Beschleunigung des Designprozesses der additiven Fertigung mit neuen CAD/CAM-Tools
Fertigungstechnik: Das neueste PowerMill 2019-Update von Autodesk fügt ein neues Additiv-Plug-In-Modul hinzu. Können Sie dieses „hochleistungsfähige“ additive Fertigungssystem und seine Funktionsweise beschreiben?
Clinton Perry: PowerMill 2019 bietet eine dedizierte Suite von Tools zum Programmieren von Hochgeschwindigkeits-Additivprozessen – allgemein bekannt als Directed Energy Deposition [DED]. Der DED-Prozess verwendet eine CNC-Werkzeugmaschine oder einen Industrieroboter, der eine Energiequelle – typischerweise einen Laser, Lichtbogen oder Elektronenstrahl – auf einen Punkt im Raum fokussieren kann. Gleichzeitig wird Material [entweder in Form von Metallpulver oder Draht] in den „Hot Spot“ eingeführt. Die Stromquelle lässt das Material schmelzen und bildet eine geschmolzene Pfütze. Indem man diese Pfütze herummanövriert, ist es möglich, 3D-Formen zu erstellen – und zwar auf sehr kontrollierte Weise.
Diejenigen, die mit Pulverbett-3D-Druckern vertraut sind, wissen, dass sie unglaublich komplizierte 3D-Formen herstellen können. Aufgrund der zugrunde liegenden Technologie sind sie jedoch hinsichtlich der Materialauftragsraten und der herstellbaren Teilegröße begrenzt. Diese Einschränkungen haben sich auf die Einführung dieser Form der additiven Fertigung in bestimmten Branchen und Anwendungen ausgewirkt.
Im Vergleich dazu verwendet der DED-Prozess höhere Leistungspegel und Materialflussraten, was zu wesentlich höheren Abscheidungsraten führt, wodurch Teile schneller gebaut werden können. Darüber hinaus bedeutet der größere Arbeitsbereich von CNC-Maschinen und Robotern, dass DED deutlich größere Teile bauen kann. Diese beiden Hauptmerkmale machen DED zu einer kostengünstigen Lösung zur Herstellung großformatiger Komponenten, die häufig in Branchen wie Luft- und Raumfahrt, Energieerzeugung usw. zu finden sind.
Das Betreiben eines DED-Prozesses erfordert hochspezialisierte Werkzeugwege, die genau steuern, wie und wo Material aufgetragen wird, und gleichzeitig lokales Überbauen vermeiden. PowerMill 2019 sieht die Bereitstellung einer dedizierten Suite von Tools zum Erstellen, Steuern und Simulieren von Abscheidungsstrategien vor, um Herstellern zu helfen, das Potenzial von DED auszuschöpfen.
ICH: Welche Vorteile bieten Hybrid-CNC/AM-Maschinen gegenüber reinen CNCs oder herkömmlichen additiven Systemen?
Perry: Die meisten etablierten Hersteller von CNC-Werkzeugmaschinen haben damit begonnen, Hybridmaschinen anzubieten, die sowohl additive als auch subtraktive Technologie liefern können. Es gibt einige offensichtliche Vorteile; Eine einzige hybride Werkzeugmaschine nimmt weniger Stellfläche ein, trägt dazu bei, die Einrichtungszeit von Teilen zu verkürzen und das Risiko menschlicher Fehler zu minimieren. Die wirklichen Vorteile sind jedoch viel grundlegender.
Bei separaten additiven und subtraktiven Arbeitsabläufen wird ein Teil normalerweise vollständig abgelegt, bevor es zum Präzisionsfräsen auf eine CNC-Maschine übertragen wird. Dies ist zwar auch mit Hybridmaschinen realisierbar, aber durch die größere Flexibilität können die beiden Verfahren auf alternative Weise kombiniert werden.
Beispielsweise kann ein Teil vor dem CNC-Fräsen kritischer Merkmale teilweise abgelegt werden. Die Bau- und Schnittphasen wechseln sich dann ab, bis das Teil fertig ist. Durch die Kombination der Technologien auf diese Weise können Hybridmaschinen Teile herstellen, die mit separaten Maschinen nicht hergestellt werden können.
Ein bemerkenswertes Beispiel dafür wurde kürzlich in der UK Advanced Manufacturing-Anlage von Autodesk gezeigt, wo eine Hamuel Reichenbacher HSTM 150 HD-Hybridmaschine zur Reparatur einer beschädigten Luft- und Raumfahrtkompressorscheibe verwendet wurde. Der Prozess begann mit dem CNC-Fräsen der beschädigten Spitzen der Schaufeln auf der Scheibe, bevor ein Laser und eine DED-Pulverform verwendet wurden, um Titan abzuscheiden, um das bearbeitete Material zu ersetzen. Schließlich verwendete die Maschine hochgenaue Sondierungen, um das überschüssige Material zu messen und CNC-zufräsen, wodurch eine nahezu perfekte Mischung zwischen altem und neuem Material zurückblieb.
ICH: Das neue PowerMill Additive-System zielt sowohl auf drei- als auch auf fünfachsige Bearbeitungssysteme plus Roboter ab. Wie unterscheidet es sich bei der Verwendung mit CNCs oder mit Robotern?
Perry: Hinsichtlich der Werkzeugwegerstellung gibt es keinerlei Unterschiede. Die additiven Werkzeugwege von PowerMill können auf einer CNC-Werkzeugmaschine oder einem Roboter ausgeführt werden. Eine Reihe von Additivstrategien wird für die folgenden Anwendungen bereitgestellt:
- Erstellen von 2D-Werkzeugwegen zum Erstellen vollständiger, prismatischer Formen.
- Erstellen von drei- oder fünfachsigen Strategien, um lokalisierte Merkmale zu vorhandenen Teilen hinzuzufügen [z. B. Anbringen von Laschen an der Seite eines Flugzeugtriebwerksgehäuses].
- Generieren einer drei- oder fünfachsigen Bewegung, um Beschichtungen entweder vollständig oder in lokalisierten Bereichen auf Teilen aufzubringen [z. B. Hinzufügen einer verschleißfesten Beschichtung auf einem Teil, das einem hohen Grad an Abrieb ausgesetzt ist].
Die additiven Strategien werden in derselben Benutzeroberfläche erstellt, die auch zum Erzeugen subtraktiver Werkzeugwege verwendet wird. Das bedeutet, dass sie mit den Werkzeugweg-Bearbeitungswerkzeugen von PowerMill optimiert werden können. Darüber hinaus ermöglicht PowerMill die punktuelle Bearbeitung wichtiger Prozessparameter wie Laserleistung, Pulverdurchfluss und Gasfluss.
Sobald Werkzeugwege erstellt und optimiert wurden, können sie mit einem virtuellen Zwilling der CNC-Werkzeugmaschine/des Roboters simuliert werden, wodurch problematische Maschinenbewegungen, wie z. B. Achsenumkehrungen und/oder Überfahren, identifiziert und vermieden werden können.
Schließlich ermöglicht PowerMill den Export von Werkzeugwegen in die Autodesk Netfabb-Simulation für eine eingehendere Analyse des gesamten Bauprozesses, einschließlich thermischer und belastungsbezogener Überprüfung. Dies gibt den Herstellern mehr Vertrauen, dass der Bauprozess gute Teile produzieren wird.
ICH: Welche Kunden oder welche Branchen oder Anwendungen verwenden das System?
Perry: AM bietet vielen Branchen erhebliche Vorteile, darunter Luft- und Raumfahrt, Öl und Gas, Formen- und Formenbau, Stromerzeugung, Motorsport und Schifffahrt. Der Rotterdamer Hafen ist einer der verkehrsreichsten Schifffahrtsknotenpunkte der Welt und ein Anlaufpunkt für große Schiffe, die gewartet werden müssen. Wenn ein kommerzielles Frachtschiff im Dock festsitzt und auf ein Ersatzteil wartet, kann dies buchstäblich Millionen von Dollar an entgangenem Geschäft kosten. Der traditionelle Ansatz wäre, Lager an wichtigen Standorten auf der ganzen Welt zu bauen und mit Ersatzteilen zu füllen – nur für den Fall, dass sie benötigt werden.
Das Team von RAMLAB [Rotterdam Additive Manufacturing Lab] hat das Potenzial erkannt, DED und Hybridfertigung einzusetzen, um Ersatzteile nach Bedarf herzustellen, wann und wo immer sie benötigt werden.
Ihr erstes Projekt umfasste die Herstellung eines Propellers aus einer Bronzelegierung mit einem Durchmesser von mehr als 1,5 m, für den mehr als 400 kg Material abgelagert werden mussten. Der fertige Propeller wurde ausgiebigen Tests unterzogen, bevor er von der zuständigen Behörde als seetüchtig zertifiziert wurde – eine Weltneuheit für einen additiv gefertigten Propeller! Durch die Herstellung von Teilen auf diese Weise kann RAMLAB die Zeit verkürzen, in der ein Frachtschiff außer Betrieb ist. Es vermeidet nicht nur Verzögerungen in Millionenhöhe, sondern beseitigt auch die Notwendigkeit eines Netzwerks voll ausgestatteter Lagerhäuser.
ICH: Welche anderen neuen Funktionen werden Maschinisten in PowerMill 2019 für die traditionelle Bearbeitung finden?
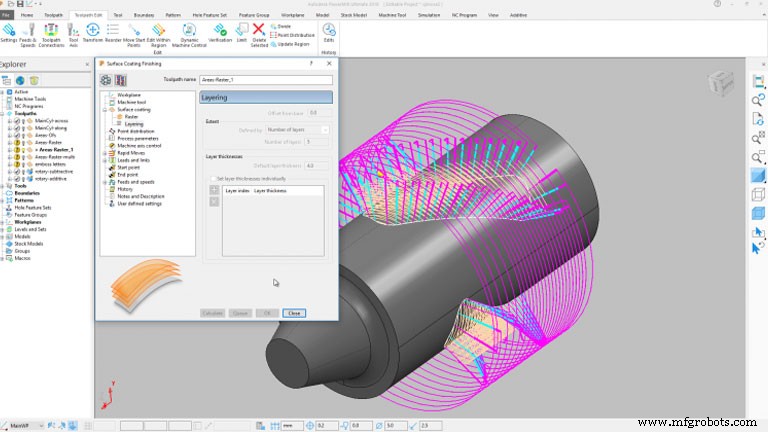
Perry: Die Software enthält mehrere Verbesserungen für die subtraktive Fertigung. PowerMill bietet seit vielen Jahren eine Fünf-Achsen-Kollisionsvermeidung an, was bedeutet, dass Werkzeugwege erstellt werden können, die Kollisionen oder Beinahe-Kollisionen mit der Schneidwerkzeugbaugruppe vermeiden. In früheren Versionen konnte der Benutzer aus einer Reihe verschiedener Vermeidungsoptionen wählen. Die getroffene Wahl hing von der Form des zu bearbeitenden Teils und der verwendeten Strategie ab. PowerMill 2019 enthält eine neue „automatische“ Werkzeugachsen-Neigungsoption, die für alle Werkzeugwegtypen und alle Modellformen funktioniert. Dies erleichtert Programmierern das Erstellen eines sicheren fünfachsigen NC-Codes und eignet sich besonders für Benutzer, die neu in der fünfachsigen Bearbeitung sind.
Die hocheffiziente Vortex-Schruppstrategie von PowerMill wurde verbessert, um eine neue „ab Lager“-Option anzubieten. Basierend auf der adaptiven Clearing-Funktion von Autodesk erstellt dies Werkzeugwege mit Versätzen basierend auf der Form des zu bearbeitenden Rohteils und führt in der Regel zu reduzierten Zykluszeiten. In Tests wurde ein P20-Kerneinsatz mit der neuen Option „ab Lager“ und dem vorherigen Werkzeugwegtyp „ab Modell“ bearbeitet. Die Option „ab Lager“ hatte eine um 33 % schnellere Zykluszeit.
ViewMill ist das Aktiensimulationstool von PowerMill. Es zeigt zu jedem Zeitpunkt des Bearbeitungsprozesses eine realistische Darstellung des Rohmaterials. Mit der Veröffentlichung von PowerMill 2019 enthält ViewMill einen neuen Dickenschattierungsmodus, der es Programmierern erleichtert, die Verteilung von Rohmaterial auf ihren Teilen zu visualisieren. Eine Reihe dynamischer Schieberegler ermöglicht es, die Farbe der Simulation zu ändern, um fertig bearbeitete Oberflächen sofort zu identifizieren und Bereiche anzuzeigen, in denen verbleibendes Material entfernt werden muss, oder lokalisierte Bereiche, in denen möglicherweise Dellen aufgetreten sind. Die Verbesserung gibt Programmierern mehr Vertrauen, dass Teile vollständig bearbeitet werden, wenn sie aus der Werkzeugmaschine entfernt werden.
PowerMill 2019 bietet auch die Möglichkeit, wichtige Fertigungsdaten in Autodesk Fusion Production zu exportieren, ein Cloud-basiertes Tool, mit dem Hersteller Arbeiten planen, Aufträge verfolgen und die Auslastung von CNC-Maschinen überwachen können. Fusion Production ermöglicht es wichtigen Projektbeteiligten, auf wichtige Informationen über den Status einer Produktionsanlage zuzugreifen, wodurch Engpässe identifiziert, Prozesse überprüft und verbessert und die Gesamtanlageneffizienz maximiert werden können. Als Cloud-basiertes System ermöglicht Fusion Production den Zugriff auf Daten jederzeit, überall und auf praktisch jedem Mobil- oder Desktop-Gerät.
Neuerscheinungen
Der Metrologieentwickler Hexagon Manufacturing Intelligence (North Kingstown, RI) hat sein PC-DMIS 2018 R1-Update der Messsoftware des Unternehmens herausgebracht, das die erste von zwei für 2018 geplanten PC-DMIS-Versionen enthält.
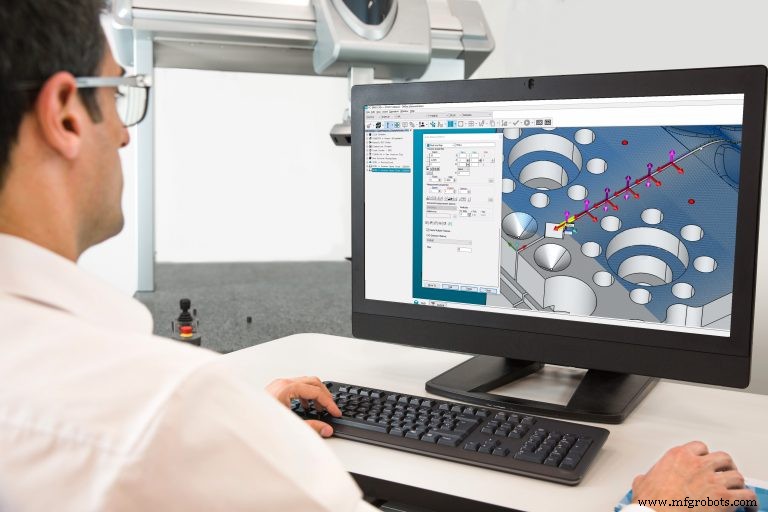
PC-DMIS 2018 R1 ermöglicht es Benutzern, AutoFeatures in Punkte umzuwandeln oder die gemessenen Treffer für neue Konstruktionen und Bemaßungen zu verwenden, die für ebene, kreisförmige und zylindrische AutoFeatures verfügbar sind, so das Unternehmen. Durch die Umwandlung jedes Treffers in einen Vektorpunkt kann die Pfadoptimierungsfunktion verwendet werden, um die Reihenfolge der Punktmessung zu verbessern, die Anzahl der Sondenspitzenwechsel und die Gesamtmesszeit zu reduzieren. Die neue Unterstützung für Q-DAS Traces ermöglicht eine einfachere Analyse von PC-DMIS-Daten. Die neue QuickSet-Steuerung ermöglicht es Benutzern, sowohl QuickFeature als auch GD&T Selection zu verwenden und dennoch Messstrategien zu ändern.
„Mit PC-DMIS 2018 R1 erfüllen wir unsere Verpflichtung, die am häufigsten nachgefragten Elemente aus dem ‚Ideenzentrum‘ der Benutzer hinzuzufügen“, sagte Ken Woodbine, Produktlinienmanager für Metrologie-Software bei Hexagon Manufacturing Intelligence. „Dazu gehören die grafische Punktmanipulationsfunktion und die „Push-to-Points“-AutoFeature-Funktionalität. Wir führen auch die Integration mit der branchenüblichen Q-DAS-Software ein, damit wichtige Prozessparameter, die sich auf die Qualität auswirken, identifiziert und verfolgt werden können.“
Die verbesserte Geschwindigkeit der QuickFeature-Messung ermöglicht es Benutzern, mehrere Kreise und Zylinder mit einem Klick zu erstellen, die für Schraubenlochmuster optimiert sind oder wann immer Oberflächen mehrere Merkmale derselben Größe und Form enthalten, so das Unternehmen. Das System führt auch einen verbesserten AutoFeature-Arbeitsablauf für „Flush and Gap“ für die Inspektion von Punktwolken ein.
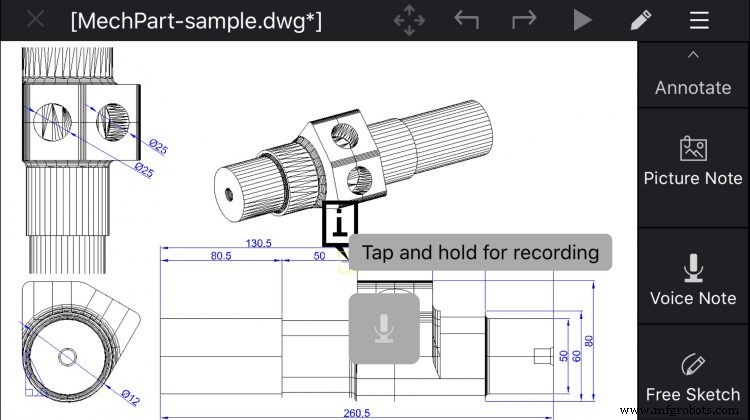
Eine iOS-Version von CorelCAD Mobile von Corel Corp. (Ottawa, ON) ist jetzt für iPhone und iPad verfügbar und bietet technischen Designern CAD-Funktionen zur Steigerung der Produktivität unterwegs. Das neue CorelCAD Mobile für iOS bietet Benutzern jetzt Optionen sowohl für Apple-Geräte als auch für Android-Mobilsysteme und bietet Außendienstbenutzern Zugriff auf 2D-Design- und Anmerkungswerkzeuge für Tablets und Smartphones.
CorelCAD Mobile ist ein eigenständiges CAD-Programm, das die Desktop-Anwendung CorelCAD 2018 für Windows und Mac ergänzt. CorelCAD Mobile-Abonnenten erhalten eine Reihe von 2D-Zeichnungs-, Bearbeitungs- und 3D-Anzeigewerkzeugen, vollständige Anmerkungsfunktionen und mehr. Für Benutzer, die nach einem leichteren Funktionsumfang suchen, ist auch eine kostenlose Version mit vereinfachten Funktionen verfügbar, einschließlich 2D- und 3D-DWG-Anzeige und einfacher Anmerkung.
CorelCAD Mobile bietet Benutzern die Möglichkeit, unterwegs Ideen zu skizzieren, Entwürfe zwischen Desktop und Mobilgerät auszutauschen, Besprechungen effizienter zu gestalten, Zeichnungen vor Ort zu kommentieren und bei Bedarf Änderungen an Zeichnungen vorzunehmen. Die Software ist ab sofort für iPhone und iPad im Apple App Store und für Android im Google Play Store erhältlich. Abonnements kosten 99,99 $ oder 9,99 $ pro Monat. Kostenlose Versionen im einfachen Modus sind ebenfalls verfügbar.
Das neueste WorkNC 2018 R1 CAM-Software-Update von Vero Software (Gloucester, UK, und Tuscaloosa, AL) enthält nicht nur das neue CAD-System WorkNC Designer „CAD for CAM“ zur direkten Modellierung, sondern auch ein neues Robotermodul. Da Roboter in der Werkstatt immer häufiger eingesetzt werden, besteht laut WorkNC Brand Manager Miguel Johann ein zunehmender Bedarf an Offline-Programmierung für sie.
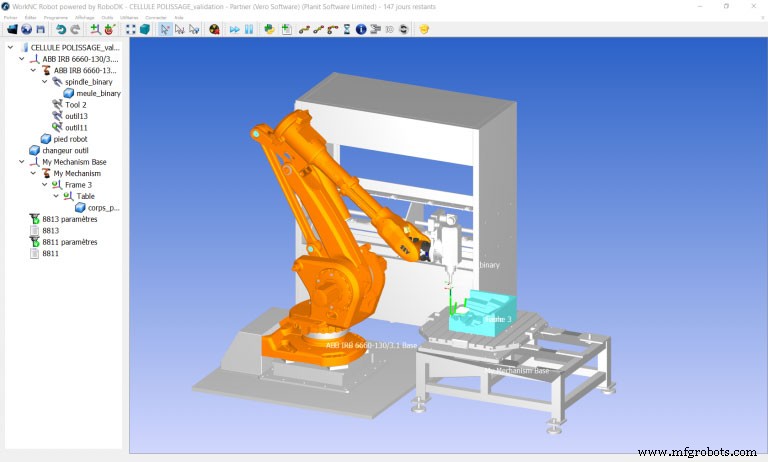
„Neue Simulations- und Singularitätsauflösungswerkzeuge in WorkNC 2018 R1 bedeuten, dass Benutzer die enormen Vorteile, die Roboter für den Fertigungsprozess bringen, voll ausschöpfen können“, sagte Johann. „Zum Beispiel befreien sie Werkzeugwege von den Beschränkungen des Fräsens, da das Werkzeug am Ende des Roboterarms auch ein Schleifer, ein Laserkopf, eine Schweißdüse oder jedes andere Werkzeug sein kann, das der Ingenieurskreativität einfällt.“
Roboter ermöglichen es auch, das Werkzeug zu fixieren und das Teil darum herum zu bewegen, anstatt der traditionellen Methode mit einer fixierten Komponente und einem beweglichen Werkzeug, sagte Johann. „Aber Roboter sind nur so gut wie die Software, die sie programmiert, und diese neueste Entwicklung in WorkNC 2018 R1 stellt sicher, dass Hersteller an der Spitze der Robotertechnologie stehen können.“
WorkNC hat auch neue Funktionen in das Wellenform-Schruppen integriert, die die Effizienz und Leistung verbessern, einschließlich der Unterstützung neuer Werkzeuge in trochoidalen Bearbeitungsstrategien.
Software Update wird von Senior Editor Patrick Waurzyniak herausgegeben.
Automatisierungssteuerung System
- Die Pandemie beschleunigt den Übergang zum 3D-Druck
- Überwachung der additiven Fertigung mit einem optischen Mikrofon
- Bewältigung der Fertigungsherausforderung mit Daten und KI
- Was gehört zum Herstellungsprozess?
- Alles drin mit Additiv
- So nutzen Sie CAD vollständig im additiven Fertigungsprozess
- Computergestützte Fertigungssoftware (CAM):Der grundlegende Prozess und die Anwendungen
- Modernste CAD/CAM-Technologie:Ein günstiger Herstellungsansatz für technische Materialien
- Straffung des Prozesses
- Programmieren Sie Ihre Fertigungsprozesse mit CAD/CAM-Software