Die Entwicklung additiver Verbundwerkstoffe
Im Oktober 2020, CW berichtete über den 3D-Druck von Verbundwerkstoffen mit Endlosfasern und lieferte eine Landschaft der zu entwickelnden Technologien sowie eine Klassifizierung der verwendeten Verfahren. Letzteres wurde von Alexander Matschinski, wissenschaftlicher Mitarbeiter und Experte für Additive Manufacturing an der TU München und dem Lehrstuhl für Carbon Composites (LCC, München, Deutschland) beigesteuert.
CW arbeitet wieder mit LCC zusammen, diesmal jedoch mit Blick auf die größere Landschaft der additiven Verbundwerkstofffertigung (ACM), insbesondere auf Prozesse, die an der Schnittstelle entwickelt werden zwischen konventionellen Verbundwerkstoffen und additiver Fertigung (AM). „Wir sehen immer mehr Technologien, die außerhalb unserer Klassifizierung für den Endlosfaser-3D-Druck liegen, sondern stattdessen die automatisierte Composite-Fertigung mit AM kombinieren und neue Lösungen anbieten, die bisher nicht möglich waren“, sagt LCC-Forscher Thomas Wettemann.
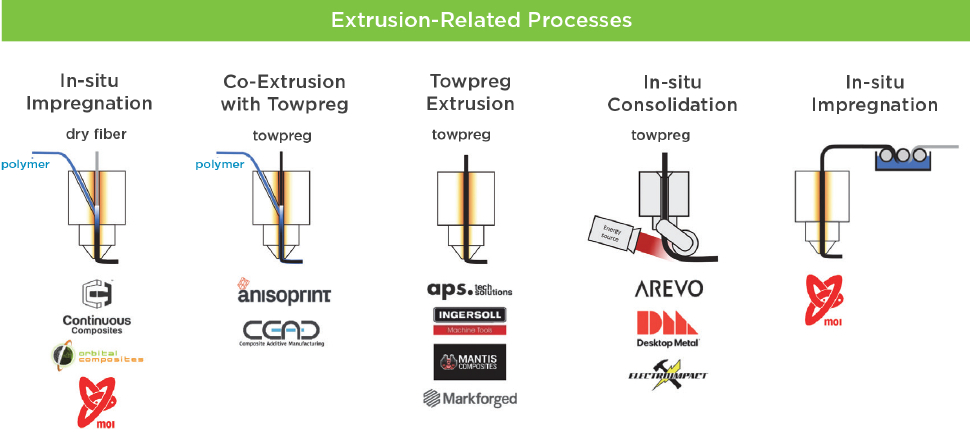
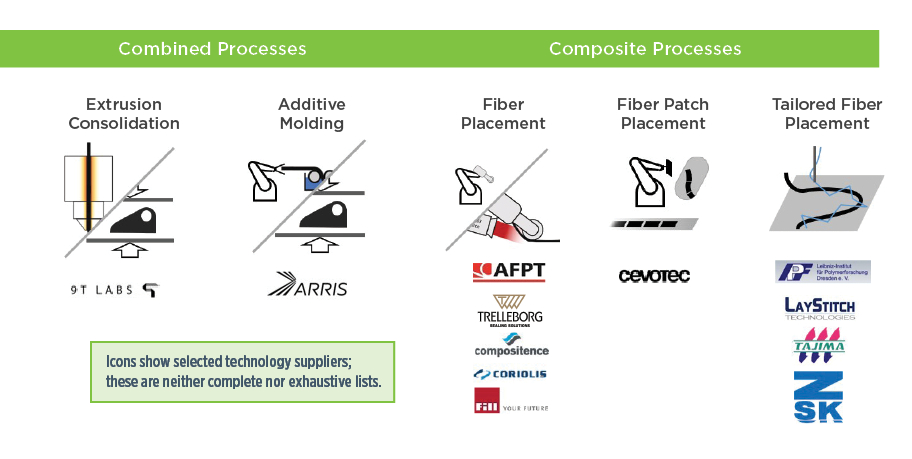
LCC selbst verwischt die Grenzen zwischen traditionellen Verfahren und 3D-Druck, indem es automatisierte Faserplatzierung (AFP) und Filament Winding (FW) mit Extrusions-basierter ACM kombiniert (siehe „Future Composite Manufacturing – AFP and Additive Manufacturing“). „Wir wechseln auch von der traditionellen Extrusion von Thermoplasten zum 3D-Druck mit Duroplasten durch die Adaption von Technologien, die wir für das Resin Transfer Moulding [RTM] entwickelt haben, und die Kombination mit Ultraschall“, sagt Dr. Swen Zaremba, stellvertretender Leiter von LCC. Gleichzeitig arbeitet LCC daran, Standards für ACM zu entwickeln und seine Materialien und Prozesse zu verbessern.
Beachten Sie, dass es eine noch breitere ACM-Landschaft gibt, die geschnittene fasergefüllte Filamente umfasst, die mit Fused Deposition Modeling (FDM) extrudiert wurden, pulverisierte Fasermaterialien, die mit selektivem Lasersintern (SLS) verarbeitet wurden, und hochgradig maßgeschneiderte Teile mit magnetisch orientierten Füllstoffen und digitaler Lichtverarbeitung (DLP), letzteres wurde von Fortify (Boston, Massachusetts, USA) entwickelt. Diese Verfahren produzieren tatsächlich Verbundteile und eröffnen neue Märkte und Anwendungen, aber diese Diskussion wird im Bereich der Endlosfaserverstärkung bleiben.
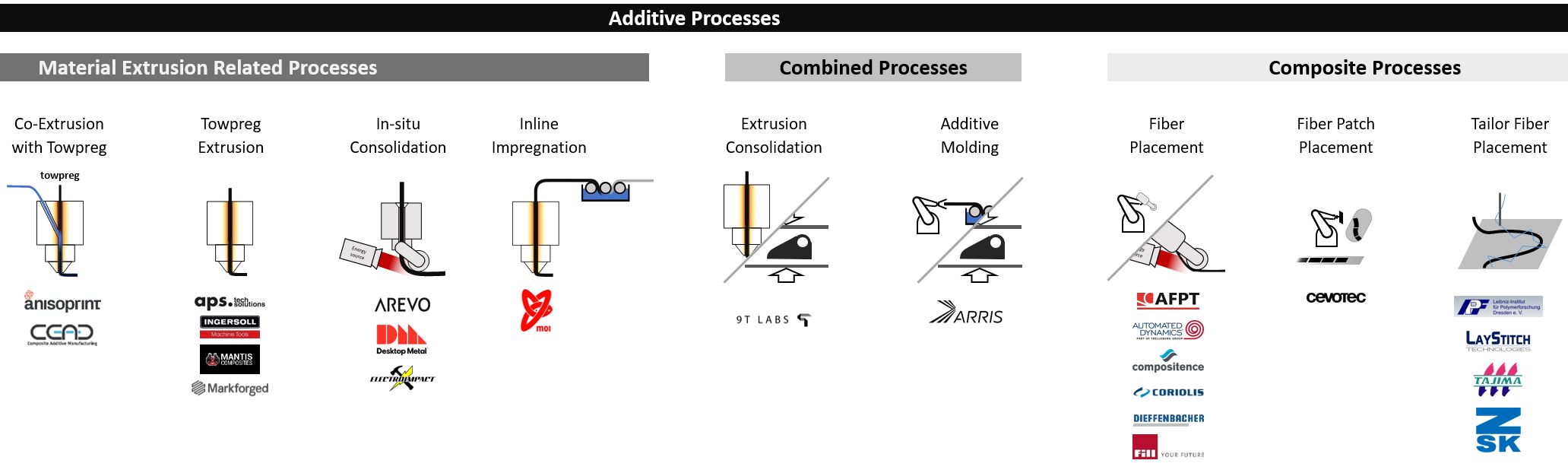
Was ist ACM?
„Diese Diskussion führen wir normalerweise zuerst und auch die Motivation, diese neuen Technologien zu entwickeln“, sagt Zaremba. Wie Wettemann in einer SAMPE-Präsentation im Januar 2019 erläuterte, ist die Motivation eine wirtschaftliche Produktion jenseits der Massenproduktion – auch in Losgröße Eins –, die zudem Ressourcen schont, Abfälle minimiert oder vermeidet sowie umwelt- und klimaschonend ist. „Außerdem bietet es eine Möglichkeit, die Prozesskette der Verbundwerkstoffe vollständig digital zu gestalten“, fügt er hinzu. „Es ist der erste Schritt auf dem Weg zu jahrzehntelangen Veränderungen.“
Zu den wichtigsten Komponenten der LCC-Definition von ACM gehören:
- Lange Prozessketten reduziert auf „Processing in a Box“ an einem Punkt
- Globale Konsolidierung/Polymerisation durch lokale Materialbehandlung und wiederkehrende Wärmebehandlung ersetzt
- Werkzeuglose Produktion
„ACM bündelt die vormals langen Verarbeitungsketten auf mehr oder weniger einen Punkt, eine Art Fertigung in einer Kiste“, sagt Zaremba. So fügt Matschinski hinzu:„Sie bearbeiten die Materialien und geben dem Teil seine Form in dieser Box und ohne Formwerkzeug.“ Beide sind sich einig, dass die „Box“ eine sehr große ACM-Zelle sein kann, zum Beispiel die von Electroimpact (Mukilteo, Washington, USA) im Jahr 2020 vorgestellte SCRAM-Zelle. „ACM kann auch außerhalb einer einzelnen Box verwendet werden“, sagt Zaremba. „zum Beispiel unsere Arbeit, größeren AFP-Teilen lokale Verstärkung und kleinere Features hinzuzufügen.“
Wettemann bemerkt jedoch:„Wir sehen jetzt Beispiele für die gesamte Composites-Prozesskette, die in einer automatisierten Linie oder Zelle enthalten sind, aber das ist nicht das, was wir als ACM definieren würden.“ Die SCRAM-Zelle hingegen hat die Fähigkeit, Material zu verarbeiten und ohne Werkzeuge Form zu geben, indem sie einen thermoplastischen AFP-Kopf (ISC) mit In-Situ-Konsolidierung (ISC) mit einem 3D-Druckkopf aus Fused Filament Fabrication [FFF, ein anderer Begriff für FDM] kombiniert. „Für uns war diese in-situ-Konsolidierung mit AFP tatsächlich der Beginn der ACM am LCC, da Sie die ausgehärteten/verfestigten Komposite während der Platzierung oder des Layups erstellen“, sagt Zaremba.
Dies bringt uns zum zweiten Kernpunkt der LCC-Definition von ACM. „Früher gab es immer einen globalen Konsolidierungsschritt und im Idealfall dieselbe Materialbehandlung und Historie für das Teil, wie es in einem Autoklaven, Ofen, beheizten Werkzeug oder einer Presse geformt wurde“, erklärt Zaremba. „Bei ACM führen wir diese Wärmebehandlung und Konsolidierung auf lokaler Basis durch, während wir das Teil bauen.“
Wettemann weist darauf hin, dass ISC einen Einstiegspunkt aus der automatisierten Composites-Fertigung in die AM-Welt bot, „dies stellt aber auch echte Herausforderungen an die Materialien und Verarbeitung, da diese lokale Materialbehandlung auch eine wiederkehrende Wärmebehandlung ist. Beachten Sie, dass wir am Anfang nur Spritzgussmaterialien für den 3D-Druck angepasst haben. Aber dann haben wir erkannt, dass es nicht wirklich für den FFF-Druck optimiert ist. Daher begannen die Unternehmen, Materialien für ihre Drucksysteme zu modifizieren, um das wiederkehrende Aufheizen und Abkühlen der Harze sowie die erforderliche Geschwindigkeit und die Notwendigkeit, Schichten zusammenzukleben und Verzug zu vermeiden, zu bewältigen. Letzteres ist auch der Grund, warum immer mehr Unternehmen auf Endlosfasern setzen.“
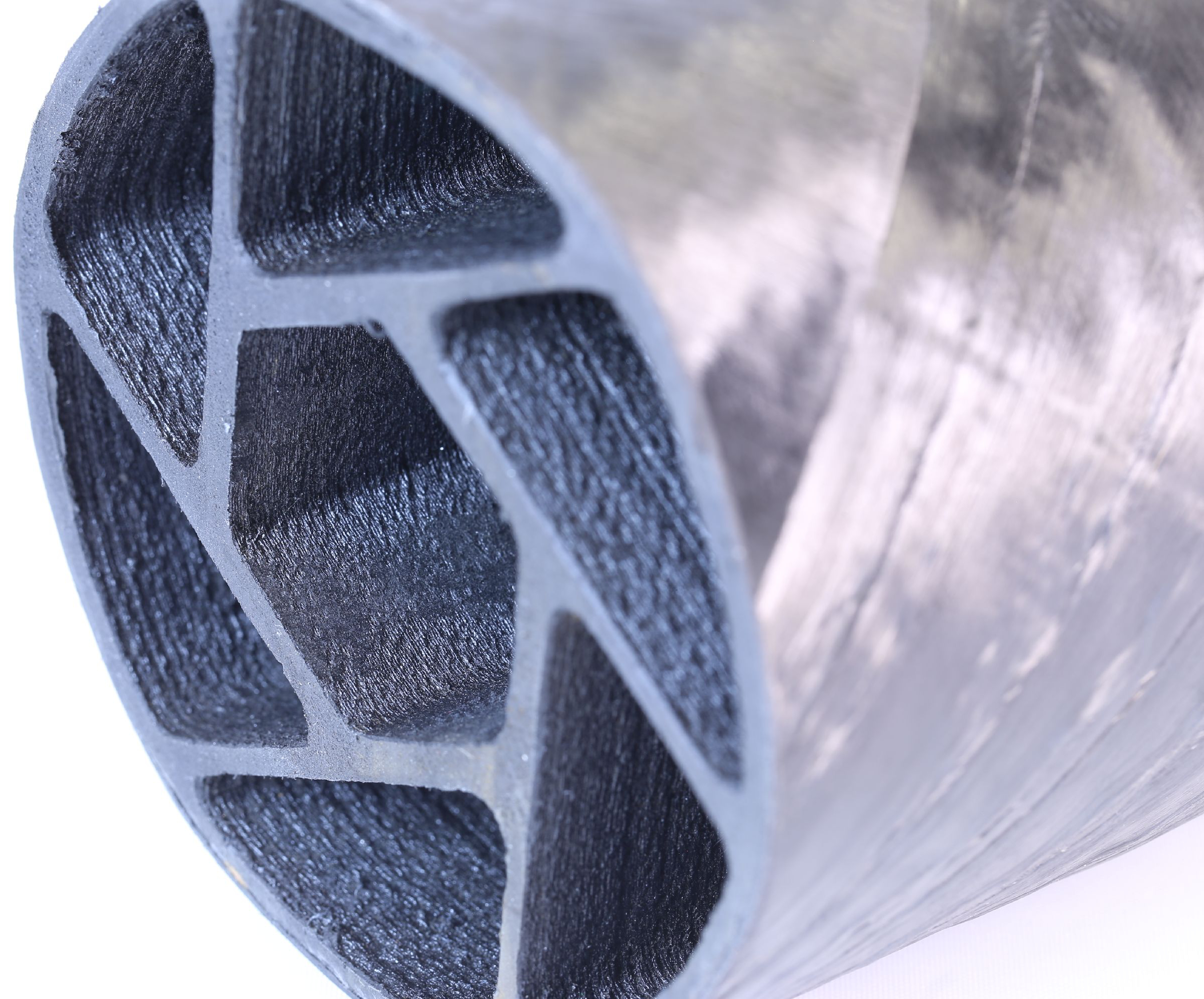
Die Integration von Endlosfasern wirft jedoch auch Probleme auf. „Das ist einer der Gründe, warum uns ACM angezogen hat“, sagt Zaremba. „3D-Druckverfahren versprachen viele Ergebnisse, aber die Ergebnisse lieferten nicht die Qualität, die wir beispielsweise für Struktur- oder Luft- und Raumfahrtanwendungen erwarten. Wir konnten eine Lücke zwischen fortschrittlichen Verbundwerkstoffen mit Endlosfasern und dem, was AM-Technologien leisten können, erkennen. LCC hat sich zum Ziel gesetzt, diese Welten zusammenzubringen und das versprochene Potenzial zu realisieren, aber auch Technologien zu kombinieren, um neue Lösungen zu erreichen.“
Verschmelzung zweier Welten
LCC sieht viele solcher neuen Lösungen, zum Beispiel das von Arris Composites (Berkeley, CA, USA) entwickelte Additive Molding-Verfahren und die von 9T Labs (Zürich, Schweiz) entwickelte Fusion Bonding-Zelle für den 3D-Druck. Volumenprozesse. „Keiner dieser Prozesse liefert die endgültige Form des Teils innerhalb des additiven Prozesses, sondern verwenden eine Art Form und einen zweiten Schritt in dieser Form“, sagt Matschinski. „Dies entspricht also nicht unserer Definition von ACM. Beide bieten jedoch interessante Lösungen, die traditionelle Verbundwerkstoffherstellung und AM-Technologien kombinieren.“
„9T Labs verwendet definitiv 3D-Drucker“, bemerkt Wettemann, „aber um einen Vorformling zu erstellen, der dann in einem digitalisierten Umformprozess verarbeitet wird, um leichte thermoplastische Verbundbauteile herzustellen, die völlig neu sind und Märkte adressieren, die zuvor keine Verbundwerkstofftechnologie verwenden konnten. ” Hier verweist er auf das Ziel von 9T Labs, Metalle in Teilen zu ersetzen, bei denen Spritzguss nicht genügend Leistung erbringen kann. „Bei LCC haben wir auch erforscht, wie man Endlosfasern in den Spritzguss einführt, aber es ist ziemlich schwierig, Endlosfasern im Spritzprozess genau zu positionieren.“ Im Gegensatz dazu bietet die Technologie von 9T Labs eine scheinbar einfach zu implementierende Fertigungsmethode für Hochleistungsteile.
Arris Composites verfolgt einen anderen Ansatz, erreicht aber ein etwas ähnliches Ziel, wenn auch um eine Größenordnung höhere Stückzahlen. „Wir ermöglichen nicht nur die Massenproduktion von Endlosfaserteilen, sondern fügen auch Multifunktionalität hinzu, die eine dynamische Teilekonsolidierung ermöglicht“, sagt Riley Reese, Mitbegründer und CTO von Arris Composites. „Zum Beispiel haben wir eine 17-Komponenten-Baugruppe in ein einziges Teil verwandelt und gleichzeitig die Festigkeit erhöht und Eigenschaften wie Radiotransparenz hinzugefügt. Beim Formpressen – zum Beispiel SMC [Sheet Molding Compound] – sind wir kostenwettbewerbsfähig, aber mit der Leistung von Endlosfasern."
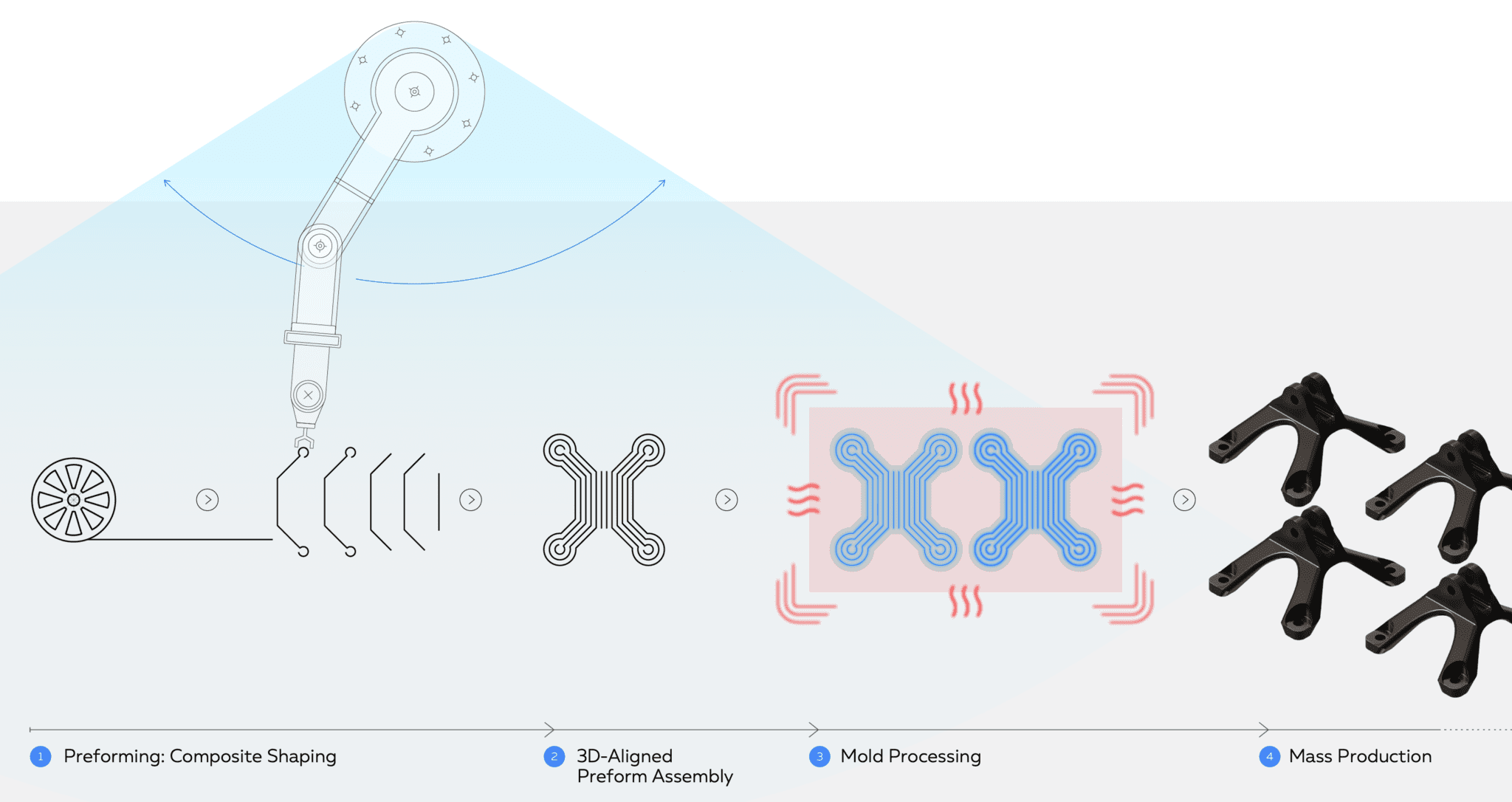
Direktes vs. indirektes ACM
Zurück zur LCC-Definition von ACM, die dritte Schlüsselkomponente würdigt die Debatte zwischen der Herstellung mit und ohne Formwerkzeug. „Direkt Bei Ansätzen entsteht die endgültige Form aus dem Druck – ich habe nie ein Werkzeug“, sagt Wettemann. „Der Vorteil ist die völlige Freiheit vom Werkzeugbau. Solange wir Formen haben, sprechen wir von indirekt Prozesse, oder wir sprechen von einer konventionelleren Herstellung von Verbundwerkstoffen, die dann durch AM-Technologien unterstützt wird.“
Wettemann stellt fest, dass solche hybriden Ansätze dazu beitragen, Faktoren wie Konsolidierung und Werkzeugausstattung zu adressieren, die die Kosten und den Zeitaufwand der traditionellen Verbundwerkstoffherstellung erhöhen. „Wir haben von 2015 bis 2017 Entwicklungen des Digital Manufacturing and Design Center der Singapore University of Technology und von Mikrosam [Prilep, Mazedonien] gesehen, bei denen automatisierte Roboter entwickelt wurden, um fortschrittliche Verbundteile in einem AFP-Prozess, aber ohne Werkzeug herzustellen“, er erklärt. „Dies geht also in Richtung ACM, in dem beide Ansätze in der digitalen Fertigung im freien Raum ohne Werkzeug erfolgreich waren, aber noch Weiterentwicklungen erforderlich sind. Die Reduzierung des Werkzeugbedarfs ist entscheidend, da uns dies auch neue Möglichkeiten sowohl für die Herstellung von Verbundkomponenten als auch für die Art der Komponenten eröffnet, die hergestellt werden können.“ Beispielsweise verfolgen die sehr organischen Lastpfade, die durch Topologieoptimierungs- und generative Designsoftware ausgegeben werden, zwar die Effizienz biologischer Strukturen wie Knochen und Bäume, sind jedoch mit Endlosfasern nur sehr schwer herzustellen.
Zukünftige Entwicklungen bei LCC
„Bei der direkten Teilefertigung sehen wir dasselbe, was Sie in Ihrer Landschaft zeigen, dass die Linien verschwimmen und wir zu einem viel hybrideren Fertigungsansatz übergehen“, sagt LCC-Forscher Patrick Consul (siehe „3D-Druck-CFK Formen für RTM-Flaperon, Exoskelette und mehr“). Anfang dieses Jahres hat sein Team erste Versuche mit einem hybriden Ansatz abgeschlossen, der Materialextrusion und gerichtete Energieabscheidung (DED) mit einer laserbasierten Prototypmaschine kombiniert, um auf vorverfestigten Laminaten und sehr großen 3D-Drucken ohne beheizte Kammer zu drucken. „Wir arbeiten auch daran, ACM mit Fräsen und AFP zu kombinieren, die wirklich gut passen, weil sie alle auf komplizierten Werkzeugwegen angewiesen sind“, sagt er. „Der Übergang zwischen ihnen wird ziemlich einfach und man braucht nicht viel zusätzliches Training.“ Dadurch wird die Prozesskette verkürzt, digitalisiert und vereinfacht.
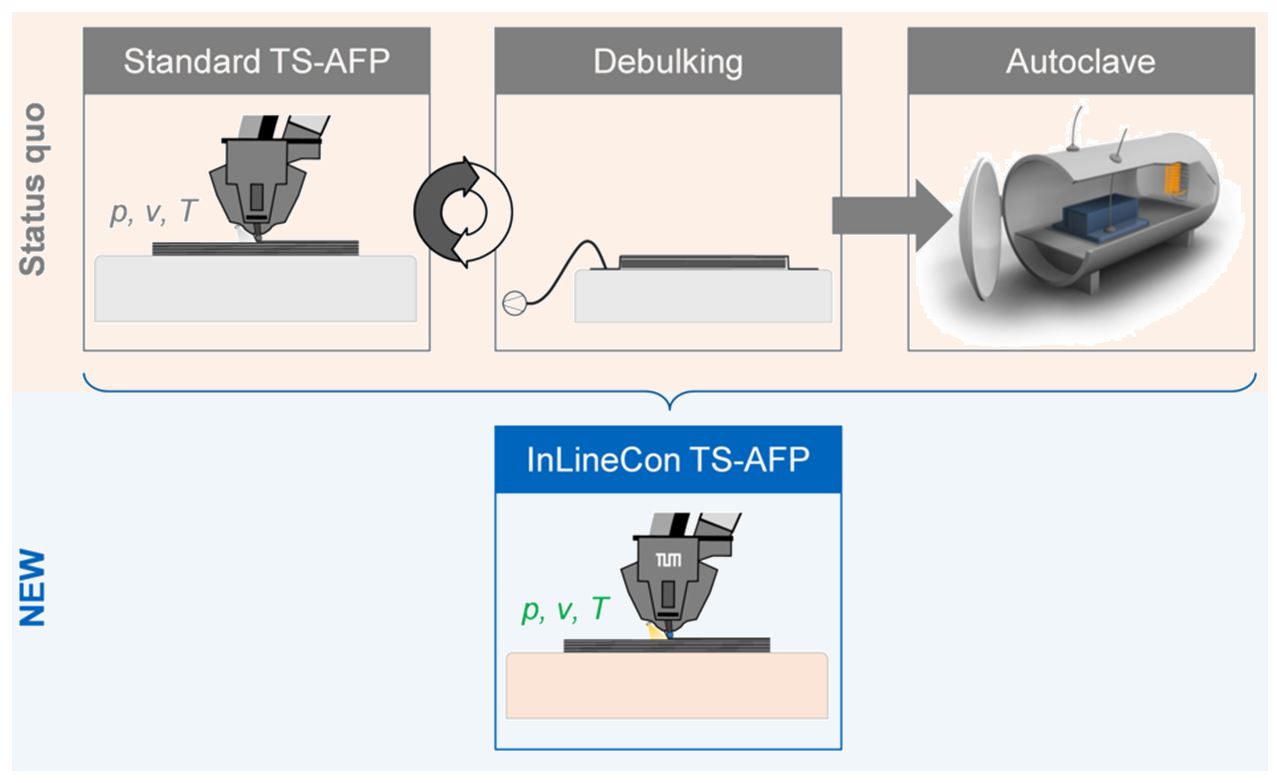
LCC treibt den hybriden Ansatz auch voran, indem es Technologien kombiniert, die für RTM und 3D-Druck entwickelt wurden. „Das Ergebnis ist ähnlich wie beim schnellen Aushärten, aber wir wollten weg von UV-härtenden Harzen, weil sie etwas zu teuer sind, wenn man größere Teile bauen möchte“, erklärt Zaremba. „Stattdessen verwenden wir eine neuartige Ultraschall-Mischtechnik, die wir für RTM entwickelt haben und passen sie nun für den Einsatz in einem typischen Extruder mit kostengünstigen, schnell aushärtenden Epoxiden an, die für die Automobilindustrie entwickelt wurden.“
Matschinski erklärt diese Technologie weiter:„Wir verwenden die Ultraschallvibration, um das Epoxidharz fast augenblicklich zu mischen und auszuhärten, während wir die imprägnierte Faser während des Druckens aufbringen.“ Inwiefern unterscheidet sich dies vom Ultraschall, der vom DLR-Institut für Verbundstrukturen und Adaptive Systeme in Braunschweig eingesetzt wird (siehe „Kostensenkung von Endlosfaser-3D-Druckmaterialien“)? Matschinski erklärt:„Das DLR nutzt die Ultraschallschwingung, um die Infiltration einer thermoplastischen Matrix in die gespreizten Fasern zu verbessern, um endlosfaserverstärkte 3D-Druckerfilamente zu erzeugen, die dann mit konventioneller Materialextrusion gedruckt werden. Wir verwenden Ultraschall zum Härten eines endlosfaserverstärkten duroplastischen Filaments.“
„Organisationen wie beispielsweise Arris Composites, 9T Labs und unsere Teams hier am LCC sind interessant, weil sie Wurzeln und Mitarbeiter sowohl aus der Composites-Welt als auch aus der AM-Welt haben“, sagt Wettemann. „Sie kommen zusammen, um neue Technologien zu entwickeln, die uns jetzt helfen können, uns von einer zukünftigen Wirtschaft zu entfernen, die potenziell ressourcen- und wachstumsbeschränkt ist und mit der Klimakrise zu kämpfen hat. Sie bieten einen Weg zu benötigten Lösungen.“
Harz
- 3D-Druck vs. Additive Fertigung:Was ist der Unterschied?
- Der Wert der additiven Fertigung in der Automobilindustrie
- Die Entwicklung der industriellen Instandhaltung
- Additive Fertigung tritt bei der AHO in die nächste Stufe ihrer Entwicklung ein
- Ist die Hybridfertigungstechnologie die Zukunft der additiven Fertigung?
- Die Entwicklung der Wartungspraxis
- SAMPE 2018-Keynote blickt in die Zukunft der Verbundwerkstoffe
- Die Entwicklung medizinischer Materialien
- Die Evolution medizinischer Geräte
- Die Entwicklung des 3D-Sehens