Wenn es um Simulationssoftware geht, ist Sehen Glauben
Müde vom Fahren auf dem roten Knopf? Simulationssoftware ist der Schlüssel zu sichereren und kürzeren Maschineneinstellungen.
In einer perfekten CNC-Welt ist der erste Teil immer gut. Es sind keine zusätzlichen Rohlinge oder Stangenmaterial erforderlich. Die Rüstzeiten sind nur so lang, wie es nötig ist, um ein paar Werkzeuge auszutauschen und ein neues Programm zu laden. Es gibt nie einen Absturz, nie die Notwendigkeit, ein ineffizientes Stück Code neu zu programmieren. Der Bediener drückt einfach den grünen Knopf und Minuten oder Stunden später kommt ein fertiges Werkstück heraus.
Was ist die magische Technologie, die diese Welt möglich macht? Es heißt Simulationssoftware, und obwohl es nur sehr wenige Geschäfte in den oben beschriebenen Zustand des Fertigungs-Nirwanas gebracht hat, ist es ein wichtiger Schritt in diese Richtung.
Indem Programmierern die Möglichkeit gegeben wird, alles über den Bearbeitungsprozess zu simulieren – die Werkzeughalter, Spindeln und Revolver, das sich ständig ändernde Werkstück und die sich um und durch es bewegenden Schneidwerkzeuge – machen Softwareentwickler ihre virtuellen Welten zu hochgenauen Vorhersagen für alles, was passieren wird sobald dieser grüne Knopf gedrückt wird. Das Endergebnis ist klar; Wenn Ihre Werkstatt keine Werkzeugweg-Simulationssoftware verwendet, um ihre NC-Programme zu prüfen, verschwenden Sie nicht nur wertvolle Produktionszeit, sondern gefährden auch teure Werkzeugmaschinen und Ihre Sicherheitsbilanz.
Versicherung abschließen
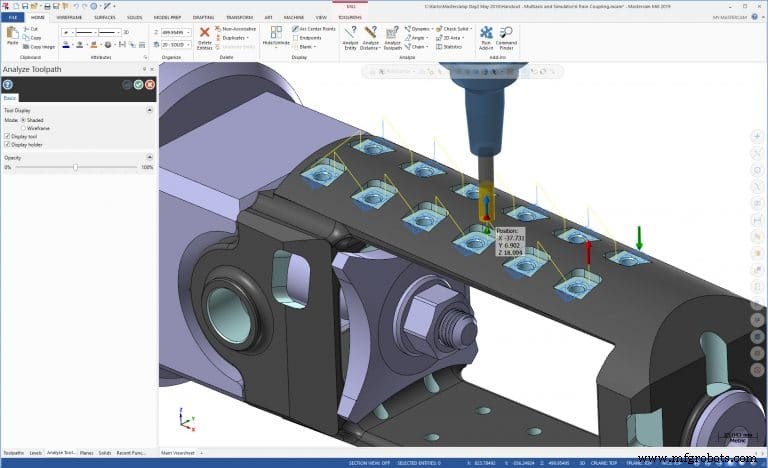
Aber Moment mal – unsere CAM-Software verfügt bereits über Simulationsfunktionen, werden Sie denken. Warum sollten wir zusätzliches Geld investieren, wenn unser aktuelles System die Arbeit erledigen kann? Laut Ben Mund, Senior Market Analyst beim Mastercam CAD/CAM-Entwickler CNC Software Inc. (Tolland, CT), könnte es einige sehr gute Gründe dafür geben.
„Die meisten CAM-Systeme bieten heute ein gewisses Maß an Werkzeugwegsimulation, das für die meisten Bearbeitungsanwendungen vollkommen akzeptabel ist“, sagte er. „Der Unterschied zwischen dieser und dedizierter Simulationssoftware besteht darin, dass CAM-Pakete in der Regel nicht den tatsächlichen nachbearbeiteten G-Code lesen, der von der Werkzeugmaschine verwendet wird. Aus diesem Grund bietet die eigenständige Werkzeugwegsimulation eine zusätzliche Sicherheitsebene für extrem hochwertige Jobs und komplexe Bearbeitungsanwendungen. Es ist wie der Abschluss einer Versicherung.“
Wie bei allem anderen in der Fertigung wird CAM-Software jedoch immer leistungsfähiger, und dazu gehört auch die Fähigkeit, einen größeren Teil des Bearbeitungsprozesses zu simulieren – wo einst grobe Drahtgittermodelle des Schneidwerkzeugs und des Werkstücks die Norm waren, bieten Mastercam und andere jetzt überraschend realistische Ergebnisse Darstellungen der gesamten Bearbeitungsumgebung, einschließlich der Werkstückspannung, der Werkzeughalter und sogar der CNC selbst.
Mund setzt diese Entwicklung mit der allmählichen Konvergenz von CAD und CAM gleich – wo die beiden einst völlig getrennte Produkte waren, wird CAM heute sehr CAD-ähnlich und umgekehrt.
„Viele Betriebe brauchen kein eigenständiges CAD-System mehr, weil ihr CAM-Paket alles erledigt, was sie brauchen“, sagte er. „Es ist eine sehr ähnliche Situation mit Maschinen- und Werkzeugweg-Simulationssoftware – CAM bietet vielleicht nicht die gleiche Verifizierungstiefe, aber auch hier erfüllt es die Aufgabe, es sei denn, Sie möchten dieses zusätzliche Maß an Sicherheit – und entwickelt sich ständig weiter.“
Durchpowern
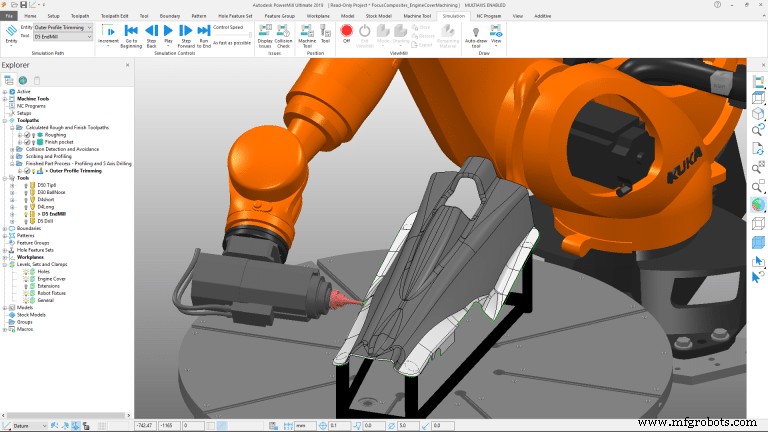
Craig Chester, PowerMill-Produktmanager bei Autodesk Inc. (San Rafael, CA), stimmt Munds Einschätzung zu. „Sehr wenige unserer Kunden verwenden spezialisierte Simulationspakete, da sie von der Zuverlässigkeit ihrer CAM-Simulation überzeugt sind“, sagte er.
Der kleine Prozentsatz der Kunden, die in Standalone-Pakete investieren, tun dies normalerweise, weil sie mehrere CAM-Lösungen haben, möglicherweise von verschiedenen Anbietern, und eine einzige, spezialisierte Lösung konsistente Ergebnisse liefert, erklärte Chester. Dies sind in der Regel größere Kunden wie Luft- und Raumfahrt- oder Verteidigungsunternehmen, die auch unterschiedliche CAM-Pakete für ihre Fräs-Dreh-Drehmaschinen, fünfachsigen Bearbeitungszentren, Erodiergeräte usw. verwenden.
Ironischerweise kann der größte Vorteil einer eigenständigen Simulationssoftware – die Fähigkeit, Maschinen-G-Code zu lesen – auch ihre Achillesferse sein.
„Der Nachteil der Simulation außerhalb des CAM-Programms besteht darin, dass der Benutzer Probleme erst entdeckt, nachdem das Teil programmiert wurde“, betont Chester. „Wenn der Fehler früh im Bearbeitungsprozess auftritt, müssen viele nachfolgende Werkzeugwege neu programmiert werden. Aber indem alles im CAM-Programm simuliert wird, können diese unnötigen und kostspieligen Neuberechnungen vermieden werden.“
Aber nicht so schnell. Tom McCollough, Director of Product Management in der CAM- und Hybrid-Fertigungsgruppe von Autodesk, stimmt zu, dass die integrierte Simulation Programmierern die Möglichkeit gibt, die Auswirkungen von Werkzeugwegänderungen schnell zu bestimmen, fügte jedoch hinzu, dass dies keine allumfassende Lösung für eine Reihe von Unternehmen.
„Stellen Sie sich vor, Sie hätten ein sehr großes Automobilwerkzeug wochenlang geschruppt und vorgeschlichtet, nur um in der Endphase in den Werkstoff zu krachen und sowohl das Teil als auch die Spindel zu beschädigen“, sagte er. „Dies kann nicht nur den betreffenden Auftrag, sondern auch andere Aufträge (für andere Kunden) in der Warteschlange beeinträchtigen. Die potenziellen Auswirkungen sind enorm, weshalb Hersteller hochwertiger Komponenten motiviert sind, eine „zweite Meinung“ von einer unabhängigen Software einzuholen.“
Die G-Code-gesteuerte Simulation in NX CAM von Siemens verwendet dieselben NC-Programme, die Werkzeugmaschinen antreiben. Laut Siemens hilft die hochpräzise Simulation Unternehmen dabei, Fehler zu beseitigen, die Teilequalität zu verbessern und die Maschinenverfügbarkeit zu erhöhen.
Tu mir was Gutes
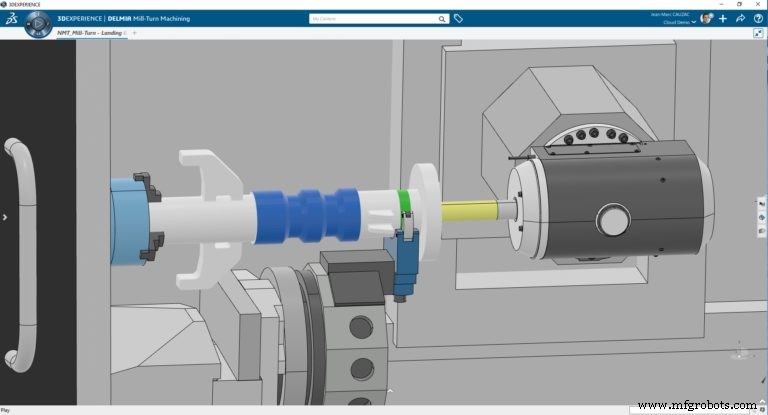
Ähnliche Empfehlungen gibt Jean-Marc Cauzac, Rollenmanager für DELMIA bei Dassault Systèmes (Waltham, MA). Wie die anderen für diesen Artikel befragten Softwareanbieter bieten die CAM-Produkte von Dassault Systèmes genaue, realistische Simulationsmöglichkeiten mit vollständigen 3D-Darstellungen der Werkzeugmaschine, einschließlich Spannvorrichtungen, Spannfutter und Backen sowie Indexierköpfen.
Laut Cauzac ist dies für die Mehrheit der Teilehersteller ausreichend, da die meisten Kollisionsprobleme lange vor der Generierung des Maschinencodes beseitigt werden können (und sollten). „Ein integriertes System ermöglicht es, alle Zugänglichkeits- und Erreichbarkeitsherausforderungen sehr früh in der Programmdefinition zu überprüfen, einschließlich Werkzeugwegfehlern wie schnelles Einfahren in das Material oder übermäßig aggressive Schnittparameter sowie mögliche Kollisionen zwischen einem der gerade aufgeführten Elemente .“
Cauzac stellte jedoch fest, dass die integrierte CAM-Simulation in gewisser Weise begrenzt ist:Einige Kunden wollen Simulationen nicht glauben, die von der Software kommen, die den Werkzeugweg erstellt, weil sie befürchten, dass der Softwareanbieter nicht sowohl Richter als auch Jury sein kann.
Wenn der Kunde mehrere CAM-Lösungen in seiner Einrichtung verwendet, wird ein einziges externes Simulationsprogramm – vorausgesetzt, es verfügt über eine genaue Schnittstelle zur CAM-Software – bevorzugt, da es eine einheitliche Validierung bieten kann.
Spezialisierte Simulationssoftware ist oft umfassender als CAM-basierte Simulation, die eher werkzeugwegorientiert ist und die vorgefertigten Zyklen und Unterroutinen nicht berücksichtigt, die auf den meisten Steuerungen verwendet werden.
Abgesehen von den Argumenten für externe Simulationssoftware schlug Cauzac vor, dass integrierte Systeme sowohl schneller als auch weniger fehleranfällig seien. „Sie bieten eine perfekte digitale Kontinuität, da alle in der Simulation verwendeten 3D-Elemente dieselbe Quelle haben“, sagte sie. „Eine Datenübertragung zwischen zwei Systemen, die zusätzlichen Aufwand und Informationsverluste mit sich bringt, entfällt.“
Nutzen Sie die Macht
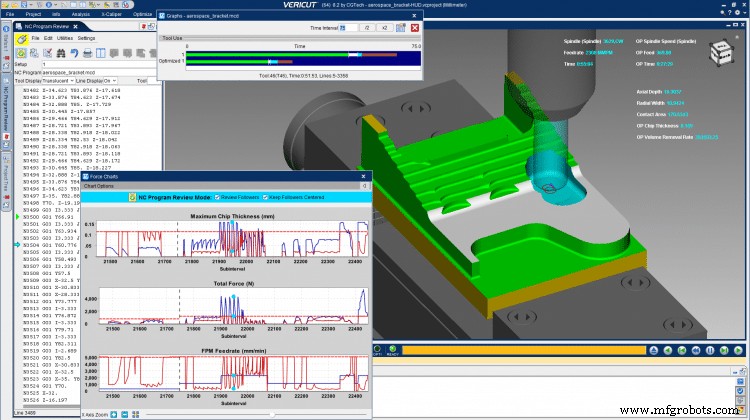
Wie Ben Mund von Mastercam bereits erwähnt hat, ist das Lesen des von der Maschinensteuerung verwendeten Codes möglicherweise das Hauptunterscheidungsmerkmal zwischen eigenständiger und integrierter Simulationssoftware. Jemand, der zu diesem Thema viel zu sagen hat, ist Gene Granata, Produktmanager für VERICUT Toolpath Simulation and Verification Software CGTech Inc. (Irvine, CA).
„Einige Leute versuchen, den Wert der Simulation durch Dritte zu zerstreuen, indem sie behaupten, sie sei unnötig oder übertrieben“, sagte er. „Aber um einen digitalen Zwilling der Werkzeugmaschine und des Bearbeitungsprozesses zu erhalten, müssen Sie Dinge wie Fünf-Achsen-Kompensation, Werkzeuglängen- und Vorrichtungsversätze, Makros und Unterprogramme und die tatsächliche Bewegung des Schneidwerkzeugs im Positioniermodus berücksichtigen. Elemente, die nicht berücksichtigt werden, wenn interne Anweisungen des CAM-Systems zum Erstellen der Simulation verwendet werden.“
Während der Streit darüber tobt, ob Werkstätten dieses Maß an Simulationsgenauigkeit benötigen, weist Granata schnell auf etwas hin, das sie benötigen:Optimierung. „Es ist eine Welt da draußen, in der Hund frisst, und im Geschäft zu bleiben, basiert oft auf hauchdünnen Gewinnmargen. Zu diesem Zweck liegt ein großer Fokus auf der Werkzeugwegoptimierung.“
Für Granata geht es bei der Optimierung nicht um CAM-spezifische Routinen, die sich auf eine effektive Taschenreinigung und konstante Spanlasten konzentrieren, obwohl dies zugegebenermaßen notwendige Teile der Bearbeitungsgleichung sind. Wichtiger sei es, sagte er, Wege zu finden, um Werkzeugwege zu optimieren, basierend auf den Möglichkeiten der Werkzeugmaschine, angesichts des Werkstückmaterials und der verwendeten Schneidwerkzeuge.
Hier kommt Force ins Spiel, ein Softwaremodul innerhalb der VERICUT-Suite, das die Werkzeugwegsimulation und die CAM-Software gleichermaßen ergänzt, unabhängig davon, wessen Logo auf der Verpackung steht.
„Dies stellt eine völlig neue Ebene der Industrie 4.0-Programmierintelligenz dar, und CGTech sowie andere Softwareentwickler kratzen wirklich nur an der Oberfläche dieser Fähigkeit“, sagte er. „Jeder Hersteller von Schneidwerkzeugen wird Ihnen sagen, dass seine Werkzeuge härter beansprucht werden können und Optimierung der beste Weg ist, dies zu erreichen.“
Lesen des G
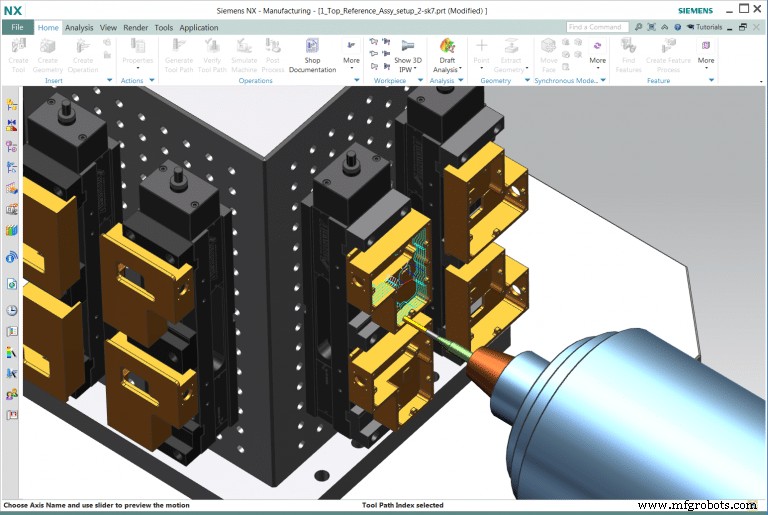
Auf dem Grat zwischen eigenständiger und integrierter Simulation liegt Siemens PLM Software Inc. (Plano, TX), das einer der ersten Partner von CGTech war und diese Rolle auch heute noch einnimmt. Aber wie Vynce Paradise, Senior Director for Advanced Part Manufacturing bei Siemens, erklärte, entschied sich das Unternehmen im Laufe der Zeit, eine eigene Spin-on-Simulation zu entwickeln, die ein integraler Bestandteil seiner NX CAM-Software ist.
„Es gibt viele gute CAM-Systeme und alle bieten ein gewisses Maß an Werkzeugwegsimulation, aber es ist wichtig zu erkennen, dass mehrere Ebenen verfügbar sind“, sagte er. „Es gibt die grundlegende Simulation, in der Sie das Rohteilmodell, das Schneidwerkzeug und vielleicht den Werkzeughalter sehen können, die sich jeweils relativ zueinander bewegen. Wir nennen das Werkzeugwegüberprüfung, und obwohl es nützlich ist, ist es nur ein Ausgangspunkt.“
Gehen Sie noch einen Schritt weiter und Sie haben eine echte Maschinensimulation, den „digitalen Zwilling“, den Granata von CGTech erwähnt hat, und ein Begriff, mit dem jeder bei Siemens vertraut ist. „Darauf konzentrieren wir uns heute“, betonte Paradise. „Es geht über die gerade beschriebenen Grundlagen hinaus und umfasst alle Aspekte des Bearbeitungsaufbaus, jeder mit seiner eigenen Kinetik und relativen Bewegung. Viele CAM-Systeme zeigen dies heute, aber was bei unserem anders ist, ist, dass wir NC-Code on-the-fly posten und ihn für die Simulation in NX CAM verwenden, um eine Lösung zu bieten, die das Beste aus beiden Welten bietet.“
Paradise bot die folgende Analogie an:Wenn Sie Airline-Pilot werden möchten, würden Sie lieber in einem Flugsimulator lernen, der generische Flugsimulationssoftware verwendet, oder in einem, der die Steuerungsumgebung des tatsächlichen Flugzeugs genauer nachbildet? „Die CAM-integrierte Simulation unter Verwendung des tatsächlichen G-Codes ist letzterem sehr ähnlich und bleibt die vollständigste Methode, um nachzubilden, was während des Bearbeitungsprozesses passieren wird.“
Sprung nach vorn
Spring Technologies Inc. (Boston), das Anfang dieses Jahres vom Technologielösungsanbieter Hexagon übernommen wurde, ist ein weiterer Entwickler von Simulations- und Verifizierungssoftware für CNC-Maschinen. General Manager Silvère Proisy stimmt mit seinen Kollegen über die Vorzüge der Werkzeugwegoptimierung und G-Code-Validierung überein, fügte jedoch einige andere Überlegungen für diejenigen hinzu, die möglicherweise mit einem dieser Softwaresysteme in die Reifen treten.
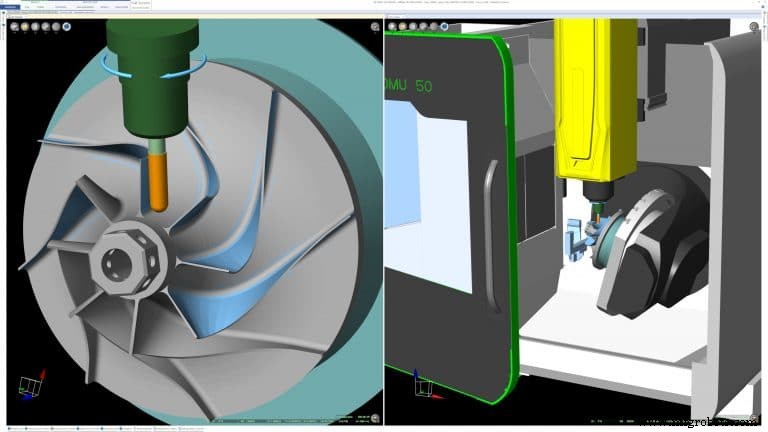
Erstens ist die Simulation nicht nur etwas für Werkstätten mit hochkomplexen Werkzeugmaschinen oder teuren Teilen. „Natürlich sind unsere Hauptkunden diejenigen mit Mehrkanal-Drehmaschinen und fünfachsigen Bearbeitungszentren, aber wir sehen eine Zunahme von Betrieben, die ihre NC-Programme optimieren möchten, und dazu gehören auch solche mit einfachen zwei- und dreiachsigen Maschinen “, sagte Proisy. „Und obwohl es sich niemand leisten kann, irgendein Investitionsgerät zum Absturz zu bringen, sind es die kleineren Geschäfte, die am stärksten betroffen sind, wenn dieses unglückliche Ereignis eintritt. Unsere NCSIMUL-Software eliminiert dieses Risiko.“
Die Werkzeugwegoptimierung mit der Werkzeugweg-Simulations- und Verifizierungssoftware Vericut von CGTech basiert auf prognostizierten Schnittkräften und trägt dazu bei, die Werkzeuglebensdauer zu verbessern und Vibrationen zu beseitigen, die zu Rattern führen, so das Unternehmen.
Mit der Werkzeugwegsimulation wissen Programmierer immer, wo das Werkzeug war und wohin es als nächstes geht, wie in diesem Mastercam-Modul.
Zu den Kritikern, die vorschlagen, dass die Verwendung einer eigenständigen Simulationssoftware sowohl zeitaufwändig als auch fehleranfällig ist, sagte Proisy, dass Benutzer die Automatisierung als nächsten Schritt in der Werkzeugwegsimulation in Betracht ziehen sollten; Durch die Installation von NCSIMUL auf einem Server, der mit dem Werkstattnetzwerk verbunden ist, ist es möglich, Werkzeugwegdateien an eine „Blackbox“ zu senden und sie automatisch überprüfen zu lassen – sofern kein Problem vorliegt, besteht die einzige Anstrengung darin, den per E-Mail gesendeten Bericht zu lesen, der den G-Code enthält gut zu gehen. Dies ist nur der erste Schritt auf dem Weg der Automatisierung.
Laut Prosiy ist die Software seines Unternehmens derzeit in der Lage, NC-Programme für den Einsatz in anderen Werkzeugmaschinen nachzubearbeiten, und zwar „auf Knopfdruck“. Für die Zukunft stellt er sich eine flexible, aber intelligente Schnittstelle vor, die diesen Schritt automatisch erledigt, je nachdem, welcher Maschine der Auftrag zugewiesen wurde.
„Der dritte Punkt ist die Konnektivität“, sagte er. „Dank unserer Partnerschaft mit Hexagon gehen wir davon aus, dass wir bald in der Lage sein werden, Daten von Sensoren an der Werkzeugmaschine abzurufen und diese Werte zu verwenden, um das Programm im laufenden Betrieb zu aktualisieren. Dies können Werkzeuglängenversätze oder Befestigungspositionen sein, oder es könnte sich um Rückmeldungen zu Spindellasten und Vibrationen handeln. Wir sind noch nicht so weit in Industrie 4.0, aber es ist definitiv etwas, das kommt.“
Das Sim-Puzzle lösen
Auch Jeff Fritsch, Vice President of Sales and Marketing bei CAMplete Solutions Inc. (Kitchener, ON), hat Industrie 4.0 und das IIoT (Industrial Internet of Things) im Visier. Die TruePath-Software des Unternehmens „bietet alles, was zum Analysieren, Modifizieren, Optimieren und Simulieren von fünfachsigen Werkzeugwegen in einer integrierten 3D-Umgebung erforderlich ist“, während seine Lite- und TurnMill-Produkte ähnliche Funktionen für dreiachsige Fräsmaschinen bzw. Drehmaschinen mit angetriebenen Werkzeugen bieten.
In Bezug auf die Funktionalität von Industrie 4.0 ist es jedoch das Intelligent Protection System (IPS) von CAMplete, das den klarsten Indikator für die Richtung bietet, die die Fertigungsgemeinschaft einschlägt. IPS wurde in Zusammenarbeit mit dem Maschinenbauer Matsuura entwickelt und nutzt die Simulationsfunktionen von TruePath, um eine intelligente Vorausschau basierend auf prozessinternen Maschinendaten bereitzustellen. Das Ergebnis ist eine nahezu crashsichere Maschinenumgebung, auch im manuellen Betriebsmodus, so Fritsch.
In Anbetracht des zunehmenden Einsatzes komplexer Fräs-Dreh-Drehmaschinen und Multitasking-Maschinen ist eine genaue Bearbeitungssimulation, wie sie DELMIA von Dassault Systèmes bietet, wichtiger denn je.
Wie bei anderen Simulationssystemen liest TruePath den G-Code und überprüft, ob er sicher in der Maschine ausgeführt werden kann“, sagte er. „Aber am Ende des Tages kann niemand sicherstellen, dass der Bediener tatsächlich das richtige Werkzeug in die Spindel einsetzt und das Teil dort sitzt, wo es hingehört.“
IPS arbeitet mit TruePath zusammen, um dieses potenzielle Problem zu beseitigen, sagte er. Anstatt sich für verschiedene Werte auf das CAM-System zu verlassen, gibt es eine Hochgeschwindigkeits-Glasfaserverbindung direkt zur Maschinensteuerung – es müssen keine Annahmen über Offsets oder Makrowerte getroffen werden, da sie in Echtzeit gelesen werden und die Maschine gestoppt wird sicher vor der problematischen Position.
Obwohl noch nicht für andere Maschinenmarken verfügbar, kommt IPS, ebenso wie intelligentes Maschinenmessen, das Teile misst, die entsprechenden Offsets vornimmt und automatisch jeden Teil des Programms erneut ausführt, der erforderlich ist, um einen Zustand außerhalb der Toleranz zu korrigieren.
„Das ist nicht anders als das, was ein menschlicher Bediener tun würde, aber wir machen es mit Software“, sagte Fritsch. „Wir sind gerade dabei, diese Logik aufzubauen, damit sich die Maschine auf automatisiertes Feedback verlassen kann, um Entscheidungen zu treffen, was letztendlich die Teilequalität verbessert und gleichzeitig Zykluszeiten und Betriebskosten reduziert. Werkstätten sollten nicht zwei oder drei Teile bearbeiten müssen, um ein gutes Teil herzustellen, oder Zeit damit verschwenden, Teile aus der Maschine zu nehmen, um sie zu messen – es sollte das erste Teil, das gute Teil sein, ohne all die menschliche Interaktion. Das ist unser Ziel.“
Automatisierungssteuerung System
- 10 Unternehmen, die modernste 3D-Druck-Simulationssoftware anbieten
- Wenn es um Verschlüsselung geht, sagen Sie Nein zum Status Quo
- Was macht eine erstklassige Robotersimulationssoftware aus?
- Verwenden der 3DG Robotersimulationssoftware zur Planung der Roboterautomatisierung
- Sehen ist Glauben
- 10 Überlegungen bei der Planung von ERP-Software
- Programmieren von 3D-Geometrie ohne CAD/CAM-Software
- Omron führt Simulationssoftware für automatisierte Fabriken ein
- Hängt das Vereinigte Königreich bei Industrierobotern hinterher?
- SinuTrain – CNC-Simulationssoftware von Siemens