Sensorbasierte Steuerung von Schneidwerkzeugen, Werkzeugmaschinen bewegen sich vom Reißbrett zum Mainstream
Ein wesentlicher Erfolgsfaktor für Initiativen zu Industrie 4.0 und IIoT (Industrial Internet of Things) ist das Aufkommen von mehr und besseren Sensoren in Bearbeitungszentren und sogar in den Schneidwerkzeugen selbst. Diese Sensoren liefern die Daten und Konnektivität, die die Grundlage für die „Fabrik der Zukunft“ bilden.
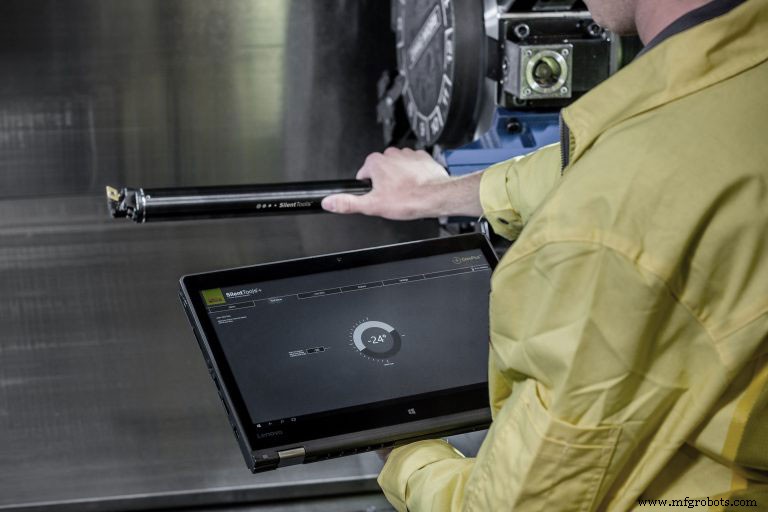
Aber weit davon entfernt, futuristisch zu sein, gibt es heute eine Reihe von „intelligenten Sensoren“, die Daten sammeln und den Bedienern den Zustand ihrer Maschinen und des Metallzerspanungsprozesses anzeigen. Die Evolution wird durch immer genauere Messung der Position des Teils und der geometrischen Form des fertigen Teils sowie der Konfiguration und Steuerung der im Prozess verwendeten Werkzeuge erreicht.
Manufacturing Engineering hat eine Reihe von Branchenexperten gebeten, den aktuellen Stand von sensorbasierten Schneidsteuerungssystemen zu bewerten und auch in die Kristallkugel zu blicken, um zukünftige Möglichkeiten zu erkennen.
Jetzt und in der Zukunft
Wo stehen wir im Bereich der sensorgestützten Steuerung und Optimierung auf dem Kontinuum vom Reißbrett zum ausgereiften Produkt? Die Antwort auf diese Frage lautet:„Es kommt darauf an.“
„Bei der grundlegenden Messung und der adaptiven Steuerung sind wir auf einem guten Weg der Lernkurve“, sagte Frank Powell, Produktmanager für Schleifprodukte bei Marposs Corp. (Auburn Hills, MI). „Werkzeugmaschinen können mit einer Vielzahl von In-Prozess-Sensoren und Wandlern ausgestattet werden. Auf der ersten Ebene dienen diese Sensoren dem Maschinenschutz, da ein System 1000-mal schneller als ein Bediener auf eine unerwartete Krafteinwirkung oder eine mögliche Kollision reagieren kann. Die Technologie schreitet durch immer genauere Messung der Position des Teils und der geometrischen Form des fertigen Teils sowie der Konfiguration und Steuerung der dabei verwendeten Werkzeuge voran.“
Laut Neil Munson, technischer Vertriebsspezialist für Silent Tools bei Sandvik Coromant (Fair Lawn, NJ), ist die digitale Fertigungstechnologie für Schneidwerkzeuge in Bezug auf Industrie 4.0 viel näher am Reißbrett als an einem ausgereiften Produkt. „Wir stehen am Abgrund eines Paradigmenwechsels in unserer Branche. Tatsächlich machen wir in unserem Unternehmen den ersten Sprung in Richtung sensorbasierter, intelligenter Schneidwerkzeuge“, sagte er.
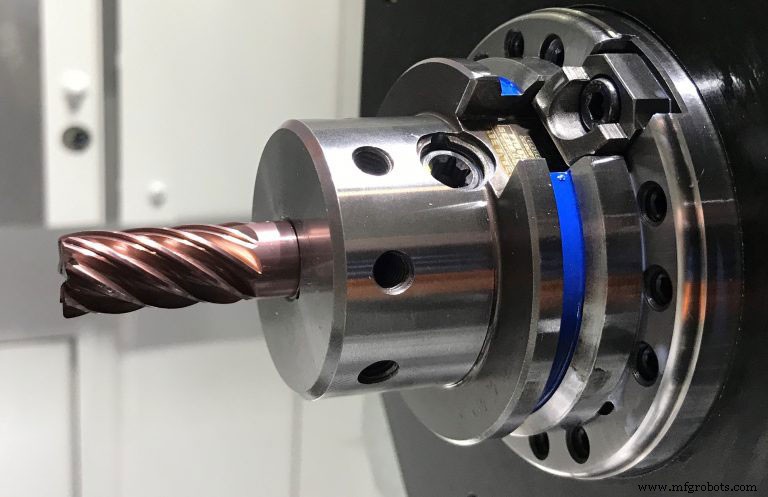
Joe Volansky von BadAxe Tooling Solutions sah das etwas anders. „Die Produkte haben sich bewährt, befinden sich auf einem guten Lernpfad und können auf revolutionäre Weise angewendet werden“, sagte Volansky. „In unserem Fall stellen wir ein auf bewährter Wissenschaft basierendes Produkt für Fräsoperationen vor, das eine Lösung am Rande der Maschinenphysik auf völlig neue Weise darstellt.“ BadAxe Tooling Solutions ist eine Allianz aus drei US-Unternehmen:Briney Tooling Systems (Bad Axe, MI), Fullerton Tool Co. (Saginaw, MI) und BlueSwarf LLC (State College, PA).
„Meiner Meinung nach befinden wir uns in Bezug auf die Entwicklung in der Mitte der Kurve“, sagte Wade Anderson, Product Specialist Manager und Tech Centers Manager bei Okuma America Corp. (Charlotte, NC). „Für die Effizienz der Grundausstattung und die Fähigkeit, mit Peripheriegeräten zu kommunizieren, gibt es eine Reihe von Standardlösungen, die sofort einsatzbereit sind. Technologien für künstliche Intelligenz (KI) und Augmented Reality (AR) sind jedoch auf dem Vormarsch.“
Angesichts der enormen Datenmenge, die jetzt von Geräten in der Werkstatt generiert wird, sind laut Andy Henderson, Vice President of Engineering bei Praemo (Kitchener, ON), die aufstrebenden Technologien, auf die Anderson sich bezieht, unerlässlich. „In der Automatisierungswelt hat es seit den 1970er Jahren eine sehr ‚physische‘ Entwicklung gegeben“, sagte Henderson. „Die nächste Grenze ist die ‚mentale‘ Evolution – das Hinzufügen von Intelligenz zu den Daten mithilfe von KI und maschinellem Lernen (ML). Auf dem Kontinuum sind diese Technologien ausgereift und werden kontinuierlich im persönlichen Bereich und im Verbraucherbereich (Google, Amazon, Facebook usw.) verwendet. Anwendungen innerhalb der Fertigungsindustrie hinken hinterher, aber Software, die diese Technologien verwendet, wie Razor, hilft Maschinenwerkstätten, den Wert von KI und ML zu erkennen.“ Razor ist ein Praemo-Produkt, das eine Verbindung zu Datenquellen herstellt, Informationen sammelt und Einblicke und empfohlene Empfehlungen bietet, um Benutzern zu helfen, vorbeugende Maßnahmen zu ergreifen, um Ausfallzeiten von Geräten zu reduzieren, Produktionsprozesse zu optimieren und Risiken zu managen.
Sensoren-Regel!
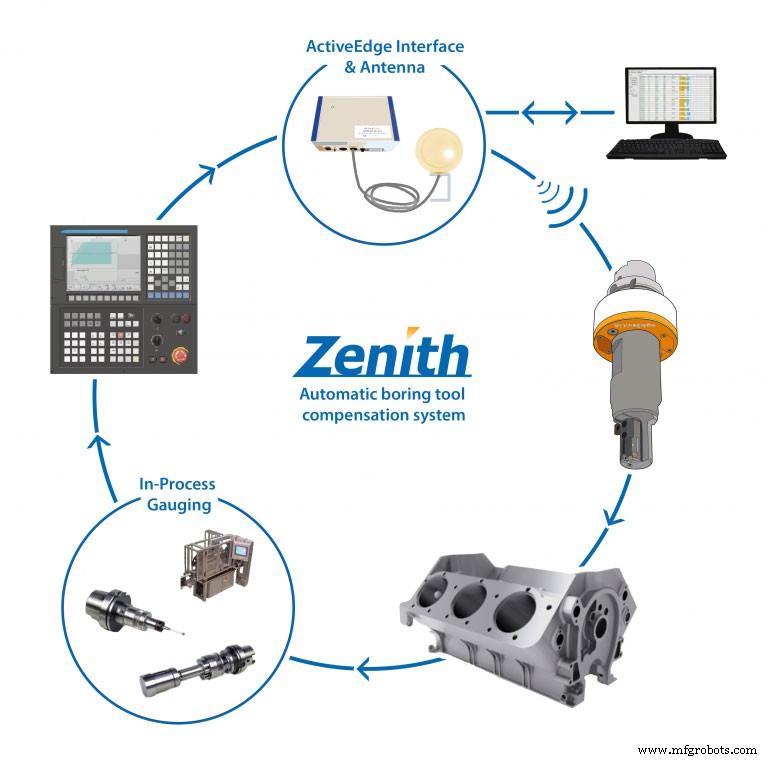
Unsere Branchenexperten waren sich alle einig, welche Schlüsselrolle Sensoren spielen. Es gibt ein altes Sprichwort:„Was gemessen wird, wird gemanagt.“ Obwohl ungewiss ist, wer es gesagt hat (einige vermuten Lord Kelvin, andere Peter Drucker), unterstreicht es die Tatsache, dass jeder Versuch, eine Maschine zu steuern oder zu optimieren, auf schnellen, genauen und zuverlässigen Daten am wichtigsten Kontaktpunkt basieren muss – wo das Schneidwerkzeug trifft auf das Werkstück.
Technisch gesehen war die Technologie zum erfolgreichen Sammeln, Verteilen und Analysieren von Daten für die adaptive Steuerung lange vor dem aktuellen Interesse an Industrie 4.0 und IIoT verfügbar. Historisch gesehen können In-Prozess-Messgeräte ihre Wurzeln über 60 Jahre zurückverfolgen (z. B. das Messgerät von Mario Possati zum Prüfen von Teilen während des Schleifens). Die größten Fortschritte bei Sensoren sind jedoch erst in jüngerer Zeit erfolgt.
Neueste Technologie
Einer dieser Fortschritte ist ein Aufbohrwerkzeug, das Schneidkantenverschleiß automatisch kompensiert. „Unabhängig davon, wie ausgereift eine CNC-Werkzeugmaschine ist, sie kann den Schneidkantenverschleiß eines Bohrwerkzeugs nicht automatisch kompensieren“, sagte Anthony Bassett, Präsident von Rigibore Inc. (Mukwonago, WI). „Unser akkubetriebenes ActiveEdge-Werkzeug automatisiert die prozessinterne Größenbestimmung der Schneidkanten von Bohrwerkzeugen. Es verwendet drahtlose Technologie, um mehrere Schneidkantendurchmesser an einem einzigen Werkzeug aus der Ferne einzustellen, die Prozessleistung zu optimieren und die Notwendigkeit eines Bedienereingriffs zu eliminieren.“
Neuland im Fräsbereich betritt das Montage- und Softwaresystem BadAxe Smart Tool. BadAxe ersetzt Trial-and-Error durch Physik, um nach Angaben des Unternehmens sofort den „Sweet Spot“ einer Maschine zu treffen, wenn sie gestartet wird. Anhand von Messungen der residenten Vibrationsfrequenzmuster für eine bestimmte Kombination aus Maschine, Spindel, Werkzeughalter und Werkzeug berechnen die patentierten Algorithmen und Analysen des Unternehmens die optimale Stabilitätszone für den Betrieb der Maschine. Das Ergebnis ist ein gebrauchsfertiges, vorgewuchteter und montierter Werkzeughalter und Werkzeug sowie eine für einzelne Maschinen optimierte Softwareschnittstelle.
„Jeder weiß, dass Vibrationen und Rattern die wichtigsten einschränkenden Faktoren bei der Hochgeschwindigkeitsbearbeitung sind“, sagte Volansky von BadAxe. „Normalerweise verwenden Bediener Trial-and-Error, um den richtigen Vorschub, die richtige Geschwindigkeit, Schnittbreite und Schnitttiefe zu finden. In vielen Fällen denken sie, dass sie in Bezug auf die Leistung an die Wand gefahren sind, obwohl in Wirklichkeit ein ratterfreier Betrieb in einer kontraintuitiven Konfiguration zu finden wäre, in der viel höhere Metallabtragsraten vorhanden sind. Dieses Setup wird von unserem Produkt sofort nach dem Start definiert, unabhängig von Step-Over, Vollschlitzschneiden oder Ecken. Organisationen wie Boeing Phantom Works, das US-Verteidigungsministerium und andere haben bewiesen, dass die zugrunde liegende Technologie den ROI eines Auftrags erheblich steigert.“
BadAxe baut eine große Datenbank für verschiedene Maschinen- und Baugruppenkombinationen auf. Wenn die Maschine eines Kunden nicht in der Datenbank vorhanden ist, kann ein einmaliger Test durchgeführt werden, um ihre Setup-Dynamik zu bestimmen.
Mit der Einführung von SilentTools+ intelligent vollzieht Sandvik Coromant den Übergang von In-Prozess- zu In-Tool-Sensoren Schneidewerkzeuge. „SilentTools+ sind gedämpfte Werkzeuglösungen, die einen enormen Einblick in Bearbeitungsprozesse mit langen Überhängen bieten, bei denen die Bediener normalerweise im Blindflug sind“, sagte Munson.
„Die Bearbeitung langer Überhänge in einer High-Tech-Anlage ist eine Herausforderung, weil [die Bediener] den Prozess bis zur Schneidspitze unter Kontrolle haben wollen“, sagte er. „Wir haben Sensoren in unsere SilentTools eingebettet, die über Bluetooth mit einer Grafikschnittstelle kommunizieren, sodass ein Bediener Augen und Ohren in der geschlossenen Maschine und tief in einer Bohrung hat. Darüber hinaus verfügt es über eine Funktion, die eine schnelle und einfache Einrichtung ermöglicht, indem festgestellt wird, wann sich die Schneidspitze in der Mitte befindet.“
Mit dem SilentTools+ System werden Werkzeugdurchbiegung, Rattern, Schnittkräfte, Werkzeugbelastung und Temperatur in Echtzeit überwacht. „Aufgrund des Einblicks in all diese Bereiche glauben wir, dass die Ausschussraten gesenkt und Produktivitätssteigerungen realisiert werden, was zu echten Einsparungen führt“, fügte Munson hinzu.
Informationen bitte!
Während einige Sensorausgaben nur zu Informationszwecken dienen, besteht der Mehrwert darin, Sensorsignale zu verarbeiten und zur Kontrolle der Teilequalität und des Werkzeugzustands zu verwenden. Hersteller können Werkzeugwege und Bearbeitungszeit minimieren, die Oberflächenbeschaffenheit verbessern, die Lebensdauer der Maschine maximieren und anspruchsvollere Teile, wie z. B. solche mit komplexen Geometrien, dünnen Wänden, Hohlzylindern und schlanken Wellen, effizient bearbeiten.
Anderson sagte:„Das Okuma-Überwachungssystem ist ein guter erster Schritt. Es ermöglicht bis zu 64 verschiedene Eingänge, die an prozessspezifische Anforderungen angepasst werden können. Wir haben Kunden, die in der Lage waren, Maschinenausfallzeiten zu messen und OEE-Daten (Gesamtanlageneffektivität) zu analysieren, um festzustellen, dass eine einfache Sache darin bestand, die Maschine abzuschalten, wenn ein Bediener an anderer Stelle beschäftigt war. Durch die Verwendung des Überwachungssystems [kann der Bediener gewarnt werden], dass ein potenzielles Problem auftritt, das durch vorbeugende Maßnahmen vermieden werden kann.“
Henderson von Praemo glaubt, dass der Weg zum Fertigungserfolg letztendlich über den Datenberg führt, den Werkzeuge in Metallzerspanungsanwendungen generieren. „Diese Daten sind ein wertvoller ‚Rohstoff‘ für die Optimierung“, sagte er. „Die Algorithmen zur Datenanalyse in unserer Razor-Software können riesige Datenmengen durchsuchen, um Zusammenhänge und Muster zu finden, die ein Mensch mit einer Tabellenkalkulation niemals aufdecken würde. KI- und ML-Technologien werden verwendet, um Modelle zu entwickeln, die Bedienern und Managern helfen, sehr schnell zu klaren Schlussfolgerungen zu gelangen – und auf der Grundlage datengesteuerter Schlussfolgerungen Maßnahmen zu ergreifen. Obwohl die Intelligenz künstlich ist, ahmt sie sehr genau nach, wie Menschen in der Fertigungswelt an die Dinge herangehen. Der einzige Unterschied besteht darin, dass es nicht von riesigen Datenmengen überwältigt wird. Je länger Daten gesammelt werden und je mehr Daten gesammelt werden, desto mehr lernt Razor.“
Nachgewiesene Fähigkeit
Laut Powell von Marposs haben die heutigen Systeme ihre Fähigkeit bewiesen, den Schneidprozess aufrechtzuerhalten, vorauszusehen, wenn etwas nicht stimmt, und einen Bediener oder die Maschine zu benachrichtigen, um Korrekturmaßnahmen zu ergreifen. „Die Entscheidung, nur zu benachrichtigen oder automatische Maßnahmen zu ergreifen, wird vom Kunden diktiert“, sagte er. „Technisch gesehen haben wir viele Möglichkeiten zur automatischen Steuerung, die in einigen Fällen nicht genutzt werden.“
Ein neues System von Marposs namens BLÚ ist das Ergebnis von über 50 Jahren Erfahrung mit Schleifmaschinen und anderen Werkzeugmaschinen. Es kombiniert alle Werkzeugmaschinenüberwachungs- und Prozesssteuerungsanwendungen in einem einzigen System für Werkzeug- und Prozessüberwachung in Echtzeit, adaptive Steuerung und Absturzminderung mit einer schnellen Verarbeitungs- und Abtastzeit. Powell sagte:„BLÚ wurde entwickelt, um sich nahezu nahtlos in die Werkzeugmaschine zu integrieren, um den Bediener in jedem Modus zu unterstützen:Einrichtung, manuell oder automatisch.“
Das Herzstück des Systems ist ein Masterknoten, der im Maschinenschrank untergebracht ist. Es verfügt über eine Busstruktur, um andere Knoten für Messungen auf der Maschine, Schallemissionsüberwachung, Radauswuchten (Schleifen), Werkzeugrückzug und andere Funktionen anzuschließen.
Laut Bassett von Rigibore ist das Zenith-System ein automatisches System mit geschlossenem Kreislauf für Bohrarbeiten. „Herkömmliche Systeme sind rein mechanisch ohne kontinuierliche Rückmeldung an die Bohrmaschine“, sagte er. „Zenith gibt der Maschinensteuerung Feedback, um zu bestätigen, dass sich das Werkzeug um den gewünschten Betrag verstellt hat. Dieses Positionssensor-Feedback verhindert, dass ein schlechtes Teil bearbeitet wird.“
Wie weit kann uns diese Technologie bringen?
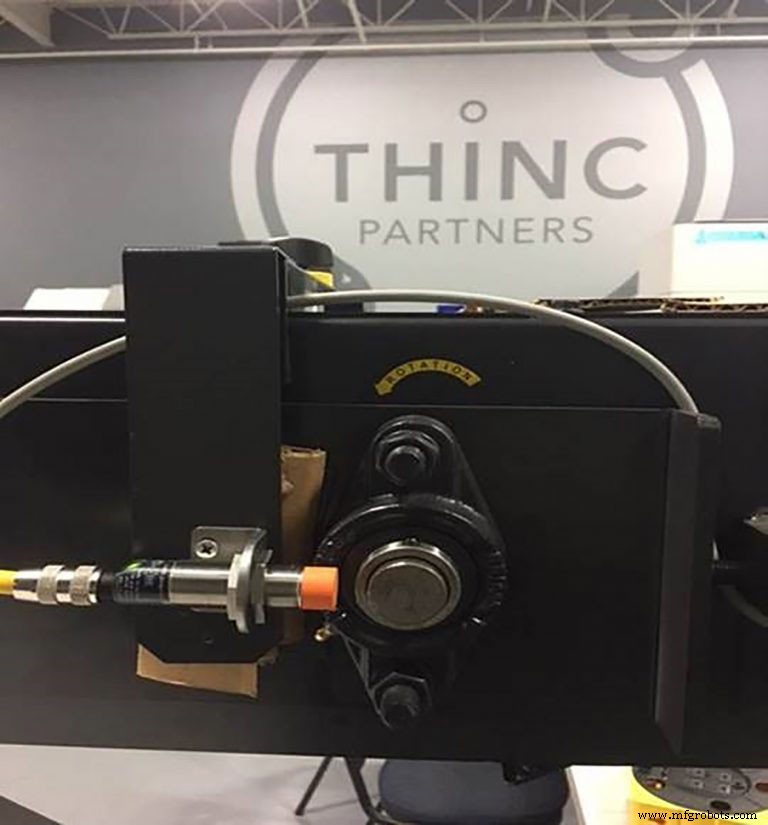
„Ich sehe nicht unbedingt ein Endspiel für digitale oder sensorbasierte Schneidwerkzeuglösungen“, sagte Munson von Sandvik Coromant. „In modernen Maschinenwerkstätten und Fertigungsanlagen werden Sensoren und der Einsatz von IIoT in Schneidwerkzeugen in den nächsten fünf bis zehn Jahren immer allgegenwärtiger werden und dem Weg der Verbraucheranwendungen folgen. Für uns ist die Integration unserer SilentTools+ in die Steuerung von CNC-Maschinen die natürliche Weiterentwicklung. Heute ist es ein eigenständiges System mit Live-Prozessansicht. Wir arbeiten mit Werkzeugmaschinenherstellern und CAM-Softwarepartnern zusammen, um von einem eigenständigen System auf eine Maschinensteuerung und Prozessintegration umzusteigen.“
Anderson von Okuma stimmte zu. „Technologie und vor allem die Implementierung von Technologie werden neue Technologien hervorbringen“, sagte er. „Vor vielen Jahren fand ich einen automatisch abblendenden Rückspiegel in einem Fahrzeug lächerlich. Nun, ich würde kein Auto ohne kaufen. In ähnlicher Weise werden neue Technologien in unserer Branche dazu beitragen, neue Märkte für alternative Fortschritte zu entwickeln.“
Powell von Marposs stimmte zu, dass es niemals ein Endspiel geben sollte. „Ich denke, dass die Technologie vorhanden ist, um alle wichtigen Parameter und Variablen zu überwachen“, sagte er. „Sicher gibt es Bereiche, die verbessert werden können, und wir arbeiten täglich daran, Sensoren zu entwickeln, die schneller und empfindlicher sind, und eine Software, die die Sensordaten schneller und intelligenter verarbeiten kann. Ich bin mir sicher, dass es innerhalb von 10 Jahren mindestens einen Game-Changer geben wird, einen technischen Durchbruch, der eine Maschinenwerkstatt effizienter und produktiver macht. Wenn sich das Spiel ändert, ändern wir uns mit.“
Volansky von BadAxe glaubt, dass sein Unternehmen gerade einen Wendepunkt hat. „Das Tempo der Entwicklung nimmt zu“, sagte er. „Kunden wollen nicht fünf oder zehn Jahre warten. Wir haben ein Produkt, das Effizienz neu definiert und Werkzeugmaschinen hilft, an den Grenzen der Physik zu arbeiten. Der nächste Schritt für uns wird jedoch sein, unsere Werkzeugbaugruppe aus der Gleichung zu entfernen, indem wir unsere proprietäre Vibrationserfassung und Datenanalyse direkt in die Maschine und ihre Logik einbetten.“ Auf diese Weise wird die Maschine nur in ihrem höchstoptimierten Zustand betrieben, ohne dass der Bediener Trial-and-Error ausführt, fügte er hinzu.
Wie Bassett von Rigibore sagte:„Einige Entwicklungsziele für uns sind die automatische Bestellung von Hartmetallwerkzeugen mithilfe der CNC-Steuerung, eine Umstellung auf weniger Eingriffe von Bedienern, Anpassungen, die von einer zentralen Stelle aus vorgenommen werden, und die Eingabe eines Volumenkörpermodells in die CNC-Maschine währenddessen ein anderer Prozess ist in Betrieb. Die größten Grenzen, mit denen wir heute konfrontiert sind, sind die Inkompatibilität und das Fehlen von Standards zwischen verschiedenen CNC-Maschinenherstellern und Herstellern von Maschinensteuerungen.“ Letztendlich begrenzt ein proprietärer Ansatz das Wachstum und ist letztendlich teurer für einen Kunden, der neue Funktionen einfach hinzufügen möchte, schloss Bassett.
Laut Henderson von Praemo definieren einige Leute die Lights-out-Fertigung ohne menschliches Eingreifen als das Endspiel. „Ich persönlich denke, dass das Ausschalten der Lichter dem Streben nach Weltfrieden ähnlich ist“, sagte er. „Für die Fertigungsindustrie ist es ein attraktives, anzustrebendes Konzept, das jedoch in vielen Situationen nicht realisierbar sein wird. In Werkzeuge und Werkzeugnetzwerke eingebaute Sensoren; Software, die Daten nahtlos sammelt, organisiert und analysiert; und Werkzeugmaschinen, die zu einer Quelle der Fabrikintelligenz vernetzt sind, bringen uns dieser Lights-out-Fabrik viel näher. Das bedeutet nicht, dass Maschinen Menschen ersetzen. Es gibt ihnen die Freiheit, Arbeiten zu erledigen, die weniger niederträchtig, befriedigender und definitiv produktiver sind. Es ist vergleichbar mit dem Aufkommen der CNC, die die manuelle Steuerung von Bearbeitungszentren automatisierte. Es ermöglichte den Menschen, sicherer und produktiver zu arbeiten.“
Automatisierungssteuerung System
- Schneidlösung für die Teppichindustrie – Digitale Schneidemaschine
- Schneidelösung für die Filmindustrie – digitale Schneidemaschine
- Digital- und Laserschneidmaschine – die beste Schneidlösung für die Stoff-/Textilindustrie
- Lieferkette zieht neue Talente aus mehreren Generationen und Branchen an
- Neue Maschine gebaut, und ein Kunde aus England hat gelernt, diese CNC-Maschine zu bedienen
- Universal Robots arbeitet mit Phillips Machine Tools India zusammen
- Drehmaschinenoperationen und Drehschneidwerkzeuge
- Was ist maschinelles Drehen?
- Multifunktionale Werkzeuge, die alle Werkstätten haben sollten
- Ein schneller Vergleich von CNC-Werkzeugmaschinen