Auswirkung flüssiger Medien auf Materialabtrag und Defekte unter der Oberfläche Entwicklung von monokristallinem Kupfer im Nanoschneidprozess
Zusammenfassung
Der Einfluss flüssiger Medien auf den Materialabtrag und die Entwicklung von unterirdischen Defekten im Nanoschneidprozess von einkristallinem Kupfer wird mittels molekulardynamischer Simulation untersucht. In diesem Artikel werden der Abtragsmechanismus des Spans und der Bildungsmechanismus der bearbeiteten Oberfläche untersucht, indem die atomare Migration und Versetzungsentwicklung des Werkstücks während des Nanoschneidprozesses unter Verwendung wässriger Medien analysiert wird. Die Temperaturverteilung und die Kristallstrukturumwandlung unter der Oberfläche werden untersucht, die durch Zentrosymmetrieparameter und gängige Nachbaranalysemethoden analysiert werden. Die Ergebnisse zeigen, dass das Werkstückmaterial durch die Extrusionsscherwirkung des Schneidwerkzeugs entfernt wird. Die Schmierung des wässrigen Mediums kann die Schnittkraft reduzieren und die Höhe der Schnittspäne verringern. Insbesondere die Kühlwirkung der fluiden Medien führt zur Ausbildung einer typischen Defekt-„Korngrenze“ im Untergrund des Werkstücks. Und die Temperatur des Werkstücks nimmt während des Nanoschneidprozesses unter Verwendung von flüssigen Medien deutlich ab.
Hintergrund
Diamantschneiden gilt weithin als effektives Verfahren zur Erzeugung nanostrukturierter Oberflächen mit Submikrometer-Abmessungsgenauigkeit und nanometrischer Oberflächengüte [1]. Der Mechanismus des Materialabtrags und der Bildung der bearbeiteten Oberfläche im Nanobereich ist entscheidend für die Verbesserung der Bearbeitungsgenauigkeit beim nanometrischen Schneidprozess. In frühen Studien konzentrierten sich die Forscher auf die Verformung des Materials [2,3,4], die Entwicklung von Oberflächendefekten [5,6,7], die Eigenspannung [8, 9] und den Kristallphasenübergang [10, 11] während des Nanoschneidprozesses in einer Vakuumumgebung. Beim tatsächlichen nanometrischen Schneiden von Metallmaterial ist die Rolle der Kühl- und Schmierflüssigkeit jedoch sehr entscheidend für die Verbesserung der Bearbeitungsleistung [12]. Daher ist es notwendig, den Einfluss flüssiger Medien auf den Mechanismus des Materialabtrags und die Entstehung von unterirdischen Defekten im Nanoschneidprozess zu untersuchen.
In den letzten Jahren wurde der Bearbeitungsmechanismus des Nanoschneidprozesses umfassend durch Molekulardynamik (MD)-Simulation untersucht, die sich als wirksame Methode zur Untersuchung von nanometrischen Schneidprozessen erwiesen hat. So untersucht Fang [13] den Einfluss der Rückgewinnung und des Seitenflusses auf die Oberflächenerzeugung und Phasenumwandlung beim Nanoschneiden. Und es hat sich herausgestellt, dass die Unterdrückung des Seitenflusses ein wirksamer Weg ist, um die erzeugte Oberflächenrauheit beim Nanoschneiden zu verbessern. Urbassek [14] wendete die MD-Simulation an, um das Verkratzen nanokristalliner Metalle zu untersuchen, und stellte fest, dass die Kornorientierung einen dominanten Einfluss auf die Form der Stapelung hat und auch den Reibungskoeffizienten stark beeinflusst. Sharma [15] untersuchte den Einfluss von sechs unterschiedlichen Kristallorientierungen auf den Materialdeformationsmechanismus, Fehler unter der Oberfläche, Schnittkräfte, spezifische Schnittenergie, Pflugeffekt und Oberflächenrauheit beim nanoskaligen Schneiden. Luo [16] demonstrierte die Formübertragbarkeit durch den Einsatz von nanoskaligen Multi-Tip-Diamantwerkzeugen beim Diamantdrehen für die Scale-up-Fertigung von Nanostrukturen.
Durch sinnvolle Wahl der Schnittparameter, wie Schnittrichtung, Schnitttiefe, Schnittgeschwindigkeit und Werkzeuggeometrie, kann die Fehlerbildung unter der Oberfläche und die Oberflächenrauheit des Nanobauteils eingeschränkt werden. Es kann jedoch nicht erfolgreich sein, die Bildung von Oberflächendefekten zu verhindern und die Oberflächenqualität durch den Erzeugungsmechanismus zu verbessern. Außerdem konzentrieren sich diese Forschungen auf den Nanoschneidprozess in einer Vakuumumgebung. Tatsächlich existierten beim Nanometerschneiden eine Atmosphäre und flüssige Kühlmedien zwischen Werkzeug und Werkstück, die den Nanoschneidmechanismus und die Oberflächenqualität der Nanostruktur beeinflussen können.
Basierend auf der obigen Überlegung haben viele Wissenschaftler Forschungen zu Nanobearbeitungsprozessen unter Verwendung flüssiger Medien durchgeführt. Mylvaganam [17] untersuchte beispielsweise die Wirkung von O2 über die Nano-Eindrückung von diamant-kubischem Silizium mittels MD-Simulation und fanden heraus, dass die O2 Molekül dissoziiert in Sauerstoffatome und geht chemische Bindungen mit Siliziumatomen ein. Rentsch [18] stellte fest, dass Kühlschmierstoff einen großen Einfluss auf die Spannungs- und Temperaturverteilung hat und wies darauf hin, dass der Kühlschmierstoff den Werkzeugverschleiß reduzieren kann. Liu [19] untersuchte den Einfluss atmosphärischer Moleküle auf die Oberflächenqualität und den Werkzeugverschleiß beim Nanoschneiden. Die Ergebnisse zeigten, dass aufgrund der Schmierung von atmosphärischen Molekülen die Schnittkraft abnimmt und der Werkzeugverschleiß reduziert wird. Singh [20] untersuchte den Einfluss von Nanopartikel-Schneidflüssigkeit auf den Metallabtragsprozess. Wang [21] diskutierte den Einfluss von Wassermolekülen auf tribologisches Verhalten und Eigenschaftsmessungen in Nano-Eindringprozessen und stellte fest, dass die Beteiligung von Wassermolekülen die anfängliche Eindrückkraft erhöht und die größte Eindrückkraft verringert. Chavoshi [22] untersuchte das Hochtemperatur-Nanokratzen von einkristallinem Silizium unter reduzierten Sauerstoffbedingungen, und in der Simulation wurden keine Überreste von Hochdruck-Siliziumphasen beobachtet.
Aus der verfügbaren Literatur basieren bisherige Forschungen zu Nanoschneidprozessen mit fluiden Medien auf Simulationsmodellen von wenigen Molekülen oder Nanopartikeln, die im Bereich der Werkzeug-Chip-Grenzfläche angesiedelt sind. In anderen Bereichen werden jedoch keine flüssigen Medien hinzugefügt und die Schmierung flüssiger Medien wird nur eingeschränkt analysiert. Aufgrund des Mangels an flüssigen Medien in den Modellen beeinflusst die Kühlwirkung der flüssigen Medien den Nanoschneidprozess nicht, während die Kühlwirkung der flüssigen Medien genauso wichtig ist wie die Schmierwirkung auf die Bearbeitungsgenauigkeit und Oberflächenqualität.
Daher werden in dieser Arbeit das Schneidwerkzeug und das Werkstück vollständig von den Schneidflüssigkeitsmedien umgeben, die nicht nur im Wirkungsbereich der Werkzeug-Span-Grenzfläche vorhanden sind, sondern auch in den Bereichen Werkstückoberfläche, bearbeitete Oberfläche und rückwärtiger Bereich vorhanden sind des Werkzeugs. Somit kann die ausreichende Schmierung flüssiger Medien zwischen Schneidwerkzeug und Werkstück untersucht werden. Darüber hinaus werden die fluiden Medien während des Nanoschneidprozesses auf eine konstante Temperatur eingestellt und auch die Kühlwirkung der fluiden Medien kann gut untersucht werden. Kühlschmierstoffe auf Wasserbasis werden häufig in Ultrapräzisionsbearbeitungsprozessen verwendet, die nicht nur Wasser, sondern auch lösliche Grundöle, Rizinusöl, Triethanolamin, Borsäure, Tenside, Polyethylenglykol und Natriumphosphat enthalten. Trotzdem ist der Hauptbestandteil des Kühlschmierstoffs Wasser, und der Massenanteil von Wasser in Kühlschmierstoff erreicht etwa 70 %. Aufgrund der Schwierigkeiten bei der Erstellung von MD-Modellen aller anderen Substanzen und der unbekannten potentiellen Funktionsparameter kann die Untersuchung zum Nanoschneiden unter Verwendung von wasserbasierten Kühlschmierstoffen nicht mit molekulardynamischen computergestützten Simulationsmethoden durchgeführt werden. Daher wird das Medium Wasser, das der Hauptbestandteil von Kühlschmierstoffen ist, in dieser Forschung verwendet, um wasserbasierte Kühlschmierstoffe während der Simulation von Nano-Schneidprozessen zu ersetzen. Basierend auf dem etablierten MD-Modell wird der Nanoschneidprozess durchgeführt, um den Einfluss von Wassermedien auf den Materialabtrag und den Mechanismus der Defektbildung unter der Oberfläche zu untersuchen. Die Entwicklung von Fehlern unter der Oberfläche, die Variation der Schnittkraft, die Temperaturverteilung des Werkstücks und die Kristalltransformation unter der Oberfläche werden mit Hilfe von Centro-Symmetry Parameter (CSP), Common Neighbor Analysis (CNA) und Dislokationsextraktalgorithmus (DXA)-Methoden untersucht .
Methoden
Simulationsmodell
Um den Einfluss flüssiger Medien auf den Materialabtrag und die Entstehung von unterirdischen Defekten beim Nanoschneiden zu untersuchen, werden die MD-Modelle mit und ohne wässrige Medien etabliert, wie in Abb. 1 gezeigt. In den Modellen werden Wassermoleküle nach den TIP4P-Modell [23,24,25]. Das CHARMM-Kraftfeld und die Lennard-Jones (L-J)-Potentialfunktion werden verwendet, um die Bewegung von Wassermolekülen genau zu berechnen. Es kann den Effekt der nichtbindenden potentiellen Energie, des Bindungsexpansionspotentials, der potentiellen Biegeenergie des Bindungswinkels und der molekularen Schwingung umfassend analysieren, was die Simulation von Wassermolekülen genauer macht. Das Werkstückmaterial ist einkristallines Kupfer und das Bearbeitungswerkzeug besteht aus Diamantmaterialien. Es enthält 62835 Wassermoleküle, 368208 Cu-Atome und 2452 C-Atome. Das Werkstück ist in drei Teile unterteilt, die Newtonschicht, Temperaturschicht und Grenzschicht sind. Um den Größeneffekt zu reduzieren, wird die periodische Randbedingung (PBC) bei [001] und [010] übernommen. Um den Druck und die Dichte von Wassermedien zu erhalten, werden die reflektierenden Wände auf beiden Seiten der [001]-Richtung verwendet. Da im eigentlichen Bearbeitungsprozess das Kühlmittel den Großteil der Schnittwärme abführt, wird die Wasserumgebung bei dieser Arbeit auf eine konstante Temperatur von 300 K eingestellt. Das MD-Simulationsmodell mit Vakuumumgebung ist in Abb. 1b gezeigt, wo die anfänglichen Simulationsbedingungen denen des Fluidumgebungsmodells ähnlich sind. Die unterschiedlichen Einstellungen zwischen den beiden Modellen sind die relevanten Einstellungen für wässrige Medien. Die detaillierten Schnittparameter sind in Tabelle 1 aufgeführt.

Die MD-Simulationsmodelle im Nano-Schneiden. a Die Verwendung von wässrigen Medien. b Die Verwendung einer Vakuumumgebung
Interatomare Potentialfunktionen
Bei MD-Simulationen spielt die Potentialfunktion eine entscheidende Rolle für die Simulationsergebnisse. Die Materialeigenschaften werden grundsätzlich durch die Wechselwirkung zwischen Atomen gesteuert. In dieser Forschung ist das Modell in drei Teile unterteilt, nämlich Werkstück, Schneidwerkzeug und wässrige Medien, und enthält vier Atomtypen, nämlich Cu-, C-, H- und O-Atome. Die Wechselwirkungen zwischen verschiedenen Atomen werden durch das Morse-Potential, das Embedded-Atom-Methode (EAM)-Potential, das Lennard-Jones (L-J)-Potential und das Tersoff-Potential berechnet. Die detaillierte Einführung der ausgewählten Potentialfunktion zwischen verschiedenen Atomen ist in Tabelle 2 dargestellt.
Morse-Potenzial
Die Wechselwirkung zwischen Cu-Atomen im Werkstück und C-Atomen im Schneidwerkzeug wird durch das Morsepotential berechnet, das als Gl. (1) [26].
$$ u\left({r}_{ij}\right)=D\left[\exp \left(-2\alpha \left({r}_{ij}-{r}_0\right)\right )-2\exp \left(-\alpha \left({r}_{ij}-{r}_0\right)\right)\right] $$ (1)wo r 0 , α , und D , bzw. sind Atomabstand, Elastizitätsmodul und Bindungsenergie. Die Werte von r 0 , α , und D sind in Tabelle 3 aufgeführt.
EAM-Potenzial
Die interatomare Funktion zwischen den Cu-Atomen im Werkstück wird durch das EAM-Potential beschrieben, das als Gl. (2) und (3) [27, 28].
$$ E\kern0.5em =\kern0.5em \sum \limits_i^N\left[F\left({\rho}_i\right)\kern0.5em +\kern0.5em \sum \limits_{j\kern0 .5em>\kern0.5em i}^Nu\left({r}_{ij}\right)\right] $$ (2) $$ {\rho}_i\kern0.5em =\kern0.5em \sum \limits_jf\left({r}_{ij}\right) $$ (3)Lennard-Jones Potenzial
Die Lennard-Jones-Potentialfunktion ist ein duales Potential, das die Wechselwirkung sowohl der weitreichenden Coulomb-Kraft als auch der kurzreichweitigen Van-der-Waals-Kraft zwischen Atomen umfasst. Das L-J-Potential wird oft verwendet, um die flüssigen Materialien zu simulieren. In dieser Arbeit wird das Lennard-Jones-Potential verwendet, um die Wechselwirkung zwischen Wassermolekülen und anderen Atomen zu berechnen, die als Gl. (4) [29].
$$ {U}_{LJ}(r)\kern0.5em =\kern0.5em 4\varepsilon \left[{\left(\frac{\sigma}{r}\right)}^{12}\kern0 .5em -\kern0.5em {\left(\frac{\sigma }{r}\right)}^6\right] $$ (4)wo σ ist der Gleichgewichtsabstand, wenn die potentielle Wechselwirkungsenergie gleich Null ist und ε ist die Tiefe der potentiellen Energiefalle.
Für verschiedene Materialien, σ und ε kann durch Gl. (5) und (6) [29].
$$ {\sigma}_{\alpha\beta}\kern0.5em =\kern0.5em \frac{\sigma_{\alpha\alpha}\kern0.5em +\kern0.5em {\sigma}_{\beta \beta}}{2} $$ (5) $$ {\varepsilon}_{\alpha \beta}\kern0.5em =\kern0.5em \sqrt{\varepsilon_{\alpha \alpha}\cdot {\varepsilon }_{\beta \beta}} $$ (6)Die in dieser Untersuchung verwendeten interatomaren L-J-Potentialparameter sind in Tabelle 4 aufgeführt.
Terseff-Potenzial
Die Wechselwirkung zwischen den Kohlenstoffatomen im Diamantwerkzeug wird durch das Tersoff-Potential berechnet, das als Gl. (7) und (8) [30].
$$ E\kern0.5em =\kern0.5em \frac{1}{2}\sum \limits_{i\ne j}{V}_{ij} $$ (7) $$ {V}_{ij }\kern0.5em =\kern0.5em {f}_c\left({r}_{ij}\right)\left[{V}_R^{\hbox{'}}\left({r}_{ ij}\right)\kern0.5em +\kern0.5em {b}_{ij}{V}_A\left({r}_{ij}\right)\right] $$ (8)wo f c (r ij ) ist die Trunkierungsfunktion zwischen Atomen, V A (r ij ) ist das duale Potential des Absorptionsterms, V R (r ij ) ist das duale Potential des Abstoßungsterms und r ij ist der Atomabstand zwischen Atom i und Atom j .
Fehleranalysemethoden
Beim Nanoschneiden von einkristallinem Kupfer werden Verformungen und Versetzungen am Untergrund des Werkstücks nukleiert. In diesem Beitrag wird der Zentrosymmetrieparameter (CSP) eingeführt, um die Versetzungskeimbildung und Defektentwicklung des Werkstücks zu analysieren. Für kubisch-flächenzentrierte (FCC) Materialien kann der CSP-Wert nach Gl. (9) [31].
$$ CSP\kern0.5em =\kern0.5em \sum \limits_{i\kern0.5em =\kern0.5em 1}^6{\left|{R}_i\kern0.5em +\kern0.5em {R }_{i+6}\right|}^2 $$ (9)wo R ich sind die benachbarten Atome mit gleichem Abstand und R i + 6 sind die Nachbaratome mit entgegengesetzter Richtung. Die CSP-Werte von FCC-Kristallen, partiellen Versetzungen, Stapelfehlern und Oberflächenatomen betragen 0, 2,1, 8,3 bzw. 24,9 [32]. Der Bereich des CSP-Werts für die typische Kristallstruktur und die Atomfärbung sind in Tabelle 5 aufgeführt.
Die CSP-Methode ist in der Lage, die atomare Konfiguration zu identifizieren, kann jedoch den lokalen atomaren Kristallstrukturzustand des Werkstücks nicht erkennen. Daher wird die Common Neighbour Analysis (CNA) eingeführt, um die lokale Kristallstruktur des Werkstücks zu identifizieren. In der ursprünglichen CNA-Methode von Honeycutt [33] werden die verschiedenen Strukturen durch Diagramme dargestellt. Gegenwärtig wird es verbessert, fünf Arten von Strukturen in der OVITO-Software schnell zu identifizieren [34, 35], nämlich kubisch flächenzentriert (FCC), hexagonal dicht gepackt (HCP), kubisch raumzentriert (BCC), ikosoedrisch (ICO) und unbekannt. In diesem Beitrag wird auch der Versetzungsextraktalgorithmus (DXA) [36] vorgestellt, um die Entwicklung von Versetzungsdefekten zu analysieren. Beim DXA-Verfahren werden die unterschiedlichen Kristallstrukturen im Werkstück mit unterschiedlichen Farben markiert und die Versetzungsfehler im Werkstück durch verschiedenfarbige Linien dargestellt.
Ergebnisse und Diskussion
Entwicklung von unterirdischen Defekten im Nanoschneidprozess mit wässrigen Medien
Die Schnittansicht des Schneidsystems ist in Fig. 2 gezeigt, das das Schneidwerkzeug, das Werkstück und das Wassermedium während des Nanoschneidprozesses enthält. Um die plastische Verformung des Werkstücks deutlich wahrzunehmen, werden die Ergebnisse mit der CSP-Methode analysiert. Die Schnappschüsse sind teilweise durch den CSP-Wert gefärbt, wie in Fig. 2 gezeigt, wobei Fig. 2a einen Schnittabstand von 5 nm und Fig. 2b einen Schnittabstand von 15 nm aufweist. Es ist zu erkennen, dass sich auf der Oberfläche von einkristallinem Kupfer eine Schicht eines kompakten Wasserfilms bildet, der in Abb. 2a als „monomolekularer Wasserfilm“ dargestellt ist. Der Wasserfilm breitet sich über die gesamten Oberflächen von Schneidwerkzeug und Werkstück aus, in denen die Sauerstoffatome das Zentrum des einkristallinen Kupfergitters einnehmen. Die regelmäßige Anordnung von Wassermolekülen ist das Ergebnis der kombinierten Wirkung der weitreichenden Coulomb-Kraft und der Van-der-Waals-Kraft zwischen Wassermolekülen und Kupferatomen.
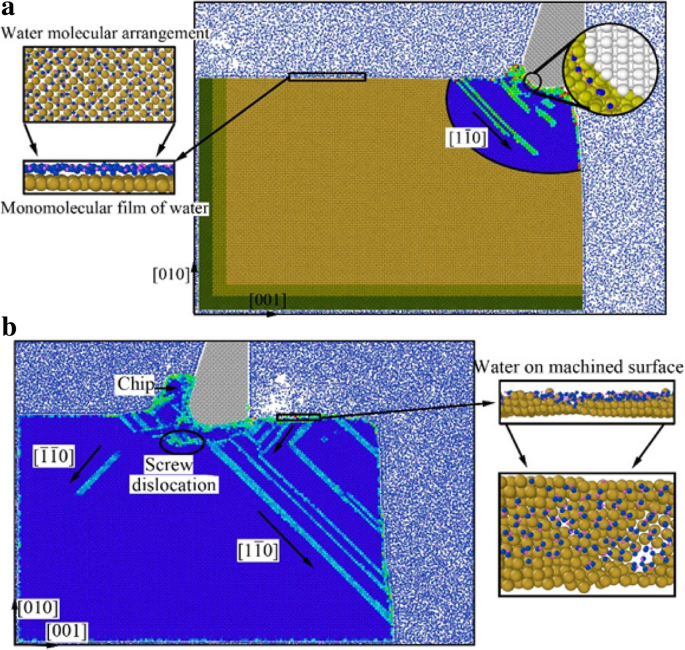
Schnittbild eines Schneidsystems mit wässrigen Medien im Nano-Schneidverfahren (Farbe online). a Schnittabstand l =5 nm. b Schnittabstand l =15 nm
Beim Nano-Schneidprozess wird die Gleitverformung durch die frühe Druckscherwirkung des Schneidwerkzeugs verursacht und als Dehnungsenergie im gebildeten Kristallgitter gespeichert. Wenn die Akkumulation der Dehnungsenergie ein bestimmtes Niveau erreicht hat, wird die Dehnungsenergie freigesetzt. Und dann wird das Gitter des einkristallinen Kupfers neu angeordnet, was zu einer Versetzungskeimbildung und -ausdehnung in Richtung \( \left[1\overline{1}0\right]\) führte, wie in Abb. 2a gezeigt. Aus Fig. 2a ist ersichtlich, dass sich der monomolekulare Wasserfilm auf der Werkstückoberfläche bildet. Darüber hinaus werden die Wassermoleküle im Wirkungsbereich der Grenzfläche Werkzeug-Span in den Untergrund des Werkstücks eingedrungen, was in Abb. 2a rechts oben dargestellt ist. Aufgrund der Schmierwirkung von Wassermolekülen, die zwischen dem Schneidwerkzeug und dem Werkstück vorhanden sind, wird die Druckscherwirkung des Schneidwerkzeugs abgeschwächt. Und die Akkumulation der Dehnungsenergie nimmt ab und die Versetzungen dehnen sich unzureichend aus. Außerdem entzogen die wässrigen Medien viel Schneidwärme, und die Energie der nukleierten Versetzungsexpansion ist unzureichend. Daher ist die Versetzungsausdehnung unzureichend und die Versetzungslinie im Untergrund des Werkstücks ist unauffällig, wie in Fig. 2a gezeigt.
Während sich das Schneidwerkzeug vorwärts bewegt, erlitt das Werkstück die Extrusions- und Reibungswirkung, die durch die Freifläche des Schneidwerkzeugs erzeugt wird. Unter der Extrusions- und Reibwirkung des Schneidwerkzeugs bildeten sich eine große Anzahl von Versetzungen und breiteten sich im Untergrund des Werkstücks aus. Ein Teil dieser Versetzungen bewegt sich entlang der Spanfläche nach oben und wird schließlich als Schneidspäne entfernt, wie in Fig. 2b gezeigt. Ein anderer Teil dieser Versetzungen bewegt sich entlang der Spanfläche des Schneidwerkzeugs nach unten und wird nach der Extrusionsreibung der Freifläche des Schneidwerkzeugs in eine rauh bearbeitete Oberfläche umgewandelt, die in Fig. 2b als „Wasseranordnung auf der bearbeiteten Oberfläche“ dargestellt ist. ” Andere Teile der Versetzungen bewegen sich nach innen entlang der \( \left[\overline{1}\overline{1}0\right] \) und \( \left[1\overline{1}0\right] \) Gleitebene und verschwinden innerhalb des Werkstücks, was zur Bildung von Schraubenversetzungen führt, wie in Fig. 2b gezeigt. Aufgrund der allmählich ansteigenden Spanhöhe können die Wassermoleküle vor dem Span im späteren Schnittverlauf nicht über den Span bis hinter das Schneidwerkzeug fließen. Und die Dichte und der Druck des Wassermediums hinter dem Schneidwerkzeug nehmen schnell ab, was dazu führt, dass die Schneidwärme während des Nanoschneidprozesses vorzeitig abgeführt wird. Daher haben die nukleierten Versetzungen genügend Energie, um sich in das Innere des Werkstücks auszudehnen, wie in Abb. 2b gezeigt.
Um die zugrunde liegende Deformation von Versetzungen und die lokale atomare Kristallstruktur von einkristallinem Kupfer während des Nanoschneidprozesses aufzuklären, werden die CSP- und DXA-Analysemethoden vorgestellt. Die Analyseergebnisse werden wie in den Fig. 1 und 2 gezeigt dargestellt. 3, 4, 5 und 6, darunter Abb. 3 und 4 werden gemäß dem CSP-Wert gerendert und die Fign. 5 und 6 werden durch das DXA-Analyseergebnis eingefärbt.
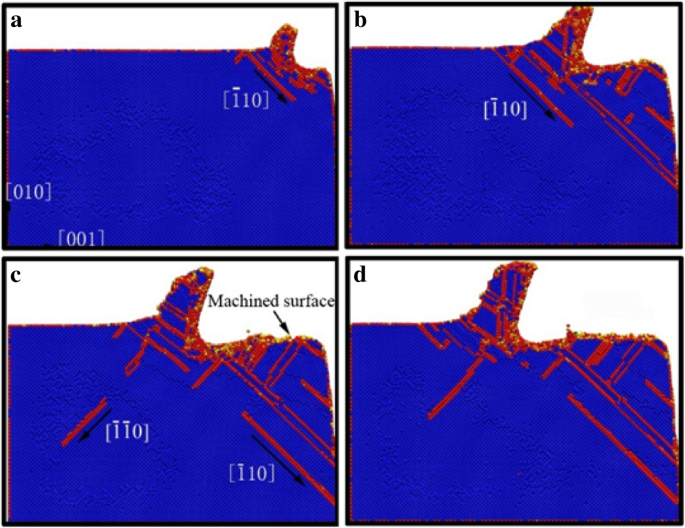
Fehlerverteilung unter der Oberfläche von Werkstücken mit wässrigen Medien im Nano-Schneidprozess. Die Schnittabstände von a , b , c , und d sind 5 nm, 8 nm, 12 nm bzw. 15 nm.
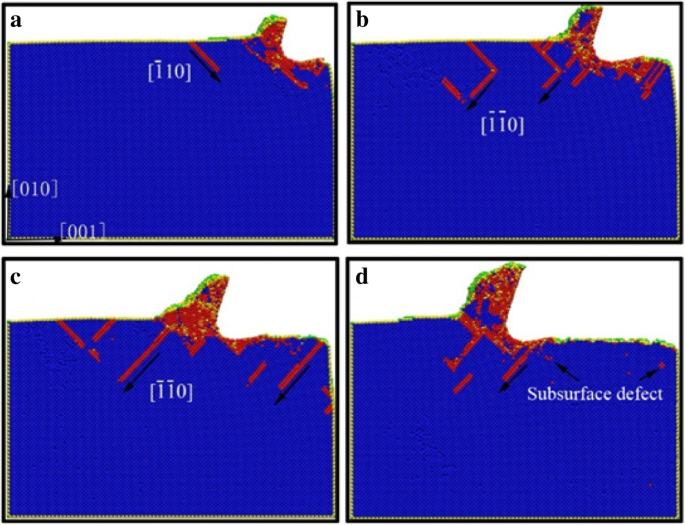
Fehlerverteilung unter der Oberfläche des Werkstücks während des Nanoschneidprozesses in einer Vakuumumgebung. Die Schnittabstände von a , b , c , und d sind 5 nm, 8 nm, 12 nm bzw. 15 nm.
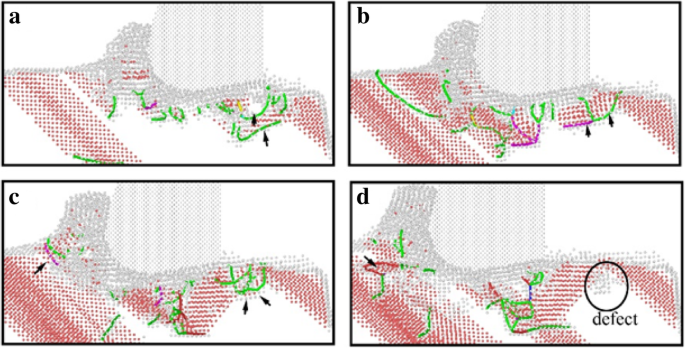
Das DXA-Bild des Werkstücks im Frühstadium des Nanoschneidens. Luxationen sind nach folgendem Schema eingefärbt:tiefblau für perfekte Luxationen, grün für Shockley-Dislokationen, rosa für Treppenstangen-Dislokationen, gelb für Hirth-Dislokationen, hellblau für Frank-Dislokationen und rot für nicht identifizierte Luxationen. Die Schnittabstände von a , b , c , und d sind 7 nm, 8 nm, 9 nm bzw. 10 nm
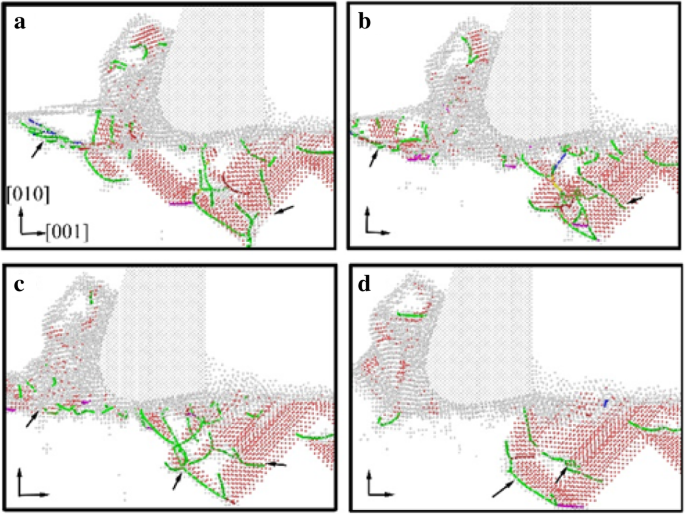
Das DXA-Bild des Werkstücks in der späteren Zeit des Nanoschneidens. Das Farbschema der Versetzungen ist das gleiche wie in Abb. 5. Die Schnittabstände von a , b , c , und d sind 17 nm, 18 nm, 19 nm bzw. 20 nm
Die unter der Oberfläche liegende Defektverteilung des Werkstücks im Nanoschneidprozess mit wässrigen Medien ist in Abb. 3 gezeigt, in dem das Wassermedium nicht angezeigt wird, um die Versetzungsfehlerentwicklung deutlicher zu beobachten. Die gelben, grünen, roten und orangefarbenen Bereiche repräsentieren Oberflächenatome, Oberflächendefektatome, Versetzungsatome bzw. unterirdische Defektatome. Die Versetzungsverteilung und Ausdehnung des Werkstücks im Nano-Schneidprozess ohne wässrige Medien ist in Abb. 4 dargestellt. Aus den beiden Abbildungen ist zu erkennen, dass die nukleierten Versetzungen entlang der \( \left[\overline{1}10 \right] \) Gleitvektor beim Nanoschneidprozess mit wässrigen Medien, jedoch entlang des \( \left[\overline{1}\overline{1}0\right] \) Gleitvektors beim Nanoschneiden unter Vakuummedien . Wie wir wissen, verursacht die Scherwirkung des Schneidwerkzeugs Versetzungen, die sich entlang der Richtung gegen das Werkzeug nach vorne erstrecken, was dem Gleitvektor \( \left[\overline{1}10\right]\) entspricht. Die Reibungswirkung des Schneidwerkzeugs führt dazu, dass die Versetzung entlang der Richtung der orthokinetischen Werkzeugbewegung wandert, die ein \( \left[\overline{1}\overline{1}0\right]\)-Schlupfvektor ist. Während des Nanoschneidprozesses in einer Vakuumumgebung sind die Aktionen des Schneidwerkzeugs auf das Werkstück Scherwirkung der Spanfläche und Reibungswirkung der Freifläche, während die Bildung von bearbeiteten Oberflächen- und Untergrundfehlern durch die Reibungswirkung der Freifläche ausgelöst wird. Daher breitete sich die Versetzungsausdehnung entlang des Gleitvektors \(\left[\overline{1}\overline{1}0\right]\) während des Nanoschneidprozesses im Vakuum aus. Durch die Schmierung der zwischen Werkzeug und Werkstück vorhandenen Wassermoleküle wird die Reibwirkung des Schneidwerkzeugs reduziert. Somit spielt die Scherwirkung eine wichtige Rolle bei der Bildung von maschinell bearbeiteten Oberflächen- und Untergrunddefekten. Daher erstrecken sich die Versetzungen beim Nanoschneiden mit wässrigen Medien hauptsächlich entlang des \( \left[\overline{1}10\right] \) Gleitvektors.
Von Feigen. In den 3 und 4 kann festgestellt werden, dass das Ausmaß der unter der Oberfläche liegenden Defekte in Wassermedien während des Nanoschneidprozesses größer ist als im Vakuum. Tatsächlich breiten sich die Versetzungsfehler über den gesamten bearbeiteten Bereich aus und erstrecken sich tief in das Werkstück. Die Schneidwärme wird durch Wassermedien abgeführt und die Energie der defekten Atome wird verringert. Daher haben die Defekte unter der Oberfläche nicht genug Energie, um vernichtet zu werden. Daher wird der Versetzungsdefektrest erhöht. Die Tiefe der unter der Oberfläche liegenden Defektschicht ist für den Nanoschneidprozess mit Wassermedien relativ höher. Aufgrund der Wechselwirkungen zwischen Wassermolekülen, Kohlenstoffatomen und Kupferatomen wird die Extrusionsreibung zwischen Schneidwerkzeug und Werkstück abgeschwächt und die atomare Unordnung der bearbeiteten Oberfläche wird beim Bildungsprozess der bearbeiteten Oberfläche verstärkt. Darüber hinaus wird der Defektrückstand im Untergrund verschlimmert und die Untergrundeigenspannung wird erhöht.
Um den Einfluss von Wassermedien auf den Entstehungsprozess von Versetzungsdefekten besser aufzuzeigen, wird die DXA-Methode verwendet, um das Werkstück im Nanoschneidprozess mit wässrigen Medien zu analysieren, wobei die Frühphase und die Spätphase wie in Abb. 5 dargestellt sind bzw. 6. Ein stabiler Kristalldefekt findet sich in mehreren Atomschichten unterhalb der bearbeiteten Oberfläche im frühen Stadium des Nanoschneidprozesses, der sich zwischen zwei Stapelfehlern befindet, wie in Fig. 5d gezeigt. Das Vorhandensein von Kristallfehlern beeinflusst die Qualität der bearbeiteten Oberfläche und führt sogar zur Bildung von Mikrorissen auf der bearbeiteten Oberfläche. Daher wird die Bildung des Defektentwicklungsprozesses untersucht. Aus Fig. 5a ist ersichtlich, dass eine Menge von Shockley-Teilversetzungen unter der Reibungswirkung der Freifläche des Schneidwerkzeugs im frühen Moment der Defektbildung nukleiert wird. Diese Shockley-Versetzungen entwickeln sich während des Vorwärtsfahrens des Schneidwerkzeugs zu einer V-förmigen Versetzungsschleife, wie in Fig. 5b gezeigt. Anschließend entwickelt sich die V-förmige Luxation allmählich zu seriellen Shockley-Teilluxationen. Schließlich werden die partiellen Versetzungen in Restdefekte im Untergrund umgewandelt. Aufgrund der Abfuhr der Schneidwärme durch Wassermedien haben die defekten Atome zu wenig Energie, um vernichtet zu werden, und werden in unbewegliche Defekte unter der bearbeiteten Oberfläche umgewandelt. Die Rauheit der bearbeiteten Oberfläche wird erhöht und Restspannungen im Untergrund verursachen eine weitere Verschlechterung. Darüber hinaus kann durch den Defekt ein Oberflächenmikroriss induziert werden.
Der Einfluss von Wassermedien auf die Scherschlupfwirkung des Schneidwerkzeugs während des Zerspanprozesses wird mit der DXA-Methode untersucht, die in Abb. 6 gezeigt ist. Aus Abb. 6a ist ersichtlich, dass eine große Anzahl von Shockley-Teilversetzungen in Vorderseite des Schneidwerkzeugs. Und die Schergleitebene wird durch diese Versetzungen gebildet. Im folgenden Schneidprozess werden serielle Stapelfehler und partielle Versetzungen nukleiert und auf der Schergleitebene verlängert. Unter der Keimbildung und Bewegung der Versetzungen vor dem Schneidwerkzeug wird der Schneidspäne nach und nach entlang der Schergleitebene entfernt, wie in Fig. 6c gezeigt. Währenddessen wird der Extrusionsreibungseffekt der Werkzeugspanfläche aufgrund der Schmierwirkung von Wassermedien gemindert. Die Versetzungskeimbildung und -ausbreitung ist unzureichend, und der Rückstand von unterirdischen Defekten ist während des Nanoschneidprozesses nicht offensichtlich, wie in Abb. 6a–d gezeigt. Dementsprechend wird die Scherwirkung des Schneidwerkzeugs auf das Werkstück bedeutender. Daher ist der gebildete Chip unter Beteiligung von Wassermedien im Nanoschneidprozess leichter zu entfernen. Gleichzeitig nimmt die Hauptschneidkraft ab, was später in diesem Artikel ausführlich besprochen wird.
Einfluss von Wassermedien auf die Variation von Schneidkraft und Schneidhitze
Beim Schneidprozess erfolgt der Materialabtrag durch die Extrusions- und Scherwirkung des Schneidwerkzeugs. Aufgrund der Festigkeit, Steifigkeit und Zähigkeit des Metallmaterials litt die Spanfläche des Schneidwerkzeugs unter der Reaktionskraft, die durch den Verformungswiderstand des Werkstückmaterials während des Materialabtragsprozesses erzeugt wird. Und die Freifläche des Werkzeugs wird durch den Reibungskraftwiderstand der bearbeiteten Oberfläche beeinflusst. Diese Kräfte setzten die Schnittkraft zusammen. Gleichzeitig wird die aufgebrachte Arbeit durch die Scherverformung der Schneidspäne sowie die Reibung zwischen Schneidwerkzeug und Werkstück in Schneidwärme umgewandelt, was zu einer erhöhten Temperatur des Werkstücks führt. Einhergehend mit der Ansammlung und Freisetzung von Materialdehnungsenergie traten Versetzungskeime und -expansion an der Untergrundschicht des Werkstücks auf, die eine Schwankung der Schnittkraft und der Schnittwärme mit der Schnittstrecke induzierten.
In dieser Forschung hat die Beteiligung von Wassermedien großen Einfluss auf die Variation von Schnittkraft und Schnittwärme. Die Variationskurven der Schnittkraft mit dem Schnittabstand im Nano-Schneidprozess mit und ohne Verwendung wässriger Medien sind in den Abbildungen und Abbildungen dargestellt. 7 und 8, in denen die schwarze, rote bzw. blaue Kurve Vorschubkraft (Fx), Gegenkraft (Fy) und Tangentialkraft (Fz) sind. Da die PBC in Z-Richtung übernommen wird und das Diamantwerkzeug in der Simulation entlang der Z-Richtung säulenförmig ist, liegt die durchschnittliche Tangentialkraft (Fz) in beiden Figuren auf dem Niveau von 0 nN. 7 und 8.
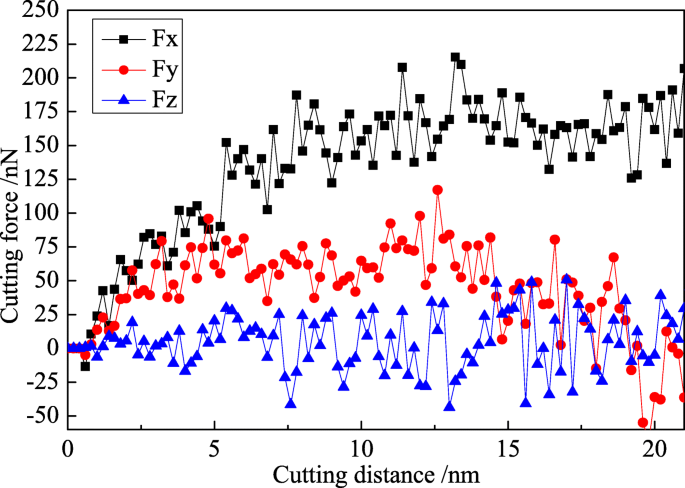
Variationskurve der Schnittkraft beim Nanoschneiden mit Vakuumumgebung
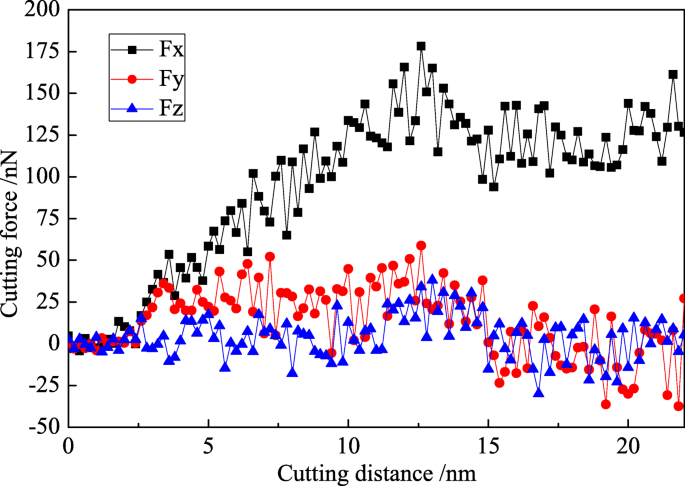
Variationskurve der Schnittkraft beim Nanoschneiden mit Wassermedien
Der Schneidprozess ist in die anfängliche Schneidphase und die stabile Schneidphase unterteilt, wie in Abb. 7 gezeigt. In der anfänglichen Schneidphase werden die Vorschubkraft und die Gegenkraft in einer geraden Linie stark erhöht. Und sie erreichten ihre Maximalwerte, wenn das Schneidwerkzeug vollständig in das Werkstück einschnitt. Im stabilen Schnittzustand schwanken die Schnittkräfte in ihrer Gleichgewichtslage auf und ab, die Vorschubkraft erreicht mehr als 200 nN und die mittlere Schnittkraft beträgt ca. 180 nN. Die Gegenkraft ist sehr gering und nimmt im späten stabilen Schnittstadium allmählich ab. Der Maximalwert der Backkraft liegt unter 100 nN, der Durchschnittswert liegt bei etwa 50 nN. Generally speaking, the specific value between average back force and average feed force (Fy/Fx) represents the friction coefficient between tool material and workpiece material in machining process. In this research, the friction coefficient between diamond and monocrystal copper is 0.278 under vacuum environment.
The feed force and the back force are decreased in nano-cutting with water media compared with vacuum environment, as shown in Fig. 8. The maximum feed force reaches 150 nN, and the mean feed force fluctuates at 120 nN. The variation tendency of back force is similar with the back force in vacuum environment, and the mean force is at about 25 nN. In nano-cutting process with the use of water medium, the friction coefficient between the cutting tool and the workpiece is reduced due to the lubrication of water. And then the frictional resistance suffered by the flank surface of cutting tool is reduced, which effectively enhances the extrusion shearing action of the rake surface of cutting tool. The removal of the workpiece material is easier to be removed. Hence, the cutting force is reduced. It can be seen from the foregoing analysis that the water molecules acted as a lubricant to prevent the friction between the cutting tool and the workpiece. Therefore, the values of feed force and back force are reduced in the water media. The specific value between the feed force and the back force is 0.208. In another words, the frictional coefficient between diamond and copper in water media is 0.208, much fewer than they are in vacuum environment (0.278).
Compared with the fluctuation of the Fy in Figs. 7 and 8, it is indicated that the Fy component decreases considerably after 15 nm of cutting distance in both cases with vacuum and water media while the Fx value is almost stable until 20 nm of cutting distance. The dynamic balance between dislocation nucleation and annihilation is achieved, and the chip is removed steadily in nano-cutting process, which results in the cutting force almost stable with the cutting distance before 20 nm. When the cutting process is carried out at a certain distance (15 nm in this research), the dynamic equilibrium between the new dislocation nucleation and the previous dislocation annihilation is established. And the scale of the internal defects of the workpiece is stabilized at a certain level. The dislocation nucleation and annihilation applied an effect on cutting tool along +Y direction, which leads to the Fy component decrease. Besides, the stable cutting chip is removed after 15 nm of cutting distance, and the applied force on the cutting tool from the chip is decreased along the Y direction. Thereby, the value of Fy is reduced. However, when the cutting distance is greater than 15 nm till 20 nm, the emotion of dislocation defect and the removal of chip cannot bring a different influence on the cutting tool along the X direction. Therefore, the value of main cutting force (Fx) is almost stable.
The temperature distribution of the workpiece during the nano-cutting process with and without the use of aqueous media is shown as Fig. 9. The cutting distances of Figs. 9a and b and Figs. 9c and d are 5 nm and 12 nm, respectively. It can be seen from Figs. 9b and d that the temperature of workpiece is distributed as a concentric gradient. The highest temperature is spread all over shear-slip zone and friction zone of the workpiece in a vacuum environment, which is above 420 K. The temperature of the chip and machined surface is higher than other regions, which is ranged from 360 to 390 K. For the whole workpiece, the temperature is at a high level, which is ranged from 340 to 360 K. From Figs. 9a and c, the temperature of the workpiece is also distributed as a concentric gradient and the highest temperature is distributed at the top area of the chip, which is around 370 K. The temperature value of the whole workpiece is at a lower level which is lower than 320 K. The temperature of the shear-slip area, the friction zone, and the machined surface are higher than other areas, which is ranged from 320 to 340 K.
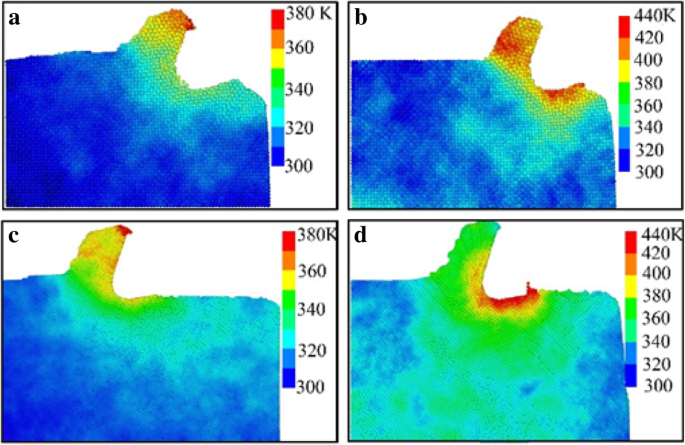
Temperature distribution of workpiece in nano-cutting. a und c are in water media, b und d are in vacuum environment
The highest temperature area of workpiece is transferred from the friction area to the cutting chip during nano-cutting process with water media as shown in Fig 9. And the highest and whole temperature of the workpiece are significantly reduced with the additional use of water media, and the temperature drop reached about 40–60 K. Due to the lubrication effect of water molecules, the friction between cutting tool and machined surface is reduced during nano-cutting process with water media. Hence, the temperature of the friction area declined dramatically. Meanwhile, the maximum shearing deformation occurred at the chip area and the maximum lattice deformation energy is stored in the chip, which makes the temperature of the chip higher than the friction area. Therefore, the highest temperature area is transferred from friction area to the cutting chip. Synchronously, a large amount of cutting heat is taken away by the water media which play a role in cooling the tool, workpiece, and cutting area. And the thermal movement of the monocrystal copper molecules is weakened. Furthermore, the kinetic energy of atomic thermal motion and the lattice deformation energy are decreased significantly. Therefore, the overall temperature and the highest temperature of the workpiece is reduced, whose degree of reduction arrived at 40–60 K. Finally, the thermal stress and thermal deformation of the workpiece are significantly reduced. Because of the participation of water media, the friction action between the flank surface of cutting tool and workpiece is weakened in cutting process. Then, the generation of heat by friction between cutting tool and workpiece is reduced. Thereby, the highest temperature area of the workpiece is transferred from the friction area of flank surface to the chip area. More importantly, the cooling effect and lubrication of water media will affect the nucleation, expansion, and annihilation of the dislocation in subsurface of the workpiece and ultimately affect the formation and evolution of the subsurface damage layers of the workpiece.
Effect of Aqueous Media on Subsurface Defects Structural Transformation
In order to clearly identify the subsurface defects of the workpiece in nano-cutting, the CNA method is used to analyze the workpiece after nano-cutting. The workpiece is colored by different atomic structure. The defect structural distribution of the workpiece during nano-cutting process with and without the use of aqueous media is shown as Figs. 10 and 11, in which the green, red, blue, and grey are FCC, HCP, BCC, and unknown structure, respectively.
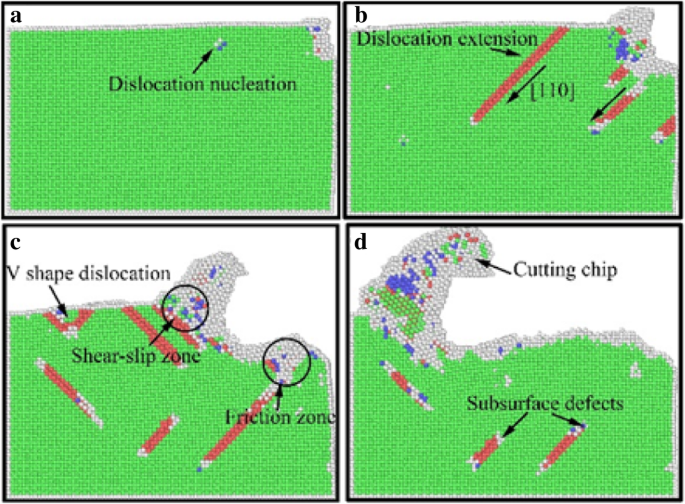
Subsurface defect evolution of workpiece in nano-cutting without aqueous media. The green, red, blue, and grey area are representative of FCC, HCP, BCC, and unknown structure. The cutting distances of a, b, c, and d are 1 nm, 3 nm, 8 nm, and 15 nm, respectively
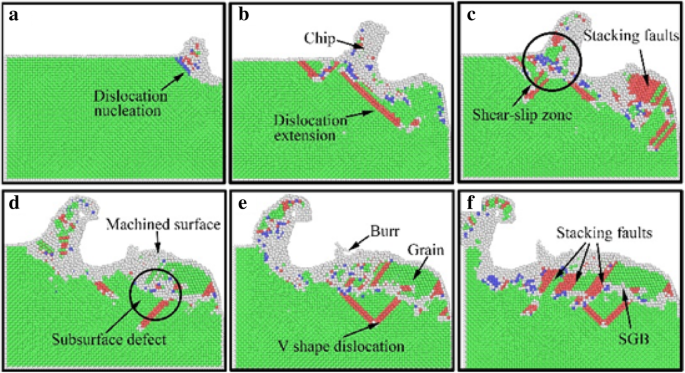
Surface and subsurface defect distribution in nano-cutting for workpiece with water media. The green, red, blue, and grey area are representative of FCC, HCP, BCC, and unknown structure. The cutting distances of a, b, c, d, e, and f are 3 nm, 8 nm, 12 nm, 15 nm, 18nm, and 20nm respectively
In nano-cutting process under vacuum environment, dislocation nucleation occurred at the subsurface of workpiece under the extrusion and shearing action of the cutting tool, and the crystal structure is transformed into BCC, which is shown as Fig. 10a. The nucleated dislocation is extended along \( \left[\overline{1}\overline{1}0\right] \) direction, and the crystal structure is transformed into HCP. The crystal structure of many atoms in the shear-slip region become BCC, as shown in Fig. 10b. Two partial dislocations are extended along the \( \left[\overline{1}\overline{1}0\right] \) and \( \left[1\overline{1}0\right] \) directions, hindered each other, and be composed of Lomer-Cottrell dislocation lock. Finally, a typical V-shaped dislocation loop is formed, as shown in Fig. 10c. Part of the atoms in the shear-slip zone are moved upward along the rake face and are removed as cutting chip. The other part of the atoms are migrated downward along the flank face and are formed into the roughness machined surface by the extrusion and friction of the cutting tool, as shown in Fig. 10d.
The subsurface defect distribution and evolution of workpiece in nano-cutting with the use of water media is shown as Fig. 11. It can be seen from the figure that the mechanisms of dislocation nucleation and crystal structure transformation are similar with the cutting process in vacuum environment. The main difference is that the dislocation nucleation and expansion is insufficient in the nano-cutting process of water media. Besides, there are many stacking faults nucleated in the subsurface of the workpiece. The structure of stacking faults is transformed into HCP structure. Nevertheless, a typical defect “similar-to-grain boundary (SGB)” is formed in the subsurface of the workpiece.
In nano-cutting process, under the action of extrusion, shearing and friction by cutting tool, intense deformation of the workpiece is generated. Plenty of deformation energy and cutting heat are produced. The atomic lattice reconfiguration of subsurface is produced by the release of cutting heat and strain energy. And the subsurface defects and local crystal structure transformation are formed, as shown in Fig. 11a and 11b. When the water media participated in the nano-cutting process, most of the heat and energy is taken away. Hence, the dislocation defects have inadequate energy to extension and movement. Furthermore, the stacking faults are annihilated in the subsurface of the workpiece where the crystal defect structure stayed behind, as shown in Fig. 11c, whereafter these crystal defect structures are connected as a whole and are composed of the subsurface damage (SSD) layer together with the newly formed dislocations, as shown in Fig. 11d. After the following MD relaxation, some subsurface dislocation defects are disappeared and transformed into FCC structure, and the structure similar to “grain” is formed between machined surface and subsurface defects layer, as shown in Fig. 11e, while the original subsurface defects are transformed into a typical structure “similar-to-grain boundary (SGB),” as shown in Fig. 11f. On the SGB structure, a typical V shape dislocation loop is formed, as shown in Fig. 11e, f.
The metamorphic layer is obviously formed by the influence of the formation of SGB and “grain” structure in the subsurface of workpiece. Moreover, the new formed crystal structures which are similar with polycrystalline material can influence the mechanical performance and processability of single-crystal materials. Besides, it will affect even the performance of machined nano-components.
Schlussfolgerungen
Based on the established MD models of single-crystal copper with and without the use of aqueous media, the simulation of nano-cutting process is carried out. The effects of fluid media on material removal and subsurface defect evolution are analyzed. The subsurface defect evolution, variation of the cutting force, the temperature distribution, and the subsurface defects crystal structure transformation of the workpiece are investigated by using CSP, DXA, and CNA methods. The novel results can be summarized as follows.
(1) The material removal of workpiece is realized by the shearing extrusion action of cutting tool on workpiece; the participation of water media has no effect on the mechanism of materials removal. Due to the lubrication action of water molecules existing between the cutting tool and the workpiece, the deformation of workpiece is decreased, the cutting force is reduced, and the height of cutting chip and depth of subsurface damage layer are lowered.
(2) The highest temperature area is transferred from the friction area to the cutting chip during nano-cutting process with the additional use of water media. And the highest and whole temperature of the workpiece are significantly reduced, and the temperature drop reached about 40–60 K. Thereby, the thermal deformation of the workpiece is reduced and the amount of subsurface defect atoms is decreased.
(3) In the subsurface layer of the workpiece, the crystal structures of nucleated dislocations are transformed into BCC, and the extended dislocations are transformed into HCP. The atomic crystal structures in the shear-slip region are becoming BCC. Under the effect of fluid media, the subsurface defects are transformed into a typical defect structure “similar-to-grain boundary (SGB)” in SSD layer, which can influence the mechanical performance and processability of single-crystal materials. Besides, it will affect even the performance of the machined nano-components.
Abkürzungen
- MD:
-
Molekulardynamik
- CSP:
-
Centro-symmetry parameter
- CNA:
-
Common neighbor analysis
- DXA:
-
Dislocation extract algorithm
- PBC:
-
Periodic boundary condition
- EAM:
-
Embedded-atom method
- L-J:
-
Lennard-Jones
- FCC:
-
Face center cubic
- HCP:
-
Close-packed hexagonal
- BCC:
-
Body centered cubic
- ICO:
-
Icosohedral
- SGB:
-
Similar-to-grain boundary
- SSD:
-
Subsurface damage
Nanomaterialien
- Studie zum Effekt der Aufprallrichtung auf den nanometrischen Schleifprozess mit Molekulardynamik
- Arten und Klassifizierung von Bearbeitungsprozessen | Fertigungswissenschaft
- Was ist Bearbeitung? – Definition, Prozess und Werkzeug
- Was ist Autogenschneiden? - Verfahren, Vor- und Nachteile
- Was ist Glühen? - Definition, Prozess und Phasen
- Verbindungsdefekte – Debris-based und Copper Bond Failure
- Die Präzision und den Prozess der Laserschneidtechnologie verstehen
- Wählen Sie die richtige Schneidflüssigkeit entsprechend dem Schneidstoff
- 5 Schneidprozess für Metall in der Fertigung
- Flachschleifservice:Prozess und Präzision