Automatisierte Kupplung verkürzt Ausfallzeit der Roboterschweißzelle
Es gibt keinen besseren Weg, ein Problem zu lösen, als es vollständig zu beseitigen. So zumindest ist KTH Parts Industries Inc. (St. Paris, OH) prüfte seine Entscheidung, einen manuellen Ausrüstungswechselprozess für seine Roboterschweißzellen zu automatisieren.
KTH wählte GA2-Versorgungskoppler von ATI Industrial Automation (Apex, NC), um das Kunststück zu vollbringen. Insbesondere die neue automatische Kopplung der Luft- und Stromversorgung an die Zellen eliminierte etwa 65 Stunden Ausfallzeit pro Jahr pro Leitung, reduzierte die Gesamtbetriebskosten und erhöhte die Auslastung und Produktivität der Ausrüstung.
KTH Parts Industries, ein globaler Tier-1-Automobilzulieferer für Unterbodenstrukturteile, hat mehr als 1100 Ingenieure und Fertigungsmitarbeiter, die an den vielen Phasen der Herstellung von Automobilteilen beteiligt sind, einschließlich Produktentwicklung, Produktanalyse, Produktformbarkeit, Prototypenbau, Produktionsstanzen, Formen, Roboterschweißen, Montage und Teileversand.
Eine der Kernkompetenzen von KTH ist die Konzeption und Umsetzung von flexiblen Schweißlinien für automobile Unterbodenkomponenten. Seine Schweißlinien verwenden komplexe Vorrichtungen oder Vorrichtungen, um die Komponenten an Ort und Stelle zu halten, während ein Roboter sie zusammenschweißt. Jedes Automodell erfordert eine andere Vorrichtung, was zu vielen Ausrüstungswechseln im Werk führt.
Um die Flexibilität zu erhöhen und die begrenzte Produktionsfläche zu optimieren, hat KTH eine doppelseitige Arbeitszelle mit einem Drehtisch geschaffen. Das Ziel dieses Designs war es, den Roboter aktiv zu halten und die Rüstzeit zu reduzieren. Die Teile werden auf einer Seite des Drehtisches in die Spannvorrichtung geladen, während der Roboter die Teile auf der anderen Seite zusammenschweißt.
Vor der Installation der GA2-Versorgungskupplungen von ATI verließ sich KTH auf Handarbeit, um Kabel anzuschließen und zu trennen und die Vorrichtungen auf die Drehscheiben zu laden. Multiplizieren Sie dies mit ein bis zwei Umstellungen pro Linie und Schicht, und Sie haben eine erstaunliche Menge an Mensch-Maschine-Interaktion in diesem Prozess.
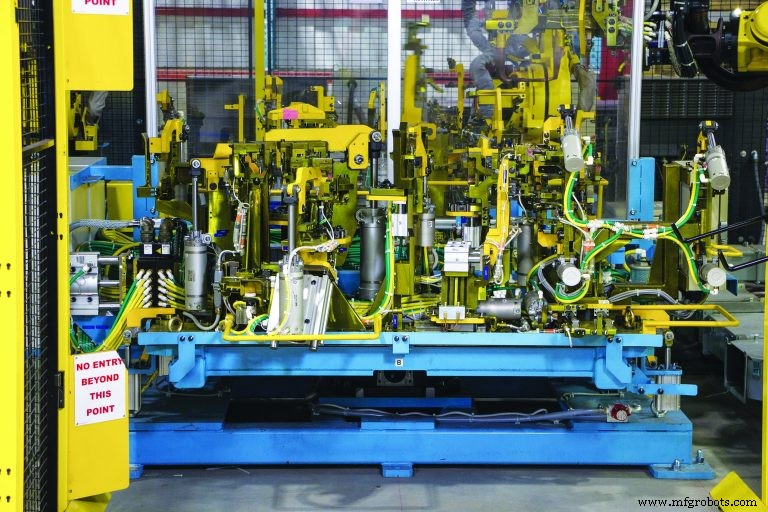
Dave Reed, Projektleiter in der Schweißabteilung von KTH, äußerte sich folgendermaßen zum alten Prozess:„Bevor wir die ATI-Versorgungskupplungen verwendeten, hatten wir eine Luftleitung und einen Verteiler und mussten sie mit Kabelbindern zusammenstecken. Auf der elektrischen Seite mussten wir die 40-Pin-Trenner verbinden, indem wir sie manuell zusammendrehten. Dieser Vorgang wurde viele Male für jeden Vorrichtungswechsel wiederholt.“
Laut KTH waren die körperlichen Arbeitsanforderungen des alten Prozesses sehr hoch, und jedes Mal, wenn ein Mitarbeiter die Arbeitszelle betrat, bestand natürlich ein inhärentes Risiko. Unter diesen Bedingungen war die hohe Häufigkeit von Kabelausfällen keine Überraschung. Das An- und Abkoppeln der Kabel mit ungleichmäßiger Kraft und ungleichmäßigem Drehmoment führte zu übermäßigem Verschleiß. Eine Fehlausrichtung der Steckverbinder führte zu beschädigten Stiften. Ohne einen speziellen Stauraum für nicht verwendete Kabel wurden diese auf dem Boden oder auf anderen Geräten in der Zelle gelassen.
„Wir hatten Luftleitungen, die durchtrennt und undicht waren, Verbindungsstücke, die beschädigt waren“, sagte Reed. „Die Wartung wurde gerufen, um zu versuchen, das Problem einzuschätzen, aber oft war es nur ein verbogener Stift an einem Stecker, der uns stundenlange Ausfallzeiten gekostet hat – etwa 65 Stunden pro Jahr pro Leitung.“
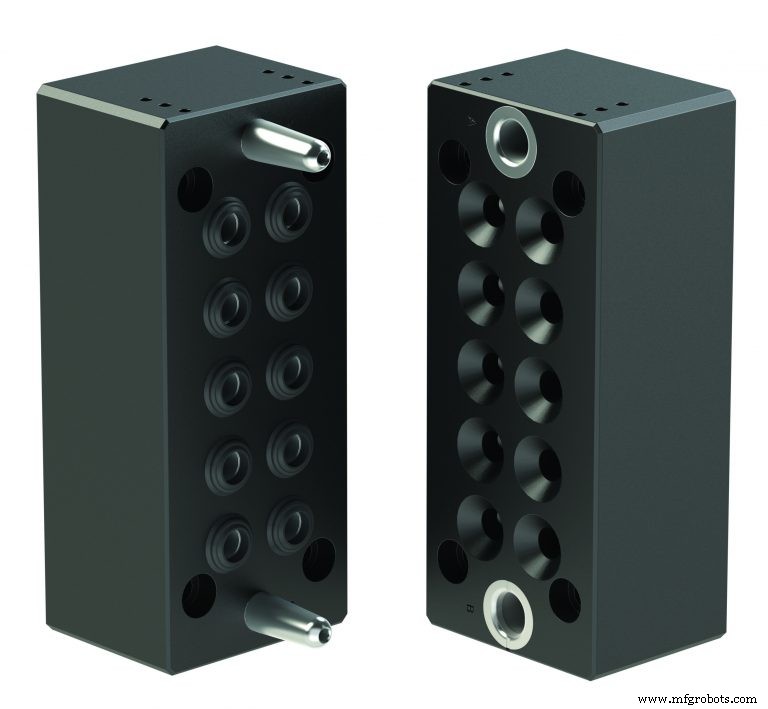
Neben übermäßiger menschlicher Interaktion und Geräteausfällen war der alte Prozess ein Albtraum für die Geräte-Support-Gruppe. Der Sektionsleiter der Gruppe, Jonah Strapp, bemerkte:„Nach einer Umstellung müsste man an irgendetwas in der Zelle herumbasteln, damit sie wieder funktioniert. Ausfallzeiten bedeuten verlorenes Geld. Wenn das passiert, gibt es ziemlich viel Druck, die Leitungen zum Laufen zu bringen.“
KTH war außerordentlich motiviert, den Schweißvorrichtungswechsel zu verbessern, um einen reibungsloseren Arbeitsablauf zu ermöglichen, die Sicherheit der Mitarbeiter zu erhöhen und Geräteausfälle zu reduzieren. Matt Myers, Staff Engineer der Engineering-Projektgruppe von KTH, erklärte:„Während unseres normalen Betriebstages versuchen wir, so viel Produktion wie möglich aus der Linie herauszuholen. Jedes Mal, wenn wir eine Umstellung vornehmen, verlieren wir Produktionszeit, was sich in unseren Büchern in einem großen finanziellen Minus niederschlägt. Alles, was wir tun können, um die Ausfallzeit zu reduzieren, ist wahnsinnig wichtig.“
Das ist genau der Punkt, an dem der Einsatz der Utility-Koppler von ATI eine effiziente und zeitsparende Lösung darstellt. Die Versorgungskupplungen von ATI eignen sich gut für die Umstellung der Schweißlinie von KTH. Sie liefern Strom, Signal und Pneumatik. Die Utility-Kupplungen von ATI verfügen über eine integrierte Rotationsnachgiebigkeit, um eine wiederholbare Kopplung in einem langlebigen Paket zu ermöglichen. Da das Design modular ist, funktionieren die Utility-Koppler mit ATIs umfangreicher Familie von Werkzeugwechsler-Utility-Modulen.
Zusammen bedienen die Versorgungskoppler und -module auch eine Reihe von Netzwerkprotokollen, erklärte Myers von KTH. „Wenn es um das Design neuer Produkte geht, kann ich mich auf das ATI-Engineering-Team verlassen, um schnell ein elektrisches oder pneumatisches Produkt zu entwerfen, das unseren Anforderungen entspricht, oder auf eines der Tausenden von [verfügbaren] Produkten auf ihrer Website verweisen.“ Für dieses spezielle System bei KTH konfigurierte ATI einen Versorgungskoppler und ein elektrisches 32-poliges diskretes I/O-Modul, das einfach in bestehende Leitungen integriert werden konnte.
„Als wir anfingen, den Versorgungskoppler auszuprobieren, war sofort klar, dass er einen großen Unterschied machen würde. Die neuen Koppler sind sehr zuverlässig und freihändig. Wir müssen uns nicht mit ihnen anlegen. Sie funktionieren jedes Mal“, sagte Strapp.
Auf die Frage, wie sich KTH für ATI als Lieferanten entschieden hat, antwortete Myers:„Angesichts unserer früheren Kundendienstbeziehung, der kurzen Lieferzeiten und unseres lokalen Kundenbetreuers war es eine einfache Entscheidung, sich für ATI zu entscheiden.“ KTH ist ein langjähriger Benutzer der robotergesteuerten Werkzeugwechslerprodukte von ATI, daher hat der Übergang zur automatischen Kopplung mit den Utility-Kupplungen von ATI gut funktioniert.
Dave Reed bestätigt die Leistung des ATI GA2 Utility-Kopplers:„Ich habe im letzten Jahr wahrscheinlich Hunderte dieser Vorrichtungen gewechselt, und ich hatte noch nie ein Problem mit dem ATI-System. Sie setzen die Vorrichtung dort ein und drücken den Knopf , es drückt hinein, klemmt, Ihre Stifte sind alle verbunden, Sie haben keine Toleranz gegenüber verbogenen Stiften oder gebrochenen Luftleitungen. Es ist so ziemlich ein makelloses Produkt. Es macht das Leben viel einfacher."
Automatisierungssteuerung System
- Verbessern Sie die Leistung durch automatisiertes Schweißen
- 4 Möglichkeiten zur Verbesserung der Roboterschweißleistung
- Wie Roboterschweißen die Schwerfertigung verändert
- Roboterschweißen:Vermeidung häufiger Ursachen für ungeplante Ausfallzeiten
- Automatisierte Produktion von Ölbohrkupplungen
- Roboterzellen ermöglichen die automatisierte Bereitstellung von Teilen
- Standardisierte FastArc-Zellen erleichtern den Einstieg in das Roboterschweißen
- Heavy-Duty-Roboterschweißzellen können ein großartiger erster Schritt sein
- Automatisierter Widerstandsschweißer:Eine Evolution
- Eine Einführung in den automatischen Widerstandsschweißer