Medizinische Bearbeitung schaltet auf Hochtouren – mit Laserunterstützung
Ob traditionelle Bearbeitung oder hybride Prozesse, die medizinische Fertigung erfordert von Maschinenbauern und Werkzeugmachern, auf Zack zu bleiben
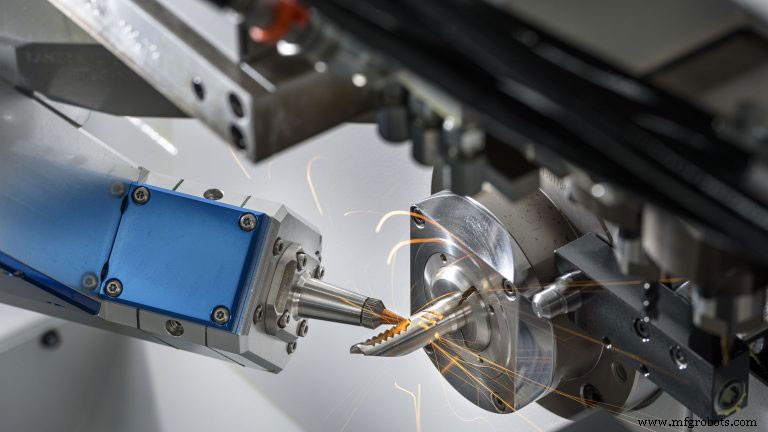
Wenn es um die Bearbeitung der heutigen fein abgestimmten medizinischen Komponenten geht, ist Geschwindigkeit – ganz zu schweigen von Standzeit und Automatisierung – von entscheidender Bedeutung.
Die ständige Weiterentwicklung der medizinischen Bearbeitung vom Werkzeugdesign bis zum fertigen Produkt erfordert nicht nur die Fähigkeit, eine breite Palette von Kunststoff- und Metallmaterialien zu handhaben, sondern auch vorhersagbare Ergebnisse zu erzielen – insbesondere angesichts strenger Vorschriften.
Ob nur Drehen und Fräsen oder hybride Prozesse mit Lasern in Kombination mit Schweizer Systemen, um Schneid- und Schweißoperationen in einer Maschine auszuführen, die medizinische Fertigung erfordert von Maschinenbauern und Werkzeugmachern, auf Trab zu bleiben.
Maximierung der Werkzeuglebensdauer und Teilequalität
Tsugami/Rem Sales LLC (Windsor, CT) hat mehrere Maschinen in seinem Portfolio mit kundenspezifischen Geschwindigkeitsvervierfachungseinheiten ausgestattet, um medizinische Teile und Merkmale so klein wie die Hexalobe in Knochenschrauben zu bearbeiten und gleichzeitig die Werkzeuglebensdauer zu verlängern.
Standardspindeln auf Maschinen im Schweizer Stil drehen angetriebene Werkzeuge normalerweise mit 6000 bis 8000 U/min, sagte Derek Briggs, Schweizer Produktmanager für Tsugami/Rem Sales. „Beim Feinschlichten und fünfachsigen Konturieren, Gravieren oder Ätzen braucht man extrem hohe Drehzahlen, weil die Werkzeuge sehr klein sind; Sie haben normalerweise einen 3,175 mm [0,125″] oder kleineren Kugelkopffräser, mit dem Sie feine Konturen bearbeiten, und Sie schneiden bei diesen Arten von Operationen in der Mitte. Sie benötigen sehr hohe Spindeldrehzahlen, um die Oberflächenlänge auf einem akzeptablen Niveau für die Werkzeuglebensdauer zu halten und die Anforderungen an die Oberflächengüte zu erfüllen.“
Die Lösung von Tsugami ist ein Anbaugerät mit Untersetzung, das die Spindeldrehzahl bis zu viermal vervielfacht, ohne den Spindelmotor zu belasten, um eine optimale Drehzahl wie 20.000 U/min zu erreichen. Tsugami/Rem Sales kann sogar die Hochgeschwindigkeitsspindeln von NSK America integrieren und mit bis zu 80.000 U/min betreiben.
Die meisten Drehmaschinen im Schweizer Stil verwenden einen Getriebezug, der drei oder vier Spindeln gleichzeitig antreibt, wenn der Motor eingeschaltet wird, sagte Briggs. Mit nur einer modularen Spindel mit reduziertem Getriebe, die schneller läuft als die anderen, „belasten Sie die anderen Spindeln nicht. Es ist schön, höhere Spindeldrehzahlen für die feine Oberflächenbearbeitung und kleine Fünf-Achsen-Arbeiten zu bekommen, nach denen der medizinische Markt heute immer mehr verlangt.“
Während ein Standard-Gewindewirbelaufsatz sicherlich ausreicht, sollten Hersteller, wenn eine Maschine den ganzen Tag ausschließlich für die Herstellung von Knochenschrauben verwendet wird, in Betracht ziehen, Keramiklager anstelle von Standard-Stahlrollenlagern anzufordern. Mit Keramiklagern können Bediener die Vorspannung stärker anziehen als bei Stahl, wodurch das System versteift und maximale Spindeldrehzahlen beibehalten werden. Keramiklager dämpfen sehr feine Obertöne und Vibrationen beim Schneiden von Knochenschrauben und können auch die Hitze bei höheren Drehzahlen aufnehmen, wodurch die Wärme viel besser verteilt wird.
Need for Speed
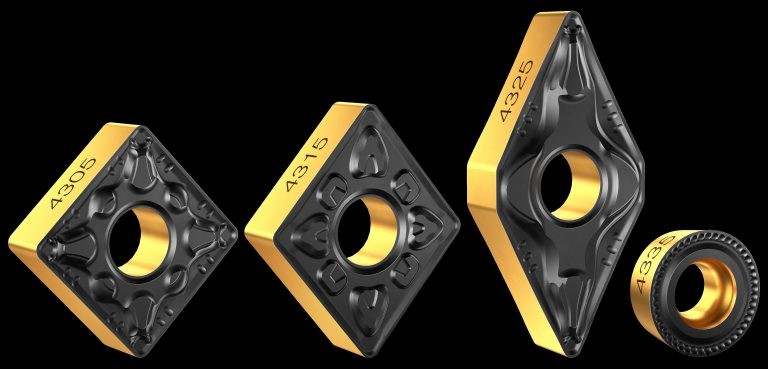
Neben der Maximierung der Spindeldrehzahlen arbeitet Tsugami/Rem Sales auch daran, mehr Schnellwechselfunktionen in die Schweizer Bearbeitung einzuführen. Das Unternehmen bietet angetriebene Werkzeugaufsätze und Mehrfachwerkzeugplatten mit abnehmbaren Köpfen an, mit denen ein Bediener eine Schraube herausnehmen, die gesamte ER-Spannzangenbaugruppe oder Werkzeugkassette entfernen, die Werkzeughöhe außerhalb der Maschine einstellen und ein vorgefertigtes Ersatzteil installieren kann – alles in 30 Sekunden, bemerkte Briggs.
Tsugami/Rem Sales entwickelt neben seinen modularen Werkzeugaufbauten für Planfräsen, Winkelfräsen und Gewindewirbelaufsätze auch schnell wechselbare Revolverhalter für seine Revolverkopfmaschinen. „Diese Halter wurden entwickelt, um Bedienerfehler zu reduzieren, die möglicherweise zu einem Maschinencrash oder gebrochenen Werkzeugen führen könnten. Dies kann auch außerhalb der Maschine auf einem Zoller oder einem anderen Voreinstellgerät erfolgen.“
Eine Tiefbohranwendung lieferte eine Fallstudie zur Verbesserung von Vorschüben und Geschwindigkeiten.
Als Tsugami/Rem Sales ein Hochfrequenzgerät zur Entfernung von Augentumoren entwickeln musste, waren die technischen Daten eine Herausforderung:Das Gerät musste 127 mm (5″) lang sein und ein durchgehendes Loch von 0,06″ (1,52 mm) aufweisen. Dazu wurde das hochfrequente pulsierende TriboMAM-System von M4 Sciences eingesetzt.
Das Gerät aus maßgefertigtem Titan ähnelt einem Vakuum und kann nur den Tumor absaugen, kein anderes Weichgewebe, erklärte Briggs. Typischerweise kann ein Kanonenbohrer nur mit weniger als einem Zehntel Zoll pro Umdrehung zugeführt werden; Die Integration von TriboMAM vervierfacht diese Geschwindigkeit, „weil die Oszillation dieses Werkzeugs Späne in sehr kleine Stücke zerbricht und Hochdruckkühlmittel sie aus dem Loch herauszieht.“ Insgesamt wurde ein Vorgang, der sonst mehrere Minuten gedauert hätte, um 75 % schneller abgeschlossen.
Eine weitere Innovation, die Low-Frequency-Vibration (LFV)-Servosystemtechnologie, „ist einer der größten Fortschritte bei der Bearbeitung von zähen Materialien, die in der Herstellung medizinischer Komponenten verwendet werden“, sagte Jim Cepican, Show Manager für den Zubehörverkauf bei Marubeni Citizen-Cincom Inc. (Allendale , NJ). LFV verbessert die Standzeit, die Spankontrolle und die Bearbeitung von schwer zu bearbeitenden Materialien.
Die Maschinen der L-Serie von MCC „werden von der Mehrheit der medizinischen Hersteller, mit denen wir zusammenarbeiten, wegen ihrer schnelleren Verarbeitungsgeschwindigkeit und verbesserten Programmierfähigkeiten verwendet“, bemerkte Cepican. „Die Anzahl der Achsen hat zugenommen, einschließlich einer B-Achse, die für die Herstellung komplexerer medizinischer Komponenten erforderlich ist.“
Der L12 ist ein besonders guter Verkaufsschlager für den medizinischen Markt, fügte Regional Sales Manager Glen Crews hinzu. „Die geringe Größe und die hohen Spindeldrehzahlen der Maschine machen sie ideal für die Bearbeitung von Miniaturkomponenten medizinischer Geräte. Für alle unsere Maschinen sind auch Optionen zur Reduzierung der Spindelgröße verfügbar, was die Materialhandhabung erleichtert.“
Für die Querbearbeitung und das Endbohren wurden schnellere Spindeln entwickelt, die mit den Standardspindeln der Maschine austauschbar sind, fügte Crews hinzu. „Da sie getriebegetrieben sind, können sie hohe Spindeldrehzahlen mit einem besseren Drehmoment erreichen, als Sie es mit den von vielen Herstellern verwendeten elektrischen oder luftbetriebenen Spindeln erreichen würden.“
Spindel versiert
Letztendlich ist die Verwendung der richtigen eigenständigen elektrisch oder pneumatisch angetriebenen Spindeln entscheidend für die Optimierung von Vorschüben und Geschwindigkeiten für die heutigen medizinischen Anwendungen, sagte Michael Gabris, Industrial Sales Manager bei NSK America Corp. (Hoffman Estates, IL).
„Sie haben vielleicht 20.000 U/min auf einer Fräsmaschine, aber wenn Sie einen Bohrer mit einem Durchmesser von 0,01″ [0,254 mm] haben, werden Sie nicht die Geschwindigkeiten erreichen, die Sie brauchen, um damit richtig zu laufen“, bemerkte er. „Sie können das Werkzeug sehr leicht zerbrechen.“
Tatsächlich entwickelt sich 0,005″ (0,127 mm) zu einem Standarddurchmesser für Vollhartmetall-Schaftfräser und -Bohrer, fügt NSK-Produktmanager Mike Shea hinzu. „Wenn Sie 200 sfm laufen lassen wollen, sind das ungefähr 76.000 U / min, wenn Sie es richtig laufen lassen“, erklärte er. „Auch wenn der [Werkzeug-]Hersteller 100 sfm empfiehlt, sind Sie immer noch knapp unter 40.000 U/min. Unsere Spindeln erfüllen die Anforderungen für die Bearbeitung von Mikro- und Nanoanwendungen, die immer häufiger vorkommen.“
Wenn eine NSK-Spindel das Werk verlässt, hat sie garantiert weniger als 1 μm Unrundheit, sagte Gabris. NSK stellt auch seine eigenen Präzisionsspannzangen her, die auf drei bis fünf Mikrometer genau sind, und bietet kostspielige Keramiklager für alle Hochgeschwindigkeitsspindeln an.
Ob in neue Maschinen eingebaut oder in ältere Maschinen nachgerüstet, „unsere Spindeln erledigen die ganze Arbeit“, sagte Gabris. Die Bediener „müssen die Hauptspindel verriegeln und unsere Spindel mit Strom und Luft versorgen, oder nur mit Luft, wenn es pneumatisch ist“, fügte Shea hinzu. „Die Hauptspindel dreht sich nicht, daher gibt es keinen Verschleiß an der Maschinenspindel. Unsere Spindeln haben keine Zahnräder. Indem sie zum Kühlen und Spülen mit einer kleinen Luftmenge beaufschlagt werden, ist ein Betrieb rund um die Uhr möglich, ohne Wärmeausdehnung oder Oberschwingungsprobleme. Dies ist ideal in einer Situation mit konstant hoher Produktion.“
Umgekehrt, wenn nur ein Speeder-Kopf mit Getriebe verwendet wird, sollte der Speeder nach 20 oder 30 Minuten Gebrauch ruhen, um die Wärme in den Zahnrädern abzuleiten, riet er.
Werkzeuge voranbringen
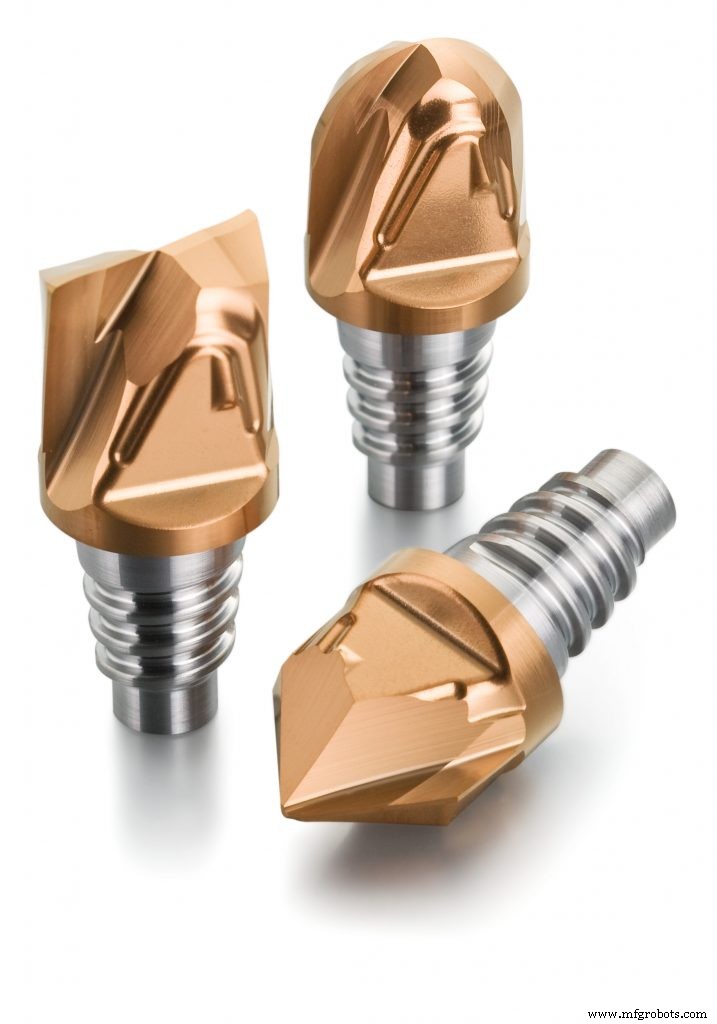
Mit Materialien für medizinische Komponenten, die von Kunststoffen über Kobaltchrom bis hin zu Titan reichen, hat Sandvik Coromant (Fair Lawn, NJ) seine Werkzeuge in den letzten Jahren erheblich weiterentwickelt.
„Ja, es geht darum, Teile schneller zu produzieren und Toleranzen einzuhalten“, sagte Patrick Loughney, Produktmanager für die Kleinteilbearbeitung, „aber es geht auch um die Vorhersagbarkeit des Prozesses und der Werkzeuge.“
Zum Beispiel bei Wendeschneidplatten, „Wir haben unsere Technologie mit unserer Inveio-Beschichtungsinnovation enorm verändert“, bemerkte er, die stärkere Substrate, eine präzisere Kantenbehandlung und eine neue Art der Beschichtung ermöglicht.
„Wir haben herausgefunden, dass die Kristalle in der Beschichtung im alten Verfahren zufällig waren, wo sie nur den Einsatz schützten“, erklärte er. „Jetzt sind wir in der Lage, diese Kristalle in eine Richtung auszurichten, in der wir eine bessere Standzeit und einen besseren Verschleiß der Wendeplatte erzielen können.“ Dies ermöglicht weniger Anpassungen an der Maschine und bietet die vorhersehbare Werkzeugstandzeit, die für einen stabilen Bearbeitungsprozess entscheidend ist. Nachdem der Einsatz geformt ist, wird die Kantenvorbereitung auf Mikrometertoleranzen ausgeführt, sagte er.
„Wir haben unsere Werkzeuge modifiziert, um verschiedene medizinische Funktionen auszuführen“, fuhr er fort. „Unsere medizinische Bohrstange haben wir speziell für die Herstellung der Manschette für Knie- und Hüftgelenke anfertigen lassen.“
Inzwischen wurde das CoroMill 316-Wechselkopf-Frässystem mit erweiterter Schnitttiefe modifiziert, insbesondere für die Herstellung von Knieschienen, die Implantate stützen.
Sandvik Coromant hat auch spezielle Wendeschneidplatten für medizinische Kunststoffe wie Polyetheretherketon entwickelt. „Die meisten Einsätze sind oben gestrahlt, damit der Kunststoff nicht anhaftet“, erklärte Loughney.
Im Oktober wird ein neuer Bohrer speziell für hitzebeständige Materialien in Medizin- und Luft- und Raumfahrtanwendungen Teil der halbjährlichen Messe des Unternehmens sein neue Produktversionen.
Die größte Hürde von Sandvik Coromant sind jedoch Wendeschneidplatten zum Gewindewirbeln. „Meistens haben Knochenschrauben eine spezielle Gewindeform“, bemerkte Loughney. „Es scheint, dass jeder Arzt, der eine Knochenschraube herausgebracht hat, seine eigene charakteristische Gewindeform hat. Daher können wir dafür nicht nur Standardeinsätze verkaufen; sie müssen alle speziell konstruiert werden. Wir müssen sehr flexibel sein, diese Wendeschneidplatten von Fall zu Fall zu schleifen.“
Laser vom Fass
Wenn die herkömmliche Bearbeitung allein nicht ausreicht, verbessert das Hinzufügen eines oder mehrerer Laser zum Prozess die Fertigungskapazitäten erheblich.
Beispielsweise wurde die Werkzeugmaschinenlinie LaserSwiss von Tsugami/Rem Sales für die medizinische Industrie entwickelt. LaserSwiss kombiniert traditionelles CNC-Swiss-Drehen und Laserschneiden in einer Maschine, erklärte Tina Carnelli, Marketingleiterin bei Tsugami LaserSwiss. „Dies bedeutet, dass medizinische Hersteller komplexe medizinische Teile wie Stents mit einer Einrichtung und einem Teileprogramm herstellen können“, sagte sie. „Wir haben die LaserSwiss-Maschine kürzlich um einen zweiten Laserkopf zum Schweißen erweitert, um drei Arbeitsgänge effektiv auf einer Maschine zu kombinieren.“
Bei Marubeni Citizen-Cincom „ist die Einführung des Laserschneidens und -schweißens auf unseren Maschinen eine der bedeutendsten Änderungen, die wir vorgenommen haben“, sagte Regional Sales Manager Rich Kuhn. „Die Möglichkeit, Bearbeitungsarbeiten und Laserschneiden in derselben Maschine durchzuführen, hat einen großen Einfluss auf die Verringerung der Anzahl der Arbeitsgänge, die zur Herstellung eines Bauteils erforderlich sind. Das Hinzufügen von Automatisierung und Laserschweißen hat unseren medizinischen Kunden zusätzliche Möglichkeiten zur Lösung einiger der ständig wachsenden Anforderungen an hohe Toleranzen ermöglicht.“
Natürlich sind Laser seit einiger Zeit eine eigenständige medizinische Fertigungslösung. Laut Salay Quaranta, Branchenmanager bei Trumpf Inc. (Farmington, CT), wird das Portfolio von Trumpf beispielsweise von Herstellern medizinischer Geräte in großem Umfang genutzt, von Laserschweiß- und Feinschneidanwendungen bis hin zu additiver Fertigung und Lasermarkierung für die Rückverfolgbarkeit.
Die additive Fertigung oder der 3D-Druck habe Trumpf zahlreiche Möglichkeiten eröffnet, fügte sie hinzu. „Der Bau verschiedenster Zahnkronen, Brücken und RPDs mit unserem TruPrint 1000 ermöglicht Herstellern die generative Fertigung kleinster Einzellosteile und Serien auf der Platte. Mit einer Multilaser-Option kann die Produktion um bis zu 80 % gesteigert werden, während gleichzeitig die Flexibilität zur Bearbeitung von Kundenaufträgen erhalten bleibt. Auch komplexe Formen lassen sich schnell und einfach aus der CAD-Konstruktion in ein 3D-Metallbauteil in Top-Qualität umwandeln.“
Es ist diese Designflexibilität, die Laser von der herkömmlichen Bearbeitung abheben kann, wenn es um die metallbasierte, Schicht-für-Schicht-Pulverbettproduktion geht.
„Durch die Nutzung der Techniken für das Design mit 3D-Druck kann ein Hersteller oder Labor ein Produkt nahezu in Endform bauen“, sagte Quaranta. „Es gibt sehr wenig Ausschuss wie bei der traditionellen Bearbeitung, und die Metallurgie ist solide. Hersteller können diese Plattformen nutzen, um eine Vielzahl von Komponenten zu bauen, von Implantaten und Zahnkronen bis hin zu Gerüsten und Konstrukten für viele Anwendungen.“
Mehr Automatisierung bei sekundären Operationen
Strenge Vorschriften, die jeden Aspekt der Herstellung medizinischer Komponenten regeln, und die Notwendigkeit, einen stabilen, vorhersehbaren Prozess zu gewährleisten, scheinen ihn ideal für die Automatisierung zu machen. Laut Loughney von Sandvik Coromant stellt diese starre Aufsicht jedoch ein Rätsel dar. Sobald ein Prozess festgelegt ist, kann es äußerst schwierig und zu zeit- oder kostenineffizient sein, ihn zu ändern – selbst wenn eine Material- oder Prozessinnovation in den Startlöchern wartet.
„Wir sehen mehr Automatisierung in der medizinischen Fertigung, aber der Großteil betrifft die Sekundäroperationen, die nicht so stark kontrolliert werden, wie das Schleifen eines Angusses von einem Schmiedestück“, sagte er. „Wir sehen, dass neuere Dinge wie Hüftschäfte automatisiert hergestellt werden.“
Bei medizinischen Komponenten, die normalerweise in Chargen mit häufigen Umstellungen hergestellt werden, sind Verantwortlichkeit und Rückverfolgbarkeit von größter Bedeutung, fuhr er fort. „Es ist ein bisschen schwieriger, so etwas zu automatisieren. Aber es ändert sich; die Systeme und Software verbessern sich dahingehend, dass sie besser nachverfolgt werden können.“
Auf einen anderen Trend, den anhaltenden Vorstoß in Richtung Industrie 4.0, reagieren Maschinenbauer mit zahlreichen Innovationen.
Auf Anfrage wird Rem Sales Maschinen von Tsugami Swiss mit FANUC-Robotik zum Be- und Entladen von Teilen, Keyence-Vision-Systemen für In-Prozess-Messungen und Autokompensation für die Automatisierung von Offset-Anpassungen im laufenden Betrieb integrieren, sagte Briggs. „Wir ziehen ein Teil mit einem Roboter vom Förderband aus der Maschine, richten es aus und platzieren es in einer Halterung am Messgerät. Wenn gemessene Abmessungen außerhalb der Toleranz liegen, gleicht das AutoComp-System von Caron Engineering die laufende Maschine automatisch aus, und der Roboter legt das schlechte Teil in einen separaten Behälter, um sicherzustellen, dass keine schlechten Teile mit guten vermischt werden.“
Für die Kunden von heute „können wir nicht einfach eine einzige Maschine zur Bearbeitung von Teilen bereitstellen“, erklärte Cepican von MCC. „Wir müssen komplette Verarbeitungssysteme liefern. Dazu gehören hochtechnische Automatisierungssysteme.“ MCC hat mehrere automatische Lade- und Entladesysteme entwickelt – zum Beispiel Systeme, die Rohteile in Maschinen laden, um sie mit einem Laserschweißen an eine bearbeitete Komponente zu schweißen.
George Bursac, General Manager von Star CNC Machine Tool Corp. (Roslyn Heights, NY), fügte hinzu:„Die Automatisierung ist seit einiger Zeit Teil der medizinischen Fertigung und wird aufgrund neuer Anforderungen erweitert.“ Während medizinische Komponenten wie Knochenschrauben, Zahnimplantate, chirurgische Instrumente und andere mit diesen Produkten verbundene Komponenten „ohne viele Änderungen gleich bleiben“, sagte er, „reagiert unser Team auf alle neuen Herausforderungen, die Fertigungsunternehmen möglicherweise benötigen.“
Automatisierungssteuerung System
- CNC-Werkzeugmaschine
- 15 Vorteile von Laserschweißgeräten
- Vielfalt der Werkzeugmaschinenautomatisierung auf der Ausstellung
- 8 wichtige Taktiken für die medizinische Präzisionsbearbeitung
- Unterricht in Hochleistungsbearbeitung:Werkzeughalter nicht vergessen
- Medizinische Bearbeitung:Hersteller von Schneidwerkzeugen bieten Einblicke und Ratschläge für den Erfolg
- Auftragseingänge für Werkzeugmaschinen gehen im September zurück
- Fuji stellt Multitasking-Maschine vor
- Methods Machine Tools zur Übernahme von Koch Machine Tool
- Bearbeitungsprozess und Werkzeugmaschine verstehen