Trends bei E/A-Systemen der Prozessautomatisierung
Zuerst einige Definitionen:
NOA – Namur Open Architecture – erfunden von der User Association of Automation Technology (NAMUR) Dies ist eine Möglichkeit, zusätzliche Werte und Asset-Management-Daten (manchmal als Stranded Data bezeichnet) von einem Instrument zu erhalten, indem ein zweiter paralleler Standardkommunikationskanal installiert wird, der drahtlos sein kann. Bluetooth, 4G/5G etc. und hat keinen Einfluss auf die bestehende primäre Automatisierungssystemanbindung für den Messwert.
Ethernet – APL™ – Ethernet Advanced Physical Layer – wurde von einem Handelsverband von Geräteherstellern einschließlich OPC entwickelt und wird Ethernet für das Feld, für einzelne Instrumente und Sensoren bereitstellen. Es befindet sich noch in der Entwicklung und ermöglicht lange Kabellängen und Explosionsschutz durch Eigensicherheit mit Kommunikation und Energie über zwei Drähte.
OPC UA – Open Platform Communications Unified Architecture – ist ein Machine-to-Machine-Kommunikationsprotokoll für die industrielle Automatisierung, das von der OPC Foundation, einer Gruppe von Geräteherstellern, entwickelt wurde.
MTP – Module Type Packages – ist eine sich entwickelnde standardisierte Methodik, ebenfalls von der NAMUR, die eine gemeinsame Sprache zur Beschreibung der Eigenschaften von Prozessmodulen unabhängig von Hersteller und Technologie bereitstellt. Dadurch ist es jedem übergeordneten Automatisierungssystem möglich, MTP zu verwenden, um ein bestimmtes Modul/Paket genau zu steuern.
Marktgröße für Prozessautomatisierungs-E/A-Systeme
Die Gesamtmarktgröße für Prozess-I/O-Systeme wird auf etwas mehr als 3 Milliarden US-Dollar geschätzt, was einem Wachstum von etwa 3,7 % CAGR entspricht. Siemens hält ungefähr 14 % dieses Sektors, ABB mit 10 %, Honeywell 9 % und Rockwell 8 %.
Allgemeine Trends bei E/A-Systemen zur Prozessautomatisierung
- Dezentralisierung – dezentrale Installation von Remote-I/O-Stationen im Feld statt zentral in der Leitwarte
=> Reduzierung der Anlagenverkabelung
- Rückgang bei Anlagenfeldbussen
- Verdrahtung der Feldsensoren direkt an E/A-Klemmenleisten
=> Wegfall von Querverdrahtungsschränken
- Größere Flexibilität mit Universal I/O alias Late Binding I/O alias e-Marshalling alias Configurable I/O
=> Automatisierungshard- und -software entkoppeln, kürzere Systemlieferungen (Time-to-Market) und frühere Feldverkabelung
- Verstärkte Implementierung „intelligenter“ Sensoren mit höherem Datensatz
=> erweiterte Steuerungsoptimierung, Ferndiagnose und Asset-Management-Daten
- Der Aufstieg der Ethernet-basierten Kommunikation im Feld
=> z.B. PROFINET und Ethernet – APL™
Eine LinkedIn-Strohumfrage der Automation-Community ergab folgende Ergebnisse:
Es ist keine Überraschung, dass „Remote I/O station in Field“ in allen 3 Gruppen leicht gewonnen hat, aber interessant ist, dass „Type of Universal I/O“ in den Instrumenteningenieuren und ISA-Gruppen, die mehr berücksichtigt werden, auf den letzten Platz geschlagen wurde Prozessautomatisierung voreingenommen als die auf Fabrikautomatisierung fokussierte Automatisierungsgruppe. Auch „Plant Fieldbus“ schnitt besser ab als erwartet und belegte in allen Gruppen den zweiten Platz.
Rückgang bei Anlagenfeldbussen
Es gibt seit vielen Jahren einen historischen Trend zur Dezentralisierung im Feld statt zurück in die Leitwarte. Das extremste Beispiel hierfür war der Einsatz von Anlagenfeldbussen, um Anlagenverkabelung einzusparen. Paradoxerweise gibt es bei Anlagenfeldbussen einen Rückgang, während sich der Trend zum Einsatz von Remote-I/O-Stationen auch in explosionsgefährdeten Bereichen fortsetzt.
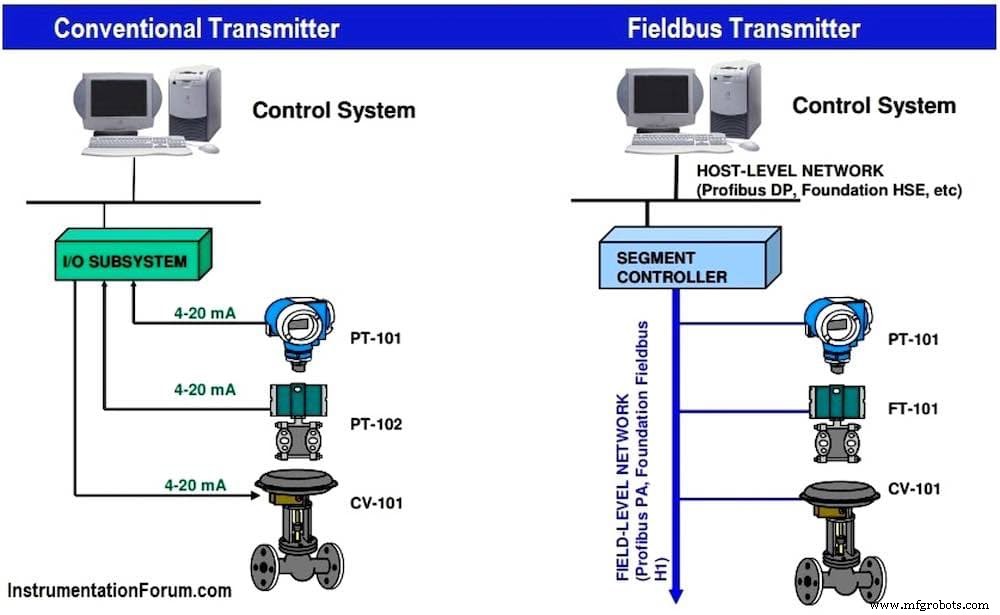
Vor allem in der Öl- und Gasindustrie sowie in der Petrochemie waren Feldbusse einst in aller Munde. Das hat sich geändert!! Anekdotisch erklärte eine große Ölgesellschaft, dass vor 20 Jahren ein Ingenieur begründen musste, warum er Foundation Fieldbus (FF) nicht für ein neues Projekt verwendet, vor 10 Jahren änderte sich dies in keine Präferenz, bis jetzt muss der Ingenieur begründen, warum er FF verwenden muss anstelle einer herkömmlichen 4-20-mA-HART-Lösung.
Einer der wichtigsten Vorteile von Feldbussen war die Kosteneinsparung und die Vereinfachung der Anlagenverkabelung – diese Einsparung ist bei Einsätzen in explosionsgefährdeten Bereichen stark reduziert und hat zusammen mit der technischen Kompetenz, die für die Entwicklung, Installation und Wartung von Feldbussystemen erforderlich ist, zu einem massiven Rückgang der Gunst geführt . FF-Installationen hatten angeblich zahlreiche Erdungs- und Erdungsprobleme. Viele der Ferndiagnose- und Asset-Management-Vorteile von Feldbussen werden ohnehin mit herkömmlichen HART-über 4-20-mA-Signalen realisiert, und tatsächlich bietet der zweite von NOA vorgeschlagene parallele Kanal dies, ohne die Hauptverbindung des Automatisierungssystems zu beeinträchtigen
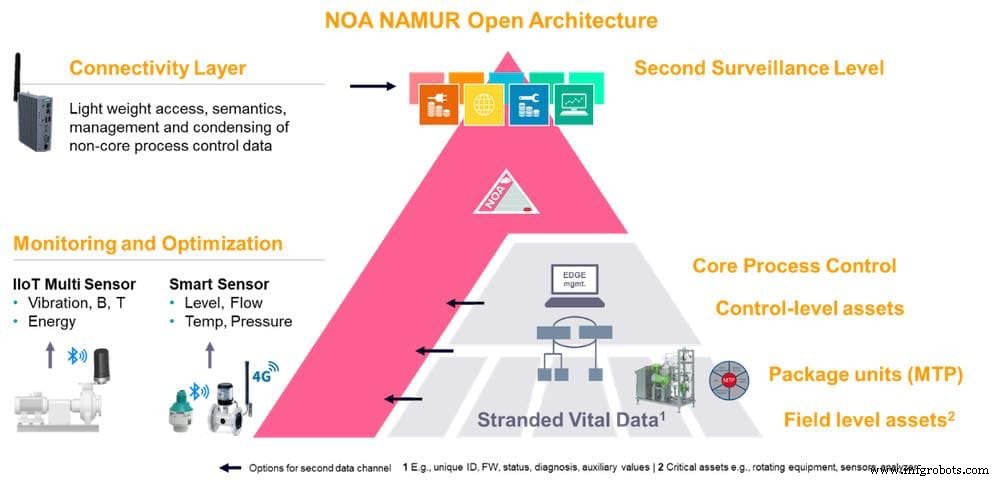
Wireless, das noch mehr Vorteile für die Anlagenverkabelung bietet, wird immer beliebter und nimmt einen Teil des FF-Marktanteils ein, aber hauptsächlich nur für Indikationen, niedrige Abtastraten und nicht kontrollierbare Messungen. Bei Funk sollte man jedoch nicht nur die Übertragungswege berücksichtigen, sondern auch die Tatsache, dass, wenn der Sender nicht selbstversorgt ist und ohnehin eine Stromverkabelung benötigt – ist das wirklich eine Ersparnis?
Warum hat PROFIBUS als Feldbus besser abgeschnitten?
PROFIBUS hat sich unter anderem deshalb besser entwickelt, weil er in Industriesektoren außerhalb der Öl- und Gasindustrie etabliert ist, zum elektrischen Systemstandard für die Kommunikation von MCCs und VSDs geworden ist und von vielen Anbietern als I/O-Bus verwendet wird. PROFIBUS entwickelt sich auch zu PROFINET, einem superdeterministischen Protokoll mit Ethernet-Geschwindigkeiten, -Medien und -Komponenten. PROFINET eignet sich besonders für Remote-I/O-Kommunikation, wie sie von Siemens verwendet wird.
Warum die wahrgenommene Popularität von Universal I/O?
Auch dies widerspricht dem Trend zur Dezentralisierung, zurück zu universellen I/Os in der Hauptregie, kontraintuitiv. Aber sicherlich geschieht dies, angetrieben von den DCS-Herstellern mit der Fülle von universellen und konfigurierbaren I/O-Systemen, die in den letzten Jahren auf den Markt kamen. Aber vielleicht zeigen die früheren Umfragen, dass dies bei den Endbenutzer-Automatisierungsingenieuren nicht so beliebt ist, wie die DCS-Unternehmen uns glauben machen wollen.
Universal-I/O hat viele Formen, einige mit 16- oder 32-Kanal-I/O-Modulen, die pro Signal konfigurierbar sind, andere, bei denen das erforderliche Modul pro Kanal ausgewählt wird. Die Vorteile sind kürzere Lieferzeiten von Automatisierungssystemen, frühzeitige Installation der Feldverkabelung; und die Handhabung von E/A-Änderungen sehr spät im Projektlebenszyklus.
Es werden jedoch viele Arten von E/A benötigt – gespeist und ungespeist, 2- und 4-Leiter, Simplex und redundant, sicherer und explosionsgefährdeter Bereich, Nicht-SIL und SIL, zunehmend Kurzschluss- und Unterbrechungsschutz, galvanische Trennung usw. – nicht alle All dies können universelle I/O-Systeme noch bewältigen.
Wenn eine Lösung beispielsweise separate Eigensicherheitsbarrieren erfordert, wird das Objekt eher umgangen. Universalbarrieren sind jetzt verfügbar, aber natürlich teurer als eine I/O-Karte mit integrierten Barrieren. Außerdem bieten viele universelle E/A-Systeme keine echte E/A-Redundanz.
Es ist ein Mythos, dass Universal-I/O durch Wegfall von Rangier- und Querverdrahtungsschränken Platz spart – dies ist eher ein Produkt des Trends, Feldverkabelung direkt auf der I/O-Platine (oder genauer gesagt auf einer festen Terminierungseinheit) zu terminieren, damit die E/A-Platine kann leicht entfernt werden). Tatsächlich ist Universal-I/O im Bereich von 55 – 140 I/O pro m im Vergleich zu 400 – 500 I/O pro m deutlich weniger dicht als feste I/O und benötigt daher viel mehr Platz als feste I/O.
Ist Universal I/O kostengünstiger?
Sicherlich ist ein dediziertes festes E/A-Modul mit hoher Dichte kostengünstiger als eine universelle Lösung, bei der jeder E/A-Typ eingebaut oder kanalweise ausgewählt werden muss? Hinzu kommen die Kosteneinsparungen für die Anlagenverkabelung, wenn dedizierte I/Os entfernt in der Nähe der Prozesseinheit verwendet werden und der reduzierte Platzbedarf – das muss ein Gewinner sein!!
Natürlich ist auch ein System, das dedizierte I/O mit hoher Dichte mit den späten Binding-Fähigkeiten von Universal I/O kombiniert, ein starkes Argument. Dies kann erreicht werden, wenn in letzter Minute mehrkanalige Module auf eine generische Backplane gesteckt werden, ohne dass die bereits terminierte Anlagenverkabelung beeinträchtigt wird.
Die Siemens ET200SP HA I/O zum Beispiel kann bis zu 896 Signale in einem Standardschrank verarbeiten und die Einheiten sind modular aufgebaut, sodass bei Bedarf die erforderliche I/O- und Terminierungsart auf eine universelle Backplane gesteckt werden kann. Hinzu kommt, dass die Verwendung der konfigurierbaren Karte (16 Signale wählbar AI/DI/DO pro Kanal) für die letzten 10 % bei Änderungen vielleicht das ultimative Allheilmittel für späte Bindung, Kosteneffizienz und Platz ist.
Beispiel Direktanschlussschrank 56 E/A-Module, bis zu 896 E/A 800 x 2000 mm (Breite x Höhe)
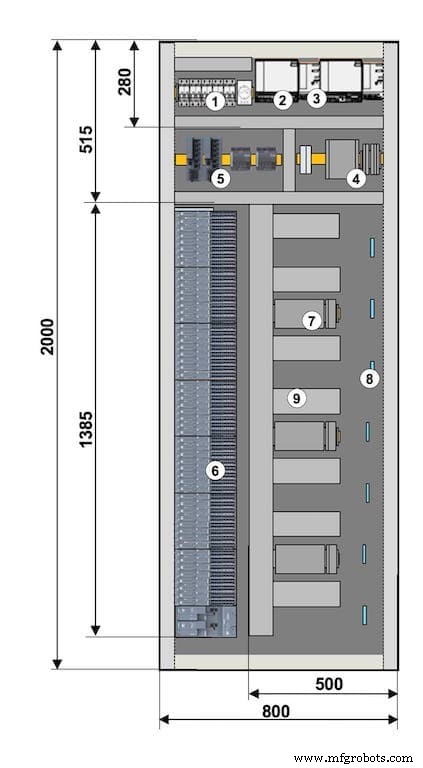
Funktionen:
- Einseitiger Zugang, 400 mm tief
- Gehäuseumgebungstemperatur -20..+40°C
- 120/230V AC redundante Stromeinspeisung
- Direktanschluss bis 2,5mm²
- PROFINET-Kommunikation über Kupfer- oder Glasfaserkabel
- Bis zu 56 Feldkabel (20 mm Durchmesser)
1 - Einspeisung MCB und RCB
2 - AC/DC SITOP Netzteil 8200 40A(Siemens, 6EP3334-8SB00-0AY0)
3 - Redundanzmodul SITOP PSE202U (Siemens, 6EP1961-3BA21)
4 - Stromverteilung und Patronensicherung
5 - hinzufügen. HW, z.B. SCALANCE XC206-2-SFP (Siemens, 6GK5 206-2Bs00-2AC2)
6 - T 200SP HA mit Interfacemodul und Busadapter
7 - Ersatzkabel und M-(Masse-)Klemmen
8 - Profil zur Kabelfixierung und Abschirmung
9 - Kabelkanal
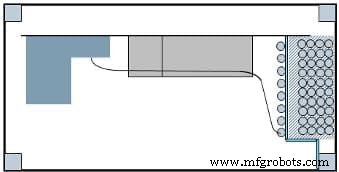
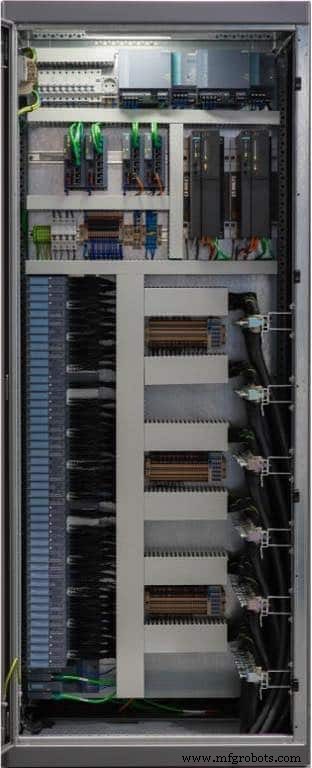
Engineering Contractors (EPCs) bevorzugen Late Binding I/O!
EPCs bevorzugen eine späte Bindung, da sie die I/O sehr spät im Projektlebenszyklus spezifizieren können. Es ist seit langem bekannt, dass die Instrumentierung abgeschlossen ist, nachdem die Rohrleitungs-, Mechanik- und Prozesskonstruktion abgeschlossen ist und jede Änderung danach schließlich auf das Automatisierungssystem durchdringt.
Universal I/O ist natürlich nicht alles, das DCS muss konfigurierbar sein, damit die Software I/O-Punkte generisch und nicht speziell Rack-Modul-Kanal anspricht. Dadurch kann die Anwendungssoftware vom Hardware-Build entkoppelt und frühzeitig im Projekt entwickelt werden, bevor die I/O endgültig definiert wird.
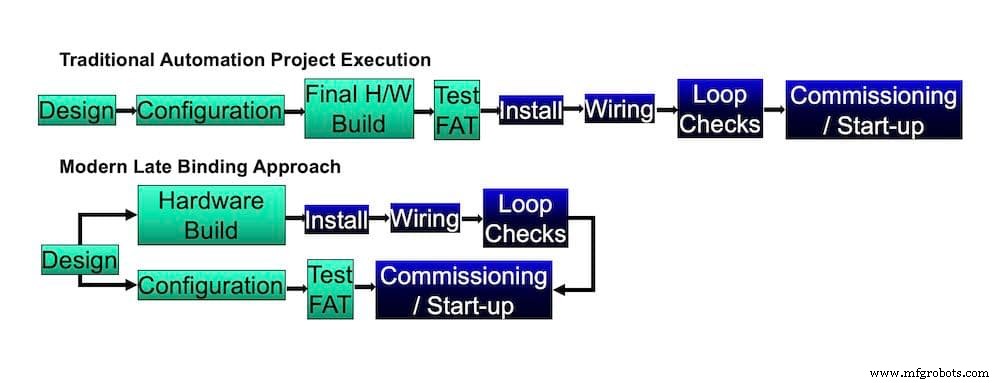
Ethernet ins Feld
Der Trend zu smarteren Instrumenten/Sensoren hat zur Initiative von Ethernet ins Feld geführt – zunächst als I/O-Bus zu dezentralen I/O-Stationen im Feld – ursprünglich PROFIBUS DP, dann mittlerweile PROFINET weit verbreitet. Dann eventuell zu Ethernet direkt zu den einzelnen Instrumenten/Sensoren. Dieser Trend wird sicherlich das Argument für Universal I/O schwächen.
Eine wirklich universelle Plug-and-Produce-Lösung
Ein Beispiel für eine wirklich universelle Plug-and-Produce-Lösung ist die Siemens Compact Field Unit (CFU), die PROFINET (bald Ethernet – APL™-Versionen) nutzt, um die Einheit entfernt in der Nähe des Prozesses zu verteilen und dann können bis zu 8 PROFIBUS PA-Instrumente angeschlossen werden angeschlossen und an jedem Port automatisch erkannt. Dies sorgt für Flexibilität, Vereinfachung und massive Einsparungen bei Anlagenverkabelung und Anschlussdosen etc. Dieses Gerät passt gut mit Ethernet in den Feldtrend und könnte eine Renaissance für Profibus PA-Instrumente hervorbringen.
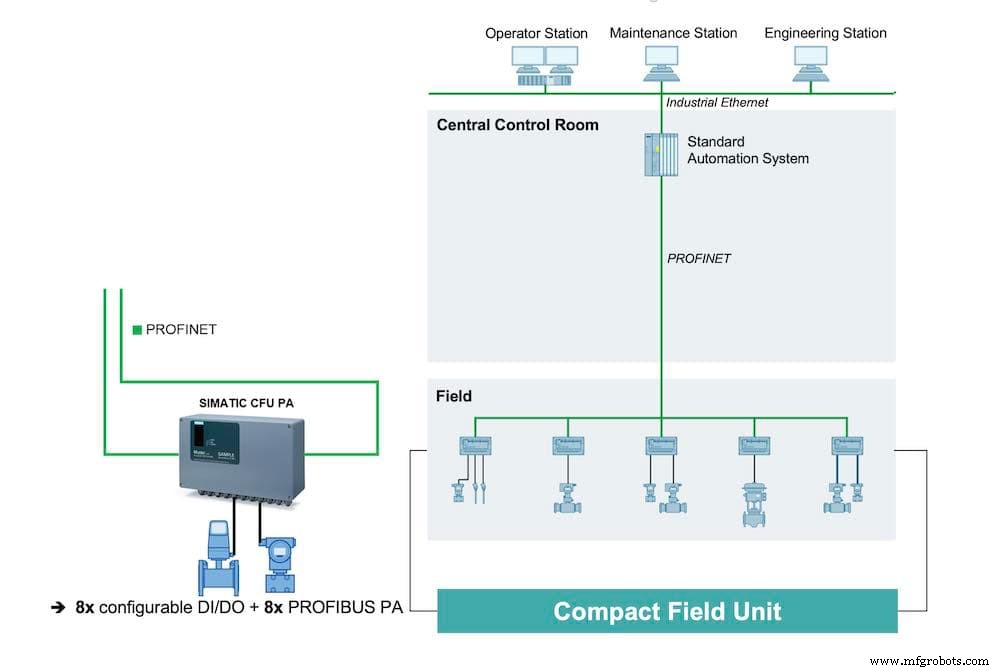
Von Instrumenten über Pakete bis hin zu MTP
Der Trend zu intelligenteren Instrumenten könnte als eigenständige Annäherung von Instrumenten an Pakete oder Module betrachtet werden. Tatsächlich sind NOA und MTP, die beide von NAMUR entwickelt wurden, komplementäre Lösungen. MTP ist für Greenfield-Installationen wichtiger, während NOA für bestehende Brownfield-Standorte zum Tragen kommt. Wenn NOA für Green Field-Anwendungen verwendet wird, würde es idealerweise OPC UA für die Kommunikation verwenden.
MTP Modular Automation und NOA NAMUR Open Architecture sind komplementär
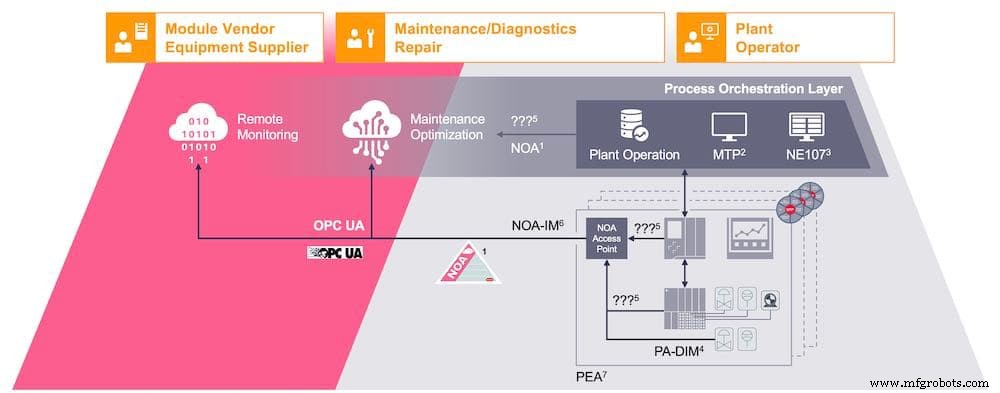
Schlussfolgerungen
- Es gibt einen historischen Trend zur Dezentralisierung von I/O-Stationen, jedoch stehen der Rückgang bei Feldbussen und der Anstieg der universellen I/O diesem Trend entgegen. Während das anhaltende Wachstum von Remote I/O und Ethernet in die Feldinitiative beweist, dass dieser Dezentralisierungstrend immer noch gültig ist.
- Feldbusse, insbesondere Foundation Fieldbus, gehen aufgrund technischer Kompetenz und historischer Probleminstallationen zurück.
- PROFIBUS ist nach wie vor beliebt, da es außerhalb von Öl und Gas eingesetzt wird, sich zu einem Defacto-Standard für die Kommunikation in elektrischen Systemen entwickelt hat und viele Hersteller PROFIBUS DP und jetzt PROFINET als E/A-Bus verwenden.
- EPCs bevorzugen spät bindende I/O-Lösungen, da sie die I/O in der letzten Minute im Projektlebenszyklus definieren können, die Lieferungen von Automatisierungssystemen reduziert werden und die Anlagenverkabelung früher installiert und abgeschlossen werden kann.
- Dedizierte E/A-Lösungen mit hoher Dichte können kostengünstiger und platzsparender sein, insbesondere wenn sie remote verwendet werden, um Anlagenverkabelung zu sparen. Dedizierte feste E/A-Systeme haben eine Dichte von bis zu ca. 470 E/A pro m, wohingegen universelle E/A nur etwa 55 E/A pro m betragen können.
- In der Praxis ist es wahrscheinlich, dass feste Remote-I/O-Systeme mit hoher Dichte, universelle I/O, NOA und Ethernet – APL™ alle für einige Zeit nebeneinander existieren und in bestimmten Bereichen bevorzugt werden. Aber wird sich eine Strategie durchsetzen? Nur die Zeit wird es zeigen – bleib für eine interessante Fahrt hier!!
Automatisierungssteuerung System
- C Eingang Ausgang (E/A)
- Python-Datei-I/O
- C - Datei-E/A
- Zukünftige Trends in der Luft- und Raumfahrtautomatisierung
- C# - Datei-E/A
- Panasonic bringt neue Fabrikautomatisierungssysteme auf den Markt
- Vorteile und Trends der ERP-Automatisierung
- Aktuelle Trends bei automatisierten Fertigungslinien
- Top-Trends zur Geschäftsautomatisierung
- Ist es möglich, Prozessautomatisierung zum Bewerben von Instagram zu verwenden?