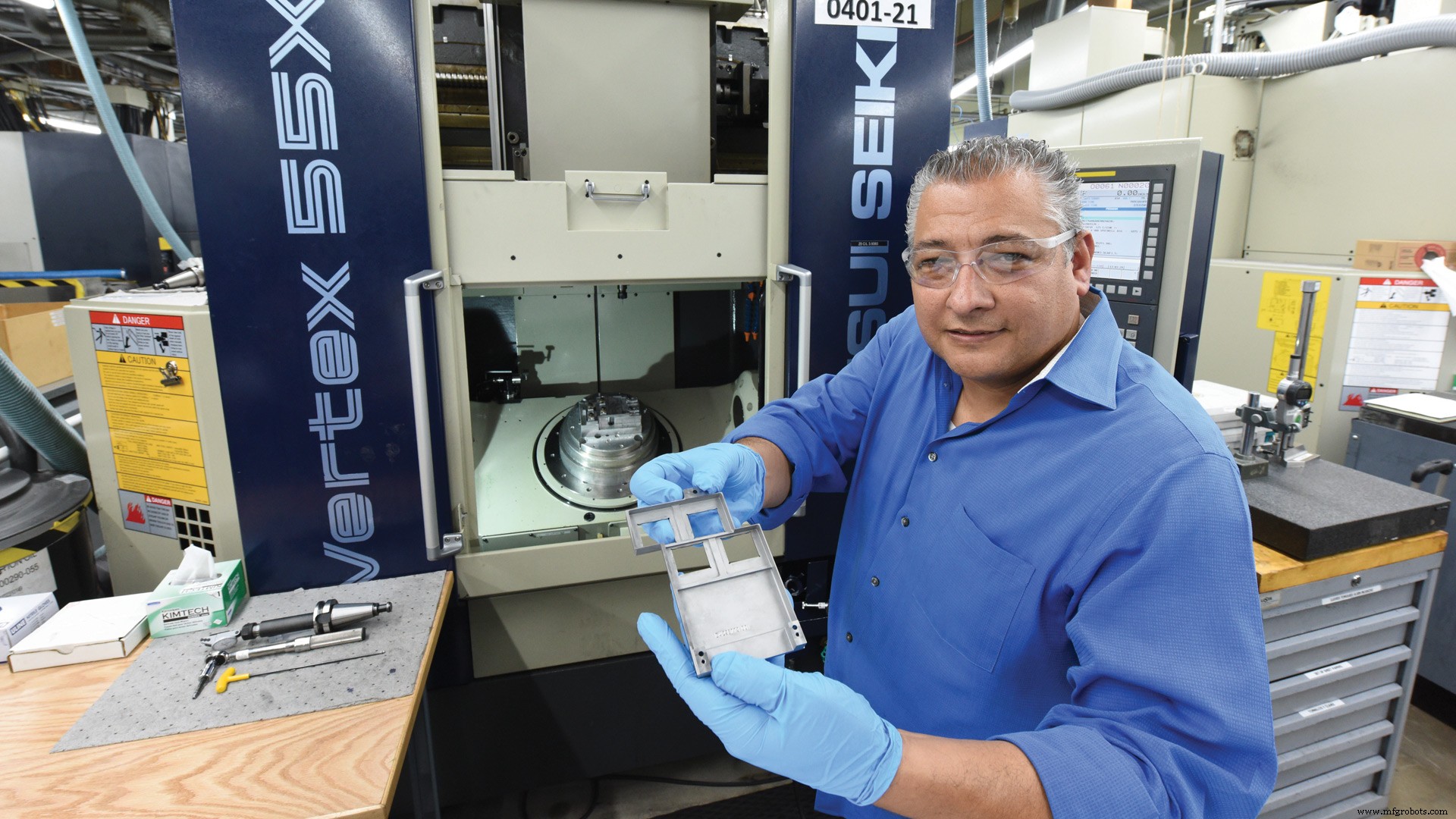
Das Erreichen mehrerer Seiten eines Werkstücks in einer oder zwei Aufspannungen ist laut Gerätehersteller nur ein Teil des Wertversprechens von VMCs. Die Automatisierung mit einem Roboter vor der Maschine oder das Hinzufügen einer Drehachse trägt zur Gewährleistung der Produktivität bei, während ein Verständnis der Maschinenkinematik – wie sich die Maschine im Laufe der Zeit bewegt – der Schlüssel zur Reproduzierbarkeit ist.
Eine breite Palette von Auswahlmöglichkeiten, von einfacheren dreiachsigen Maschinen bis hin zu fünfachsigen Maschinen – sowohl 3 plus 2 als auch in geringerem Umfang kontinuierliche Versionen – bietet Werkstätten eine Fülle von Möglichkeiten, VMCs bei kleinen und hohen Stückzahlen einzusetzen . Und Möglichkeiten zur Herstellung von Reshore-Teilen bieten einen weiteren Anreiz.
VMC-Geschäft ist gut
Zunächst einmal ist die Nachfrage nach VMCs trotz der Unsicherheit und der konfusen Politik im Zusammenhang mit der COVID-19-Pandemie, die sich in ein drittes Jahr des Tumults zieht, stark. Die Versorgung ist jedoch wenig überraschend ein Problem.
„Die Branche ist ziemlich heiß“, versicherte Jeff Wallace, General Manager, National Engineering bei DMG Mori USA in Hoffman Estates, Illinois. „Wir verkaufen alles, was nicht festgeschraubt ist. Wir verkaufen Sachen, die verschraubt sind. Das gute Problem ist, dass wir alles verkaufen, was wir haben; Das schlimme Problem ist, dass sich die Vorlaufzeiten von vier bis sechs Wochen auf vier bis sechs Monate verlängert haben.“
VMCs sind in mehreren Anwendungen beliebt, sagte Wallace, sogar bei „einigen Produktionszentren mit geringem Volumen, in denen wir einige vereinfachte prismatische Teile herstellen. Auch die vertikalen Dreiachsmaschinen sind sehr gefragt.“
Angesichts des durch die Pandemie noch verschärften Arbeitskräftemangels ist die Automatisierung von VMCs zu einem Hauptanliegen geworden.
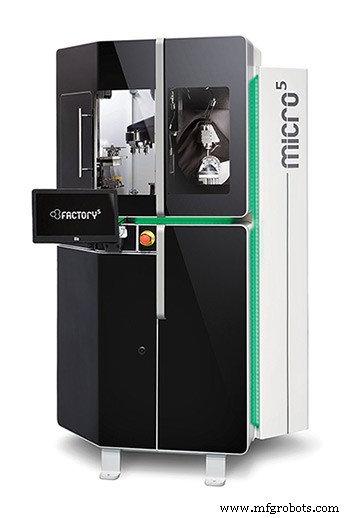
„Häufig sehen wir bei den Vertikalen, dass wir eine Drehachse nachrüsten könnten, um mehr als eine Seite des Bauteils zu erreichen. Kunden möchten so viel wie möglich automatisieren – sogar einige der vertikalen Drei-Achsen-Bearbeitungszentren automatisieren. Hinzufügen einer Rotationsachse oder sogar einer doppelten Rotationsachse, um das Teil umdrehen und auf die andere Seite bringen zu können, damit wir es nicht aus einem Schraubstock brechen und in einen anderen Schraubstock bringen müssen – egal ob in dieser oder einer anderen Maschine Maschine – ist derzeit sehr beliebt. Kunden prüfen, wie sie diese VMCs optimieren und mehr Produktivität aus ihnen herausholen können.
„Das Schöne an den VMCs ist, dass sie relativ kostengünstig und einfach einzurichten sind. Sie lassen sie auf den Boden fallen und die meisten haben ein Dreipunkt-Nivellierungssystem. Für einen Kunden ist der Einstieg in ein VMC, insbesondere für Kleinauflagen, sehr kostengünstig. Die Nachfrage nach fast allen unseren Produkten ist auf breiter Front hoch – und das ist gut für die Branche. Wir sind nicht die Einzigen; Alle anderen Bauherren sehen ähnliche Bedingungen. Der Kuchen ist ziemlich groß und ich bin froh, dass die Branche gesund ist.“
Mithilfe seines ROI-Rechners hilft DMG Mori dabei, zu veranschaulichen, wie seine VMCs den Geschäften helfen können, ihr Endergebnis zu verbessern – insbesondere „bei all den laufenden Reshorings. Wir sehen, dass viele Produkte in die USA zurückkehren – kostengünstige, prismatische Teile, die wir in den letzten 20 Jahren auf der anderen Seite des Meeres gekauft haben. Kleine bis mittelgroße Betriebe sind bei der Herstellung dieser Standardkomponenten sehr effizient geworden – Dinge, für die ein VMC sehr gut geeignet ist.
„Der Haken an der Sache ist die Manpower und ob man automatisieren will:Steckt man einen einfachen Roboter vor die Maschine oder setzt man die Drehachse auf? Wir haben eine DMG Mori-interne Automatisierungsgruppe, und die Cobots beginnen, auf diesen VMC-Plattformen abzuheben. Wir müssen der Tür nicht einmal etwas so Einfaches wie einen Luftzylinder hinzufügen; wir lassen den Roboter die Tür öffnen.“ Durch diese Schritte, so Wallace, sehen die Kunden Produktionssteigerungen von fünf bis sechs Prozent.
Mehrachsige VMCs setzen sich in den USA immer mehr durch, schloss er – sie explodierten tatsächlich, da DMG Mori in den letzten Jahren eine Verzehnfachung der Verkäufe verzeichnete. Europa hatte anfangs den Vorteil bei der Einführung, sagte er, aber „in typisch amerikanischer Manier, sobald wir aufwachen, ist es wie ‚OK, aus dem Weg‘. Amerika ist aufgewacht, wiederum hauptsächlich getrieben von den Personalproblemen. Da die Leute die Arbeit nicht machen wollen oder wir keine Talente finden können, wie minimieren Sie diese Interaktion mit der Maschine, um ein Teil herzustellen? Hier glänzt der Multiaxis. Wenn ich meinen Riegel richtig vorbereiten kann, muss ich diesen Teil vielleicht nie wieder anfassen, bis er fertig ist.“
Die Automatisierung wird durch die Celos-Mensch-Maschine-Schnittstellensteuerung des Unternehmens erleichtert, die es Maschinenbedienern ermöglicht, eine Reihe von Robotern schnell zu manipulieren, um verschiedene Aufgaben auszuführen. „Wir haben Anwendungen entwickelt, bei denen, wenn man einen Roboter vor einer Maschine absetzt, der Bediener kein Roboterprogrammierer sein muss. Es gibt eine grafische Drag-and-Drop-Benutzeroberfläche, die dem Bediener beim Programmieren hilft. Unser Ziel ist es, diese Technologie in die Hände der Menschen zu bringen, damit sie der Automatisierung nicht so skeptisch gegenüberstehen, sondern sich damit wohlfühlen.“
Der VMC-Vorteil
VMCs sind im Allgemeinen einfacher zu installieren, „sind in der Regel in kürzerer Zeit einsatzbereit und bieten weniger Unterbrechungen im Tagesgeschäft“, erklärte Bill Malanche, COO von Mitsui Seiki. „Sie sind in der Regel auch kleiner als viele horizontale Maschinen, wodurch die Gesamtnutzung wertvoller Werksfläche reduziert wird. Das Design unserer Maschinen gibt Werkstätten und großen Fabriken mehr Möglichkeiten auf einer kleineren Plattform. In unserer Vertex-Linie von VMCs bietet die Y-Achse einen größeren Hub als die X-Achse, wodurch die Gesamtbreite der Maschine kleiner wird. Die meisten VMCs sind typischerweise breiter als tief.“
Im Laufe seiner Karriere, erinnert sich Malanche, installierte er Dutzende vertikaler Maschinen in Unternehmen in den USA und im Ausland. „Bis heute treffe ich noch gelegentlich auf einer Messe einen Kunden, der sich daran erinnert, dass ich seine Maschine installiert habe, und sagt, dass er sie immer noch hat und sie noch ein paar Zehntel hält.“
Mitsui Seiki legt Wert auf Maschinen im Jig-Bore-Stil, die für ultrahohe Präzision in einem engen Arbeitsraum ausgelegt sind, bemerkte er, was sie ideal für die Produktion von hohen Dollars und geringen Stückzahlen macht.
„Wir haben einen Kunden, der komplizierte Komponenten für die Luft- und Raumfahrt herstellt, die extrem enge Toleranzen erfordern“, erklärte Malanche. „Die von ihnen verwendeten vertikalen Maschinen produzieren eine Familie von Teilen, die nicht nur für die Produktion, sondern auch für den laufenden Außendienst konzipiert sind. Diese Umgebung bedeutet, dass die Maschinen eines Tages für die Produktion von Teilen verwendet werden könnten, aber unerwarteterweise gezwungen sein könnten, ausgetauscht zu werden, um die Anforderungen des Außendiensts auszugleichen.
„Dieser Kunde hat qualifizierte Maschinisten, die die Teile herstellen, aber das Arbeitsniveau ist nicht geeignet, um einfach den ‚Zyklusstart‘ zu erreichen; Die Werkstücke haben zahlreiche integrierte Bohrungen und Prozesskontrollen, die während der Produktion der Teile durchgeführt werden müssen.“ Dieser Kunde begann mit fünf Mitsui Seiki VMCs und hat jetzt 16 in Betrieb.
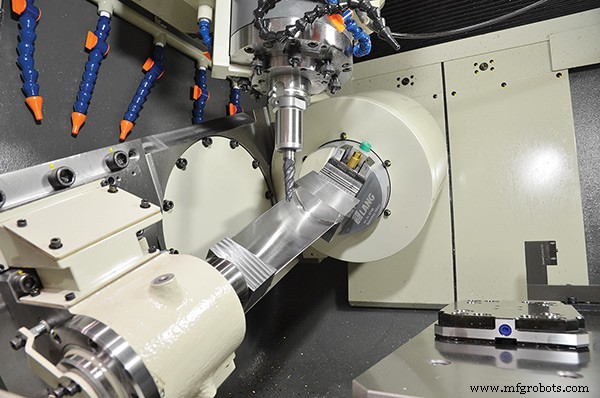
In Fällen, in denen Teile von Maschinen zur „In-Prozess“-KMG-Inspektion kommen müssen, um von Betrieb zu Betrieb zu gehen, sagte Malanche:„Wir haben dem Kunden geholfen, die Prozesse halb zu automatisieren, wobei er die Maschinen mit einer ‚Nullpunkt‘-Vorrichtungsbasis ausstatten konnte Platten, um zu ermöglichen, dass die gleichen Teile von Maschine zu Maschine und zum CMM mit minimalem Rüst- und Verifizierungsaufwand übertragen werden können.“
Manchmal können eher kleine optionale Verbesserungen an Basislinien-VMCs vorgenommen werden, um die Automatisierung zu unterstützen. Elemente wie Werkzeugmesstaster und Spindelmesstaster können verwendet werden, um Umrüstungen zu beschleunigen, und die Integration von hochgradig wiederholbaren Nullpunkt-Basisplatten kann die Vielseitigkeit erhöhen.
„Aber ich denke, der größte Vorteil liegt darin, Maschinen zu haben, die für die Fünf-Achs-Bearbeitung ausgestattet sind“, versichert Malanche. „Obwohl das Hinzufügen einer fünften Achse zu den meisten VMCs im Allgemeinen kostspielig ist, lohnt sich die Investition und zahlt sich bei kritischen Anwendungen manchmal schnell aus. Die Einführung hochpräziser fünfachsiger Drehtische, die in die Maschinenstruktur integriert sind, bietet Herstellern den Vorteil einer noch größeren Vielseitigkeit im Prozessablauf.“
Mitsui Seiki habe seine VMC-Plattformen so konzipiert, dass sie viele einzigartige Fertigungsherausforderungen bewältigen, fuhr er fort. Die grundlegende fünfachsige Vertex-Serie des Unternehmens wird in drei Größen angeboten, um Teile mit einem Durchmesser von 500 mm bis 1200 mm zu handhaben. „Wir haben sie mit Anpassungen gebaut, die darauf abzielen, viele Fertigungsherausforderungen und neue Methoden zu bewältigen. Unsere Maschinen sind nicht auf einer gemeinsamen Plattform mit verlängerten Kugelumlaufspindeln für größere Hübe aufgebaut; Diese sind auf einzelnen Eisengussteilen aufgebaut, die für jahrelangen Einsatz und Lebensdauer ausgelegt sind. Unsere kleinste Version, die Vertex 550-5X mit einem 400-mm-Drehtisch, wiegt 20.000 Pfund und die Vertex 100X ist dreimal so viel. Dies sind keine ‚Wegwerf‘-VMC-Maschinen.“
Vertex-Maschinen werden mit Optionen wie Drehachsenmotoren mit Direktantrieb gebaut, die für eine verbesserte Kontursteuerung auf dem Airfoil-Markt benötigt werden, fügte er hinzu. „Wir verfügen über kombinierte Plattformmaschinen, die für Multiprozessfähigkeiten wie additive/subtraktive Metallabscheidung, Fräsen und Schleifen und den Hochgeschwindigkeits-Elektroerosionsprozess namens Blue Arc ausgelegt sind, der von General Electric lizenziert wird.“ Mit diesen Optionen können Benutzer Materialien wie Keramik, Graphit, Aluminium, Titan, Inconel und mehr schneiden.
Diese Art von Flexibilität hilft VMCs dabei, ihren Platz auf dem Markt wieder zu behaupten, wo im Laufe der Jahre die Anforderungen einer höheren Produktion in Verbindung mit reduzierten Arbeitskapazitäten den HMCs Platz gemacht haben. „In einem scheinbar relativ kurzen Zeitraum trat der Bedarf an VMCs gegenüber HMCs mit größeren Werkzeugwechslern, Palettenwechslern und vollwertigen flexiblen Fertigungssystemen in den Hintergrund“, sagte Malanche. „Vor 30 Jahren verließen sich die meisten Betriebe mit mittlerer bis mittlerer Produktion aus zahlreichen Gründen stark auf VMCs, darunter Einrichtungszeitpunkt, leichter Zugang, einfache Wartung, Verfügbarkeit von Facharbeitern und Produktmix. VMCs haben auf dem Markt für hochpräzise Teilefertigung neues Leben eingehaucht.“
Maschinen in Bewegung
Das kritische Konzept der Kinematik, oder wie sich eine Maschine bewegt, betont YCM Technology USA in Carson, Kalifornien, mit seiner integrierten Kinematikkalibrierung für den nordamerikanischen Markt. Diese Pakete – mit Messtastern, Werkzeuglängenmessung und Werkzeugkugeln – werden Standard bei YMCs 3-plus-2- oder kontinuierlichen Fünf-Achsen-Maschinen sein, sagte Brian Huff, Business Development Manager für den Mittleren Westen.
Wenn eine Maschine ihre Funktionen ausführt, kann sich die Genauigkeit ändern, bemerkte Huff, und „es ist üblich, dass ein Bediener denkt, dass die Maschine nicht genau ist oder der Aufnehmer nicht genau war.“ Um dies anzugehen, müssen Drehzentren für die vierte und fünfte Achse definiert und kalibriert werden können. Früher hätten Hersteller das Rotationszentrum als Teil der Maschineninstallation festlegen können, sagte er. „Wenn der Kunde mit der Genauigkeit zu kämpfen hat, wäre ein Serviceanruf erforderlich, und er kommt zurück, um diese Rotationszentren neu zu definieren – was kostspielig sein kann. Dinge passieren, Maschinen bewegen sich, das Gewicht des Werkstücks ändert sich – und andere Dynamiken spielen eine Rolle. Einige Hersteller haben die Bedeutung der Kinematikkalibrierung bereitwilliger angenommen. Daher ist es unser Interesse, es unseren Benutzern und Betreibern leicht zu machen; Es ist kein Serviceeinsatz erforderlich, und Sie haben die Maschine auf höchstem Genauigkeitsniveau.“
Wie oft sollten VMCs kalibriert werden? Huff riet, je nach Anwendung einmal pro Woche, einmal im Monat oder sogar täglich.
„Wir sagen unseren Kunden, dass Sie das Kinematikprogramm ausführen sollten, wenn Sie kritischere Arbeiten haben und mehr Abweichungen bemerken. Wenn Sie Arbeiten mit engen Toleranzen ausführen, führen Sie die Kinematik aus; Führen Sie es vor dem Job aus, führen Sie es täglich aus, um sicherzugehen. Wenn Sie im Laufe einer Woche eine Abweichung von 0,0005 Zoll sehen, lassen Sie es vielleicht wöchentlich laufen.“ Das entspricht 0,0127 mm.
Im Idealfall möchte Huff „Kinematik zu einem normalen Gespräch machen“ und versuchen, die Lücke zwischen den Unternehmen zu schließen, die Rotationszentren bei der Installation definieren, und denjenigen, die der Meinung sind, dass die Kinematikkalibrierung leicht zugänglich und schnell ausgeführt werden sollte. „Es wird zu einer Lebensart für alle Hersteller.“
Ein weiterer Weg, wie YCM die Genauigkeit angeht, ist die Partnerschaft mit Kessler, dessen Spindeln und Köpfe auf YCM-Vertikalmaschinen erscheinen, um die Klemmkraft für die A- und C- oder B- und C-Achsen zu adressieren und die Steifigkeit an der Spitze des Schneidwerkzeugs aufrechtzuerhalten. „Unsere Standardspindel auf unserer 5-Achs-Doppelständer-Werkzeugmaschine leistet maximal 54 PS“, sagt Huff, oder 40,2 kW. „Es ist ein HSK 100 mit 16.000 U/min, der bei 2.500 U/min die volle Leistung bringt. Hohe Steifigkeit, Drehmoment, Drehzahl und Leistung sorgen für eine wirklich vielseitige Spindel- und Kopfkonfiguration. Unsere Luft- und Raumfahrtversion erreicht bis zu 18.000 U/min, mit einer HSK 63-Spindel, die 94 PS [70 kW] produziert und für die Aluminiumbearbeitung bestimmt ist.“ Darüber hinaus bietet die Partnerschaft mit Kessler YCM eine Ressource im Mittleren Westen für Spindelreparaturen.
Besonderes Augenmerk legt YCM Technology auf seine Fünf-Achs-Maschinen. Während 3-plus-2-Konfigurationen beliebter sind, wächst die Nachfrage nach vollen fünf Achsen, stellte Huff fest. Auch er sieht eine Zunahme der Anfragen nach Automatisierung.
„Wir sehen immer wieder Anfragen nach Automatisierung als Teil des Maschinenpakets. Es ist nicht nur Palettierung; Wir sehen mehr Akzeptanz und Interesse für die Pick-and-Place-Automatisierung. Es ist eine natürliche Ergänzung zu Fünfachsen, da Sie in vielen Fällen in einer oder zwei Aufspannungen das gesamte Werkstück komplett bearbeiten können. Die Werkstückhaltung in diesem Fall ist entscheidend, und es dürfen keine Beeinträchtigungen durch Vorrichtungen oder Klemmen im Weg des Schneidwerkzeugs auftreten. Wenn Sie ein Werkstück von der Unterseite halten können und fünf Seiten zugänglich sind, ist das ideal. Für die Werkstückspannung von unten gibt es Hersteller, die Systeme entwickelt haben, die hervorragende Arbeit leisten; Wir arbeiten derzeit mit Unternehmen zusammen, die diese Art von Lösungen anbieten. Außerdem bieten wir palettierte Automatisierungspakete mit den YCM-Maschinen an und entwickeln kollaborative und Pick-and-Place-Automatisierungspakete weiter.“
Anstreben einer hohen Produktion
In den letzten zwei bis drei Jahren waren die meisten VMC-Rollouts von Chiron robuste Produktionsplattformen für hohe Stückzahlen, die darauf ausgelegt sind, die Bearbeitungsanforderungen großer Automobil- und Luft- und Raumfahrtkomponenten zu erfüllen, sagte Business Development Manager Simon Knecht von Chiron America in Charlotte, N.C. P>
„Mit diesen erfolgreich etablierten und für unsere nordamerikanischen Kunden weithin verfügbaren Bearbeitungszentren stärken wir unser Produktportfolio am anderen Ende des Fertigungsspektrums weiter:hochpräzise, mikrobearbeitete Komponenten“, sagte Knecht.
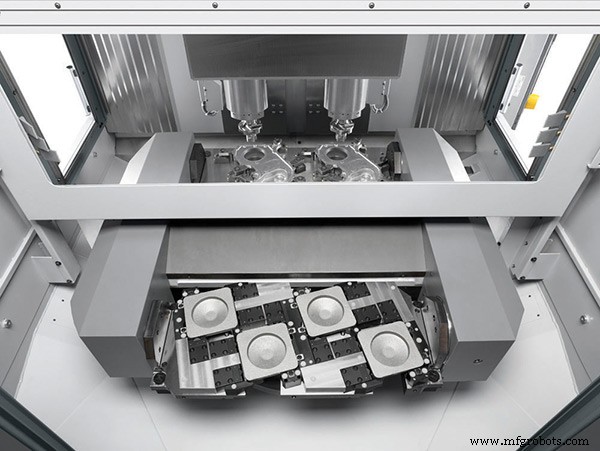
Dieses Jahr bringt Chiron sein in der Schweiz entwickeltes Bearbeitungszentrum Micro5 auf den Markt, das für kleine Werkstücke im Bereich von 50 × 50 × 50 mm ausgelegt ist, sagte er. „Die Geschwindigkeit und Dynamik dieses Bearbeitungskonzepts sind darauf ausgelegt, Kunden mit gesteigerter Produktivität zu unterstützen. Neben den Maßstäben hoher Geschwindigkeit und minimaler bewegter Masse ist die Maschine eine modulare Plattform und kann mit integrierter Automatisierung ausgestattet werden. Darüber hinaus wurde der Micro5 für eine flexible Skalierbarkeit entwickelt, die Herstellern die Möglichkeit gibt, nahtlose Produktionslinien mit mehreren Maschinen zu erstellen.“
VMCs basieren im Allgemeinen auf einem modularen Konzept, erklärte er; Es ist üblich, von der vierten auf die fünfte Achse zu wechseln. „Oft haben unsere Kunden die Maschinenkonfiguration auf eine andere Tischeinstellung geändert, indem sie die vierte oder fünfte Achse auf dem Tisch verwendet haben.“
Wie andere Anbieter adressiert Chiron America die Lücke bei den Bedienerqualifikationen. Intelligente Automatisierung „ist ein Teil einer Lösung, die den Durchsatz während der geplanten Produktionszeiten sicherstellt“, sagte Knecht. „Automatisierungstechnologien, insbesondere Roboter, haben in der Regel eine hohe technische Verfügbarkeit und laufen mit hoher Zuverlässigkeit. Mit Prozessen und Zellen, die für kleinere Chargen ausgelegt sind, sind unsere Automatisierungslösungen sogar in der Lage, Vorrichtungen in der Maschine zu wechseln. Im Gegensatz zu einer manuellen Einrichtung, die oft mehr als eine Stunde dauern kann, um die Vorrichtungen zu wechseln, verbessert die Automatisierung des VMC mit einem Nullspannsystem den Durchsatz und bringt die Maschine zurück zu dem, wofür sie ausgelegt ist:Bearbeitung. Unsere Maschinentisch-Achsenkonfigurationen sind für diese Spannmethoden ausgelegt.“
Trends wie die Verlagerung hin zur E-Mobilität und durch Pandemien belastete Lieferketten fordern mehr Flexibilität von der Ausrüstung – was VMC zur Reduzierung der Einrichtung zu einem entscheidenden Werkzeug macht. „Die Möglichkeit, schnell zu einem anderen Werkstück auf einer Maschine zu wechseln, treibt den Ansatz voran, die Anzahl der Aufspannungen zu reduzieren und so viele Operationen wie möglich innerhalb derselben Maschine fertigzustellen“, sagte Knecht. Der integrierte Werkstückwechsel von Chiron ermöglichte das Be- und Entladen von Teilen, während die fünfachsigen VMCs laufen.
Die Nutzung dieser Flexibilität und der Einsatz eines VMC für viele verschiedene Werkstücke „wird zu greifbaren Vorteilen in Bezug auf den ROI führen“, schloss Knecht. „Zu oft habe ich spezielle Maschinen und Anlagen gesehen, die nach dem Verlust eines Auftrags oder Projekts stillstehen, während der Hersteller die Maschine nicht voll ausnutzen kann.“
Automatisierungssteuerung System
- Die verschiedenen Präzisionsbearbeitungstechnologien
- CNC-Bearbeitung in der Automobilindustrie
- Verbesserung der Bearbeitbarkeit von Aluminium
- Die Bedeutung der schnellen Bearbeitung in der Fertigung
- VMCs, Drehmaschinen werden ausgestellt
- Die Grundlagen eines vertikalen Bearbeitungszentrums (VMC)
- Die 3 Vorteile vertikaler Bearbeitungszentren
- Alles über VMCs (vertikale Bearbeitungszentren)
- Die Kosten der CNC-Bearbeitung
- Die Wirtschaftlichkeit der Metallbearbeitung