Kompressions-RTM für die Produktion zukünftiger Flugzeugstrukturen
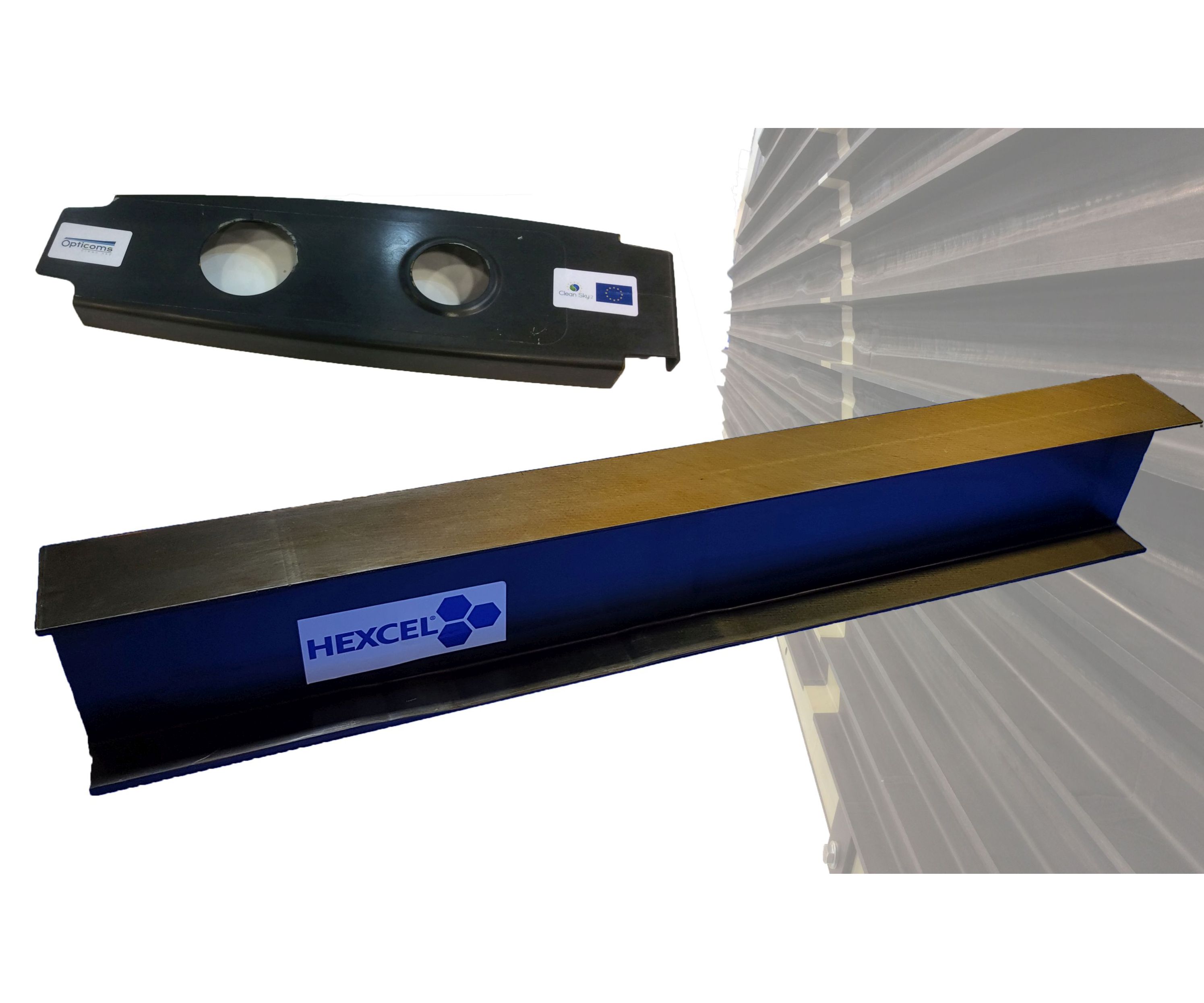
Verbundwerkstoffe haben sich einen festen Platz in den Flugzeugzellen von Verkehrsflugzeugen gesichert, weil sie hochfeste Leichtbaustrukturen ermöglichen, die im Vergleich zu Metall niedrigere Wartungskosten bieten. Aktuelle Prognosen für die nächste Generation von Groß- und Schmalrumpfflugzeugen zeigen ein anhaltendes Wachstum bei Verbundzellen, jedoch nur, wenn Materialien und Prozesse die anspruchsvollen Ziele für niedrige Kosten und hohe Produktionsraten erfüllen können. Obwohl autoklavgehärtetes Epoxid-Prepreg bei Flugzeugzellen aus kohlenstofffaserverstärktem Polymer (CFK) bis heute die Vorrangstellung einnimmt, verfolgen die Entwickler von Flugzeugen der nächsten Generation aggressiv Technologien außerhalb des Autoklaven (OOA) mit integrierter Automatisierung und Inline-Inspektion als Schlüsselfaktoren für zukünftige Industrie 4.0-Produktion.
Der Ausrüstungs- und Automatisierungsanbieter Techni-Modul Engineering (Coudes, Frankreich) und seine US-Tochter Composite Alliance Corp. (Dallas, Texas, USA) haben eine Partnerschaft mit den britischen und französischen Geschäftseinheiten des Anbieters fortschrittlicher Materialien Hexcel (Stamford, Connecticut, USA) geschlossen. zur Demonstration der automatisierten OOA-Produktion von CFK-Rippen und -Stringern. Die Teile werden durch automatisiertes Vorformen von trockenen Hexcel-Kohlefaserverstärkungen und einem C-RTM-Verfahren (Compression Resin Transfer Moulding) hergestellt, das eine schnelle Infiltration von Hexcel HexFlow RTM6 flüssigem Epoxidharz ermöglicht, um Teile mit 60 % Faservolumen und weniger als 1 % Hohlräume herzustellen in einem 2,5- bis 3,0-Stunden-Zyklus, der skaliert werden kann, um mehrere Teile für die Hochgeschwindigkeitsproduktion zu produzieren.
Entwicklung von Trockenverstärkungen
„Wir sehen in Liquid Composite Molding (LCM) eine Antwort auf die dreifache Herausforderung, Kosten zu senken, bereit zu sein und die Leistung der Primärstruktur bereitzustellen“, erklärt Rémy Pagnac, Hexcel technischer Support-Ingenieur für Flüssig-Verbundguss. Hexcel hat sein HiMax Non-Crimp-Gewebe (NCF) und HiTape unidirektionale (UD) Kohlefasermaterialien entwickelt, um die Leistungsanforderungen der Primärstruktur bei der Verwendung von LCM-Prozessen zu erfüllen. HiMax ermöglicht das schnelle Auflegen großer, flacher Strukturen wie Wingskins, während HiTape maßgeschneiderte Layups für große, komplexe Strukturen mit minimalem Abfall ermöglicht. „Wir können Eigenschaften erreichen, die denen von UD-Prepregs der neuesten Generation entsprechen“, fügt Pagnac hinzu.
Hexcel hat mit HiMax NCF, einschließlich eines feinen 20 dTex-Stichgarns, daran gearbeitet, das Volumen zu reduzieren und die Drapierbarkeit zu verbessern. HiMax-Materialien werden im früheren Formax-Werk in Leicester, Großbritannien, hergestellt, das Hexcel im Jahr 2016 erworben hat 1 Rennwagen. Nun wurden NCF-Materialien in einem Tragflächen-Demonstratorprojekt verwendet, das von Airbus Defence and Space (Airbus DS, Cadiz, Spanien) und Danobat (Elgoibar, Spanien) abgeschlossen wurde, wobei letztere die Automated Dry Material Placement (ADMP)-Technologie – eine Art automatisierte Faserplatzierung – verwenden (AFP) für NCF (siehe „Nachweis der Tragfähigkeit für Trockengewebeinfusion für große Flugzeugstrukturen“) – und im von Airbus gesponserten ZAero-Projekt für Null-Fehler-CFK-Strukturen wie Stringer-versteifte Tragflächen (siehe „Zero-defect-Manufacturing of Composite Parts .) “).
Sowohl bei HiMax als auch bei HiTape integriert Hexcel Schichten aus dünnem thermoplastischem Filamentschleier mit geringem Flächengewicht, die als Bindemittel fungieren, wodurch Pulverbindemittel, die in der Vergangenheit in Trockenmaterialien für das Vorformen und Flüssigformen verwendet wurden, überflüssig werden. Bei HiMax wird dieser Schleier zwischen NCF-Lagen gelegt; bei HiTape wird der Schleier auf beiden Seiten des Kohlefaser-Uniape aufgebracht. „Damit brauchen Sie kein Pulverbindemittel zu verwenden, um die UD-Schichten an Ort und Stelle zu halten“, erklärt Pagnac. „HiTape ist kalibriert und kein geschlitztes Band, daher gibt es keinen Fuzz und weniger Variationen in der Breite für eine verbesserte AFP-Verarbeitung. Der thermoplastische Schleier verleiht dem fertigen Laminat außerdem Zähigkeit, und wir haben gezeigt, dass wir mit der nächsten Generation von AFP-Maschinen hohe Materialauftragsraten erzielen können.“ In einem SAMPE-Papier vom Mai 2015 beschreibt Hexcel einen Einzelkrümmungs-Vorformling, der mit 0,25 Zoll breitem HiTape hergestellt wurde, das mit einer laserausgerüsteten Coriolis Composites (Quéven, Frankreich) AFP-Maschine mit einer Auflegegeschwindigkeit von 1 Meter/Sekunde aufgetragen wurde. Es hat auch mit Electroimpact (Mukilteo, Washington, U.S.) AFP-Geräten zusammengearbeitet, um Abscheidungsraten von bis zu 150 kg/Stunde für eine große Holm-Flugzeugstruktur zu demonstrieren.
Abb. 1 Kompressions-RTM
Bei C-RTM wird der trockene Vorformling in eine RTM-Form gelegt, aber die Form ist nur teilweise geschlossen, wobei eine Lücke zwischen dem trockenen Vorformling und der oberen Formoberfläche verbleibt. Anschließend wird Vakuum angelegt, Harz eingespritzt und die Presse schließt die Lücke im Werkzeug, indem das flüssige Harz in z-Richtung über das gesamte Teil nach unten in den Vorformling gedrückt wird. Quelle | Hexcel

Anpassung von C-RTM für die Luft- und Raumfahrt
C-RTM wurde erstmals mit Hochdruck-RTM (HP-RTM) für Automobil-Verbundwerkstoffe eingeführt. Wie bei konventionellem RTM beinhaltet C-RTM das Einlegen eines trockenen Faservorformlings in eine angepasste Metallform, das Einspritzen von flüssigem Harz in den Vorformling und das anschließende Anwenden von Hitze und Druck unter Verwendung einer angetriebenen Presse. Bei C-RTM ist die Form jedoch nur teilweise geschlossen, so dass ein Spalt zwischen dem trockenen Vorformling und der oberen Formoberfläche verbleibt (Abb. 1). Dann wird Vakuum angelegt, eine präzise Dosis des gemischten Harzes eingespritzt und die Presse schließt die Lücke im Werkzeug, wodurch das flüssige Harz in z-Richtung über das gesamte Teil in den Vorformling gedrückt wird. „Das ist viel schneller, als das Harz in der Ebene durch das Teil zu injizieren“, erklärt Thomas Chevallet, Verfahrensingenieur von Techni-Modul Engineering.
Techni-Modul Engineering sah in seiner Rolle als Partner im Clean Sky 2 „Optimized Composite Structures“ (OPTICOMS)-Projekt die Möglichkeit, C-RTM für die Luft- und Raumfahrt anzupassen. OPTICOMS ist im Arbeitspaket B-1.2 („Erschwinglichere Verbundstrukturen“) organisiert und zielt darauf ab, die Produktionskosten von Kleinflugzeugen (z. OPTICOMS hat einen Composite-Flügel-Demonstrator entwickelt, der eine obere Flügelhaut mit drei Holmen umfasst, die als integrierte Struktur in einem One-Shot-Verfahren hergestellt werden. Der Full-Scale-Flügel (Abb. 2) ist Teil eines AIRFRAME Innovative Technology Demonstrators (ITD) zur Evaluierung und Ausreifung von Technologien in Richtung Technology Readiness Level (TRL) 6 für Flugzeuge der nächsten Generation in Produktion ab 2025. Israel Aerospace Industries (Lod, Israel) wurde im Juli 2016 als Koordinator für OPTICOMS ausgewählt. Das Konsortium umfasst auch den Kleinflugzeug-OEM Piaggio Aerospace (Savona, Italien), Techni-Modul Engineering und die AFP-Ausrüster Coriolis Composites und Danobat.
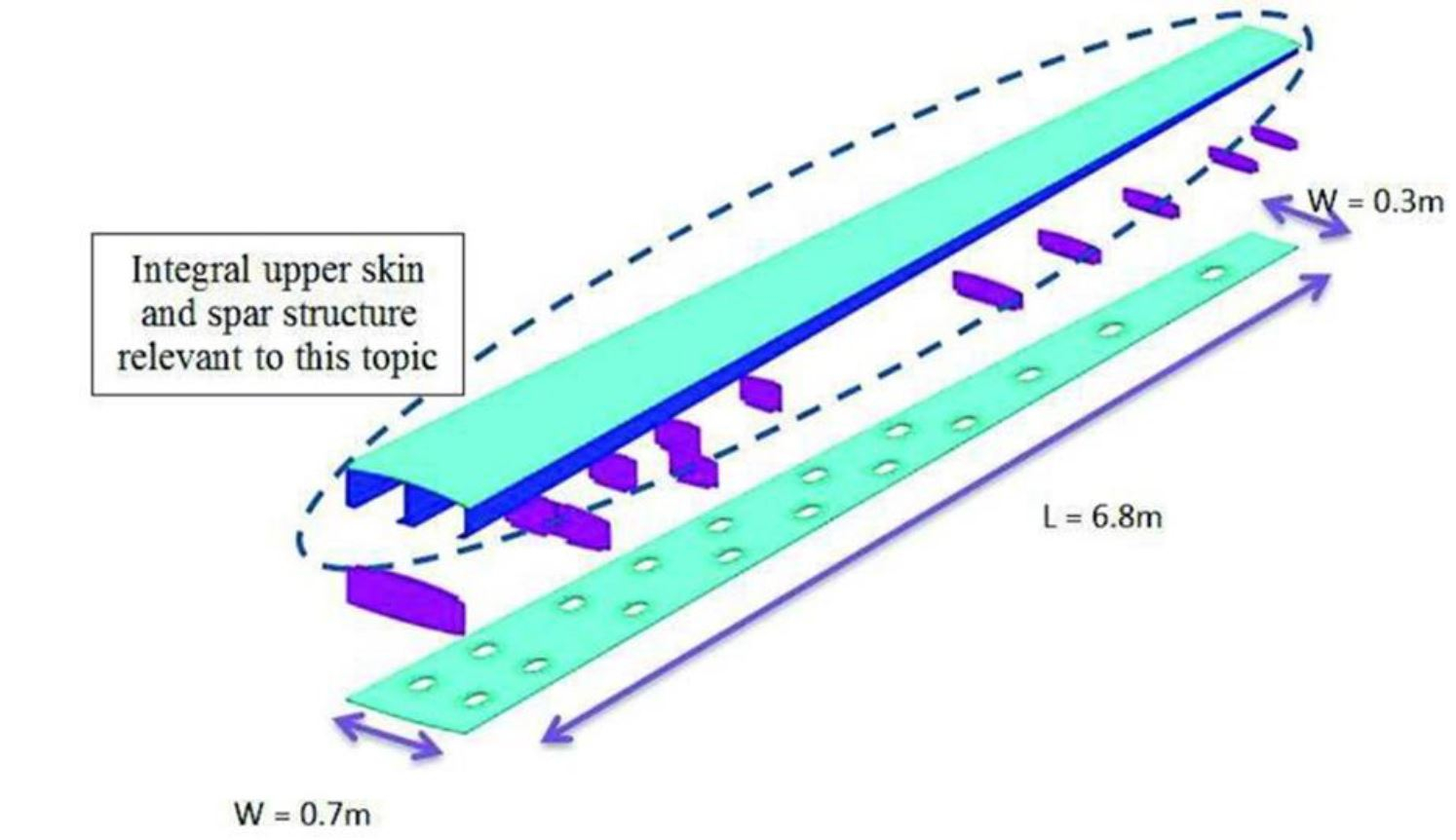
Abb. 2 Clean Sky 2 OPTICOMS Rippe
Techni-Modul ist Partner im Clean Sky 2 Projekt „Optimized Composite Structures“ (OPTICOMS), das einen Demonstrator aus Verbundtragflächen entwickelt hat, der aus einer unteren Flügelhaut, mehreren Rippen und einer oberen Flügelhaut mit drei Holmen besteht. Letztere wird als integrierte Struktur in einem One-Shot-Verfahren hergestellt. Der Demonstrator wird für Flugzeuge der nächsten Generation in der Produktion ab 2025 evaluiert. Quelle | Sauberer Himmel 2
„C-RTM war in der Branche gut bekannt“, erklärt Chevallet, „aber mit HP-RTM wird noch eine große Druckmaschine benötigt. Unsere Entwicklung bestand darin, C-RTM für eine schnelle Injektion mit niedrigeren Drücken anzupassen, um eine kostengünstigere Produktion von Luft- und Raumfahrtteilen mit sehr strengen Anforderungen an hohes Faservolumen, Faserausrichtung und geringe Hohlräume zu ermöglichen. Injektionszeit für die 0,7 Meter lange und 0,2 Meter breite Flügelrippe im Projekt OPTICOMS wurde von 40 auf fünf Minuten verkürzt. In einem separaten Testprogramm für einen 900 Millimeter langen und 150 Millimeter hohen I-Träger-Stringer wurde die Injektionszeit von einer Stunde auf unter fünf Minuten verkürzt.

„Diese Verkürzung der Einspritzzeit, die C-RTM bietet, wäre für große Teile wie komplette Flügelfelle oder Hubschrauber-Rotorblätter noch größer“, fügt Chevallet hinzu. Er stellt fest, dass C-RTM auch das Einspritzen von hochviskosen Harzen sowie Einspritzsysteme mit niedrigerem Druck und Pressen mit geringerer Tonnage ermöglicht, was die Kosten senkt. „Der Formdruck bei C-RTM beträgt nur 6 bar, viel niedriger als bei HP-RTM“, erklärt Chevallet. „Das Verfahren erzielt Verbundwerkstoffe in Luft- und Raumfahrtqualität, funktioniert aber gut für große, dünne Teile und kleinere, komplex geformte Teile.“
Automatisiertes Vorformen
Obwohl schnellere und kostengünstigere Harzinjektion und OOA-Spritzgießen Schlüsselelemente dieses Ansatzes für eine kostengünstigere Herstellung von Aeroverbundwerkstoffen sind, erfordert die Prozesskette immer noch mehrere Schritte zum Schneiden und Auflegen von Materialien und Vorformen. „Für uns ging es bei OPTICOMS auch um Automatisierung“, sagt Chevallet. Techni-Modul Engineering lieferte für das OPTICOMS-Projekt nicht nur ein C-RTM-Injektionssystem, sondern auch einen Pick-and-Place-Roboter und eine Hot-Drape-Forming (HDF)-Maschine, die alle in eine vollautomatische Fertigungszelle integriert sind.
Kurz nach dem Start von OPTICOMS im Jahr 2016 gewann die Techni-Modul Engineering-Tochter CAC auf der CAMX 2016 (26.-29. September, Anaheim, Kalifornien, USA) den ACE Equipment and Tooling Innovation Award in der Kategorie Manufacturing für ihre automatisierte 3D-Preforming-Zelle. Die Zelle konnte 3D-Preforms aus Trockenfasern oder Prepreg herstellen und nutzte Vakuumsauggreifer, um geschnittene Lagen aufzunehmen, zu platzieren und auf eine beheizte Preform-Form zu falten. Techni-Modul Engineering und CAC haben eine Software entwickelt, um die Schnittlagen von 2D-Materialien für die Formgebung in komplexe und abwickelbare Oberflächen vorzubereiten. Diese Zelle wurde in OPTICOMS und dem I-Beam-Testprojekt weiterentwickelt.
Schritt 1
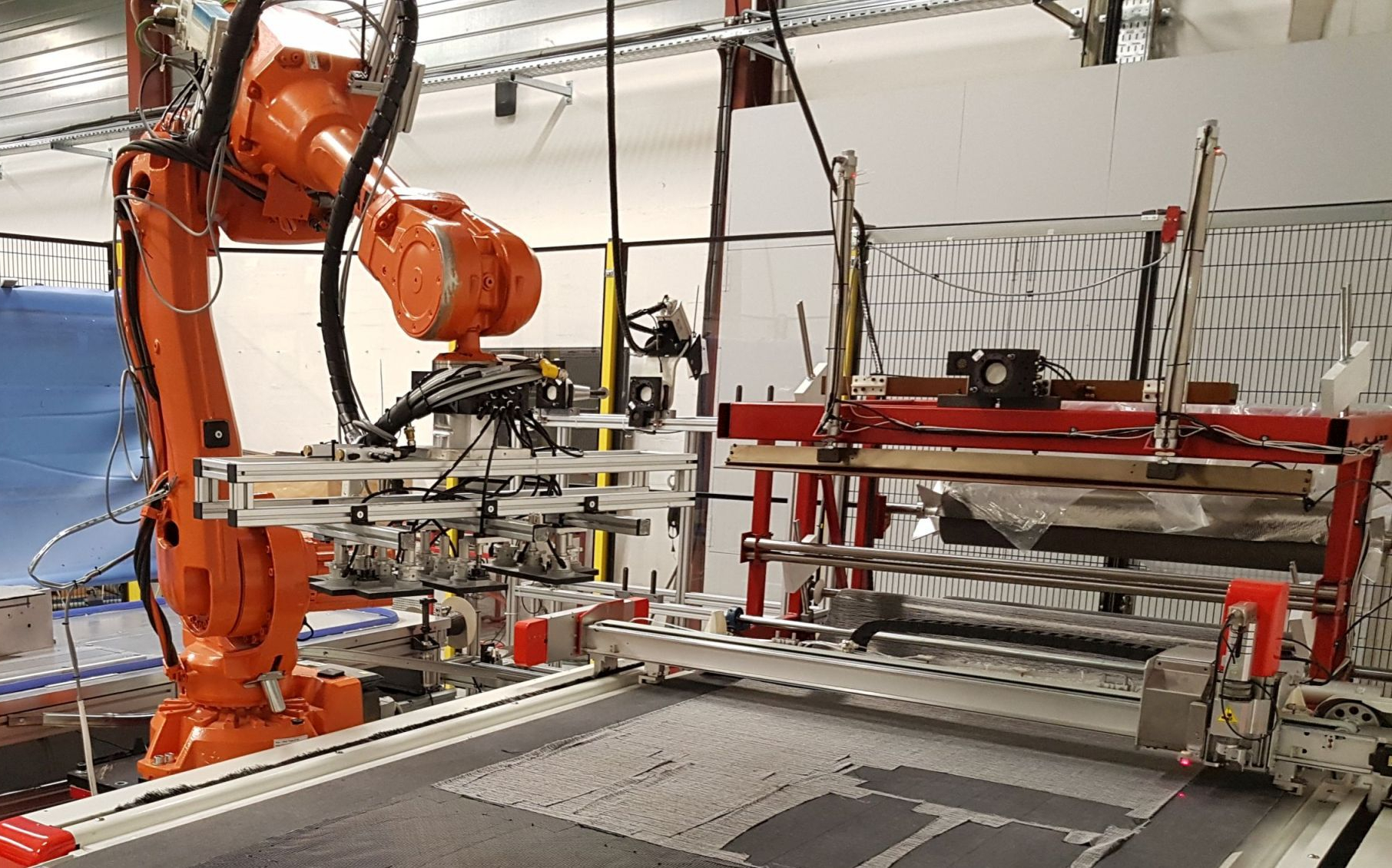
Quelle, alle Stufenbilder | Technik-Modul Engineering
In der automatisierten Zelle von Techni-Modul Engineering entnimmt ein Pick-and-Place-Roboter Lagen von einem automatisierten Schneidegerät und legt sie auf ein beheiztes Vorformwerkzeug.
Schritt 2

Die Vorformwerkzeuge sitzen auf einem Verdichtungstisch mit einer aufklappbaren wiederverwendbaren Vakuummembran (blau, links), die verwendet wird, um während des Auflegens alle 5-8 Lagen eine erhitzte Debulk zu vervollständigen.
Schritt 3
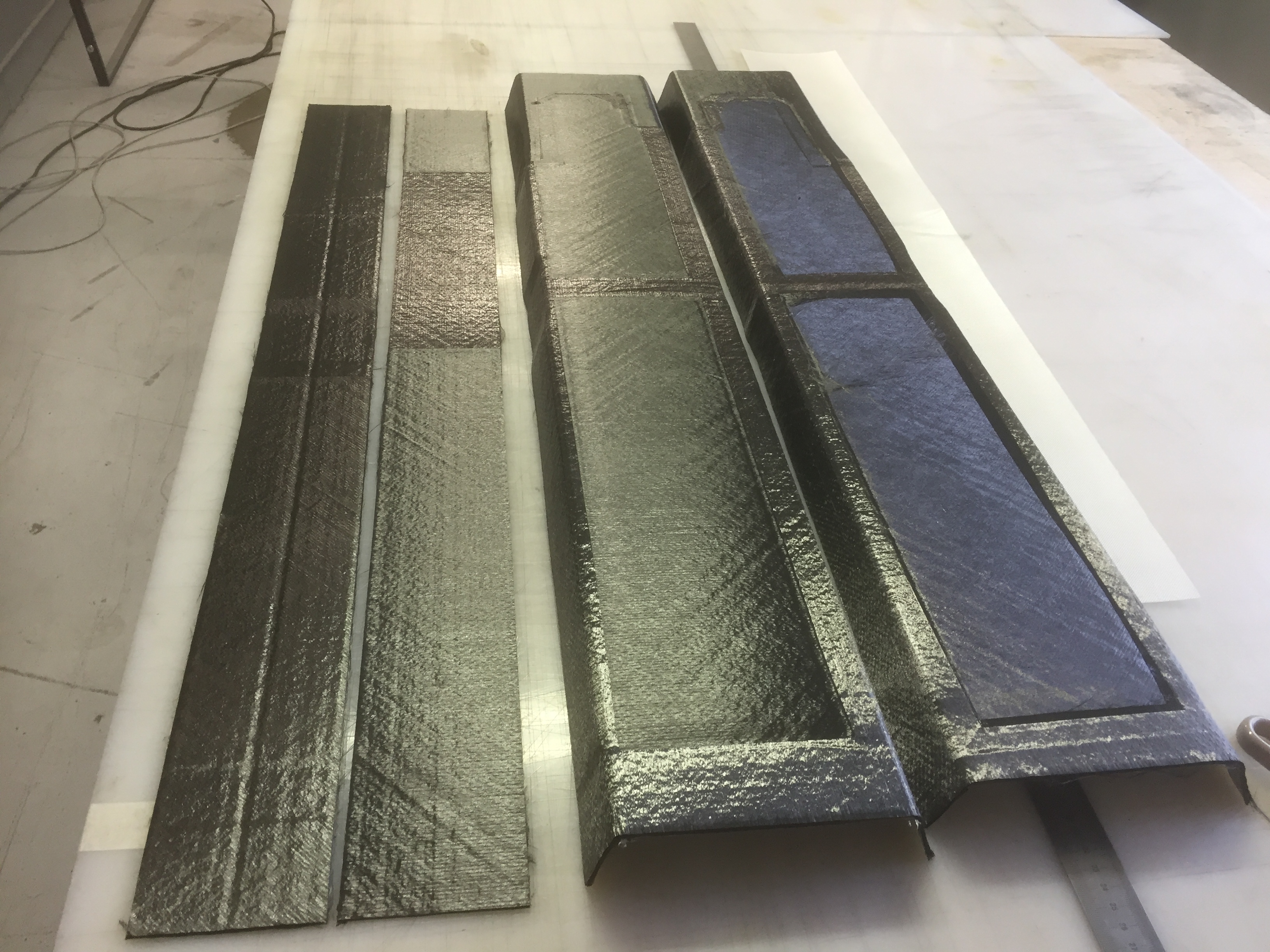
Jeder Stringer-Vorformzyklus erzeugt einen C-Träger-Vorformling (zwei umfassen den I-Träger-Steg) und einen Flachflansch-Vorformling. Zwei Sätze, die für jeden I-Beam Stringer erforderlich sind, werden hier gezeigt.
Schritt 4
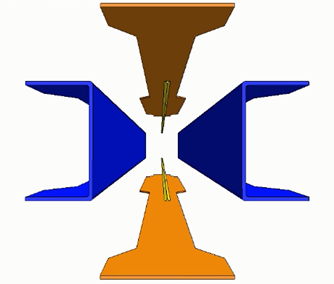
Die vier I-Träger-Stringer-Preforms werden in die RTM-Form gelegt, Vakuum angelegt und die Harzinjektion ist in 5 Minuten abgeschlossen.
Schritt 5
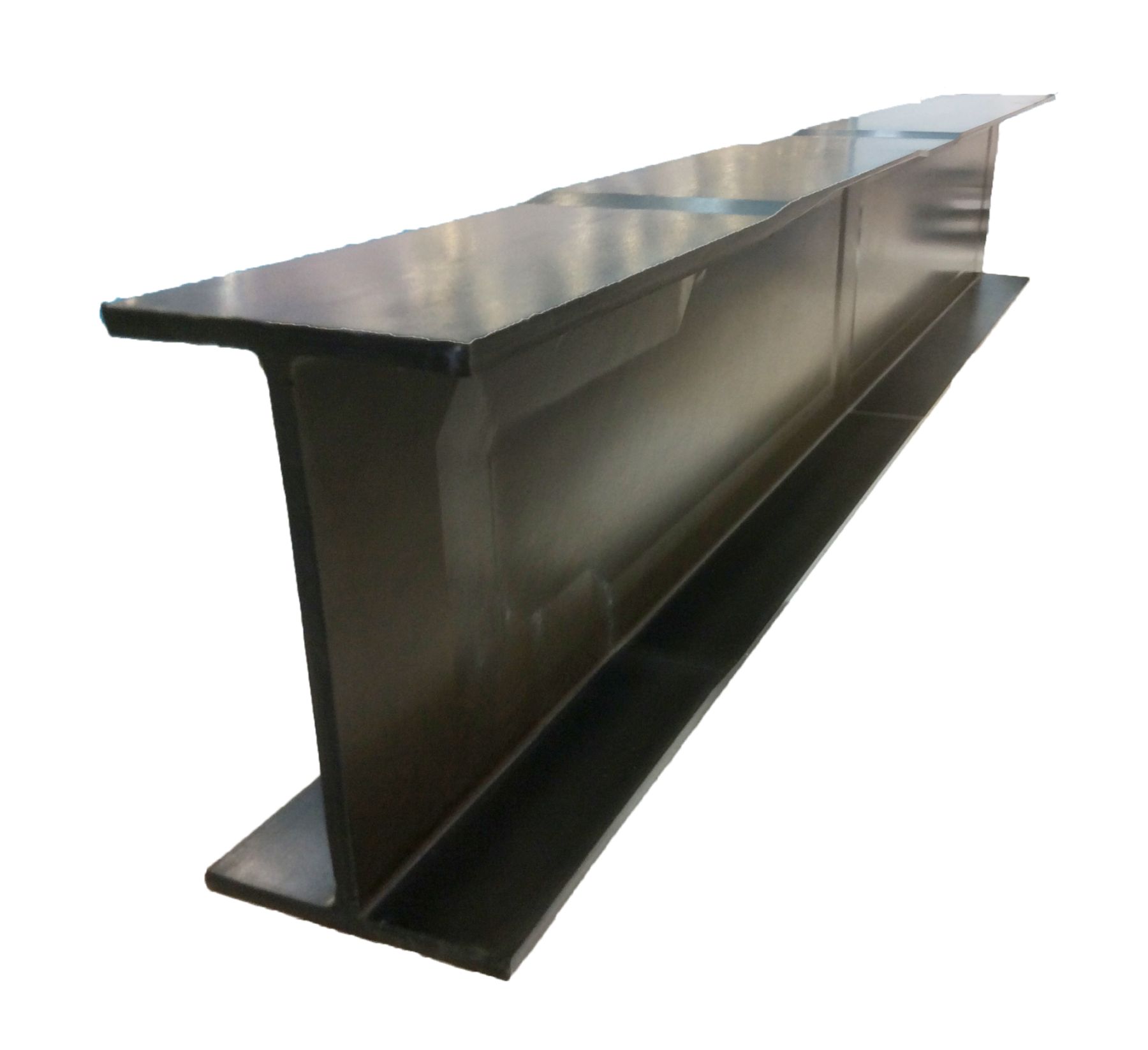
Nach einer 90-minütigen Aushärtung wird der Stringer entformt und der Harzgrat wird für einen vollständigen Teilezyklus von 4,5 Stunden getrimmt.

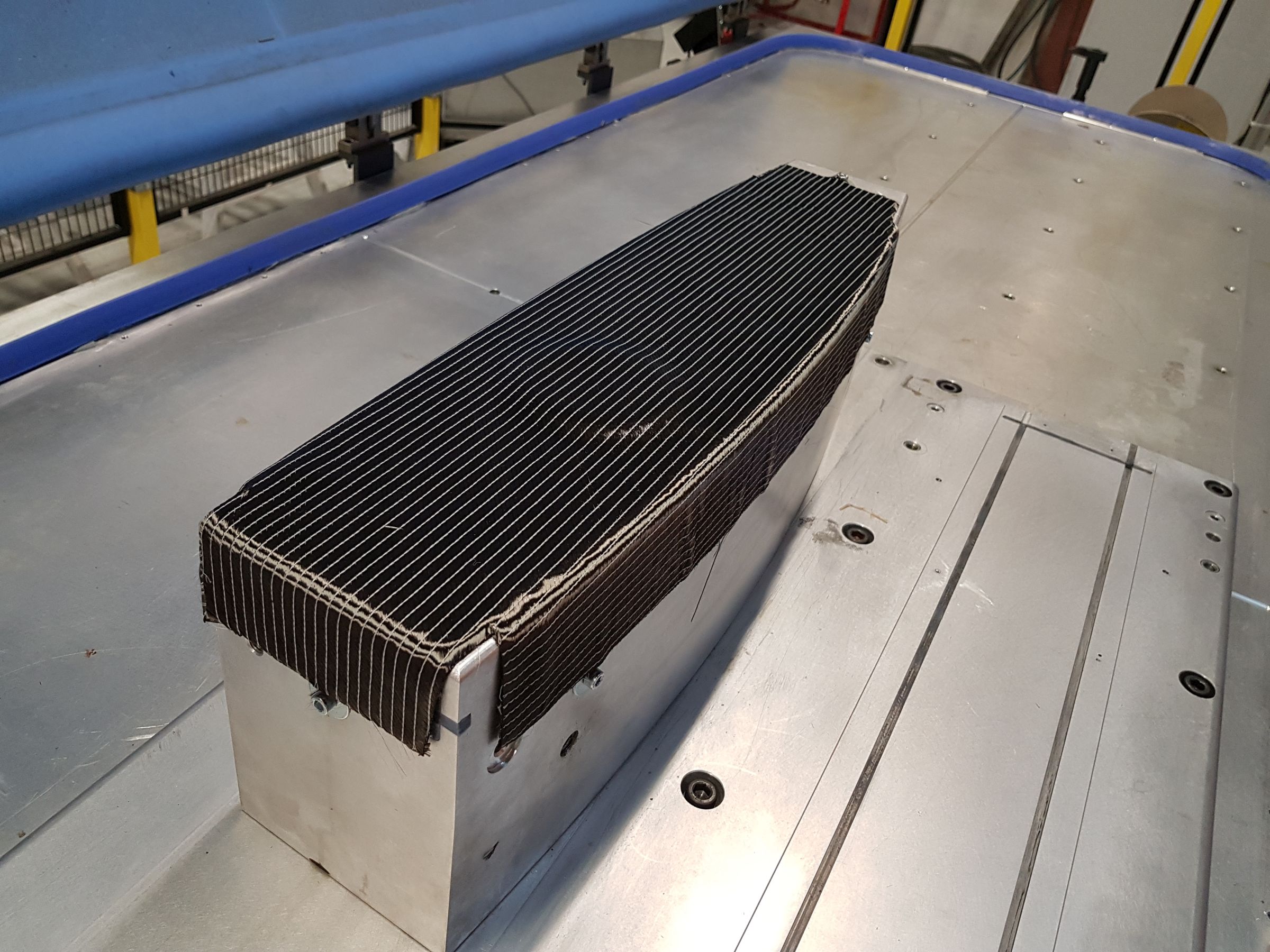
Ein Roboter legt Schnittlagen auf das beheizte Vorformwerkzeug. Alle 5-8 Lagen wird ein erhitzter Debulk fertiggestellt, um den Vorformling zu verdichten.

Vor dem Debulking wird eine blaue Trennfolie aufgetragen.
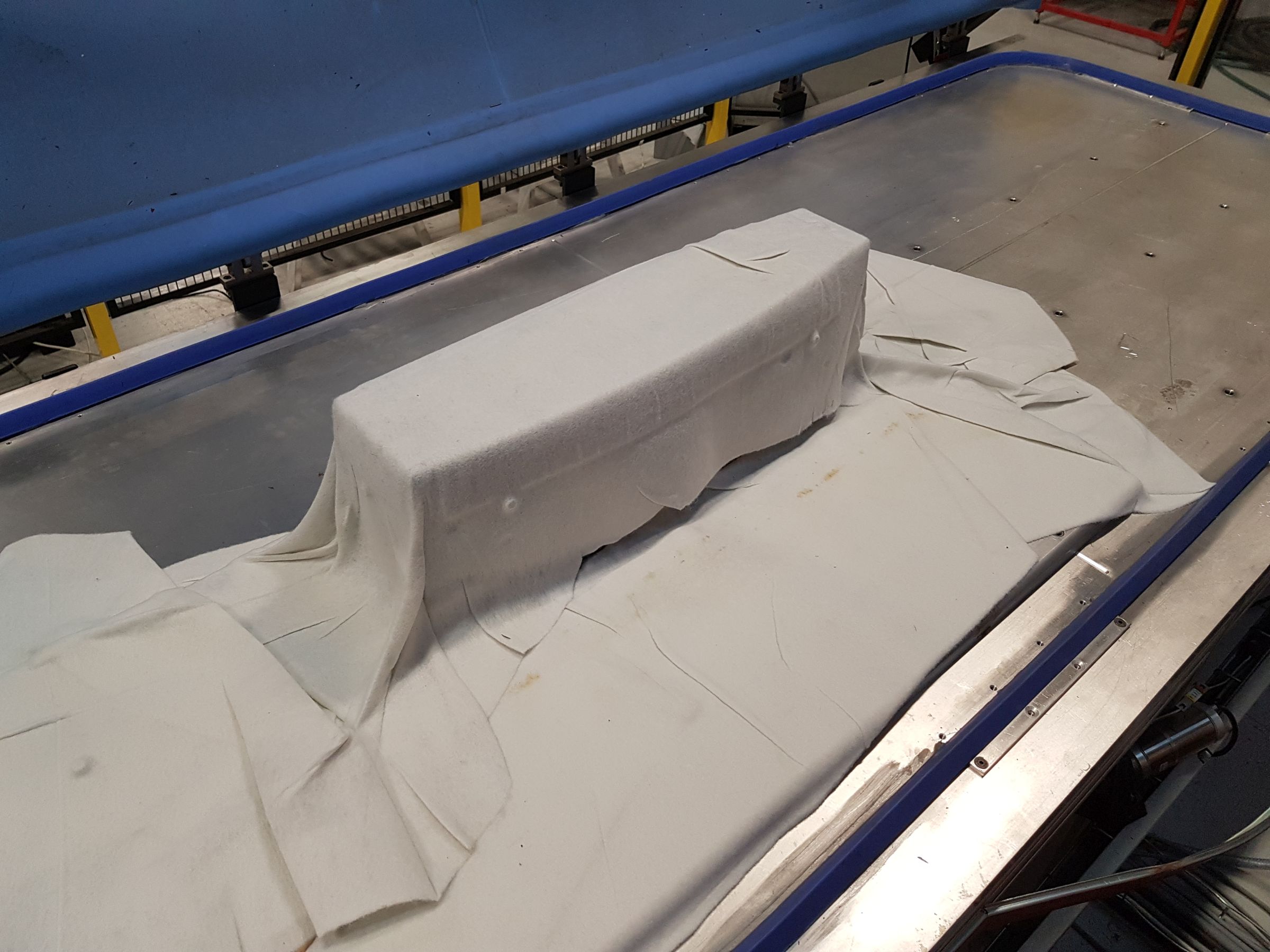
Die Entlüftung wird verwendet, um Luft über den Vorformling abzusaugen.
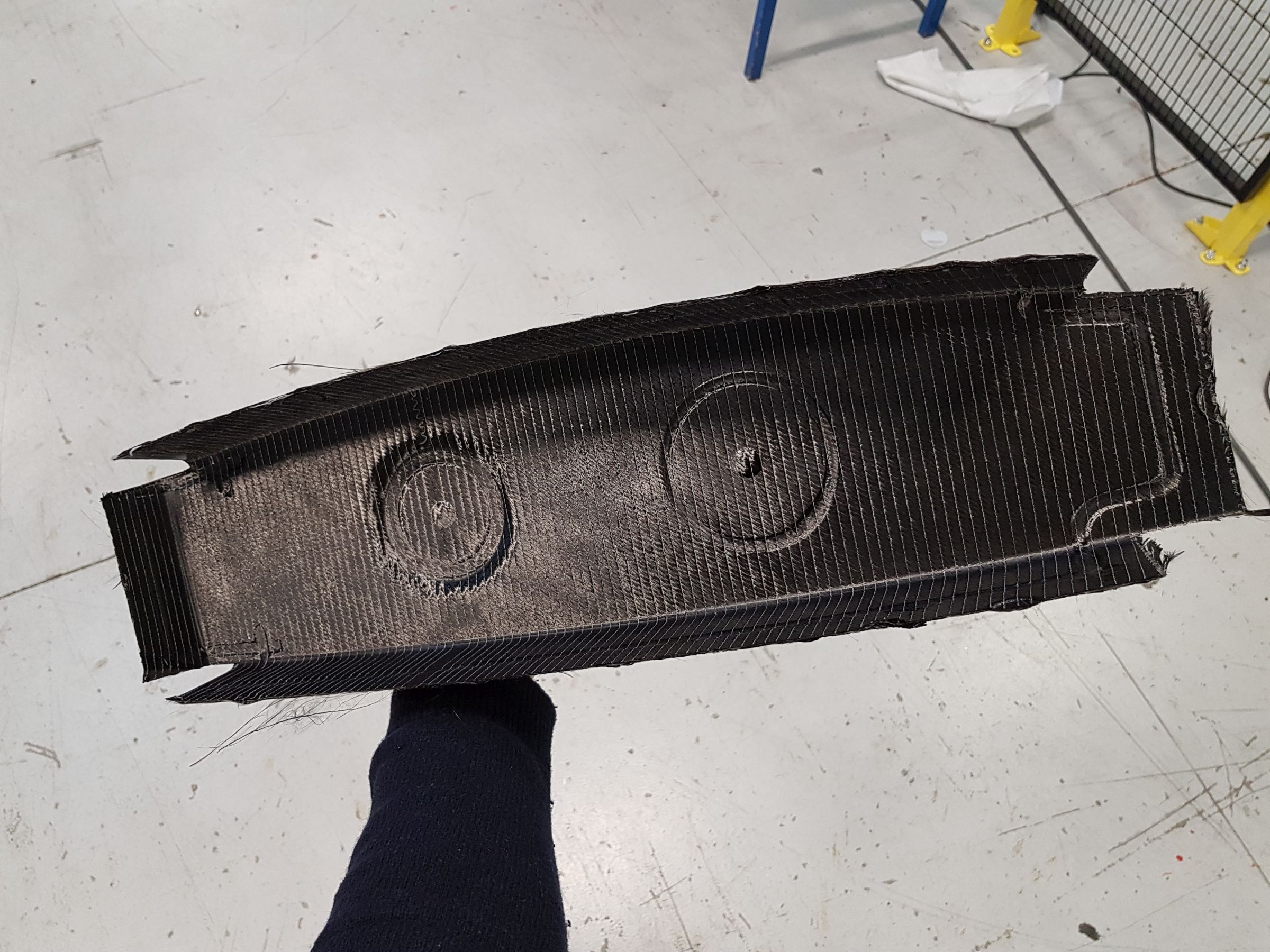
Nach dem endgültigen Debulk wird der Preform auf dem Werkzeug abgekühlt und die Ausschnitte werden besäumt (unten).
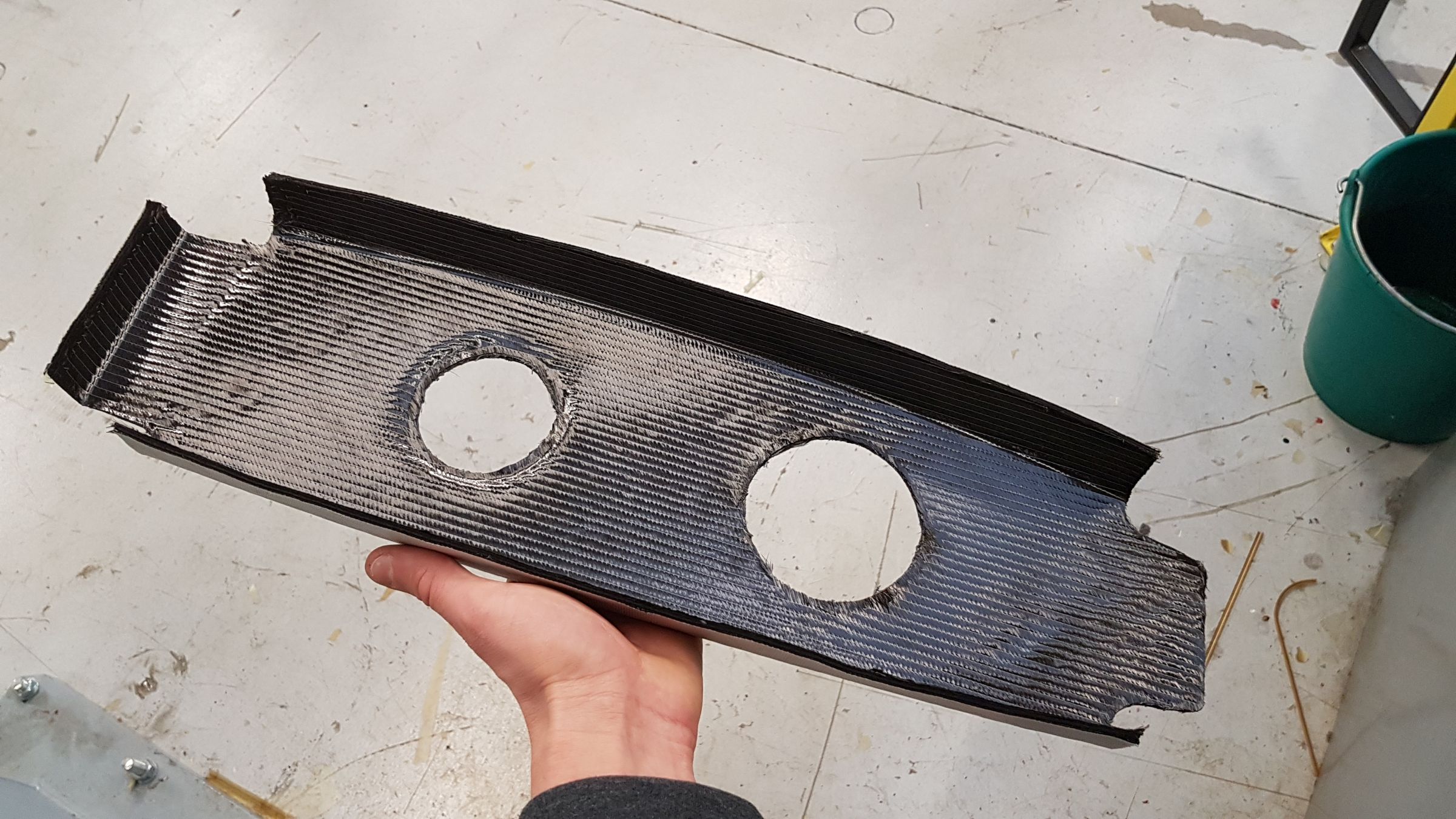
„Wir haben das klassische manuelle Stapeln von Lagen mit Roboter-Pick-and-Place automatisiert“, sagt Chevallet. „Der Roboter nimmt Lagen von einem automatisierten Cutter auf und übergibt diese an das beheizte Preform-Werkzeug, das auf einem Verdichtungstisch sitzt [Schritt 1 und 6].“ Eine Abziehschicht (blaue Folie in Schritt 6), ein Entlüfter (weißes Material in Schritt 6) und eine aufklappbare wiederverwendbare Vakuummembran (hellblau links in Schritt 2 und 6) werden aufgebracht, gefolgt von Vakuum und Erhitzen, um die Luft vorzuformen und die Luft zu entfernen Textilstapel (Hot-Drape-Forming, HDF), während die dünnen thermoplastischen Schleier geschmolzen werden, um eine verdichtete Vorform zu erhalten.
„Wie viele Lagen Sie gleichzeitig verdichten können, hängt von den Materialien und der Form des Teils ab“, erklärt Chevallet. „Bei Teilen mit geringer Krümmung, wie einer Flügelhaut, könnte man möglicherweise alle 50 Lagen verdichten. Die OPTICOMS-Rippe hat jedoch 90-Grad-Winkel, und der Test-I-Träger-Stringer hat T-Form, daher müssen Sie beim Vorformen darauf achten, keine Falten in den Lagen zu bilden.“ Er fügt hinzu, dass solche komplexen Formen möglicherweise alle 5-8 Lagen verdichtet werden müssen, aber dennoch Teil eines großvolumigen, industrialisierten Prozesses sein können:Stapellagen, 2-Minuten-HDF verdichten, wieder öffnen und wieder stapeln, gefolgt von wiederholten Verdichtungszyklen mit einer abschließenden Abkühlung des Vorformlings auf dem Werkzeug vor der Übergabe an die RTM-Form.
„Unsere automatisierte Zelle kann mit einer Geschwindigkeit von 15 Sekunden pro Lage platziert werden“, bemerkt Chevallet. „Der Aufbau für die OPTICOMS-Rippe mit insgesamt weniger als 20 Lagen war in 20 Minuten abgeschlossen.“ Layup für den I-Beam Stringer war länger – 45 Minuten aufgrund seiner komplexen Form und Laminatstapel, einschließlich Dickenvariationen von 1,2 bis 6 Millimeter. „Dies ist immer noch viel schneller als manuelle Prozesse und reduziert das Fehlerrisiko, erhöht die Wiederholbarkeit und Qualität bei gleichzeitiger Kostensenkung“, fügt er hinzu.
Schritt 7
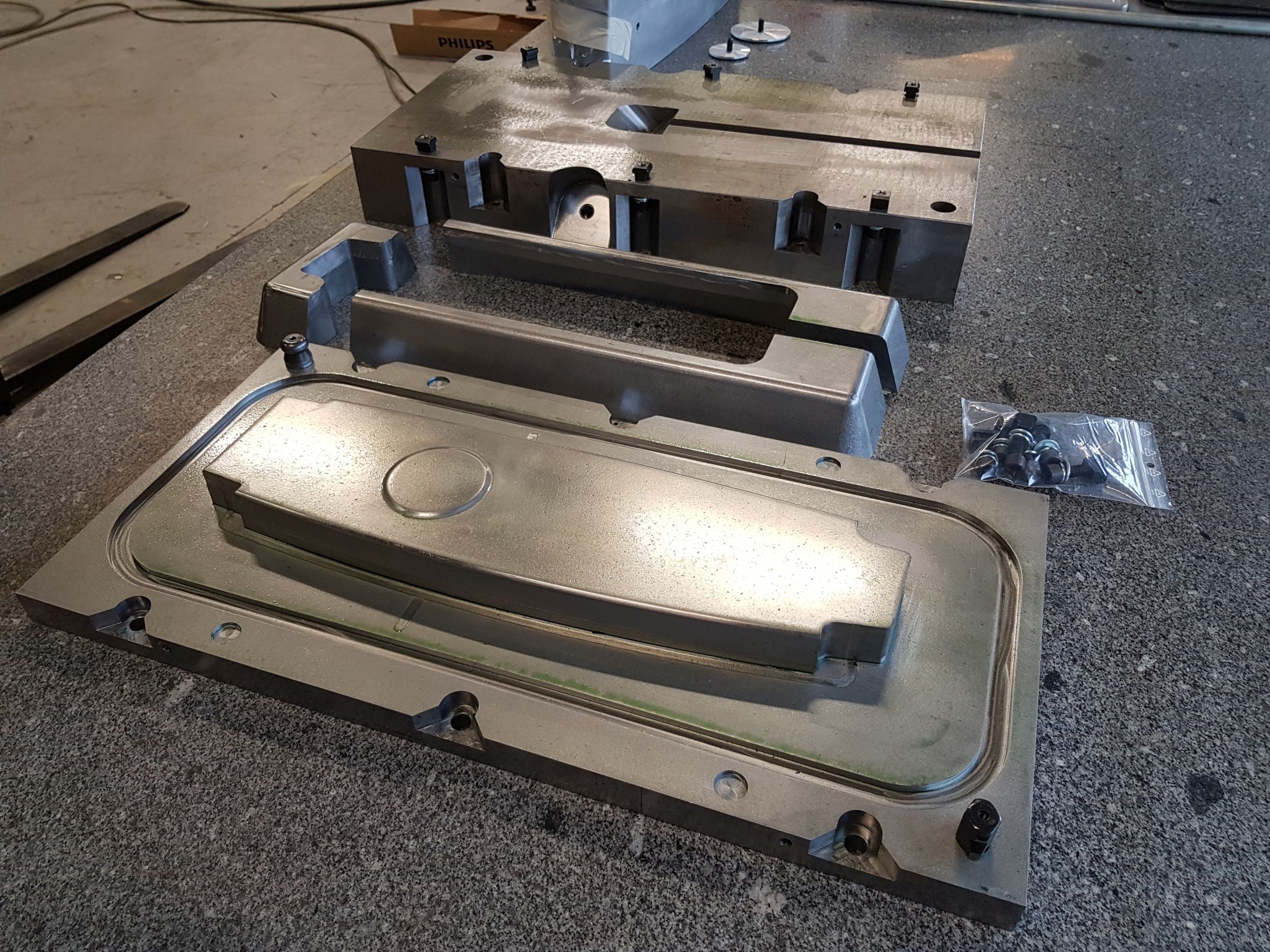
Das RTM-Tool für die OPTICOMS-Rippe besteht aus mehreren Teilen.
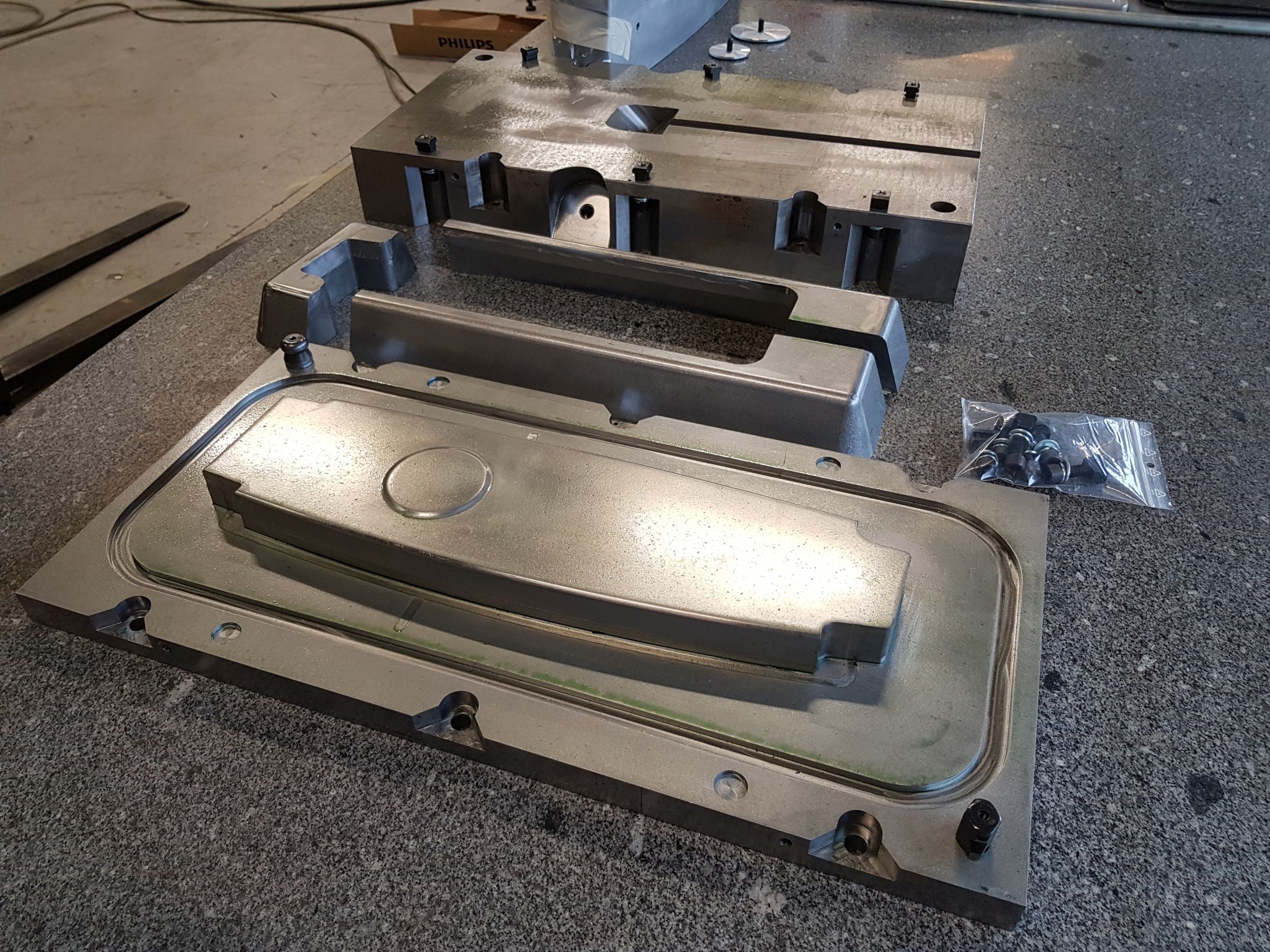
Schritt 8
Der Rippenvorformling wird in das RTM-Werkzeug eingelegt.
Schritt 9
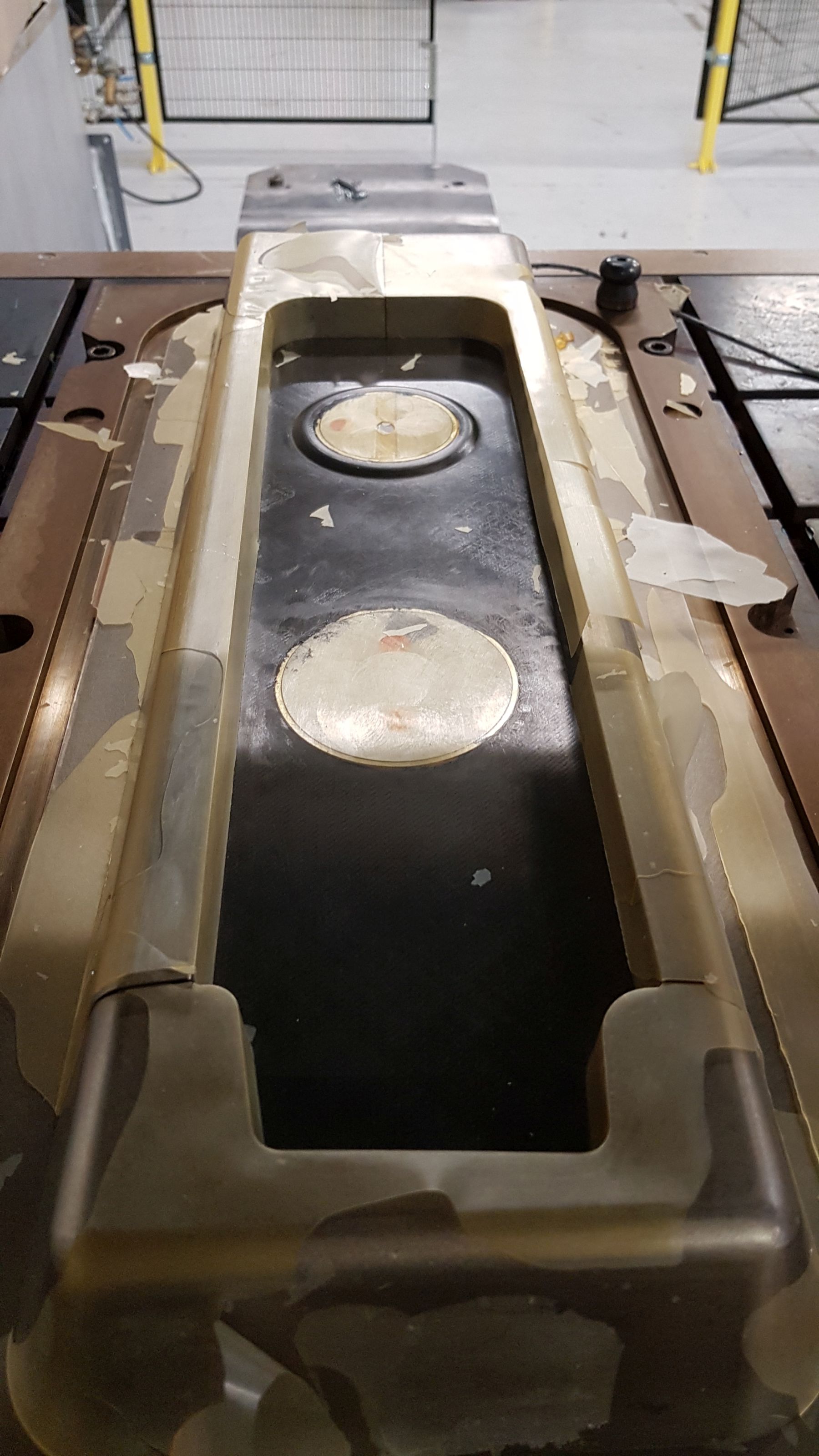
Vakuum wird angelegt, Harz wird eingespritzt und infiltriert den Vorformling, gefolgt von einer 90-minütigen Aushärtung. Hier wurde die Presse geöffnet, um das gehärtete Teil freizugeben.
Schritt 10
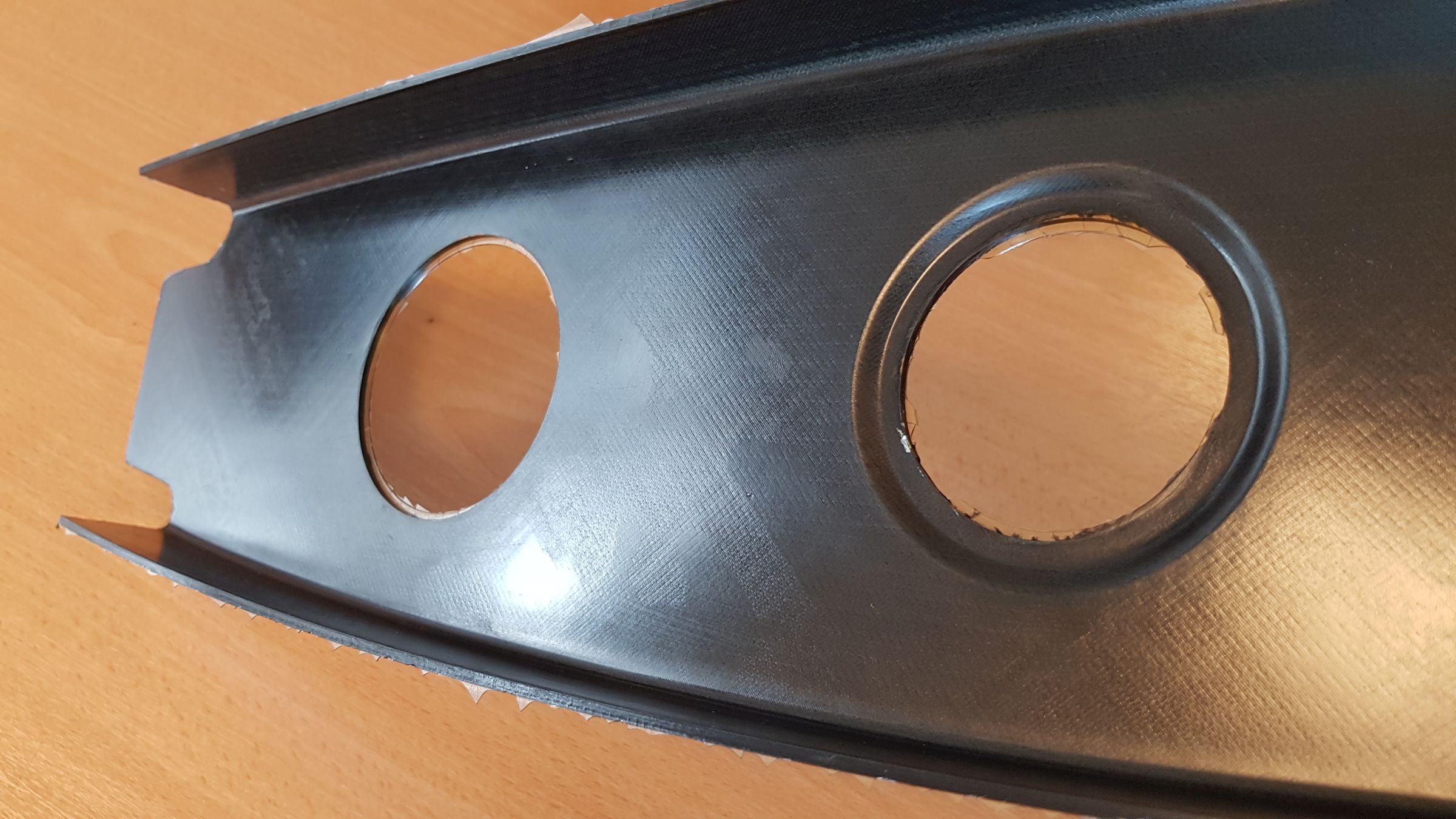
Nachdem die Entformung abgeschlossen ist, wird der Harzüberzug für einen vollständigen Teilezyklus von 4 Stunden entfernt.
Intelligente Steuerung
Ein weiteres wichtiges Merkmal der automatisierten Preforming-Zelle von Techni-Modul Engineering ist das integrierte Steuerungssystem. Das als SMART CONTROL bezeichnete Rückgrat ist ein Kamerasystem und eine Mehrzwecksoftware, die während der Bearbeitung aufgenommene Bilder mit der CAD-Datenbank des Teils vergleicht und so die Formerkennung der Preform, die Kontrolle der Faserorientierung, die Lagenpositionierung und die Erkennung von Defekten und Fremdkörperablagerungen (FOD .) ermöglicht ). Das SMART CONTROL-Feedback weist den Roboter an, die Lagen in der richtigen Reihenfolge und zum richtigen Zeitpunkt aufzunehmen und zu platzieren, warnt aber auch den Zellenbediener, wenn er Fehler erkennt. „Das System kann so konfiguriert werden, dass der Bediener die Lage dann manuell entfernt und das System neu startet, um sie zu ersetzen“, erklärt Chevallet, „oder wir können mit dem Kunden zusammenarbeiten, um eine automatisierte Lösung zum Entfernen defekter Lagen und Korrigieren von Fehlern zu entwickeln.“
Dieselben optischen Bilder, die zur Erkennung von Lagenkanten und -konturen verwendet werden, werden auch zur Kontrolle der Faserorientierung verwendet. Chevallet räumt ein, dass, wenn das Teil sehr groß ist (z. B. 2 Meter lang im Vergleich zu 200 mal 200 Millimetern), „Sie möglicherweise eine Kamera benötigen, die Bilder [aus einer] höheren vertikalen Position aufnimmt, um die Kanten der Lagen zu erkennen, und dann näher heranfahren das Teil zur Überprüfung der Faserorientierung. Sie kalibrieren diese Sequenz für jeden Teiletyp. Zur Erkennung von Falten und FOD gibt es eine Datenbank mit verschiedenen Defekten, die Sie ergänzen können, sodass sich der Deep-Learning-Algorithmus mit der Zeit verbessert. Die Idee ist, ein anpassungsfähiges System zu haben.“
Zykluszeit und zukünftige Produktion
Vorformlinge für die OPTICOMS-Rippe wurden mit HiMax hergestellt und der I-Träger-Stringer mit HiTape. Das Harzsystem für beide war das einkomponentige (1K) flüssige Epoxidharz HexFlow RTM6 von Hexcel, das einen Aushärtungszyklus von 90 bis 120 Minuten bei 180 °C hat. Diese Härtung ist der längste Schritt in den Teilzykluszeiten sowohl für die OPTICOMS-Rippe als auch für den Test-I-Träger-Stringer, wie in Tabelle 1 zu sehen ist.
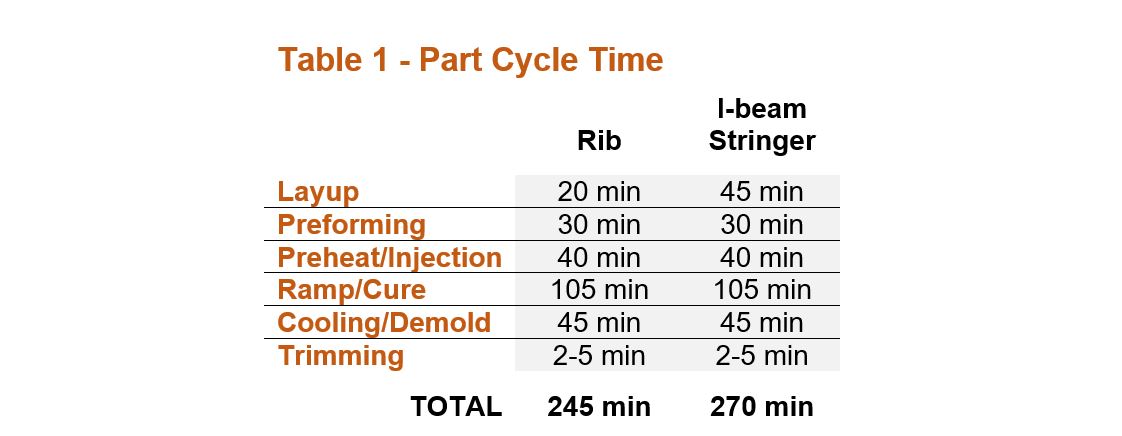
Quelle | Technik-Modul Engineering
Bis heute ist dies das einzige Epoxid, das für RTM von Luft- und Raumfahrtstrukturen geeignet ist. Das Interesse an der Qualifizierung von Zweikomponentensystemen, die am Injektionskopf gemischt werden, wächst jedoch, bietet eine erhöhte Flexibilität des Härtungszyklus und macht einen gekühlten Versand und eine erforderliche Lagerung überflüssig, um eine vorzeitige Reaktion des vorgemischten RTM6 zu verhindern.
Airbus Helicopters (Donauworth, Deutschland) arbeitete mit Alpex Technologies (Mils, Österreich) im SPARTA-Projekt zusammen, um einen HP-RTM-Prozess mit einer Zweikomponentenversion von HexFlow RTM6 zu demonstrieren, um eine 30-minütige Härtung bei 180 °C für eine A350-Tür zu erreichen Rahmen, bei dem es sich um eine komplex geformte Primärstruktur von 2 Metern Höhe, 200-250 Millimeter Breite und 8-10 Millimeter Dicke handelt (siehe „HP-RTM zur Serienfertigung kostengünstiger CFK-Flugzeugstrukturen“). Airbus hat auch eine 1,5 mal 0,5 Meter große CFK-Rippe demonstriert, die von seiner Tochtergesellschaft Composite Technology Center (CTC, Stade, Deutschland) mit HP-RTM hergestellt wurde und 20-minütige Spritzzyklen für Teile mit 60 % Faservolumen und weniger als 2 Zoll erreicht % Lücken. Im vergangenen Jahr hat CTC mit einer Reihe von Tierlieferanten zusammengearbeitet, um für die A320 handlaminierte Prepreg-Teile auf HP-RTM umzustellen. 2K-Harzsysteme müssen jedoch für die Herstellung von Flugzeugstrukturen qualifiziert werden, und CTC ist besorgt über die Fähigkeit, die Mischqualität von 2K-Harzsystemen vor Ort kontinuierlich sicherzustellen. Alpex setzt hierfür In-Mold-Sensoren von Netzsch (Selb, Deutschland) und Kistler (Winterthur, Schweiz) ein. Weitere Lösungen werden entwickelt (siehe „Zweikomponenten-Epoxid für eine erhöhte Produktion von Verbund-Flugzeugstrukturen“).
Auch ohne 2K-Anlagen sind eventuell höhere Produktionsmengen möglich. Türrahmen im SPARTA-Projekt wurden nach der ersten 30-minütigen Aushärtung bei 180 °C entfernt und aus der Presse unter Vakuum nachgehärtet, um thermische Spannungen abzubauen und die mechanischen Eigenschaften sicherzustellen. Dafür braucht es laut Alpex-F&E-Chef Bernhard Rittenschober zwar zusätzliche Werkzeugsätze, aber nur eine einzige Press- und Spritzeinheit. Er erklärt, dass die zusätzlichen Werkzeugkosten durch niedrigere Prozess- und Pressenkosten ausgeglichen werden und selbst bei einem geringen Volumen von 500-1.000 Teilen/Jahr schnell amortisiert werden können.
„Die wichtigste Errungenschaft dieser Demonstratoren ist die Fähigkeit, primäre Flugzeugstrukturen mit einer kurzen Harzinjektion herzustellen, im Vergleich zu herkömmlichen RTM-Prozessen für die Luft- und Raumfahrt, bei denen es ein schwieriger und langwieriger Prozess war, Harz in so große Teile mit UD-Kohlefaserverstärkungen zu infiltrieren“, sagt Pagnac . „Wir stehen erst am Anfang dessen, was wir mit dieser intelligenten automatisierten Preforming- und C-RTM-Verarbeitung erreichen können“, ergänzt Chevallet. „Es hat das Potenzial, eine kostengünstigere und nachhaltigere Produktion von versteifungsintegrierten Außenhautstrukturen zu erreichen, die für zukünftige Flugzeuge ins Auge gefasst werden.“
Harz
- 3D-Druckmaterialien für die Raumfahrt?
- Drei Möglichkeiten, wie Unternehmen Verbundwerkstoffe in der Luft- und Raumfahrt für die Zukunft einsetzen
- Henkel bietet Werkstoffplattform für die additive Fertigung
- Materials:Lightweight Honeycomb Production Technology auf der K 2019
- Materialien:Flammhemmendes Hochtemperatur-Polyamid für den 3D-Druck
- Vorbereitung auf eine autonome Zukunft
- Trelleborg gibt neuen Distributor für Werkzeugmaterialien an
- Arkema Inc. baut US-PEKK-Produktionsanlage
- 10 stärkste Materialien für den 3D-Druck
- Materialien für Invar 36-Komponenten