Automatisiertes Preforming, Teil 7:Fill Gesellschaft
Dies ist der letzte Teil einer siebenteiligen Serie über Preforming. Um mehr über diese Serie zu erfahren, klicken Sie auf die folgenden Links:
QUELLE:Fill Gesellschaft
Automatisierungs-Fallgeschichten
Die ersten Maschinen von Fill wurden entwickelt, um die Skiproduktion für Fischer zu automatisieren. Heute braucht es 25 Prozent der Arbeiter, um 80 Prozent des ursprünglichen Jahresproduktionsvolumens zu produzieren. Beachten Sie auch, dass Ski ein Hybriddesign sind, das aus Schichten aus Glas- und/oder Kohlefaserverbundstoff, Holzkernen, Stahlkanten und verschiedenen Kunststoffarten besteht.
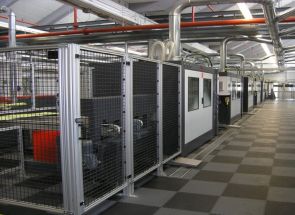
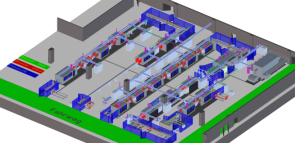
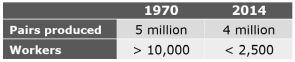
Fill hat geliefert mehrere Generationen von automatisierten Anlagen zur Herstellung von Verbundskiern.
QUELLE:Fill Gesellschaft 2017 CAMX Präsentation.
BMW
Als BMW den i3, i8 und die neuen 7er-Modelle entwickelte, die alle kohlenstofffaserverstärkte Kunststoffe (CFK) verwenden, lieferte Fill eine Reihe von Automatisierungslösungen.
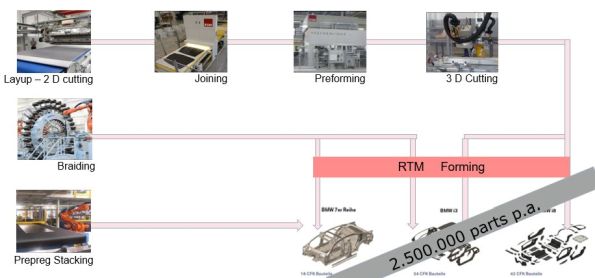
QUELLE:Fill Gesellschaft 2017 CAMX Präsentation
Monocoques aus Verbundwerkstoff
Darüber hinaus entwickelte Fill eine einzigartige Produktionslinie für Mubea CarboTech, mit der CFK-Monocoques für zwei verschiedene Automodelle hergestellt werden können:den Volkswagen VW XL1 und den Porsche 918 Spyder. Diese automatisierte Linie umfasste mehrteilige angetriebene Formwerkzeuge, eine High-Press-Harz-Transfer-Molding-(HP-RTM)-Presse, Nachhärtungs- und Bearbeitungsfunktionen.
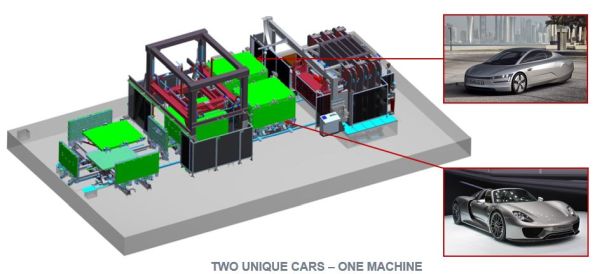
Beigestelltes ausfüllen Composite-Monocoque-Produktionslinie für Mubea CarboTech.
QUELLE:Fill Gesellschaft 2017 CAMX Präsentation
Layup automatisieren
Für das automatisierte Auflegen hat Fill Anlagen für unterschiedliche Materialien entwickelt, darunter auch Trockengewebe bis 3 m Breite (für die Serienfertigung bei BMW). Das automatische Holmverlegesystem SpeedLayer 800 für Windturbinenblätter trägt unidirektionales Kohlefaser-Prepreg mit einer Breite von bis zu 800 mm mit einer gemeldeten Geschwindigkeit von 1,5 m/s und einer Genauigkeit von ±1,5 mm auf. Es kann 600-kg-Prepreg-Rollen verarbeiten und integriert Prozessvalidierungs- und Qualitätssicherungsfunktionen.
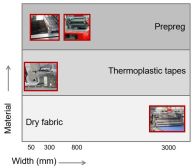
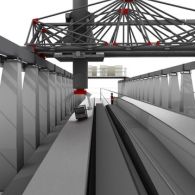
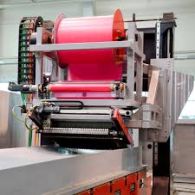
Fill wurde entwickelt eine Reihe von automatisierten Layup-Systemen (links), darunter SpeedLayer 800 für Windblattholmkappen mit UD-Carbon-Prepreg bis 800 mm Breite (rechts).
QUELLE:Fill Gesellschaft 2017 CAMX Präsentation
Das Projekt Low-Cost Flexible Integrated Composite Process (LOWFLIP) war eine 3-jährige (Okt 2013-Okt 2016) EU-finanzierte Initiative, an der Fill und neun weitere Partner beteiligt waren und die darauf abzielten, Prepreg-Layup für den aus dem Autoklaven (OOA) ausgehärteten Transport zu automatisieren Strukturen. Es bestand aus drei Demonstranten:
- 2,5 × 2,9 m Vorderwand für einen LKW-Anhänger
- 1,2 m langer Automobilquerträger
- 1,0 × 1,2 m versteiftes Flugzeugheckleitwerk
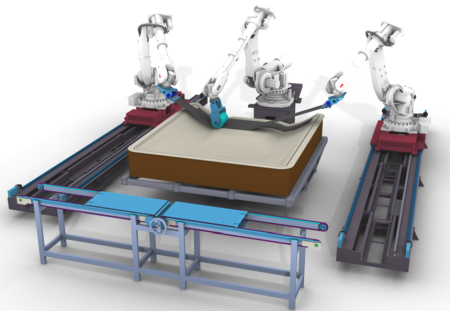
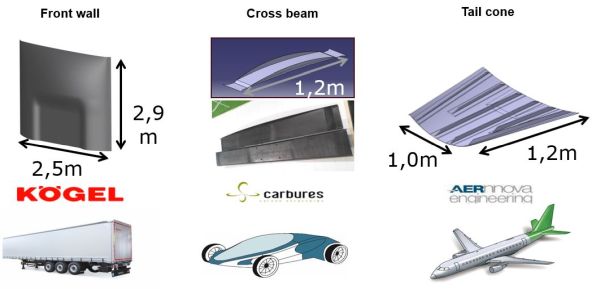
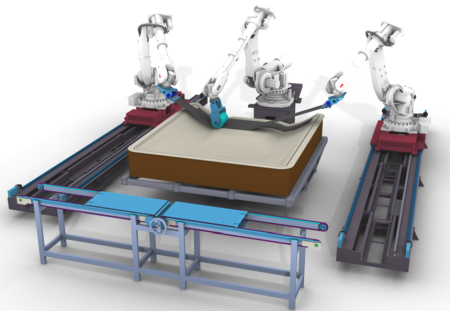
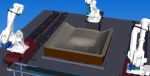
Animation
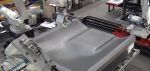
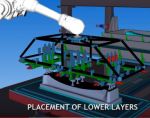
Fill arbeitete mit neun Partnern in LOWFLIP zusammen, um eine automatisierte Layup-Zelle für die Produktion großer Verbundtransportstrukturen ohne Autoklaven zu entwickeln.
QUELLE:Fill Gesellschaft 2017 CAMX Präsentation
„Wir haben das Werkzeug mit einer elektrischen Widerstandsheizung auf 120 °C erhitzt“, erinnert sich Wilhelm Rupertsberger, Leiter des Fill Kompetenzzentrums Composites and Plastics. „Das Material stand während des automatisierten Auflegens immer unter Spannung“, fügt er hinzu, „und wir erreichten ein faltenfreies Drapieren direkt in die Form. Wir haben einen menschlichen Prozess entwickelt, der jedoch Roboter verwendet, um die Wiederholbarkeit zu verbessern.“
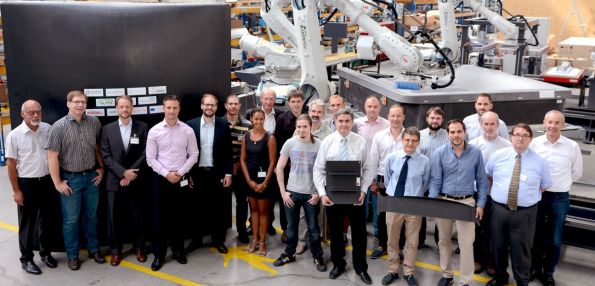
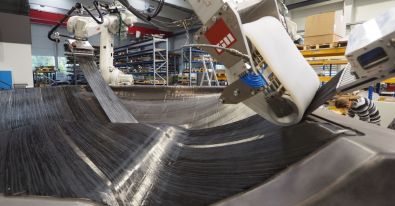
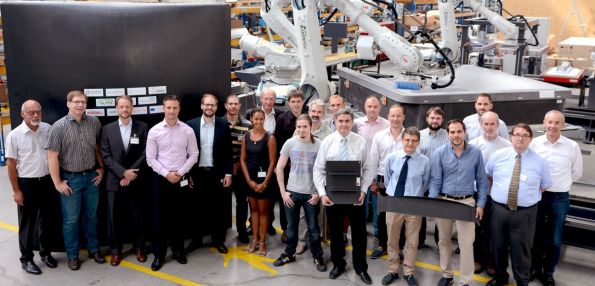
Auf dem LOWFLIP-Teamfoto oben sehen Sie die LKW-Anhängerwand auf der linken Seite sowie die Demonstratoren der Pkw-Querträger und Flugzeugheckkonus-Panels .
QUELLE:Fill Gesellschaft 2017 CAMX Präsentation
Multi-Layup zu Multilayer-System
Das Multi-Layup-System von Fill wurde für die Herstellung von Karosseriebauteilen (BIW) wie Rückwänden und unteren Stoßfängerversteifungen mit thermoplastischen Bändern entwickelt. Es war vorgesehen, dass diese Teile umspritzte Rippen und andere Merkmale aufweisen, sodass der Layup-Zyklus für den Vorformling mit dem nachfolgenden Spritzgusszyklus übereinstimmen muss.
Mein Post-Show-Blog-Beitrag von JEC 2017 enthielt ein Video des Multi-Layup-Systems, bei dem Bänder von mehreren Rollen zugeführt werden und alle Bänder, die pro Schicht benötigt werden, gleichzeitig und nicht seriell einzeln platziert werden. Auf diese Weise wurde eine Zykluszeit von 10-15 Sekunden pro Schicht erreicht.
Fill hat das System nun weiter modifiziert und in Multilayer umbenannt. Er führt, schneidet und legt bis zu 16 Bänder in Breiten bis 50 mm (je 0,01-0,04 mm Dicke) auf einen Drehtisch. Das Tapelegebett kann Teile bis 1,6 × 1,6 m herstellen. Klebebänder werden mit einer Geschwindigkeit von ≈500 m 2 . aufgebracht /h – alle 12-15 Sekunden wird eine Teileschicht in voller Größe für ungefähr eine Minute Zykluszeit pro fertigem Vorformling aufgetragen. Die Schichten werden nicht vollständig verfestigt, sondern durch thermisches Bonden verbunden. Wenn jede Spule kein Band mehr hat, wird sie automatisch gewechselt, ohne die Maschine anzuhalten.
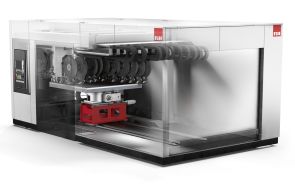
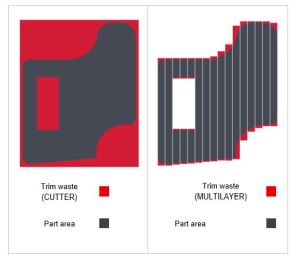
Multilayer von Fill automatisiert Das Preforming-System ermöglicht eine erhebliche Reduzierung des Beschnittabfalls, während die Bänder nur dort platziert werden, wo sie benötigt werden, und sie nach Bedarf ausrichten, um maßgeschneiderte Laminate zu erzielen.
QUELLE:Fill Gesellschaft 2017 CAMX Präsentation
Fertige Preforms werden anschließend in einer Presse konsolidiert. „Wir haben Multilayer mit einer automatisierten Konsolidierungspresse und einer Engel-Spritzgusszelle integriert, die zusammen eine Zykluszeit von 1 Minute liefern“, sagt Rupertsberger. Fill erhielt Anfang des Jahres einen Auftrag für das erste Multilayer-System von der Swinburne University of Technology (Melbourne, Australien) und wird die Ausrüstung zum ersten Mal live auf der JEC World 2019 (12.-14. März, Paris, Frankreich) demonstrieren.
RTM-Pressen und adaptive Injektion
Fill hat mehrere RTM-Druckmaschinen, einschließlich HP-RTM-Druckmaschinen, an SGL Composites geliefert.
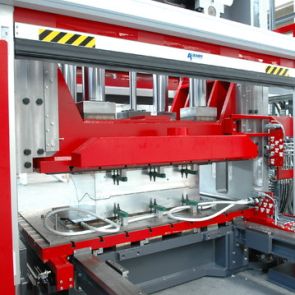
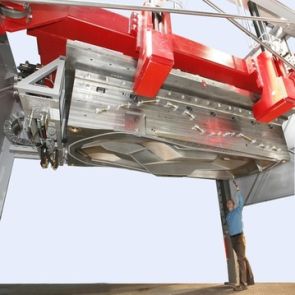
Fill hat geliefert eine Vielzahl von Pressen für die Composites-Produktion, darunter HP-RTM-Pressen bis hin zu SGL Composites (rechts).
QUELLE:Füllen Gesellschaft
Fill hat mit Airbus Operations (Stade, Deutschland) und dem Institut für Kunststoffverarbeitung (IKV) der RWTH Aachen eine innovative adaptive Spritzeinheit für RTM zunächst für Aerocomposite-Strukturen entwickelt. Bevor mit RTM hergestellte Teile in einem Flugzeug fliegen können, müssen sie einen zeit- und kostenintensiven Qualitätssicherungsprozess (QS) durchlaufen. Um diesen Prozess zu verkürzen, wurden RTM-Umformwerkzeuge mit Sensoren ausgestattet, sodass die QS inline während der Produktion eingesetzt werden kann. IKV, Airbus und Fill haben diese Sensoren nun in das Spritzsystem integriert, sodass die Ausrüstung jedes einzelnen Umformwerkzeugs entfällt. Durch die Verwendung von Einwegkartuschen, ähnlich wie Kolbeninjektionssysteme in typischen RTM-Systemen, ist die adaptive Injektionseinheit mit einer Sensorbox ausgestattet, mit der folgende Daten vor Ort gemessen und aufgezeichnet werden können:
- Temperatur
- Druck
- Harzviskosität
- Vernetzungsdichte des Harzsystems
- Glasübergangstemperatur (Tg).
Neben der Sicherstellung der Formteilqualität können diese Daten auch zur Steuerung und Steuerung des Spritzgießprozesses verwendet werden. Dieses adaptive Industrie-4.0-Einspritzsystem wird für Aerocomposites entwickelt und auch auf andere Branchen wie die Automobilindustrie ausgeweitet.
Hot-Drape-Formung
In den letzten Tour-Artikeln, die Sara Black und ich über Hochleistungs-Verbundwerkstoffe in Israel geschrieben haben, stellten wir fest, dass die meisten Unternehmen die Warmumformung verwenden. Tatsächlich sagte unser Reiseleiter Jonathan Hulaty bei Elbit Cyclone:„Ich weiß nicht, wie Sie diese Art der Hochgeschwindigkeits-Prepreg-Teileproduktion ohne Heißdrapierung durchführen“ und bezog sich dabei auf Träger und Stützen für Boeing 787-Baugruppen. Hot-Drape-Former (HDF) werden auch von FBM und Israel Aerospace Industries als unverzichtbar angesehen. Fill liefert seit Jahren HDF-Systeme, darunter mehrere Einheiten in der Produktion bei FACC. Sie sind im Wesentlichen Vakuumformsysteme, die mit Infrarot- oder anderen Arten von Heizelementen und einer wiederverwendbaren Silikonkautschukmembran ausgestattet sind, um Prepreg-Layups vor dem Aushärten auf ihren Werkzeugen zu erhitzen und zu komprimieren – debulk. HDF wird zu einem wichtigen Bestandteil der unten gezeigten kompletten Aerocomposites-Produktionslinie.
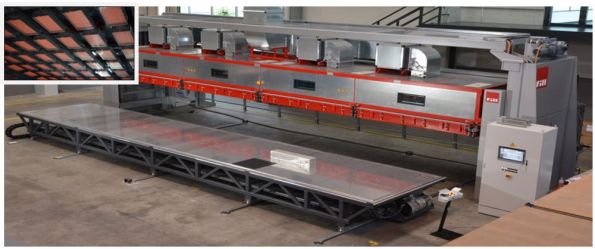
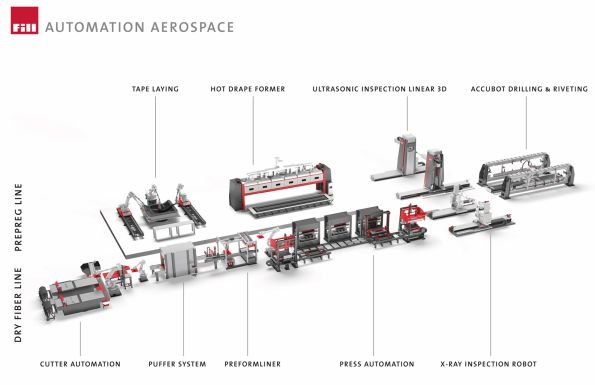
Hot-Drape-Formung hat sich zu einem wichtigen Enabler für die Massenproduktion von Prepreg-Composite-Flugzeugstrukturen entwickelt und wird von Fill als Teil seiner vollständigen Prozesskettenlösungen automatisiert. QUELLE: Fill Gesellschaft
Industrie 4.0 Produktionszellen für CFK
Ende 2013 begann Fill in Zusammenarbeit mit dem Tier-Lieferanten mit der Entwicklung einer Produktionsanlage zur Herstellung von CFK-Stringern, die zur Versteifung der Landeklappenschalen des Airbus A320 verwendet werden. Bei der Installation konnte dieses System erfolgreich die Anzahl der Stationen reduzieren, den Produktionsfluss verbessern und auch die Benutzerfreundlichkeit verbessern. Es umfasst:
- Automatische Aufbewahrung von Formwerkzeugen
- HDF-Sender
- Press-Dreh-Hebestation, wo Laminate zu Stringern verarbeitet werden.
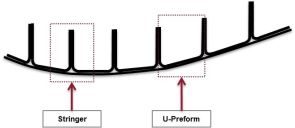
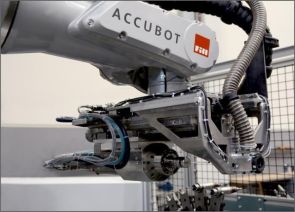
Fill hat sich entwickelt drei Generationen automatisierter Fertigungszellen (rechts) für Fahrwerksklappenstringer aus Prepreg (links).
QUELLE: Fill Gesellschaft
2017 wurde eine Anlage der zweiten Generation zur Produktion gleichartiger Teile in Betrieb genommen. Während bei der ersten Anlage die Optimierung einzelner Stationen im Vordergrund stand, zielte diese spätere Anlage auf die Minimierung manueller Tätigkeiten und die Integration der gesamten Werkzeuglogistik. Drei zentrale Entwicklungsbereiche ermöglichen diesem System der zweiten Generation eine hohe Reproduzierbarkeit und eine deutlich gesteigerte Produktivität:
- Die manuelle Entnahme und Lagerung von Umformwerkzeugen wird durch eine vollautomatische Werkzeugrückführung ersetzt, was die logistischen Prozesszeiten verkürzt. Dadurch reduziert sich auch der Platzbedarf um mehr als 50 Prozent.
- Weitere Automatisierung von Teilprozessen hat die unproduktive Zeit reduziert.
- Industrie 4.0 Digitalisierung der gesamten Erfassung und Berichterstattung. Eine von Fill entwickelte Software ermöglicht die jederzeitige Visualisierung des Prozesses und die Aufzeichnung der Historie jedes Bauteils entlang der gesamten Prozesskette. Sensoren erkennen die Verfügbarkeit von Werkzeugen und Materialien, um Engpässe zu vermeiden und Nachbestellungen zu verbessern.
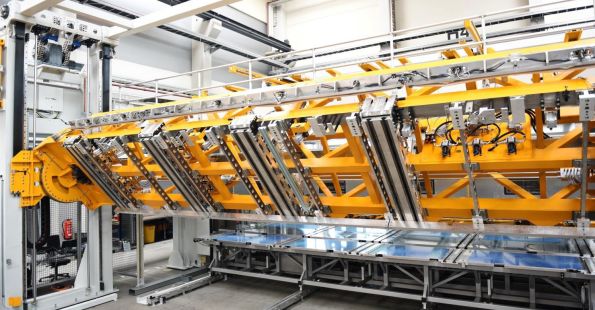
Drücken-Drehen -Hebestation in automatisierten Fertigungszellen für A320- und A350-Fahrwerksklappenstringer.
QUELLE: Fill Gesellschaft
Fill arbeitet derzeit an einem Produktionssystem der dritten Generation für Landeklappenschalen für den Airbus A350-900. Auch sie umfasst Werkzeuglager, Membranumformstation (HDF), Press-Dreh-Hebestation und automatische Werkzeugrückführung, wurde aber um ein Transportsystem für Autoklavenwerkzeuge erweitert und ersetzt bisherige Handtransportwagen und Elektroschlepper durch fahrerlose Transportsysteme (FTS .). ). Fill arbeitet bereits an zukünftigen Systemen und untersucht, wie die Zusammenarbeit von Mensch und Maschine weiter verbessert werden kann.
Akkubot
Noch bevor die Verbundwerkstoffindustrie begann, ihren zukünftigen Bedarf an einer Arbeitszelle mit mehreren Arbeitsgängen zu verbalisieren, entwickelte Fill bereits die ersten Prototypen, den sogenannten Accubot. Die Idee war, einen präzisen Roboter zu entwickeln, der einen Lasertracker zur räumlichen Kompensation sowie direkte externe Messsysteme verwendet. Dieser Roboter wäre in der Lage, Funktionen mit Endeffektoren auszutauschen und würde nicht nur eine Zelle für zerstörungsfreie Prüfung (ZfP), sondern auch eine Bearbeitungszelle. Accubot-Anwendungen umfassen:
- Bohren
- Nieten
- NDT – Ultraschall mit einer Spritze
- NDT – Röntgen
- NDT – Computertomographie
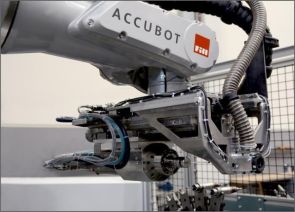
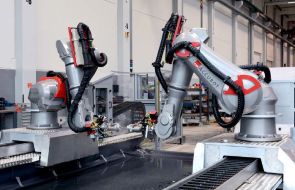
Accubot zum Bohren (links) und ZfP mit Hochgeschwindigkeits-Ultraschallscan (rechts).
QUELLE:Fill Gesellschaft.
FlexHyJoin
Fill ist Mitglied des EU-finanzierten Projekts Flexible Production Cell for Hybrid Joining (FlexHyJoin). Ziel dieses dreijährigen Programms ist die Entwicklung eines vollautomatischen Pilotprozesses zum Fügen von metallischen Halterungen/Beschlägen mit thermoplastischen Verbundwerkstoffen in Automobilanwendungen durch die Kombination von Laser- und Induktionsfügetechnologien. Fill hat die automatisierte Zelle inklusive Software und Integration der verschiedenen Technologien entworfen und gebaut.
Die Forschung und Entwicklung von Fill geht weiter. Es versteht, dass innovative und intelligente Produktionssysteme erforderlich sind, um die Herstellung von Verbundteilen wirtschaftlicher und für höhere Stückzahlen zugänglich zu machen. Und es ist bestrebt, diese Systeme entsprechend der Größe und den spezifischen Anforderungen seiner Kunden zu entwickeln.
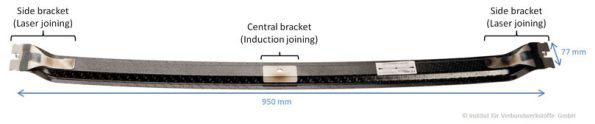
QUELLE:FlexHyJoin.
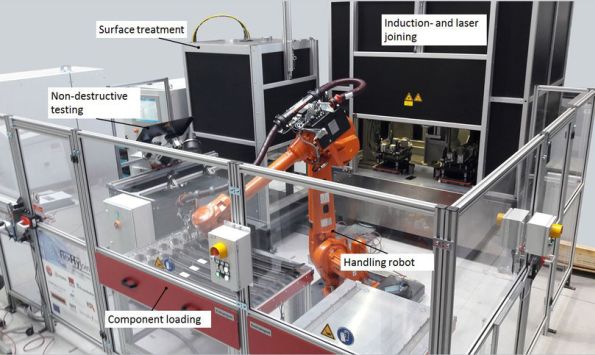
Harz
- Damm füllen
- C#-Präprozessordirektiven
- Python strftime()
- Python strptime()
- Ihre stärksten Teile mit Kohlefaser-3D-Druck – isotrope Füllung Teil 1
- Einführung in Harmonische:Teil 1
- Nachhaltigkeit in der Fertigung – Teil 3
- Drehen ist optional
- Inline, automatisierte CT-Scan-Datenprüfung von elektronischen Steckverbindern
- Zylindrizität in GD&T