Design für die additive Fertigung von Vorrichtungen und Werkzeugen
Aus diesem Grund wird das Design für die additive Fertigung noch immer nicht von den meisten Unternehmen übernommen. Das traditionelle Vorrichtungsdesign wird durch die Fähigkeiten und Einschränkungen der Maschinen bestimmt, auf denen wir sie herstellen. Hersteller verwenden am häufigsten 3-Achsen-CNCs oder manuelle Werkzeugmaschinen, um Fertigungseinrichtungen zu erstellen.
Um sowohl zeit- als auch kosteneffektiv zu sein, neigen diese Vorrichtungen dazu, sehr sperrig zu bleiben. Dies liegt daran, dass Hersteller den Zeitaufwand für Produktionsanlagen begrenzen und mehr Zeit für die Herstellung der Produkte der Kunden aufwenden möchten. Dies führt dazu, dass Unternehmen die Herstellung von Vorrichtungen trotz ihrer Bedeutung für die Herstellung von Endprodukten als nicht wertschöpfende Tätigkeit betrachten.
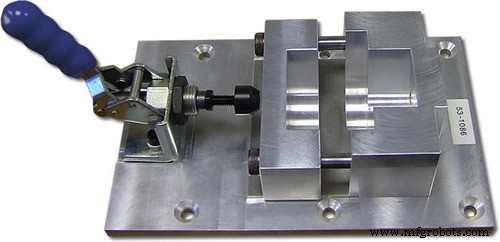
Die Probleme, mit denen diese Hersteller am Ende zu uns kommen, sind ihre Maschinenzeit (d. h. Teildurchlaufzeit) und der Mangel an verfügbaren Arbeitskräften. Die Lieferzeiten für die Teilebeschaffung in einer Maschinenwerkstatt werden oft in Wochen berechnet, und wenn Sie endlich Maschinenzeit bekommen, stören oder verzögern Sie etwas anderes. Sobald Sie die Maschine haben, benötigen Sie entweder einen Maschinisten, der den Code schreibt, oder Sie erledigen die Arbeit manuell. Sie benötigen also einen erfahrenen Bediener, der die Arbeit ausführen kann.
Obwohl wir in der Regel komplexe Teile mit organischen Geometrien herstellen, landen wir oft beim Vorrichtungsdesign „Blocks on a Plate“. Dies ist jedoch sinnvoll. Wir möchten die Zeit, die wir für unsere Maschinen benötigen, begrenzen und unser Lagermaterial wird normalerweise in Vierkantstangen, Rohren oder Blechen geliefert. Dieser Status Quo hinterlässt lange Vorlaufzeiten, große sperrige Vorrichtungen, die in unseren Einrichtungen gelagert werden müssen, und ein hohes Kosten-Teile-Verhältnis, wenn wir die Arbeitskosten und die Maschinenzeit berücksichtigen.
Der Zusatz „Quick Fix“
Als Reaktion auf diese Herausforderungen haben viele Hersteller die additive „Quick Fix“-Lösung übernommen. Sie haben sich der additiven Fertigung zugewandt, um interne Zeit- und Ressourcenherausforderungen zu bewältigen.
Ohne Konstruktionsänderungen vornehmen zu müssen, bietet der Drucker sofort ein Ablassventil in der Maschinenwarteschlange und dreht Teile schneller um und läuft Tag und Nacht unbeaufsichtigt. Es ermöglicht eine kostengünstigere Herstellung von Vorrichtungen, erfordert keine manuelle Arbeit und verwendet eine Vielzahl von Materialien, um die Teileanforderungen zu erfüllen. In vielen Fällen bietet es auch eine sofortige ergonomische Verbesserung gegenüber einem massiven Gegenstück aus Metall.
Wenn wir uns also bei den Fertigungsbenutzern von FDM melden, sehen wir viele dieser Designs.
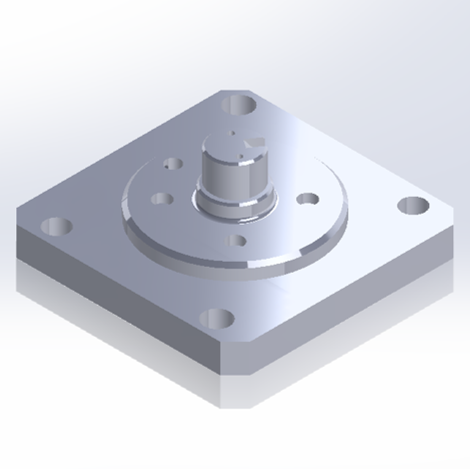
Dies ist ein Beispiel von einem unserer Kunden. Jährlich werden 12 dieser Leuchten aus Aluminium gefertigt. Ihr Geschäft ist immer voll, sodass sie ihre Produktion am Ende auslagern. Mit ihren derzeitigen Methoden kostet eine Vorrichtung über 3.000 US-Dollar und die Beschaffung dauert 4-6 Wochen. Dieses Szenario kommt nur allzu häufig vor, wenn wir mit produzierenden Unternehmen sprechen.
Vergleichen Sie das mit einer soliden 3D-gedruckten Halterung aus ABS. Die Kosten belaufen sich auf 190 US-Dollar und die Herstellung dauert etwa 19 Stunden, also etwas weniger als einen Tag.
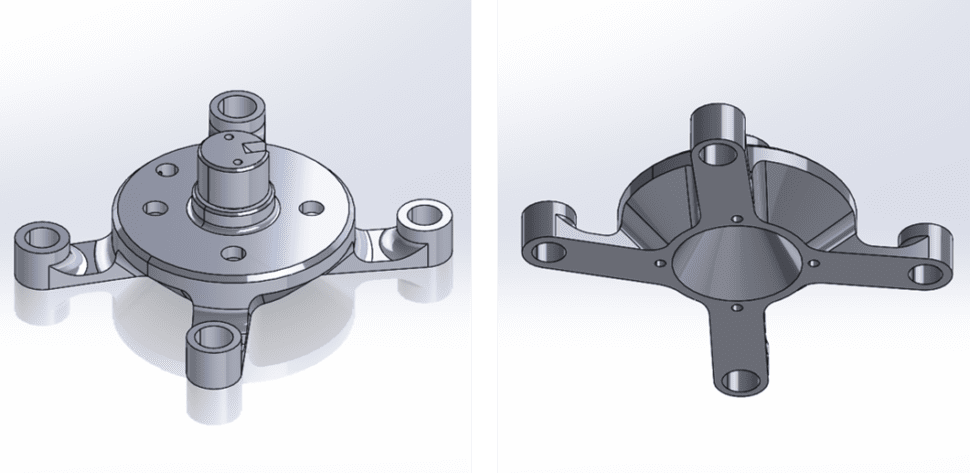
Wenn wir Design für additive Prinzipien anwenden, können wir diese Verbesserungen noch einen Schritt weiterführen. Durch die Verwendung des oben gezeigten Designs können wir die Kosten wieder auf 76 US-Dollar und die Druckzeit auf 11 Stunden senken. Das sind 60 % Kosten- und 42 % Zeitersparnis im Vergleich zum Drucken des traditionellen Designs.
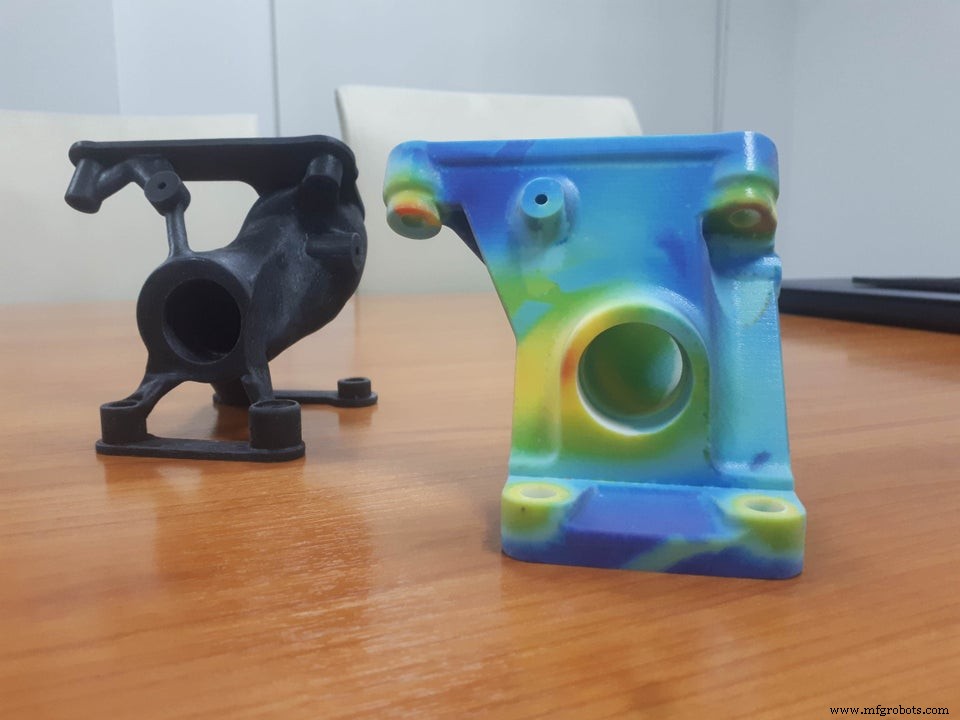
Häufige Fehler beim Design für die additive Fertigung
Bevor wir uns mit den besten Designpraktiken befassen, möchte ich ein paar Missverständnisse über Design für Additiv durchgehen und 2 häufige Fehler hervorheben, die ich sehe.
Der Begriff „Design for Additiv“ ist ein sehr weit gefasster Begriff. Sie können es sich als eine Ebene unter einem Begriff wie „Design for Manufacturing“ vorstellen. Manchmal sind die Leute verwirrt, wenn sie uns nach Design für Additiv fragen und wir fragen:"Was versuchst du zu tun?" und „Welche Maschine verwenden Sie?“
Dies ist wichtig, da jede Art von 3D-Drucker ihre eigenen Best Practices hat. Es gibt mittlerweile Dutzende von 3D-Druckern, Namen wie FDM, SLA, Polyjet, Binder Jet, DMLS usw. Jeder hat Variationen innerhalb dieser Unterfamilie. So wie eine Mühle und eine Drehmaschine unterschiedliche Konstruktionsprinzipien haben, hat jedes Additivsystem ein einzigartiges Regelwerk.
Viele Leute gehen auch davon aus, dass die additive Fertigung alle ihre Probleme ohne Nachteile löst. Obwohl Additiv extrem vielseitig ist und enorme Auswirkungen auf die Herstellung hatte, ist es nicht die Wunderwaffe, die es sein kann. Ein Beispiel hierfür könnten Komponenten sein, die Sie leicht günstig beziehen können. Wir hatten Anfragen, Teile zu drucken, die Sie für ein paar Cent online kaufen können, wie Bolzen, Schrauben und andere. Wir müssen verstehen und bewerten, für welche Anwendungen 3D-Druck erforderlich ist und wann Massenkomponenten die bessere Option sind.
Häufige Fehler
Die beiden häufigsten Fehler, die wir bei der Konstruktion für die additive Fertigung sehen, sind das Schälen und Aushöhlen von FDM-3D-gedruckten Teilen. Damit meine ich nicht keine oder extrem spärliche Füllung, sondern die Modellierung von Hohlräumen in der Teilegeometrie, um Materialkosten einzusparen.
Fast jedes Mal hat dies das Gegenteil der beabsichtigten Wirkung. FDM-Drucker benötigen Stützmaterial für Überhänge. Beim Konstrukteur von Hohl- oder Schalenteilen entstehen oft sehr große Überhänge, die mit Stützmaterial wieder aufgefüllt werden müssen. Manchmal können ausgehöhlte Teile Trägermaterial haben, das nach Abschluss des Drucks nicht mehr entfernt werden kann!
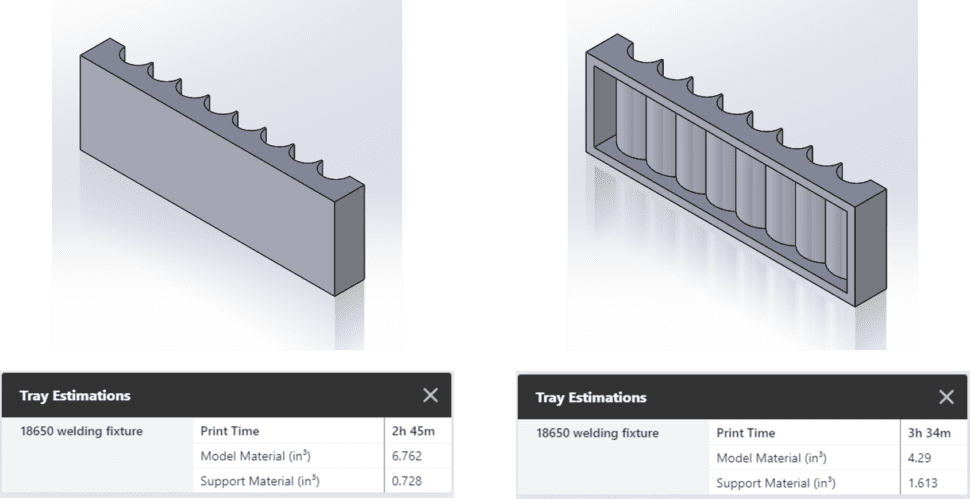
In diesem Beschussbeispiel haben wir einen leichten Rückgang des Gesamtmaterialverbrauchs, aber unsere Bauzeit hat sich um fast eine Stunde verlängert. Dies liegt daran, dass Systeme, die zwischen Modell und einzigartigem Trägermaterial wechseln, ständig jede Schicht zwischen den beiden Materialien wechseln müssen.
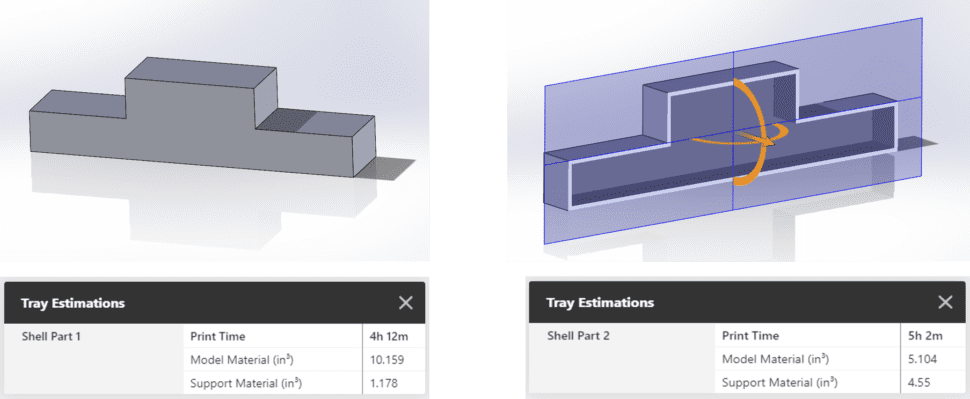
Das Aushöhlen zeigt uns erneut einen leichten Rückgang des Gesamtmaterialverbrauchs, aber eine Zunahme der Druckzeit. Darüber hinaus erzeugt dieses Szenario eingeklemmte Träger, die niemals aus dem endgültigen Druck entfernt werden können.
6 Design für additive Regeln für FDM
Nachdem wir nun die Herausforderungen und Missverständnisse beim Design für die additive Fertigung (DFAM) verstanden haben, wollen wir uns einige der einfachsten und gebräuchlichsten Designregeln ansehen, die Sie mit Ihrem FDM-Drucker verwenden können.
1. Selbsttragende Winkel
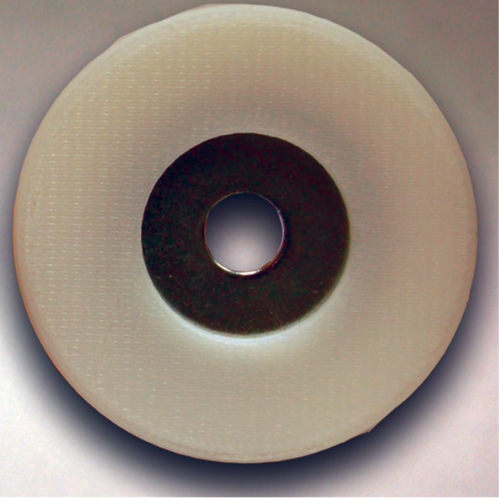
Diese Regel wird manchmal als 45-Grad-Regel bezeichnet und besagt, dass FDM-Teile keine Stützen benötigen, solange die Überhänge weniger als 45 Grad von der Vertikalen entfernt sind. Dies ist eine der schnellsten und einfachsten Konstruktionsänderungen, die Sie an bestehenden Teilen vornehmen können. Dadurch wird der Materialverbrauch reduziert und die Druckzeiten verkürzt. Ein wichtiger Hinweis zu dieser Regel ist, dass nicht alle Materialien 45 Grad als Cutoff verwenden. Dies variiert je nach Materialtyp und liegt im Allgemeinen zwischen 40 Grad und 60 Grad.
2. Eliminieren von Material aus sperrigen Funktionen
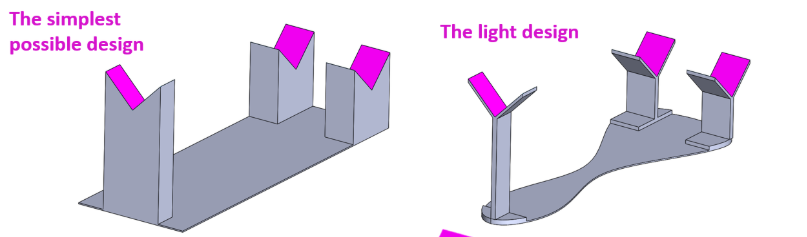
Die Eliminierung von Material aus sperrigen Elementen ist normalerweise das Ziel von Ingenieuren, wenn sie Schalen- oder Hohlteile konstruieren. Es stimmt, dass Sie beim 3D-Druck den Materialverbrauch erheblich reduzieren können, aber wir müssen darauf achten, wie wir es tun.
Einer der Tricks, die Sie anwenden können, wenn Sie versuchen, Material zu eliminieren, besteht darin, sich auf die passenden Oberflächen zu konzentrieren. Beginnen Sie mit dem Entwerfen von Kontaktpunkten, wie dem oben gezeigten Rosa, an denen das Teil mit der Vorrichtung interagiert. Von diesem Punkt an kann Ihr Design auf dem Endziel des Teils basieren, egal ob es sich um zusätzliche Festigkeit oder allgemein um leichtes Gewicht handelt.
3. Selektive Stärke nach Gesichtern
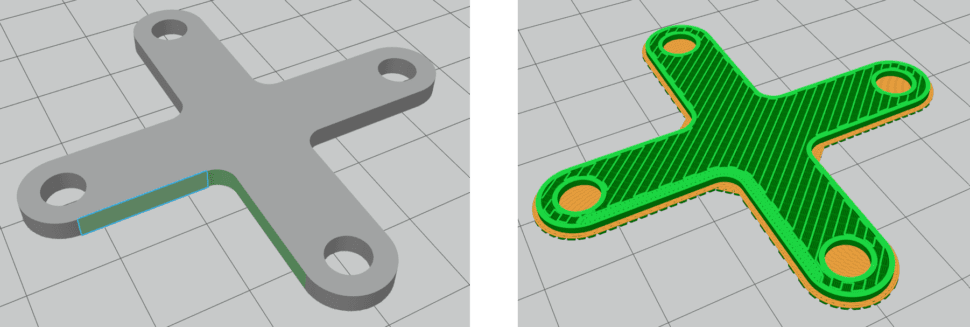
Die selektive Festigkeit nach Fläche ist ein weiteres Werkzeug, das verwendet wird, um leichte Teile unter Beibehaltung der strukturellen Integrität zu konstruieren. GrabCAD Print ermöglicht es Benutzern, native CAD-Geometrie zu importieren; Dinge wie Gesichter und Körper können innerhalb des Programms referenziert werden. Wir können einzelne Körper und Flächen auswählen und Fülldichten und Wandstärken festlegen. Dadurch können wir nur Material dort platzieren, wo wir zusätzliche Festigkeit benötigen, sodass wir nicht das gesamte Teil vollständig massiv drucken müssen.
4. Selektive Kraft nach Körper
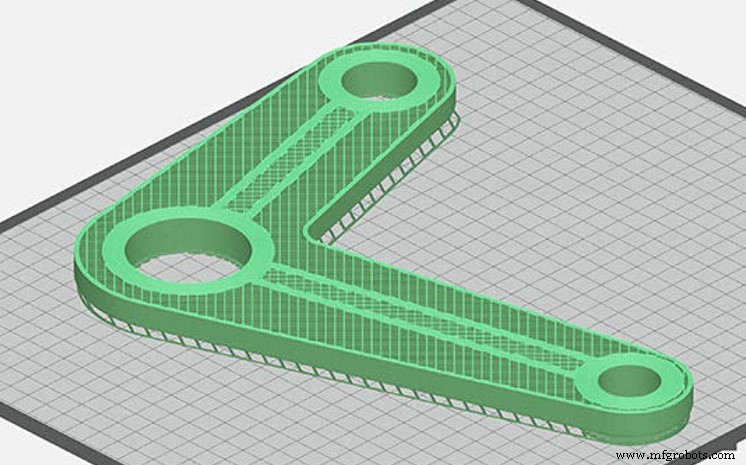
Genau wie die selektive Stärke nach Fläche ermöglicht die selektive Stärke nach Körpern Benutzern die Steuerung der Füllgrade zwischen separaten CAD-Körpern. Dies ist ein vereinfachtes Beispiel, aber durch Hinzufügen dünner Körper innerhalb eines Teils können Sie Strukturrippen erstellen, die die mechanische Leistung sicherstellen und gleichzeitig ein dünnes, leichtes Teil beibehalten.
5. Metalleinsatz
Metalleinsätze sind eine ausgezeichnete Wahl, wenn ein Bereich eines 3D-gedruckten Teils übermäßigem Verschleiß ausgesetzt ist. Anstatt ständig das gesamte Teil neu drucken zu müssen, ermöglicht das Anbringen eines Metalleinsatzes wie einer Mutter, einer Unterlegscheibe oder eines thermofixierten Gewindeeinsatzes eine längere Lebensdauer des Teils.
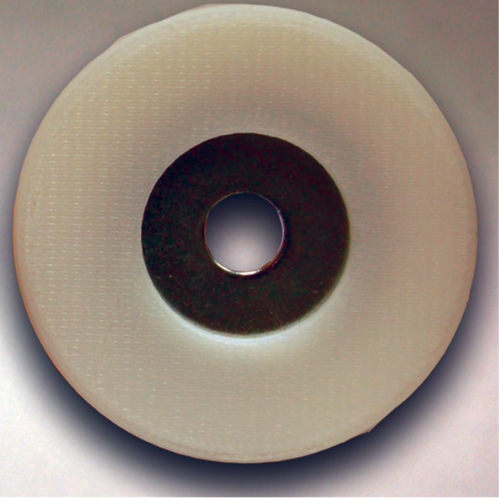
Eingebettete Einsätze wie Muttern und Unterlegscheiben erfordern, dass ein Loch in die CAD-Geometrie modelliert wird, wo sie platziert werden. Um eine Unterlegscheibe oder Mutter in Ihren Druck aufzunehmen, stellen Sie Ihren Drucker so ein, dass er eine oder zwei Schichten anhält, bevor er das Loch abdeckt, in dem der Einsatz platziert wird. Auf diese Weise können Sie zum Drucker gehen, die Beilage einlegen und den Druckvorgang fortsetzen. Wenn Sie direkt auf eine Metalloberfläche drucken, empfehlen wir Ihnen, die Gegenmetalloberfläche mit einem Acrylspray zu besprühen, um die Druckqualität zu gewährleisten.
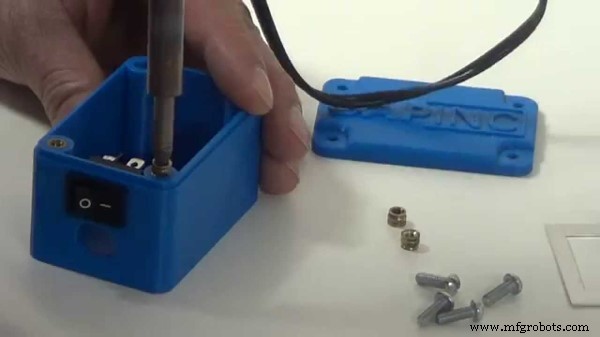
Heißfixierte Einsätze ermöglichen wiederholtes Einfädeln, dem blanker Kunststoff nicht standhalten kann. Diese werden nach dem Drucken mit einem Lötkolben platziert. Es ist wichtig, dass Sie an den Seiten des Lochs, wo es platziert werden soll, etwas extra festes Material lassen, damit der Einsatz hineinbeißt. In GrabCAD Print können Sie angeben, welche Einsatzgröße Sie verwenden möchten, und die Software ändert automatisch die Lochgröße und stellt zusätzliches Wandmaterial bereit.
6. Konsolidierte Baugruppen
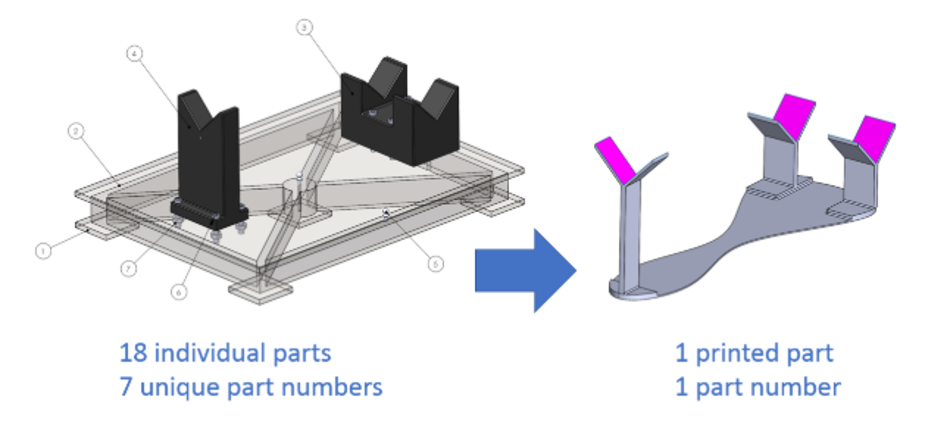
Wenn wir auf das Beispiel für sperrige Vorrichtungen zurückkommen, können wir sehen, dass das Drucken dieses Teils die Anzahl der Teile von 18 auf 1 reduziert und ohne jegliche Montage hergestellt werden kann.
Eine andere beliebte Methode, die von denen verwendet wird, die komplexere Vorrichtungen benötigen, ist die Verwendung sogenannter Hybridwerkzeuge. Diese Hybridwerkzeuge beinhalten Dinge wie Metallbefestigungen, Hydraulik, Schlauchleitungen und andere notwendige Anbauteile für fortschrittlichere Anwendungen.
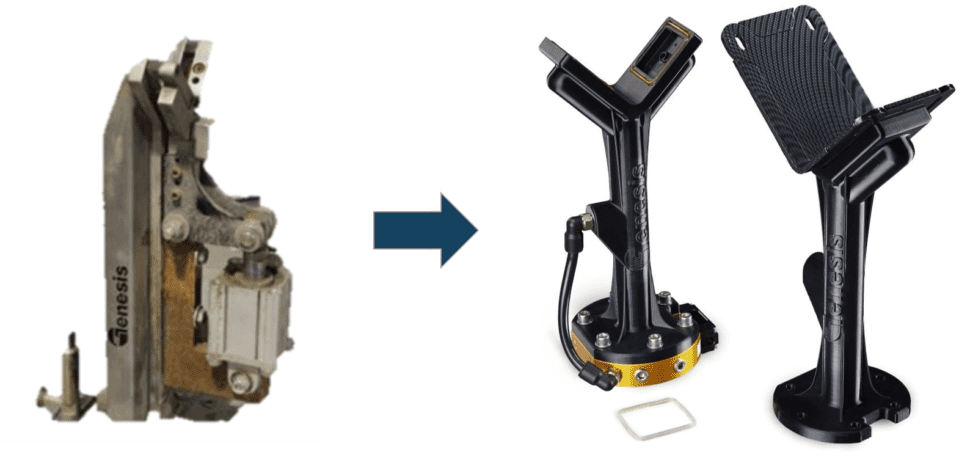
Dieses Beispiel von Genesis Systems zeigt ein traditionell hergestelltes End-of-Arm-Tool neben einem neu gestalteten 3D-gedruckten Tool, das Luftleitungen und Metallbefestigungen enthält. Genesis konnte das Gewicht des Werkzeugs erheblich reduzieren, sodass für diese Anwendung ein schnellerer, kleinerer und kostengünstigerer Roboter verwendet werden konnte.
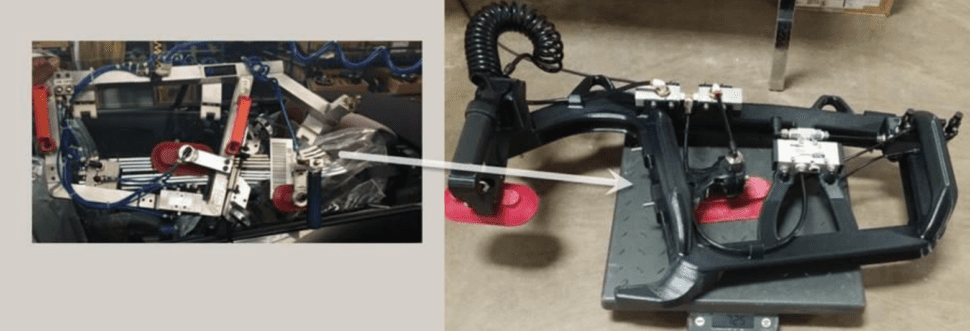
Dieses nächste Beispiel stammt von Ford. Das Originalwerkzeug auf der linken Seite ist aus Aluminium gefertigt und wird verwendet, um Fahrer bei der Installation von Fenstern an ihren Cabriolets zu unterstützen. Diese Leuchte war sehr sperrig, obwohl sie aus Aluminium gefertigt war. Es würde auch die Lackierung des Autos beschädigen, wenn es nicht kontrolliert wird, was zu Verzögerungen und zusätzlichen Kosten führt. Das 3D-gedruckte Redesign auf der rechten Seite enthält die gleichen notwendigen Luftleitungen und Befestigungselemente, während interne Rippen zur Unterstützung verwendet werden. Das neue 3D-gedruckte Design wiegt weniger als 7,5 Pfund.
Design für additive Schlussfolgerung
Zusammenfassend haben wir über Folgendes gesprochen:
- Traditionell hergestellte Werkzeuge und wie unsere Herstellungsmethoden und Rohstoffe unsere Designentscheidungen beeinflussen. Wir sprachen über den Wunsch, die Lieferzeiten für die Teilebeschaffung zu verkürzen, sowie über die Haupteinschränkungen in der Maschinenverfügbarkeit und qualifizierten Arbeitskräften.
- Selbst bei der Verwendung traditioneller Designs sehen Unternehmen immer noch Vorteile durch den Wechsel zur additiven Fertigung. Diese direkt gedruckten Designs verbessern in der Regel die Vorlaufzeit, die Kosten und die allgemeine Ergonomie aufgrund des geringen Gewichts.
- Missverständnisse in Bezug auf den Begriff „Design für die additive Fertigung“, wie zum Beispiel, dass der Begriff zu weit gefasst ist. Wir haben uns die häufigsten Fehler beim Aushöhlen und Schälen bei der Verwendung der FDM-Drucktechnologie angesehen.
- Schließlich haben wir uns 6 einfache Designtipps angesehen, die Sie in Ihre zukünftigen Designs implementieren können, um die Zeit bis zum Teil und die Kosten des Teils weiter zu reduzieren und die Gesamtfunktionalität zu verbessern
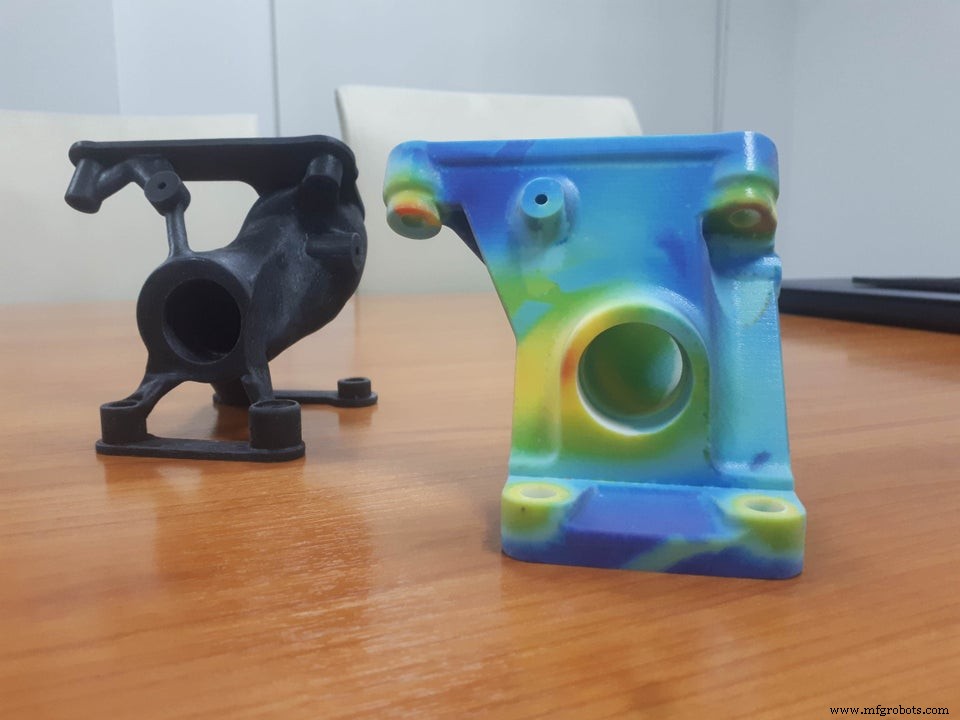
Optimieren Sie Ihre Designs für den 3D-Druck
Vom Konzept bis zur Produktion. CADimensions kann Ihnen bei jedem Schritt helfen
CADimensions-Dienste3d Drucken
- 4 vielversprechende Automatisierungstrends in der additiven Fertigung
- Additive Fertigung und Spritzguss – eine neue Vision für den Produktionslebenszyklus
- 6 Gründe, warum Sie Design für die additive Fertigung in Betracht ziehen sollten
- 4 brennende Fragen für die additive Fertigung im Jahr 2019
- Experteninterview:Robert Yancey von Autodesk über additive Fertigung, generatives Design und Industrie 4.0
- Einführung von AM Fridays und Additive Podcast
- Essentium und Lehvoss kooperieren bei der Entwicklung von Materialien für die additive Fertigung
- Design für die Herstellung von Leiterplatten
- Additive Fertigung in Medizin und Zahnmedizin
- Warum Design für die Fertigung wichtig ist