Überwachung der additiven Fertigung mit einem optischen Mikrofon
Technologien der additiven Fertigung (AM) haben in den letzten Jahren eine bemerkenswerte Akzeptanz in der Branche erfahren. Da Digitalisierung und On-Demand-Fertigung das Gesicht von Produktionsstätten zu vollautomatisierten Produktionslinien verlagern, werden zuverlässige Methoden zur Prozessüberwachung immer wichtiger.
Bei der laserbasierten Bearbeitung von Metallen ist es eine bekannte Tatsache, dass optische und akustische Emissionen während des Prozesses in Echtzeit analysiert und mit der endgültigen Teilequalität korreliert werden können. 1,2,3 Dieser Ansatz bietet einen erheblichen Mehrwert, da das Auftreten von Poren, Rissen oder anderen Inhomogenitäten, die während des Produktionsprozesses entstehen, die mechanischen Eigenschaften stark beeinflusst und das Risiko von fehlerhaften Bauteilen erhöht. Eine sofortige Reaktion auf warnende Prozesssignale kann somit Ausschuss reduzieren und Zeit sparen.
Heutzutage werden optische Systeme wie Pyrometer, Hochgeschwindigkeitskameras, IR-Kameras und Fotodioden weit verbreitet verwendet, um laserbasierte AM-Prozesse sowohl im akademischen als auch im industriellen Kontext zu überwachen. 4 Obwohl sie wichtige Einblicke in die Laser-Metall-Wechselwirkungszone geben, sind sie blind für relevante Aspekte, die nach dem Abschalten des Lasers geschehen, z. Rissbildung durch thermische Belastung.
Körperschallsensorsysteme sind kürzlich kommerziell verfügbar geworden, beispielsweise im Rahmen von Powder Bed Fusion (PBF)-Prozessen. 5 Herausgefordert werden Körperschalldetektoren jedoch bei Prozessen wie Laser Metal Deposition (LMD) oder Wire Arc Additive Manufacturing (WAAM), bei denen sich der strukturgebundene Signalpfad während der Bauzeit ändert oder sogar unterbrochen werden kann. In solchen Fällen bietet ein luftgekoppelter akustischer Sensor mit festem Abstand eine leistungsfähige Lösung.
Eine neue Ultraschallprüftechnik
Im Gegensatz zu herkömmlichen akustischen Sensoren auf Membran- oder Piezobasis arbeitet das optische Breitbandmikrofon von XARION Laser Acoustics mittels Interferometrie. Sein akinetisches Detektionsprinzip beruht auf Schallwellen, die eine Änderung des Brechungsindex der Luft innerhalb des 2-mm-Interferometerhohlraums verursachen, der oben auf dem in Abbildung 1a gezeigten Sensorkopf sitzt. Dies verursacht kleine Verschiebungen in der Wellenlänge des Lasers, der innerhalb des Resonators enthalten ist und hin und her reflektiert wird. Die geringfügige Abweichung der Wellenlänge verursacht eine Variation der Interferenz und somit der Lichtintensität, die von der Kavität zurückkommt. Die Intensitätsänderung wird dann von einer externen Fotodiode gemessen.
Dieses akustische Wandlerverfahren – das komplett ohne bewegliche Elemente auskommt – bietet den breitesten Frequenzbereich auf dem Mikrofonmarkt und übertrifft den Stand der Technik um den Faktor 10. Da Hintergrundgeräusche, z.B. B. von nahegelegenen Maschinen, sind typischerweise auf niedrigere Frequenzen (<100 kHz) begrenzt, der Bereich des optischen Mikrofons von 10 Hz bis 1 MHz ermöglicht eine klare spektrale Trennung zwischen wertvollem Prozesssignal und unerwünschtem Rauschen. Die Obergrenze dieses Frequenzgangs ist teilweise durch das Medium selbst vorgegeben, da die Absorption von Luft die Schallausbreitung sehr stark dämpft. Beispielsweise liegt die Dämpfung eines akustischen 2-MHz-Signals in Luft in der Größenordnung von 640 dB/m. 6
In den folgenden Fällen werden mehrere Anwendungen diskutiert. Bei allen Konfigurationen wird der analoge elektrische Ausgang des Sensors in ein Hochgeschwindigkeits-Datenerfassungs- und Analysesystem eingespeist, das eine Echtzeit-FFT-Berechnung und spektrale Anzeige der luftgetragenen Prozessemissionen durchführt.
Laser Metal Deposition (LMD)

Ein häufiges Problem bei LMD-Prozessen ist die Rissbildung durch thermische Belastung. Diese Risse können innerhalb der Verarbeitungszeit, aber auch einige Minuten danach auftreten. Das roboterbasierte LMD-Verfahren, draht- oder pulverbeschickt, ermöglicht die Einhaltung eines konstanten Messabstands. Der Vorteil eines am Roboterkopf montierten luftgekoppelten Akustiksystems ist die Möglichkeit, Signale aus der Laser-Material-Wechselwirkung sowie das Materialverhalten nach dem Lasern zu analysieren. Ein Beispiel für einen Messaufbau mit entsprechender akustischer Signatur ist in Abbildung 2 dargestellt.
Da Risssignale in der Regel breitbandig sind, kann ein Hochpassfilter angewendet werden, um das Auftreten von Rissen während und nach dem Prozess ohne Störung durch Produktionsgeräusche sicher zu erkennen. In diesem Aufbau wurde ein Filter von 350 kHz bis 1 MHz angewendet, der die stärkste Korrelation zu Risszahlen aus zerstörungsfreien Prüfmethoden der Röntgenbildgebung und Wirbelstromprüfung zeigte, wie in Referenz 7 näher beschrieben.
Pulverbettfusion (PBF)

Um die Ultraschallemission während eines PBF-Prozesses aufzunehmen, wurde das optische Mikrofon in der Baukammer etwa 30 cm von der Bauplatte entfernt positioniert, wie in Abbildung 1b gezeigt. Eine typische akustische Prozesssignatur ist in Abbildung 3 dargestellt, die auch den Vorteil der Hochfrequenz-Ultraschallanalyse zeigt, nämlich das Fehlen von Nachhall, der im niedrigeren Frequenzbereich das Signal „verschmieren“ kann, und folglich die überlegene zeitliche Auflösung des Prozesses Veranstaltungen.
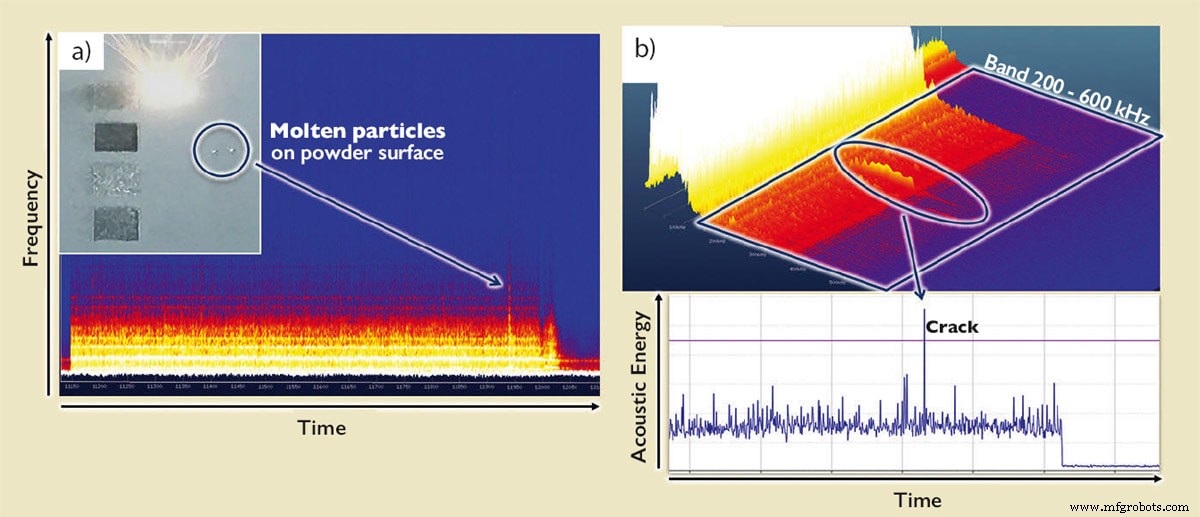
Im Gegensatz zum LMD-Aufbau verwendet PBF Spiegelgalvanometer, um den Prozesslaser über das Pulverbett zu richten. Dieser Vorgang bewirkt eine entfernungs- und frequenzabhängige Dämpfung des Luftsignals, die einem bekannten Zusammenhang folgt und somit bei gleichzeitiger Verfolgung der Laserkoordinaten berücksichtigt werden kann. In vielen Fällen ist es auch nicht erforderlich, einen konstanten Signalmassepegel aufrechtzuerhalten, z. zur Erkennung kurzfristiger spektraler Anomalien. Zwei Beispiele hierfür sind in Abbildung 4 dargestellt:Abbildung 4a zeigt einen Breitbandpeak im Spektrogramm, der von einem Laserdurchgang über ein geschmolzenes Partikel auf dem Pulver herrührt, und Abbildung 4b zeigt ein Risssignal in der 3D-Spektrogrammansicht (oben) und die entsprechende 2D-Energiekurve (unten) integriert über ein Frequenzband von 200-600 kHz.
Wire Arc Additive Manufacturing (WAAM)
Ein ähnlicher Aufbau wie in LMD kann für WAAM-Prozesse angewendet werden (Abbildung 5). Die Signatur des akustischen Signals unterscheidet sich stark, obwohl es bis 600 kHz ebenfalls breitbandig ist. Hauptphänomene sind der Tropfenbildungszyklus (eindeutige Blöcke erscheinen etwa alle 10 ms), ein tonales Signal, das mit der Lichtbogenmodulationsrate (hier:80 kHz) zusammenhängt, und eine breitbandige Prozessemission, die mit der Metallverdampfung zusammenhängt.

Zwei der kritischsten Parameter für den Prozess sind die Stabilität des Lichtbogens und der Formationszyklus. Zur Überwachung ersterer kann ein schmaler Bandpassfilter auf die Modulationsfrequenz und ihre höheren Harmonischen angewendet werden, und für letztere kann eine FFT-Analyse des hochpassgefilterten Zeitsignals durchgeführt werden, um die vergleichsweise langsame Tröpfchenrate zu berechnen frei von Hintergrundgeräuschen.
Schlussfolgerung
Durch die Verfügbarkeit eines membranlosen Breitbandmikrofons für höchste Ultraschallfrequenzen können nun bisher nicht zugängliche Informationen nutzbar gemacht und genutzt werden, um akustische Prozessphänomene in Echtzeit zu überwachen. Zukünftige Entwicklungen beinhalten die Anwendung der Triangulation, damit Schallursprünge lokalisiert werden können, um Bedienern, Verfahrenstechnikern und Maschinenherstellern das Erkennen potenzieller Fehler weiter zu erleichtern. Darüber hinaus wird die Einbeziehung von Onboard-KI-Methoden angestrebt, die sich für akustische Datenströme eignen und die Weiterentwicklung der Technologie hin zu komplexeren, industriellen Überwachungsanwendungen erleichtern.
Bestätigung
Die Autoren danken dem AIMEN Technology Center (Spanien) und Damon Northeast (Renishaw plc) für die Unterstützung.
Referenzen
- D. F. Farson und K. R. Kim:Erzeugung optischer und akustischer Emissionen in Laserschweißfahnen , Journal of Applied Physics 85, 1329 (1999);
- M. Bastuck et al.:Überwachung und Qualitätssicherung des Laserschweißprozesses ultrahochfester Karosseriestähle durch integriertes ZfPVerfahren , DGZfP-Jahrestagung – Mi.2.A.4 (2013);
- J Shao und Y Yan:Überprüfung von Techniken zur Online-Überwachung und -Inspektion des Laserschweißens , Journal of Physics:Conference Series 15, 101–107 (2005)
- S. Everton et al.:Review of in-situ process monitoring and in-situ metrology for metaladditive Manufacturing , Materialien und Design 95 (2016) 0431-445
- Anas Essop, 3D Printing Industry, 10. Dezember 2019, Zugriff am 26. Juni 2020.
- M. Bass, Atmospheric Absorption of Sound, JASA (1990)
- Camilo Prieto et al.:In-situ-Prozessüberwachung durch optisches Mikrofon zur Risserkennung in Laser Metal Deposition-Anwendungen, Messdaten vom AIMEN Technology Center (Spanien) , LANE-Konferenz, Industriebeitrag (2020)
Dieser Artikel wurde von Martin Ursprung, Anwendungstechniker, verfasst; Thomas Heine, Leiter F&E; Balthasar Fischer, CEO; Wolfgang Rohringer, Entwicklungsingenieur; und Ryan Sommerhuber, Anwendungsingenieur, XARION Laser Acoustics GmbH (Wien, Österreich). Für weitere Informationen wenden Sie sich bitte an Herrn Sommerhuber unter Diese E-Mail-Adresse ist vor Spambots geschützt! JavaScript muss aktiviert werden, damit sie angezeigt werden kann. oder besuchen Sie hier .
Sensor
- Flüssige additive Fertigung:Erstellen von 3D-Objekten mit Flüssigkeit
- Additive Fertigung vs. subtraktive Fertigung
- Vorteile der additiven Fertigung
- Verbesserung der additiven Fertigung durch Reverse Engineering
- 5 Tipps für den Erfolg Ihres Unternehmens bei der additiven Fertigung
- Prozess vs. diskrete Fertigung
- 4 Anwendungen, die Sie mit additiver Fertigung herstellen sollten
- Das additive Fertigungsverfahren
- Stratasys:Nachhaltiger sein mit 3D-Druck
- Additive Fertigung in der Luft- und Raumfahrt