Roboter ergreifen neue Fähigkeiten
Die Automatisierung bleibt ein Schwerpunkt in der Fertigung – aus all den offensichtlichen Gründen – und Roboteranbieter führen weiterhin beeindruckende neue Fähigkeiten ein. Viele würden Zach Spencer, Robotics Automation Manager bei Methods Machine Tools Inc., Sudbury, Mass., zustimmen, wenn er sagt:„Das große, aufregende Ding im Moment sind kollaborative Roboter. Cobots sind innovative Automatisierungssysteme, die neue Bearbeitungsmöglichkeiten eröffnen und Ihren Return on Investment steigern. Einige Kunden haben in weniger als drei Monaten für Cobots bezahlt.“
Spencer fügte hinzu, dass Cobots vor allem wegen ihrer intuitiven Programmierbarkeit beliebt sind. „Anstatt durch das Programmierhandgerät gehen zu müssen, um den Roboter so zu programmieren, dass er sich zu einem bestimmten Punkt bewegt, können Sie den Roboter manuell ziehen und einen Sollwert im Programmierhandgerät erstellen. Dann ziehen Sie den Roboter an die nächste Position und bestimmen den zweiten Punkt. Das ist eine der besseren Technologien mit kollaborativen Robotern.“
Die Hersteller von Cobots haben auch die Automatisierung revolutioniert, indem sie die Integration mit Zubehör von Drittanbietern erleichtert haben, darunter spezielle Greifer, Bildverarbeitungssysteme, Schweißköpfe und Betriebssoftware. Universal Robots mit Sitz in Ann Arbor, Michigan, ist mit über 300 Produkten in seinem UR+-Programm und Hunderten weiteren in der Pipeline führend auf diesem Gebiet. Senior Manager of Applications Joe Campbell nennt UR+ einen „App Store für Universal Robots. Wir geben den Entwicklern tiefen Zugriff [auf unser Betriebssystem], damit sie Software entwickeln können. Und dann validieren und testen wir es und zertifizieren es.“
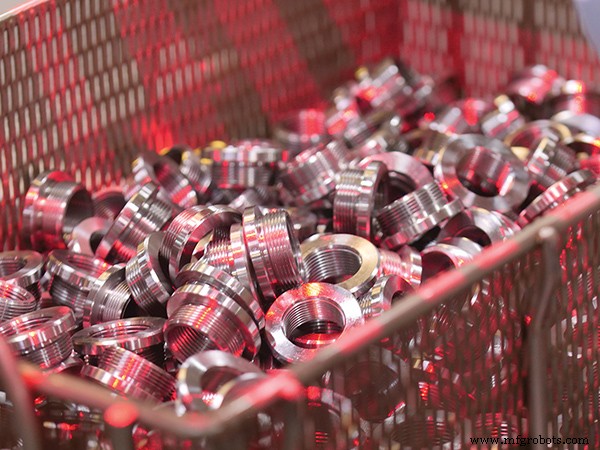
Erweiterte Bin-Picking
Die Fähigkeit eines Roboters, Teile aus einem Behälter aufzunehmen, selbst wenn sie zufällig ausgerichtet sind, ist nicht neu. Aber Anbieter wie Universal Robots erleichtern die Implementierung solcher Systeme. In der Vergangenheit, erklärte Campbell, musste man Wochen damit verbringen, Code zu schreiben, um all die verschiedenen Szenarien abzudecken, die in solchen Situationen auftreten. Aber die ActiNav-Lösung von UR enthält bereits „einen großen Teil des Codes, der über einen langen Zeitraum entwickelt wurde, der die gesamte Programmierung entfernt, die traditionell erforderlich ist, um zu definieren, wie Sie vom Abholort zum Abstellort gelangen. … Mit ActiNav bringen Sie ihm das Teil bei … bringen ihm den Abgabeort bei, … definieren den Behälter, der ihn im Wesentlichen an vier Punkten berührt, … und definieren alle anderen Barrieren im Raum. Und dann plant das System vollständig seinen eigenen Roboterweg und seine Trajektorie, um von jedem identifizierten Aufnahmepunkt zu einem Platzierungspunkt zu gelangen, ohne benutzerdefinierte Programmierung.“
Campbell fügt hinzu, dass es so einfach ist, ActiNav „das Teil beizubringen“, wie eine CAD-Datei des Werkstücks zu importieren und dann die Oberflächen zu bestimmen, an denen der Cobot es greifen soll. Das Teil muss nicht einfach sein, es muss nur „Oberflächen haben, die es Ihnen ermöglichen, eine genaue Auswahl zu treffen. Es ist sehr einfach. Ich habe gesehen, wie Leute ein brandneues Teil genommen haben, an dem das System noch nie zuvor gearbeitet hat, und es in etwa zwei Stunden aufgebaut haben.“ Darüber hinaus, so Campbell, ist ActiNav im Gegensatz zu den E-Commerce-Lösungen, die oft mit zufälligem „Griff in die Kiste“ in Verbindung gebracht werden, präzise genug, um eine Werkzeugmaschine automatisch zu beladen.
Wie Sie vielleicht erraten haben, benötigt ActiNav ein 3D-Sichtsystem, um den Cobot für jeden Pick-up auszurichten. In diesem Fall ist es ein Sensor des UR+ Partners Photoneo, Bratislava, Slowakei. Das Gerät wird über dem Behälter montiert und erzeugt fast sofort ein detailliertes Bild, sagte Campbell. (Das System erfasst 3,2 Millionen 3D-Punkte pro Scan.) Die Entscheidungs- und Ladezeit ist ebenfalls schnell, und Campbell sieht Aufträge mit einer Zykluszeit von etwa 30 Sekunden als ideal für das Produkt an. Das ist zu schnell für einen Bediener, um mehrere Maschinen zu bedienen, aber innerhalb der Verarbeitungszeit von ActiNav. Wenn die Zeit viel kürzer als 30 Sekunden ist, würde ActiNav den Maschinenzyklus verlangsamen. Natürlich gibt es auch andere Situationen, in denen Sie gerne eine langsamere Taktzeit in Kauf nehmen würden, wie zum Beispiel die Automatisierung einer sonst unproduktiven Nachtschicht.
Smart Bin Picking ist nicht auf Cobots beschränkt, und Spencer von Methods Machine Tools lieferte ein reales Beispiel, bei dem FANUC-Roboter geschmiedete Aluminium-Brennerkörper aus einem Behälter greifen und sie zur Bearbeitung in einen FANUC RoboDrill laden. Der Schlüssel ist das iRVision-System von FANUC, das eine 3D-Punktwolke der Objekte im Behälter erstellt. „Und diese Informationen beziehen sich auf den Roboter, sodass er weiß, in welchem Winkel er sich dem Teil nähern muss, um es genau auswählen zu können.“
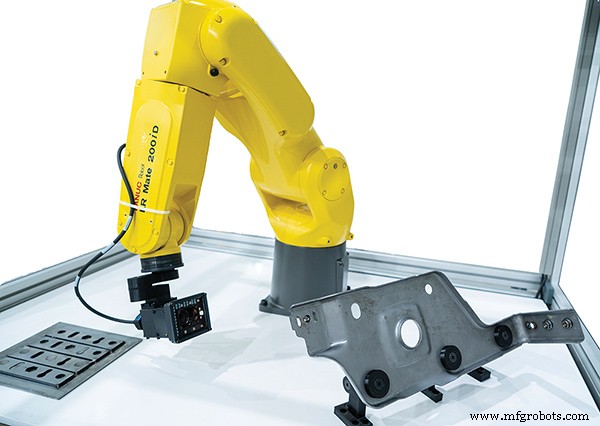
Spencer wies darauf hin, dass beim Schmieden eine Trennlinie entsteht, an der sich die beiden Gesenke treffen, und die Linie nicht immer an derselben Stelle ist. Die komplexen, konturierten Merkmale des Teils stellten eine weitere Herausforderung dar. Aber wie bei ActiNav „laden Sie ein 3D-Modell in die Software hoch und sagen ihr, dass dies die Form ist, nach der wir suchen“, erklärte Spencer. „Die Software von FANUC berücksichtigt Größenabweichungen und ermöglicht es Ihnen hervorragend, Grenzen für diese Abweichungen festzulegen.“ Der Hersteller dieser Brennerkörper aus dem Mittleren Westen wechselte von riesigen Rundtaktmaschinen mit Handbeschickung zu einer automatisierten Zelle mit vier RoboDrills, die von zwei Robotern gewartet werden. Infolgedessen produzieren sie die Teile jetzt „mit verbessertem Durchsatz, längerer Betriebszeit und einer viel geringeren Ausschussrate als auf den Transfermaschinen.“
Ein neueres Beispiel, das Spencer erwähnt, ist das automatische Laden großer Achsen für Baumaschinen von Holzkufen in die Wärmebehandlung und dann in eine Maschine. Die Achsen unterscheiden sich in Länge, Durchmesser und Gewicht (von etwa 200 bis 500 lb), und die Losgrößen sind klein. Sogar die Höhe der Holzkufen variiert, fügte Spencer hinzu. Methods schuf ein System, das es dem Bediener ermöglichte, eine 1,22 × 1,22 m (4 × 4') große Palette mit verschiedenen Achsen – alle vertikal stehend, mit der Flanschseite nach unten – einfach mit einem Gabelstapler in die Zelle zu bewegen. Dann bestimmen die FANUC-Software und 2D-Vision-Kameras, die für eine Seitenansicht ausgerichtet sind, wie weit unten die Greifer positioniert werden müssen, um jedes Teil zu greifen, während eine Overhead-Kamera die richtige Position auf dem Boden (in X und Y) bestimmt. Spencer sagte, die vertikale Positionierung sei „die große technologische Verbesserung. … Tatsächlich in der Lage zu sein, ein Bild mit einem Roboter aufzunehmen und dieses Bild zu messen [ist eine große Verbesserung.]“
Weitere Verbesserungen des Sichtsystems
Aus Campbells Sicht ist ActiNav ein Beispiel dafür, wie die heutige Robotik „unglaublich komplexe“ Technologie vor dem Benutzer verbirgt. In ähnlicher Weise sprach Mika Laitinen, Solution Sales Director bei Fastems Oy AB, Tampere, Finnland, und West Chester, Ohio, darüber, dass die Aufgabe, X- und Y-Koordinaten mit einer Kamera zu erfassen, scheinbar einfach ist, aber tatsächlich eine fortschrittliche Bildgebung erfordert Algorithmen. Er verwies beispielsweise auf den US-Kamerahersteller Cognex, dessen neueste Smart-Kamera-Veröffentlichung „neuronale Netzwerkberechnungen für bestimmte Bildgebungsalgorithmen“ verwendet. Er fügte hinzu, dass solche Systeme eine ehemals schwierige Aufgabe wie das optische Zeichenlesen in eine generische, robuste Fähigkeit verwandeln. Die Rechenkapazität dieser Systeme verbessert sich, sodass „künstliche Intelligenz kein separates Thema von Robotik ist. … Heutzutage wird künstliche Intelligenz zunehmend in intelligente Sensoren und intelligente Kamerasysteme eingebettet.“
David Bruce, Engineering Manager für das allgemeine Industrie- und Automobilsegment, FANUC America Corp., Rochester Hills, Michigan, sagte, dass die iRVision-Systeme des Unternehmens „ohne zusätzliche Hardware“ über eine integrierte Fehlerprüfung mit künstlicher Intelligenz (KI) verfügen. iRVision verfügt über eine Roboterführung auf der Grundlage von 2D- oder 3D-Bildverarbeitung, und „FANUCs hochzuverlässige Robotersteuerung“ übernimmt sowohl die Roboterbewegung als auch „die Bildverarbeitung, einschließlich der KI-Fehlerprüfungsfunktion.
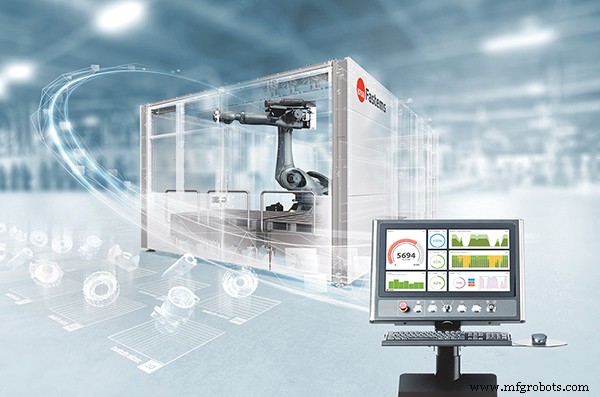
„Da iRVision weder einen PC noch eine intelligente Kamera verwendet, wirkt sich dies nicht negativ auf die Zuverlässigkeit einer Arbeitszelle aus“, fuhr Bruce fort. „Durch die Bereitstellung mehrerer Beispiele für gute und schlechte Teile unterscheidet das AI Error Proofing-Tool während des Produktionslaufs zwischen den beiden. Während des Einrichtens kann der Bediener mehrere Beispiele von Werkstücken präsentieren und sie in zwei Kategorien einteilen – gut und schlecht. Sobald der Bediener die Bilder klassifiziert hat, klassifiziert die AI Error Proofing-Funktion die Teile automatisch während der Produktionsläufe.“
Laitinen von Fastems vermutete, dass die LiDAR-Technologie (Light Detection and Ranging) letztendlich Stereo-Vision-Systeme (d. h. die Verwendung mehrerer Kameras zur Messung in X, Y und Z) ersetzen wird. „2D-Kameras sind klein, handlich und lassen sich einfach überall hinstellen. Sie können sie im Roboterhandgelenk verstecken und erhalten alle Informationen. Aber wenn Sie 3D-Vision verwenden möchten, ist die Ausrüstung viel größer und kann zusätzliche Laserprofilscanner oder eine andere Technologie umfassen, die zum Messen der dritten Koordinate verwendet wird.“
Umgekehrt sehen LiDAR-Einheiten nicht anders aus als 2D-Kameras, erfassen jedoch 3D-Daten. (Laitinen verwies ausdrücklich auf Sensoren der SICK AG, Waldkirch, Deutschland, und Minneapolis, Minn.) „Die Verwendung der LiDAR-Technologie zur Messung der X-, Y- und Z-Koordinaten mit nur einer Kamera wäre eine Art Revolution“, wie Laitinen es ausdrückte . Fastems hat ein solches System noch nicht im Einsatz, hat aber Machbarkeitsstudien mit mehreren Kunden durchgeführt.
Neue robotergestützte Messfunktionen
Die Verwendung eines Roboters zur Bedienung eines KMG oder einer Messstation ist weder überraschend noch neu, aber die Verwendung der Greifer eines Roboters zur tatsächlichen Durchführung einer Messung ist es. Laut Campbell hat New Scale Robotics, Victor, N.Y., ein UR+-Anbieter, einen Greifer entwickelt, der zusätzlich zu seiner Pick-and-Place-Funktion als hochpräziser Messschieber dient. Und es ist auf 2,5 µm genau.
Laut Campbell können die Benutzer „entweder das Teil aufheben und die Messung aufzeichnen, während das Teil gegriffen wird, oder sie können den Greifer verwenden, um über das Teil zu mikrofonieren und mehrere Stellen zu testen, bevor sie es erfassen, aufnehmen und bewegen. Es ist ein großartiges Beispiel für die Einbettung des Messverfahrens mitten in den Fertigungsprozess.“
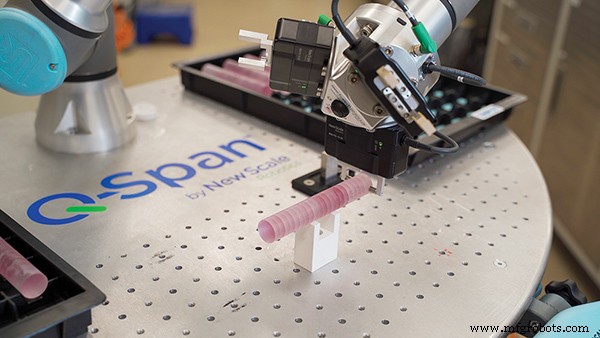
New Scale Robotics, ein Geschäftsbereich von New Scale Technologies, kombiniert den hochpräzisen Greifer mit einem UR3e-Cobot von Universal Robots, um die Q-Span Workstation zu erstellen. Ein Kunde, OptiPro Systems, Ontario, N.Y., verwendet den Q-Span für die 100-prozentige In-Prozess-Inspektion der optischen Glaszylinder, die aus seiner OptiSonic-Schleifmaschine kommen. Teile, die die Prüfung bestehen, werden zur endgültigen Validierung an ein KMG weitergeleitet. Dadurch entfallen nicht nur die zuvor vom Unternehmen durchgeführten manuellen Prüfungen, der Q-Span ist auch viermal genauer als manuelle Messschieber, was laut Hersteller zu einer strengeren Kontrolle des Herstellungsprozesses und weniger Ausschuss führt. Campbell sagte, dass die New-Scale-Greifer auch in einem Zyklus das erreichen, wofür ein Mensch sechs Schritte braucht. Außerdem kann OptiPro eine Vielzahl von Teilen mit demselben Greifersatz handhaben.
Daten vom Roboter
Laitinen stellte fest, dass das Sammeln von Servodaten über die Bewegung und den Zustand des Roboters auch zwei wichtige Vorteile bietet. Das erste ist die Möglichkeit, Trends für die vorausschauende Wartung zu untersuchen, wobei das ZDT-Programm (Zero Down Time) von FANUC ein bemerkenswertes Beispiel ist. Die zweite ist QC-bezogen, „Sammeln anwendungsspezifischer Prozessdaten und deren Verteilung an die übergeordnete Steuerungssoftware“. Dies gilt für Anwendungen, bei denen der Roboter auf das Werkstück einwirkt, anstatt eine andere Maschine zu bedienen.
Laitinen sagte, dass die Luft- und Raumfahrtindustrie gute Beispiele für den Einsatz von Robotern auf diese Weise bietet – z. „Leute in der Luft- und Raumfahrtindustrie verstehen, dass es besser ist, sich um die Kontrolle des Prozesses zu bemühen, als Teile herzustellen und anschließend die Qualität zu überprüfen“, sagte er. Es führt zu einem Verständnis der Herstellung des Teils und aller wichtigen Leistungsvariablen und wie diese Werte während des Herstellungsprozesses variieren. Richtig gemacht, verwenden sie diese Daten, um Korrekturen in Echtzeit vorzunehmen oder, falls erforderlich, einen Roboter automatisch offline zu schalten und die Arbeit an andere Einheiten umzuleiten, bevor sie fehlerhafte Teile produzieren.
„Das ist die Erfolgsgeschichte von Fastems in der Luft- und Raumfahrtindustrie. Unsere Steuerungssoftware kann sich an solche Änderungen in der Produktionslinie anpassen, ohne die Produktion zu stoppen.“ Er fügte hinzu, dass die COVID-19-Pandemie das Unternehmen gezwungen habe, Kunden außerhalb der kommerziellen Luftfahrt zu finden, und dass es diese Philosophie, „den Prozess und nicht das Teil zu messen“, auf die neuen Kunden überträgt.
Kooperative Roboter
Es ist schon lange so, dass einige automatisierte Linien erfordern, dass ein Roboter ein Teil an einen anderen übergibt. Und beim Schweißen ist es manchmal so, dass ein Mehrachsenroboter das Teil hält, während ein anderer den Brenner bewegt, wobei beide Roboter von einer einzigen Steuerung gesteuert werden. Aber es ist relativ selten, dass mehrere Roboter dasselbe Teil bewegen. Ein solches System hat Fastems kürzlich in den USA installiert. Die Teile sind riesige Ringe mit einem Durchmesser von bis zu 2,4 m und unterschiedlichen Dicken und Gewichten. Laitinen erklärte, dass das Anheben mit einem Roboter einen sehr großen und teuren Dreipunktgreifer erfordert hätte, ganz zu schweigen von einem sehr großen Roboter, „und die Zugänglichkeit wäre sehr schwierig gewesen.“
„Stattdessen verwenden wir zwei Roboter auf derselben langen linearen Bahn [die parallel zur Produktionslinie von Werkzeugmaschinen, Waschstationen usw. verläuft]. Die Roboter bewegen sich wie ein zweiarmiger Roboter“, sagte er. „Dies wird von einer einzigen Robotersteuerung gesteuert und beide Roboter werden von einem Programm angewiesen.“ Alle Pick-and-Place-Aufgaben werden mit einfachen Zwei-Finger-Greifern erledigt, die das Teil an beiden Enden greifen, gleichzeitig anheben und bewegen.
Automatisierungssteuerung System
- Automatisierung:Neue Quelle und Möglichkeiten für kollaborative Roboter
- Spritzguss:Neue Roboter auf der Fakuma
- Neue Roboter:wirtschaftlich und erstklassig
- Neue Spitzen-Servoroboter mit Industrie 4.0-Konnektivität
- Spritzguss:Neue Modelle für wirtschaftliche Roboter
- Spritzguss:Neuer Kommissionierer, Roboter und Kartonpacker
- Spritzguss:Neue Roboter auf der K 2019
- Automatisierung:Neue Hardware und Software für kostengünstige Roboter
- Ein Überblick über die Vorteile und Fähigkeiten von Verpackungsrobotern
- RIA veröffentlicht neuen technischen Bericht über kollaborative Roboter