Herstellung von Polydimethylsiloxan-Nanofluidik-Chips im AFM-Nanofräsprozess auf Spitzenbasis
Zusammenfassung
Im aktuellen Forschungsbereich werden auf Polydimethylsiloxan (PDMS) basierende nanofluidische Geräte häufig in medizinischen, chemischen und biologischen Anwendungen eingesetzt. In der vorliegenden Arbeit wurde eine neuartige Nanofrästechnik (bestehend aus einem AFM-System und einem piezoelektrischen Aktor) vorgeschlagen, um Nanokanäle (mit kontrollierbaren Größen) auf PDMS-Chips herzustellen, und die Nanokanalgröße wurde durch die an den piezoelektrischen Aktor eingegebene Antriebsspannung und -frequenz gesteuert . Darüber hinaus wurden Mikrokanal- und Nanokanalformen jeweils durch UV-Lithographie und AFM-Spitzen-basiertes Nanofräsen hergestellt, und schließlich wurden PDMS-Platten mit Mikro-/Nanokanälen durch einen Transferprozess erhalten. Die Einflüsse des PDMS-Gewichtsverhältnisses auf die Nanokanalgröße wurden ebenfalls untersucht. Der Verbindungsprozess von Mikrokanal- und Nanokanalplatten wurde auf einem selbstgebauten Ausrichtungssystem durchgeführt, das aus einem optischen monokularen Mikroskop und Präzisionstischen bestand. Darüber hinaus wurden die Auswirkungen der Nanokanalgröße auf die elektrischen Eigenschaften der KCl-Lösung (Konzentration 1 µM) analysiert. Daher kann der Schluss gezogen werden, dass PDMS-Nanofluidik-Geräte mit mehreren Nanokanälen mit einer Tiefe von weniger als 100 nm effizient und wirtschaftlich durch das vorgeschlagene Verfahren hergestellt werden können.
Hintergrund
Aufgrund ihres beträchtlichen Potenzials in chemischen, medizinischen und biologischen Bereichen werden mikro-/nanofluidische Systeme häufig in der DNA-Analyse [1,2,3,4], der Zelltrennung [5], der Proteinforschung [6,7,8], Lebensmittelsicherheit [9] und Umweltüberwachung [10]. Mit der schnellen Entwicklung der Nanofabrikationstechnologie steigt die Nachfrage nach nanofluidischen Geräten mit einer eindimensionalen Größe von weniger als 100 nm kontinuierlich an [11]. Nanofluidische Chips können auch effektiv zum Virusnachweis [12], zur Manipulation von Nanopartikeln [13] und zur Untersuchung der Ionendiffusion [14] verwendet werden. Die Detektionseffizienz und Empfindlichkeit der nanofluidischen Chips hängt jedoch von den Merkmalsabmessungen und der Verteilung der Nanokanäle ab. Es ist unabdingbar, die Merkmalsdimensionen der Nanokanäle für eine auf Nanofluidik basierende markierungsfreie Detektion genau zu kontrollieren. Die Herstellung von Nanokanälen mit kontrollierbaren Merkmalsabmessungen und -verteilung ist immer noch eine Herausforderung für die Anwendung im Bereich der Nanofluidik.
Bis jetzt gibt es mehrere Verfahren, die zur Herstellung von Nanofluid-Chips verwendet werden können. Für die Herstellung von nanofluidische Geräte; jedoch weisen alle diese Methoden ihre eigenen Beschränkungen auf. Reaktives Ionenätzen und konventionelle Photolithographie sind die Mainstream-Methoden für die Mikro-/Nanofluid-Kanalherstellung. Die lateralen Abmessungen der hergestellten Kanäle hängen jedoch von der Wellenlänge des einfallenden Lichts ab, sodass die Breiten der erzeugten Kanäle oft im Mikrometerbereich und nicht im Nanobereich gefunden werden [22]. Außerdem ist es unbequem, die Fotomasken zu wechseln, wenn Mikro-/Nanostrukturen mit unterschiedlichen Eigenschaften hergestellt werden. Fokussierte Ionenstrahllithographie (FIB) und Elektronenstrahllithographie (EBL) sind beides Hochenergiestrahl-Verarbeitungsverfahren, die leicht hochpräzise nanofluidische Chips mit Sub-100-nm-Nanokanälen herstellen können. Allerdings sind die Investitionen für die Fertigungsanlage extrem hoch und die strengen Umweltauflagen notwendig [23]. Interferenzlithographie (IL) eignet sich zum Herstellen einfacher periodischer Strukturen über einen großen Bereich; es ist jedoch nicht geeignet, einen einzelnen Nanokanal zu bearbeiten [24, 25]. Die Verarbeitungsauflösung des Nanoimprinting hängt von den Templateigenschaften ab, die entscheidende Frage bei diesem Ansatz ist die Herstellung des Templats mit hochpräzisen Nanostrukturen [26]. Darüber hinaus werden auch Opferformen und Verfahren auf der Grundlage von Knarren verwendet, um Mikro-/Nano-Bauelemente herzustellen [27, 28]; jedoch ist die genaue Kontrolle der Nanokanalgröße bei diesen Ansätzen sehr schwierig. Daher wird ein praktikabler Herstellungsansatz mit den Eigenschaften hoher Bearbeitungspräzision, Benutzerfreundlichkeit, großem Verarbeitungsbereich und geringen Umgebungsanforderungen für die Herstellung von nanofluidischen Geräten benötigt.
In den letzten Jahren werden aufgrund ihrer hohen Bearbeitungsgenauigkeiten Ultrapräzisionsverfahren wie Nanofräsen, Präzisionsschleifen und Ultrapräzisionsdrehen weit verbreitet in der Mikro-/Nanostrukturfertigung eingesetzt [29,30,31,32]. Darüber hinaus ist seit der Erfindung des Rasterkraftmikroskops (AFM) im Jahr 1986 die Nanofabrikation auf der Basis von AFM-Spitzen eine leistungsstarke Methode zur Herstellung von Nanostrukturen [33]. Das traditionelle Nanokratzen auf Spitzenbasis weist einige Einschränkungen auf, wie beispielsweise eine begrenzte Bearbeitungsbreite und eine geringe Fertigungseffizienz. Die Breite des durch diesen Ansatz hergestellten Nanokanals hängt von der Geometrie der AFM-Spitze ab, was bedeutet, dass die Nanokanäle mit kontrollierbarer Breite nicht zugänglich sind. Außerdem ist die Herstellungseffizienz des traditionellen Nanokratzprozesses auf Spitzenbasis relativ gering, insbesondere für den Fall, dass ein Vorschub im Bearbeitungsprozess verwendet wird, um die Tiefe und Breite der erhaltenen Nanostruktur zu vergrößern. Aufgrund seiner bedeutenden Vorteile, wie kontrollierbare Bearbeitungsgröße und hohe Fertigungseffizienz, wird das spitzenbasierte Nanofräsen weit verbreitet zur Herstellung von Nanokanälen eingesetzt. Gözen et al. [34, 35] stellten Nanostrukturen auf Polymethylmethacrylat (PMMA) durch einen Nanofräsprozess her. Zhanget al. [36,37,38] stellten dreidimensionale Nanostrukturen mit AFM her und untersuchten die Auswirkungen verschiedener Bearbeitungsparameter. Parket al. [39] untersuchten den Mechanismus des Nanobearbeitungsprozesses und fanden heraus, dass die Intensitäten der Schnittkraft signifikant reduziert wurden; Bei dem vorgeschlagenen System stellte sich jedoch heraus, dass die Bearbeitungseinrichtungen relativ kompliziert waren und der Materialabtragsprozess nicht im Detail untersucht wurde. Die Beziehung zwischen den Bearbeitungsparametern einschließlich der Antriebsfrequenz und -spannung und den Merkmalsabmessungen des erhaltenen Nanokanals wurde nicht untersucht. Außerdem konzentrierte sich ihre Arbeit nicht auf die Anwendung der hergestellten Nanokanäle. Daher sind weitere Arbeiten erforderlich, um den Anwendungsbereich dieses auf AFM-Spitzen basierenden Nanomilling-Ansatzes zu erkunden. Polycarbonat (PC) wird aufgrund seiner hervorragenden Bearbeitbarkeit häufig für die Nanofabrikation verwendet [40]; dennoch wird es selten ausgewählt, um nanofluidische Chips herzustellen. Im Gegensatz dazu wird Polydimethylsiloxan (PDMS) häufig verwendet, um mikrofluidische und nanofluidische Chips zu verarbeiten. Mata et al. [41] untersuchten den Einfluss des PDMS-Gewichtsverhältnisses auf die Zugspannung. Parket al. [42] entwickelten eine neue Methode zur Verbesserung der Steifigkeit von PDMS. Die Anwendungen von Nanofluidik-Chips im markierungsfreien Testfeld hängen hauptsächlich von der elektrischen Leitfähigkeit der Nanokanäle ab [43], daher werden die Messergebnisse oft von den Abmessungen der Nanokanäle beeinflusst [44].
Um die Nachteile des traditionellen spitzenbasierten Ritzprozesses zu überwinden, wird daher in dieser Studie der Nanomilling-Ansatz verwendet, um den Herstellungsprozess von Nanokanälen durchzuführen. Darüber hinaus wurde PC-Folie als Versuchsprobe ausgewählt, um den Spitzenverschleiß zu mindern sowie die Herstellungskosten zu reduzieren. Außerdem wurde die Nanokanalgröße auf der PC-Folie durch die dem piezoelektrischen Aktuator zugeführte Antriebsspannung und -frequenz gesteuert. Die Einflüsse des PDMS-Gewichtsverhältnisses auf die Nanokanalgröße wurden ebenfalls untersucht. Um die Auswirkungen unterschiedlicher Dimensionsgrößen auf die elektrische Leitfähigkeit von Nanokanälen zu überprüfen, wurde außerdem der Strommesstest mit KCl-Lösung durchgeführt.
Methoden
Einrichtung des Nanomilling-Systems
Das vorgeschlagene Nanofrässystem auf AFM-Spitze bestand aus einem kommerziellen AFM (Dimension Icon, Firma Bruker, Deutschland) und einem piezoelektrischen Aktor (P-122.01, Firma PI, Deutschland) (Abb. 1a). Die Stellwege des Piezoaktors sowohl in x- als auch in y-Richtung wurden auf 1 μm begrenzt. Darüber hinaus wurde der piezoelektrische Aktor durch sinusförmige Signale mit geeigneten Spannungen (erzeugt von einer kommerziellen Signalgeneratorvorrichtung (AFG1022; Tektronix, Inc., USA)) unter der Verstärkung eines Signalverstärkers (PZD350A; TREK, Inc., USA) angesteuert. Auf dem selbstgebauten Halter (aus Epoxidharz) wurde eine PC-Platte mit einer Befestigungsschraube befestigt. Der Nanobearbeitungsvorgang wurde unter Verwendung einer rechteckigen pyramidenförmigen diamantbeschichteten Spitze mit einer Dicke von 100 nm (DT-NCLR, Nanosensors, Schweiz) durchgeführt. Der Cantilever der Spitze (normale Federkonstante 68 N/m) bestand aus Silizium (Abb. 1b) und eine Siliziumspitze (Radius 10 nm) (TESPA, Firma Bruker, Deutschland) wurde verwendet, um die Rillen nach Bearbeitung.
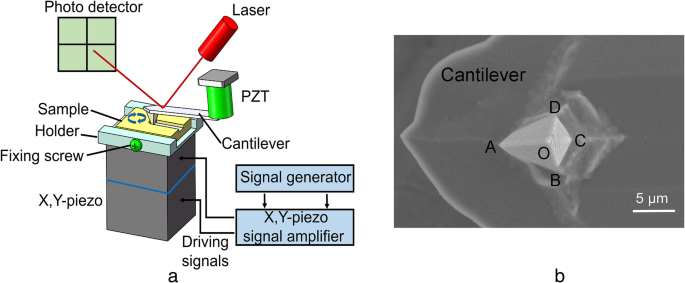
a Schematische Darstellung des Nanomilling-Systems. b REM-Aufnahme einer diamantbeschichteten AFM-Spitze
Herstellung von Nanokanal- und Mikrokanal-Formen
Der Herstellungsweg von Nanokanälen auf einem PDMS-Chip ist in Abb. 2 dargestellt. Das AFM-System und der piezoelektrische Aktor wurden verwendet, um Nanokanalformen (mit kontrollierbaren Größen) auf PC-Platten herzustellen. Die PC-Folie (Molekulargewicht 35.000) mit einer Größe von 15 mm × 12 mm × 1 mm wurde von Goodfellow bezogen. Der Mittelwert und die Standardabweichung der Oberflächenrauheit (Ra) des PC-Blatts wurden mit 0,6 nm bzw. 0,2 nm gemessen (diese Werte wurden durch Abtasten einer Fläche von 50 &mgr;m × 50 &mgr;m der Probe im AFM-Tippmodus erhalten). Um eine Kreisbewegung zu erzeugen, wurde der Piezoaktor durch sinusförmige Signale mit 90° Phasendifferenz in x- und y-Richtung angetrieben. Die Breiten der bearbeiteten Nanokanäle hingen von der Amplitude der erzeugten Kreisbewegung ab. Der Bereich der dem piezoelektrischen Aktuator zugeführten Antriebsspannung wurde von 30 V bis 150 V mit einem Abstand von 30 V eingestellt, und zusätzlich wurden zwei Tauchfrequenzen von 100 Hz und 1500 Hz ausgewählt. Während der Bearbeitung entlang der Kante-Vorwärts-Richtung werden Materialien in Stapelbildung ausgestoßen und werden oft auf beiden Seiten eines Nanokanals gleichmäßig verteilt gefunden [45], und es hilft, jegliches Austreten von Nanofluid-Chips während des Bondprozesses zu vermeiden; daher wurde in der vorliegenden Studie die kantenvorwärts gerichtete Bearbeitungsrichtung gewählt. Mit dem Nanoman-Modul des AFM-Systems wurden Nanokanäle von 80 µm Länge hergestellt. Jeder Bearbeitungsprozess wird durch den Vorschubwert beeinflusst; daher sollte, um diesen Einfluss zu eliminieren, die Vorschubgeschwindigkeit mit der Antriebsfrequenz variiert werden. In der vorliegenden Studie wurde der Vorschubwert auf 10 nm eingestellt und die Vorschubgeschwindigkeiten für die Frequenzen 100 Hz und 1500 Hz wurden mit 1 µm/s bzw. 15 µm/s berechnet. Die normale Belastung der Spitze hing von der vom positionsempfindlichen Photodetektor (PSD) erzeugten Ausgangsspannung ab; somit wurden unterschiedliche Normallasten, die in unserer Studie verwendet wurden, durch Einstellen einer relativen Spannung (Sollwert) erreicht. Nach unserer bisherigen Arbeit [46] wurde die Bearbeitungsnormallast nach Gl. (1) und die Empfindlichkeit wurde aus der Steigung der erhaltenen Kraft-Weg-Kurve gemessen [47].
$$ {F}_{\mathrm{N}}={V}_{\mathrm{Sollwert}}\times Sensitivity\times {K}_{\mathrm{N}} $$ (1)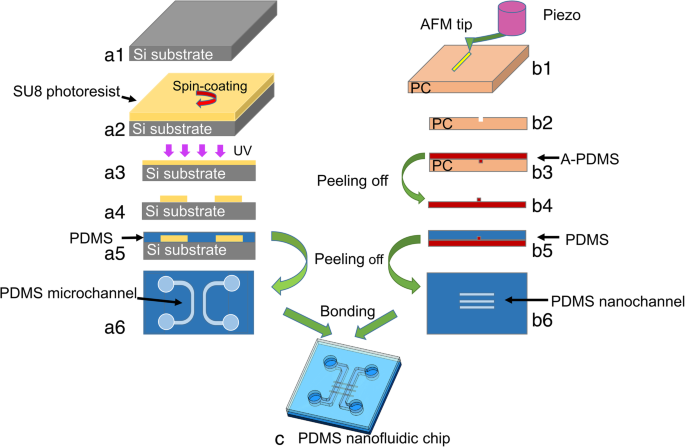
Flussdiagramm der nanofluidischen Chipherstellung:(a1)–(a6) Arbeitsschritte der Mikrokanalherstellung auf einem PDMS-Chip; (a1) Siliziumfolie, die für das Lithographiesubstrat verwendet wird; (a2) Spin-Coating von SU8-Photoresist auf einem Si-Substrat; (a3) Exposition der SU8-Schicht gegenüber UV-Licht; (a4) Erhaltene konvexe Mikrostrukturen; (a5) PDMS-Beschichtung auf einer Mikrokanalform; (a6) Endgültiger PDMS-Chip mit Mikrokanälen; (b1)–(b2) Arbeitsschritte der Nanokanalherstellung auf einem PDMS-Chip; (b1) AFM-Spitzenkratzer auf PC-Blatt; (b2) Erhaltene Nanokanalform nach dem Kratzen; (b3) A-PDMS-Beschichtung auf einer Nanokanalform; (b4) A-PDMS-Chip mit konvexen Nanostrukturen; (b5) Regelmäßige PDMS-Beschichtung auf der A-PDMS-Form; (b6) Endgültiger PDMS-Chip mit Nanokanälen; (c) PDMS-Nanofluid-Chip nach dem Bonden
Daher wurden die normalen Belastungen für den Nanomilling-Prozess auf 17 μN und 25 μN festgelegt. Zum Vergleich wurden auch Nanokanalformen auf PC-Platten vibrationsfrei hergestellt, dieses Verfahren wird als Einzelkratzen bezeichnet. Die normalen Belastungen für den einzelnen Ritzvorgang wurden mit 25 μN, 33 μN, 42 μN, 50 μN und 58 μN festgelegt. Das schematische Diagramm des Nanokanalformquerschnitts ist in Fig. 2(b2) dargestellt.
Mikrokanalformen wurden durch ein UV-Lithographieverfahren hergestellt. Das Flussdiagramm in 2(a1–a4) zeigt die Betriebsdetails des Lithographieprozesses. Der Photoresist (SU-82015; MicroChem, USA) wurde auf einem Si-Substrat bei 500 rps für 30 s und bei 4000 /s für 120 s aufgeschleudert. Ein Paar von „U“-förmigen Mikrokanälen bildete den Mikrokanal-Chip (Abb. 2(a6)), der durch Nanokanäle überbrückt wurde, um den endgültigen nanofluidischen Chip zu bilden. Die Breite des Mikrokanals betrug 30 µm und der Durchmesser des Reservoirs betrug 1 µm. Darüber hinaus betrug der Abstand zwischen zwei „U“-förmigen Mikrokanälen 50 µm (Zusatzdatei 1:Abbildungen S1 und S2).
Transferdruck von Mikrokanälen und Nanokanälen
Die konvexe Mikrokanalform (Abb. 2(a4)) und die konkave Nanokanalform (Abb. 2(b2)) wurden durch PDMS (Sylgard 184, Dow Corining, USA) übertragen, um den endgültigen nanofluidischen Chip herzustellen. Abbildung 2 (b3)–(b6) zeigen den technologischen Prozess des Nanokanal-Formentransfers, der aus zwei Schritten bestand:dem ersten Transfer und dem zweiten Transfer. Um die Auswirkungen des Gewichtsverhältnisses von Monomer zu Härtungsmittel auf die Nanokanalgröße zu untersuchen, wurden drei verschiedene PDMS-Gewichtsverhältnisse (A-PDMS) sowohl während des ersten als auch des zweiten Transferprozesses verwendet. Die PDMS-Gewichtsverhältnisse für den ersten Transferdruckprozess wurden mit 9:1, 7:1 und 5:1 festgelegt, während die Werte für den zweiten Transfer mit 10:1, 9:1 und 8:1 festgelegt wurden. Abbildung 2(a5) und (a6) zeigen den Transferprozess einer Mikrokanalform unter Verwendung eines einstufigen Transferansatzes. Das PDMS-Gewichtsverhältnis von 10:1 wurde für die Übertragung von konvexen Mikrokanälen verwendet. Bei allen Transferdruckprozessen wurde zweikomponentiges PDMS-Elastomer zunächst gleichmäßig gerührt und dann zur Vorbereitung der Form in eine Dose gegossen. Das Gehäuse wurde dann 30 min in einem Vakuumexsikkator aufbewahrt und 2–3 Mal entgast, um alle eingeschlossenen Luftblasen zu entfernen. Die vorbereitete Form wurde 4 Stunden lang in einem Heizofen bei 80 °C gehalten und schließlich wurde die PDMS-Replik vorsichtig von der Form abgezogen.
Chipbonden
Die hergestellten nanofluidischen Chips wurden durch Sauerstoff-Plasma-Behandlung (Zepto, Diener electronic, Deutschland) für eine Dauer von 32 s unter einem Kammerdruck von 1,5 mbar und einer Kammerleistung von 81 W gebondet (Abb. 2(c)). Die Oberflächen von Mikrokanälen und Nanokanälen wurden mit Klebebändern gereinigt und die vier Reservoirs auf PDMS-Mikrokanalchips wurden vor dem Bonden gestanzt. Entionisiertes Wasser wurde verwendet, um die Chips nach der Plasmabehandlung sauber zu halten, und die Chips wurden mit einem selbstgebauten Ausrichtungssystem, das aus einem Halter, einem monokularen Mikroskop und einem eindimensionalen Präzisionstisch (TSDT-401S; SIGMAKOKI, Japan) bestand, ausgerichtet gehalten ) (Abb. 3a). Die Details des selbstgebauten Ausrichtungssystems finden Sie im ESI. Die Chips wurden dann bei einer Temperatur von 95 °C für 20 min gebondet, um einen eingeschlossenen Mikro-/Nanokanal-Chip zu erhalten (Abb. 3b).
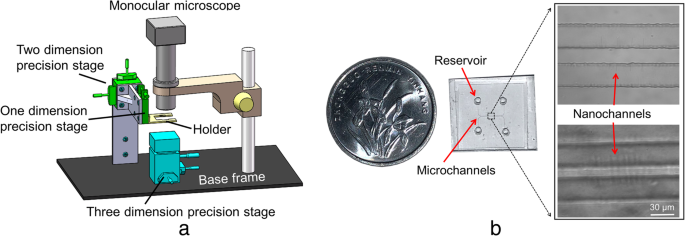
a Schematische Darstellung des selbstgebauten Ausrichtungssystems und b Nanofluid-Chip
Ergebnisse und Diskussion
Rotationsbahn des piezoelektrischen Aktors
Der zweidimensionale piezoelektrische Aktor ist eine kritische Komponente, um eine Drehbewegung in einem auf AFM-Spitzen basierenden Nanofrässystem durchzuführen. Daher wurden zur Charakterisierung seiner Bewegungen unter einem Bereich von Antriebsspannungen und -frequenzen vorläufige Kratztests durchgeführt. Beim Kontaktmodell mit einem Scanbereich von 0 nm näherte sich die AFM-Spitze zuerst der Oberfläche des PC-Blechs unter einer gegebenen normalen Last und wurde statisch gehalten. Die Drehung des zweidimensionalen piezoelektrischen Aktors wurde durch eine voreingestellte Frequenz und Spannung gesteuert. Nach Beendigung des Kratzvorgangs wurde die AFM-Spitze von der Oberfläche der PC-Platte abgehoben. Auf diese Weise wurde die Bewegungsamplitude des piezoelektrischen Aktors als Funktion der Antriebsspannung und -frequenz erhalten. Die Antriebsspannungen wurden im Bereich von 30–150 V mit einem Abstand von 30 V eingestellt, während die Antriebsfrequenzen auf 100 Hz und 1500 Hz eingestellt wurden. Der Zusammenhang zwischen gemessenen Amplituden und Antriebsspannungen bei zwei Antriebsfrequenzen ist in Zusatzdatei 1 dargestellt:Abbildung S3. Es ist offensichtlich, dass die Werte der Bearbeitungsamplitude mit steigenden Antriebsspannungen anstiegen und der Wert der Bearbeitungsamplitude bei 1500 Hz größer war als der von 100 Hz. Es wurde festgestellt, dass die Breiten des Nanokanals, der durch unser vorgeschlagenes Verfahren hergestellt wurde, von 350 nm bis 690 nm reichten.
Herstellung von Nanokanalformen auf PC-Platten
Die Beziehungen zwischen der Nanokanalgröße und den Bearbeitungsparametern beim Einzelkratzen und beim Nanofräsen sind in 4a bzw. b dargestellt. Die Breiten und Tiefen der bearbeiteten Nanokanäle werden durch W . dargestellt 0 und D 0 , bzw. (Abb. 5a).
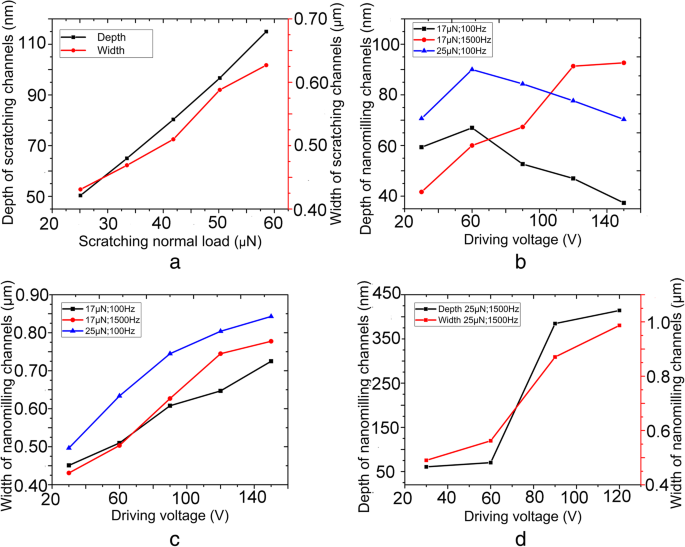
Beziehung zwischen bearbeiteter Nanokanalgröße und Bearbeitungsparametern:a einzelnes Kratzen bei normalen Belastungen von 25 μN bis 58 μN, b Tiefe und c Breite der bearbeiteten Kanäle bei der Herstellung mit normalen Lasten von 17 μN, 25 μN und Antriebsfrequenzen von 100 Hz, 150 Hz, d die Tiefe und Breite der bearbeiteten Kanäle bei der Herstellung mit einer normalen Belastung von 25 μN und einer Antriebsfrequenz von 1500 Hz
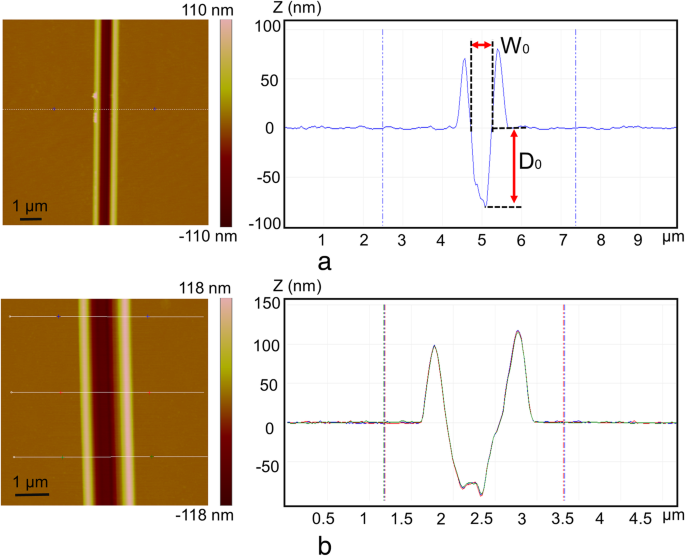
Typische AFM-Bilder des bearbeiteten Nanokanals mit verschiedenen Bearbeitungsparametern:a Kratzen unter einer normalen Belastung von 42 μN. b Nanofräsen unter einer normalen Last von 25 μN, einer Frequenz von 100 Hz und einer Antriebsspannung von 60 V
Aus Fig. 4a ist ersichtlich, dass die Breiten und die Tiefen der hergestellten Nanokanäle mit steigender Normalbelastung zunahmen. Das typische AFM-Bild des Kratzens unter einer normalen Belastung von 42 µN ist in Abb. 5a gezeigt. Auffällig ist, dass Materialien aus dem Nanokanal ausgestoßen wurden, um Anhäufungen zu bilden, die gleichmäßig auf beiden Seiten des Nanokanals verteilt waren. Weil die Form der AFM-Spitze symmetrisch zu der Oberfläche ist, die während des Bearbeitungsprozesses durch die Kante „OA“ gebildet wurde (Abb. 1b). Somit wurden Materialien während des Kanten-Vorwärts-Kratzens gleichmäßig von der Vorderkante der Spitze ausgestoßen. Abbildung 4b, c und d veranschaulichen die Beziehung zwischen der bearbeiteten Nanokanalgröße und der Antriebsspannung. Aus Fig. 4b ist ersichtlich, dass die Tiefe des Nanokanals am Anfang zugenommen hat und dann bei einer Frequenz von 100 Hz mit normalen Lasten von 17 µN und 25 µN abgenommen hat. Die in unserer Studie verwendete PC-Platte war ein amorphes Polymer, das ein elastisch-viskoplastisches Verhalten in Kombination mit einer exponentiellen Kaltverfestigung bei hohen Dehnungen zeigt [48, 49]. Die Normalbelastung während der Bearbeitung wurde nach Gl. (2), wobei \( \overrightarrow{n} \) und \( \overrightarrow{t} \) die Einheitsnormale bzw. die Einheitstangente zum Flusslinienvektor sind, p und τ bezeichnet den lokalen Normaldruck bzw. die Schubspannung und \( \overrightarrow{z} \) ist die vertikale Einheit [50].
$$ {F}_{\mathrm{N}}=p\cdot \int \overrightarrow{n}\cdot \overrightarrow{z} ds-\tau \cdot \int \overrightarrow{t}\cdot \overrightarrow{zds } $$ (2)In der vorliegenden Studie wurden die Dimensionsgrößen der hergestellten Nanokanäle im Nanobereich gefunden, daher wurden die Werte des lokalen Normaldrucks und der Schubspannung als konstant angenommen. Weiterhin gilt Gl. (2) wurde in die vereinfachte Form von Gl. (3), wobei S n und S h sind jeweils die horizontale und die vertikale Projektion der Grenzfläche zwischen AFM-Spitze und Probe.
$$ {F}_{\mathrm{N}}=p\cdot {S}_n-\tau \cdot {S}_h $$ (3)Die Beziehung zwischen S n und S h wird in Gl. (4), wobei α und β sind jeweils die eingeschlossenen Winkel zwischen der Spitzenoberfläche und den vertikalen und horizontalen Ebenen.
$$ {S}_{\mathrm{n}}=\frac{S_{\mathrm{h}}}{\cos\alpha}\cdot \cos\beta $$ (4)Die Normallast wurde nach Gl. (5).
$$ {F}_{\mathrm{N}}=\left(p\cdot \frac{\cos\beta }{\cos\alpha}-\tau\right)\cdot {S}_h $$ (5 )Aus Gl. (1) dass die Werte der Normallast während des gesamten Bearbeitungsprozesses konstant waren. Nach Briscoe et al. [51] wurde der Wert der mittleren Dehnungsrate nach Gl. (6), wobei V und w bedeuten Spitzengeschwindigkeit bzw. ungeschnittene Spandicke. Der maximale Wert der ungeschnittenen Spandicke wurde mit ~ 10 nm gefunden.
$$ {}_{\varepsilon}^{\bullet}=\frac{\mathrm{d}\varepsilon }{\mathrm{d}t}\approx \frac{V}{w} $$ (6)Außerdem wurden die Werte der Spitzengeschwindigkeit aus Gl. (7), wobei f ist die Eingangssignalfrequenz.
$$ V=\pi \cdot {W}_o\cdot f $$ (7)Die Werte der mittleren Dehnungsrate bei 100 Hz wurden im Bereich von 1,42 × 10 4 . gefunden s -1 ~2,27 × 10 4 s -1 . Die Werte des lokalen Normaldrucks (p ) begann mit der Zunahme der Dehnungsraten zu steigen, als die Dehnungsraten im Bereich von 1,42 × 10 4 . lagen s -1 bis 2,27 × 10 4 s -1 [52]. Der Wert von τ war viel kleiner als das von p , bedeutet dies, dass die normale Belastung hauptsächlich von p . abhing . Um die Werte der Normallast (FN ) während des gesamten Bearbeitungsprozesses konstant, sollten die Werte der Bearbeitungstiefe bei höheren Antriebsspannungen kleiner sein. Die endgültige Dimensionsgröße des hergestellten Nanokanals wurde jedoch durch die Rückgewinnung des Probenmaterials beeinflusst. Die Erholung der Probe nahm mit zunehmender Bearbeitungsgeschwindigkeit im Bereich von 142-227 µm/s ab [53]:Dies deutet also darauf hin, dass bei 30 V eine höhere elastische Rückstellung auftrat und die Tiefe des hergestellten Nanokanals bei 30 V (~142 µm/s) war flacher als 60 µV (~161 µm/s). Zusätzliche Datei 1:Abbildung S4(a) und Abbildung 5b sind die typischen AFM-Bilder des Nanokanals, die bei 100 Hz unter normalen Lasten von 17 µN bzw. 25 µN bearbeitet wurden. Es ist offensichtlich, dass die Anhäufung auf der rechten Seite des Nanokanals größer ist als auf der linken. Die Rotationsbewegung der Probe während des Nanomilling-Prozesses erfolgt gegen den Uhrzeigersinn und der Schnittwinkel der Hauptschneide ändert sich mit der Rotation. Die ungeschnittene Spandicke ist zu gering, um am Anfang und am Ende eines Zyklus des Nanofräsprozesses Späne zu bilden. Die ungeschnittene Spandicke in der Mitte eines Zyklus des Nanofräsprozesses ist relativ groß; der kleine Angriffswinkel trägt jedoch zur Bildung der Pil-Ups bei. Dadurch werden mehr Materialien auf die rechte Seite des Kanals geschoben und die Stapel sind somit asymmetrisch. Die Details zur Bildung asymmetrischer Pile-Ups finden Sie in unserer vorherigen Studie [54].
Aus Fig. 4b und d ist ersichtlich, dass die Tiefe des Nanokanals mit steigenden Ansteuerspannungen bei 1500 Hz unter normalen Lasten von 17 μN und 25 μN zuzunehmen begann. Abbildung 4d zeigt, dass die Nanokanaltiefe von 60 V (~ 2,64 mm/s) auf 90 V (~ 4,10 mm/s) unter einer normalen Belastung von 25 µN stark angestiegen ist. Nach Geng et al. [55] wird der Materialabtragszustand wesentlich von der Schnittgeschwindigkeit beeinflusst. Während der Bearbeitung mit einer Geschwindigkeit von 2,64 mm/s wurden Materialien in Stapelform aus dem Nanokanal ausgestoßen, während sich der Materialabtragszustand von Stapelung zu Span mit 4,10 mm/s änderte (Zusätzliche Datei 1:Abbildung S4(b)) . Daher kann die Zunahme der Bearbeitungstiefe bei 90 V (~4,10 mm/s) auf die Änderung des Materialabtragszustands zurückgeführt werden. Die Breite des hergestellten Nanokanals begann mit steigenden Ansteuerspannungen zuzunehmen. Abbildung 6 zeigt das schematische Diagramm der Flugbahn der AFM-Spitze während des Nanofräsens. Die gestrichelten Ellipsen, die schwarzen ausgefüllten Ellipsen und die blauen Pfeile repräsentieren den fertigen Bearbeitungsprozess, den laufenden Bearbeitungsprozess bzw. die Bewegungsrichtung der AFM-Spitze. Die Breite (W 2 ) des bearbeiteten Kanals in Fig. 6(b) war größer als der (W 1 ) in Fig. 6(a). AS1 und AS2 (rote durchgezogene Linien) stellen die Kontaktlänge zwischen dem Querschnitt der AFM-Spitze und dem Probenmaterial dar. Der Wert von AS1 wurde als größer als der von AS2 . festgestellt wenn die Bearbeitungsbreite „L 1 “ war gleich „L 2. ”
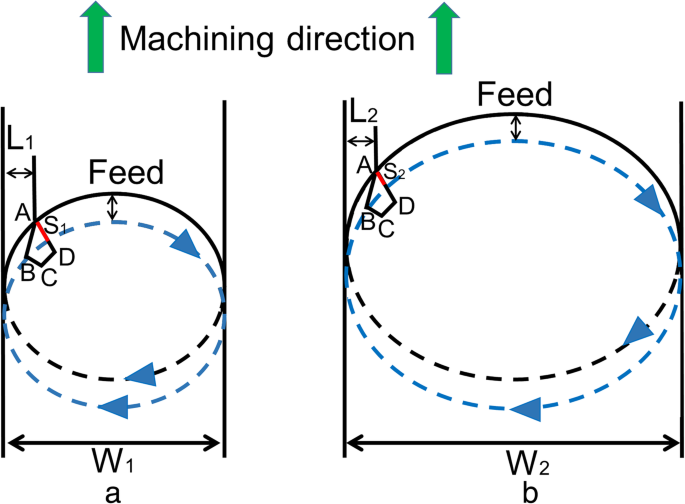
Schematische Darstellung der Flugbahn der AFM-Spitze während des Nanofräsprozesses:die bearbeitete Breite des Nanokanals (a ) ist kleiner als Nanokanal (b ) und die gestrichelten Ellipsen, die schwarzen ausgefüllten Ellipsen und die blauen Pfeile repräsentieren den fertigen Bearbeitungsprozess, den laufenden Bearbeitungsprozess bzw. die Bewegungsrichtung der AFM-Spitze
Der Wert von Sh in Gl. (5) wurde nach Gl. (8), wobei D bzw. AS die Tiefe des bearbeiteten Kanals und die Kontaktlänge zwischen dem Querschnitt der AFM-Spitze und dem Probenmaterial sind.
$$ {S}_h=\frac{1}{2}\cdot \left|D\left|\cdot \right|\; AS\rechts| $$ (8)Daher ist Gl. (5) wurde in Form von Gl. (9).
$$ {F}_{\mathrm{N}}=\frac{1}{2}\cdot\left(p\cdot\frac{\cos\beta}{\cos\alpha}-\tau\right) \cdot \left|D\left|\cdot \right| AS\rechts| $$ (9)Die Werte von α und β wurden während des gesamten Bearbeitungsprozesses konstant gehalten. Die Werte der Dehnungsrate bei 1500 Hz wurden im Bereich von 2,03 × 10 5 . gefunden ~3,66 × 10 5 s -1 ; daher kann angenommen werden, dass der lokale Normaldruck (p ) hat bei 1500 Hz seinen Grenzwert erreicht. Darüber hinaus zeigte die Bearbeitungsgeschwindigkeit keinen Einfluss auf die Rückgewinnung der Probe während der Bearbeitung bei 30–150 V (~ 2,03–3,66 mm/s) [53]; somit wurden die endgültigen Abmessungsgrößen des Nanokanals nur durch die Bearbeitungsabmessungen bestimmt. Die Werte von AS2 (Abb. 6(b)) waren kleiner als die von AS1 (Abb. 6(a)) für größere bearbeitete Breiten und nach Gl. (9) war der Wert von D größer für einen kleineren Wert von AS. Daher nahmen die Werte der Bearbeitungstiefe mit steigenden Antriebsspannungen zu. Ein typisches AFM-Bild des Nanokanals, der unter einer normalen Last von 25 μN, einer Steuerspannung von 120 V und einer Frequenz von 1500 Hz hergestellt wurde, ist in Zusatzdatei 1 dargestellt:Abbildung S4(b). Auffällig ist, dass sowohl bei der Span- als auch der Stapelbildung Material abgetragen wurde und sich die ausgestoßenen Materialien nur auf einer Seite des Nanokanals ansammelten. Darüber hinaus sammelten sich die ausgestoßenen Materialien bei der Spanbildung am Boden des Nanokanals während der Bearbeitung bei 150 V unter einer normalen Belastung von 25 μN. Daher waren die Größendaten des hergestellten Nanokanals während der Bearbeitung bei einer Spannung von 150 V und einer Frequenz von 1500 Hz (unter einer normalen Last von 25 μN) in 4d leer
Aus Fig. 4c ist ersichtlich, dass die Nanokanalbreite mit steigenden Treiberspannungen zuzunehmen begann. Darüber hinaus war die Breite des bei einer Frequenz von 1500 Hz hergestellten Nanokanals breiter als die von 100 Hz, wenn die Werte der normalen Last und der Ansteuerspannung konstant gehalten wurden. Darüber hinaus war die Bearbeitungstiefe des bei 1500 Hz hergestellten Nanokanals tiefer als die von 100 Hz, und es wurde festgestellt, dass die Querschnittsgröße der Spitze während der Bearbeitung eines tieferen Nanokanals größer war. Daher wurden die Nanokanäle bei tieferer Bearbeitung breiter hergestellt.
Erster Transfer von Nanokanalformen
Für den ersten Transferprozess wurden Nanokanäle verwendet, die unter normalen Belastungen von 25 μN, 33 μN, 41 μN, 50 μN und 58 μN durch das Single-Scratching-Verfahren bearbeitet wurden. Darüber hinaus wurden im Transferprozess auch Nanokanalformen verwendet, die durch Nanofräsen bei einer Frequenz von 100 Hz im Antriebsspannungsbereich von 30–150 V (mit einem Abstand von 30 V) hergestellt wurden. Nanokanäle (80 nm Tiefe und 510 nm Breite), die durch Einzelritzverfahren bearbeitet wurden, wurden als „Nanokanal I“ bezeichnet, während Nanokanäle (50 nm Tiefe und 610 nm Breite, 90 nm Tiefe und 630 nm Breite), die durch Nanofräsen hergestellt wurden, als „Nanokanäle“ bezeichnet wurden II“ bzw. „Nanokanal III“. Im ersten Transferprozess wurden drei verschiedene PDMS-Gewichtsverhältnisse (5:1, 7:1 und 9:1) verwendet.
Abbildung 7a und b zeigen die Auswirkungen unterschiedlicher PDMS-Gewichtsverhältnisse auf die Wandgröße unter einer normalen Last von 25 µN und einer Frequenz von 100 Hz, und die schwarze gestrichelte Linie repräsentiert die ursprüngliche Nanokanalgröße vor der Übertragung. Das typische AFM-Bild und der entsprechende Querschnitt der Wand, die von Nanokanal III bei einem Gewichtsverhältnis von 5:1 während des ersten Transfers erhalten wurde, sind in Abb. 7c und d dargestellt, und diese Wand wurde als „Wand III“ bezeichnet. Die Auswirkungen unterschiedlicher PDMS-Gewichtsverhältnisse auf die Wandgröße bei einem einzelnen Ritzprozess mit einer normalen Belastung von 17 μN und einer Frequenz von 100 Hz wurden in ESI gezeigt (siehe Zusatzdatei 1:Abbildungen S5, S6, S7 und S8 von ESI für Details). Die aus „Nanokanal I“ und „Nanokanal II“ erhaltenen Wände wurden als „Wand I“ bzw. „Wand II“ bezeichnet. Es ist offensichtlich, dass die Höhen aller Wände bei unterschiedlichen PDMS-Gewichtsverhältnissen ungefähr gleich waren. The widths of the walls were larger than the original nanochannel width, and the width at the weight ratio of 5:1 was found to be the largest. Due to the thermal expansion of PC sheet, a small deviation was noticed between final wall size and original nanochannel size. It was also observed that the elasticity of PDMS increased as the PDMS weight ratio decreased from 5:1 to 7:1 [41, 42]. Hence, the wall obtained at the weight ratio of 5:1 was stiffer and its elastic recovery was smaller; thus, the width of the wall obtained at the weight ratio of 5:1 was the largest.
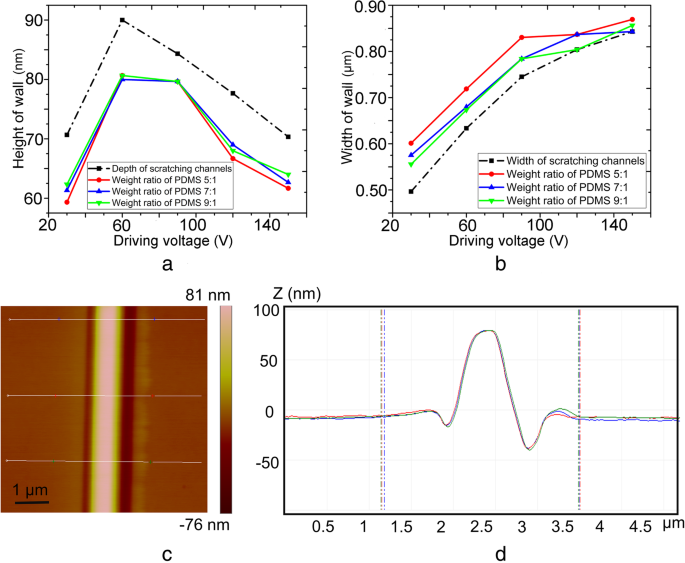
Relationship between a wall height, b wall width, and transfer parameters (various weight ratio of PDMS) during first transfer process, where the channel molds were fabricated with a normal load of 25 μN and a frequency of 100 Hz, and c typical AFM image and d corresponding cross-section of the wall obtained from nanochannel III at a weight ratio of 5:1
Second transfer of nanochannel molds
The final PDMS slabs with nanochannels were obtained during second transfer process based on the wall obtained at a weight ratio of 5:1 in the first transfer process. Three different PDMS weight ratios (10:1, 9:1, and 8:1) were used during second transfer process. Figure 8a and b present the relationship between nanochannel size obtained under a normal load of 25 μN and a frequency of 100 Hz and transfer parameters during second transfer. It is clear from Fig. 8a that the depths of the nanochannels were larger than the original machining size, moreover, the depth at 10:1 was found to be larger than other two ratios. Further, the widths of the wall were also larger than the original size, and the width at 10:1 was found to be the largest (Fig. 8b). Figure 8c and d present a typical AFM image and corresponding cross-section of the nanochannel (120 nm depth and 690 nm width) obtained from wall III at a weight ratio of 10:1 during second transfer, and it was termed as “nanochannel C.” The relationship between the nanochannel sizes obtained under single scratching process with a normal load of 25 μN and a frequency of 100 Hz and the transfer parameters during the second transfer process were shown in ESI (see Additional file 1:Figures. S9, S10, S11 and S12 of ESI for details), the nanochannels obtained from “wall I” and “wall II” were termed as “nanochannel A” and “nanochannel B”, respectively.
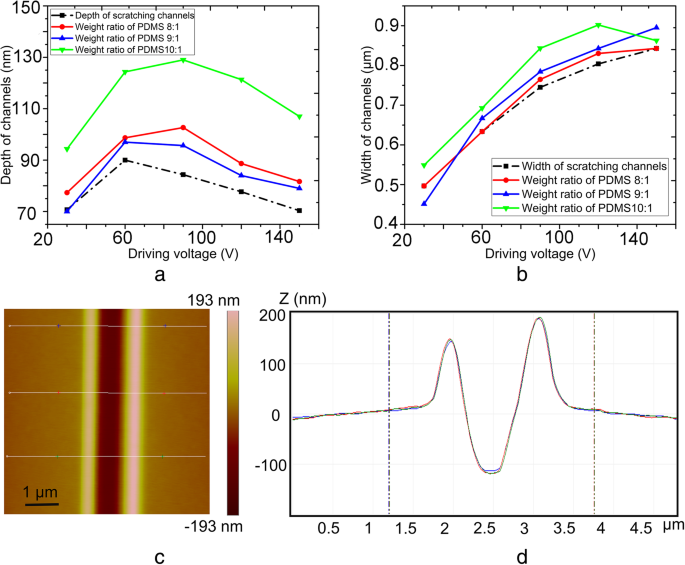
Relationship between a nanochannel height, b nanochannel width, and transfer parameters (various weight ratio of PDMS) during second transfer, where the channel molds were fabricated with a normal load of 25 μN and a frequency of 100 Hz, and c typical AFM image and d corresponding cross-section of the nanochannel obtained from wall III at a weight ratio of 10:1 during second transfer
The depths of nanochannels obtained from walls II and III were larger than the original machining size, whereas the depth obtained from wall I was smaller than the initial machining size. Furthermore, the changes in width were identical to the changes in depth. The aspect ratio of wall I was larger than those of walls II and III, thus each wall manifested different thermal expansion values. Hence, the changing trends of width and depth during second transfer were different though at the same PDMS weight ratio. The values of the depth and width of walls II and III at 9:1 and 8:1 were found to be closer to the original machining size compared with 10:1. Because the elastic recoveries of PDMS at 9:1and 8:1 are closer to 5:1 than 10:1, which indicates an almost similar recovery trend for PDMS at 9:1, 8:1, and 5:1.
Application of nanochannel devices in electric current measurement
Nanochannel devices are often used in the fields of single nanoparticle manipulation, electrokinetic transport phenomena, DNA analysis, and enzymatic reaction detection. The main working principle of nanofluidic chips depends on the variation in electric current; therefore, it is important to measure the electrical conductivities of nanochannel devices. The electrical conductance in a nanochannel can be estimated by Eq. (10) [56].
$$ G={10}^3N\;{}_Ae\frac{wh}{l}\sum {\mu}_i{c}_i+2{\mu}_e\frac{w}{l}{\delta}_n $$ (10)wobei μ ich is the mobility of ion i , c ich is the concentration of ion i , δ n is the effective surface charge inside the nanochannel, and NA and e signify Avogadro constant and electron charge, besides, w , h und l are the nanochannel width, height and length, respectively. It is obvious that the electrical conductance of a nanochannel is affected by the nanochannel feature dimensions and the solution concentration. The electric double layer (EDL) plays an important role in the nanochannel when the ratio of DEL thickness to the nanochannel height increases. The diffuse layer thickness of EDL is 3~5 times of the Debye length (λ D ), which can be expressed by Eq. (11) [57].
$$ {\lambda}_D=\sqrt{\frac{\varepsilon_0{\varepsilon}_r{k}_bT}{2{n}_{i\infty }{(ze)}^2}} $$ (11)wo n ich ∞ denotes ion density in the solution, ε o is the permittivity of vacuum, ε r is the dielectric constant of electrolyte solution, z is the valency of buffer solution (z = z + − z − = 1 for KCl), and kb und T are the Boltzmann constant and temperature, respectively. In the present study, three different nanofluidic chips were obtained after the completion of transfer process. Nanofluidic chips consisted of nanochannels A, B, and C were termed as nanofluidic chips A, B, and C, respectively. Each nanofluidic chip contained four nanochannels. The widths and the depths of nanofluidic chips A, B, and C were measured as 60 nm and 500 nm, 80 nm and 680 nm, and 120 nm and 690 nm, respectively. The effective length of nanochannels in all chips was calculated as 50 μm. As shown in Fig. 8, pile-ups distribute on the sides of the nanochannels A, B, and C. The pile-ups may fill into the nanochannels and lead to a failure of the preparation for the nanofluidic chips. Thus, in order to verify the reliability of the fabricated nanochannel devices, electrical conductivity measurement test was conducted. KCl with 1 mM concentration was as the electrolyte solution in our study, and the values of electrical current were measured by an electrometer (Model 6430, Keithley, USA). The schematic sketches of the measurements for electric current in microchannel and nanochannel are presented as the inset figures in Fig. 9a and b, respectively. The experiments were carried out under DC power (applied by an Ag electrode) with an increment of 2 V for 3-s duration. Figure 9a presents the measured I -V curves of microchannels in three different nanofluidic chips, and a linear relationship between current and voltage was observed. Moreover, as the effect of EDL in microchannels was negligible and the dimensional sizes of microchannels in different nanofluidic devices were identical, the values of current in different chips were nearly the same. It is evident from Fig. 9b that the values of current in different nanofluidic devices were distinct due to different nanochannel sizes. For KCl solution of 1 mM concentration, the value of λ D was about 10 nm, thus the diffuse layer thickness of EDL was found as 30~50 nm [57]. Consequently, EDL got overlapped along the depth (60 nm) of nanofluidic chip A; however, no overlapping was observed in nanofluidic chip C (depth of 120 nm). However, it was difficult to determine whether EDL got overlapped or not in nanofluidic chip B (depth of 80 nm). It assumes that the effective surface charges (δ n ) in all nanochannels are identical as the charge density of a surface is material property [58, 59]. The concentration of the ions in a nanochannel depends on the EDL field, the stronger the EDL field, the higher the ion concentration in the nanochanel [44]. In the present study, the EDL field in nanofluidic chip A is the strongest as the highest ratio of the DEL thickness to the nanochannel height, which signifies that the ion concentration in the nanochannel of nanofluidic chip A is the highest. Nach Gl. (10), the nanochannel of nanofluidic chip A is more conductive due to the higher ion concentration. Hence, the value of electrical current in nanofluidic chip A was the largest, whereas nanofluidic chip C yielded the smallest value. In addition, at larger width sizes, EDLs did not overlap along the width directions of nanochannels. In nanofluidic chip B, when the value of applied electric field was lower than 25 V, a linear relationship was noticed between current and applied voltage; however, a limiting region appeared as the value of applied voltage increased and finally, became liner again as the electrical field increased further, this phenomenon belongs to ohmic-limiting-overlimiting current characteristic [60, 61]. The results of electrical current measurement revealed that the nanofluidic devices fabricated by the proposed method were effective, the pile-ups of the nanochannels A, B, and C had almost no influence on the performance of the nanofluidic devices.
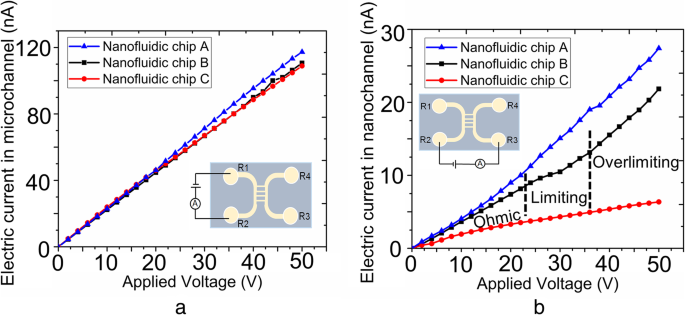
Electric current measurement results based on the fabricated nanochannel devices, the cross-section size (depth × width) of nanochannels for nanofluidic chip A, B, and C are 60 × 500 nm, 80 × 680 nm and 120 × 690 nm, respectively. a Current in microchannels. b Current in nanochannels. The insets display the schematic sketches of the measurements
Schlussfolgerungen
In the present research, nanochannels with controllable sizes (sub-100-nm depth) were fabricated by AFM tip-based nanomilling, and for the first time, the machined nanochannels were applied to prepare nanofluidic devices. The multichannel nanofluidic devices were prepared in four steps:(1) fabrication of nanochannels by AFM tip and piezoelectric actuator, (2) fabrication of microchannels by lithography, (3) transfer of micro- and nanochannels, and (iv) bonding. Further, nanochannel sizes were controlled by changing the driving voltages and frequencies inputted to the actuator. The heights of the wall obtained during first transfer were smaller than the original machining size, whereas the widths were larger than the original machining size. The experiment results revealed that during second transfer process, nanochannel sizes affected PDMS weight ratios. Finally, micro-nanofluidic chips with three different nanochannel sizes were obtained by bonding a PDMS nanochannel chip on a PDMS microchannel chip. Moreover, the electrical current measurement experiment was conducted on the fabricated nanofluidic chips, and it was found that the values of current were affected by nanochannel sizes. Therefore, PDMS nanofluidic devices with multiple nanochannels of sub-100-nm depth can be efficiently and economically fabricated by the proposed method.
Compared with other fabrication approach, the proposed method for fabrication of the nanofluidic devices in the study is easy to use and low cost; besides, the nanochannels with controllable dimension size can be obtained easily. However, the commercial AFM system cannot equip with a large-scale high-precision stage due to the spatial limitation; thus, the maximum fabrication length of the nanochannel is confined as 80 μm. In addition, the tip wear cannot be neglected after long-term fabrication due to the high machining speed, which should be investigated in future work.
Abkürzungen
- AFM:
-
Rasterkraftmikroskop
- DC:
-
Gleichstrom
- EDL:
-
Electric double layer
- KCL:
-
Potassium chloride
- PC:
-
Polycarbonate
- PDMS:
-
Polydimethylsiloxane
- PSD:
-
Position-sensitive photodetector
Nanomaterialien
- Stanzen:Ein Crashkurs zu diesem Herstellungsprozess
- Blog:Den PDMS-Fertigungsprozess verstehen
- Die beliebtesten Verfahren zur Herstellung von Verbundwerkstoffen
- Die verschiedenen Möglichkeiten des Finishing-Prozesses, den Metallherstellungsprojekten einen funktionalen Mehrwert zu verleihen
- Verwendung eines 3D-Druckers zur Verbesserung Ihres Fertigungsprozesses – Video
- Ihr Leitfaden zum Scheren im Metallherstellungsprozess
- Die Herstellung von Prozessrohren erfordert eine einfallsreiche Routenplanung
- Die Herstellung von Prozessleitungen erfordert die Einhaltung exakter Spezifikationen
- Wie viel Zeit benötigt Ihr Herstellungsprozess?
- Die Vorteile des Sandstrahlens für Ihr individuelles Metallherstellungsprojekt