Kurzanleitung zum Versiegeln von FDM mit Insight
Sie sind also daran interessiert, dieses neue Produktdesign zu qualifizieren, das flüssig hält, aber die erforderliche Nachbearbeitung fürchtet? Bewahre Ruhe und Einsicht.
Im Zuge der Weiterentwicklung der Additive Manufacturing (AM)-Technologie scheint es eine endlose Anzahl von Anwendungen zu geben. Nichtsdestotrotz erledigen diejenigen, die AM für funktionelles Prototyping und Endverbrauchsteile suchen, die Arbeit weiterhin mit einem 25 Jahre alten Arbeitspferd – der Fused Deposition Modeling (FDM)-Technologie. Satte 85% des Marktes basieren auf FDM und das ist keine Überraschung. Es produziert genaue und funktionale Teile aus einer Vielzahl von technischen Produktionskunststoffen.
Abgesehen von all seinen Vorteilen ist FDM auch von Natur aus porös. Für viele Anwendungen spielt dies überhaupt keine Rolle. Wenn Sie Thermoformen sind, würden Sie diesen Fehler akzeptieren. Wenn Sie jedoch versuchen, ein Gas oder eine Flüssigkeit (in oder aus) zu halten, ist dies eine eklatante Einschränkung. Wenn Porosität ein Problem darstellt, ist der Beginn mit der Insight-Verarbeitungssoftware der beste Weg, um sicherzustellen, dass Ihre Anwendung erfolgreich ist.
Die Geometrie hat großen Einfluss darauf, welche Technik oder Kombinationen von Techniken erforderlich sind, um das Teil zum Testen und dann zum Endgebrauch zu versiegeln. Der Einsatz der Insight-Software von Stratasys, die in der Fortus-Produktlinie von Stratasys enthalten ist, ist eine einfache Möglichkeit, Porositätsprobleme bei den meisten Geometrien zu lösen; umgekehrt können einige komplexe Geometrien möglicherweise eine arbeitsintensive Nachbearbeitung erfordern. Wenn Sie also der sparsame Typ sind, sollten Sie Ihre Anstrengungen unternehmen, um STLs im Voraus mit einer Ultem-Faust zu verarbeiten, um sicherzustellen, dass diese manuellen Vorgänge nicht erforderlich sind. Und rate was? Im Gegensatz zu den meisten Nachbearbeitungsmethoden ändert diese Strategie die Teilegeometrie nicht.
Wenn Sie mit FDM bereits vertraut sind, wissen Sie vielleicht, warum Porosität oft notwendig ist. Wenn nicht, aus folgendem Grund:Das Modell kann Bereiche aufweisen, die nicht selbsttragend sind, sodass die Stützen entfernt und aufgelöst werden müssen. Die natürliche Porosität ermöglicht es der löslichen Lösung, das Trägermaterial zu erreichen und aus denselben Bereichen, die möglicherweise verdeckt sind, abzufließen. Mit anderen Worten, manchmal ist Auslaugen hilfreich. Denken Sie daran.
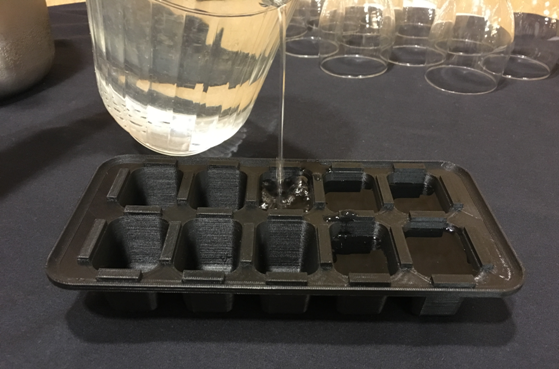
Versiegeln mit Einsicht
Mit Insight haben Sie die Möglichkeit, das Problem der Porosität zu kontrollieren oder sogar zu beseitigen, insbesondere bei einfachen Geometrien. Dies gilt, solange die Anwendungsanforderungen darin bestehen, ein Gas oder eine Flüssigkeit um Atmosphärendruck zu halten. Bei höheren Drücken/Vakuum oder bei komplexen Teilegeometrien wird es nicht so effektiv sein.
Der erste Schritt befasst sich mit der Ausrichtung des Builds auf der Plattform. Dies erfordert Ihr Urteilsvermögen und die Anforderungen der Anwendung. Die wichtigste Regel ist, das Teil so auszurichten, dass die meisten Oberflächen vertikal ausgerichtet sind.
Nachdem Sie die optimale Ausrichtung bestimmt haben, fügen Sie im nächsten Schritt mehrere Konturen zu den vertikalen Wänden hinzu (Bild unten). Grundsätzlich beruht diese Technik auf der Verwendung zusätzlicher Konturen und reduziert oder eliminiert wiederum Raster aus diesen Schichten. Das Vorhandensein von Rastern innerhalb eines Modells erhöht das Leckagerisiko aufgrund der Luftspalte, die sie erzeugen, wie unten gezeigt (oberes Bild).
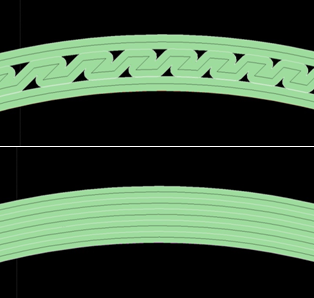
In der Gruppen-Symbolleiste können Sie die Parameter einrichten, um Luftspalte zu reduzieren, indem Sie die folgenden Schritte ausführen:
- Bestimmen Sie Ihre Wandstärke, indem Sie an jeder Schicht messen, und führen Sie dann die Berechnung durch, sodass die Wandstärke gleich der Anzahl der Konturen multipliziert mit der Konturenbreite ist. Sie können eine Reihe von Schichten auswählen, die die gleichen Wandstärken haben.
- Einrichten von benutzerdefinierten Gruppen für jede Dicke und fügen Sie die Schichten zu den Gruppen hinzu. Innerhalb jeder Gruppe können Sie die Anzahl der Konturen und ihre jeweilige Breite steuern.
- Wählen Sie die Link-Konturen und fügen Sie nach Möglichkeit einen leichten negativen Luftspalt von Kontur zu Kontur hinzu. Diese Funktion erstellt kontinuierliche Werkzeugwege, indem Start- und Stopppunkte zwischen den einzelnen Konturen eliminiert werden.
In diesem Beispiel, das in den Parametern für eine benutzerdefinierte Gruppe angezeigt wird, habe ich eine Wandstärke von 0,100. Ich habe fünf (5) Konturen mit einer Konturbreite von 0,020 verwendet. Ich habe auch die Link-Kontur Kontrollkästchen aktiviert und gab ihm einen Luftspalt von -0,001. Alternativ können Sie Konturbreite apply anwenden und Konturen verknüpfen global, wenn es Ihren Anforderungen entspricht, über das Werkzeugweg-Setup Menü.
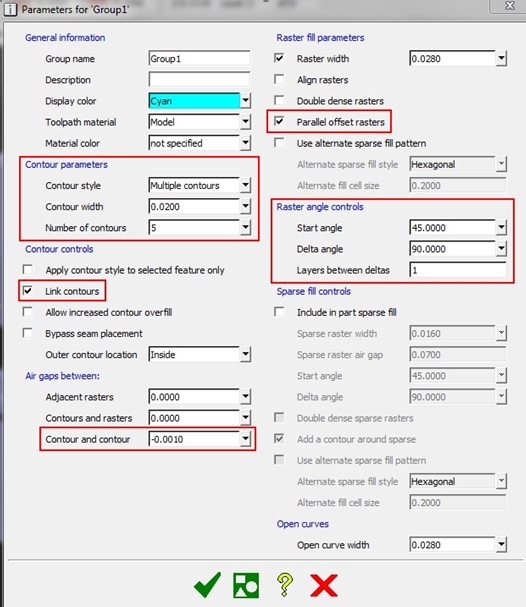
Hinweis: Das Ändern einiger dieser Parameter kann Ihre Bauzeit und Ihren Materialverbrauch verändern. Die beste Vorgehensweise besteht darin, eine „grüne Flagge“ als Kontrolle zu verwenden und die geschätzte Zeit und das Material zu notieren, bevor Parameter geändert werden.
Als Nächstes sehen wir uns Raster an, da Sie wahrscheinlich einige Bereiche haben, die sie benötigen. Standardmäßig sind Rasterwinkelsteuerungen so eingestellt, dass sie bei 45° beginnen und sich mit 90°-Delta abwechseln (siehe oben). Diese abwechselnden Umkehrbereiche hinterlassen Pfade oder Luftspalten durch die Schichten, d. h. die schwarzen Dreiecke, wo die Raster auf die Innenkanten der Konturen treffen.
Durch Auswahl von Parallelversatz Rasters, Insight ändert drei Parameter.
- Variiert die Anzahl der Konturen auf jeder Ebene, um die Raster-Umkehrungen zu verbergen. Dies gilt auch dann, wenn Sie bereits mehrere Konturen eingerichtet haben.
- Positioniert die Raster-Werkzeugwege parallel zu benachbarten Layern (0° Delta).
- Versetzt die Raster-Werkzeugwege, sodass sie die Nähte der vorherigen Ebenen abdecken.
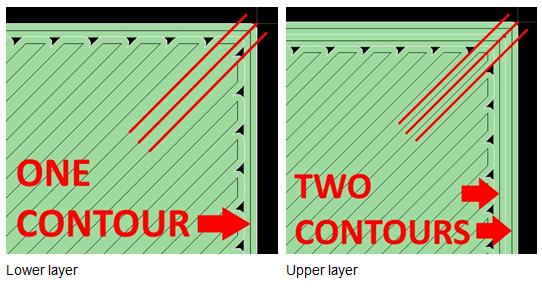
Damit ist der Deal ungefähr besiegelt. Dies sollte Ihnen einen hervorragenden Ausgangspunkt für die Verarbeitung von STLs als Vorbereitung für FDM-Dichtungsanwendungen bieten.
Hier ist ein Artikel über einige andere Nachbearbeitungstechniken, die die Versiegelung auf die nächste Stufe heben. Aber seien Sie vorsichtig, denn sie wirken sich auf Ihre Geometrie aus.
Tags:FDM-Technologie, Thermoformen, Ultem
3d Drucken
- Ein Leitfaden zum 3D-Druck mit HPs Multi Jet Fusion
- Fräsen – Eine Kurzanleitung
- Java 8 – Kurzanleitung
- Kurzanleitung zur GD&T-Parallelität
- Eine Kurzanleitung zur Kaltpressmaschine
- Eine Kurzanleitung zum Planetengetriebe
- Eine Kurzanleitung zur Servopressmaschine
- Eine Kurzanleitung zum Getriebeabwickler
- Eine Kurzanleitung zu CNC-Drehmaschinenachsen
- Eine Kurzanleitung zu Power Chucks