Integration von QK-Messdaten in Fertigungssysteme
Das Internet der Dinge (IoT) – und im weiteren Sinne die Vierte Industrielle Revolution (Industrie 4.0) – ist das allgegenwärtige neue Paradigma in der heutigen Fertigung, das tiefgreifende Auswirkungen auf die Art und Weise hat, wie Hersteller arbeiten oder zu arbeiten planen. Die Verbesserung der Gesamtanlageneffektivität (OEE) ist eine wichtige neue IoT-Anforderung, und die Optimierung der OEE erfordert genaue, aktuelle Daten im gesamten Unternehmen, einschließlich Mess- und Testdaten, die sowohl aus Qualitätslabors als auch direkt aus der Fertigung stammen.
Die Erhöhung der Geschwindigkeit, des Volumens und der Genauigkeit der Erfassung von Mess- und Inspektionsdaten ist von entscheidender Bedeutung, da sie aussagekräftige Erkenntnisse liefert, die für die Verbesserung der Effizienz und die beständige Herstellung von Qualitätsteilen unerlässlich sind. In Bezug auf das Erfassen/Sammeln von Präzisionsmessdaten für Qualitätskontrollzwecke führt der klarste Weg zu diesen Vorteilen über die drahtlose und mobile Abruftechnologie.
Drahtlose Datenerfassungssysteme sollten mobil sowie robust verschlüsselt und gesichert sein und für vielfältige Anforderungen geeignet sein, die von uneingeschränkten Entfernungen und Messgerätkompatibilität bis hin zu Benutzerfreundlichkeit und praktischer Integration in automatisierte Fertigungsabläufe reichen. Die besten drahtlosen Datenerfassungssysteme können die Produktivität drastisch steigern, das Fehlerpotenzial eliminieren, eine vollständige Dokumentation bereitstellen und den Datenerfassungsprozess automatisieren. Systeme sollten alle diese Vorteile beinhalten, egal ob sie von einem einzelnen Mitarbeiter oder in einem ganzen Unternehmen mit einem integrierten Qualitätskontrollsystem verwendet werden.
Es gibt viele Gründe, warum Hersteller genaue, zeitnahe und vollständige Mess- und Inspektionsdaten sammeln müssen. OEE-, Lean- und Six-Sigma-Initiativen erfordern vertrauenswürdige Daten, um die besten Qualitätskontrollpraktiken zu unterstützen. Hersteller – insbesondere solche in Branchen wie Medizin, Biomedizin, Luft- und Raumfahrt und Verteidigung – müssen häufig gesetzliche Anforderungen erfüllen und eine rückverfolgbare, zuverlässige Dokumentation für die Herstellung kritischer Teile bereitstellen.

Allgemeine Einschränkungen von Datenerfassungssystemen
Mögliche menschliche Fehler und Verzögerungen: Systeme, die Mitarbeiter auffordern, Schlüsselmessungen manuell zu verfolgen, erfordern eine äußerst genaue Aufmerksamkeit für Details, die viele Dutzend oder sogar Hunderte Male in einer einzigen Schicht ausgeführt werden müssen – all dies ist oft schwierig und unrealistisch, um es konsequent zu tun, selbst wenn es überhaupt erst durchgeführt wird . Bildung ist ein weiteres Problem – Mitarbeiter verfügen möglicherweise nicht über den erforderlichen Hintergrund, um Daten vollständig zu verstehen und genau zu erfassen und zu transkribieren. Vertauschte Ziffern, falsch platzierte Dezimalpunkte und ähnliche Probleme können häufig auftreten. Darüber hinaus muss ein Mitarbeiter möglicherweise die Produktionsarbeit unterbrechen, um Messungen zu erfassen und aufzuzeichnen, was die Gesamtproduktivität verringert.
Digitale Sicherheitsprobleme: Ungesicherte Netzwerke, die zur Übertragung von Messdaten verwendet werden, können Hackern einen breiteren Zugang zu den Daten eines Unternehmens verschaffen. Wenn Messdaten ohne angemessene digitale Sicherheitsmaßnahmen übertragen werden, stellt dies ein potenziell ernstes Sicherheitsrisiko dar.
Mangelnde Skalierbarkeit: Unternehmenswachstum und Diversifizierung können mehr Qualitätskontrollprozesse erfordern, die über eine Einrichtung oder mehrere Standorte verteilt sein können. Wenn ein Datenerfassungssystem nicht skalierbar ist, ist die Einrichtung separater Datenerfassungsprozesse bestenfalls zeitaufwändig, umständlich und kann zu Verwirrung, Ungenauigkeiten und verzögerter Kommunikation führen. Schlimmer noch, Produktablehnungen, Fehler und rechtliche Konsequenzen für Kunden können die Folge sein.
Unvollständige Analyse durch eine Stichprobenstrategie: Eine Stichprobenstrategie kann einfach nicht das vollständige Bild liefern, das eine 100-prozentige Messung jeder produzierten Komponente bietet. Diese Struktur, die bei einigen herkömmlichen QC-Prozessen üblich ist, kann dazu führen, dass abweichende Produktionstoleranzen nicht vorhergesagt und identifiziert werden können. Darüber hinaus ist diese Strategie nicht einmal eine Option für Branchen wie Medizin oder Militär, die eine 100-prozentige Teileprüfung und rückverfolgbare Dokumentation erfordern.
Erhöhte Wahrscheinlichkeit von Ablehnungen: Jedes abgelehnte Teil bedeutet Geld, Zeit und verlorene Ressourcen. Ohne den vollständigen Einblick, der durch eine 100-prozentige Messung bereitgestellt wird, riskieren Hersteller zusätzliche Kosten und potenziell schädliche Beziehungen zu Kunden. Wenn ein potenziell abgelehntes Teil zu einem Kunden gelangt – insbesondere zu einem, der eine strenge Einhaltung von Standards erfordert – können die Ergebnisse schwerwiegende, wenn nicht katastrophale Auswirkungen haben.
Neue Systeme verbessern, modernisieren und rationalisieren die Datenerfassung
Ein zugrunde liegendes Prinzip besteht darin, es Herstellern zu ermöglichen, große Mengen an Messdaten genau und konsistent zu erfassen, um die Anforderungen von Industrie 4.0 zu erfüllen. Die heutigen drahtlosen Messdatenerfassungssysteme sollten vollständig, skalierbar, sicher und robust für Industrie 4.0 sein. Das bedeutet, grundlegende Vorteile durch Automatisierung, einfache Bedienung, optimierte Skalierbarkeit, robuste Datenverschlüsselung und -schutz sowie uneingeschränkte Entfernungen und uneingeschränkte Nutzung für die Übertragung zu bieten. Das Ergebnis ist eine erhöhte Produktivität, weniger Fehler, die Bereitstellung einer vollständigen Dokumentation und ein zuverlässiger Datenerfassungsprozess, der durch Automatisierung angetrieben wird.
Durch den Betrieb mit der neuesten drahtlosen Netzwerktechnologie, die Kurzwellen-Funkfrequenzen verwendet, um Mobiltelefone, Computer und drahtlose elektronische Geräte miteinander zu verbinden, ermöglicht dies viel schnellere Geschwindigkeit, größere Bandbreite und größere Reichweite für einen höheren Datendurchsatz. Systeme wie diese bieten eine Vielzahl entscheidender Vorteile, darunter:
Automatisierung: Wenn Mitarbeiter wiederholt die Arbeit unterbrechen müssen, um eine Messung aufzuzeichnen, wird die Produktivität sicherlich negativ beeinflusst. Außerdem können manuelle Datenerfassungsprozesse Fehler in die Datensatzdatenbank einführen, mit dem Potenzial, die Genauigkeit erheblich zu verringern und Fehler in der Zukunft fortzusetzen. Mit den neuesten Messdatenerfassungssystemen können Messdaten auf Knopfdruck übertragen werden, was eine erhebliche Zeitersparnis bedeutet; Beispielsweise ist es mindestens viermal schneller, eine Taste zu drücken, als Daten zu schreiben und sie dann in einen Computer einzugeben.
Die Automatisierung wird während des gesamten Messdatenerfassungsprozesses der Qualitätskontrolle maximiert, wodurch die Prozesseffizienz und die Genauigkeit der erfassten Messungen verbessert werden. Funktionen wie die automatische Zeitstempelung bieten einen kritischen Kontext zu jedem Datenpunkt, der für die Rückverfolgbarkeit und Einhaltung von Qualitätskontroll-/Produktionsspezifikationen erforderlich ist. Auch das Senden einer Empfangsbestätigung an das Messwerkzeug ist hilfreich.
Geschwindigkeit: Mit Systemen, die höhere Bitraten und eine sehr schnelle Verbindung von weniger als 50 ms Datenlaufzeit sowie ein Netzwerk mit ultraniedriger Latenz verwenden, können hohe Datenmengen auch bei voller Auslastung ohne Verzögerung verarbeitet werden.
Einfache Bedienung: Die Etablierung eines Messdatenerfassungsprozesses kann auf Widerstände auf mehreren Ebenen stoßen. Für die Unternehmensleitung kann Unsicherheit darüber bestehen, ob die Einführung einer neuen Methode greifbare Vorteile bringt. Für Bediener kann es beim Erlernen eines neuen Prozesses zu einer gewissen Angst vor dem Unbekannten und Beklommenheit kommen. Um diese Bedenken auszuräumen, hat die Benutzerfreundlichkeit hohe Priorität, damit sich die Bediener schnell sicher fühlen und der Datenerfassungsprozess in kurzer Zeit optimiert wird. Die einfache Bedienung erstreckt sich beispielsweise auch auf die mobile App, wodurch die Notwendigkeit entfällt, größere Hardware, wie z. B. einen Laptop, in den Außendienst zu bringen.
Vielseitigkeit: Eine neue Netzwerktopologiestruktur kann für viele einfache oder komplexe Situationen konfiguriert werden, und es können auch verteilte entfernte Gateways verwendet werden. Der modulare Aufbau heutiger Systeme macht es einfach, einen Messdatenerfassungsprozess für die Qualitätskontrolle zu erweitern oder zu verkleinern, ohne ein neues Datenerfassungssystem erwerben zu müssen. Daten werden von Messgeräten, die entweder über eingebaute Funksender oder extern montierte Endknoten verfügen, an Gateways übertragen und können sowohl auf Android™ als auch auf iOS ® betrieben werden mobile Plattformen und Windows ® -basierte Computer einschließlich Laptops, Desktop-PCs, Thin-Client-PCs und Server. Repeater- und Bridge-Komponenten können auch direkt mit SPS und anderen seriellen Hochgeschwindigkeits-Automatisierungsgeräten verbunden werden, um Daten in Echtzeit zu erfassen oder Maschinen aus der Ferne zu bedienen.
Für die drahtlose Messung ist es äußerst produktiv, drahtlose Messgeräte zu verwenden, die eingebettete Funkgeräte enthalten, wodurch sie für die Datenerfassung einfacher zu verwenden sind. Es ist auch vorteilhaft, dass ein Messdatenerfassungssystem mit einer breiten Palette von elektronischen Präzisionswerkzeugen und Messgeräten kompatibel ist. Rucksackfunkgeräte erweitern die Funktionalität, sind unauffällig und einfach anzubringen. Anwender moderner Messdatenerfassungssysteme können im Gegensatz zu herkömmlichen Systemen mit nur einem Gateway mehrere Gateways nutzen, die als zentrale oder verteilte Punkte zur Datenerfassung dienen. Kompakte Gateways und Repeater passen problemlos in eine Handfläche.
Darüber hinaus sind Anwendungen für die Datenerfassung unglaublich vielfältig und das System sollte vielseitig genug sein, um alle diese Anwendungen abzudecken. Die neuesten Messdatenerfassungssysteme sind an nahezu jeden Anwendungsfall anpassbar, mit Beispielen, die von der Automobil- und Landwirtschaft bis hin zur 100%-Messung aller Teile und Komponenten in stark regulierten Branchen wie Verteidigung, Luft- und Raumfahrt, Medizin, Energie und mehr reichen. P>
Skalierbarkeit: Die neuesten Datenerfassungssysteme wurden entwickelt, um präzise Messdaten in einer Vielzahl von Anwendungen und Entfernungen zuverlässig und genau zu erfassen. Von nur einem oder wenigen Messwerkzeugen über kurze Entfernungen bis hin zu Konfigurationen mit vielen Messwerkzeugen, die in einer großen Fabrik Hunderte von Metern voneinander entfernt oder in mehreren Einrichtungen über eine Meile verteilt sind, können erweiterte Entfernungen und erhöhte Anwendungsanforderungen problemlos als Messdaten berücksichtigt werden Sammlungsanforderungen entwickeln und wachsen.
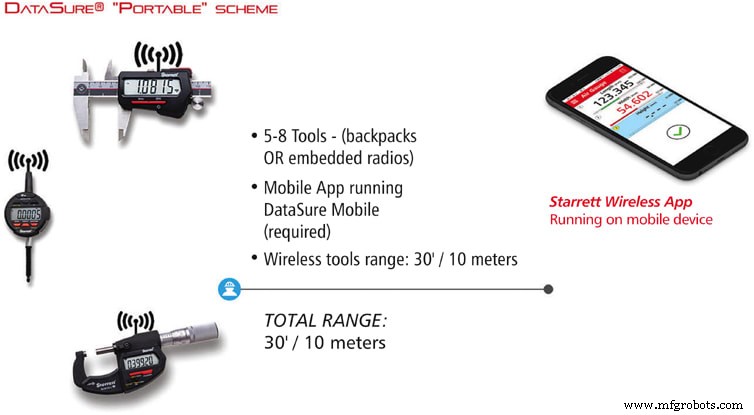
In seiner einfachsten Anwendung verfügt ein tragbares Schema über eine drahtlose App, die auf einem mobilen Gerät ausgeführt wird. Bei dieser unkomplizierten Einrichtung kann ein drahtloses Messwerkzeug mit einem eingebetteten Funkgerät Daten bis zu 10 Meter (30 Fuß) an ein mobiles Gerät übertragen. Oder, je nach mobilem Gerät, kann ein tragbares Schema 5 bis 8 Messwerkzeuge haben, die sich mit der mobilen App verbinden, um Daten bis zu 10 Meter zu übertragen. Außerdem können Benutzer Messdaten problemlos bis zu 10 Meter weit von einem (oder mehreren) drahtlosen Messgerät(en) zu einem Laptop oder PC übertragen, der über ein USB-Gateway verfügt (Abbildung 1).
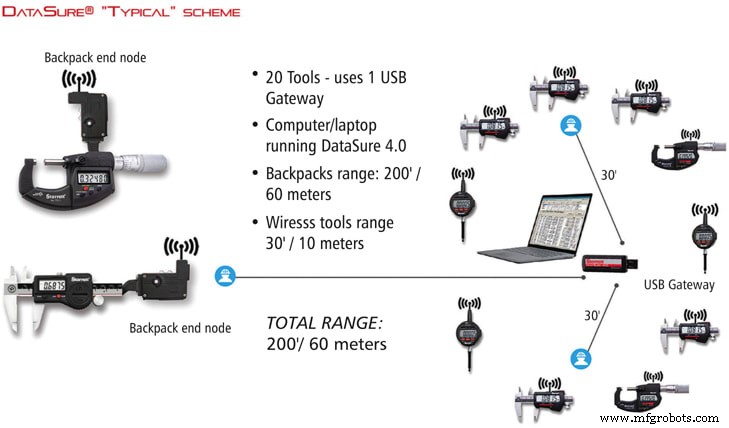
In einem typischen Schema könnte der Hersteller einen Computer oder Laptop haben, auf dem das Messdatenerfassungssystem läuft, um 20 Messwerkzeuge beim Datenerfassungsprozess über eine Entfernung von bis zu 200 Fuß zu unterstützen. In diesem Setup ist ein USB-Gateway enthalten und Rucksack-Endknoten an den Messwerkzeugen erhöhen die Übertragungsreichweite von 30 Fuß auf 200 Fuß (Abbildung 2).
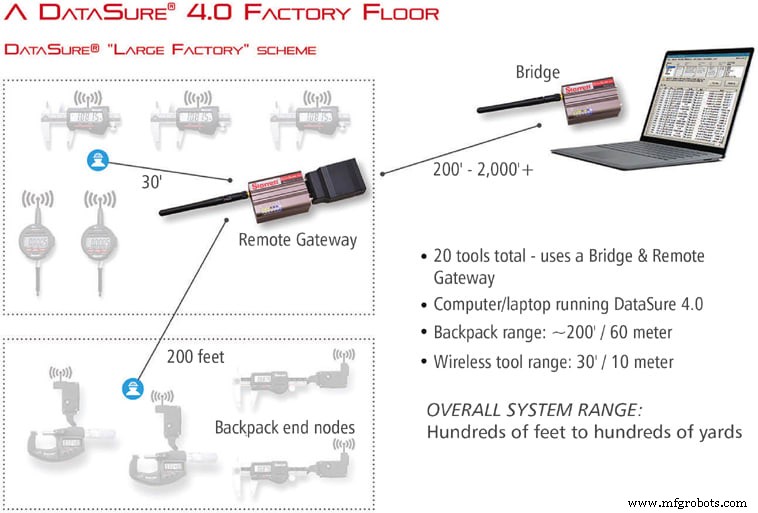
In einem Beispiel einer großen Fabrik können 20 Messgeräte eine Brücke und ein Remote-Gateway verwenden, um die gesamte Datenübertragungsreichweite auf Hunderte von Fuß oder Yards zu erweitern (Abbildung 3). Und in einem Unternehmensschema kann die Messdatenübertragung von Hunderten von Yards auf über eine Meile erhöht werden. Durch die Verwendung von Remote-Gateways, Bridges und möglicherweise das Hinzufügen von Repeatern können über 100 Messwerkzeuge integriert werden. Jedes Remote-Gateway kann 20 Messwerkzeuge unterstützen. Für noch größere Entfernungen können Yagi-Langstreckenantennen in das Schema integriert werden (Abbildung 4).
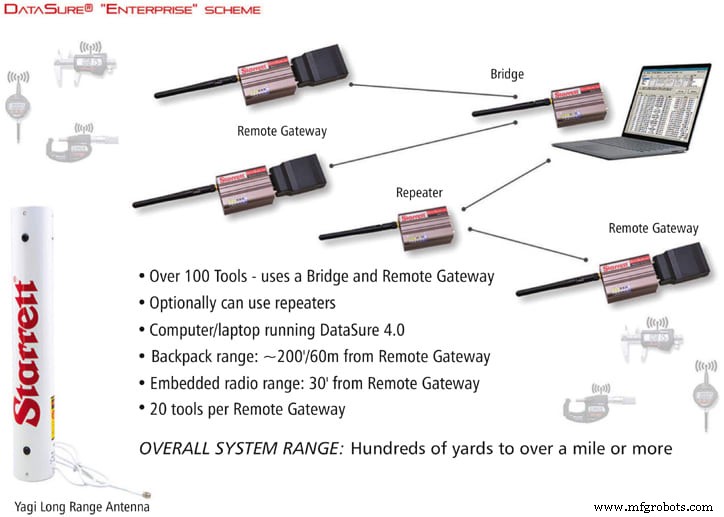
Robuste Datenverschlüsselung und -schutz: Datensicherheit ist für alle Hersteller, einschließlich Militär, oberstes Gebot. Und während Qualitätskontrollmessdaten an sich für Hacker möglicherweise nicht besonders wertvoll sind, können Cyberkriminelle immer noch die Netzwerke fälschen, die zur Übertragung von Qualitätskontrolldaten verwendet werden, um einen allgemeineren Zugriff auf die digitale Infrastruktur zu erhalten. Messdatenerfassungssysteme gehen dieses Problem durch eine Vielzahl von Maßnahmen an, einschließlich Sicherheitsbemühungen, die eine hochsichere drahtlose Plattform aufweisen. Transportierte Daten werden mit einem mehrschichtigen Ansatz verschlüsselt, der jeden Zugriff von außen auf die Daten, ob passiv oder aktiv, absolut verhindert.
Darüber hinaus verbindet sich die mobile App nicht mit dem Betriebssystem eines Smartphones oder Tablets, wodurch unbeabsichtigter Zugriff an einem kritischen Punkt eingeschränkt wird. Zur Aufrechterhaltung einer guten Sicherheit gehört auch das häufige Beheben neu auftretender Schwachstellen in der Funkübertragung, um die Systeme auch in Zukunft sicher zu halten, womit Ihr Anbieter von Messdatenerfassungssystemen Schritt halten sollte.
Uneingeschränkte Entfernungen und unbelastete Nutzung für die Übertragung: Die Nutzung von Remote-Gateways, Bridges und Repeatern bietet einen effizienten und zuverlässigen Rahmen für die Datenübertragung. Systemstrukturen können so wenige Komponenten wie einen Rucksack oder ein eingebettetes Funkgerät zusammen mit einem mobilen Gerät umfassen, auf dem die mobile App ausgeführt wird, oder Bridges, Gateways und Repeater verwenden, um die Übertragungsreichweiten in einer großen Fabrikkonfiguration erheblich zu erweitern.
Die Softwareanwendung der neuesten Messdatenerfassungssysteme verwendet ein drahtloses Netzwerk, um Informationen von mehreren Messwerkzeugen zu sammeln. Das drahtlose Netzwerk stützt sich auf die eingebettete drahtlose Technologie oder die Endknoten der Messwerkzeuge, um Daten zu sammeln und dann an den PC zurückzusenden. Das Datenerfassungssystem kann auch Signale an die Netzwerkkomponenten senden, um Übertragungen zu verifizieren und Daten anzufordern. Die Hardwarekomponenten des Systems sind USB-Gateway, Remote-Gateway, Bridge-Extender und Endknoten. Der Endknoten ist ein Funksender/-empfänger, der an ein Messwerkzeug angeschlossen wird. Das USB-Gateway ist ein an einen PC angeschlossener Funksender/-empfänger. Das Remote Gateway ist dasselbe wie das USB Gateway, erweitert aber auch die Kommunikationsreichweite vom PC, indem ein Bridge-Extender verwendet wird, um die Signale zwischen dem Remote Gateway und dem PC zu verstärken. Das Remote Gateway hat die gleiche Reichweite wie das USB Gateway, kann aber sehr weit vom PC entfernt aufgestellt werden.
Unabhängig von der eingesetzten Systemarchitektur ist das Ergebnis eine zuverlässige, genaue und schnelle Lösung zum Erfassen von Qualitätskontrollmessdaten von jedem Betriebspunkt, an dem eine Datenerfassung erforderlich ist.
Praktikum: Es ist effizient, wiederaufladbare Endknoten und drahtlose Messgeräte zu verwenden, wodurch der Batteriewechsel und die damit verbundenen Kosten entfallen. Erwägen Sie auch die Verwendung von Endknoten und drahtlosen Messwerkzeugen, die ein IP67-Schutzniveau für den Einsatz in rauen Geschäftsumgebungen bieten. Die Anpassungsfähigkeit an die meisten bestehenden SPC-, MRP- und ERP-Programme ist ein weiterer Vorteil des Messdatenerfassungssystems.
Weitere zu berücksichtigende Details und Funktionen
-
Die Betriebsreichweite von Gateways oder Mobilgeräten beträgt bis zu 10 Meter (30 Fuß) für drahtlose Messwerkzeuge.
-
Die Betriebsreichweite von Gateways beträgt bis zu 61 Meter (200 Fuß) für Rucksack-Endknoten.
-
Ein Gateway-System verwaltet bis zu 20 Messwerkzeuge, hauptsächlich Messschieber, Mikrometer und Indikatoren.
-
Zusätzliche Remote Gateways erweitern die Anzahl der unterstützten Messgeräte in Schritten von jeweils 20, und ein Repeater kann die Übertragungsreichweite auf Meilen erhöhen.
-
Endknoten-Funkgeräte können bis zu 10 Messwerte speichern, wenn das Hauptsystem ausgefallen oder beschäftigt ist.
-
Die Sendereichweite beträgt bis zu 610 Meter (2.000 Fuß) zwischen Remote Gateways und Bridge.
-
Virtuelle Multiplexer, die in dem Messdatenerfassungssystem bereitgestellt werden, nehmen viele Eingaben (Werkzeugdaten) und teilen sie über eine einzige Ausgaberessource, die ein virtueller COM-Anschluss ist. Der virtuelle Multiplexer nimmt Werkzeugdaten und sendet sie zur Verarbeitung an einen COM-Port für SPC-Software und andere SW-Pakete.
-
Fernzugriff über ein LAN auf den Datenerfassungsserver über Remote-Client-Software.
-
Optionale Antennentypen für verschiedene Einsätze.
Das Wissen, der Service und die Unterstützung des Lieferanten sind der Schlüssel bei der Auswahl eines drahtlosen Messdatenerfassungssystems. Ein umfassendes Maß an Erfahrung in Kombination mit Fachkenntnissen in der Qualitätskontrolle trägt wesentlich zu einer erfolgreichen Implementierung bei.
Dieser Artikel wurde von Jeff Wilkinson, Director, Research &Development und General Manager – Advanced Technology Division bei der L.S. Starrett Company (Athol, MA). Weitere Informationen finden Sie hier .
Sensor
- Wie man ein datengesteuerter Hersteller wird
- Datengesteuerte Fertigung ist da
- Der Wert der analogen Messung
- Integration analoger Steuerungen in IIoT-Systeme
- Arch Systems arbeitet mit Flex für die Transformation von Fertigungsdaten zusammen
- Der Einfluss von Sensoren in der Fertigung
- Integration von Cobots in die Fertigung
- Datenrekorder unterstützen Erdstaub-Mission
- Warum Rückverfolgbarkeit eine wesentliche Grundlage für IIoT-fähige Fertigungssysteme ist
- Kann KI Arbeitsplätze in der Fertigung schaffen?