Erzielung besserer Ergebnisse bei der additiven Fertigung im generativen Design
Lesen Sie diesen Artikel in:English (English)
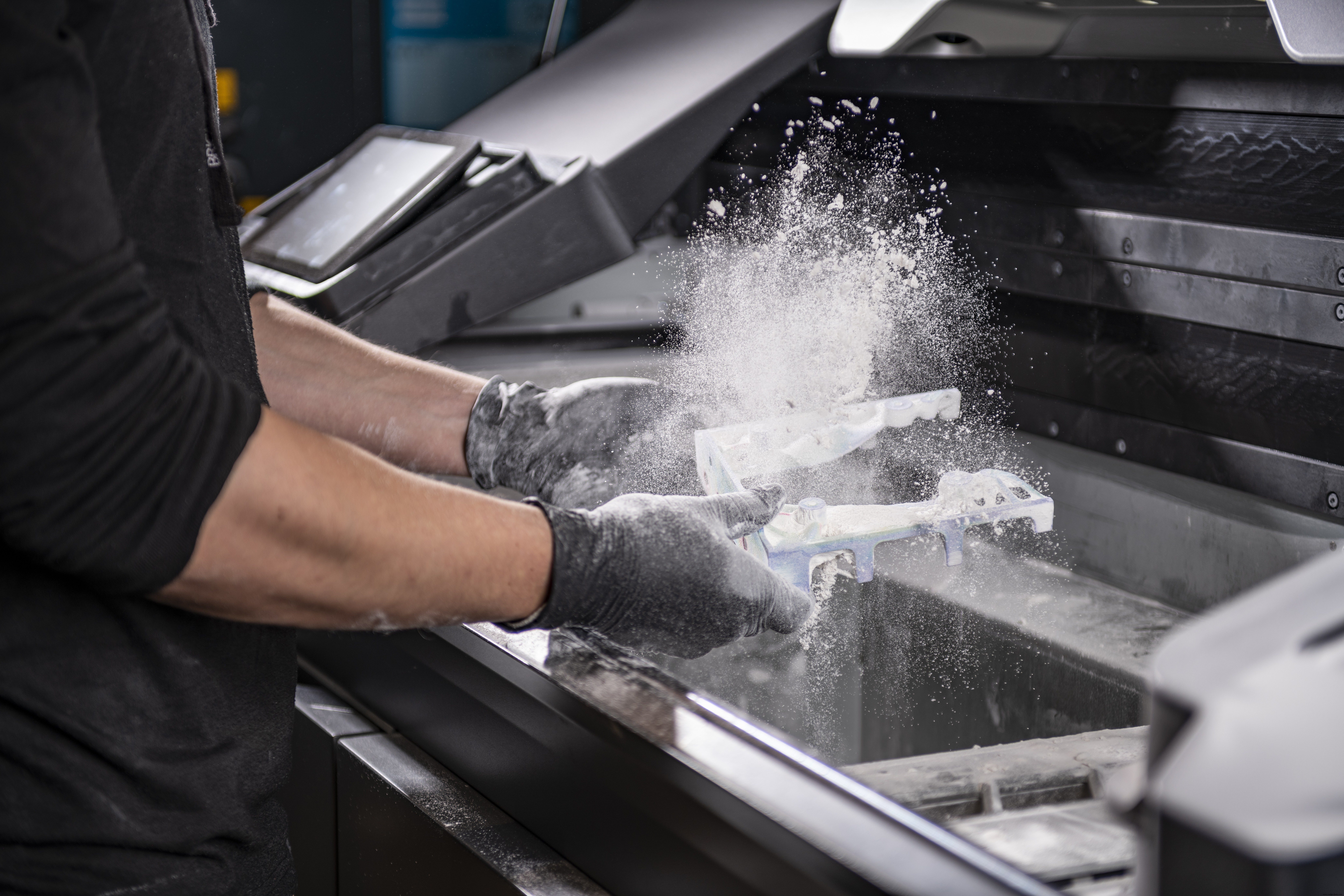
Als Teil des Fusion 360-Updates vom Dezember 2020 haben wir pünktlich zu den Feiertagen ein verstecktes Geschenk geliefert:eine neue Methode zur Generierung von Ergebnissen aus der additiven Fertigung. Intern nennen wir dieses Projekt Additive 2.0, und es ist Teil unserer Vorschau auf Experimental Generative Solvers and Features. Diese neue Methode sollte die Formqualität und Druckbarkeit der Ergebnisse im Vergleich zu dem, was Sie bisher im generativen Design gesehen haben, erheblich verbessern. Dies war ein Geschenk, auf das viele von uns sehnsüchtig gewartet haben, und mein Team und ich würden gerne alles „auspacken“, was wir geliefert haben.
Verwenden des neuen Additive 2.0-Algorithmus
Zunächst einmal müssen Sie die Vorschau unserer experimentellen generativen Solver und Funktionen in Ihren Benutzereinstellungen aktivieren.
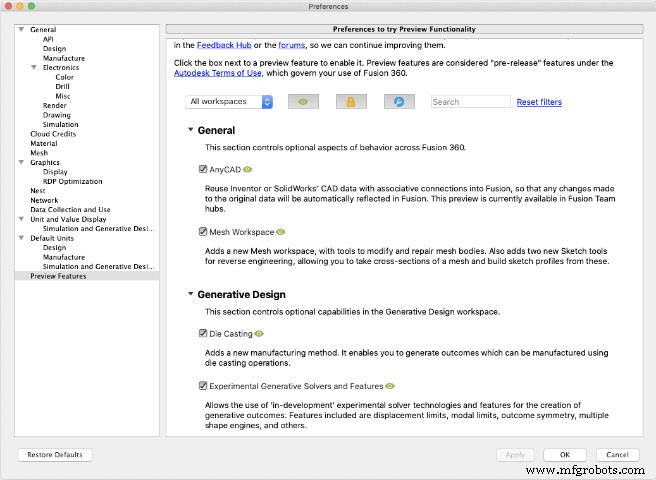
Wenn die Vorschau aktiviert ist, müssen Sie Alternative Ergebnisse in den Studieneinstellungen aktivieren. Richten Sie von dort aus Ihr Arbeitszimmer wie gewohnt ein. Aktivieren Sie die Einschränkung für die additive Fertigung im Dialogfeld "Fertigungseinschränkungen", wählen Sie die gewünschten Druckausrichtungen aus und lassen Sie unsere Solver den Rest erledigen.
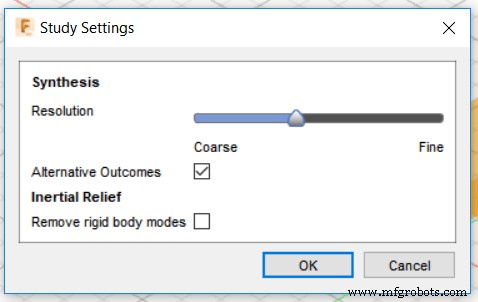
Einmal in Explore generiert Additive 2.0 für jeden Satz additiver Ergebnisse (wobei ein Satz einem gegebenen Material und einer gegebenen Richtung entspricht) das zweite Ergebnis in jedem Satz. Kurzer Tipp:Der einfachste Weg, dies zu sehen, besteht darin, zur Eigenschaftenansicht zu wechseln, bis zur additiven Fertigungsmethode zu isolieren und das Dropdown-Menü „Sortieren nach“ auf „Material“ einzustellen.
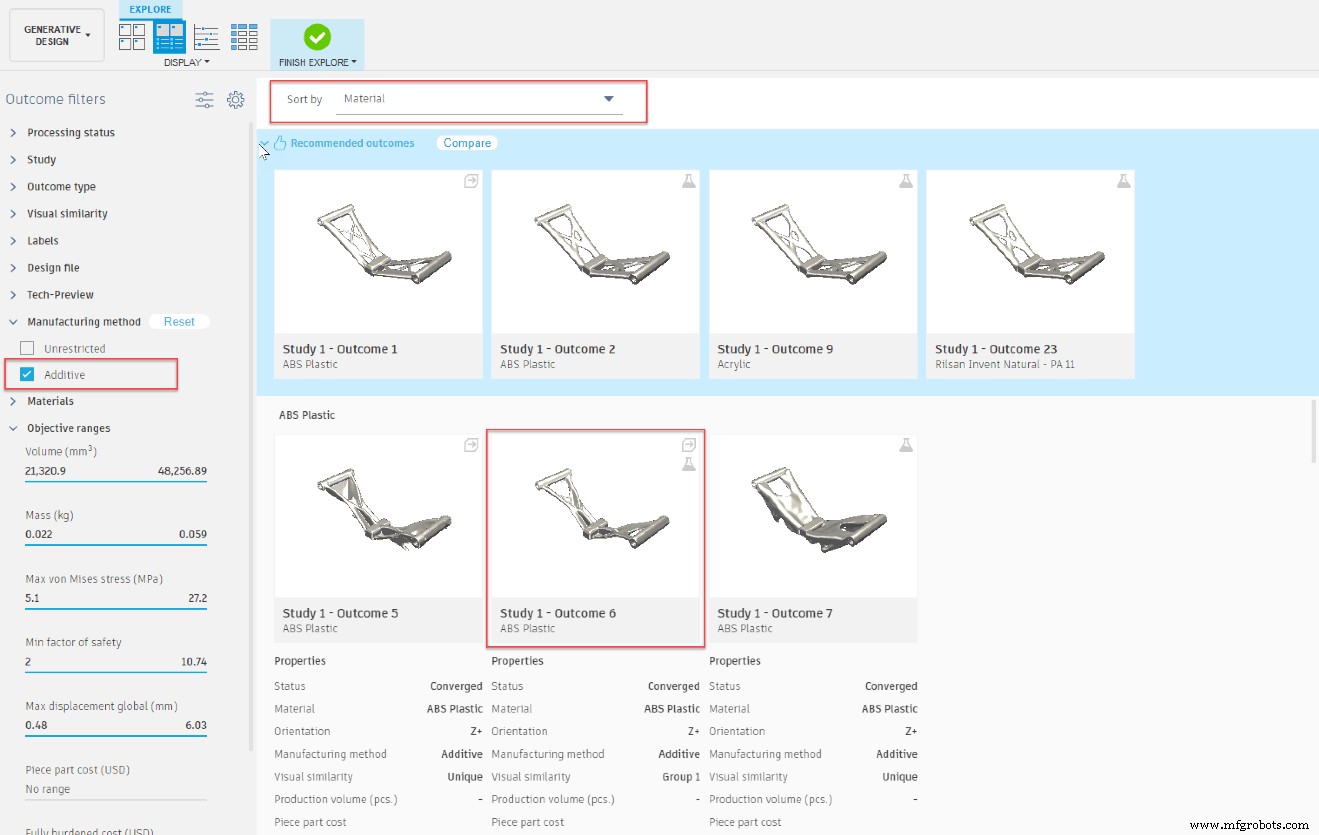
Wie ist Additiv 2.0 besser?
Unser anfänglicher Ansatz zur Generierung additiver Ergebnisse ließ in vielen Szenarien in Bezug auf die Formqualität zu wünschen übrig (viele von Ihnen haben uns das gesagt, und wir haben zugehört!). Es war üblich, Ergebnisse mit ausgeprägtem Treppensteigen und anderen Artefakten zu sehen, als wir versuchten, die Überhanganforderungen zu erfüllen und vollständig selbsttragend zu sein. Mit unserem neuen Ansatz können unsere Solver die Anforderungen an die Mindestdicke viel besser erfüllen, die Konstruktionsmasse ausgleichen und das Stützmaterial minimieren. Dieser neue Ansatz wird die Formqualität nicht opfern, um vollständig selbsttragend zu sein.
Sehen wir uns einige Beispiele an, die zeigen, wie sich diese Verbesserungen auf die von uns erzielten Ergebnisse auswirken.
Unser erstes Beispiel ist der unten gezeigte einfache generative Aufbau (Lasten und Randbedingungen sind ausgeblendet). Wir beabsichtigen, dieses Teil in der in Abbildung 1 (unten) gezeigten Ausrichtung herzustellen und das rote Hindernis durch die Bauplatte zu ersetzen.
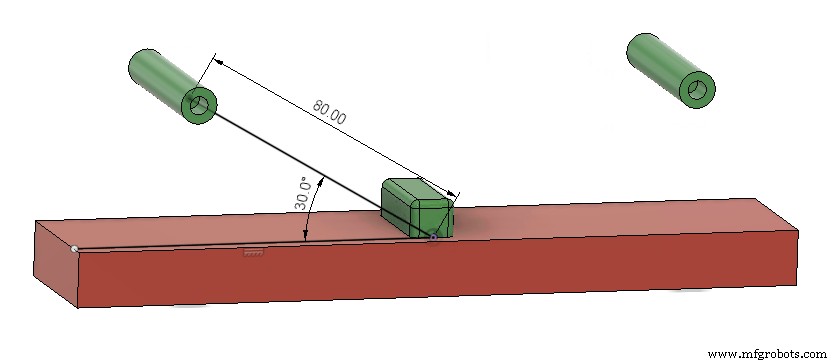
Dieser Aufbau erzeugt ein uneingeschränktes Ergebnis, wie in Abbildung 2 (unten) zu sehen, das aus verschiedenen Gründen schwierig herzustellen ist. Erstens erfordert eine große Fläche unter der Teilegeometrie Stützstrukturen (rot hervorgehobene Bereiche in der zweiten Hälfte der Abbildung). Außerdem sind die dünnen Merkmale in der Nähe der Mitte des Teils zerbrechlich und können beim Entfernen der Stütze brechen. Obwohl dieses Design additiv hergestellt werden kann, ist es noch lange nicht optimiert.
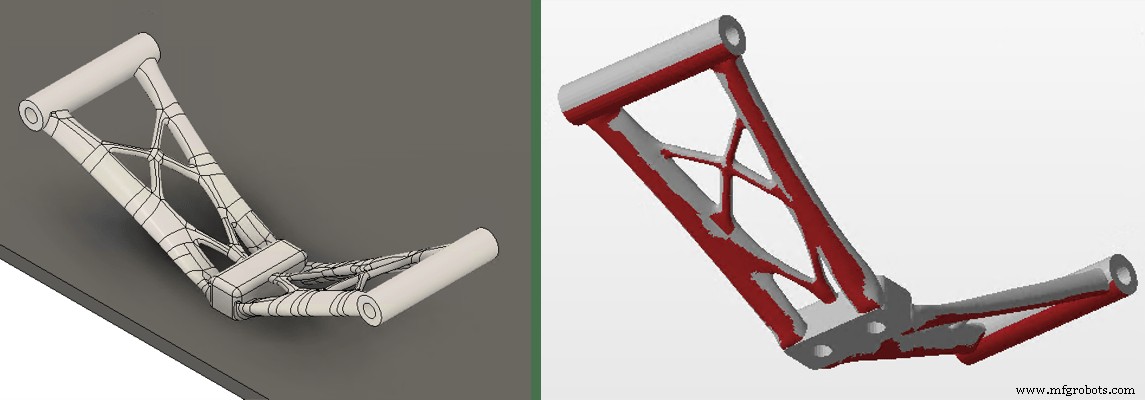
Wenn wir beginnen, Additiv 2.0 Seite an Seite mit unseren bestehenden additiven Einschränkungen (Additiv 1.0) zu betrachten, werden die Unterschiede offensichtlich, wie in Abbildung 3 (unten) gezeigt. In beiden Fällen haben wir die additive Beschränkung mit einem Überhangwinkel von 45 Grad und einer Mindestdicke von 3 mm konfiguriert.
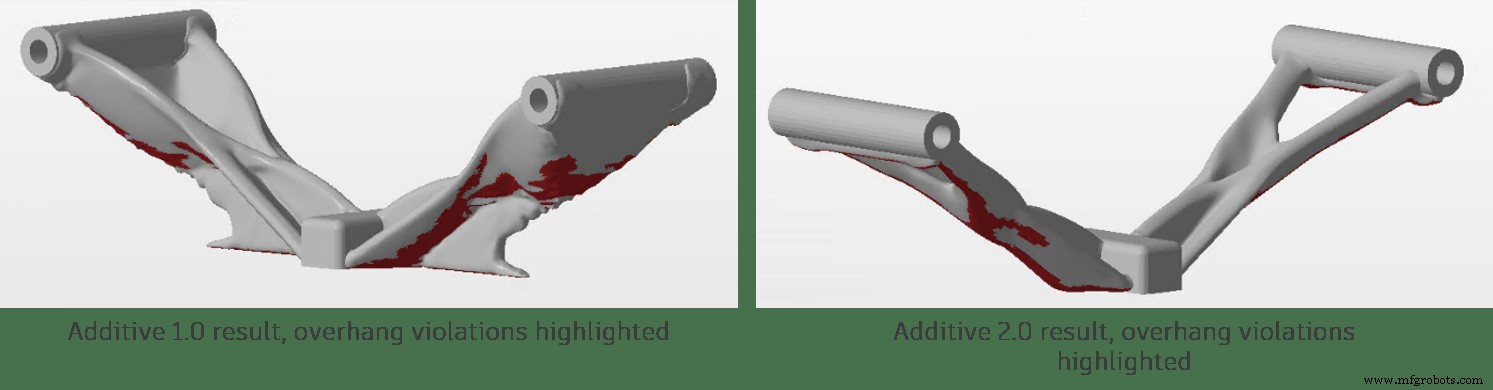
In beiden Fällen wird die Menge an benötigtem Stützmaterial reduziert, aber nicht eliminiert. Das Additiv 1.0-Ergebnis, das Material von der Bauplatte aufbaut, um die gesamte Struktur zu stützen, ist jedoch 50 % schwerer als das nicht eingeschränkte Ergebnis. Es weist Treppenstufenartefakte auf, die bei der ursprünglichen additiven Fertigungslösung ein häufiges Ärgernis waren. Additiv 2.0 reduziert auch die Menge an benötigtem Stützmaterial erheblich, tut dies jedoch mit subtileren Änderungen an der Geometrie und erhöht die Masse bei diesem Modell nur um 11%. Beide Additiv-Designs erfüllen die Mindeststrukturgröße von 3 mm, aber Additive 2.0 behält eine Struktur bei, die viel näher an der uneingeschränkten liegt, und verschmilzt die zu dünnen Gitterträger zu einer dickeren organischen Struktur. Die neuen Additive 2.0-Ergebnisse eliminieren auch einen Großteil der schlechten Oberflächenqualität im ursprünglichen Ergebnis.
Theoretisch reduzieren die neuen Einschränkungen von Additive 2.0 die unterstützte Fläche und eliminieren dünne Träger bei einer minimalen Erhöhung der Gesamtteilmasse. Aber sind diese Designs tatsächlich besser herstellbar? Lassen Sie uns den Druckvorbereitungsprozess durchgehen und sehen.
Validieren des Druckvorgangs
FFF-Beispiel
Abbildung 4 (unten) vergleicht die Ergebnisse für Additiv 1.0 und Additiv 2.0 mit dem ursprünglichen uneingeschränkten Ergebnis. Jedes dieser Ergebnisse wurde mithilfe des additiven Arbeitsbereichs von Fusion 360 durch den generischen FFF-Workflow geführt. Die Modelle wurden mit Fusion 360 geschnitten und nachbearbeitet, bevor sie auf einer Desktop-FFF-Maschine gedruckt wurden. Jedes Teil wurde mit denselben Druckeinstellungen, derselben Maschine und demselben PLA-Filament nachbearbeitet. Die in Abbildung 3 gezeigten Ergebnisse zeigen deutlich die Verbesserung zwischen Additiv 2.0 und 1.0 mit einer signifikanten Reduzierung der Teilemasse um 41,3 %. Der Vorteil von Additive 2.0 im Vergleich zur Nutzung der uneingeschränkten Beschränkungen wird ebenfalls hervorgehoben, mit einer 47,8 %igen Reduzierung des erforderlichen Stützmaterials.
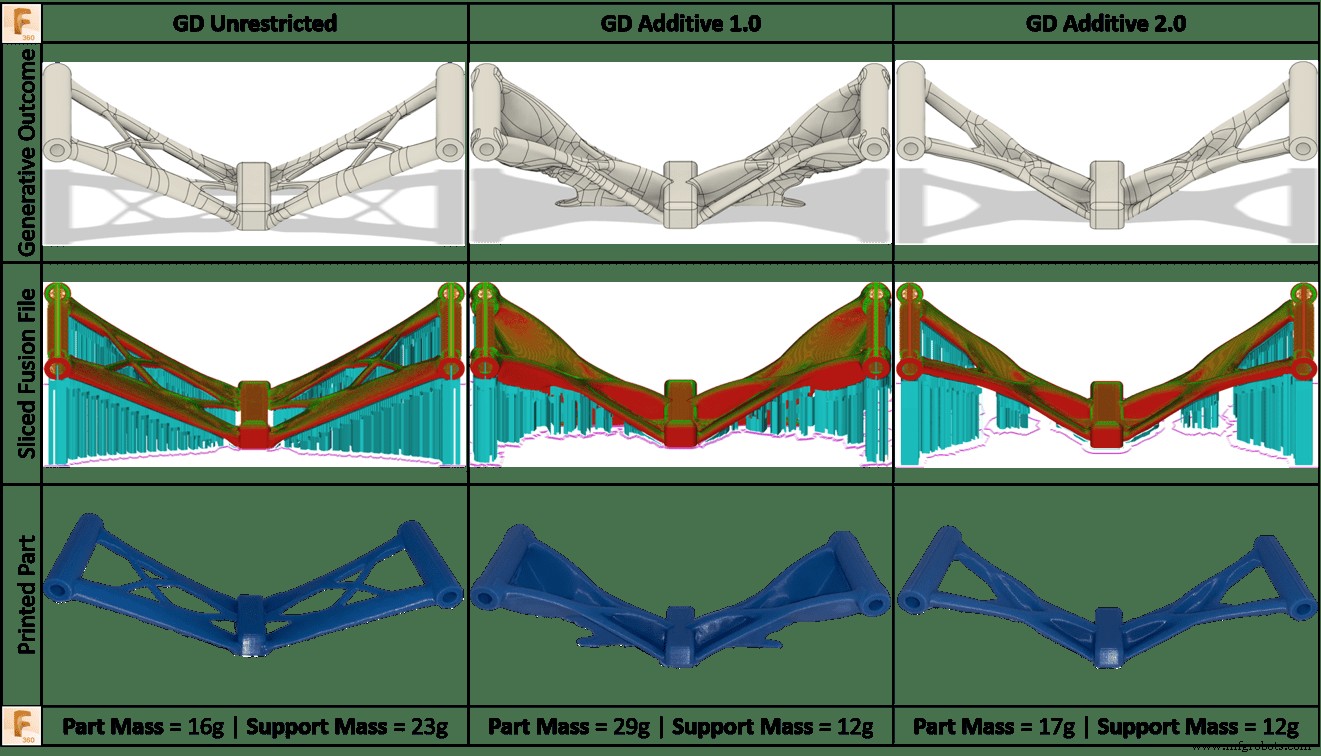
SLA-Beispiel
Abbildung 5 (unten) vergleicht die Ergebnisse für Additiv 1.0 und Additiv 2.0 mit dem ursprünglichen uneingeschränkten Ergebnis, das für den Druck in einem SLA-Prozess vorbereitet wurde. Jedes dieser Ergebnisse wurde mit Netfabb durch den generischen SLA-Workflow geführt. Ähnlich wie bei den obigen Ergebnissen zeigt Abbildung 5 deutlich die Verbesserung von Additiv 1.0 zu 2.0. Sowohl Teilmasse als auch Stützmaterial erforderten diesen Prozess ebenfalls.
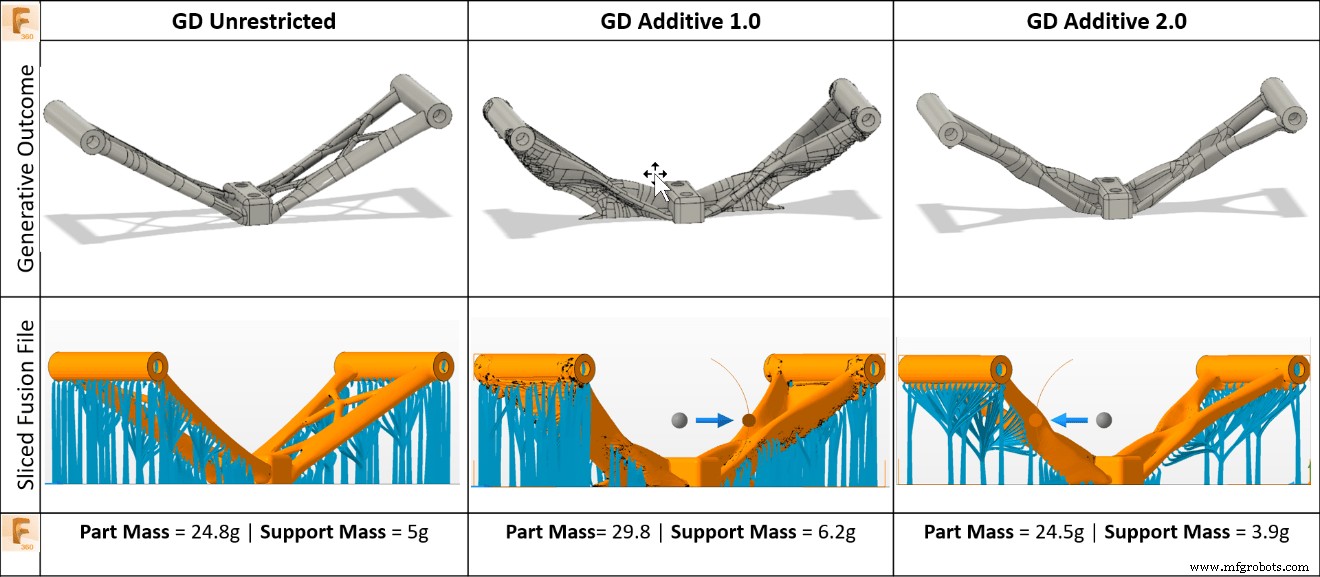
SLM-Beispiel
Schauen wir uns ein weiteres, realeres Beispiel an. Das Beispielproblem „Motorrad-Dreifachklemme“ in den Schulungsmaterialien für generatives Design führt durch die Konstruktion einer Strukturkomponente, die die Gabelrohre mit dem Lenkschaft eines Motorrads verbindet. Für dieses Beispiel wollen wir das Bauteil aus Aluminium mittels selektivem Laserschmelzen (SLM) additiv fertigen.
Vor dem Ausführen der generativen Studie haben wir die Baurichtung für die Komponente ausgewählt. Die Bauhöhe ist ein wichtiger Kostentreiber, daher haben wir die +X-Richtung vermieden. Aus Erfahrung wissen wir, dass wir die meisten großen Löcher während des Druckens mit Material füllen und dann nachbearbeiten müssen, um die erforderliche Toleranz zu erhalten. Sobald die Löcher gefüllt sind, hat die +Y-Ausrichtung eine schnelle Änderung der Querschnittsfläche an der oberen Fläche des Teils, was zu einer schnellen Abkühlung einer großen Oberfläche führt und Bauprobleme verursachen kann. Aus diesem Grund haben wir die +Y-Ausrichtung verworfen und uns für die +Z-Baurichtung entschieden.
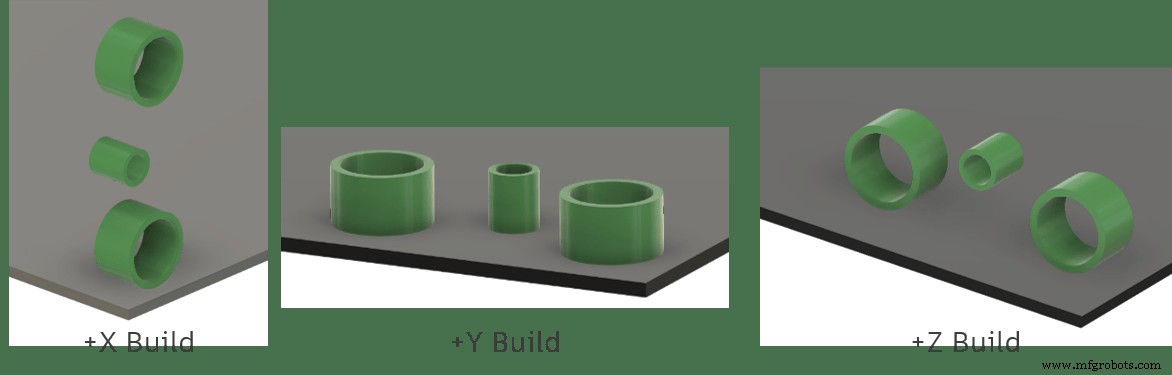
Wir haben eine Mindeststrukturgröße von 0,25 Zoll (6,35 mm) gewählt, um sicherzustellen, dass alle hergestellten Träger groß genug sind, um den Kräften durch das Entfernen der Stütze standzuhalten. Der Überhangwinkel wurde entsprechend den Parametern des SLM-Prozesses auf 45° eingestellt. Das Ergebnis von Additive 2.0 ist im Bild unten dargestellt.
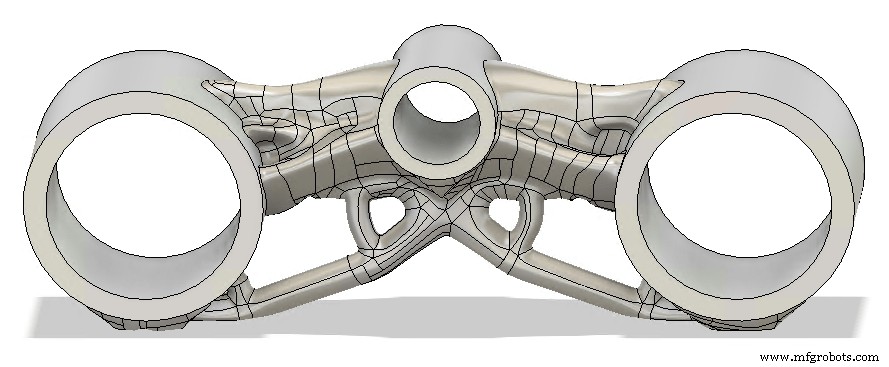
Normalerweise würden wir an dieser Stelle wahrscheinlich Designänderungen an der organischen Form vornehmen und die Designleistung validieren. Für heute überspringen wir diese Schritte und gehen direkt zum Fertigungsarbeitsbereich, um es für den Druck vorzubereiten.
Wir werden einen Renishaw AM250 verwenden, um das Design herzustellen, was die Additive Build Fusion-Erweiterung erfordert. Zuerst müssen wir die großen Löcher mit Material füllen, damit wir sie später auf Toleranz bearbeiten können. Wir tun dies im Arbeitsbereich Fertigung, indem wir ein Fertigungsmodell erstellen, in dem wir die Löcher auf einen kleineren Durchmesser drücken/ziehen.
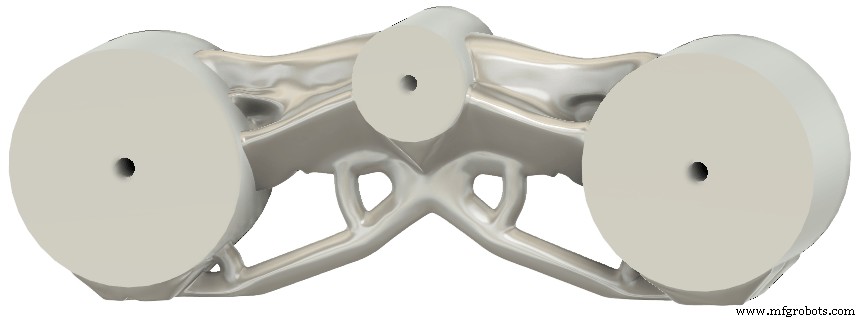
Jetzt erstellen wir ein neues Setup, wählen die Renishaw-Maschine und unsere modifizierte Geometrie aus. Nach ein wenig Arbeit mit dem Move-Befehl ist unser Teil auf der Bauplattform positioniert.
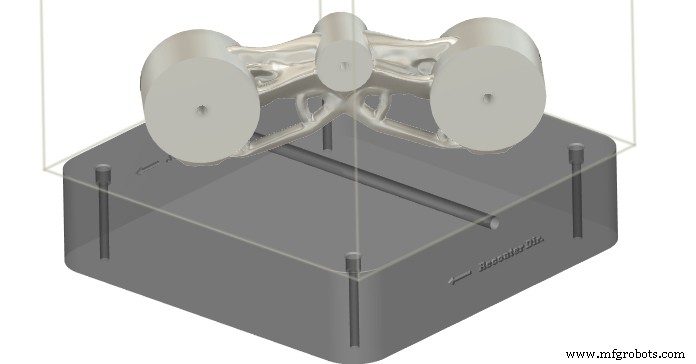
Jetzt verwenden wir den Volume Support-Befehl, um Support-Material zu generieren.
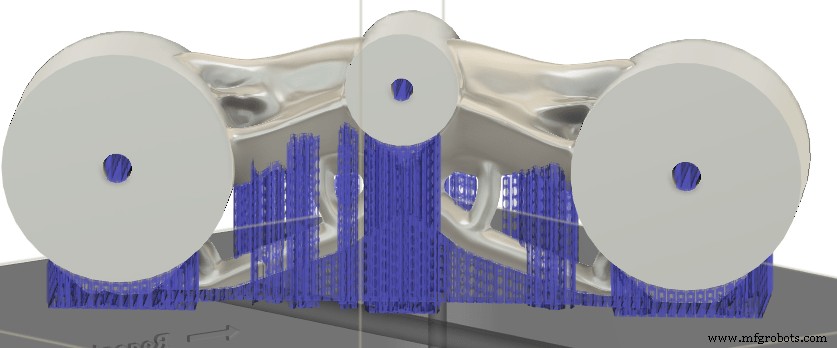
An diesem Punkt sind wir bereit, den Druck zu simulieren, dann den G-Code zu generieren und ihn an die Maschine zu senden.
Abbildung 7 (unten) vergleicht das Additive 2.0-Design mit den uneingeschränkten und bestehenden additiven Fertigungslösungen, und wir sehen einen ähnlichen Trend wie im vorherigen Beispiel. Die Ergebnisse von Additiv 1.0 sind schwerer, erfordern genauso viel Unterstützung wie der uneingeschränkte Teil und leiden unter Problemen mit der Oberflächenqualität. Additiv 2.0 verbessert die Formqualität, reduziert das erforderliche Stützmaterial und bringt die Teilemasse wieder auf nahezu das gleiche Maß wie das uneingeschränkte Ergebnis.
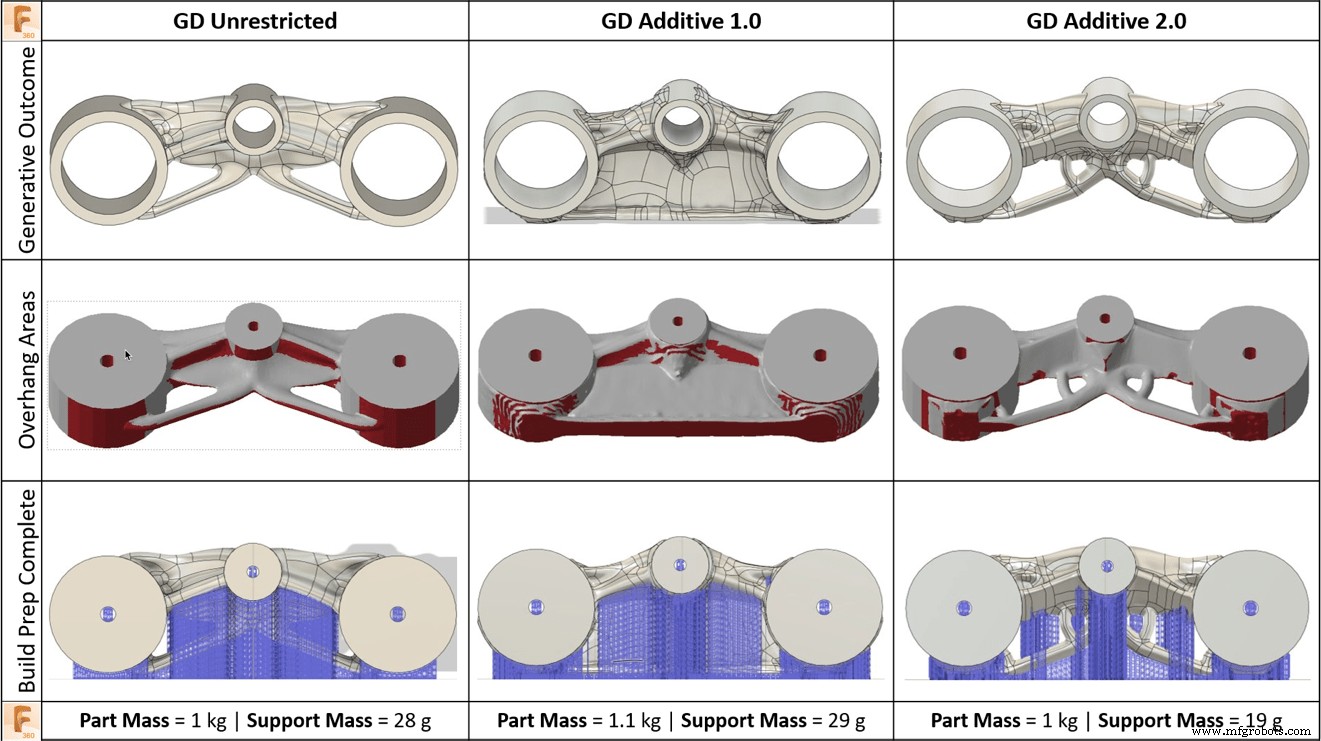
Probieren Sie Additiv 2.0 selbst aus
Wir hoffen, dass Sie von diesen Verbesserungen der additiven Fertigung genauso begeistert sind wie wir, sie in das Produkt einzubringen. Während die Bilder in diesem Blog eine großartige Geschichte erzählen, wollten wir Ihnen die Modelle zur Verfügung stellen, mit denen wir die Verbesserungen demonstriert haben, damit Sie sich selbst ein Bild machen können. Diese Modelle können ausgeführt, geöffnet und die verfügbaren Studien generiert werden.
Additiv 2,0 V-förmiges Spannstangen-Setup
Additiv 2.0 Motorrad-Gabelbrücken-Setup
Wenn Sie Fragen oder Anmerkungen zu unseren neuen Einschränkungen für die additive Fertigung haben, kontaktieren Sie uns bitte unter [email protected]. Außerdem möchte ich mich bei einem großartigen Expertenteam, das diese Lösung entwickelt und validiert hat, und bei Ben Weiss, Adam Day, Matt Oosthuizen und Divy Kishor Tiwary ganz herzlich dafür bedanken, dass sie mir beim Verfassen dieses Blogbeitrags geholfen haben. Ich wünsche Ihnen allen frohe Feiertage und einen guten Rutsch ins neue Jahr!

Industrietechnik
- Additive Fertigung vs. subtraktive Fertigung
- Vorteile der additiven Fertigung
- 4 vielversprechende Automatisierungstrends in der additiven Fertigung
- Eine Umfrage zu Arbeitsabläufen in der additiven Fertigung
- Generatives Design und 3D-Druck:Die Fertigung von morgen
- Design für die Herstellung von Leiterplatten
- Alles drin mit Additiv
- Additive Fertigung in der Elektronik
- So nutzen Sie CAD vollständig im additiven Fertigungsprozess
- Additive Fertigung in der Luft- und Raumfahrt