Verbundstoff-Abtriebswelle bereit für den Automobiltest
In vielen Fahrzeugen mit Allrad- und Allradantrieb sind Stahlantriebswellen segmentiert, um die erforderlichen Drehmoment- und Schwingungsleistungseigenschaften bereitzustellen. Im Gegensatz zu diesen segmentierten Gegenstücken aus Stahl kann eine einteilige Antriebswelle aus kohlenstofffaserverstärktem Polymer (CFK) die erforderliche Leistung erbringen, da sie den gesamten Weg vom Getriebe bis zum Differenzial überspannt, typischerweise zwischen 1.000 Millimeter (Pkw) und 3.000 Millimeter ( Nutzfahrzeuge). Eine einzige CFK-Antriebswelle kann daher nicht nur die Stahlantriebswelle ersetzen, sondern auch die Flansche und Zwischenlager, die die beiden Segmente verbinden. Als einheitliches Bauteil steigert die CFK-Antriebswelle die Leistung, trägt zu weniger Gewicht bei und hat sich in Hochleistungsfahrzeugen als kostengünstig erwiesen.
Aber ist CFK immer noch eine praktikable Option, wenn die Spannweite keine Rolle mehr spielt?
Dies ist bei den Abtriebswellen der Fall, die den kurzen Weg (typischerweise 250 bis 500 Millimeter) vom Antriebsstrang zu den Rädern verbinden. Bei der Untersuchung, ob CFK-Abtriebswellen in Serienfahrzeugen eingesetzt werden können, war das Designteam von Dynexa (Laudenbach, Deutschland) angenehm – und zugegeben – von den Ergebnissen überrascht.
Dynexa, ein Unternehmen der Avanco Group (Herford, Deutschland) für Filamentwickel- und Antriebstechnik, hat im Rahmen einer Vorentwicklungsstudie mit einem deutschen OEM die Konstruktion und Demonstration einer CFK-Abtriebswelle durchgeführt. Im Jahr 2014 begann Dynexa damit, den OEM mit CFK-Antriebswellen zu beliefern, die im Vergleich zu einer segmentierten Stahlwelle und Zwischenlagern eine Gewichtsreduzierung von 40 % erreichten. Die damit einhergehende Reduzierung der rotierenden Masse verbesserte auch das Fahrverhalten des Fahrzeugs.
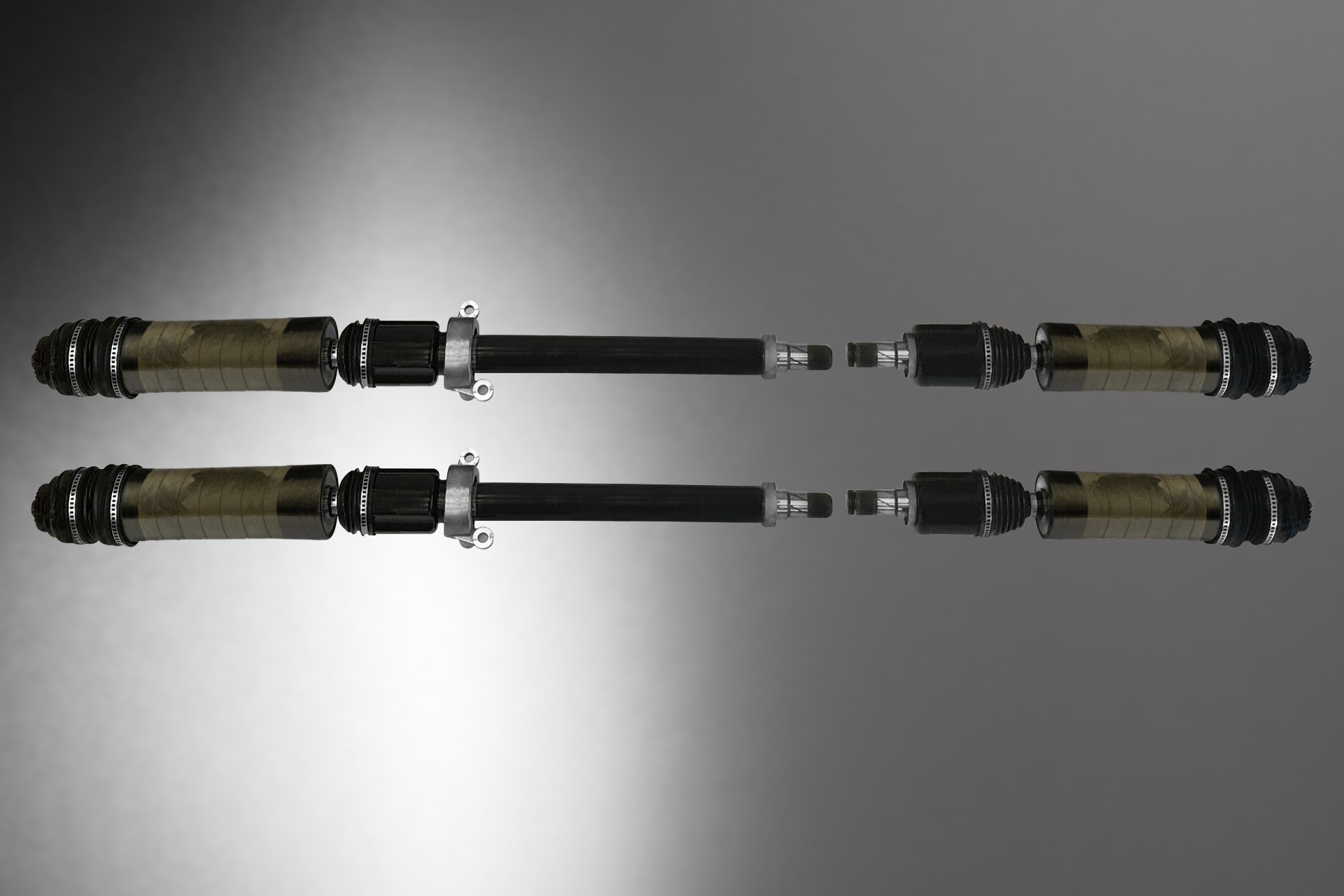
Seit 2006 hat Dynexa mehr als 100.000 CFK-Rohre und -Wellen für Automobil-Prototypen- und Serienanwendungen fadengewickelt. Das Unternehmen verwendet typischerweise eine Epoxidmatrix, die von Huntsman (The Woodlands, Texas, USA) oder Hexion (Columbus, Ohio, USA) geliefert wird. Dynexa arbeitet mit vielen großen Kohlefaserlieferanten zusammen, darunter Teijin (Chiyoda-ku, Japan), Toray (Tokio, Japan), SGL (Wiesbaden, Deutschland), Mitsubishi (Tokio, Japan) und Nippon Graphite Fiber Corp. (Himeji, Japan .) ). (Fasern für jede Anwendung werden entsprechend den Produkt- und Produktionsanforderungen ausgewählt, um die Materialeigenschaften optimal zu nutzen.) Trotz dieser Historie und Erfahrung hegte das Dynexa-Team zunächst Zweifel am Einsatz von CFK für Abtriebswellen.
Vom Zweifel zur Demo
Eine Vollmetall-Abtriebswelle ist heute in Serienfahrzeugen die Regel, und zunächst war sich das Dynexa-Team unsicher, welchen Wert eine CFK-Alternative haben könnte. „Im Gegensatz zu mehrteiligen Metallantriebswellen würden wir hier keine hohen Gewichtseinsparungen erzielen“, sagt Matthias Bruckhoff, Vertriebs- und Marketingleiter von Dynexa.
Warum auf CFK-Abtriebswellen umsteigen? Die hohe Leistungsfähigkeit von CFK könnte potenziell nützlich sein in Elektrofahrzeugen, bei denen die Abtriebswellen ungewöhnlich hohen Kräften ausgesetzt sind. Darüber hinaus kann sich die CFK-Abtriebswelle aufgrund eines bei allen Arten von Kraftfahrzeugantriebssträngen üblichen Phänomens sowohl bei Elektro- als auch bei Gasfahrzeugen als nützlich erweisen. Das als „Power Hop“ bezeichnete Phänomen tritt auf, wenn reibungsarme Fahrbahnoberflächen dazu führen, dass die Reifen von Fahrzeugen mit Frontantrieb bei hoher Motorbeschleunigung zyklisch die Haftung auf der Fahrbahn verlieren. „Der Fahrer hört ein lautes, zyklisches Rattern der Vorderachse und spürt ein starkes Vibrieren an Sitz und Lenkrad“, erklärt Linda Senger, BMW Forschung Hybridantrieb, Mechanik und Struktur. Das Auftreten von Kraftsprüngen hängt stark von der Ausgangswelle und ihrer Torsionssteifigkeit ab.
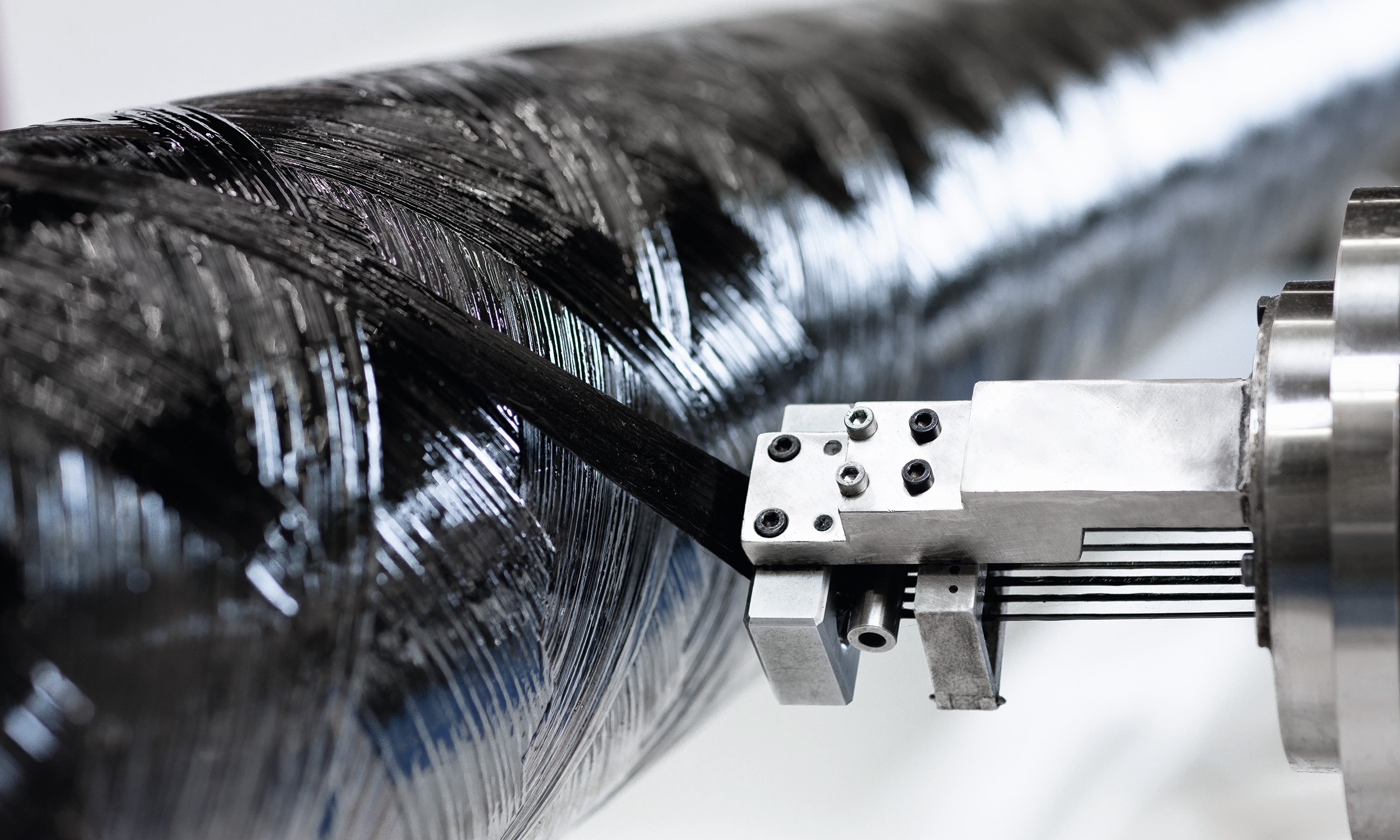
Anwendung zum Aufwickeln von Filamenten. Nachdem Dynexa mehr als 100.000 CFK-Rohre und -Wellen für Prototypen- und Serienanwendungen in der Automobilindustrie filamentgewickelt hat, hat Dynexa diese Erfahrung auf die neuen Herausforderungen der Abtriebswellenanwendung übertragen. Von besonderem Interesse sind das Schwingungsverhalten und die Torsionssteifigkeit der Wellen. Quelle | Dynexa
„Im Fokus der Entwicklung stand der Einfluss einer höheren Torsionsdämpfung bei CFK-Abtriebswellen im Vergleich zu Stahlwellen bei gleicher Torsionssteifigkeit auf den Kraftsprung“, so Senger weiter. CFK-Wellen weisen eine fünf- bis zehnfache Torsionsdämpfung gegenüber Stahlwellen auf. Dieses Dämpfungsverhalten ist an die Anforderungen der Anwendung anpassbar.“
Im Allgemeinen versuchen Automobildesigner, die Schwingungseigenschaften von Fahrzeugkomponenten zu modifizieren, um Geräusche, Schwingungen und Rauhigkeit (NVH) zu minimieren. „Wenn Sie Gas geben“, erklärt Marcus Schwarz, Leiter der Produktentwicklung bei Dynexa, „erhöhen die Kräfte und Vibrationen im System, was zu NVH führt.“ Das Team von Dynexa hat Erfahrung in der Optimierung der Schwingungseigenschaften von CFK-Komponenten. „Durch die Gestaltung der Faserverbundstruktur und die Anpassung des Schichtaufbaus kann eine gewünschte Frequenz erreicht werden, um die Dynamik des Teils während des Laufs zu beeinflussen“, sagt Schwarz.
Die unterschiedlichen Schwingungseigenschaften von CFK und Stahl stehen im Mittelpunkt der Abtriebswellenstudie von Senger. Um zu testen, ob die CFK-Vibrationsdämpfung dazu beitragen würde, die Intensität der Kraftsprünge zu reduzieren, stellte Senger Dynexa eine Reihe von Konstruktionsparametern für die CFK-Abtriebswelle zur Verfügung. Da der Test an einer bestehenden Baugruppe für ein Gasfahrzeug inklusive Getriebeanbindung und Gelenken durchgeführt werden sollte, musste die CFK-Welle als direkter Ersatz für die Metallwelle ausgelegt werden.
Dynexa hat die CFK-Welle so konstruiert, dass sie der Fähigkeit der Metallwelle entspricht, eine statische Torsionsbelastung von bis zu 3.000 Newtonmetern zu bewältigen. Wichtig war, dass die CFK-Welle auch der geringen Torsionssteifigkeit der Metallwelle von 225 Newtonmeter pro Grad gerecht werden musste. „Die geringe Steifigkeit der Abtriebswellen bei gasbetriebenen Fahrzeugen ist wegen der Drehungleichförmigkeit der Kurbelwelle notwendig“, erklärt Senger. „Drehschwingungen verursachen eine Schwingung des Antriebsstrangs und aller angrenzenden Komponenten; Mit einer geringen Steifigkeit können Sie sowohl Vibrationen als auch Geräusche reduzieren.“
Eine Konstruktionsoptimierung mit den Parametern, die Sengers Team vorgab, führte zu einer 350 Millimeter langen Abtriebswelle mit 80 Millimeter Durchmesser. Die massive Stahlwelle hat einen kleineren Durchmesser als die hohle CFK-Rohrwelle, dennoch ist genügend Platz für die Aufnahme der größeren CFK-Welle vorhanden.
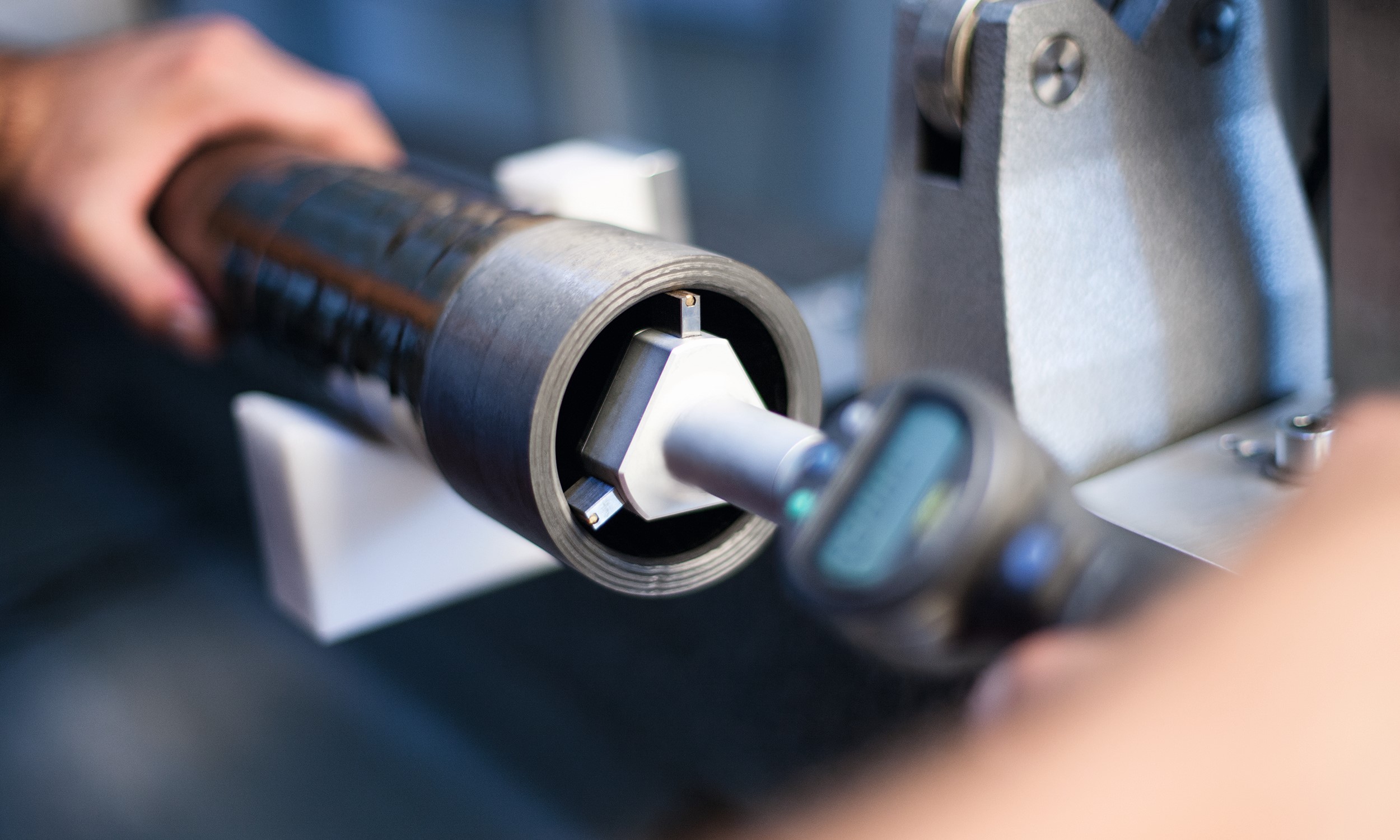
Entscheidend für das Wellendesign ist auch, wie es mit anderen – normalerweise metallischen – Komponenten im Antriebsstrang verbunden ist. „Man muss wissen, welche Kräfte zu berücksichtigen sind, wie man die Welle konstruiert, wie man das Metall vorbereitet und wie man es zusammenbaut“, sagt Schwarz. Eine Abtriebswelle aus Metall überträgt das Drehmoment über eine Schweißverbindung zwischen der Welle und anderen Metallkomponenten. Beim CFK-Schaft hingegen erfolgt die Verbindung über eine Press-Fit-Verbindung, bei der ein Metallteil in das CFK-Rohr eingesetzt wird. Der Außendurchmesser des Metallteils ist etwas größer als der Innendurchmesser des CFK-Rohrs, wodurch der für die Drehmomentübertragung erforderliche Fügedruck entsteht. Es wird kein Kleber verwendet. Dynexa unterstützt seine CFK-Metall-Verbindung mit äußeren CFK-Stützringen und einem inneren, speziell entwickelten Einpressverbinder. Letzteres, eine über 20 Jahre bewährte Dynexa-Technologie, erklärt Schwarz, dass die Drehmomentübertragung durch eine Kombination aus der durch den Gelenkdruck erzeugten Reibung und dem Formschluss durch Mikrozähne (Verzahnung) am Metallteil gewährleistet wird. Durch eine Spaltdichtung zwischen CFK-Rohr und Metallteil wird galvanische Korrosion minimiert. Die Einpresstechnologie von Dynexa „kombiniert Leichtbau mit hoher Torsionsleistung, sowohl unter statischer Belastung als auch über lange Zeiträume unter Ermüdungsbelastung“, sagt Bruckhoff.
Im Vergleich zur Stahl-Abtriebswelle ist die CFK-Version 20 bis 30 % leichter. Zu den Gewichtseinsparungen zählen sowohl die leichtere Welle (trotz des zusätzlichen Gewichts der äußeren Stützringe, die nicht Teil der Metall-Metall-Verbindung sind) als auch der Wegfall der bei der Metallausführung erforderlichen Schwingungsdämpfer. Obwohl die tatsächliche Gewichtseinsparung bei gasbetriebenen Fahrzeugen keinen signifikanten Wert hat, könnte sie bei Elektrofahrzeugen hilfreich sein, die selbst bei geringen Gewichtseinsparungen eine größere Reichweite erzielen können.
Potenziellen Wert erkennen
Der Test der CFK-Welle mit geringer Torsionssteifigkeit hat gezeigt, wie wichtig die Torsionssteifigkeit für die Power-Hop-Reduktion ist. Entsprechend der geringeren Torsionssteifigkeit der Stahlwelle verbesserte der Prototyp der CFK-Abtriebswelle die Power-Hop-Leistung nicht, berichtet Senger. „Fahrversuche zeigen, dass der Powerhop des Fahrzeugs bei den CFK-Wellen die gleiche Intensität hat wie beim Einbau der Stahlwellen.“
Die Studie legt nahe, dass bei Gasfahrzeugen, die eine geringere Torsionssteifigkeit in der Abtriebswelle benötigen, eine erfolgreiche Reduzierung des Kraftsprungs Änderungen an der Rohrgeometrie erfordern würde. „Um einen weiteren Mehrwert zu erzielen, ist der Einsatz eines längeren CFK-Rohrs notwendig“, so Bruckhoff abschließend. „Die Reduzierung des Außendurchmessers ist auch für den Einstieg in Großserienfahrzeuge mit Composite-Standardbauteilen wünschenswert.“
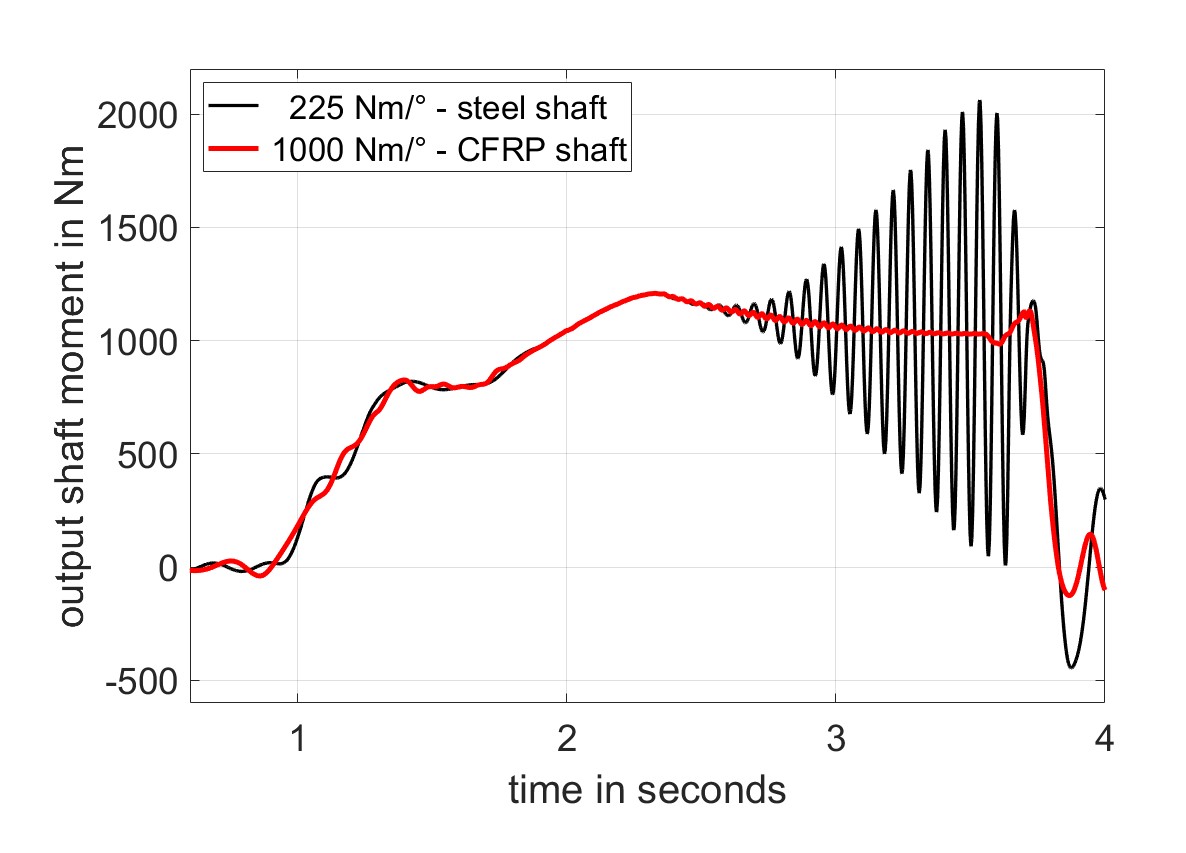
Die Torsionssteifigkeit macht den Unterschied. Eine Simulation mit Matlab Simulink legt nahe, dass eine CFK-Abtriebswelle mit hoher Torsionssteifigkeit das Power-Hop-Phänomen eliminieren kann. Das simulierte Fahrmanöver ist die Beschleunigung eines frontgetriebenen, gasbetriebenen Fahrzeugs aus dem Stand auf nasser und ebener Fahrbahn. Obwohl gasbetriebene Fahrzeuge bei anderen Fahrleistungsproblemen durch eine geringere Torsionssteifigkeit besser bedient werden könnten, sind elektrisch betriebene Fahrzeuge starke Kandidaten für die Weiterentwicklung der CFK-Abtriebswelle. Quelle | Linda Senger
Bei Elektroautos sieht Senger jedoch den Schlüssel zum Erfolg von CFK-Abtriebswellen in der hohen Torsionssteifigkeit, die CFK bieten kann. „Eine hohe Steifigkeit sorgt für ein direkteres Ansprechverhalten des Fahrzeugs und verbessert damit die Fahrdynamik“, sagt sie. Elektrifizierte Antriebsstränge können Wellen mit hoher Torsionssteifigkeit verwenden, da sie nicht die gleiche Ungleichförmigkeit der Kurbelwelle erfahren, die in gasbetriebenen Fahrzeugen zu finden ist. Es sind der Verbrennungsprozess des Gasmotors und die resultierenden Kräfte auf die Kurbelwelle, die die Ungleichförmigkeit erzeugen, und elektrische Energie erzeugt diese Kräfte nicht.
Eine steifere Abtriebswelle erhöht die Torsionseigenfrequenz des Antriebsstrangs (die Frequenz, bei der eine Betriebsschwingung die Komponente zum Mitschwingen bringt und diese Schwingung verstärkt). „Der Schwingungsmodus einer Welle mit hoher Torsionssteifigkeit belastet alle Komponenten, die durch das Power-Hop-Phänomen angeregt werden, deutlich weniger“, betont Senger. Eine Simulation hat gezeigt, dass eine CFK-Abtriebswelle mit hoher Torsionssteifigkeit unter den gleichen Fahrbedingungen die Kraftsprünge einer Metallwelle mit geringer Torsionssteifigkeit eliminiert.
Vorwärts gehen
Rückblickend auf die bisherige Abtriebswellenarbeit sagt Bruckhoff:„Die Produktgruppe CFK-Abtriebswelle schafft neue Mehrwerte in puncto Fahreigenschaften und Komfort. Gemeinsam mit unseren Partnern werden wir diese Vorteile herausarbeiten und ein anforderungs- und preisoptimiertes Produkt realisieren.“
Weitere Studien zu möglichen CFK-Abtriebswellenanwendungen wurden vom OEM noch nicht angekündigt, erscheinen aber wahrscheinlich. Für das Dynexa-Team hat dieses Vorentwicklungsprojekt neue Einblicke in CFK-Anwendungen gebracht; Insbesondere Fahrzeugtests validieren theoretische Annahmen und verbessern kontinuierlich die Designkompetenz. „Wichtig ist, dass wir am Ball bleiben und diese Produktgruppe gemeinsam mit unseren OEM-Partnern weiterentwickeln“, betont Bruckhoff. „Unser Ziel ist es, erfolgreiche Entwicklungen Schritt für Schritt in eine Serienanwendung zu überführen.“
Harz
- Ist meine Fabrik bereit für einen Roboter?
- Glasgefülltes PET für Automobilaußenteile
- Materialien:Glas- und kohlenstofffaserverstärktes PP für die Automobilindustrie
- PIR-Content-TPEs für den Automobilaußenbereich
- TPE mit recyceltem Inhalt für die Fahrzeuginnenausstattung
- Zähe, hitzestabilisierte PPA-Compounds für anspruchsvolle Automobilanwendungen
- Impossible Objects arbeitet mit BASF für den 3D-Verbunddruck zusammen
- Thermoplastische Tür eine Premiere für Automobilverbundwerkstoffe
- Techsil bringt durchsichtigen Epoxidklebstoff für Verbundsubstrate auf den Markt
- Rhodes Interform fertigt Verbundpresse für AMRC