Das Design der Emissionsschicht für Elektronenvervielfacher
Zusammenfassung
Die Verstärkung des Elektronenvervielfachers hängt eng mit dem Sekundärelektronenemissionskoeffizienten (SEE) der Emissionsschichtmaterialien zusammen. Der SEE hängt eng mit der Dicke der Emissionsschicht zusammen. Wenn die Emissionsschicht dünn ist, verursacht der niedrige SEE die geringe Verstärkung der Elektronenvervielfacher. Wenn die Emissionsschicht dick ist, kann die leitfähige Schicht die Ladung der Emissionsschicht nicht rechtzeitig ergänzen, und die Verstärkung des elektronischen Verstärkers ist ebenfalls gering. Die Elektronenvervielfacher wählen normalerweise Al2 O3 und MgO-Film als Emissionsschicht wegen des hohen SEE-Niveaus. Leichtes Zerfließen von MgO in Mg(OH)2 Mg2 (OH)2 CO3 und MgCO3 was zu einem niedrigeren SEE-Niveau führt. Das SEE-Niveau von Al2 O3 ist niedriger als MgO, aber Al2 O3 ist stabil. Wir haben ein kugelförmiges System zum Testen des SEE-Niveaus von Materialien entwickelt und vorgeschlagen, niederenergetische Sekundärelektronen anstelle eines niederenergetischen Elektronenstrahls zur Neutralisation zu verwenden, um das SEE-Niveau von Al2 . zu messen O3 , MgO, MgO/Al2 O3 , Al2 O3 /MgO, und steuern Sie die Filmdicke durch Verwendung von Atomlagenabscheidung genau. Wir schlagen vor, den SEE unter der Energie benachbarter einfallender Elektronen zu vergleichen, um den SEE-Wert des Materials aufzuteilen und vier empirische Formeln für die Beziehung zwischen SEE und Dicke zu erhalten. Da die Hauptmaterialien, die die Verringerung des SEE verursachen, Mg2 . sind (OH)2 CO3 und MgCO3 , verwenden wir die durch XPS gemessene Atomkonzentration des C-Elements, um die Zerfallstiefe des Materials zu untersuchen. Wir schlagen vor, das Konzept der Übergangsschicht für die SEE-Interpretation von Mehrschichtmaterialien zu verwenden. Durch Experimente und Berechnungen haben wir eine neue Emissionsschicht für Elektronenvervielfacher vorgeschlagen, einschließlich 2–3 nm Al2 O3 Pufferschicht, 5–9 nm MgO-Hauptkörperschicht, 1 nm Al2 O3 Schutzschicht oder 0,3 nm Al2 O3 Verstärkungsschicht. Wir haben diese Emissionsschicht auf eine Mikrokanalplatte (MCP) vorbereitet, was die Verstärkung von MCP signifikant verbessert. Wir können diese neue Emissionsschicht auch auf einen Kanalelektronenvervielfacher und einen separaten Elektronenvervielfacher anwenden.
Einführung
Der Sekundärelektronenemissionskoeffizient (SEE) eines Materials ist definiert als das Verhältnis der emittierten Sekundärelektronenzahl zur auf das Material einfallenden Elektronenzahl. Das Anwendungsgebiet von Sekundärelektronen ist sehr breit gefächert und gliedert sich hauptsächlich in das Gebiet der Elektronenvervielfachung, das Gebiet der Materialoberflächenzusammensetzung und Strukturanalyse und das Gebiet der Mikroentladungsunterdrückung. Das Gebiet der Elektronenvervielfachung umfasst Kanalelektronenvervielfacher (CEM), Mikrokanalplatte (MCP), separate Elektronenvervielfacher, Mikropulskanone (MPG), dielektrisches Fenster, Atomuhren usw. [1,2,3,4,5, 6,7,8,9]. Das Gebiet der Materialoberflächenzusammensetzung und Strukturanalyse umfasst Transmissionselektronenmikroskop (TEM), Rasterelektronenmikroskop (REM), Schneckenelektronenspektrometer (AES), Elektronendiffraktometer usw. [10,11,12,13]. Das Gebiet der Unterdrückung von Mikroentladungen umfasst das Problem der Elektronenwolke auf der Innenfläche des Ringbeschleunigers, die Zuverlässigkeit und Lebensdauer von Hochleistungs-Mikrowellen-Vakuumgeräten im Weltraum, den Durchbruch des dielektrischen Fensters von Hochleistungs-Mikrowellenquellen, die Aufladung/ Entladungsprobleme auf der Oberfläche des Raumfahrzeugs usw. [1, 14].
Unser Hauptforschungsgebiet ist das Anwendungsgebiet der Elektronenvervielfachung. Elektronenvervielfacher bestehen aus dem Substrat, der leitfähigen Schicht und der Emissionsschicht. Das einfallende Elektron, das auf die Emissionsschicht trifft, führt zur Erzeugung von Sekundärelektronen aus der Emissionsschicht. Das Sekundärelektron wird durch die Vorspannung weiter beschleunigt, um auf die Emissionsschicht zu treffen und zu mehr und mehr Sekundärelektronen zu führen, was zu einer Elektronenlawine und der Emission einer Elektronenwolke aus dem Ausgang führt. Die Emissionsschicht verlor eine große Menge an elektrischer Ladung aufgrund von immer mehr Sekundärelektronen, so dass die leitende Schicht für den Verlust der Elektronenemission kontinuierlich die Ladung liefert [15].
Der SEE hängt eng mit der Dicke der Emissionsschicht zusammen. Wenn die Emissionsschicht dünn ist, verursacht der niedrige SEE die geringe Verstärkung der Elektronenvervielfacher. Wenn die Emissionsschicht dick ist, kann die leitfähige Schicht aufgrund der Elektronenlawine die Ladung nicht rechtzeitig zur Verlustladung der Emissionsschicht ergänzen, was zu einer geringen Verstärkung der Elektronenvervielfacher führt. Die experimentelle Erfahrung, dass die Emissionsschicht zwischen 5 und 15 nm geeignet ist. Daher hängt die Verstärkung von Elektronenvervielfachern eng mit dem SEE-Niveau der Materialien und der Dicke der Emissionsschicht zusammen. Es wird sehr wichtig, die Dicke der Emissionsschicht und den SEE-Wert der Materialien zu untersuchen.
Es ist bekannt, dass der SEE-Wert von Al2 O3 ist sehr hoch [16]. Daher ist Al2 O3 wird üblicherweise als Emissionsschichtfilm in den Elektronenvervielfachern ausgewählt. Aber der SEE-Wert von MgO ist viel höher als der von Al2 O3 [2, 17]. Es gibt vier Gründe, warum MgO nicht ausgewählt wurde. Erstens zerfällt MgO leicht in Mg(OH)2 Mg2 (OH)2 CO3 und MgCO3 , wodurch das SEE-Niveau so niedrig wird wie das von Al2 O3 wie in Abb. 1 gezeigt; zweitens ist der Film unter dem gesättigten SEE-Niveau von MgO sehr dick (35 nm), die leitfähige Schicht kann die Ladung der Oberfläche der Emissionsschicht nicht rechtzeitig wieder auffüllen; drittens die Eigenschaften von Al2 O3 sind in der Atmosphäre lange stabil; viertens der Herstellungsprozess von Al2 O3 ist einfacher als die von MgO. Die Atomlagenabscheidung (ALD) kann einen kontinuierlichen Film ohne Pins erzeugen, hat eine ausgezeichnete Abdeckung und kann die Dicke und Zusammensetzung des Atomfilms steuern. Daher wählen wir ALD als wichtiges Vorbereitungsverfahren zur Untersuchung der Dicke der Emissionsschicht [18,19,20,21].
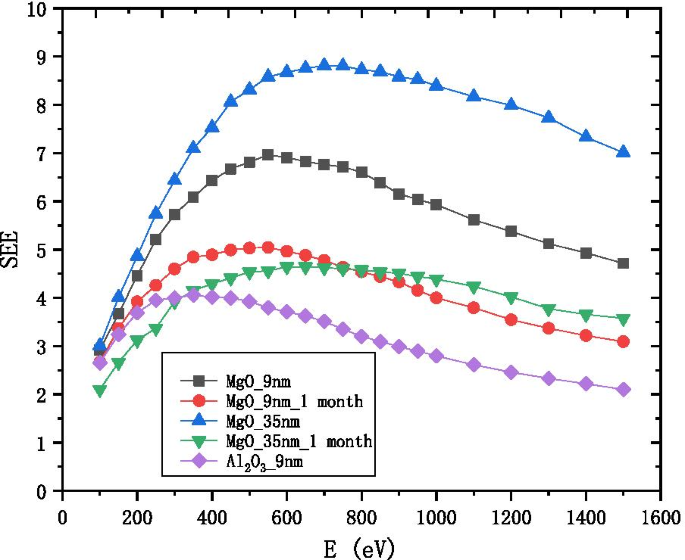
Variation des SEE von 9 nm-Al2 O3 9 nm-MgO und 35 nm-MgO mit der einfallenden Elektronenenergie und das Ergebnis gemessen nach 1 Monat Luftzerfließen der Probe
Es ist bekannt, dass die Endprodukte von zerfließendem MgO hauptsächlich Mg2 . sind (OH)2 CO3 und MgCO3 , so dass der Gehalt an C-Atomkonzentration in verschiedenen Tiefen des Materials die Zerfallstiefe von MgO widerspiegeln kann. Die Oberfläche wird durch Ar-Ionenstrahlsputtern geätzt und durch Röntgen-Photoelektronenspektroskopie (XPS) analysiert. Die beiden werden abwechselnd aufgeführt. Die Ätztiefe wird durch Steuern der Ätzzeit gesteuert, und die prozentualen Änderungen der relativen Atomkonzentration von C- und Mg-Elementen werden durch XPS erhalten. Wenn XPS den relativen Konzentrationsprozentsatz des C-Elements nicht messen kann, ist die Ätztiefe zu diesem Zeitpunkt die zerfließende Tiefe von MgO. Die obige Methode zeigt, dass die zerfließende Tiefe von MgO etwa 3,8 nm und 1 nm Al2 . beträgt O3 kann MgO vor Zerfließen schützen.
Um das SEE-Niveau von Materialien zu messen, haben viele Laboratorien auf der ganzen Welt ihre eigenen dedizierten Messgeräte gebaut, darunter das Stanford Linear Accelerator Center [14], die University of Utah [22], die Princeton University [23]; ONERA/DESP [24]; University of Science and Technology of China, Xi'an Jiaotong University, 504 Institute of Aerospace, China Spallation Neutron Source, University of Electronic Science and Technology of China usw. Wir haben ein kugelförmiges System zum Testen des SEE-Niveaus von Materialien entwickelt, um die vollständige Sammlung von Sekundärelektronen und helfen, die Genauigkeit der Messergebnisse zu verbessern. Außerdem empfehlen wir die Verwendung niederenergetischer Sekundärelektronen anstelle von niederenergetischen Elektronenstrahlen zur Neutralisation, um den SEE von Isoliermaterialien wie MgO und Al2 . zu messen O3 , es vermeidet die Nachteile der Neutralisationsdosis und Neutralisationszeit [24, 25], diese Methode ist bequem und kostengünstig.
Wir haben die Emissionsschicht des Elektronenvervielfachers mit der Idee des Hausbaus entworfen und gute Ergebnisse erzielt. Wir vergleichen den SEE-Wert unter der einfallenden Elektronenenergie der Nachbarn und verwenden diese als Standard, um das Material in einen Niedrigenergiebereich, einen Mittelenergiebereich und einen Hochenergiebereich zu unterteilen. Dies unterscheidet sich vom Bereich der Unterdrückung von Mikroentladungen [14]. Es hat sich herausgestellt, dass der mittlere Energiebereich die Interferenz der einfallenden Elektronenenergie auf den SEE-Wert eliminieren kann. Daher wird der mittlere Energiebereich als Standard ausgewählt, um das SEE-Niveau des Materials zu messen, und Al2 O3 , MgO, MgO/Al2 O3 , Al2 O3 /MgO werden untersucht, um die empirische Formel zu erhalten.
Das derzeit hauptsächlich vorgeschlagene physikalische SEE-Modell ist das Dionne-Modell [26, 27]. Das vorgeschlagene Doppelschichtmodell [28] wird weiter überarbeitet und ist für die aktuellen experimentellen Daten nicht geeignet. Daher schlagen wir vor, das Konzept der Übergangsschicht zu verwenden, um Mehrschichtmaterialien zu erklären, was eine gute Erklärung der Materialeigenschaften des Designs geben kann.
Unsere Experimente und Berechnungen haben ergeben, dass nach dem Wachsen von Al2 O3 und dann wachsendes MgO, kann das gesättigte SEE-Niveau von MgO aufgedeckt werden, wenn dieser Film dünner als der MgO-Film ist. Dies löst das Problem, dass der MgO-Film zu dick ist und die leitfähige Schicht die Ladung für die Emissionsschicht nicht ergänzen kann. Und wir fanden heraus, dass nach dem Züchten von MgO und dann dem Züchten von Al2 O3 , Al2 O3 über 3 nm zeigt nicht mehr den SEE-Spiegel von MgO an; das 1 nm Al2 O3 kann den Schäden der äußeren Umgebung durch MgO widerstehen und den SEE-Wert von MgO für lange Zeit halten; das 0,3 nm Al2 O3 kann den gesättigten SEE-Wert von MgO erhöhen. Daher schlagen wir vor, dass der Vorbereitungsprozess der neuen Emissionsschicht darin besteht, eine 9 nm große MgO-Hauptschicht auf dem 2 nm großen Al2 . wachsen zu lassen O3 Pufferschicht und wachsen dann 1 nm Al2 O3 Schutzschicht oder 0,3 nm Al2 O3 Anreicherungsschicht darauf, die das Problem der MgO-Mängel der Emissionsschicht in den Elektronenvervielfachern lösen kann. Durch das Aufwachsen dieser neuartigen Emissionsschicht im Mikrokanal der Mikrokanalplatte (eine Art Elektronenvervielfacher) haben wir die Verstärkung der Mikrokanalplatte stark verbessert. Die Designdicke dieser neuen Emissionsschicht ist von großer Bedeutung für die Verbesserung der Verstärkung und Stabilität des Elektronenvervielfachers.
Experiment und Methoden
Die Emissionsschicht mit atomarer Schichtabscheidung
Atomic Layer Deposition (ALD) ist eine Art Technologie, bei der das Precursorgas und das Reaktionsgas abwechselnd mit einer kontrollierten Geschwindigkeit in die Basaloberfläche eintreten, physikalische oder chemische Adsorption an der Oberfläche oder oberflächengesättigte Reaktion an der Oberfläche auftritt, das Material wird abgeschieden Schicht für Schicht in Form eines einzelnen Atomfilms auf der Oberfläche. ALD kann einen kontinuierlichen Film ohne Pin-Mikrokanäle herstellen, hat eine ausgezeichnete Abdeckung und kann die atomare Filmdicke und -zusammensetzung steuern. Daher wählen wir ALD als wichtige Präparationsmethode zur Untersuchung der Dicke der Emissionsschicht.
Das Folgende ist die chemische Reaktionsgleichung der Verwendung von ALD zum Züchten von Al2 O3 :
$$\begin{ausgerichtet} {\text{A}} &:{\text{Substrat}} - {\text{OH}}^{*} + {\text{Al}}\left( {{\text {CH}_{3} } \right)_{3} \to {\text{Substrat}} - {\text{O}} - {\text{Al}}\left( {{\text{CH }}_{3} } \right)_{2}^{*} + {\text{CH}}_{4} \uparrow \\ {\text{B}} &:{\text{Substrate}} - {\text{O}} - {\text{Al}}\left( {{\text{CH}}_{3} } \right)_{2}^{*} + 2{\text{H }}_{2} {\text{O}} \to {\text{Substrate}} - {\text{O}} - {\text{Al}}\left( {{\text{OH}}} \right)_{2}^{*} + 2{\text{CH}}_{4} \uparrow \\ {\text{C}} &:{\text{Al}} - {\text{OH }}^{*} + {\text{Al}}\left( {{\text{CH}}_{3} } \right)_{3} \to {\text{Al}} - {\text {O}} - {\text{Al}}\left( {{\text{CH}}_{3} } \right)_{2}^{*} + {\text{CH}}_{4 } \uparrow \\ {\text{D}} &:{\text{Al}} - {\text{CH}}_{3}^{*} + {\text{H}}_{2} { \text{O}} \to {\text{Al}} - {\text{OH}}^{*} + 2{\text{CH}}_{4} \uparrow \\ \end{aligned}$ $Wie die Gleichung von A und B bzw. C und D zeigt, war die Basalfläche ursprünglich mit –OH bedeckt. Die chemische Reaktion von –OH und Al(CH3 )3 (TMA) bildete das neue –CH3 Oberfläche und setzte CH4 . frei (Nebenprodukt). Das neue –CH3 Oberfläche, die Wasserdampf ausgesetzt war, erzeugte ihre Reaktion die neue –OH-Oberfläche und setzte CH4 . frei wieder. Die Reaktionstemperatur beträgt 200 °C. Zeitpunkt und Reihenfolge des Wachstums einer Schicht von Al2 O3 Atom wie in Abb. 2 gezeigt:
$${\text{TMA/N}}_{2} {\text{/H}}_{2} {\text{O/N}}_{2} =0.1\sim 1{\text{s }}/5\sim 45{\text{s}}/0.1\sim 1{\text{s}}/5\sim 45{\text{s}}{.}$$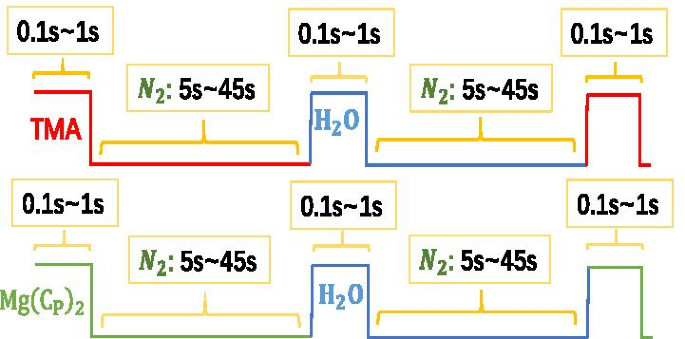
Schematische Darstellung des Wachstumsprozesses von Al2 O3 und MgO
Das Folgende ist die chemische Reaktionsgleichung der Verwendung von ALD zum Züchten von MgO:
$$\begin{aligned} {\text{E}} &:{\text{Substrat}} - {\text{OH}}^{*} + {\text{Mg}}\left( {{\text {C}}_{5} {\text{H}}_{5} } \right)_{2} \to {\text{Substrat}} - {\text{O}} - {\text{MgC }}_{5} {\text{H}}_{5}^{*} + {\text{C}}_{5} {\text{H}}_{6} \uparrow \\ {\ text{F}} &:{\text{Substrat}} - {\text{O}} - {\text{MgC}}_{5} {\text{H}}_{5}^{*} + {\text{H}}_{2} {\text{O}} \to {\text{Substrat}} - {\text{OH}}^{*} + {\text{C}}_{5 } {\text{H}}_{6} \uparrow \\ {\text{G}} &:{\text{Mg}} - {\text{OH}}^{*} + {\text{Mg }}\left( {{\text{C}}_{5} {\text{H}}_{5} } \right)_{2} \to {\text{Mg}} - {\text{ O}} - {\text{MgC}}_{5} {\text{H}}_{5}^{*} + {\text{C}}_{5} {\text{H}}_ {6} \uparrow \\ {\text{H}} &:{\text{Mg}} - {\text{C}}_{5} {\text{H}}_{5}^{*} + {\text{H}}_{2} {\text{O}} \to {\text{Mg}} - {\text{OH}}^{*} + {\text{C}}_{ 5} {\text{H}}_{6} \uparrow \\ \end{aligned}$$Wie die Gleichung von E und F bzw. G und H zeigt, war die Basalfläche ursprünglich mit \(-{\text{OH}}\) bedeckt. Die chemische Reaktion von \(-{\text{OH}}\) und \({\text{Mg}}\left( {{\text{C}}_{5} {\text{H}}_{5} } \right)_{2}\)(\({\ text{Mg}}\left( {{\text{C}}_{{\text{P}}} } \right)_{2}\)) bildete das neue \(- {\text{C}} _{5} {\text{H}}_{5}\) Oberfläche und freigesetzter \({\text{C}}_{5} {\text{H}}_{6}\) (Nebenprodukt) . Die neue \(- {\text{C}}_{5} {\text{H}}_{5}\) Oberfläche, die Wasserdampf ausgesetzt war, ihre Reaktion erzeugte das neue \(- {\text{OH}} \) Oberfläche und löste \({\text{C}}_{5} {\text{H}}_{6}\) wieder.
Wir erhitzen \({\text{Mg}}\left( {{\text{C}}_{{\text{P}}} } \right)_{2}\) auf 60 °C, um daraus Staub. Die Temperatur der Reaktionskammer beträgt 200 °C. Die Zeit und Reihenfolge des Wachstums einer Schicht aus MgO-Atom, wie in Abb. 2 gezeigt:
$${\text{Mg}}\left( {{\text{Cp}}} \right)_{2} {\text{/N}}_{2} {\text{/H}}_{ 2} {\text{O/N}}_{2} =0,1\sim 1{\text{s}}/5\sim 45{\text{s}}/0,1\sim 1{\text{s} }/5\sim 45{\text{s}}{.}$$Das Design der Emissionsschicht
Die Proben werden auf vier Arten hergestellt, wie in Fig. 3 gezeigt:verschiedene Dicken von \({\text{Al}}_{2} {\text{O}}_{3}\) auf einem Si-Wafer wachsen lassen; verschiedene Dicken von MgO auf einem Si-Wafer wachsen lassen; unterschiedliche Dicken von \({\text{Al}}_{2} {\text{O}}_{3}\) auf Si-Wafer wachsen lassen und dann feste Dicken von MgO wachsen lassen; wachsen eine feste Dicke von MgO auf dem Si-Wafer und wachsen dann eine andere Dicke von \({\text{Al}}_{2} {\text{O}}_{3}\). Wir haben verschiedene Dicken von \({\text{Al}}_{2} {\text{O}}_{3}\) auf Si-Wafer (1 nm, 3 nm, 7 nm, 9 nm, 30 nm .) gewachsen , 50 nm). Wir haben verschiedene Dicken von MgO auf Si-Wafern gezüchtet (1 nm, 3 nm, 5 nm, 9 nm, 15 nm, 20 nm, 35 nm). Wir wachsen verschiedene Dicken von \({\text{Al}}_{2} {\text{O}}_{3}\) auf einem Si-Wafer (0,6 nm, 1 nm, 3 nm, 30 nm) und wachsen dann feste Dicken von MgO (9 nm). Wir wachsen eine feste Dicke von MgO auf dem Si-Wafer (35 nm) und wachsen dann eine andere Dicke von \({\text{Al}}_{2} {\text{O} }_{3}\) (0,3 nm, 0,6 nm, 1 nm, 3 nm, 5 nm, 7 nm, 10 nm, 20 nm).
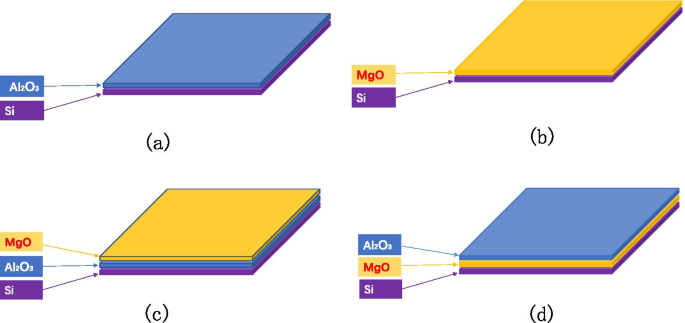
Erforschung des Zusammenhangs zwischen Schichtdicke und SEE durch das Design des Emissionsschichtexperiments
Die neue Testmethode für SEE
Wir verwenden die Kollektormethode, um zu messen, wie in Abb. 4 gezeigt:Verbinden Sie zuerst den Probentisch mit dem Kollektor, der vom Pikoamperemeter gemessene Strom ist der einfallende Elektronenstrom, bezeichnet als \(I_{{\text{p}}}\ ); Trennen Sie unter den gleichen Störfallbedingungen die Probe und den Kollektor. Zu diesem Zeitpunkt ist der gemessene Strom am Kollektor der Sekundärelektronenstrom, bezeichnet als \(I_{{\text{s}}}\).
$${\text{SEE}} =\frac{{I_{{\text{s}}} }}{{I_{{\text{p}}} }}$$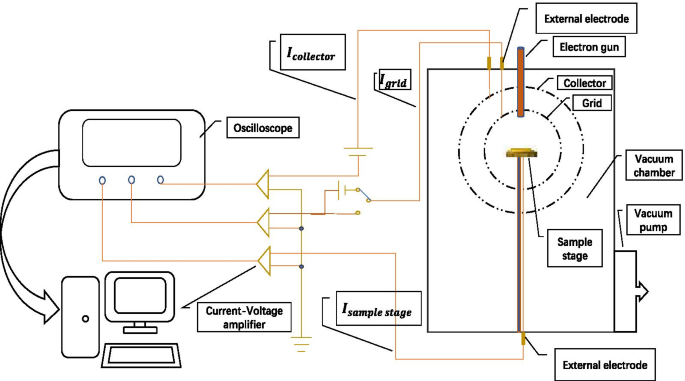
Schematische Darstellung des Sekundärelektronen-Emissions-Effizienzsystems
Wir haben das Gerät in einer global geformten Struktur entwickelt, um die vollständige Sammlung von Sekundärelektronen zu gewährleisten und die Genauigkeit der Messergebnisse zu verbessern.
Wenn das Isoliermaterial von einfallenden Elektronen beschossen wird, emittiert die Oberfläche des Materials Sekundärelektronen und sammelt aufgrund des Elektronenverlusts positive Ladungen an. Die positive Ladung lässt das Potential ansteigen. Denn die Sekundärelektronen werden innerhalb weniger Nanometer der Materialoberfläche erzeugt und haben eine niedrige Energie (~ eV). Die Sekundärelektronen sind sehr anfällig für das positive Potential. Das positive Potential beeinflusst den nächsten Sekundärelektronenemissionsprozess, was zu einer Abnahme der Sekundärelektronenausbeute führt.
Um den Effekt der Ladungsakkumulation auf das Messergebnis des SEE der isolierenden Probe zu eliminieren und den SEE der isolierenden Probe genau zu messen, verwendet das traditionelle Verfahren direkt einen niederenergetischen Elektronenstrahl, um die isolierende Probe zu bestrahlen, und der positive Ladung auf der Probenoberfläche wird durch das niederenergetische Elektron neutralisiert. Die traditionelle Methode hat zwei Nachteile. Erstens muss die Neutralisationsdosis genau berechnet werden, es ist leicht, eine positive Ladung auf der Probenoberfläche aufgrund einer unzureichenden Neutralisationsdosis oder eine negative Ladung auf der Probenoberfläche aufgrund einer übermäßigen Neutralisation zu haben; zweitens muss es mit einer weiteren niederenergetischen Elektronenkanone ausgestattet werden [24, 25].
Wir schlagen vor, zur Neutralisation niederenergetische Sekundärelektronen anstelle eines niederenergetischen Elektronenstrahls zu verwenden, was die Mängel traditioneller Methoden überwindet und genaue Sekundärelektronen erhält, wie in Abb. 5 [29] gezeigt. Wir legen das zu prüfende Isolationsmuster auf die Hälfte des Probentisches und lassen die andere Hälfte leer. Der Probentisch besteht aus Edelstahl 304 und das elektrische Potenzial beträgt 0 V.
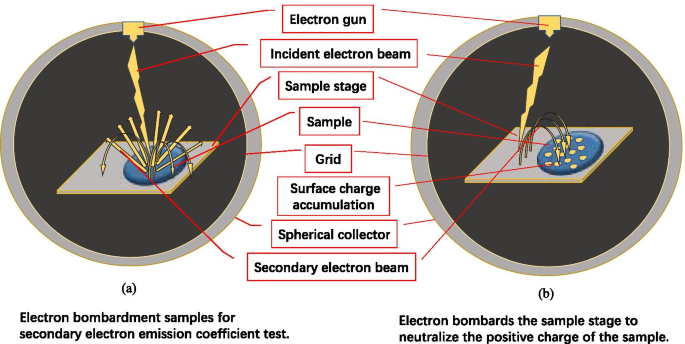
Schematische Darstellung des neuen Prüfverfahrens für den Sekundärelektronen-Emissionskoeffizienten des Materials
Beim Testen einer isolierenden Probe bombardieren die von der Elektronenkanone erzeugten Elektronen die Oberfläche der isolierenden Probe, wie in Fig. 5a gezeigt, was zu einem positiven Ladungsbereich führt, wie in Fig. 5b gezeigt. Beim Neutralisieren der Oberflächenladung der isolierenden Probe wird der halbleere Bereich des Probentischs beschossen, indem der Winkel der Elektronenkanone eingestellt wird, damit der Probentisch Sekundärelektronen emittiert, wie in Abb. 5b gezeigt.
Aufgrund der gegenseitigen Anziehung positiver Ladungen und Elektronen werden Sekundärelektronen zur Ladungsneutralisation von der Probenoberfläche angezogen. Wenn die positive Ladung abnimmt, werden weniger Elektronen angezogen. Wenn die positive Ladung auf der Probenoberfläche neutralisiert wird, kehrt die Oberfläche der isolierenden Probe in ihren ursprünglichen Zustand zurück. Da keine positive Ladung vorhanden ist, zieht es die vom Probentisch erzeugten niederenergetischen Sekundärelektronen nicht weiter an, sodass keine übermäßige Neutralisation stattfindet, die zu einer negativen Ladung der Probenoberfläche führt.
Die von uns verwendete Elektronenkanone bombardiert die Probenoberfläche jedes Mal an der gleichen Position und lenkt dann den gleichen Winkel ab, um dieselbe Position auf dem Probentisch zu beschießen, wie in Abb. 6 gezeigt. Aufgrund des Langzeit-SEE-Testprozesses ist die Position auf dem Probentisch, der lange Zeit von der Elektronenkanone beschossen wurde, wurde ein schwarzer Fleck, wie in Abb. 6 gezeigt.
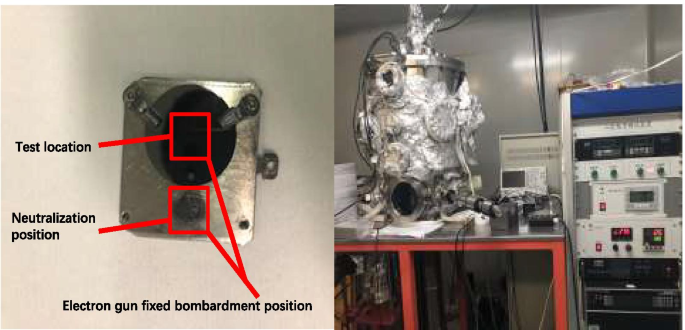
Fotos der Probe, des Probentisches und der Testausrüstung für den Sekundärelektronenemissionskoeffizienten
Ergebnis und Diskussion
SEE Zoning und Analyse
Wir vergleichen den SEE-Wert unter der Energie benachbarter einfallender Elektronen, um die Änderung von SEE mit der Energie der einfallenden Elektronen zu beschreiben und definieren sie als
$$R_{{{\text{SEE}}}} =\frac{{{\text{SEE}}\left( {x + b} \right)}}{{{\text{SEE}}\left ( {x } \right)}}$$und der SEE des Materials wird durch die Größe des \(R_{{{\text{SEE}}}}\)-Wertes in drei Bereiche unterteilt, nämlich den niederenergetischen Bereich des einfallenden Elektrons (\(R_{{{ \text{SEE}}}} \ge 1.02\)), der mittlere Energiebereich des einfallenden Elektrons (\(0.98 \le R_{{{\text{SEE}}}}} <1.02\)) und die hohe Energie Bereich des einfallenden Elektrons (\({\text{R}}_{{{\text{SEE}}}} \ge 0,98\)). Der Bereich der einfallenden Elektronenenergie des Materials, das wir zum Testen von SEE verwenden, beträgt (100 eV, 1500 eV), x die einfallende Elektronenenergie darstellt und b repräsentiert die Schrittlänge der einfallenden Elektronenenergie im SEE-Test.
\({\text{Al}}_{2} {\text{O}}_{3}\) SEE bleibt nach 7 nm grundsätzlich unverändert, wie in Abb. 7 gezeigt. Wie in Abb. 7a, b gezeigt, ist die Bereich niedriger Energie von \({\text{Al}}_{2} {\text{O}}_{3}\) liegt zwischen 100 und 250 eV, der \(R_{{{\text{SEE}}) }}\) nimmt von 1,25 auf 1,02 ab, was darauf hindeutet, dass mit zunehmender einfallender Elektronenenergie der SEE zunimmt und sich schließlich stabilisiert. Wie in Abb. 7c, d gezeigt, liegt der mittlere Energiebereich von \({\text{Al}}_{2} {\text{O}}_{3}\) zwischen 250 und 500 eV, der \( R_{{{\text{SEE}}}}\) gilt als konstant innerhalb des Intervalls von [0.98, 1.02], d. h. \(R_{{{\text{SEE}}}}\) ist ungefähr gleich bis 1, was anzeigt, dass die SEE im Wesentlichen unverändert ist, wenn die einfallende Elektronenenergie zunimmt. Wie in Abb. 7e, f gezeigt, liegt der hochenergetische Bereich von \({\text{Al}}_{2} {\text{O}}_{3}\) zwischen 500 und 1500 eV für jede Erhöhung von 200 eV der einfallenden Elektronenenergie nimmt der SEE um etwa das 0,9-fache ab.
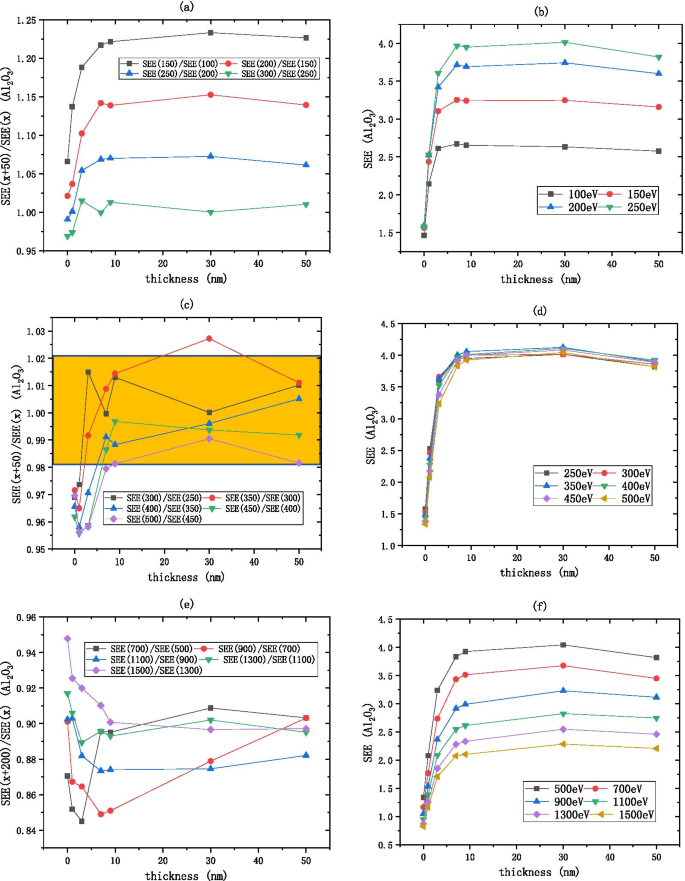
Nach Division der einfallenden Elektronenenergie durch \(R_{{{\text{SEE}}}} =\frac{{\text{SEE(x + b)}}}{{\text{SEE(x)}}} \) wie in a . gezeigt , c , e die Änderung von Al2 O3 (Auf dem Siliziumwafer wachsen xnm-Al2 O3 ) SEE mit Dicke wie im b gezeigt , d , f
Der MgO-SEE bleibt grundsätzlich nach 20 nm unverändert, wie in Abb. 9 gezeigt. Wie in Abb. 8a, b gezeigt, liegt der niederenergetische Bereich von MgO zwischen 100 und 500 eV, der \(R_{{{\text{SEE}) }}}\) von 1,3 auf 1 sinkt, was darauf hinweist, dass mit steigender einfallender Elektronenenergie der SEE zunimmt und sich schließlich stabilisiert. Wie in Abb. 8c, d gezeigt, liegt der mittlere Energiebereich von MgO zwischen 500 und 1000 eV, \(R_{{{\text{SEE}}}}}\) gilt als konstant innerhalb des Intervalls von [0,98, 1,02 ], d. h. \(R_{{{\text{SEE}}}}\) ist ungefähr gleich 1, was darauf hindeutet, dass die SEE im Wesentlichen unverändert bleibt, wenn die einfallende Elektronenenergie zunimmt. Wie in Abb. 8e, f gezeigt, liegt der Hochenergiebereich von MgO zwischen 1000 und 1500 eV. Für jede Zunahme der einfallenden Elektronenenergie um 100 eV nimmt der SEE um das 0,94-fache ab.
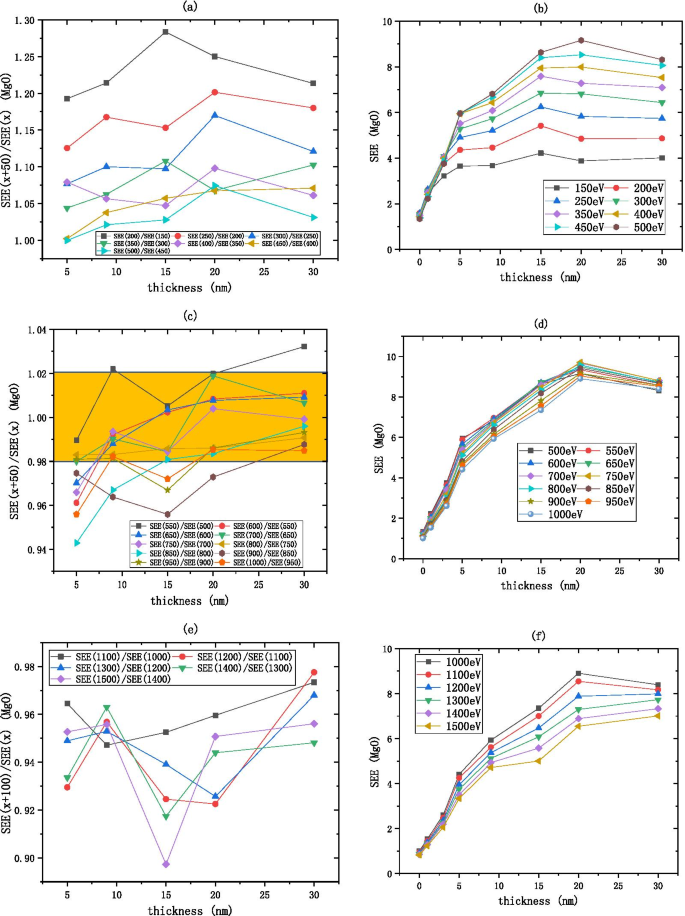
Nach Division der einfallenden Elektronenenergie durch \(R_{{{\text{SEE}}}} =\frac{{\text{SEE(x + b)}}}{{\text{SEE(x)}}} \) wie in a gezeigt , c , e die Änderung von MgO (auf dem Siliziumwafer, wachsen xnm-MgO) SEE mit Dicke wie in b . gezeigt , d , f
Wie in Abb. 9 gezeigt, haben die SEE von \({\text{Al}}_{2} {\text{O}}_{3}\)/MgO und MgO eine ähnliche Verteilung der einfallenden Elektronenenergie, die SEE von \({\text{Al}}_{2} {\text{O}}_{3}\)/MgO bleibt nach 3 nm grundsätzlich unverändert. Wie in Abb. 9a, b gezeigt, liegt der niederenergetische Bereich von \({\text{Al}}_{2} {\text{O}}_{3}\)/MgO zwischen 100 und 450 eV, der \(R_{{{\text{SEE}}}}\) sinkt von 1,4 auf 1,05, was darauf hinweist, dass mit steigender einfallender Elektronenenergie der SEE zunimmt und sich schließlich stabilisiert. Wie in Abb. 9c, d gezeigt, liegt der mittlere Energiebereich von \({\text{Al}}_{2} {\text{O}}_{3}\)/MgO zwischen 500 und 1000 eV, der \(R_{{{\text{SEE}}}}\) gilt als konstant innerhalb des Intervalls von [0.98, 1.02], d. h. \(R_{{{\text{SEE}}}}\) ist ungefähr gleich 1, was anzeigt, dass die SEE im Wesentlichen unverändert ist, wenn die einfallende Elektronenenergie zunimmt. Wie in Abb. 9e, f gezeigt, liegt der hochenergetische Bereich von \({\text{Al}}_{2} {\text{O}}_{3}\)/MgO zwischen 1000 und 1500 eV, für bei jedem Anstieg der einfallenden Elektronenenergie um 100 eV sinkt der SEE um etwa das 0,95-fache. Da der SEE von \({\text{Al}}_{2} {\text{O}}_{3}\)/MgO im mittleren Energiebereich stabil ist, kann die einfallende Elektronenenergie als Variable ausgeschlossen werden Faktor.
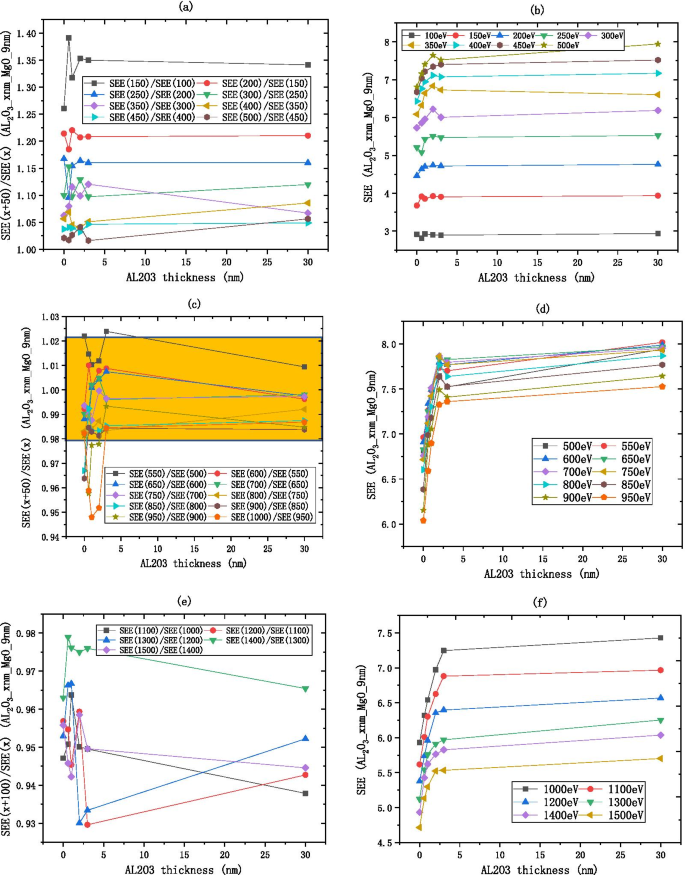
Nach Division der einfallenden Elektronenenergie durch \(R_{{{\text{SEE}}}} =\frac{{\text{SEE(x + b)}}}{{\text{SEE(x)}}} \) wie in a . gezeigt , c , e die Änderung von Al2 O3 /MgO (auf dem Siliziumwafer xnm-Al2 wachsen lassen) O3 und dann 9 nm-MgO) wachsen lassen) SEE mit einer Dicke wie in b . gezeigt , d , f
Wie in Abb. 10 gezeigt, ist der SEE von MgO/\({\text{Al}}_{2} {\text{O}}_{3}\) und \({\text{Al}}_{ 2} {\text{O}}_{3}\) haben eine ähnliche einfallende Elektronenenergieverteilung, die SEE von MgO/\({\text{Al}}_{2} {\text{O}}_{3 }\) bleibt nach 3 nm grundsätzlich unverändert. Wie in Abb. 10a, b gezeigt, liegt der niederenergetische Bereich von MgO/\({\text{Al}}_{2} {\text{O}}_{3}\) zwischen 100 und 300 eV, der \(R_{{{\text{SEE}}}}\) sinkt von 1,8 auf 1, was darauf hinweist, dass mit steigender einfallender Elektronenenergie der SEE zunimmt und sich schließlich stabilisiert. Wie in Abb. 10c, d gezeigt, liegt der mittlere Energiebereich von MgO/\({\text{Al}}_{2} {\text{O}}_{3}\) zwischen 300 und 500 eV, der \(R_{{{\text{SEE}}}}\) gilt als konstant innerhalb des Intervalls von [0.98, 1.02], wenn \({\text{Al}}_{2} {\text{O}} _{3}\) ist dünn, \(R_{{{\text{SEE}}}}\) weicht von 1 ab, und der Unterschied in SEE bei verschiedenen einfallenden Elektronenenergien ist offensichtlich; wenn \({\text{Al}}_{2} {\text{O}}_{3}\) dick ist, ist \(R_{{{\text{SEE}}}}\) nahe 1 , und der Unterschied ist nicht offensichtlich. Wie in Abb. 10e, f gezeigt, liegt der hochenergetische Bereich von MgO/\({\text{Al}}_{2} {\text{O}}_{3}\) zwischen 500 und 1500 eV, wenn \({\text{Al}}_{2} {\text{O}}_{3}\) ist dünn, \(R_{{{\text{SEE}}}}\) ist nahe 1, und der Unterschied im SEE bei unterschiedlichen einfallenden Elektronenenergien ist nicht offensichtlich; wenn \({\text{Al}}_{2} {\text{O}}_{3}\) dick ist, weicht \(R_{{{\text{SEE}}}}\) von 1 ab. und der Unterschied ist offensichtlich; für jede Erhöhung der einfallenden Elektronenenergie um 200 eV sinkt der SEE um das 0,9-fache.

Nach Division der einfallenden Elektronenenergie durch \(R_{{{\text{SEE}}}} =\frac{{\text{SEE(x + b)}}}{{\text{SEE(x)}}} \) wie in den a, c, e gezeigt , die Änderung von MgO/Al2 O3 (Auf dem Siliziumwafer wachsen 35 nm-MgO und dann xnm-Al2 O3 ) SEE mit Dicke wie in b gezeigt , d, f
Da der \({\text{Al}}_{2} {\text{O}}_{3}\) SEE im mittleren Energiebereich stabil ist, kann die einfallende Elektronenenergie als variabler Faktor ausgeschlossen werden. Wir wählen die mittlere einfallende Elektronenenergie 300 eV als Standard zur Messung des SEE-Niveaus von \({\text{Al}}_{2} {\text{O}}_{3}\), der empirischen Formel für die Dicke von \({\text{Al}}_{2} {\text{O}}_{3}\) und den besten SEE erhält man durch Anpassung wie in Abb. 11a (Tabelle 1) gezeigt.
$${\text{B}}\_{\text{SEE}}_{{{\text{Al}}_{2} {\text{O}}_{3} }} =3,99 - 2,5{ *}e^{{ - \frac{{{\text{thickness}}}}{1.73}}}$$ (1)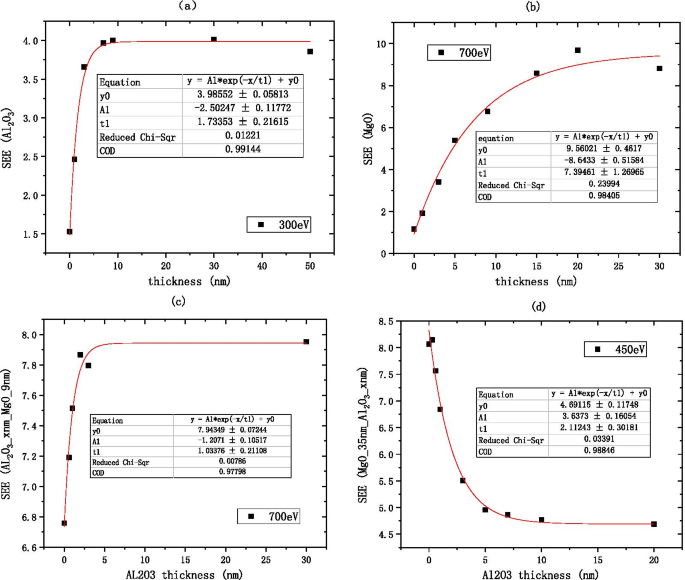
Beziehung zwischen dem besten Sekundärelektronenemissionskoeffizienten des Materials und der Filmdicke, a shows the information of Al2 O3 (on the silicon wafer, grow xnm-Al2 O3 ), b shows the information of MgO (on the silicon wafer, grow xnm-MgO), c shows the information of Al2 O3 /MgO (on the silicon wafer, grow xnm-Al2 O3 , and then grow 9 nm-MgO), and d shows the information of MgO/Al2 O3 (on the silicon wafer, grow 35 nm-MgO, and then grow xnm-Al2 O3 )
Because the MgO SEE is stable in the medium energy region, the incident electron energy can be excluded as a variable factor. We choose the medium incident electron energy 700 eV as the standard to measure the SEE level of MgO, the empirical formula for the thickness of alumina material and the best SEE is obtained by fitting as shown in Fig. 11b.
$${\text{B}}\_{\text{SEE}}_{{{\text{MgO}}}} =9.56 - 8.64*e^{{ - \frac{{{\text{thickness}}}}{7.39}}}$$ (2)Because the SEE of \({\text{Al}}_{2} {\text{O}}_{3} /{\text{MgO}}\) is stable in the medium energy region, the incident electron energy can be excluded as a variable factor. We choose the medium incident electron energy 700 eV as the standard to measure the SEE level of \({\text{Al}}_{2} {\text{O}}_{3}\)/MgO, the empirical formula for the thickness of alumina material and the best SEE is obtained by fitting as shown in Fig. 11c.
$${\text{B}}\_{\text{SEE}}_{{{\text{Al}}_{2} {\text{O}}_{3} /{\text{MgO}}}} =7.94 - 1.21\,*\,e^{{ - \frac{{{\text{thickness}}}}{1.03}}}$$ (3)Because the SEE of MgO/\({\text{Al}}_{2} {\text{O}}_{3}\) is stable in the medium energy region, the incident electron energy can be excluded as a variable factor. We choose the medium incident electron energy 450 eV as the standard to measure the SEE level of MgO/\({\text{Al}}_{2} {\text{O}}_{3}\), the empirical formula for the thickness of alumina material and the best SEE is obtained by fitting as shown in Fig. 11d.
$${\text{B}}\_{\text{SEE}}_{{{\text{MgO}}/{\text{Al}}_{2} {\text{O}}_{3} }} =4.69 + 3.64\,*\,e^{{ - \frac{{{\text{thickness}}}}{2.11}}}$$ (4) $$\frac{{{\text{B}}\_{\text{SEE}}_{{{\text{MgO}}}} \left( 9 \right)}}{{{\text{B}}\_{\text{SEE}}_{{{\text{Al}}_{2} {\text{O}}_{3} }} \left( {30} \right)}} =\frac{{9.56 - 8.64\,*\,e^{{ - \frac{9}{7.39}}} }}{{3.99 - 2.5\,*\,e^{{ - \frac{30}{{1.73}}}} }} \approx 1.755$$According to formulas 1 and 2, the SEE level of 9 nm MgO is 1.755 times higher than that of 30 nm \({\text{Al}}_{2} {\text{O}}_{3}\).
$$\begin{aligned} \frac{{{\text{B}}\_{\text{SEE}}_{{{\text{Al}}_{2} {\text{O}}_{3} /{\text{MgO}}}} \left( 3 \right)}}{{{\text{B}}\_{\text{SEE}}_{{{\text{Al}}_{2} {\text{O}}_{3} }} \left( {30} \right)}} &=\frac{{7.94 - 1.21\,*\,e^{{ - \frac{3}{{1.03}}}} }}{{3.99 - 2.5\,*\,e^{{ - \frac{{30}}{{1.73}}}} }} \approx 1.973 \\ \frac{{{\text{B}}\_{\text{SEE}}_{{{\text{Al}}_{2} {\text{O}}_{3} /{\text{MgO}}}} \left( 3 \right)}}{{{\text{B}}_{{{\text{SEE}}\,{\text{MgO}}}} \left( 9 \right)}} &=\frac{{7.94 - 1.21\,*\,e^{{ - \frac{3}{{1.03}}}} }}{{9.56 - 8.64\,*\,e^{{ - \frac{9}{{7.39}}}} }} \approx 1.124 \\ \end{aligned}$$We deposit 0–30 nm \({\text{Al}}_{2} {\text{O}}_{3}\) and redeposit 9 nm MgO on the Si wafer as the film, as shown in Fig. 12a. formulas 1 and 3 show that the SEE level of 9 nm MgO grown on 3 nm \({\text{Al}}_{2} {\text{O}}_{3}\) is 1.973 times higher than that of \({\text{Al}}_{2} {\text{O}}_{3}\). formulas 2 and 3 show that the SEE level of 9 nm MgO grown on 3 nm \({\text{Al}}_{2} {\text{O}}_{3}\) is 1.124 times higher than that of 9 nm MgO.
$$\frac{{{\text{B}}\_{\text{SEE}}_{{{\text{MgO}}/{\text{Al}}_{2} {\text{O}}_{3} }} }}{{{\text{B}}\_{\text{SEE}}_{{{\text{Al}}_{2} {\text{O}}_{3} }} }} =\frac{{4.69 + 3.64\,*\,e^{{ - \frac{1}{2.11}}} }}{{3.99 - 2.5\,*\,e^{{ - \frac{30}{{1.73}}}} }} \approx 1.743$$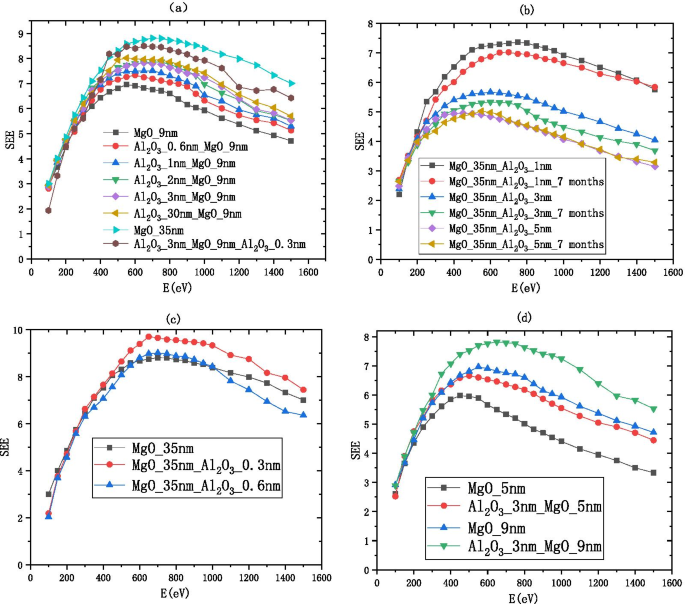
Change of secondary electron emission coefficient with different incident electron energy, a shows the information of Al2 O3 /MgO (on the silicon wafer, grow xnm-Al2 O3 , and then grow 9 nm-MgO), b shows the information of MgO/Al2 O3 and deliquescent MgO/Al2 O3 (on the silicon wafer, grow 35 nm-MgO, and then grow 1 nm-Al2 O3 ), c shows the information of MgO/Al2 O3 (on the silicon wafer, grow 35 nm-MgO, and then grow 0.3 nm-Al2 O3 ), and d shows the information of Al2 O3 /MgO (on the silicon wafer, grow 3 nm-Al2 O3 , and then grow 5 nm-MgO)
The SEE level of MgO after deliquescent drops significantly as shown in Fig. 1. Then, we deposit 35 nm MgO and redeposit 1 nm \({\text{Al}}_{2} {\text{O}}_{3}\) on the Si wafer as the film. We found the SEE of this film exposed to the air 7 months is close to the SEE without exposed to the air as shown in Fig. 12b. Formulas 1 and 3 show that the SEE level of 1 nm \({\text{Al}}_{2} {\text{O}}_{3}\) grown on MgO is 1.743 times higher than the SEE of \({\text{Al}}_{2} {\text{O}}_{3}\) and can be long-term maintain a high SEE level (no obvious deliquescence in 7 months).
$$\begin{aligned} \frac{{{\text{B}}\_{\text{SEE}}_{{{\text{MgO}}/{\text{Al}}_{2} {\text{O}}_{3} }} \left( {0.3} \right)}}{{{\text{B}}\_{\text{SEE}}_{{{\text{Al}}_{2} {\text{O}}_{3} }} \left( {30} \right)}} &=\frac{{4.69 + 3.64\,*\,e^{{ - \frac{0.3}{{2.11}}}} }}{{3.99 - 2.5\,*\,e^{{ - \frac{30}{{1.73}}}} }} \approx 1.967, \\ \frac{{{\text{B}}\_{\text{SEE}}_{{{\text{MgO}}/{\text{Al}}_{2} {\text{O}}_{3} }} \left( {0.3} \right)}}{{{\text{B}}\_{\text{SEE}}_{{{\text{MgO}}}} \left( 9 \right)}} &=\frac{{4.69 + 3.64\,*\,e^{{ - \frac{0.3}{{2.11}}}} }}{{9.56 - 8.64\,*\,e^{{ - \frac{9}{7.39}}} }} \approx 1.12 \\ \end{aligned}$$We deposited 35 nm MgO on the Si wafer and re-deposited 0.3 nm \({\text{Al}}_{2} {\text{O}}_{3}\) as a thin film as shown in Fig. 12c. It can be seen from formulas 1, 2 and 4 that the SEE level of 0.3 nm \({\text{Al}}_{2} {\text{O}}_{3}\) grown on MgO is 1.967 times higher than that of \({\text{Al}}_{2} {\text{O}}_{3}\) and 1.12 times higher than that of MgO;
The emission layer of the electron multiplier pursues thinner and higher SEE level, so we sacrificed some SEE level to make the film thinner. We deposited 3 nm \({\text{Al}}_{2} {\text{O}}_{3}\) on the Si wafer and re-deposited 5 nm MgO as a thin film as shown in Fig. 12d.
We propose to grow 2–3 nm \({\text{Al}}_{2} {\text{O}}_{3}\) as a buffer layer, grow 5–9 nm MgO as the main layer, and grow 0.3 nm \({\text{Al}}_{2} {\text{O}}_{3}\) as an enhancement layer or 1 nm \({\text{Al}}_{2} {\text{O}}_{3}\) as a protective layer as the \({\text{Al}}_{2} {\text{O}}_{3}\)/MgO/\({\text{Al}}_{2} {\text{O}}_{3}\) emissive layer of electron multipliers as shown in Fig. 13. SEE level of \({\text{Al}}_{2} {\text{O}}_{3}\)/MgO/\({\text{Al}}_{2} {\text{O}}_{3}\) emission layer (\({\text{Al}}_{2} {\text{O}}_{3}\)/MgO/\({\text{Al}}_{2} {\text{O}}_{3}\) = 3 nm/9 nm/0.3 nm) is shown in Fig. 12a. And, we tested a traditional microchannel plate with good gain and then grew \({\text{Al}}_{2} {\text{O}}_{3}\)/MgO/\({\text{Al}}_{2} {\text{O}}_{3}\) emission layer on microchannel wall of microchannel plate, and the gain result obtained by the test was significantly improved. Then, another piece of the first convention microchannel plate with close gain is grown with \({\text{Al}}_{2} {\text{O}}_{3}\) emission layer. Compared with the gain results obtained by the test, the \({\text{Al}}_{2} {\text{O}}_{3}\)/MgO/\({\text{Al}}_{2} {\text{O}}_{3}\) emission layer structure is more superior as shown in Fig. 14.
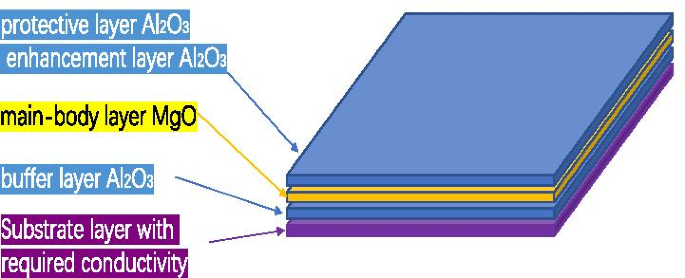
Schematic diagram of sandwich structure (Al2 O3 /MgO/Al2 O3 )
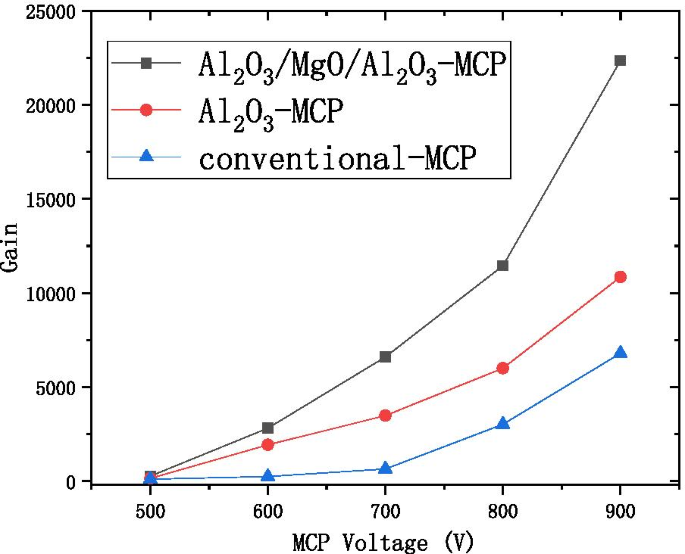
Relationship between the voltage and gain of the three microchannel plates (conventional microchannel plate, microchannel plate for growing Al2 O3 emission layer, microchannel plate for growing Al2 O3 /MgO/Al2 O3 emission layer)
XPS Characterization and Transition Layer Concept
SEE data usually uses Dionne model for fitting analysis [26, 27]. The current double-layer model based on Dionne model does not consider the existence of a transition layer between the two materials. Through the design of the emission layer structure this time, the SEE difference between \({\text{Al}}_{2} {\text{O}}_{3}\)/MgO and \({\text{Si}}\)/MgO can be clearly observed. Under the same SEE level, MgO exhibits a very large thickness difference. Sample (0.3 nm \({\text{Al}}_{2} {\text{O}}_{3}\) grown on MgO) can get a higher SEE than MgO. Sample (1 nm \({\text{Al}}_{2} {\text{O}}_{3}\) grown on MgO) maintain a high SEE level. The current double-layer model [28] can no longer explain the above phenomenon, so we put forward the concept of transition layer, there are two kinds of materials at the interface, forming two processes:the process of destroying the bottom material and the process of building the top material. The following are two X-ray photoelectron spectroscopy (XPS) test experiments to prove and the concept of transition layer to understand the SEE phenomenon of multilayer materials.
XPS test experiment 1:
First, the sample (0.3 nm \({\text{Al}}_{2} {\text{O}}_{3}\) grown on MgO) in the air for 1 year are tested for XPS as shown in Fig. 15a. We use an Ar ion gun to etch the surface of the material, and then test the various elements in the material by XPS. The two are alternately performed. The etching depth is controlled by controlling the etching time, and the relative atomic concentration percentage changes of various elements are obtained by XPS. Al element is almost undetectable after 8 s of etching as shown in Fig. 16a. The etching rate of \({\text{Al}}_{2} {\text{O}}_{3}\) is known, \({\text{Etching}}\,{\text{rate}}_{{{\text{Al}}_{2} {\text{O}}_{3} }} =0.7{\text{{\AA}/s}}\),
$$\begin{aligned} &{\text{Etching}}\_{\text{Thickness}}_{{{\text{Al}}_{2} {\text{O}}_{3} }} ={\text{Etching rate }}_{{{\text{Al}}_{2} {\text{O}}_{3} }} *{\text{Etching time}}_{{{\text{Al}}_{2} {\text{O}}_{3} }} =0.7\,{\text{{\AA}/s}}\,*\,8\,{\text{s}} =5.6{\text{\AA}} \\ &{\text{Cycle}}\_{\text{Thickness}}_{{{\text{Al}}_{2} {\text{O}}_{3} }} =1.29\,{\text{{\AA}/cycle}}\,*3\,{\text{cycle}} =3.87{\text{\AA}} \\ &{\text{Etching}}\_{\text{Thickness}}_{{{\text{Al}}_{2} {\text{O}}_{3} }}> {\text{Cycle}}\_{\text{Thickness}}_{{{\text{Al}}_{2} {\text{O}}_{3} }} \\ \end{aligned}$$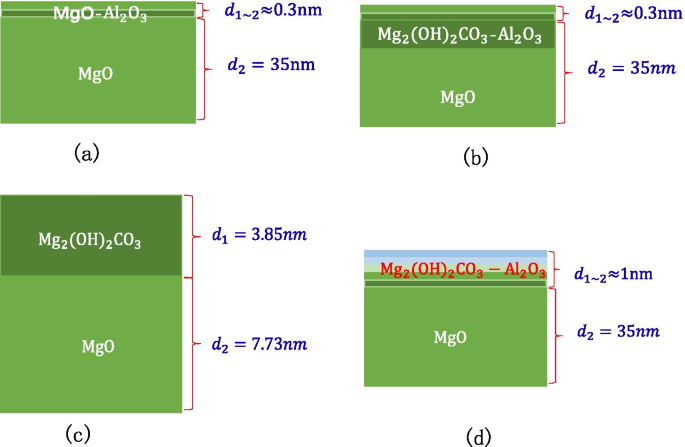
Schematic diagram of XPS test experiment sample, a shows the information of MgO/Al2 O3 (on the silicon wafer, grow 35 nm-MgO, and then grow 0.3 nm-Al2 O3 ), b shows the information of deliquescent MgO/Al2 O3 (on the silicon wafer, grow 35 nm-MgO, and then grow 0.3 nm-Al2 O3 ), c shows the information of deliquescent MgO (on the silicon wafer, grow 11 nm-MgO), d shows the information of deliquescent MgO/Al2 O3 (on the silicon wafer, grow 35 nm-MgO, and then grow 1 nm-Al2 O3 )
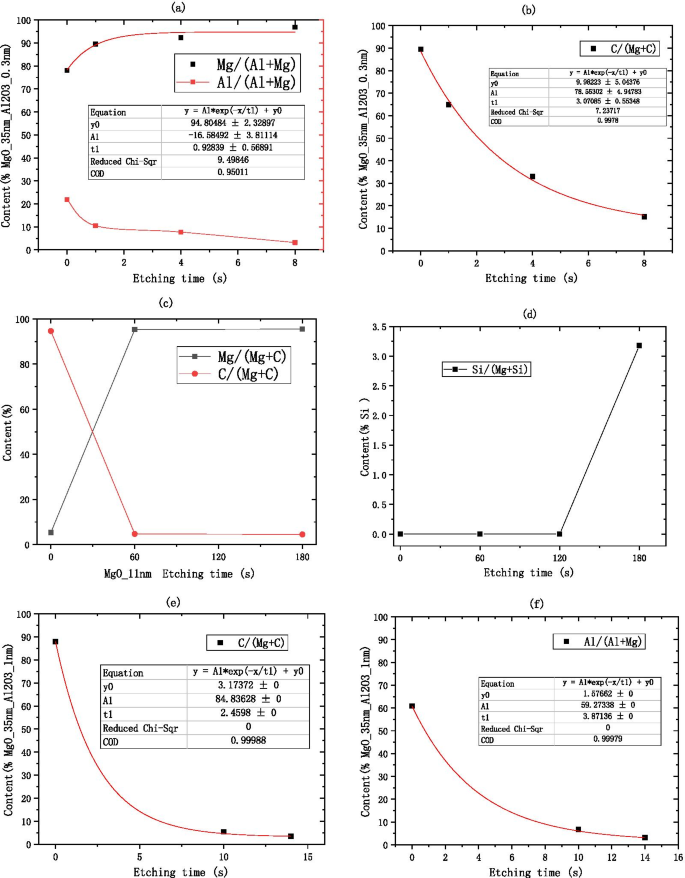
Atomic concentration percentage of C, Al, Si elements relative to Mg element obtained by XPS. a Shows the Al element information of deliquescent MgO/Al2 O3 (on the silicon wafer, grow 35 nm-MgO, and then grow 0.3 nm-Al2 O3 ), a shows the C element information of deliquescent MgO/Al2 O3 (on the silicon wafer, grow 35 nm-MgO, and then grow 0.3 nm-Al2 O3 ), c shows the C element information of deliquescent MgO (on the silicon wafer, grow 11 nm-MgO), d shows the Si element information of deliquescent MgO (on the silicon wafer, grow 11 nm-MgO), e shows the C element information of deliquescent MgO/Al2 O3 (on the silicon wafer, grow 35 nm-MgO, and then grow 1 nm-Al2 O3 ). f shows the Al element information of deliquescent MgO/Al2 O3 (on the silicon wafer, grow 35 nm-MgO, and then grow 1 nm-Al2 O3 )
Therefore, it shows that \({\text{Al}}_{2} {\text{O}}_{3}\) must exist in the MgO part, that is, \({\text{Al}}_{2} {\text{O}}_{3}\) destroys the lattice state of the MgO surface. \({\text{Al}}_{2} {\text{O}}_{3}\) forms a finite solid solution in MgO [30]. At this time, the experimentally measured SEE level increased. As we all know, the higher the SEE level, the better the insulation of the material. Due to the destruction of the surface lattice, the surface layer of MgO is more insulating, which further confirms the process of destroying the underlying material in the concept of the transition layer.
According to the results of the SEE experiment, the SEE level has dropped significantly. A small amount of \({\text{Al}}_{2} {\text{O}}_{3}\) in the top layer cannot protect the MgO in the bottom layer. MgO is still deliquescent in the air. The air contains \({\text{O}}_{2} ,{\text{H}}_{2} {\text{O}},{\text{CO}}_{2} ,{\text{CO}},{\text{N}}_{2}\), etc. When air enters MgO, the reaction of MgO and \({\text{CO}}_{2}\) and \({\text{H}}_{2} {\text{O}}\) proceeds at the same time.
$$\begin{aligned} &{\text{MgO}} + {\text{H}}_{2} {\text{O}} ={\text{Mg}}\left( {{\text{OH}}} \right)_{2} \\ &{\text{MgO}} + {\text{CO}}_{2} ={\text{MgCO}}_{3} \\ &{\text{Mg}}\left( {{\text{OH}}} \right)_{2} + {\text{CO}}_{2} \rightleftharpoons {\text{MgCO}}_{3} + {\text{H}}_{2} {\text{O}} \\ &2{\text{MgO}} + 2{\text{H}}_{2} {\text{O}} + {\text{CO}}_{2} ={\text{Mg}}_{2} \left( {{\text{OH}}} \right)_{2} {\text{CO}}_{3} \\ \end{aligned}$$The above four chemical reactions occur, the deliquescent reaction of air and MgO is mainly the reaction of MgO and \({\text{CO}}_{2}\) and \({\text{H}}_{2} {\text{O}}\) to produce \({\text{MgCO}}_{3}\) and \({\text{Mg}}_{2} \left( {{\text{OH}}} \right)_{2} {\text{CO}}_{3}\). As long as the prepared MgO is exposed to the air, \({\text{Mg}}\left( {{\text{OH}}} \right)_{2}\) will be produced. After being placed in the air for 28 days, \({\text{MgCO}}_{3}\) is the main product [31]. Because the tested MgO sample needs to be transferred to the SEE test equipment, the actual test is the SEE level of MgO–\({\text{Mg}}\left( {{\text{OH}}} \right)_{2}\). Main reason for the decrease in SEE level is the \({\text{Mg}}_{2} \left( {{\text{OH}}} \right)_{2} {\text{CO}}_{3}\) and MgCO3 produced by deliquescent. Therefore, when using XPS, C can be selected as the calibration element for the deliquescent depth of MgO in the air. As shown in Fig. 16b, after 8 s of etching, no Al content is detected, but C content is still detected, indicating that the MgO in the bottom layer continues to deliquesce and is not protected by a small amount of \({\text{Al}}_{2} {\text{O}}_{3}\) as shown in Fig. 15b.
XPS test experiment 2:
First, the MgO sample in the air for 1 year are tested for XPS. After 1 min of etching, there was almost no C element as shown in Fig. 16c, indicating that the thickness of the dense \({\text{Mg}}_{2} \left( {{\text{OH}}} \right)_{2} {\text{CO}}_{3}\) film formed was the thickness of 1 min of etching.
After etching for 3 min, the sample begins to show Si element as shown in Fig. 16d, the etching rate of MgO and the thickness of \({\text{Mg}}_{2} \left( {{\text{OH}}} \right)_{2} {\text{CO}}_{3}\) film can be calculated through these data.
$$\begin{aligned} &{\text{Etching rate }}_{{{\text{MgO}}}} =\frac{{{\text{Thickness}}_{{{\text{MgO}}}} }}{{{\text{Etching time}}_{{{\text{MgO}}}} }} =\frac{{11.58\,{\text{nm}}}}{{180\,{\text{s}}}} =0.643{\text{{\AA}/s}} \\ &{\text{Etching}}\_{\text{Thickness}}_{{{\text{Mg}}_{2} \left( {{\text{OH}}} \right)_{2} {\text{CO}}_{3} }} \approx {\text{Etching}}\_{\text{Thickness}}_{{{\text{MgO}}}} \\ &\quad ={\text{Etching rate }}_{{{\text{MgO}}}} \,*\,{\text{Etching time}}_{{{\text{MgO}}}} =0.643{\text{\AA}}/{\text{s*}}60\,{\text{s}} \approx 3.85\,{\text{nm}} \\ \end{aligned}$$The 3.85 nm \({\text{Mg}}_{2} \left( {{\text{OH}}} \right)_{2} {\text{CO}}_{3}\) film layer acts as an air barrier layer to prevent further deliquescent of deep MgO as shown in Fig. 15c.
When 1 nm \({\text{Al}}_{2} {\text{O}}_{3}\) is grown on MgO, the XPS test data show that there is basically no C content and no Al content in the sample after the etching time of 14 s as shown in Fig. 16e, f.
$${\text{Etching}}\_{\text{Thickness}}_{{{\text{Al}}_{2} {\text{O}}_{3} }} ={\text{Etching rate }}_{{{\text{Al}}_{2} {\text{O}}_{3} }}* {\text{Etching time}}_{{{\text{Al}}_{2} {\text{O}}_{3} }} =0.7\,{\text{{\AA}/s}}\,*\,14\,{\text{s}} =9.8{\text{\AA}}$$It can be known by testing the C content that the depth of air penetration into the material is about 1 nm at this time. According to the concept of the transition layer, there are two kinds of materials at the interface to form the process of destroying the bottom layer material and constructing the top layer material. At the interface, \({\text{Al}}_{2} {\text{O}}_{3}\) destroys the crystal lattice on the surface of MgO. In order to prevent excessive infiltration of air, a complete \({\text{Al}}_{2} {\text{O}}_{3}\) atomic level is formed at least at 1 nm. When a complete \({\text{Al}}_{2} {\text{O}}_{3}\) atomic layer is not formed, the infiltration of air into the material cannot be prevented as in Example 1 above. The \({\text{Al}}_{2} {\text{O}}_{3}\) and \({\text{ Mg}}_{2} \left( {{\text{OH}}} \right)_{2} {\text{CO}}_{3}\) in the inner layer are mixed to help MgO form a dense air barrier layer in advance as shown in Fig. 15d.
The concept of transition layer understands the SEE phenomenon of multilayer materials:
The schematic diagram shown in Fig. 17a shows the concept of the transition layer, The thickness of the top layer material is \(d_{1}\), the thickness of the bottom layer material is \(d_{2}\) and the thickness of the transition layer is \(d_{1\sim 2}\).The schematic diagram is shown in Fig. 17b, c when there is enough thick \({\text{Al}}_{2} {\text{O}}_{3}\) or MgO, the incident electron depth is \(d_{{{\text{max}}\_1}}\), and there is no transition layer between \({\text{Al}}_{2} {\text{O}}_{3}\) and \({\text{Al}}_{2} {\text{O}}_{3}\) (there is no transition layer between MgO and MgO), that is, the thickness of the transition layer is 0. Through XPS test experiment 2, we get that the thickness of the transition layer between MgO and \({\text{Al}}_{2} {\text{O}}_{3}\) is 1 nm as shown in Fig. 17d, e.
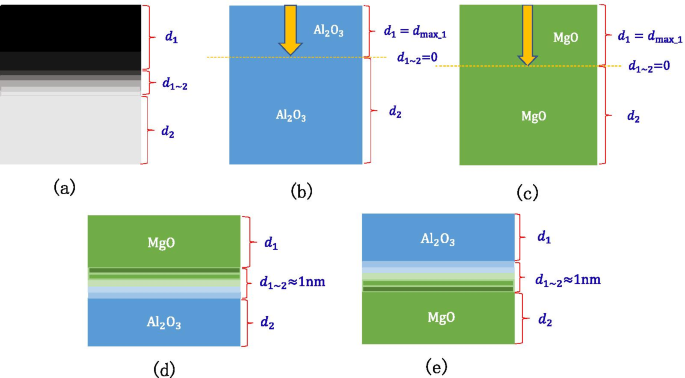
a Schematic diagram of the transition layer of the double layer structure, b schematic diagram of the Al2 O3 transition layer and incident electron depth, c schematic diagram of the MgO transition layer and incident electron depth, d schematic diagram of the Al2 O3 /MgO transition layer, e schematic diagram of the MgO/Al2 O3 transition layer
When the top layer material in the double-layer structure is MgO, the thickness of the MgO that reaches the saturated SEE level is different when the bottom layer material is different. If electrons are incident on the bottom layer material, the SEE level of the bottom layer material is low and cannot reach the saturated SEE level. Therefore, to reach the saturation SEE level, a complete MgO incident electron path needs to be formed. When the bottom layer material is different, such as Si or \({\text{Al}}_{2} {\text{O}}_{3}\), the thickness of the transition layer will be different, so the top layer MgO shows a different thickness.
It is found through experiments that a sample that grows 2 nm \({\text{Al}}_{2} {\text{O}}_{3}\) on a Si wafer and then grows 15 nm MgO can reach the SEE level of MgO saturation. Knowing that the thickness of the MgO–\({\text{Al}}_{2} {\text{O}}_{3}\) transition layer is 1 nm, it can be inferred that the thickness of the \({\text{Al}}_{2} {\text{O}}_{3}\)–Si transition layer is 1 nm, and the maximum depth of incident electrons of MgO is 14 nm as shown in Fig. 18a. It is found through experiments that the sample of 20 nm MgO grown on the Si wafer can reach the SEE level of MgO saturation. It has been inferred that the maximum depth of incident electrons of MgO is 14 nm, so the thickness of the MgO–Si transition layer can be calculated to be 6 nm as shown in Fig. 18b. Therefore, it can be explained that the SEE level of growing 2 nm \({\text{Al}}_{2} {\text{O}}_{3}\) on Si wafer and then growing 9 nm MgO is higher than the SEE level of 9 nm MgO growing on Si wafer. This is because the thickness of the MgO–\({\text{Al}}_{2} {\text{O}}_{3}\) transition layer is thinner than that of the MgO–Si transition layer. The actual MgO thickness of 8 nm involved in incident electrons is much thicker than 3 nm as shown in Fig. 18c, d.
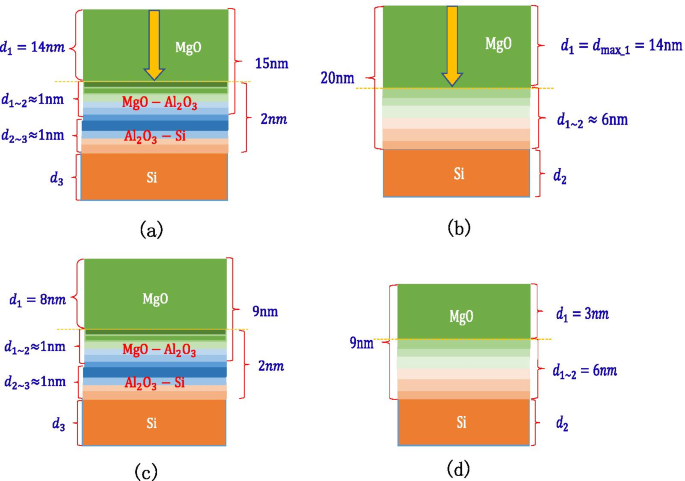
Schematic diagram of the thickness of each layer of a multilayer structure, a shows the thickness of Al2 O3 /MgO (on the silicon wafer, grow 2 nm-Al2 O3 , and then grow 15 nm-MgO), b shows the thickness of MgO (on the silicon wafer, grow 20 nm-MgO), c shows the thickness of Al2 O3 /MgO (on the silicon wafer, grow 2 nm-Al2 O3 , and then grow 9 nm-MgO), d shows the thickness of MgO (on the silicon wafer, grow 9 nm-MgO)
It can be seen through experiments that growing 7 nm \({\text{Al}}_{2} {\text{O}}_{3}\) on Si wafers can reach the SEE level of \({\text{Al}}_{2} {\text{O}}_{3}\) saturation, so it can be calculated that the maximum depth of incident electrons of \({\text{Al}}_{2} {\text{O}}_{3}\) is 6 nm; growing 7 nm \({\text{Al}}_{2} {\text{O}}_{3}\) on 35 nm MgO can reach the SEE level of \({\text{Al}}_{2} {\text{O}}_{3}\) saturation, the thickness of the MgO-\({\text{Al}}_{2} {\text{O}}_{3}\) transition layer is 1 nm, and the maximum depth of incident electrons of \({\text{Al}}_{2} {\text{O}}_{3}\) is calculated again to be confirmed by 6 nm, as shown in Fig. 19a, b.
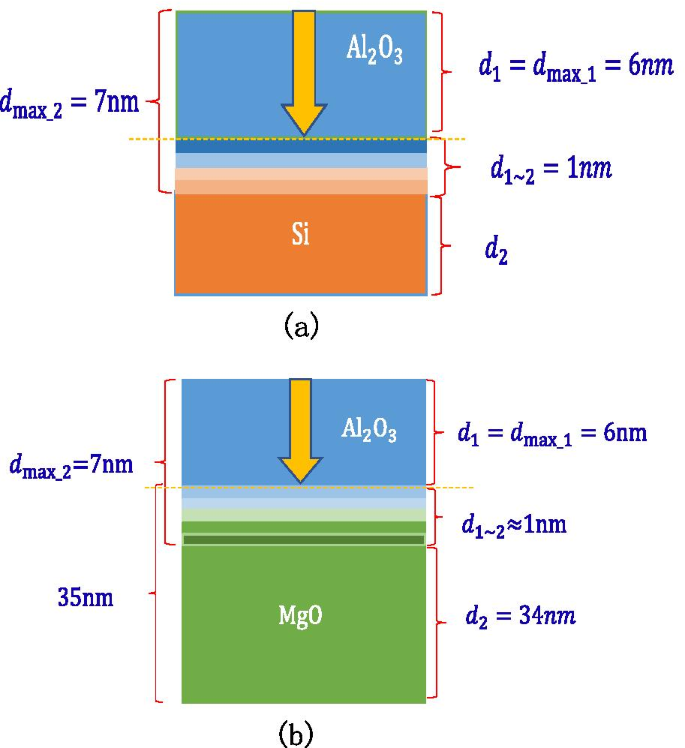
Schematic diagram of the thickness of each layer of a multilayer structure, a shows the thickness of Al2 O3 (on the silicon wafer, grow 7 nm-Al2 O3 ), b shows the thickness of MgO/Al2 O3 (on the silicon wafer, grow 20 nm-MgO, and then grow 7 nm-Al2 O3 )
Conclusions
In conclusion, we designed a global-shaped structure device for testing the SEE of the material and propose to use low-energy secondary electrons instead of low-energy electron beam for neutralization to measure the insulating material. We designed the emission layer of the electron multiplier with the idea of building a house to study the relationship between \({\text{Al}}_{2} {\text{O}}_{3}\) and MgO. We propose the nearest neighbor SEE ratio and use this to divide the SEE incident electron energy of the material into the high-energy region, the middle-energy region and the low-energy region. We have obtained four empirical formulas for SEE and thickness by studying \({\text{Al}}_{2} {\text{O}}_{3}\), MgO, MgO/\({\text{Al}}_{2} {\text{O}}_{3}\),\({\text{ Al}}_{2} {\text{O}}_{3}\)/MgO. We propose to use the concept of transition layer for SEE interpretation of multilayer materials and obtained the optimal \({\text{Al}}_{2} {\text{O}}_{3}\)/MgO/\({\text{Al}}_{2} {\text{O}}_{3}\) three-layer structure thickness suitable for electron multiplier through formula analysis and experimental experience. The thin film with this structure can maintain a high SEE level for a long time. This new emission layer will have broad application prospects in the channel electron multiplier (CEM), microchannel plate (MCP), independent electron multiplier and other devices.
Verfügbarkeit von Daten und Materialien
The authors do not wish to share their data. Because the authors have academic competition with other institutions. The authors want to protect their academic achievements and seek research funding for future research.
Nanomaterialien
- Der entscheidende Bedarf an mechanischen Konstruktionsdienstleistungen
- Die Herausforderungen des Produktdesigns
- Finde den Sweet Spot durch Design für die additive Fertigung
- Hygienisches Design für die Lebensmittel- und Verarbeitungsindustrie
- Die Bedeutung des Designs für die Fertigung
- Design für die Herstellung von Leiterplatten
- Wir haben die Ressource „So gestalten Sie benutzerdefinierte Gehäuse für Motherboards“ aktualisiert
- Ultiboard – Der ultimative Leitfaden für das Beste für Anfänger
- Danke für die Erinnerungen!
- Ein Fokus auf wichtige Designrichtlinien für die einfache Leiterplattenherstellung