Luft- und Raumfahrtbearbeitung nutzt vollständige CAD/CAM/CAE-CNC-Fähigkeit
DMG Mori (Hoffman Estates, IL) liefert Fertigungstechnologien an Luft- und Raumfahrt-OEMs und Produktionswerkstätten, unterstützt durch ein Paket aus CAD/CAM/CNC-Hardware, Software und Engineering-Dienstleistungen von Siemens Industry Inc. (Elk Grove Village, IL) für die Luft- und Raumfahrtbearbeitung. Als langjähriger Partner von Siemens baut DMG Mori eine Vielzahl konventioneller Zerspanungs- und Ultraschall-Bearbeitungszentren.
Für die Luft- und Raumfahrtindustrie sind große Sorgfalt und Planung im Luft- und Raumfahrtbearbeitungsprozess erforderlich, um die gewünschte Genauigkeit und Gesamtproduktionseffizienz zu erreichen. Zu den typischen hergestellten Komponenten gehören solche aus leichten, aber harten Materialien wie Titan und verwandten Legierungen sowie Aluminiumwerkstücke, bei denen ein erheblicher Materialabtrag stattfindet. Aufgrund langer Zykluszeiten und anderer hoher Rohstoffkosten ist die Bearbeitung solcher Komponenten eine Herausforderung.
Zwei aktuelle Anwendungen veranschaulichen, wie DMG Mori sich an Siemens wenden konnte, um die Teileproduktion zu verbessern, einschließlich der Reduzierung von Design-to-Part-Protokollen, der Bearbeitungszeit in der Luft- und Raumfahrt, der Werkzeuglebensdauer, der Oberflächenbeschaffenheit, der Maßgenauigkeit und der Gesamtproduktionseffizienz.
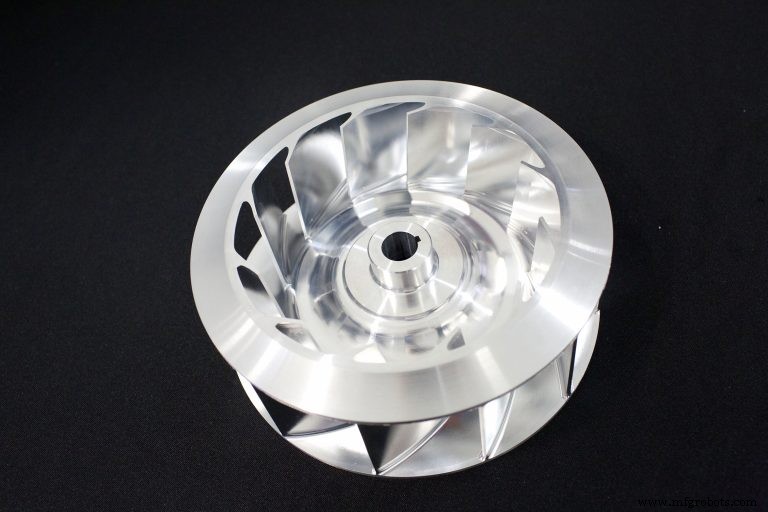
Zunächst sollte eine Schubumkehrkomponente für ein Strahltriebwerk aus Ti Gal-4-V gefertigt werden, einem Material, das aufgrund seiner elastischen Steifigkeit häufig in der Luft- und Raumfahrt verwendet wird. Ausgehend von der CAD-Datei führte das PLM-Team (Product Lifecycle Management) von Siemens das Programm durch sein NX CAM mit einer VoluMill-Zusatzfunktion, die maximale Materialabtragsraten berechnet. Die benutzerdefinierte Ereignisfunktion (UDE) im NX-Programm ermöglicht Kontrollkästchen zum Auslösen von Postprozessorreferenzen für Kühlmitteldruck, Amplitude, Ultraschallgeneratoreinstellungen und mehr. Dies vermeidet manuelles Programmieren und reduziert dadurch die Programmwechselzeit von bis zu zwei Tagen auf ca. 30 Minuten.
Sobald das Programm für die Steuerung bereit war, ermöglichten die Funktionen der Sinumerik 840D sl CNC eine optimierte Simulation des tatsächlichen Schnittpfads. Die 3D-Quick-Set-Compressor-Funktion bietet eine parametrische, aufgeschlüsselte Datendatei für alle Bahnbewegungen, wodurch Kollisionen eliminiert und in Verbindung mit dem NC-Kern und der SPS auf der Werkzeugmaschine der optimale Werkzeugweg sichergestellt wird.
Wie Randy Pearson, Leiter des technischen Anwendungszentrums bei Siemens, feststellte:„Diese Funktion ist eine enorme Zeitersparnis für unseren Kunden, da die Testkugel und der Messtaster im Spindelmechanismus an jedem Punkt des Zyklus laufen können, um die tatsächliche Maschinenkinematik zu testen Jederzeit. Das Verfahren kann auch so automatisiert werden, dass es in vorgeschriebenen Zeitintervallen auf dem Tisch ausgeführt wird.“
Die Hochgeschwindigkeitsbearbeitung wird durch Zyklus 800 hervorgehoben, eine statische Ebenentransformation, die es einer Fünf-Achs-Maschine ermöglicht, eine gedrehte Arbeitsebene im Raum zu definieren. In der Branche ist es allgemein als 3+2-Programmierung bekannt. Der Zyklus rechnet den aktuellen Werkstücknullpunkt und die Werkzeugkorrekturen auf die gedrehte Fläche um. Zu beachten ist hier, dass der Zyklus bestimmte Maschinenkinematiken berücksichtigt und die physikalischen Achsen senkrecht zur Arbeitsebene positioniert. Dies wird als TRAORI oder Transformationsorientierung bezeichnet.
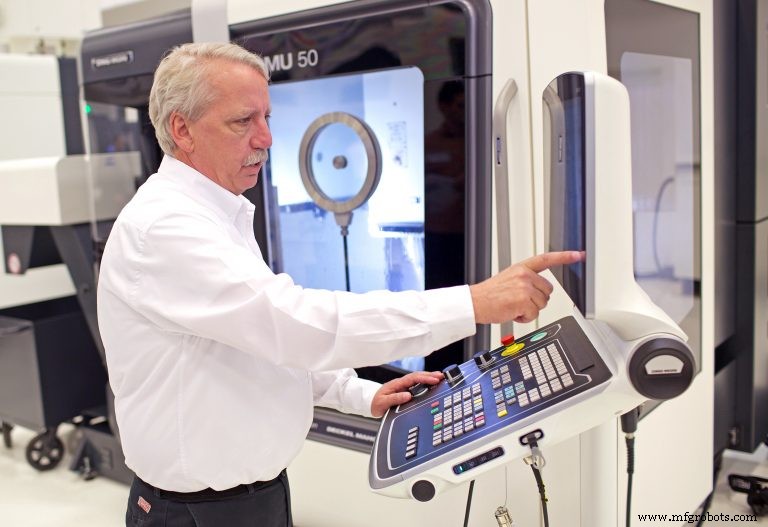
Die Benutzeroberfläche Sinumerik CNC Operate auf der Maschine ermöglicht es dem Bediener, integrierte Werkzeugverwaltungs- und Informationsverwaltungsfunktionen auszuführen, die alle über eine USB- oder Netzwerkverbindung transportiert werden können.
In der Simulation werden das Laden und Fixieren des Werkstücks virtuell in NX CAM durchgeführt, das auch eine konsistente Spanlast berechnet, die bei diesen großen Materialabtragungsanwendungen entscheidend ist. Die Simulation überprüft außerdem die Werkzeuglänge an jedem Schnittabschnitt und das Programm wird für den Start der Maschine fertiggestellt. Es ist buchstäblich so, als würde man mit einem „Digitalen Zwilling“ der Maschine arbeiten.
Während der Produktion führte dieser Prozess zu einer 2,25-fachen Verbesserung der Standzeit bei diesem sehr harten Material, so Luke Ivaska, nationaler Produktmanager bei DMG Mori. „Mit der Kombination aus NX CAM und der Sinumerik 840D sl auf der Maschine und allem, was sie kann, hatten wir einige anfängliche Herausforderungen, da die meisten Softwareprogramme speziell entwickelte CAM-Pakete sind, die von jedem schnell und einfach verwendet werden können. Sie haben jedoch erhebliche Einschränkungen, da die Software den Werkzeugweg steuert und der Bediener nur sehr wenig Kontrolle hat. Mit NX CAM und Sinumerik haben wir viel mehr Einfluss auf die Erstellung des Werkzeugwegs. Ich habe noch kein Problem gefunden, das ich mit NX nicht lösen konnte.“ Als Ergebnis wird das fertige Teil aufgrund des Ultraschallaktors in 4½ Stunden mit einer Verbesserung der Oberflächengüte von 62,5 Ra auf 35 Ra bearbeitet.
Im zweiten Beispiel, einem konventionellen fünfachsigen Spanschneide-Bearbeitungszentrum, wird die DMU 50 der Einstiegsklasse verwendet, um einen 7″ (177,8 mm) Durchmesser × 2″ (50,8 mm) hohen Block aus 6061 Aluminium in einen zu schneiden Laufradlüfter für die Luft- und Raumfahrtindustrie, mit mehr als 90 % Materialabtrag. Dieselbe NX CAM-Software begann mit dieser Prozesskette, mit dem anfänglichen Vorteil erheblicher Zeiteinsparungen bei der Einrichtung der fünf Achsen und einer umfassenden G-Code-Simulation und -Verifizierung in einem einzigen System.
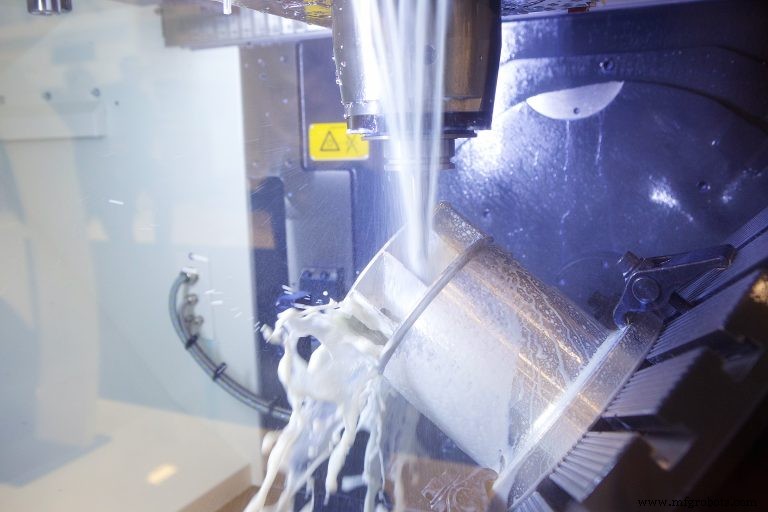
Aufgrund der beschaufelten Struktur dieser Impeller-Lüfterkomponente war während der Bearbeitung nur ein Abstand von 0,5 zwischen dem Teil und dem Werkzeughalter zulässig. Simulation mit NX CAM verhinderte Kollision von Werkzeug und Teil. DMG Mori Engineering wandte sich an einen weiteren langjährigen Werkzeugpartner, Haimer, und seinen schlanken Halter, um eine praktikable Lösung für diese Anwendung bereitzustellen. In der Zwischenzeit wurden die interpolierten Werkzeugachsen und Schnittansichten auf NX CAM ausgeführt, um den Betrieb des Werkzeugs in dem engen Arbeitsbereich zu überprüfen.
Bei der Sinumerik 840D sl sorgte die gleiche 3D-Schnelleinstellungskompressorfunktion für den richtigen Werkzeugweg, während das Hochgeschwindigkeitsbearbeitungs-Setup und der Zyklus 800 für dieses Projekt erneut verwendet wurden. Sinumerik Operate, die grafische Benutzeroberfläche der CNC, bietet dem Bediener des Endbenutzers und dem Fertigungstechniker Zugriff auf die Produktionsbedingungen, einschließlich aller Schrupp- und Schlichtdaten im Klartext sowie aller fünfachsigen Transformationsorientierungsdaten, die für einen Neustart nach jeder Unterbrechung und manuellen Neustart protokolliert werden .
Der variable stromlinienförmige Betrieb der Werkzeugmaschine wird mit einem interpolierten Vektor kombiniert, um eine glattere Oberflächenbeschaffenheit zu erzeugen, wenn Schaufeloberflächen in einem einzigen Werkzeugweg bearbeitet werden. Die Maschine wechselt von der quadratischen zur runden Bearbeitung und dann zu den extremen Winkelpfaden, die erforderlich sind, um die Innenseiten der Schaufeln genau zu bearbeiten. Der Teil des Programms mit einer einzelnen Blattrippe wurde automatisch erfasst, sodass ein Step-and-Repeat-Programm aufgebaut werden konnte.
Die Simulation jedes Blattflossen-Schnittpfads wurde sowohl mit dem NX CAM- als auch mit dem CNC-Programm durchgeführt. Dieses vektorisierte Programm ist mit vergleichbaren Ergebnissen auf jede Maschine übertragbar, so Randy Pearson und Matthias Leinberger, PLM Director of Business Development bei Siemens, die kommentierten:„Gerade weil die Maschinenkinematik bekannt ist, kann dieses einmal erstellte Programm übertragen werden mehrere Maschinen innerhalb derselben Einrichtung oder in Betrieben auf der ganzen Welt, die alle durch die Steuerung miteinander verbunden sind. Es besteht vollständige Kontinuität zwischen den Vorgängen, dem Datenerfassungsprotokoll und dem für die Produktionsanalyse erhaltenen Feedback.“
Beide Projekte wurden mit dem neuen CELOS an Bord der DMG Mori-Maschinen durchgeführt. CELOS erleichtert in diesen Anwendungen die Interaktion zwischen Mensch und Maschine. Es verfügt über zahlreiche Apps, die den sofortigen Abruf von Ist-Zuständen, einen vollständigen Datenabgleich durch eine Verbindung zu CAD- und CAM-Produkten sowie eine vollständige Schnittstelle zum ERP-System des Kundenunternehmens für Protokollierung und Analyse mit Fernanpassung im Prozess ermöglichen. Im Falle dieser Luft- und Raumfahrtkunden wird auch eine interaktive Kommunikation mit einem globalen Produktionsnetzwerk bereitgestellt.
Automatisierungssteuerung System
- um Geld für CNC-Maschinenteile zu sparen
- Was sind die Verwendungszwecke von CNC-Maschinen
- Komponenten von CAM und ihre Rolle in der CNC-Bearbeitung
- CNC-Bearbeitung:Definition und Arten von CNC-Maschinen
- Verschiedene Arten der CNC-Bearbeitung
- 3 Mindset-Änderungen für Lights-Out-CNC-Bearbeitung
- Wie sich KI und maschinelles Lernen auf die CNC-Bearbeitung auswirken
- Vorteile und Grenzen der CNC-Bearbeitung
- Die Vorteile der 5-Achsen-CNC-Bearbeitung
- Was ist CNC-5-Achsen-Bearbeitung?