Entwicklung der additiven Fertigung zur Nutzung der Anisotropie
Anisoprint (Esch-sur-Alzette, Luxemburg) wurde 2014 von CEO Fedor Antonov gegründet und ist eines von einer wachsenden Zahl von Technologieunternehmen, die den 3D-Druck von Verbundwerkstoffen mit Endlosfasern vorantreiben . Es zieht es jedoch vor, als Vorreiter bei der Abkehr von der additiven Fertigung (AM) von Metallen bekannt zu sein zu Verbundwerkstoffen.
„Die gerichteten Eigenschaften von Verbundwerkstoffen sind ein Vorteil, kein Nachteil“, sagt Antonov. „Unidirektionale Kohlefaserverbundstoffe sind stärker und leichter als Metalle. Konventionelle Fertigung und metallbasierte AM betrachten die gerichtete Anisotropie von Verbundwerkstoffen als einen Nachteil, der abgeschwächt werden muss. Aber der Ansatz von Anisoprint nutzt diese Anisotropie, indem er die Fasern so ausrichtet und platziert, dass sie die strukturellen Belastungen präzise erfüllen, wodurch das Teilegewicht erheblich reduziert wird und gleichzeitig eine hohe Festigkeit und Steifigkeit beibehalten wird.“
Effizientere Verbundwerkstoffe ermöglichen
Antonov weist darauf hin, dass bei der konventionellen Herstellung von Verbundwerkstoffen typischerweise Verfahren aus der Metallindustrie verwendet wurden, darunter quasi-isotrope Laminate, Bohrlöcher und mechanische Befestigungselemente. „Diese annullieren die Gewichts- und Leistungsvorteile von Verbundwerkstoffen“, sagt Antonov. „Die Anisodrucktechnologie bietet eine viel schnellere und flexiblere, automatisierte Methode für die Produktion.“ Es bietet auch eine Möglichkeit, die effizienteren Strukturen zu erreichen, die jetzt durch Topologieoptimierung und generatives Design ausgegeben werden Software.
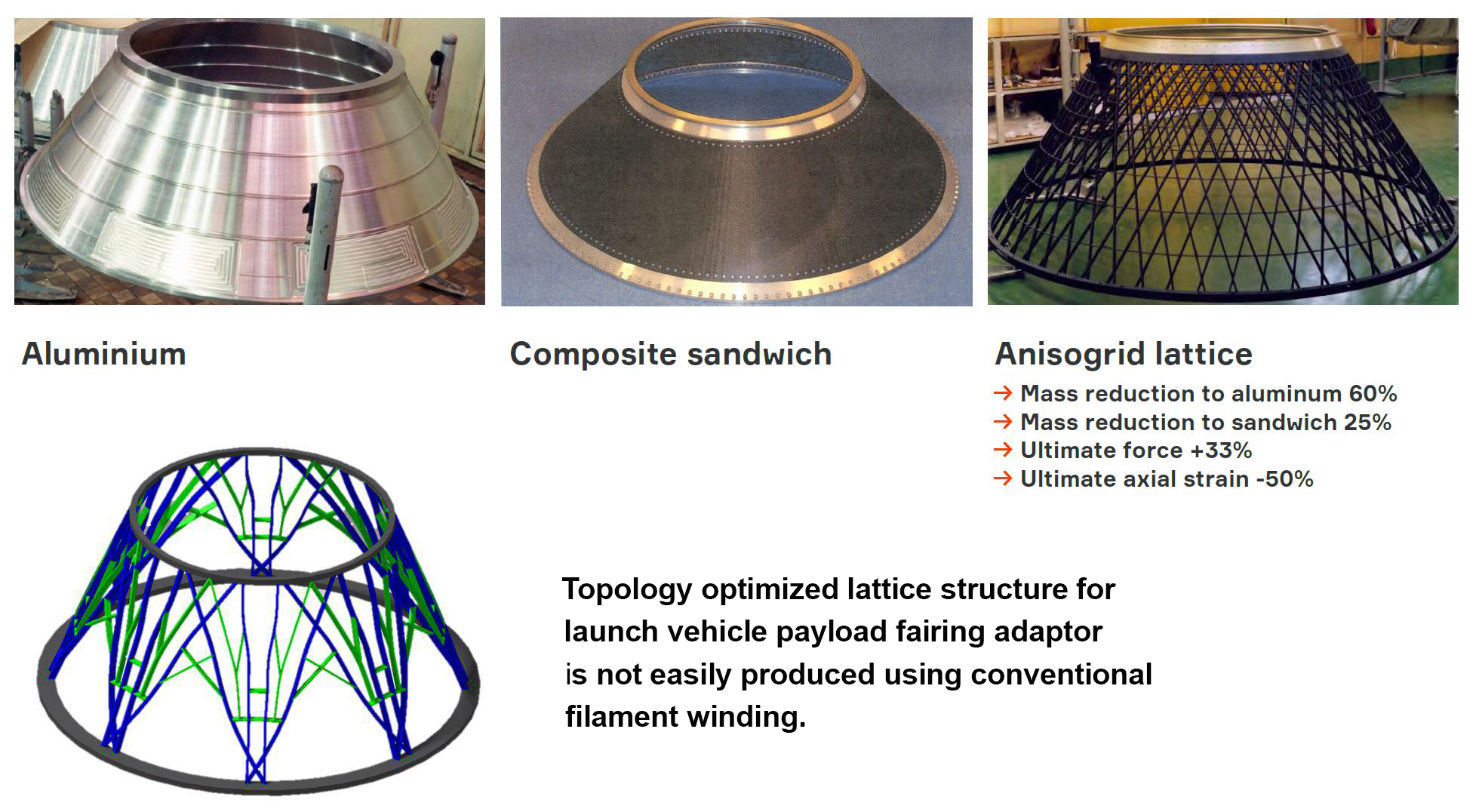
„Die effizientesten Strukturen der Natur, wie Bäume und Knochen, nutzen Richtungseigenschaften, indem sie lasttragendes Material hauptsächlich entlang von Lastpfaden ausrichten“, stellt Antonov fest. Diese Typen von topologieoptimierten Strukturen sind jedoch schwierig herzustellen. Zum Beispiel werden Gitterstrukturen, die starke und leichte Nutzlast-Verkleidungsadapter für Raumfahrzeuge ermöglicht haben, typischerweise unter Verwendung von Filamentwickeln hergestellt. Eine topologieoptimierte Version , was eine zusätzliche Gewichtseinsparung von 30 % bietet , ist weder mit herkömmlichen Verbundprozessen noch mit neueren automatisierten Faserplatzierungen (AFP) einfach herzustellen.
„Herkömmliche gewickelte Anisogrid-Filamentstrukturen werden durch Rillen in den Werkzeugen erreicht, und ein relativ geringer Faservolumenanteil in den Rippen ermöglicht es, sie zu kreuzen“, sagt Antonov. „Diese Art von Anisogrid-Strukturen waren unser ursprüngliches Ziel. Dies funktioniert mit AFP jedoch nicht, da Ihr Faservolumengehalt immer konstant ist und sich kreuzende Rippen ohne Schneiden der Fasern oder lokale Dickenschwankungen nicht möglich sind.“
(Hinweis:Weitere Studien dazu finden Sie unter https://www.researchgate.net/publication/321081593_Anisogrid_Payload_Adaptor_Structure_for_Vega_Launcher)
Faserlenkung
Fiber Steering ist eine Technik, die derzeit in der Verbundstoffproduktion unter Verwendung von AFP angewendet wird und die es ermöglicht, Fasern in krummlinigen Pfaden aufzubringen – AFP verwendet traditionell gerade lineare Pfade. Die Faserlenkung ermöglicht die Optimierung des Faserverlaufs und damit des mechanischen Ansprechverhaltens der Verbundplatte, um eine höhere Leistung als bei herkömmlichen Laminaten zu erzielen. In einem Beispiel erzeugt dieser Ansatz ein Verbundsubstratpaneel für ein Solararray eines Weltraumfahrzeugs, das eine um 44% höhere erste Eigenfrequenz hat (minimiert die Amplitude von Vibrationen und ermöglicht eine schnellere Dämpfung) als ein äquivalentes konventionelles Paneel mit geraden Faserpfaden und der gleichen Masse. Alternativ könnte ein Panel mit geringerem Gewicht bei gleicher Frequenzleistung erreicht werden.
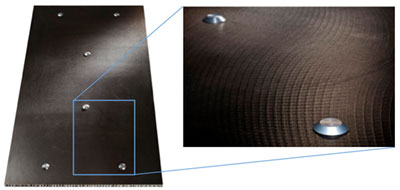
Fiber Steering ermöglicht die Konstruktion und Herstellung von Teilen wie Strukturblechen für Satelliten oder Hochgeschwindigkeits-Maschinenkomponenten mit sehr hoher Leistung. Es ist ein wiederholbarer Prozess, der eine hohe und gleichbleibende Qualität erreicht und innovative neue Designs ermöglicht. Es kann auch zur Gewichtsreduzierung bei gleichem geometrischem Design verwendet werden. QUELLE | „Fibre-Steering technology for Advanced Composite Panels“ (der ursprüngliche Link ist hier angegeben, aber nicht mehr über den esa-tec-Server verfügbar:http://www.esa-tec.eu/space-technologies/from-space/fibre-steering -technology-for-advanced-composite-panels/)
„Anisoprinting ist eine Kombination aus Gitterstrukturen und Faserlenkung, die verwendet wird, um topologieoptimierte Teile zu erhalten“, sagt Antonov. „Dies ist eine Schlüsseltechnologie für gedruckte Verbundwerkstoffe. Wie baut man beispielsweise eine Rumpfplatte für ein Verkehrsflugzeug mit Ausschnitten oder Löchern?
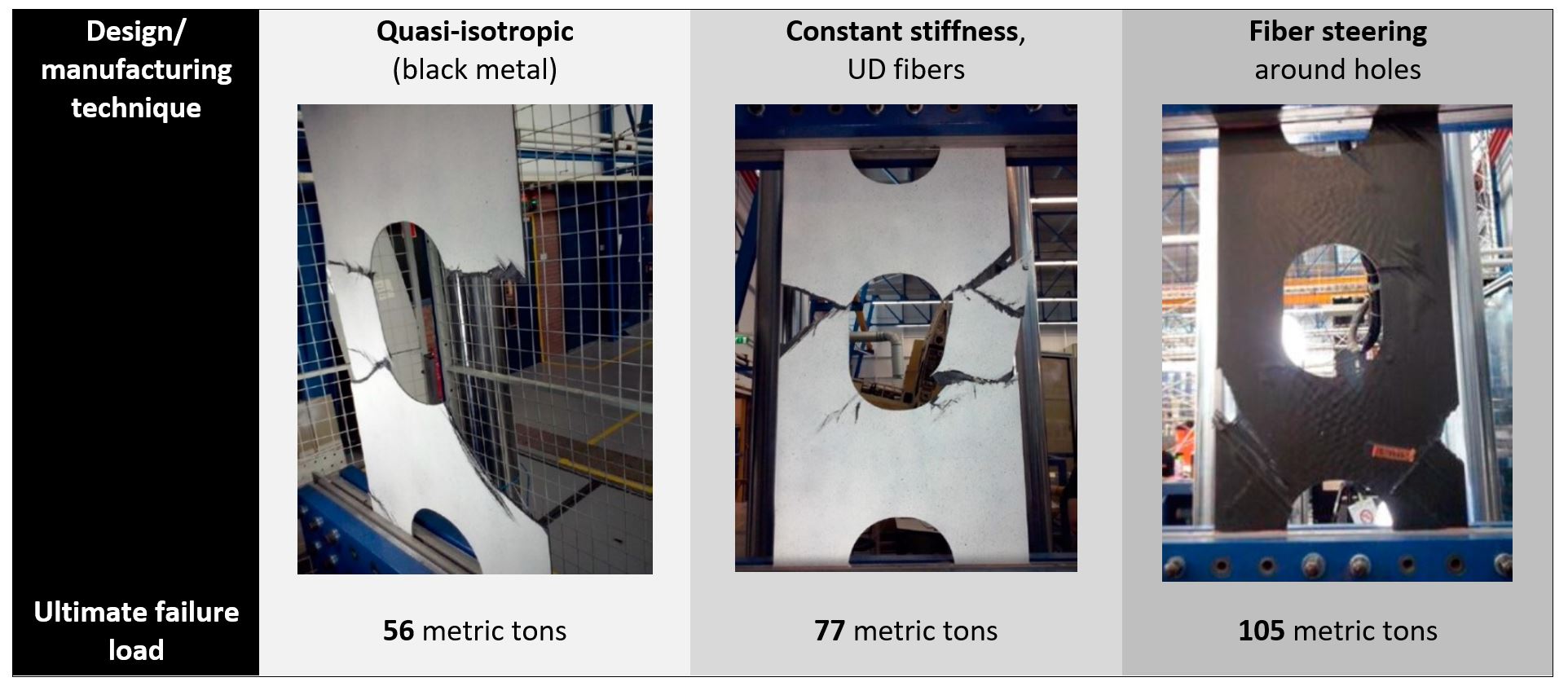
Er gibt drei verschiedene Techniken an, die verwendet werden, um zusammengesetzte Proben gleicher Dicke und gleichem Gewicht herzustellen, jede mit CNC-gefrästen Löchern (siehe Tabelle unten). Er stellt fest, dass die mit Faserlenkung hergestellte Probe bei Kompressionstests eine doppelt so hohe Druckbelastung wie ein quasi-isotroper Verbundwerkstoff („schwarzes Aluminium“) und 30 % mehr als ein UD-Laminat mit konstanter Steifigkeit aufweist. „Daher ist Fiber Steering ein mächtiges Werkzeug“, sagt Antonov. „Anisoprinting wird sich in Richtung AFP-Faserlenkung bewegen, da wir das Faservolumen und die Produktivität erhöhen, und AFP wird mit mehr Flexibilität auf uns zustreben.
Die „Flexibilität“, auf die sich Anotov bezieht, ist ein Maß dafür, wie weit es möglich ist, eine Faser entlang eines beliebigen Pfades im dreidimensionalen Raum zu platzieren. Arevo, ein weiteres Unternehmen, das den Endlosfaser-3D-Druck vermarktet, behauptet, diese Art von Flexibilität zu haben. „Die Technologie von Arevo unterscheidet sich nicht wesentlich von AFP-Unternehmen wie Coriolis, Automated Dynamics, Electroimpact usw.“, sagt Antonov. „Sie haben es lediglich miniaturisiert und verwenden statt eines dünnen und breiten Bands ein dickes und schmales mit einem Laser-AFP-Kopf. Es ist alles das Gleiche." Beachten Sie, dass die 3D-Drucktechnologie von Arevo von Anfang an roboterbasiert war. Wie wird sich die Technologie von Anisoprint beim Übergang zu Roboterplattformen verändern?
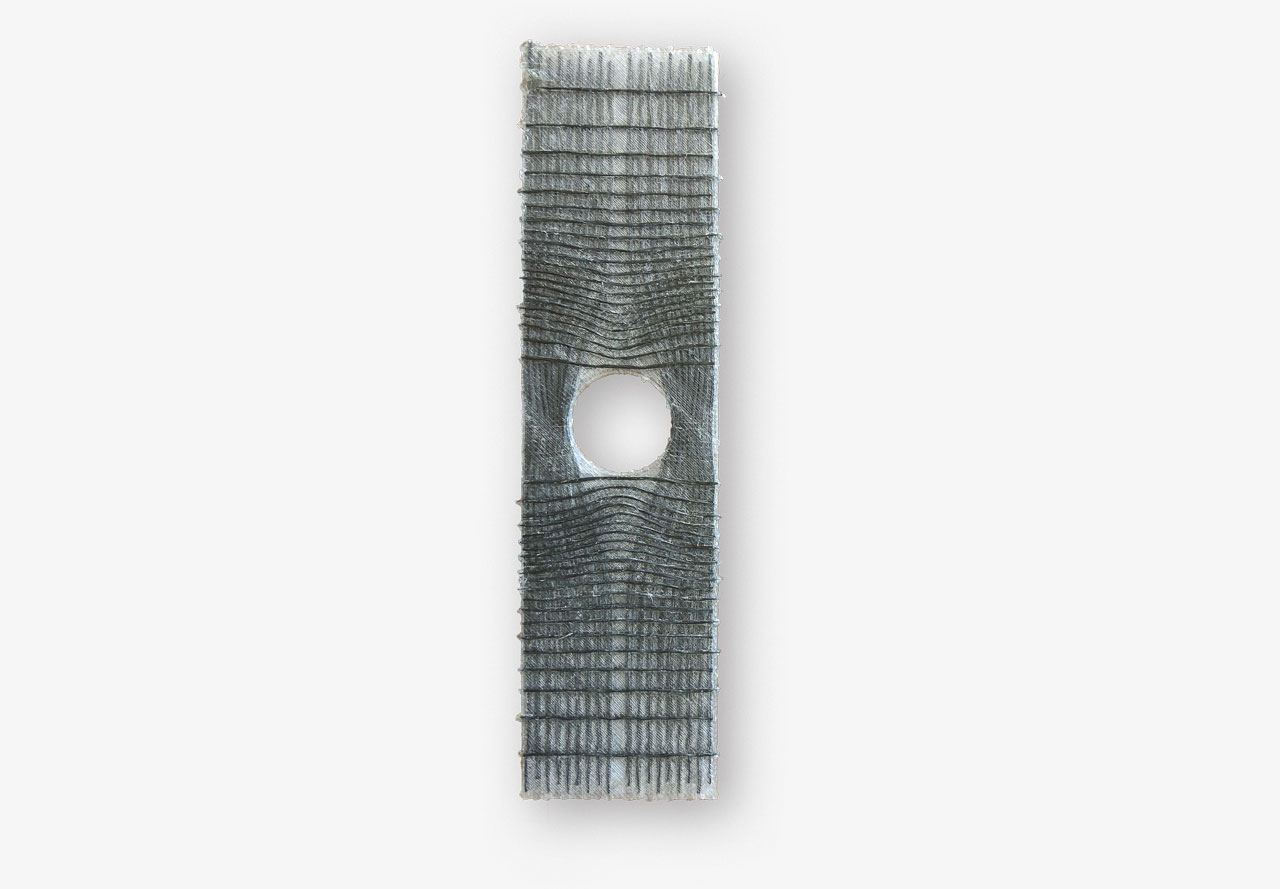
Beispiel für ein 3D-gedrucktes Verbundmuster mit Anisoprint unter Verwendung von Faserlenkung.
Anisoprints Geschichte und TS-TP-Ansatz
Antonov und seine Mitbegründer (Andrey Azarov, Alexey Khaziev, Mikhail Golubev und Zafer Gürdal) waren an einer neuen Universität im Westen Moskaus namens Skolkovo Institute of Science and Technology (Skoltech), die 2011 gegründet wurde. Antonov arbeitete am Bau des neuen Zentrums für Verbundwerkstofftechnologie von Skoltech und begann mit der Entwicklung des 3D-Drucks. Der damalige Leiter des Composites Centers war Zafer Gürdal, der 2015 das Zentrum verließ und an das McNair Center der University of South Carolina zurückkehrte. Letzteres ist heute für seine Forschung und Entwicklung in den Bereichen Verbundwerkstoffe und Endlosfaser-3D-Druck bekannt.
„Wir haben uns entschieden, von Skoltech abzuspalten, als Zafer Gürdal gegangen ist“, erklärt Antonov. „Bis Sommer 2015 hatten wir einen Prototyp eines CFC-Druckkopfs entwickelt. Unser nächstes Ziel war die Entwicklung eines Desktop-Druckers.“
Anisoprint stellte 2017 seinen Composer-Desktopdrucker vor. Ähnlich wie bei den Endlosfaserdruckern von Markforged verwendet der Composer von Anisoprint zwei Druckdüsen:eine für die Endlosfaserverstärkung und eine für die Kunststoffmatrix. Das in einer Glasdruckkammer untergebrachte Glasdruckbett von Composer kann auf bis zu 120 °C erhitzt werden, wodurch Schrumpfungseffekte minimiert werden. Derzeit ist es in zwei Größen erhältlich:
- A3 (420 x 297 x 210 Millimeter)
- A4 (297 x 210 x 147 mm)
Bei einem Standard-Düsendurchmesser von 0,4 Millimetern wird die Druckgeschwindigkeit des Composer mit 10-80 Millimeter/Sekunde unverstärkt und 1-20 Millimeter/Sekunde mit Endlosfaserverstärkung angegeben. Anisoprint kann viele Kunststoffe extrudieren, darunter PLA, PETG, ABS, Nylon und PC. Es kann diese mit seinen Composite Carbon Fiber (CCF) Materialien verstärken und hat kürzlich ein Composite Basalt Fiber (CBF) Druckmaterial auf den Markt gebracht.
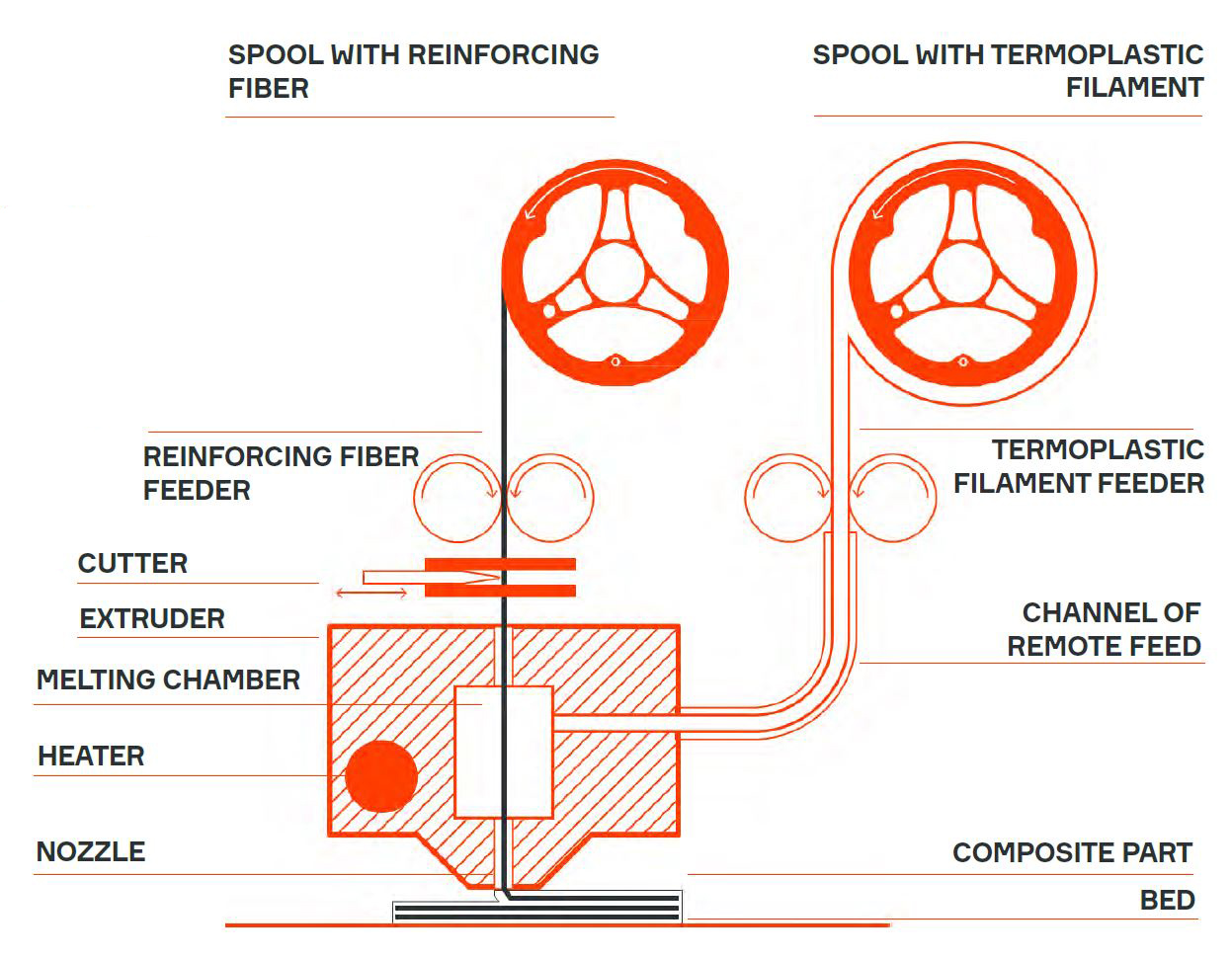
Anisoprint unterscheidet sich jedoch erheblich von anderen Endlosfaser-3D-Drucktechnologien, da es imprägniert zunächst Endlosfaserverstärkungen mit einem Duroplast Polymer und extrudiert dieses dann während des Druckens in das geschmolzene thermoplastische Filament. „Dieser Zwei-Matrix-Ansatz gewährleistet eine geringe Porosität, eine gute Haftung der Faser an dem Polymer und ausgezeichnete mechanische Eigenschaften.“ Antonov behauptet.
Er fährt fort:„Der Erfinder des filamentgewickelten Anisogitters für den Nutzlastadapter der Proton-M-Trägerrakete, V.V. Vasiliev, der in unserem Beirat ist, hat tatsächlich gezeigt, dass diese Idee der Verwendung von Dual-Matrix- Duroplast-Thermoplasten (TS-TP)-Materialien haben Vorteile gegenüber der Verwendung einer einzelnen Duroplast- oder Thermoplastmatrix. Duroplastische Matrixmaterialien haben Probleme mit der Sprödigkeit, so dass die Matrix viel früher zu reißen beginnt, als die Faser versagt. Vasiliev hat bewiesen, dass er dies mit dem Dual-Matrix-Ansatz mildern kann.“
Der Duroplast, den Anisoprint verwendet, ist ein Mehrkomponenten-Epoxid und fertig gedruckte Laminate haben einen Fasergehalt von bis zu 45%, wie von der Technischen Universität München (TUM) getestet.
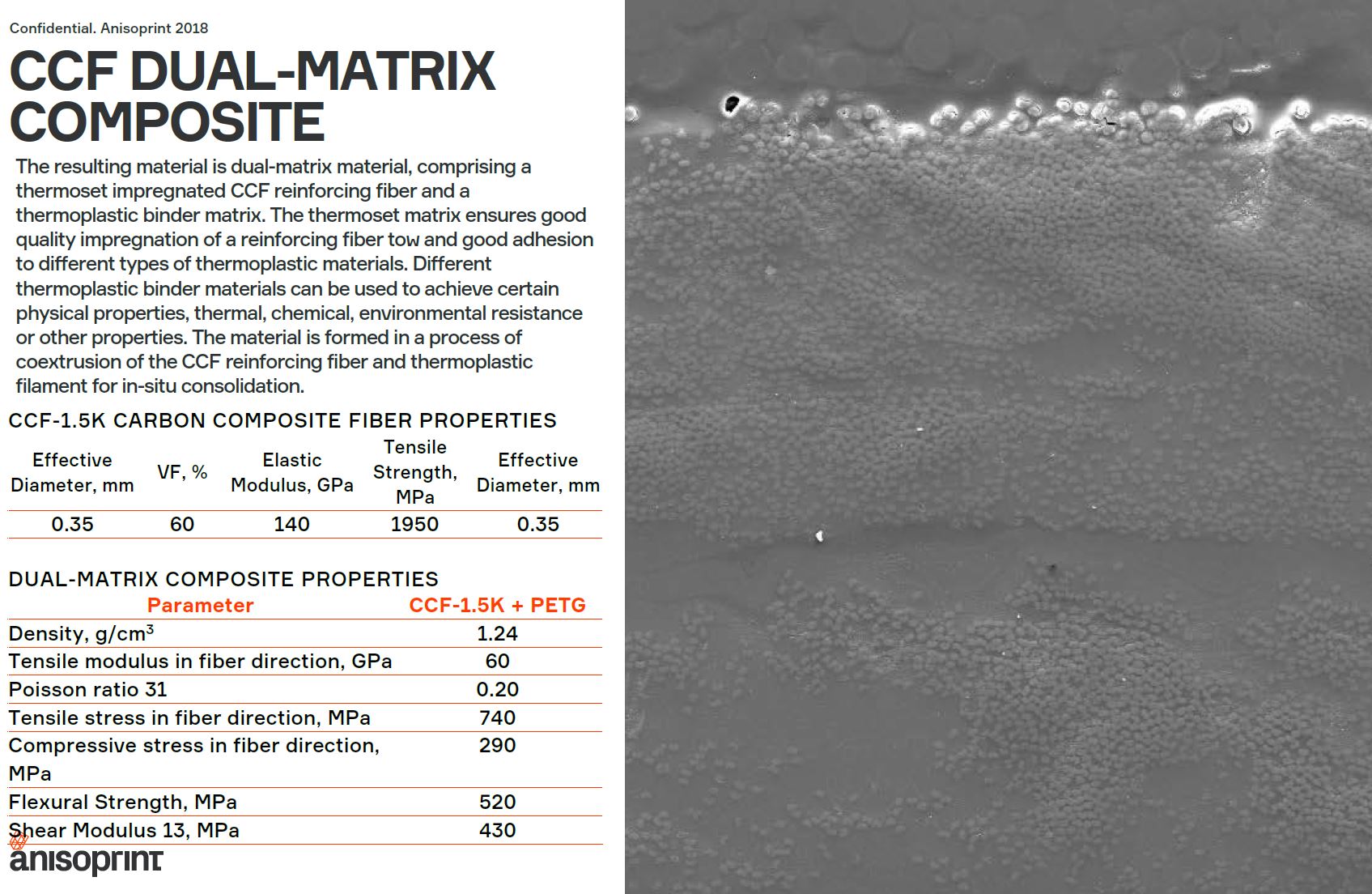
Zu den patentierten Angeboten von Anisoprint gehören:
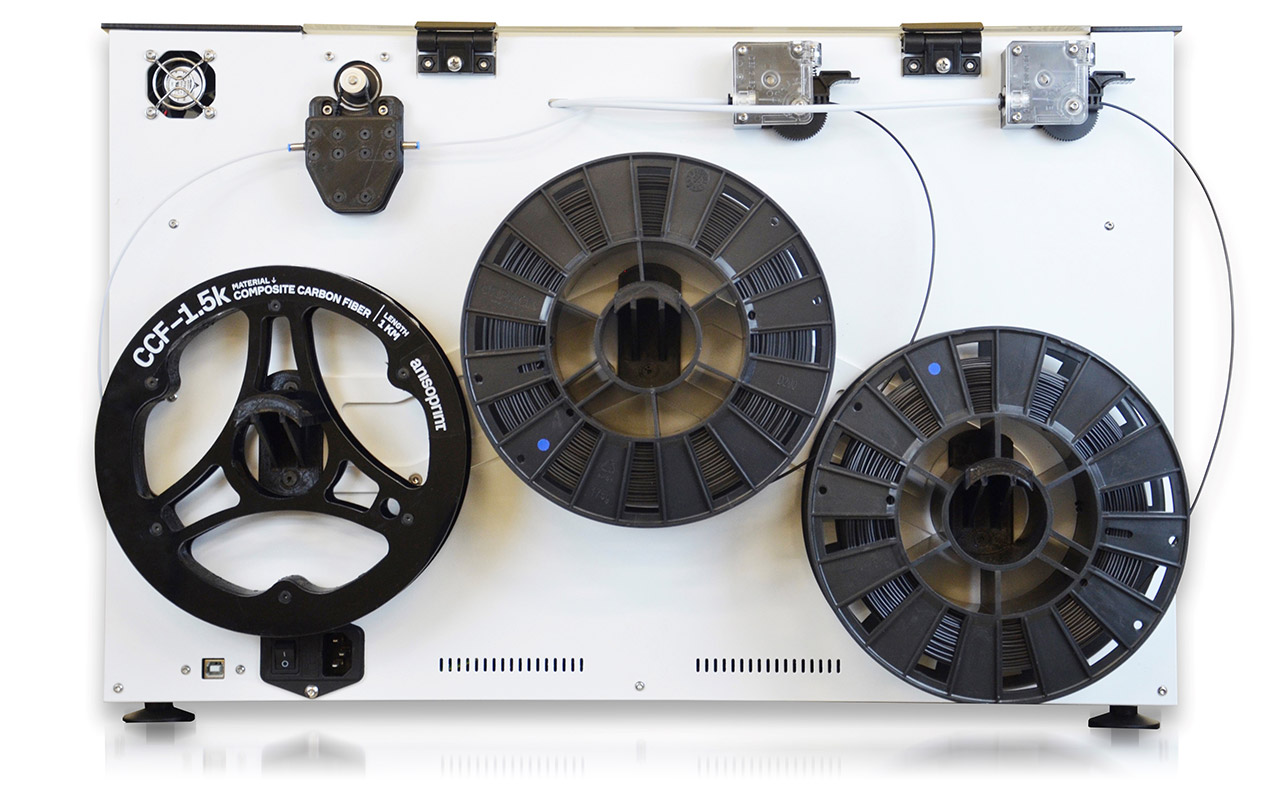
Composite Fiber Co-Extrusion (CFC)-Technologie für die additive Fertigung unter Verwendung verschiedener thermoplastischer Polymere, die mit Endlosfasern verstärkt sind (z. B. Kohlenstoff, Basalt), die in einem automatisierten, einstufigen Prozess verfestigt und ausgehärtet werden, der weder Werkzeuge noch Nachbearbeitung erfordert.
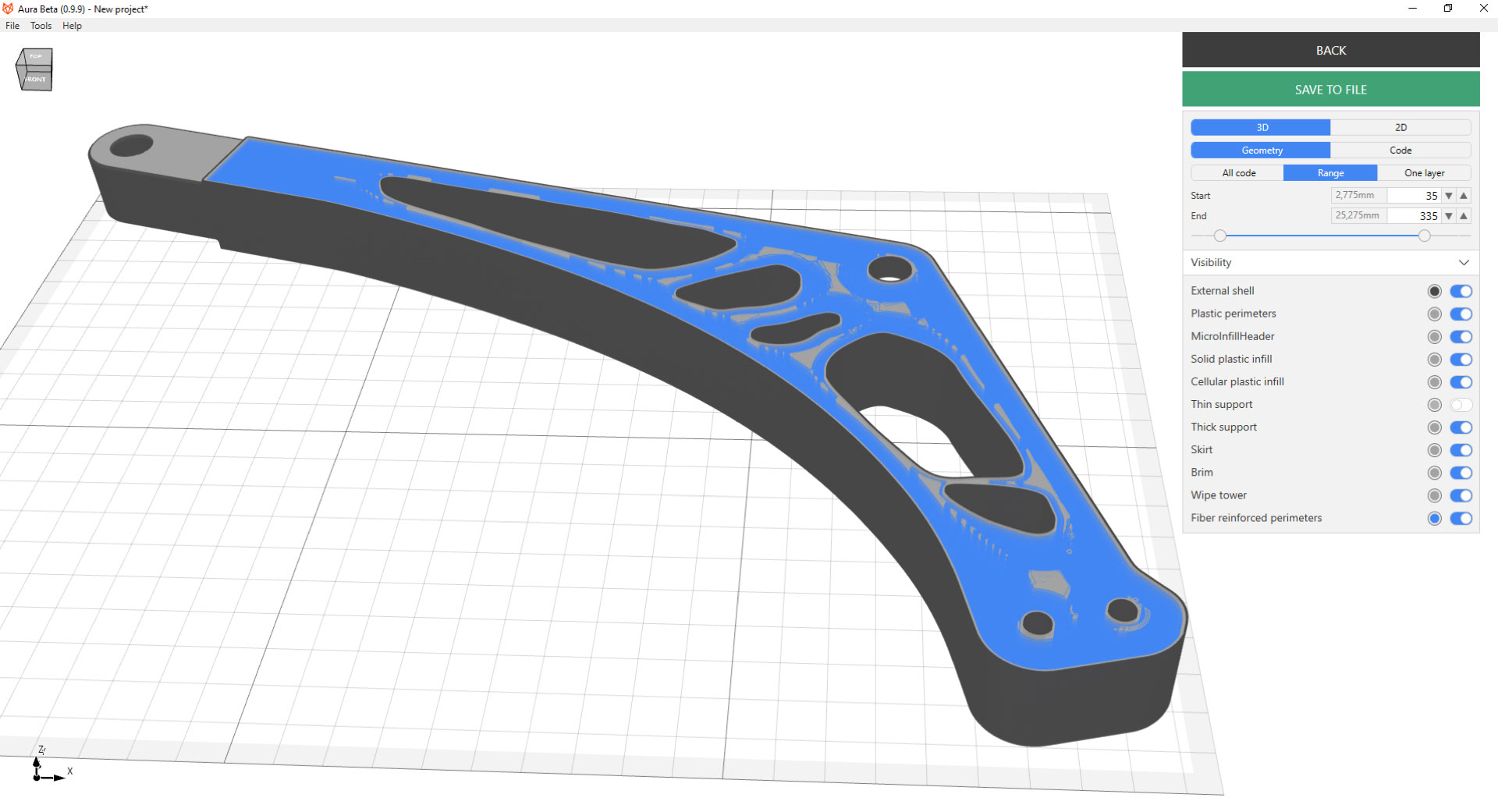
Aura Slicer-Software, die 3D-Modelle für die Herstellung von Teilen mit Composer CFC-Druckern sowie herkömmlichen FFF-Druckern aufbereitet.
Composer Desktop-3D-Drucker in drei Größen erhältlich (A4, A3, A2).
PROM Familie industrieller Drucksysteme mit Roboter- und Portaloptionen, im Handel ab 2020 erhältlich.
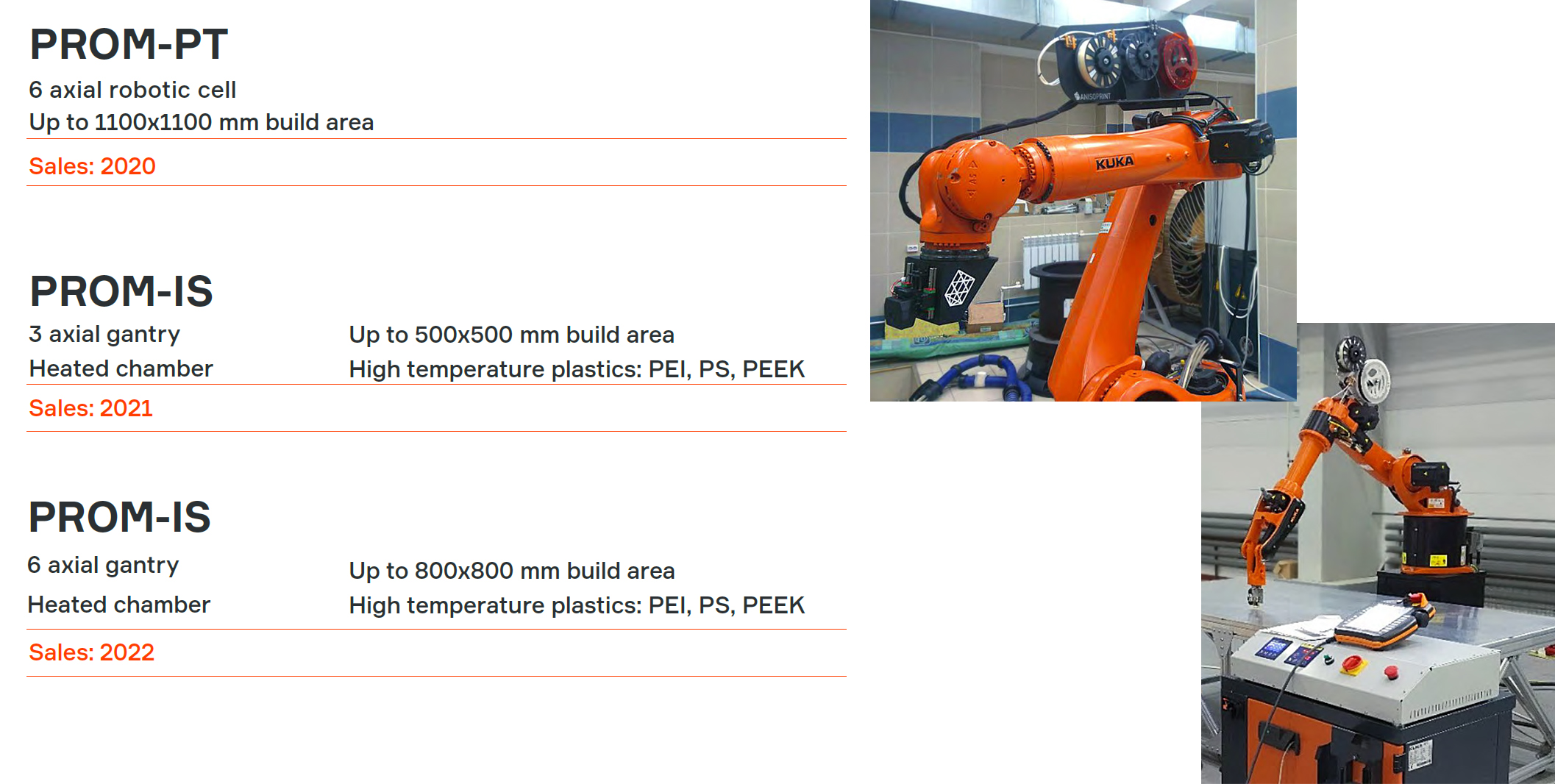
Roboterentwicklung vs. Desktop
„Der Roboter hat einen anderen Druckkopf, weil Sie den Kopf bewegen müssen, damit er während des Druckens in beengte Räume passt und hineinreicht“, erklärt Antonov. „In einer 2D-Ebene ist das kein Problem. Aber im 3D-Raum müssen Sie Fasern dort platzieren, wo bereits eine gewisse Struktur vorhanden ist. Die optimale Zugänglichkeit wird mit einer Nadel erreicht. Wir brauchen also einen Kompromiss, einen nadelähnlicheren Druckkopf.“
Er weist auf andere Unterschiede hin, wie zum Beispiel industrielle Kontrollen. „Die Desktop-Drucker basieren auf Unterhaltungselektronik wie Arduino. Aber für größere Robotersysteme benötigen Sie industrielle Bewegungssteuerung und Schnittstellen und alle Arten von in-situ-Qualitätssicherung, wie zum Beispiel Laservermessung, die Markforged auf seiner größeren Maschine hat. Sie müssen auch die Heizungs-/Kühlungssensoren und -steuerungen ändern.“ Er fügt hinzu, dass all dies Zeit und Ressourcen erfordert und ihre Priorität in den letzten zwei Jahren darin bestand, die Desktop-Maschine zu entwickeln, aber jetzt arbeiten sie auch an den Robotersystemen.“
Software:Aura
Antonov beschreibt die Software von Anisoprint als flexibel und ermöglicht sowohl Anfängern als auch Fortgeschrittenen. „Die Software ist einfach zu bedienen, aber es ist wichtig, dass F&E-Labors die Möglichkeit haben, Druckparameter zu ändern“, erklärt er. Zu den Kunden zählen das Forschungsinstitut MFPA (Weimar, Deutschland), das Brightlands Materials Center (Geleen, Niederlande) und die Technische Universität München sowie Hersteller wie Schunk Carbon Technology, Airbus und BMW.
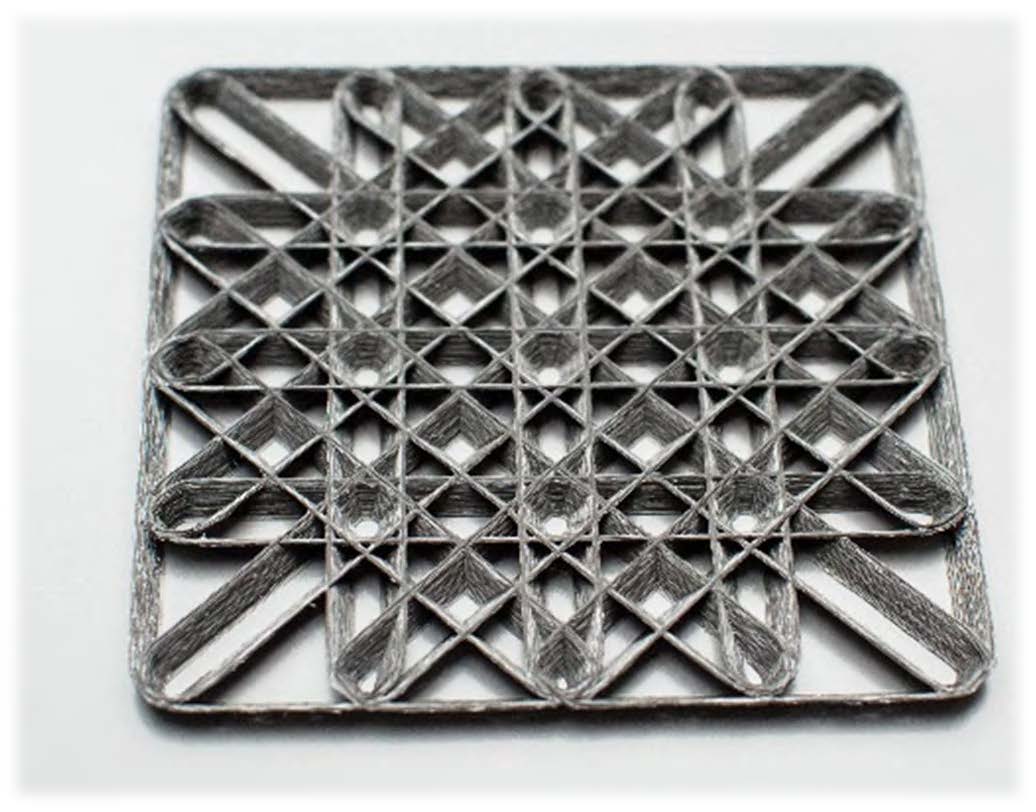
Anisoprint bietet 3D-gedruckte Mikrosatelliten-Verbundteile mit einer Gewichtsreduzierung von bis zu 45 % gegenüber Leichtmetallen.
Partnerschaften für kontinuierliche Lösungen
Anisoprint, das sich selbst als offene Materialplattform bewirbt, möchte auch weitere Partnerschaften für neue Druckmaterialien und Teile eingehen. Im Juni gab es eine Vereinbarung mit dem maltesischen Thought3D über die Verwendung der Magigoo-Klebstoffe des letzteren bekannt. Diese kleben die erste Druckschicht auf das Druckbett und verhindern so das Ablösen von Teilen. „Eine schlechte Haftung der ersten Schicht ist eines der häufigsten Probleme, die gedruckte Teile ruinieren können, und das nicht unbedingt zu Beginn des Baus“, erklärt Antonov. „Das ist besonders wichtig für unser offenes Materialsystem, bei dem der Kunde aus verschiedenen Thermoplasten wählen kann. Jeder erfordert unterschiedliche Druckparameter und aus diesem Grund haben wir mehrere Einstellungen für die erste Schicht in unserer Aura-Slicer-Software eingeführt. Aus diesem Grund werden wir auch Magigoo-Sticks in jeder Composer-Box enthalten, um sicherzustellen, dass unsere Kunden eine geeignete Lösung für eine gute Haftung der ersten Schicht in der Hand haben.“
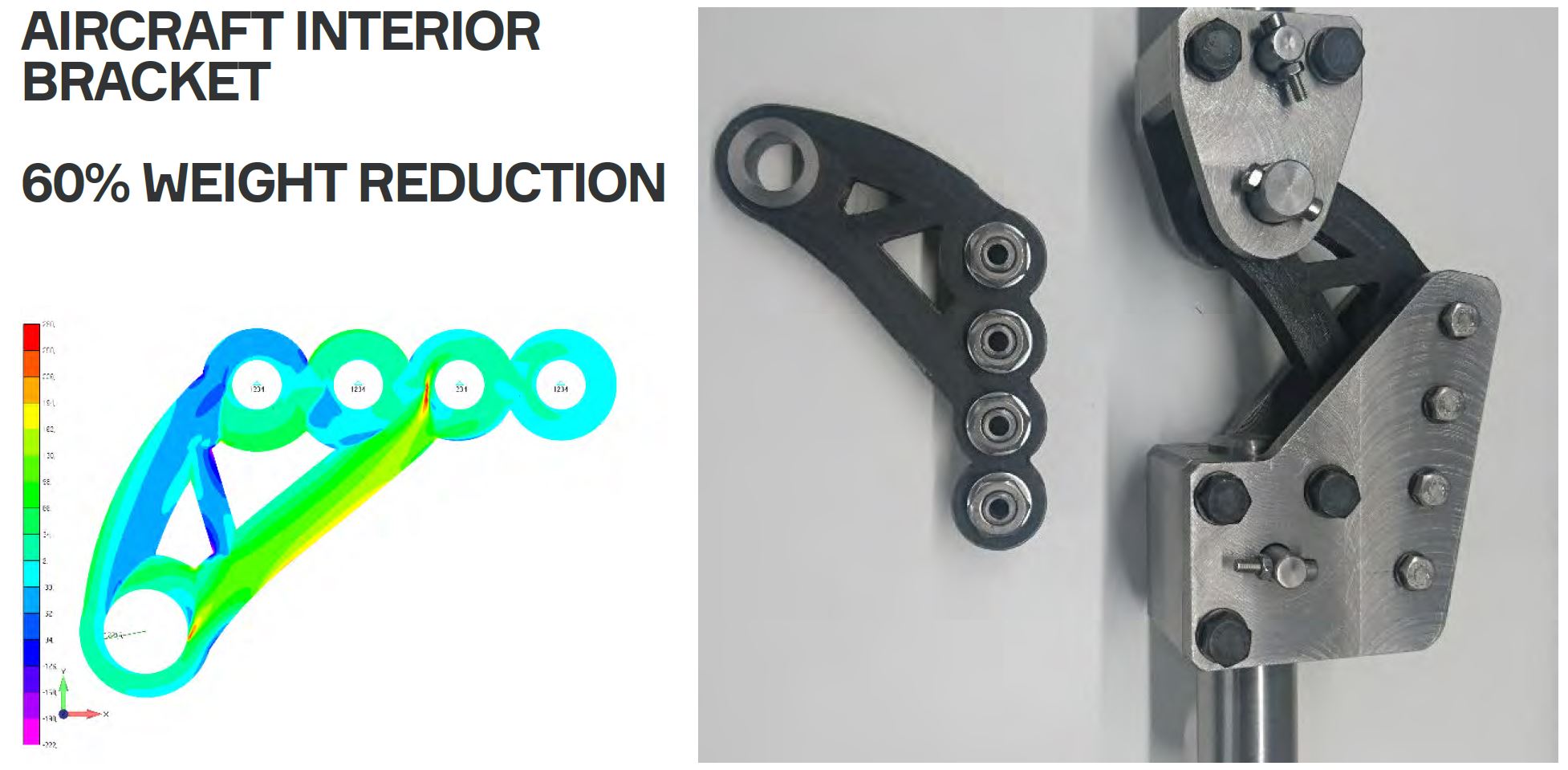
Anisoprinting-Anwendungen
Anisoprint sagt, dass seine Technologie in vielen Bereichen eingesetzt werden kann, von der Luft- und Raumfahrt über Konsumgüter bis hin zum Gesundheitswesen. Ein Beispiel ist ein Flugzeugsitzträger, der 1,5 Tonnen Last trägt, bei einer Gewichtsreduzierung von 40 % gegenüber Aluminium. Bei 100 solcher Vorrichtungen in einem durchschnittlichen Single-Aisle-Passagierflugzeug kann diese Gewichtsreduzierung zu erheblichen Einsparungen bei den Treibstoff- und Gesamtbetriebskosten führen.
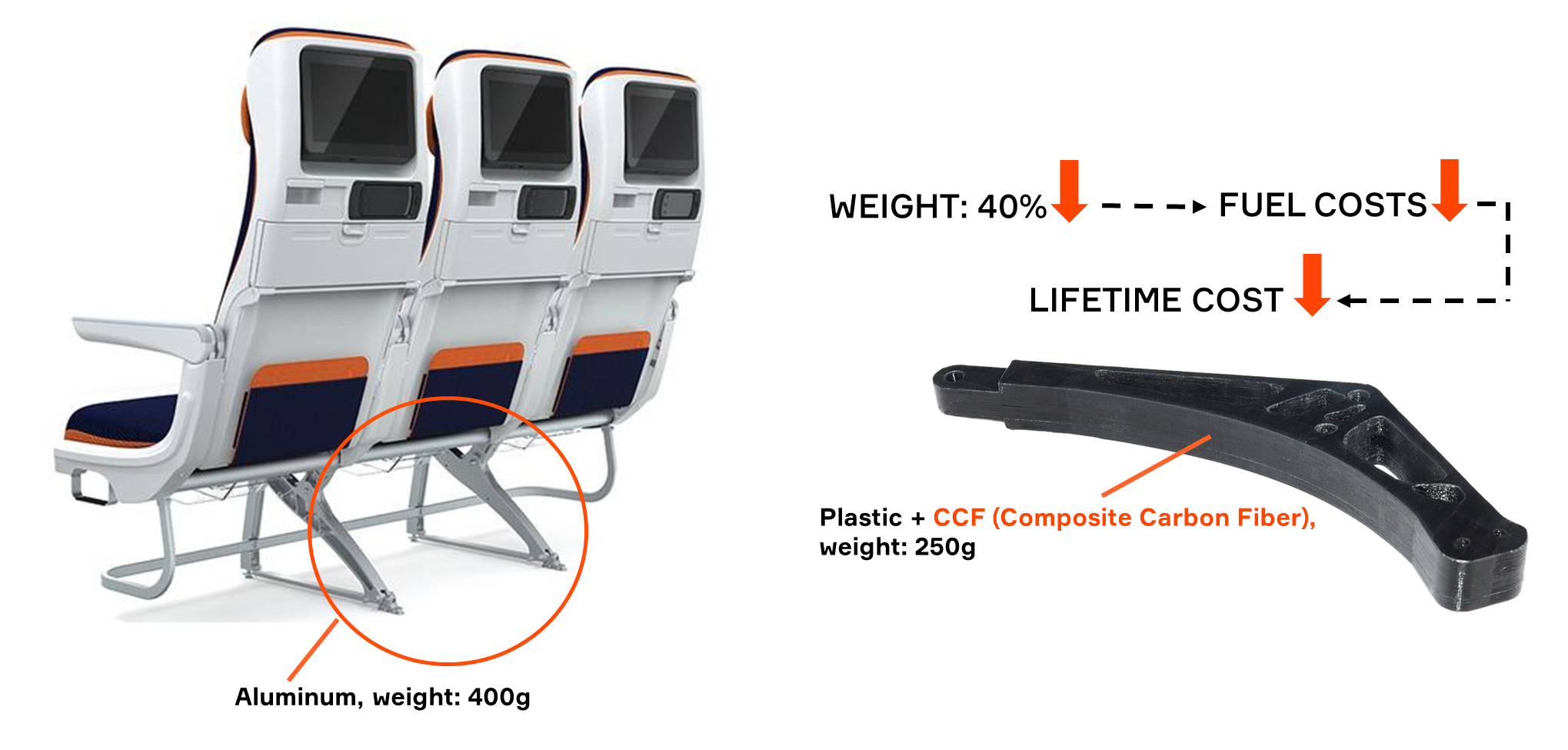
Anisoprint 3D-gedruckte Verbundwerkstoff-Flugzeugsitzträger erzielen 40% Gewichtseinsparungen gegenüber Aluminium.
Ein anderer Fall ist ein Kolben zum Formen von Joghurtbechern, der in einer Milchproduktionslinie verwendet wird. Typischerweise werden solche Kolben aus gefrästem Polyamid hergestellt, aber der Austausch solcher Teile bei Beschädigung dauert drei Monate, wobei die Produktionslinie für diese Zeit stillsteht. Das von einem Anisoprint Composer gedruckte Teil hat angeblich eine längere Lebensdauer und reduziert die Ausfallzeit der Produktionslinie von 3 Monaten auf 24 Stunden.
Anisoprint erfüllte mit seinem 3D-gedruckten Verbundkolben die Anforderungen an eine Komponente einer Milchproduktionslinie, jedoch mit einer drastisch verkürzten Austauschzeit.
„Anisoprinting ermöglicht das Design und die Herstellung optimaler Verbundstrukturen durch Verbundfaser-Coextrusion“, sagt Antonov. „Thermoplastische Polymere werden in einem einstufigen, vollautomatischen Prozess ohne Nachbearbeitung mit Endlosfasern verstärkt, verfestigt und ausgehärtet. Als Ergebnis erhalten wir Teile, die um ein Vielfaches stärker, leichter und billiger sind als herkömmliche Metalle und Kunststoffe und auch herkömmlichen Verbundwerkstoffen überlegen sind.“
Harz
- 5 gängige additive Fertigungsverfahren
- Additive Fertigung vs. subtraktive Fertigung
- Vorteile der additiven Fertigung
- Eine Umfrage zu Arbeitsabläufen in der additiven Fertigung
- Die 10 wichtigsten Fortschritte in der Fertigungstechnologie für Verbundwerkstoffe
- Verbundwerkstoffherstellung:Die Herstellung von Verbundwerkstoffen
- Additive Fertigung mit Verbundwerkstoffen in der Luft- und Raumfahrt und Verteidigung
- Henkel bietet Werkstoffplattform für die additive Fertigung
- Additive Fertigung in der Elektronik
- Additive Fertigung in der Luft- und Raumfahrt