Fünf-Achsen-Maschinen von Matsuura verleihen der Werkstatt unbeaufsichtigte Kapazität
Seit seiner Gründung im Jahr 2001 in Palästina, Illinois, wurde das Luft- und Raumfahrttechnikunternehmen Flying S mit der Absicht gegründet, qualitativ hochwertige Teile zu bauen. Als die von ihnen hergestellten fünfachsigen Teile immer komplizierter wurden, wurde klar, dass eine größere Maschinenleistung erforderlich war, um einen zuverlässigen unbeaufsichtigten Betrieb zu erreichen.
„Viele unserer Raumausstattungen erfordern Merkmale mit engen Toleranzen“, sagt Fertigungsingenieur Peter Bowman. „Unser Mangel an zuverlässiger Positionsgenauigkeit und Wiederholbarkeit aufgrund von Wärmeausdehnung oder anderen Variablen hat unsere Bemühungen, konstant ein gutes erstes Teil und nachfolgende Teile danach herzustellen, wirklich beeinträchtigt.“
Aber als die Anforderungen an die Werkstatt wuchsen und die Erwartungen an den lang gehegten Einschichtplan blieben, begann Flying S mit der Suche nach einer neuen Mehrachsentechnologie. Matsuura erregte die Aufmerksamkeit des Shops, und frühere positive Erfahrungen mit seinem lokalen Distributor Yamazen gaben dem Shop das Vertrauen, die fünfachsigen MX-520 PC4 und MX-850 PC4 von Matsuura zu kaufen.
Bessere Teile, weniger Aufwand
Diese Maschinen erwiesen sich schnell als gut geeignet für die Bedürfnisse von Flying S. Mehrere Paletten ermöglichten einen unbeaufsichtigten Betrieb mit großer Prozesszuverlässigkeit, das Werkstattpersonal war bereits mit der FANUC-Steuerung vertraut, die Maschinen boten eine Wiederholgenauigkeit von 0,000039 Zoll, und die Wiederholgenauigkeit jeder Rotationsachse A/C beträgt ±2 Bogensekunden, was für große Anlagen wichtig ist Werkstückherstellung.
Yamazen schulte die Werkstattingenieure in CAMplete und Maschinenfunktionen und unterstützt die neuen Matsuura-Maschinen von Flying S weiterhin bei Bedarf per Telefon und E-Mail.
Flying S ließ seinen Standard-Genauigkeitstestblock, der mehrere sich kreuzende fünfachsige Bohrungen umfasst, auf dem MX-520 laufen und war beeindruckt von der nahezu perfekten Genauigkeit des Teils. „Wir waren auch von der Spindelbetriebszeit beeindruckt, die wir erreichen konnten, und wir begannen innerhalb der ersten Woche nach der Installation mit dem Betrieb von 24-Stunden-Schichten“, sagt Bowman.
Da die Matsuura-Maschinen das erste Teil viel schneller und mit viel weniger Aufwand als in der Vergangenheit fertigstellten, bestand die nächste Herausforderung für die Werkstatt darin, einen neu geschaffenen Engpass in der Inspektionsabteilung zu beheben. Flying S musste die Größe dieser Abteilung physisch erweitern, um die endgültige Teileinspektion aufgrund des Volumens der von den Matsuura-Maschinen produzierten Teile zu ermöglichen.
Teileproduktivität und -qualität
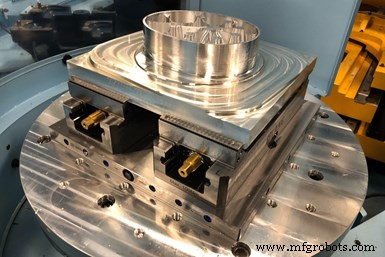
In den ersten sechs Betriebsmonaten fertigte Flying S 533 Teile auf dem MX-520 und 144 auf dem MX-850, was einer Gesamtlaufzeit von 5.187 Stunden mit nur zwei Maschinisten entspricht. Das ist ungefähr die gleiche Leistung wie vier ihrer anderen Fünf-Achs-Bearbeitungszentren, die im gleichen Zeitraum von drei bis vier Maschinenbedienern bedient werden. Um die Fähigkeit der Matsuuras zu veranschaulichen, eine High-Mix-, Low-Volume-Produktion mit der richtigen Planung und Ausführung zu bewältigen, hebt Flying S die Errungenschaften des MX-520 hervor. Wenn man 533 Teile mit einer durchschnittlichen Losgröße von sieben einbezieht, bedeutet dies, dass 75 Rüstvorgänge zum ersten Teil gingen, während die Spindelbetriebszeit zu 75 % aufrechterhalten wurde.
Flying S berichtete auch, dass eine Matsuura-Maschine in einem Zeitraum von sieben Monaten mehr Spindelstunden produzierte als die anderen fünfachsigen Maschinen, die sie seit fünf Jahren besaßen.
Bei schwierigeren Teilen würde ein typisches Fünf-Achsen-Setup für das erste Teil erfordern, dass ein erstes Teil auf Versätze geprüft wird, und dann hätte ein zweites Teil eine 50-prozentige Chance, korrekt zu sein. Nachfolgende Teile würden mit einer Wahrscheinlichkeit von 80-90 % während des gesamten Prozesses fehlerfrei bleiben. Dieser langwierige Prozess verbrauchte viele Arbeitsstunden und engte Inspektionsressourcen ein. Zwischen den Matsuura-Maschinen fertigte Flying S 677 Teile mit einer durchschnittlichen Losgröße von sieben, was ungefähr 100 Einstellungen für das erste Teil bedeutete. Kurz gesagt, die Werkstatt hat bei der Bearbeitung mit den Matsuuras in über 90 % der Fälle beim ersten Versuch eine Erstteilintegrität erreicht. Seit der Installation wurde bei keinem Matsuura ein einziges Teil aufgrund eines maschinenbezogenen Fehlers verschrottet.
Auswirkung
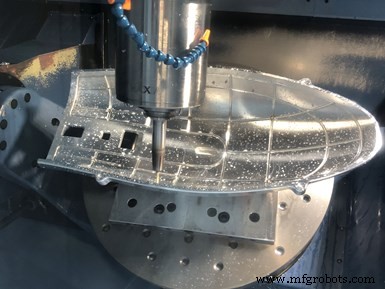
Vieles von dem, was Flying S herstellt, kann nicht für die ITAR-Konformität nachgewiesen werden, aber auch Formen und Vorrichtungen für Verbundwerkstoffarbeiten werden oft auf ihren Matsuuras hergestellt.
Aufgrund fehlender Palettierung konnte Flying S die fünfachsigen Wettbewerbsmaschinen des Unternehmens nicht für zusätzliche Rüstvorgänge anderer Teile während der Inspektion des ersten Teils verwenden. Außerdem mussten alle Werkzeuge jedes Mal neu gebaut und in diese Maschinen geladen werden.
Die Matsuura-Maschinen haben normalerweise zwei oder drei verschiedene erste Teile, die gleichzeitig von derselben Maschine inspiziert werden. Die Maschinen verfügen über zusätzliche Werkzeugwechslerkapazitäten, die mit den Werkzeugbibliotheken von Flying S gut funktionierten. Flying S nutzte auch die Nullpunkt-Werkstückspannung von Lang und kombinierte sie mit der Genauigkeit der Palettenlokalisierungsfunktion, um das Prüfen von Teilen unnötig zu machen.
Werkstattleiter Ben Parish äußert sich besonders positiv über die Matsuura MX-520 PC4 und MX-850 PC4. Er freut sich darüber, „dass er sich im Wesentlichen keine Gedanken über die Positionsgenauigkeit, Wiederholbarkeit oder Konsistenz der Maschine machen muss, wodurch einige der besorgniserregendsten Risiken bei der Herstellung fehlerhafter Produkte beseitigt werden.“ Er lobt auch die Steuerungsschnittstelle von Matsuura und stellt fest, dass sie die Option für eine traditionelle FANUC-Schnittstelle für Bediener bietet, die Erfahrung mit dieser Schnittstelle haben und sie bevorzugen.
„CAMplete ist ein echter Komfort“, fügt Parish hinzu. „Die Kombination aus Maschinendefinition/Postprozessor/NC-Code-Überprüfungssoftware trägt dazu bei, potenzielle Probleme und Kollisionen weiter zu eliminieren. Es bietet auch die Möglichkeit, den Stift anzupassen und eine Werkzeugwegverfeinerung einzubeziehen, um die Schnittqualität zu verbessern und gleichzeitig die Genauigkeit der Merkmale und die Oberflächenqualität zu verbessern.“
Automatisierungssteuerung System
- Boy Machines zeigt sein volles Angebot in Orlando
- Negri Bossi bringt neue Generation vollelektrischer Maschinen auf den Markt
- Bright Machines startet „erste softwaredefinierte Mikrofabrik“
- Bright Machines führt „Microfactory-as-a-Service“ ein
- Steuerungssystemintegration
- Ein Fünf-Achsen-Prozess, 10 Automatisierungselemente
- Die Evolution medizinischer Geräte
- Esprit Automation:Britischer Hersteller von Schneidemaschinen
- Shop verbessert sich kontinuierlich durch die Einführung von Rundtaktmaschinen
- Arbeiten mit Inhouse-Integrationssystemen