Roboter, Werkstattpersonal zusammenarbeiten, Synergie und Sicherheit maximieren
Effiziente Fertigung erfordert aufeinander abgestimmte Systeme aus Werkstattpersonal, Ausrüstung und Software. Diese Systeme umfassen zunehmend Robotertechnologie, da Hersteller die Zuverlässigkeit, Wiederholbarkeit und Flexibilität erkennen, die Roboter bieten. Laut der International Federation of Robotics wird die Zahl der weltweit im Einsatz befindlichen Industrieroboter bis 2019 auf rund 2,6 Millionen steigen, rund eine Million mehr als 2015. Etwa 70 % der Industrieroboter werden in den Branchen Automotive, Elektro/Elektronik und Metall eingesetzt und Maschinenindustrie.
Sicherheit steht bei jedem Herstellungsvorgang an erster Stelle; Der sichere Einsatz von Industrierobotern erfordert traditionell die Einhaltung festgelegter Abstände zwischen Werkstattpersonal und Robotern sowie die Positionierung von Schutzvorrichtungen und Käfigen um die Roboter herum, um Verletzungen der Arbeiter zu vermeiden. Eine wachsende Auswahl an Robotern, Software und Implementierungsstrategien zielt auf eine engere und produktivere Interaktion zwischen Mensch und Roboter ab.
Die Kontrolle dieser Beziehung reicht von der sensorgesteuerten Unterbrechung der Bewegung eines Roboters, wenn sich Arbeiter in potenziell gefährliche Bereiche begeben, bis hin zum Einsatz von vollständig „kollaborativen“ Robotern, auch Cobots genannt, die so konstruiert sind, dass sie Seite an Seite mit menschlichen Arbeitern sicher arbeiten. Unterschiedliche Formen der Zusammenarbeit ermöglichen es Herstellern, die vollen Möglichkeiten von Robotersystemen und Werkstattpersonal zu nutzen.
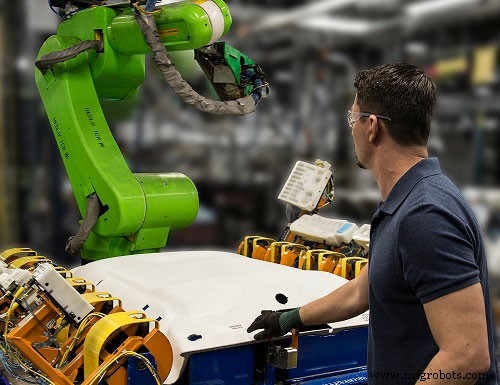
Das Dumpfe, Gefährliche und Schmutzige
Der aktuelle Fachkräftemangel in den USA treibt einen Großteil der Nachfrage nach kollaborativen Robotern voran. Die Pensionierung von erfahrenem Ladenpersonal und nicht genügend jüngere Mitarbeiter, die in die Fertigungsbelegschaft eintreten, haben den Ladenbesitzern Personalengpässe beschert.
Um diese Qualifikationslücke zu schließen, verwenden Hersteller Roboter für sich wiederholende und/oder gefährliche Vorgänge und versetzen Arbeiter in Jobs, die mehr Nachdenken und Fähigkeiten erfordern. „Wir beobachten, dass Mitarbeiter neu zugewiesen werden“, sagte Craig Tomita, Vertriebsleiter für die westliche Region bei Universal Robots USA Inc. (Ann Arbor, MI), einem Hersteller von vollständig kollaborativen Robotern.
Laut Tomita ist die Implementierung von kollaborativen Robotern relativ einfach, da sie in einer menschengerechten Umgebung arbeiten und nicht die Schutzvorrichtungen erfordern, die bei herkömmlichen Industrierobotern erforderlich sind. Eine Umgestaltung des Shopfloors ist nicht erforderlich und die Raumnutzung ändert sich nicht. „Sie platzieren kollaborative Roboter einfach dort, wo menschliche Bediener derzeit die Arbeit erledigen“, sagte er und fügte hinzu, dass kollaborative Roboter zwar sicher sind, die Risikobewertung – die Bestimmung aller potenziellen Gefahren in einem System und das Finden von Wegen, sie zu mindern – jedoch von entscheidender Bedeutung ist.
Benutzerfreundlichkeit ist ein Schlüsselmerkmal von vollständig kollaborativen Robotern. Obwohl die Fähigkeiten kleiner kollaborativer Roboter denen kleiner traditioneller Roboter ebenbürtig sind, sind die Anforderungen an kollaboratives Training und Programmierung minimal. „Die einfache Programmierung im UR-System ist ein Wendepunkt“, sagte Tomita. „Wenn beispielsweise ein Roboter in ein größeres Fertigungssystem integriert werden muss, können die Einheiten von Universal über einen tragbaren Touchscreen programmiert und betrieben werden. Bei Bedarf können übergeordnete Benutzer den Roboter auch mit seiner Python-ähnlichen Skriptsprache programmieren.“
Kollaborative Roboter können problemlos von kleineren Geschäften eingesetzt werden, in denen Integrationskosten eine Eintrittsbarriere waren. „Wenn Sie es wie einen Eisberg betrachten, ragt der Roboterteil aus dem Wasser“, sagte Tomita. „Der Integrationsprozess ist das, was unten ist. Man nimmt den Eisberg als Ganzes und es wird richtig teuer. Ein kollaborativer Roboter kostet ungefähr so viel wie ein Standard-Industrieroboter, aber die Integrationskosten sind viel geringer“, sagte er.
Der Einsatz von Robotern kann auch dazu beitragen, die Arbeitskosten zu senken, sagte Tomita:„Unternehmen, die kollaborative Roboter einsetzen, können oft Aufträge anbieten, die sie vorher nicht machen konnten, weil ihre Arbeitskosten außerhalb des Stadions lagen.“
Mögliche Anwendungen sind weit offen. „An Anzahl und Art der Anwendungen für unsere kollaborativen Roboter muss noch gedacht werden“, sagte Tomita. „Die Leute sind so daran gewöhnt zu denken, dass der Roboter dort drüben hinter einem Käfig ist, die Menschen hier drüben, und die beiden werden sich niemals treffen. Das ändert sich.“
Universal Robots bietet drei Modelle von sechsachsigen kollaborativen Robotern an, von UR3-Einheiten, die Nutzlasten von bis zu 3,3 kg (7,26 lb) handhaben und einen Arbeitsradius von 500 mm (19,7″) haben, bis hin zu UR10-Robotern mit einem 10-kg (22- lb) Nutzlast und Arbeitsradius von 1300 mm (51,2″).
Ein typischer Kunde von Universal Robots ist CleanLogix LLC (Santa Clarita, CA), das Produkte entwickelt, die CO2 für Reinigung, Kühlung und andere Anwendungen verwenden. CleanLogix-Präsident David Jackson sagte:„Wir können Sprühnebel in eine Schneidzone sprühen und ein sehr sauberes und umweltfreundliches Mittel zum Kühlen eines Schneidwerkzeugs in einem Prozess bereitstellen.“ Er stellte fest, dass ein einzelner Roboter verschiedene Aufgaben ausführen kann; zum Beispiel das Platzieren eines Teils in einem Bearbeitungszentrum und das anschließende Wechseln des Endeffektor-Werkzeugs, um Kühlmittel bereitzustellen. „Sie haben also einen Multitasking-Roboter und eine insgesamt grüne, schlanke Lösung. Wir freuen uns sehr über diese Small-Form-Factor-Roboter.“
Die Fähigkeit von kollaborativen Robotern, sicher mit Menschen zusammenzuarbeiten, ermöglicht es, den Betrieb so zu organisieren, dass Synergien maximiert werden; Beispielsweise kann ein Roboter eine Reihe von Komponenten zusammenbauen, während ein menschlicher Arbeiter winzige Drähte einführt, die Geschicklichkeit und kognitive Wahrnehmung erfordern. Roboter sind ideal für Vorgänge, die Wiederholung, Zuverlässigkeit und Genauigkeit erfordern, einschließlich Verpackung, Palettierung, Montage und Pick-and-Place-Vorgänge.
Wiederholbarkeit und Genauigkeit sind separate, aber verwandte Messungen der Roboterleistung. Die Wiederholbarkeit ist ein Maß für die Fähigkeit eines Roboters, immer wieder zu einer bestimmten Position zurückzukehren. Die behauptete Wiederholbarkeit verschiedener kollaborativer Roboter liegt im Bereich von etwa ±0,02 bis ±0,1 mm (0,0008 bis 0,004″) oder darunter.
Die Genauigkeit hingegen misst, wie nahe sich ein Roboter an eine gewünschte Position oder einen gewünschten Pfad bewegen kann, und kann als Positionsgenauigkeit und Pfadgenauigkeit kategorisiert werden. Aufgaben wie Bohren, bei denen der Roboter eine Position anfährt und anhält, während das Loch gebohrt wird, erfordern Positionsgenauigkeit. Pfadgenauigkeit ist für Prozesse wie Laserschneiden oder Lackieren erforderlich, bei denen der Prozess stattfindet, während sich der Roboter zwischen Punkten bewegt.
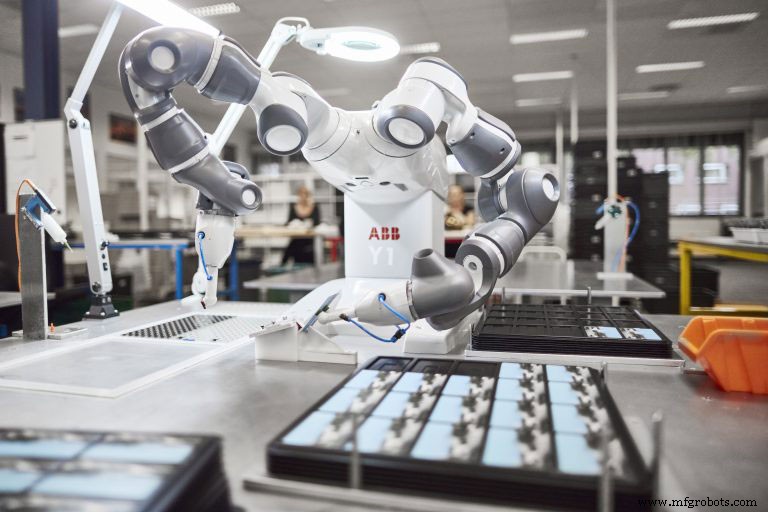
Anwendung bestimmt Zusammenarbeit
Im Allgemeinen wird die Aktivität von Werkstattpersonal und Robotern Seite an Seite mit kollaborativen Robotern erreicht, die kleine Nutzlasten bei langsamen Geschwindigkeiten handhaben – typischerweise in der Nähe von 1 m/s (39,4 ips). Allerdings, so Nicolas De Keijser, Geschäftsbereichsleiter Montage und Test der Robotics and Motion Division von ABB Inc. (Cary, NC), garantieren die Last, die ein Roboter trägt, oder die Geschwindigkeit, mit der er sich fortbewegt, noch keinen sicheren, kooperativen Betrieb . Eine sehr leichte, aber gefährliche Nutzlast könnte eine Rasierklinge oder eine Injektionsnadel sein. Eine sich langsam bewegende, aber schwere Nutzlast könnte eine Quetschgefahr für das Fertigungspersonal darstellen. Ebenso könnte ein Greiferausfall beim Bewegen einer mittelgroßen Nutzlast mit mäßiger Geschwindigkeit dazu führen, dass die Nutzlast durch die Werkstatt geschleudert wird.
Ein Robotersystem ist nur relativ zu seiner Anwendung kollaborativ. „Wenn die Operation gefährlich ist, möchten Sie nicht in der Nähe des Roboters sein, egal wie kollaborativ der Roboter ist“, sagte De Keijser und fügte hinzu, dass eine vollständige Sicherheitsbewertung der Lösung in jeder Anwendung erforderlich ist. „Wenn Sie die Standards lesen, diktieren sie immer, dass wir über einen kollaborativen Betrieb sprechen, nicht über einen kollaborativen Roboter.“
ABB verfolgt zwei Ansätze, um eine sichere Koexistenz von Arbeitern und Robotern zu gewährleisten. Wirklich kollaborative Anwendungen wie die Montage von Kleinteilen können im Allgemeinen vom tischmontierten, zweiarmigen YuMi-Roboter des Unternehmens erfüllt werden. Die Reichweite des 38 kg (84 lb) schweren Roboters beträgt 599 mm (24″) und die Nutzlast 500 kg (1,1 lb) pro Arm. Es nimmt einen Bereich in menschlicher Größe ein und arbeitet sicher neben dem Ladenpersonal.
Andererseits erleichtert ABB den sicheren Betrieb großer Standard-Industrieroboter durch redundante Systeme, die sorgfältige Programmierung und Sicherheitsüberwachungssoftware kombinieren. Nachdem ein Roboter für einen sicheren Betriebsbereich programmiert wurde, bietet die sicherheitszertifizierte Roboterüberwachungssoftware SafeMove2 von ABB redundanten Sicherheitsschutz durch Überwachung der Roboteraktivität, einschließlich sicherer Geschwindigkeitsgrenzen, Stillstandsüberwachung und Achsbereichen sowie Positions- und Ausrichtungsüberwachung. Die Software ist in die Robotersteuerung integriert und kann laut De Keijser Einrichtungszeit sparen und eine höhere Produktivität ermöglichen, während gleichzeitig die Gesamtinvestitionskosten gesenkt werden.
Das Kinetiq Teach-System von Yaskawa Motoman ist ein Beispiel für den Handführungsmodus der Mensch-Roboter-Interaktion, der in den ISO-Normen 10218-1 und 10218-2 beschrieben ist.
Eingebaute adaptive Steuerung
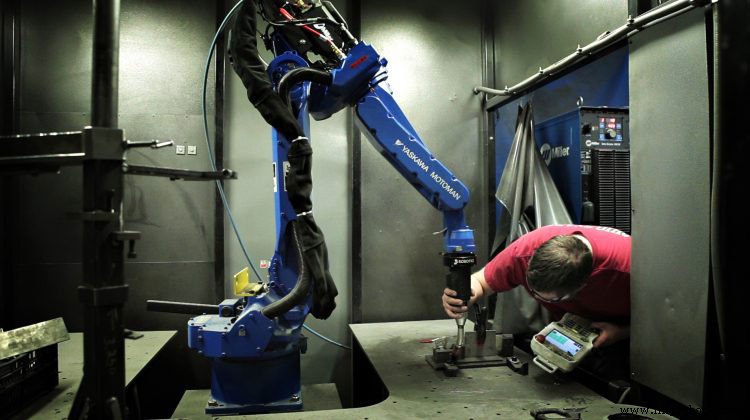
Eine andere Form der Roboterkollaboration kombiniert die Fähigkeiten und Erfahrungen eines Handwerkers mit der Fähigkeit eines Roboters, in gefährlichen Bereichen zu operieren. Schweißen ist im Allgemeinen kein benutzerfreundlicher Vorgang. Laut Zane Michael, Director of Thermal Business Development bei Yaskawa America Inc., Motoman Robotics Division (Miamisburg, OH):„Auf dem heutigen Markt bedeutet das Wort kollaborativ, dass sich ein Roboter- und ein Bedienerbereich überschneiden. Sie arbeiten eng zusammen. Ich habe noch nie gesehen, dass das Wort Zusammenarbeit in diesem Sinne auf die Schweißumgebung angewendet wird.“
Obwohl das Roboterschweißen nicht unbedingt als kollaborativ bezeichnet werden kann, unterstützt eine Form der Zusammenarbeit zwischen einem erfahrenen Schweißer und einem Roboter eine konsistente Leistung. Es ist nicht so, dass der Betrieb eines Schweißroboters übermäßig schwierig wäre. „Das Programmieren und Betreiben des Roboters ist einfach“, sagte Michael. „Bei Motoman haben wir ein System namens Kinetiq Teach, bei dem Sie die Taschenlampe greifen und den Roboter auf dem gewünschten Weg bewegen können, diesen Weg aufzeichnen und schon kann es losgehen.“ Er fügte jedoch hinzu, dass der Betrieb eines Schweißroboters ohne Schweißkenntnisse „ein harter Kampf“ sei, wenn episodische Schweißfehler wie Hinterschneidungen oder Durchbrennungen auftreten.
In diesen Fällen kann ein erfahrener Schweißer die Aktionen des Roboters anpassen, um die Probleme zu lösen. Adaptive Steuerungssysteme mit Lasern oder anderen Sensoren sind für die grundlegende Nahtverfolgung erhältlich, aber die meisten Schweißsysteme werden ohne solche Systeme ausgeliefert. „Der menschliche Schweißer hat, wie ich es nenne, eine eingebaute adaptive Steuerung“, sagte Michael.
Je nach betrieblicher Komplexität und Volumenfähigkeit besitzen Roboterzellen unterschiedliche Formen von Automatisierungs- und Sicherheitssystemen. Die ArcWorld C30-Einzelstationszelle von Motoman ist für die Einzelstückverarbeitung kleinerer Teile mit geringem Volumen vorgesehen. Wenn sich die Zellentür öffnet, damit ein Bediener ein Schweißteil auf den Positionierer in der Zelle laden kann, befindet sich der Roboter im Notstoppmodus. Nachdem der Bediener die Zelle verlassen hat, senkt sich die Tür und das Schweißen findet statt. Andererseits verfügen die großvolumigen Maschinen der Serie 6000 von Motoman für große Teile über einen Positionierer, der Teilehalterungen wie ein Riesenrad indexiert und von außerhalb der Zelle beladen werden kann, während mehrere Roboter eine Baugruppe im Inneren schweißen.
Schweißunternehmen sind mit einem ähnlichen Arbeitskräftemangel konfrontiert wie andere Fertigungssegmente. Basierend auf Statistiken des US Bureau of Labor schätzt die American Welding Society einen Schweißermangel von 290.000 in den USA bis 2020. Michael sagte, dass zukunftsorientierte Schweißzulieferer mit Berufsschulen und Karrierezentren zusammenarbeiten, um Lehrpläne für Schweißer zu erstellen. Zum Beispiel hat Motoman ein Schweiß-STEM-Programm und einen passenden Lehrplan für die Schweißausbildung sowohl in der High School als auch in der Erwachsenenbildung erstellt.
Roboter, das IoT
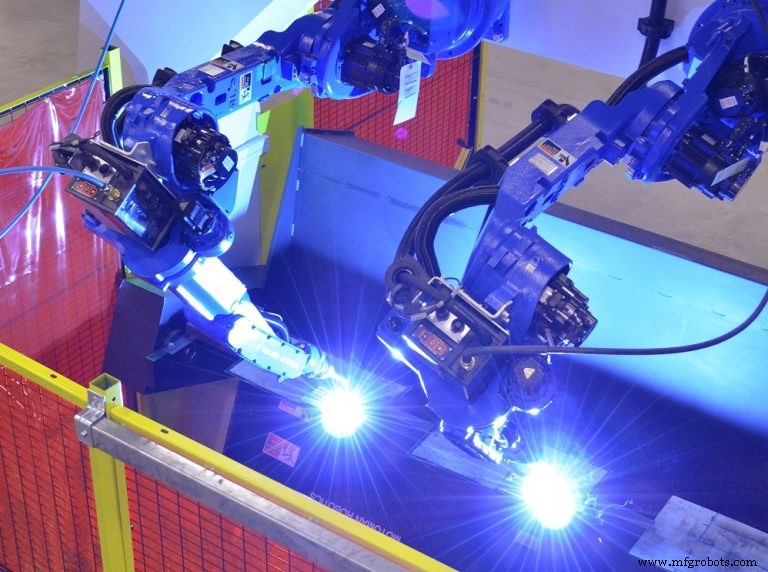
Cloud Computing und das Internet der Dinge erleichtern die Zusammenarbeit zwischen Robotern, Benutzern und Roboterherstellern. Hersteller überwachen routinemäßig die Betriebszeit der Roboter, um die Produktivität zu dokumentieren, sagte Mark Scherler, General Manager des Segments Materials Joining beim Roboterlieferanten FANUC America Corp. (Rochester Hills, MI):„Aber es gehört noch mehr dazu. Wir nutzen das Internet, um Daten von den Robotern zu sammeln und den Herstellern zu helfen, die Betriebszeit zu verbessern.“
FANUC bietet sowohl kollaborative als auch Standard-Industrieroboter an. Um die von den Robotern gesammelten Daten voll auszuschöpfen, hat das Unternehmen eine ZDT-Diagnoseanwendung (Zero Downtime) entwickelt, die kritische Informationen zum mechanischen Betriebs- und Wartungsstatus eines Roboters erkennt und analysiert. ZDT, das beispielsweise an Robotern in der Einrichtung eines Herstellers installiert ist, kann erkennen, dass ein Roboter zunehmende Drehmomentniveaus erfährt, die auf ein Problem mit einer bestimmten Achse hinweisen können. Über die Cloud-Technologie sendet die ZDT-Anwendung die Betriebsinformationen zur Analyse an das FANUC-Rechenzentrum. Kritische Probleme lösen beim Roboterbenutzer die Übertragung von Benachrichtigungen an bestimmte intelligente Geräte aus.
Gleichzeitig bestätigt FANUC die Verfügbarkeit von Teilen, die möglicherweise zur Behebung des Problems erforderlich sind. Die Daten können auch zur Optimierung von Robotersystemen im Hinblick auf die Verbesserung der Zykluszeit, die Reduzierung des Energieverbrauchs und die Verlängerung der Roboterlebensdauer durch bessere Wartung verwendet werden.
Automatisierungsflexibilität
Jeff Estes, östlicher Regionalverkaufsleiter für die Morris-South-Division der Morris Group (Charlotte, NC) und ehemaliger Direktor, Partner bei THINC für Okuma America Corp., sagte, die hochvolumige Automobilindustrie sei seit Jahrzehnten führend bei der Einführung der Automatisierung. Heutzutage suchen Hersteller kleinerer Stückzahlen nach der Zuverlässigkeit und Vorhersagbarkeit der Automatisierung, wollen aber auch die Flexibilität, um schnelle Umstellungen von einem Produktionslos auf ein anderes zu ermöglichen. Zu diesem Zweck ermöglicht die Robotertechnologie einem Geschäft, Programmierdetails und Endeffektoren schnell zu ändern.
Estes wies darauf hin, dass die Roboterautomatisierung einer Werkzeugmaschine nicht nur das Be- und Entladen von Teilen beinhaltet. „Der Schlüssel liegt darin, einen Betrieb mit geringer oder keiner Anwesenheit zu erreichen“, sagte er. In einer vollautomatisierten Zelle werden zahlreiche Elemente, darunter eine Werkzeugmaschine, ein Roboter, ein Messgerät, ein Bildverarbeitungssystem und Materialhandhabungsgeräte, zusammengeführt, um einen „geschlossenen Kreislauf zu schaffen, der ohne menschliche Interaktion weiterlaufen und grundlegende Entscheidungen treffen kann. “, sagte Estes. Die mehreren Elemente einer Zelle generieren Informationen über einzelne Vorgänge, aber „bis sie anfangen, miteinander zu arbeiten, sind das nur Informationen“. Ein Integrator wählt und ordnet Zellenelemente an und koordiniert ihre Funktionen.
Einige Werkzeugmaschinenlieferanten verfügen über interne Integrationsmöglichkeiten, um schlüsselfertige Systeme bereitzustellen. Methods Machine Tools Inc. (Sudbury, MA) beschäftigt mehr als 30 Automatisierungsingenieure in den USA sowie Personal für Konstruktion, Steuerung, Elektrik/Mechanik, Systemintegration und Außendienst/Installation. Als Ergänzung zu seinen Aktivitäten als Anbieter von Werkzeugmaschinen und Systemintegratoren hat Methods kürzlich ein Automatisierungs- und Integrationszentrum in seinem Werk in Charlotte, NC, eingerichtet. Automatisierungsspezialisten und Systemintegrationsingenieure bieten Kunden Beratung in Bezug auf Ausrüstung und Fähigkeiten, die von der Definition und dem Bau von Zellen bis hin zur Durchführung von Abflüssen reichen. Der Schwerpunkt der neuen 10.000 ft2 (929 m2) großen Anlage „liegt auf der Bereitstellung einer maßgeschneiderten, umfassenden Lösung für unsere Kunden“, sagte Methods Automation Manager John Lucier.
Ganzheitliche Automatisierung
Technologien wie kollaborative Roboter verändern die Art und Weise, wie Hersteller über Automatisierung denken. Estes ermutigt Hersteller, die Leistungsfähigkeit der von einem Automatisierungssystem generierten und gesammelten Daten zu nutzen.
Die Datenanalyse kann zu anderen Aspekten der Produktion beitragen, einschließlich Produktqualität, Werkzeugmanagement, Materialfluss und Logistik. Bei der Implementierung von Robotertechnologie sollten Hersteller „eher einen ganzheitlichen Ansatz verfolgen“, sagte Estes. „Anstatt einer Person nur das Be- und Entladen einer Maschine zu ersparen, sollte ein Hersteller fragen:‚Kann ich mit diesem Roboter noch etwas tun, um ihn auch IOT- oder Industrie 4.0-bezogen zu machen?'“ Roboter und Automatisierungssysteme wurden nicht gewürdigt Fähigkeiten, sagte er:„Auch wir als OEM-Anbieter lernen jeden Tag, wie viel leistungsfähiger wir sie machen können.“
Was macht einen Roboter kollaborativ?
Der Begriff „kollaborative Robotik“ wird häufig verwendet, um jede Situation zu beschreiben, in der Roboteraktionen gesteuert werden, um menschlichen Arbeitern entgegenzukommen. In Wirklichkeit variieren die möglichen Beziehungen zwischen Arbeitern und Robotern stark je nach Roboter und Anwendung.
2011 wurden die ISO-Normen 10218-1 und 10218-2 „Safety Standards for Applications of Industrial Robots“ veröffentlicht. Sie listen Anforderungen an die sichere Konstruktion, Schutzmaßnahmen und Anwendung von Industrierobotern auf. Die Standards definieren vier verschiedene Arten der sicherheitsbezogenen Interaktion zwischen Ladenpersonal und Robotern.
Ein Modus ist die Fähigkeit, einen sicherheitsüberwachten Stopp durchzuführen. Sensoren überwachen einen vorbestimmten Bereich um einen Roboter herum, und die Bewegung des Roboters stoppt, wenn ein Mensch diesen Bereich betritt. Dieses Niveau der Sicherheitsüberwachung ist zufriedenstellend, wenn der menschliche Eingriff minimal ist, obwohl häufige Unterbrechungen die Produktivität verringern können. Ein zweiter Modus umfasst Handführung, bei der ein Bediener einem Roboter beibringt, einem gewünschten Weg zu folgen, indem er den Roboterarm ergreift und ihn zu gewünschten Punkten auf dem Weg bewegt, während er die Punkte mit einem Programmierhandgerät aufzeichnet. Ein Kraft-Momenten-Sensor im Roboter erkennt die manuelle Führung des Bedieners. Der Sensor fungiert nicht als Sicherheitssystem und außerhalb des Lernmodus muss der Roboter über andere Geräte oder Systeme verfügen, um eine sichere Interaktion mit Menschen zu gewährleisten.
Im Geschwindigkeits- und Abstandsüberwachungsmodus erkennt ein optisches System Menschen in einer ausgewiesenen Sicherheitszone um den Roboter herum. Wenn der Abstand zwischen dem Roboter und dem Menschen abnimmt, wird der Roboter allmählich langsamer; Bei einer bestimmten Entfernung stoppt die Roboterbewegung. Wenn der Mensch dann die Sicherheitszone verlässt, nimmt der Roboter seine Arbeit mit normaler Geschwindigkeit wieder auf. Dieser abgestufte Sicherheitsmodus trägt dazu bei, die Produktivität auch bei Arbeitereingriffen aufrechtzuerhalten.
Der vierte Kollaborationsmodus ermöglicht die Seite-an-Seite-Aktivität von Robotern und Menschen und eliminiert die Notwendigkeit von Schutzgittern und Käfigen. Die beschriebenen Roboter werden leistungs- und kraftbegrenzende Roboter genannt. Wenn Sensoren ungewöhnliche Kräfte auf den Roboter erkennen, wie sie beispielsweise durch Kontakt mit einem Arbeiter entstehen, wird der Roboter sofort langsamer, stoppt oder fährt rückwärts. Diese beschriebenen Roboter werden leistungs- und kraftbegrenzende Roboter genannt. Wenn Sensoren ungewöhnliche Kräfte auf den Roboter erkennen, wie sie beispielsweise durch Kontakt mit einem Arbeiter ausgeübt werden, wird der Roboter sofort langsamer, stoppt oder fährt rückwärts. Diese Roboter sind im Allgemeinen kleiner und weniger leistungsstark als herkömmliche Industrieroboter und haben außerdem abgerundete Formen und geschlossene Gelenke, um Quetschverletzungen zu vermeiden.
Im Jahr 2016 veröffentlichte die ISO die technische Spezifikation ISO/TS 15066, die die ISO-Normen 10281-1 und 2 um Details und Erläuterungen ergänzt. TS 15066 definiert kollaborative Roboter als solche, die für die direkte Interaktion mit einem Menschen in einem kollaborativen Arbeitsbereich entwickelt wurden, in dem Mensch und Roboter arbeiten können Aufgaben gleichzeitig. Die Spezifikation gibt an, wie viel Kraft ein Roboter auf einen Menschen ausüben kann, ohne Schmerzen oder Verletzungen zu verursachen. Die Kraftniveaus wurden durch Schlagversuche an bestimmten Stellen des menschlichen Körpers ermittelt. Dennoch ist es wichtig, Risikobewertungen des durchgeführten Vorgangs und der Teile und Werkzeuge durchzuführen, die an einer bestimmten Anwendung beteiligt sind, um absolute Sicherheit zu gewährleisten.
Automatisierungssteuerung System
- Kollaborative Roboter:Auf dem Weg zum Mainstream?
- Neue Roboter:wirtschaftlich und erstklassig
- Kollaborative Roboter und ihr Einfluss auf die Fertigung
- Mit kollaborativen Robotern arbeiten und wachsen
- Notstopp und Stoppsteuerung
- Warum einen kollaborativen Roboter verwenden?
- Cobots und Fertigung:3 Möglichkeiten, wie kollaborative Automatisierung Ihrem Geschäft helfen kann
- Cobots und die Zukunft fortschrittlicher Robotik in der Fertigung
- Die Zukunft des Testens:Automatisierung und kollaborative Roboter
- Was sind Cobots (kollaborative Roboter)?